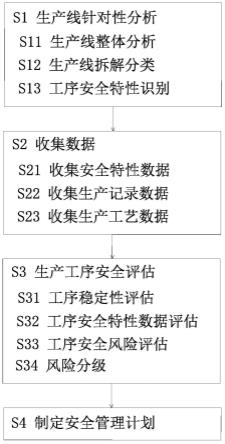
1.本技术涉及生产安全管理的领域,尤其是涉及一种制造业生产线的生产安全评估管理方法及系统。
背景技术:
2.在生产线生产过程中,安全规范标准是进行安全评价与安全绩效考核的尺度。“事故处理”与“安全检查”是传统建设安全控制的日常工作重心,强调的是一种事后控制。但是传统的安全规范标准中定性的描述较多,定量的描述较少,不能充分发挥安全控制中风险识别、评价、预测方面的优势。为了能够将建设过程中存在的各种安全隐患有机的联系在一起全面分析,就应该进行“全过程”、“全寿命周期”的安全控制和管理,这也是传统安全控制模式根本无法实现的。
3.cn201911045483.6公开了一种工业企业安全生产风险辨识系统,其技术方案为:包括数据采集模块、摄像头、数据库、识别单元、比对单元、监测模块、分析模块、警报单元、风险判定模块和智能设备;所述数据采集模块用于采集材料信息和工人移动速度数据,所述数据采集模块将材料信息传输到识别单元,所述识别单元通过rohs有害物质检测设备将材料分别标记为有害材料数据和无害材料数据,并将无害材料数据传输至比对单元,所述数据库内存储有有害材料反应数据、特征数据和两者反应时间数据,所述比对单元从数据库内获取有害材料反应数据,并将其与无害材料数据进行比对操作,得出该无害物质不存在安全隐患和该无害物质存在安全隐患;所述摄像头用于对生产线周边的物质进行监控并自动获取影像信息,并将影像信息传输至识别单元,所述识别单元通过影像识别出影像信息中的影像特征数据,并将影像特征数据传输到比对单元,比对单元将影像特征数据与特征数据进行特征对比操作,得出两者反应时间数据;所述监测模块用于监测生产车间出口的位置数据和工人的位置数据,并将其传输至分析模块,所述数据采集模块将工人移动速度数据传输至分析模块,分析模块用于对生产车间出口的位置数据、工人的位置数据和工人移动速度数据进行分析操作,得出平均撤离时间;监测模块还用于对设备的状态进行监控并自动获取设备影像信息,所述监测模块将设备影像信息经识别单元识别分析后传输到分析模块,所述数据库内还存储有设备的长度数据、宽度数据和高度数据,分析模块获取数据库内存储的设备长度数据、宽度数据和高度数据;所述分析模块还用于对设备影像信息、设备的长度、宽度和高度进行设备安全解析操作,得出倾斜角度;所述风险判定模块用于对倾斜角度和平均撤离时间进行风险判断操作,得出撤离一级风险信号、撤离二级风险信号、撤离三级风险信号、设备一级倒塌信号和设备二级倒塌信号,警报单元将其转化成撤离一级风险警报、撤离二级风险警报、撤离三级风险警报、设备一级倒塌警报和设备二级倒塌警报,并将警报发送至智能设备。
4.该工业企业安全生产风险辨识系统具有以下优点:通过分析模块计算出工人在发生事故时脱离生产车间的时间,并将工人脱离时间与两者的反应时间进行比对,从而得出工人在事故发生时撤离的风险,对撤离风险进行评估,提前发现材料中的安全隐患,并做好
安全撤离的风险,增加对员工的生命保障;通过监控模块对设备的状态记忆改变的位置的检测,从而对设备的倾斜进行判定,并计算其倾斜角度,从而对设备对员工的危害进行分析,评定危害等级,增加对员工生命的保障。
5.但是,该工业企业安全生产风险辨识系统也具有以下缺点:未考虑生产稳定性对生产安全的影响,生产稳定性较差的生产线易发生较大的生产偏差,从而引发安全隐患;未能对生产线各工序进行针对性分析,评价方式无法满足生产线中各生产工序的多样性。
6.因此,需要一种考虑生产稳定性对生产安全的影响、对生产线各工序进行针对性分析的方法或系统。
技术实现要素:
7.为了解决未考虑生产稳定性对生产安全影响、评价方式无法满足各工序多样性的问题,本技术提供一种制造业生产线的生产安全评估管理方法及系统。
8.本技术提供一种制造业生产线的生产安全评估管理方法,包括以下步骤:步骤s1,生产线针对性分析,先对生产线整体分析,后将生产线拆解为若干工序,对拆解后的生产工序分别分析;步骤s2,收集数据,收集数据并录入安全管理平台的数据库中;步骤s3,生产工序安全评估,对工序分别进行多维度安全性评估;步骤s4,制定安全管理计划,根据对生产线的安全评估实时结果,制定并动态调整生产线管理计划。
9.进一步的,所述步骤s1包括:步骤s11,生产线整体分析,对生产线进行整体生产路线分析;步骤s12,生产线拆解分类,将生产线拆解为若干工序,对工序的生产类别进行识别,将工序具体划分为加工工序、移动工序、储存工序,并将相同类别的生产工序进行归类;步骤s13,工序安全特性识别,结合工序类别,根据工序生产内容识别工序中的安全特性;所述步骤s13中,加工工序的安全特性包括但不限于:工业介质温度参数、生产设备温度参数、生产设备实时功率参数、生产环境参数;移动工序的安全特性包括但不限于:移动坐标;储存工序的安全特性包括但不限于:储存环境湿度、储存环境温度。
10.进一步的,所述步骤s2包括:步骤s21,收集安全特性数据,针对步骤s13识别的各工序的安全特性,由生产线监控终端对生产线进行实时监控并采集安全特性数据,将安全特性数据上传至安全管理平台;步骤s22,收集生产记录数据,由生产记录终端采集生产过程的生产参数,并将生产参数数据上传至安全管理平台;步骤s23,收集生产工艺数据,由生产设备终端采集录入生产设备的标准工艺参数,并将标准工艺参数数据上传至安全管理平台。
11.进一步的,所述步骤s3包括:步骤s31,工序稳定性评估,提取各工序的生产记录数据和生产工艺数据,对工序稳定性进行评估;步骤s32,工序安全特性数据评估,提取工序的安全数据,并对各种类安全特性数据分别进行评估;步骤s33,工序安全风险评估,结合工序稳定性和工序各种类安全特性数据的评估结果,综合分析后对工序进行安全风险评估;步骤s34,风险分级,根据各工序的安全风险评估结果,对各工序进行风险级别划分。
12.进一步的,所述步骤s31中,工序的稳定性评价方法为:若工序类别为加工工序,则生产稳定指数计算方法如下:
,其中,α表示为生产线拆解后的某加工工序的生产稳定指数;a表示为该加工工序中所有生产参数的种类数量;x1表示为该加工工序中种类编号为1的生产参数值;y1表示为该加工工序中种类编号为1的标准工艺参数值;`x1表示为该加工工序中种类编号为1的生产参数平均值;x2表示为该加工工序中种类编号为2的生产参数值;y2表示为该加工工序中种类编号为2的标准工艺参数值;`x2表示为该加工工序中种类编号为2的生产参数平均值;xa表示为该加工工序中种类编号为a的生产参数值;ya表示为该加工工序中种类编号为a的标准工艺参数值;`xa表示为该加工工序中种类编号为a的生产参数平均值;若工序类别为储存工序或移动工序,则将该工序的安全特性数据代入为x,将安全特性数据的安全上限和安全下限的平均值代入为y计算工序的稳定性。
13.通过采用上述技术方案,对生产过程的生产稳定性进行评价,生产稳定性越差则安全事故的发生率越高,并且生产稳定性越差对安全事故发生率的影响能力越大,增加了对生产安全风险评估的维度,提高了生产安全评估的准确性。
14.进一步的,所述步骤s32中,首先对生产工序的各种类安全特性数据进行安全评估,然后汇总各种类安全特性数据对生产工序进行安全评估;,其中,j表示为某生产工序中的安全特性数据种类编号;λj表示为该生产工序中种类编号为j的安全特性数据的安全指数;qj表示为该生产工序中种类编号为j的安全特性数据的安全上限值;pj表示为该生产工序中种类编号为j的安全特性数据的安全下限值;i表示为该生产工序中的数据时刻样本编号;n表示为该生产工序中所有数据时刻样本的总数量;s
ij
表示为该生产工序中种类编号为j、数据时刻样本编号为i的安全特性数据数值;`sj表示为该生产工序中种类编号为j的安全特性数据在样本编号1-n中的平均数值;,其中,η表示为某生产工序的安全风险系数,且安全风险系数η越大,则该工序发生安全事故的可能性越高,安全风险系数η越小,则该工序发生安全事故的可能性越低;m表示为生产线中所有生产工序的总数量;λ1表示为该生产工序中种类编号为1的安全特性数据的安全指数;λ2表示为该生产工序中种类编号为2的安全特性数据的安全指数;λm表示为该生产工序中种类编号为m的安全特性数据的安全指数;α表示为该生产工序的生产稳定指数。
15.通过采用上述技术方案,首先提取安全特性数据,后评估各种类安全特性数据,最后结合生产稳定性和各种类安全特性数据对工序进行安全风险评估,提高了安全风险评估的准确性。
16.进一步的,所述步骤s4中,若某生产工序安全风险级别升高,则调整安全管理计划并提高管理频度;若某生产工序安全风险级别降低,则调整安全管理计划并降低管理频度;持续进行步骤1-步骤3并将实时上传分析结果至安全管理平台,对安全管理计划管理频度进行动态更新;所述安全管理计划包括:日常检查计划、周期性维护计划、部件更换计划。
17.通过采用上述技术方案,根据各工序的安全风险评估结果,针对性地调整安全管理计划,满足了各工序的多样性,提高了对各种类生产工序的适应能力。
18.一种制造业生产线的生产安全评估管理系统,包括:安全管理平台、生产线监控终端、生产设备终端、生产记录终端;所述安全管理平台包括:存储器;处理器,与存储器连接;数据库,设置在存储器内,用于存储大量数据;工序稳定性评估模块,运行在所述处理器上,用于运行指定算法对各工序稳定性进行评估;工序安全特性数据评估模块,运行在所述处理器上,用于运行指定算法对工序各种类安全数据进行安全评估;工序安全风险评估模块,运行在所述处理器上,用于运行指定算法对各工序安全风险进行评估。
19.进一步的,所述生产线监控终端与安全管理平台连接,用于监控生产线生产过程并采集安全特性数据;所述生产设备终端与安全管理平台连接,用于提取录入生产设备的工艺参数,并上传至安全管理平台;所述生产记录终端与安全管理平台连接,用于采集实时生产数据并上传至安全管理平台。
20.综上所述,本技术包括以下有益技术效果:1.通过对生产过程的生产稳定性进行评价,生产稳定性越差则安全事故的发生率越高,并且生产稳定性越差对安全事故发生率的影响能力越大,增加了对生产安全风险评估的维度;2.首先提取安全特性数据,然后评估各种类安全特性数据,最后结合生产稳定性和各种类安全特性数据对工序进行安全风险评估,提高了安全风险评估的准确性;3.通过对工序的拆解评价和分别管理,根据各工序的安全风险评估结果,针对性地调整安全管理计划,满足了各工序的多样性,提高了对各种类生产工序的适应能力。
附图说明
21.图1是本技术实施例的一种制造业生产线的生产安全评估管理方法的步骤图。
22.图2是本技术实施例的一种制造业生产线的生产安全评估管理系统的结构图。
23.附图标记说明:1、安全管理平台;2、存储器;21、数据库;3、处理器;4、工序生产稳定性评估模块;5、工序安全特性数据评估模块;6、工序安全风险评估模块;7、生产线监控装置;8、生产设备终端;9、生产记录终端。
具体实施方式
24.下面对照附图,通过对实施例的描述,本技术的具体实施方式如所涉及的各构件
的形状、构造、各部分之间的相互位置及连接关系、各部分的作用及工作原理、制造工艺及操作使用方法等,作进一步详细的说明,以帮助本领域技术人员对本发明的发明构思、技术方案有更完整、准确和深入的理解。为方便说明,本技术提及方向以附图所示方向为准。
25.参照图1-图2所示,一种制造业生产线的生产安全评估管理方法,包括以下步骤:步骤s1,生产线针对性分析,先对生产线整体分析,后将生产线拆解为若干工序,对拆解后的生产工序分别分析;步骤s2,收集数据,收集数据并录入安全管理平台1的数据库21中;步骤s3,生产工序安全评估,对工序分别进行多维度安全性评估;步骤s4,制定安全管理计划,根据对生产线的安全评估实时结果,制定并动态调整生产线管理计划。
26.所述步骤s1包括:步骤s11,生产线整体分析,对生产线进行整体生产路线分析;步骤s12,生产线拆解分类,将生产线拆解为若干工序,对工序的生产类别进行识别,将工序具体划分为加工工序、移动工序、储存工序,并将相同类别的生产工序进行归类;步骤s13,工序安全特性识别,结合工序类别,根据工序生产内容识别工序中的安全特性;所述步骤s13中,加工工序的安全特性包括但不限于:工业介质温度参数、生产设备温度参数、生产设备实时功率参数、生产环境参数;移动工序的安全特性包括但不限于:移动坐标;储存工序的安全特性包括但不限于:储存环境湿度、储存环境温度。
27.所述步骤s2包括:步骤s21,收集安全特性数据,针对步骤s13识别的各工序的安全特性,由生产线监控终端7对生产线进行实时监控并采集安全特性数据,将安全特性数据上传至安全管理平台1;步骤s22,收集生产记录数据,由生产记录终端9采集生产过程的生产参数,并将生产参数数据上传至安全管理平台1;步骤s23,收集生产工艺数据,由生产设备终端8采集录入生产设备的标准工艺参数,并将标准工艺参数数据上传至安全管理平台1。
28.所述步骤s3包括:步骤s31,工序稳定性评估,提取各工序的生产记录数据和生产工艺数据,对工序稳定性进行评估;步骤s32,工序安全特性数据评估,提取工序的安全数据,并对各种类安全特性数据分别进行评估;步骤s33,工序安全风险评估,结合工序稳定性和工序各种类安全特性数据的评估结果,综合分析后对工序进行安全风险评估;步骤s34,风险分级,根据各工序的安全风险评估结果,对各工序进行风险级别划分。
29.所述步骤s31中,工序的稳定性评价方法为:若工序类别为加工工序,则生产稳定指数计算方法如下:,其中,α表示为生产线拆解后的某加工工序的生产稳定指数;a表示为该加工工序中所有生产参数的种类数量;x1表示为该加工工序中种类编号为1的生产参数值;y1表示为该加工工序中种类编号为1的标准工艺参数值;`x1表示为该加工工序中种类编号为1的生产参数平均值;x2表示为该加工工序中种类编号为2的生产参数值;y2表示为该加工工序中种类编号为2的标准工艺参数值;`x2表示为该加工工序中种类编号为2的生产参数平均值;xa表示为该加工工序中种类编号为a的生产参数值;ya表示为该加工工序中种类编号为a的标准工艺参数值;`xa表示为该加工工序中种类编号为a的生产参数平均值;
若工序类别为储存工序或移动工序,则将该工序的安全特性数据代入为x,将安全特性数据的安全上限和安全下限的平均值代入为y计算工序的稳定性。
30.所述步骤s32中,首先对生产工序的各种类安全特性数据进行安全评估,然后汇总各种类安全特性数据对生产工序进行安全评估;,其中,j表示为某生产工序中的安全特性数据种类编号;λj表示为该生产工序中种类编号为j的安全特性数据的安全指数;qj表示为该生产工序中种类编号为j的安全特性数据的安全上限值;pj表示为该生产工序中种类编号为j的安全特性数据的安全下限值;i表示为该生产工序中的数据时刻样本编号;n表示为该生产工序中所有数据时刻样本的总数量;s
ij
表示为该生产工序中种类编号为j、数据时刻样本编号为i的安全特性数据数值;`sj表示为该生产工序中种类编号为j的安全特性数据在样本编号1-n中的平均数值;,其中,η表示为某生产工序的安全风险系数,且安全风险系数η越大,则该工序发生安全事故的可能性越高,安全风险系数η越小,则该工序发生安全事故的可能性越低;m表示为生产线中所有生产工序的总数量;λ1表示为该生产工序中种类编号为1的安全特性数据的安全指数;λ2表示为该生产工序中种类编号为2的安全特性数据的安全指数;λm表示为该生产工序中种类编号为m的安全特性数据的安全指数;α表示为该生产工序的生产稳定指数。
31.所述步骤s4中,若某生产工序安全风险级别升高,则调整安全管理计划并提高管理频度;若某生产工序安全风险级别降低,则调整安全管理计划并降低管理频度;持续进行步骤1-步骤3并将实时上传分析结果至安全管理平台1,对安全管理计划管理频度进行动态更新;所述安全管理计划包括:日常检查计划、周期性维护计划、部件更换计划。
32.一种制造业生产线的生产安全评估管理系统,包括:安全管理平台1、生产线监控终端7、生产设备终端8、生产记录终端9;所述安全管理平台1包括:存储器2;处理器3,与存储器2连接;数据库21,设置在存储器2内,用于存储大量数据;工序稳定性评估模块4,运行在所述处理器3上,用于运行指定算法对各工序稳定性进行评估;工序安全特性数据评估模块5,运行在所述处理器3上,用于运行指定算法对工序各种类安全数据进行安全评估;工序安全风险评估模块6,运行在所述处理器3上,用于运行指定算法对各工序安全风险进行评估。
33.所述生产线监控终端7与安全管理平台1连接,用于监控生产线生产过程并采集安全特性数据;所述生产设备终端8与安全管理平台1连接,用于提取录入生产设备的工艺参数,并上传至安全管理平台1;所述生产记录终端9与安全管理平台1连接,用于采集实时生产数据并上传至安全管理平台1。
34.本技术实施例,一种制造业生产线的生产安全评估管理方法及系统的工作原理为:对生产过程的生产稳定性进行评价,生产稳定性越差则安全事故的发生率越高,并且生产稳定性越差对安全事故发生率的影响能力越大,增加了对生产安全风险评估的维度;首先提取安全特性数据,然后评估各种类安全特性数据,最后结合生产稳定性和各种类安全特性数据对工序进行安全风险评估,提高了安全风险评估的准确性。
35.本技术实施例中,通过对工序的拆解评价和分别管理,根据各工序的安全风险评估结果,针对性地调整安全管理计划,满足了各工序的多样性,提高了对各种类生产工序的适应能力。
36.以上示意性地对本发明及其实施方式进行了描述,该描述没有限制性,附图所示的也只是本发明的实施方式之一,实际的结构并不局限与此。所以,如果本领域的普通技术人员受其启示,在不脱离本发明创造宗旨的情况下,不创造性地设计出与该技术方案相似的结构方式及实施例,均应属于本发明的保护范围。
再多了解一些
本文用于企业家、创业者技术爱好者查询,结果仅供参考。