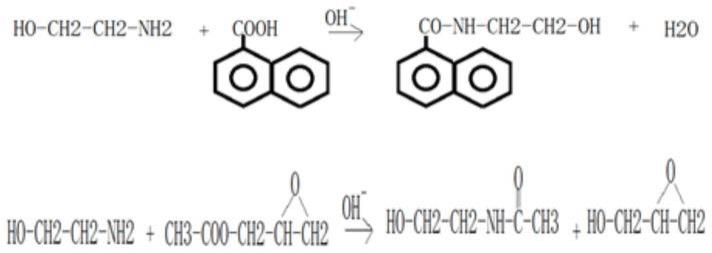
1.本发明属于阻焊油墨技术领域,具体涉及一种减少铜面油墨黑点污染的方法。
背景技术:
2.在pcb印制线路板行业中,会在阻焊前处理中增加氧化铝磨板微蚀,对铜面进行粗化和咬蚀,用于提高阻焊油墨与铜面的结合力和表面处理的抗攻击的性能。然而现有的阻焊显影线多为水平生产线,因铜面前处理方式为氧化铝磨板微蚀,铜面较为粗糙,显影过程油墨大部分以小颗粒的形式与碱性的显影药水发生皂化反应,脱离板面,但是因油墨为小颗粒的形式,容易返粘在直接接触的滚轮片上,随着做板的数量不断增加,因此滚轮片上粘附的油墨会更加多,因显影线的滚辘与阻焊油墨直接接触,会在显影后出现油墨颗粒残留在铜面上、水平线的显影段和水洗段不够充分的问题,容易出现油墨颗粒在滚轮上返沾,经过高温后固化以后,导致出现铜面出现阻焊黑点,形成报废,行业内只能通过降低滚辘的使用时间,提高保养的频率,采用人工的方式,手动擦拭和清洁滚辘上杂物,从而减少油墨返粘和杂物交叉污染,这种方式难以有效的减少铜面油墨黑点污染。
技术实现要素:
3.为了克服现有技术的不足,本发明的目的在于提供一种减少铜面油墨黑点污染的方法,更加高效的脱离残胶和油墨颗粒,解决了铜面黑点污染的问题,最大程度减少铜面黑点异物的报废,提高经济效益。
4.本发明的目的采用如下技术方案实现:
5.一种减少铜面油墨黑点污染的方法,包括外层显影蚀刻褪膜的步骤、自动光学检测的步骤、氧化铝磨板处理的步骤、丝印的步骤、预烤的步骤、曝光的步骤、显影的步骤、后烤和uv固化的步骤、喷砂的步骤和沉镍金的步骤,其特征在于,还包括氧化铝磨板前处理的步骤和铜面黑点清洗的步骤。进一步地,所述氧化铝磨板的步骤包括外层褪膜的步骤;
6.所述外层显影蚀刻褪膜的步骤是对贴附在线路板外层的曝光过的有对应阻焊的图形的外层干膜进行显影蚀刻褪膜,以在线路板铜面上蚀刻成和线路的图形相同的图形;
7.所述自动光学检测的步骤是通过光学检查,用于扫描和修理外层线路图形开路、短路缺陷;
8.所述氧化铝磨板前处理的步骤是在所述氧化铝磨板处理的步骤之前清除在所述外层显影蚀刻褪膜线和所述自动光学检测步骤后残留在铜面上的部分残胶;
9.所述氧化铝磨板处理的步骤是通过酸洗微蚀液对铜面进行微蚀,粗化铜面表面,增加阻焊油墨与铜面的结合力,然后使用风管对铜面进行热风烘干;
10.所述丝印的步骤是通过丝网印刷的方式,将阻焊油墨丝印到铜面上,覆盖对应阻焊的图形和基材区域;
11.所述预烤的步骤是将所述丝印后的阻焊油墨通过烤箱进行低温预烤,将阻焊油墨中的有机溶剂进行烘干予以挥发掉,使阻焊油墨处于半固化状态;
12.所述曝光的步骤是通过曝光机灯管的uv光固化对应阻焊的图形;
13.所述显影的步骤是将接受光固化的对应阻焊的图形区域保留下来,未接受光固化的区域通过皂化反应进行溶解掉;
14.所述后烤和uv固化的步骤是对所述预烤后处于半固化状态下的阻焊油墨进行高温固化和光固化,促进阻焊油墨中的树脂和光敏剂进一步的交联反应;
15.所述铜面黑点清洗的步骤是使所述显影的步骤中残留的、经所述后烤和uv固化在铜面上的阻焊油墨颗粒以及残胶发生溶解反应或进行化学微蚀,削弱油墨颗粒点与铜面的结合力;
16.所述喷砂的步骤是通过物理性打磨和清洗铜面上阻焊油墨颗粒和残胶,使阻焊油墨颗粒和残胶更容易从铜面脱离下来;
17.所述沉镍金的步骤是在催化剂作用下,在铜面上进行沉积镍层以及置换反应沉积金层。
18.进一步地,所述氧化铝磨板前处理的步骤包括氧化铝磨板的步骤和外层褪膜的步骤。
19.进一步地,所述氧化铝磨板的步骤是使用尼龙刷,并以800目氧化铝颗粒作为研磨材料,通过高速旋转对铜面进行清洁。
20.进一步地,所述氧化铝磨板处理的步骤,在热风烘干过程中,使用的风管是透明色pet耐高温材料制成的风管。
21.进一步地,所述氧化铝磨板处理的步骤,在热风烘干过程中,鼓风机前端增加高效过滤器,用于过滤气流中的杂物。
22.进一步地,所述显影的步骤依次包括显影段和水洗段,所述显影段中显影线上的每根滚轮包括14个轮片,所述水洗段用于冲洗干净铜面和所述轮片上的阻焊油墨颗粒。
23.进一步地,所述显影段的显影速度为2.5~2.8m/min,对应的显影浸泡时间45~55s。
24.进一步地,所述显影的步骤中在所述水洗段后面还包括烘干段,通过热风烘干,且使用的风管是透明色pet耐高温材料制成的风管,鼓风机前端增加所述高效过滤器,用于过滤气流中的杂物。
25.进一步地,所述后烤和uv固化的步骤后,所述铜面黑点清洗的步骤包括碱洗段,所述碱洗段使用的药剂包括质量浓度为50%的naoh、50%的乙胺醇和去离子水,所述质量浓度为50%的naoh、所述50%的乙胺醇和所述去离子水的质量比为1:1.6:8。
26.进一步地,所述后烤和uv固化的步骤后,所述铜面黑点清洗的步骤包括微蚀段,所述微蚀段使用的药剂包括h2o2溶液、h2so4溶液和去离子水,所述h2o2溶液、h2so4溶液和去离子水的质量比为1:1:13。
27.相比现有技术,本发明的有益效果在于:
28.1.本发明的一种减少铜面油墨黑点污染的方法,一方面通过氧化铝磨板前处理的步骤,对铜面进行清洁,清除在外层显影蚀刻褪膜线和光学自动光学后残留在铜面上的部分残胶,另一方面通过铜面黑点清洗的步骤中包括碱的洗段和微蚀段,进一步清洁氧化铝磨板铜面上胶渍,小油墨(主要含有ba元素的颗粒)黑点等杂物,可以实现更加高效的脱离残胶和油墨颗粒,解决了铜面黑点污染的问题,最大程度减少铜面黑点异物的报废,提高经
济效益。
29.2.自动光学检测铜面黑点从改进前的6-7点/面下降到0.49-0.63点/面,实际金面黑点报废率也从改进前前的3.53%下降到0.3-0.4%,基本达到预期报废率0.5%的报废目标。
附图说明
30.图1显示铜面表面上残留的残胶。
31.图2是氧化铝磨板清洁过的铜面在3000倍下的扫描电镜图。
32.图3是改进前氧化铝磨板处理后的铜面在3000倍下的扫描电镜图。
33.图4是碱洗段的药剂溶解油墨颗粒和胶渍物质的示意图。
34.图5是微蚀段的药剂削弱油墨颗粒点与铜面的结合力的示意图。
35.图6是氧化铝图喷砂过程中油墨颗粒和胶渍物质脱落的示意图。
36.图7是经过氧化铝磨板前处理的步骤后top面黑点平均数的示意图。
37.图8是经过氧化铝磨板前处理的步骤后bot面黑点平均数的示意图。
具体实施方式
38.下面,结合具体实施方式,对本发明做进一步描述,需要说明的是,在不相冲突的前提下,以下描述的各实施例之间或各技术特征之间可以任意组合形成新的实施例。
39.如图1所示,一种减少铜面油墨黑点污染的方法,包括外层显影蚀刻褪膜的步骤、自动光学检测的步骤、氧化铝磨板处理的步骤、丝印的步骤、预烤的步骤、曝光的步骤、显影的步骤、后烤和uv固化的步骤、喷砂的步骤和沉镍金的步骤,还包括氧化铝磨板前处理的步骤和铜面黑点清洗的步骤。
40.外层显影蚀刻褪膜的步骤具体是对贴附在线路板外层的曝光过的有对应阻焊的图形的外层干膜进行显影蚀刻褪膜,以在线路板铜面上蚀刻成和线路的图形相同的图形。
41.自动光学检测的步骤具体是通过光学检查,用于扫描和修理外层图形开路、短路等缺陷,还用于对铜面上黑点等异物进行扫描和确认,评估铜面黑点的数量(点数/面)。
42.氧化铝磨板处理的步骤具体是使用酸洗微蚀液对铜面进行微蚀,粗化铜面表面,增加阻焊油墨与铜面的结合力,微蚀量为1.2-1.4μm,然后使用风管对铜面进行热风烘干。
43.丝印的步骤具体是通过丝网印刷的方式,将阻焊油墨丝印到铜面上,覆盖对应阻焊的图形和基材区域,丝印压力为3-5kg/cm2;丝印速度为250-350mm/sec。
44.预烤的步骤具体是将所述丝印后的阻焊油墨通过烤箱进行低温预烤,将阻焊油墨中的有机溶剂进行烘干予以挥发掉,使阻焊油墨处于半固化状态,78*38min。
45.曝光的步骤具体是通过曝光机灯管的uv光固化对应阻焊的图形,uv光固化:70-80mj/cm2。
46.显影的步骤具体是将接受光固化的对应阻焊的图形区域保留下来,未接受光固化的区域通过皂化反应进行溶解掉,k2co3的浓度为7-9g/l;显影时间为50-65s。
47.后烤和uv固化的步骤具体是对所述预烤后处于半固化状态下的阻焊油墨进行高温固化和光固化,促进阻焊油墨中的树脂和光敏剂进一步的交联反应,提高油墨的相关可靠性测试,高温固化:150℃*60min;uv光固化:800-1000mj/cm2。
48.喷砂的步骤具体是使用氧化铝粉的材料,使用高压喷嘴的形式,物理性打磨和清洗铜面上油墨异物黑点,提高铜面洁净度,使用的氧化铝粉800目,1.8-2.3kg/cm2。
49.沉镍金的步骤具体是在催化剂作用下,铜面上进行沉积镍层以及通过置换反应沉积金层,用于确保后期焊接的铜面不被氧化和污染。
50.请参阅图1-3,图1显示了铜面表面上残留的残胶,图2是氧化铝磨板清洁过的铜面在3000倍下的扫描电镜图,图3是改进前氧化铝磨板处理后的铜面在3000倍下的扫描电镜图,在所述氧化铝磨板处理的步骤之前,本发明中氧化铝磨板前处理的步骤包括外层褪膜的步骤和氧化铝磨板的步骤,其中,氧化铝磨板的步骤是使用尼龙刷,并以800目氧化铝颗粒作为研磨材料,通过高速旋转对铜面进行清洁,清除在外层显影蚀刻褪膜线和自动光学检测后残留在铜面上的部分残胶,避免直接使用氧化铝磨板处理的步骤,相反在微蚀过程粗化了铜面表面,反而让残胶,胶渍等更加难去掉。
51.请参阅附图4-6,所述后烤和uv固化的步骤后,铜面黑点清洗的步骤包括碱洗段和微蚀段,其中,碱洗段使用的药剂按照质量浓度为50%的naoh、50%的乙胺醇和去离子水的质量比为1:1.6:8配置,oh-离子浓度为6.5-8.5g/l,在该溶液下,使所述显影的步骤中残留的、经所述后烤和uv固化在铜面的含有环氧树脂的阻焊油墨颗粒和胶渍物质,会发生溶解反应,削弱油墨颗粒点与铜面的结合力,容易被后工序进行攻击而脱落;
52.碱洗段化学反应式如下:
[0053][0054]
微蚀段使用的药剂按照h2o2溶液、h2so4溶液和去离子水的质量比为1:1:13配置,h
离子浓度为2.5-3.5g/l,将附着铜面黑点的油墨底部进行化学微蚀,削弱油墨颗粒点与铜面的结合力,更容易被后工序进行攻击而脱落,从而降低铜面黑点数量,传送速度优选为0.8m/min,对应的显影浸泡时间45~55s,相对应的微蚀量控制为0.6μm以上。
[0055]
微蚀段化学反应式如下:
[0056]
cu h2o2 2h
→
cu2
2h2o
[0057]
进一步地,氧化铝磨板处理的步骤中通过热风烘干中,且使用的风管是透明色pet耐高温材料制成的风管,鼓风机前端增加高效过滤器,提高风管的洁净度,用于过滤掉烘干段产生的黑色异物、胶状异物和毛毛丝等铜面黑点形成物质。
[0058]
进一步地,显影的步骤依次包括显影段、水洗段,其中,显影段中显影线上的每根滚轮包括14个轮片,水洗段中每根滚轮包括14个轮片,相比于显影段中每根滚轮包括28个轮片,显影段轮片与板接触次数少,减少了滚辘的油墨颗粒返沾到粗糙的铜面的机率,而且水洗段更长,充分冲洗干净铜面和所述轮片上的阻焊油墨颗粒,避免部分顽固油墨颗粒黏附在滚辘上,将会残留在实际板面图形上,在铜面上形成黑点,形成铜面杂物报废。
[0059]
其中,显影段具体是碱性药水与未光固化的油墨发生皂化反应,由板面上片状下
油区满满变成颗粒状油墨碎,脱离板面,显影段的显影速度优先为2.5~2.8m/min,对应的显影浸泡时间45~55s;
[0060]
水洗段具体是在皂化反应过程中,因油墨表面与滚辘接触,部分顽固油墨颗粒会黏附在滚辘上,经过水洗,目的是利用高压水洗,冲掉残留在板面和滚辘上的油墨颗粒,但如果水洗不充分,则会有部分顽固油墨颗粒会黏附在滚辘上,滚辘的油墨颗粒返沾到粗糙的铜面,将会残留在实际板面图形上,在铜面上形成黑点,形成铜面杂物报废。
[0061]
进一步地,显影的步骤还包括显影补充段、烘干段,烘干段和氧化铝磨板处理的步骤一样,在热风烘干过程中,使用的风管是透明色pet耐高温材料制成的风管,鼓风机前端增加高效过滤器,提高风管的洁净度,用于进一步过滤掉烘干段产生的黑色异物、胶状异物和毛毛丝等铜面黑点形成物质。
[0062]
实施例1
[0063]
本实施例提供一种减少铜面油墨黑点污染的方法,依次包括如下步骤:铜面外层显影蚀刻褪膜的步骤、自动光学检测的步骤、氧化铝磨板的步骤、氧化铝磨板处理的步骤、丝印的步骤、预烤的步骤、曝光的步骤、显影的步骤、后烤和uv固化的步骤、碱洗段、微蚀段、喷砂的步骤和沉镍金的步骤。
[0064]
实施例2
[0065]
本实施例提供一种减少铜面油墨黑点污染的方法,依次包括如下步骤:铜面外层显影蚀刻褪膜的步骤、自动光学检测的步骤、外层褪的步骤、氧化铝磨板处理的步骤、丝印的步骤、预烤的步骤、曝光的步骤、显影的步骤、后烤和uv固化的步骤、碱洗段、微蚀段、喷砂的步骤和沉镍金的步骤。
[0066]
实施例3
[0067]
本实施例提供一种减少铜面油墨黑点污染的方法,依次包括如下步骤:铜面外层显影蚀刻褪膜的步骤、自动光学检测的步骤、氧化铝磨板的步骤、氧化铝磨板处理的步骤、丝印的步骤、预烤的步骤、曝光的步骤、显影的步骤、后烤和uv固化的步骤、碱洗段、喷砂的步骤和沉镍金的步骤。
[0068]
实施例4
[0069]
本实施例提供一种减少铜面油墨黑点污染的方法,依次包括如下步骤:铜面外层显影蚀刻褪膜的步骤、自动光学检测的步骤、氧化铝磨板的步骤、氧化铝磨板处理的步骤、丝印的步骤、预烤的步骤、曝光的步骤、显影的步骤、后烤和uv固化的步骤、微蚀段、喷砂的步骤和沉镍金的步骤。
[0070]
实施例5
[0071]
本实施例提供一种减少铜面油墨黑点污染的方法,依次包括如下步骤:铜面外层显影蚀刻褪膜的步骤、自动光学检测的步骤、氧化铝磨板的步骤、氧化铝磨板处理的步骤、丝印的步骤、预烤的步骤、曝光的步骤、显影的步骤、后烤和uv固化的步骤、碱洗段、微蚀段、沉镍金的步骤。
[0072]
实施例6
[0073]
本实施例提供一种减少铜面油墨黑点污染的方法,依次包括如下步骤:铜面外层显影蚀刻褪膜的步骤、自动光学检测的步骤、氧化铝磨板的步骤、氧化铝磨板处理的步骤、丝印的步骤、预烤的步骤、曝光的步骤、显影的步骤、后烤和uv固化的步骤、碱洗段、微蚀段、
喷砂的步骤和沉镍金的步骤,显影段的显影速度优先为2.5m/min,对应的显影浸泡时间45s。
[0074]
实施例7
[0075]
本实施例提供一种减少铜面油墨黑点污染的方法,依次包括如下步骤:铜面外层显影蚀刻褪膜的步骤、自动光学检测的步骤、氧化铝磨板的步骤、氧化铝磨板处理的步骤、丝印的步骤、预烤的步骤、曝光的步骤、显影的步骤、后烤和uv固化的步骤、碱洗段、微蚀段、喷砂的步骤和沉镍金的步骤,显影段的显影速度优先为2.8m/min,对应的显影浸泡时间55s。
[0076]
实施例8
[0077]
本实施例提供一种减少铜面油墨黑点污染的方法,依次包括如下步骤:铜面外层显影蚀刻褪膜的步骤、自动光学检测的步骤、氧化铝磨板的步骤、氧化铝磨板处理的步骤、丝印的步骤、预烤的步骤、曝光的步骤、显影的步骤、后烤和uv固化的步骤、碱洗段、微蚀段、喷砂的步骤和沉镍金的步骤,针对微蚀段不同传送速度所对应的微蚀量对铜面黑点数进行研究。
[0078]
对比例1
[0079]
本对比例提供一种减少铜面油墨黑点污染的方法,依次包括如下步骤:铜面外层显影蚀刻褪膜的步骤、自动光学检测的步骤、氧化铝磨板处理的步骤、丝印的步骤、预烤的步骤、曝光的步骤、显影的步骤、后烤和uv固化的步骤、喷砂的步骤和沉镍金的步骤,其中显影的步骤为2.8m/min,对应的显影浸泡时间55s。
[0080]
对比例2
[0081]
本对比例提供一种减少铜面油墨黑点污染的方法,依次包括如下步骤:铜面外层显影蚀刻褪膜的步骤、自动光学检测的步骤、氧化铝磨板的步骤、氧化铝磨板处理的步骤、丝印的步骤、预烤的步骤、曝光的步骤、显影的步骤、后烤和uv固化的步骤、喷砂的步骤和沉镍金的步骤。
[0082]
对比例3
[0083]
本对比例提供一种减少铜面油墨黑点污染的方法,依次包括如下步骤:铜面外层显影蚀刻褪膜的步骤、自动光学检测的步骤、氧化铝磨板的步骤、氧化铝磨板处理的步骤、丝印的步骤、预烤的步骤、曝光的步骤、显影的步骤、后烤和uv固化的步骤、沉镍金的步骤。
[0084]
对比例4
[0085]
本对比例提供一种减少铜面油墨黑点污染的方法,依次包括如下步骤:铜面外层显影蚀刻褪膜的步骤、自动光学检测的步骤、氧化铝磨板处理的步骤、丝印的步骤、预烤的步骤、曝光的步骤、显影的步骤、后烤和uv固化的步骤、碱洗段、微蚀段、喷砂的步骤和沉镍金的步骤,显影段的显影速度优先为2.8m/min,对应的显影浸泡时间55s。
[0086]
实验例1
[0087]
将实施例1~2的氧化铝磨板前处理的步骤的结果和对比例1进行比较,结果请参阅附图7~8所示,从图中可以看出,氧化铝磨板的步骤和外层褪膜的步骤都能显著降低top面黑点平均数和bot面黑点平均数(p<0.05)。
[0088]
实验例2
[0089]
将实施例3~5铜面黑点清洗步骤的结果和对比例2~3进行比较,结果如表1所示,
铜面中含有正排状的金手指的设计是top面,无该金手指的设计的设计是bot。
[0090]
表1
[0091][0092]
从表中可以看出,铜面黑点清洗步骤中增加碱洗段、增加微蚀段、增加sm喷砂都能降低top面黑点平均数和bot面黑点平均数,增加碱洗段、增加微蚀段降低top面黑点平均数和bot面黑点平均数(p<0.05)。
[0093]
实验例3
[0094]
将实施例8铜面黑点清洗步骤中针对微蚀段不同传送速度所对应的微蚀量对铜面黑点数进行研究的结果如表2所示。
[0095]
表2
[0096]
[0097][0098]
从表中可以看出,在降低top面黑点平均数和bot面黑点平均数中,传送速度优选为0.8m/min,相对应的微蚀量控制为0.6μm以上。
[0099]
实验例4
[0100]
将实施例6~7显影的步骤中针对显影速度对铜面黑点数的影响进行研究,和对比例1进行比较,结果如表3所示。
[0101]
表3
[0102][0103]
从表中可以看出,显影的步骤中,显影段的显影速度优先为2.5m/min,对应的显影浸泡时间45s,能显著降低top面黑点平均数和bot面黑点平均数(p<0.05)。
[0104]
实验例5:油墨的相关可靠性测试
[0105]
表4
[0106][0107]
测试结果表明,本发明实施例1的改进方案相比对比例1的改进前的方案,各项可靠性测试都合格,达到预期目标,满足产品生产合格要求。
[0108]
综上所述,自动光学检测铜面黑点从改进前的6-7点/面下降到0.49-0.63点/面,实际金面黑点报废率也从改进前前的3.53%下降到0.3-0.4%,基本达到预期报废率0.5%的报废目标。
[0109]
上述实施方式仅为本发明的优选实施方式,不能以此来限定本发明保护的范围,本领域的技术人员在本发明的基础上所做的任何非实质性的变化及替换均属于本发明所要求保护的范围。
再多了解一些
本文用于企业家、创业者技术爱好者查询,结果仅供参考。