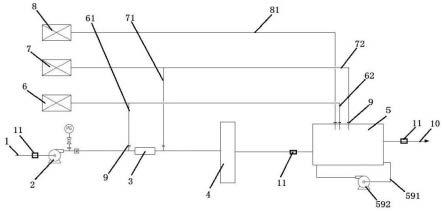
1.本发明涉及油气田复杂废液处理领域,尤其是涉及一种油气田复杂废液多功能预处理装置及预处理方法。
背景技术:
2.随着油田开发的逐步深入,产生废液的成分也越来越复杂、性质也越来越多变,使得废液达标处理的难度不断加大。此外,由于地层压裂条件的不同,每口钻井压裂液的成分各异,这也对产出水处理工艺处理不同水质的适应性提出了挑战。另外,各大油田已逐步加大对边远小区块的开发力度,但由于边远小区块的地理位置偏远,产出水量少,且产出水多为间歇、非连续的,若经拉运或管输至集中处理站则处理成本高。针对上述情况,如采用单一的预处理技术则需要根据不同的废液(包括产出水)性质选择不同的预处理方式,而单一的预处理方式通常无法满足复杂废液的处理需要,无法达到较好的处理效果,因此,需要依据不同的废液性质糅合不同的预处理工艺以形成组合工艺。结合目前油田废液处理工艺所广泛采用的重力除油、混凝沉降、溶气气浮、过滤等组合工艺流程,不仅流程长,使得工艺装置规模较大,难于橇装化,而且针对难降解废液处理的适用性也不是很强,出水效果并不理想,且对于边远小区块零散废液处理的适用性较差。若为确保出水水质而加大药剂的投放量,则势必会造成药剂使用量与污泥产生量的增加,从而使运行和处置成本上升。
3.此外,参考油田废液处理的相关技术,申请号为201620765032.5的专利文件公开了一种油气田废水平台化处理系统,其为依次连接返排井场、缓存罐、压裂返排液处理系统和回用水暂存池,其中压裂返排液处理系统包括依次连接的氧化池、除硬池、絮凝沉降装置、介质过滤器和污泥处理装置,但是该装置工艺流程过于复杂,使得装置规模较大,运营成本投入较大,且无法橇装化,不适用于边远小区块的零散废液的处理。申请号为201310120660.9的专利文件公开了一种油气田废水处理装置及其处理方法,其是利用废热资源,通过高效浮动床直接接触废水加热系统,通过废水与空气逆流接触使其蒸发成水蒸气,之后冷凝成净化水,分离出的有效成分高度浓缩后可回用,但是该技术需要用到废热资源,而一般的废液处置现场很难满足条件,因此,该技术虽然装置规模不大且废液处理效率较高,但难以在一般的废液处置现场推广应用。申请号为201520937062.5的专利文件公开了一种移动式橇装油气田废水处理装置,该装置设有气浮室、过滤室、消毒室,通过气浮室对废水中的油性物质进行去除,且过滤室对悬浮物的去除效果也较好,虽然该装置规模较小,能够橇装化,并具有较大的成本优势,但是该装置对于水质较差的废液的适应性并不好。
4.因此,设计一种可实现多种预处理功能,以满足不同性质废液处置过程,并可根据废液性质的多变进行灵活调整,且装置规模较小,可用于边远小区块零散废液处理的预处理装置及处理方法,已成为本领域丞待解决的课题之一。
技术实现要素:
5.本技术方案要解决的技术问题是,如何提供一种可以满足不同性质废液处置过程,且装置内部结构紧凑,装置整体规模较小,并可实现多级加药混凝、微泡破胶、多级氧化、溶气气浮、沉降及加药澄清的工艺串联流程,以对不同废液实施去除固体悬浮物、破胶、除油、降解功能的高效处理装置及处理方法。
6.为了解决上述技术问题,本技术方案提供了一种油气田复杂废液多功能预处理装置,其包括:提升泵、管道混合器、加气絮凝装置、强化絮凝分离装置、第一加药装置、第二加药装置及第三加药装置;其中,废液来水管线连接提升泵的泵入端,提升泵的泵出端通过管线连接管道混合器的输入端,管道混合器的输出端通过管线连接加气絮凝装置的进水端,加气絮凝装置的出水端通过管线连接强化絮凝分离装置的进水端,强化絮凝分离装置的出水端连接排水管,第一加药装置通过第一加药管线连接管道混合器的输入端的管线且于第一加药管线上设置有阀门,第二加药装置通过第二加药管线连接管道混合器的输出端的管线且于第二加药管线上设置有阀门,第一加药装置还通过第三加药管线连通强化絮凝分离装置的第一反应室且于第三加药管线上设置有阀门,第二加药装置还通过第四加药管线连通强化絮凝分离装置的第二反应室且于第四加药管线上设置有阀门,第三加药装置通过第五加药管线连通强化絮凝分离装置的第一反应室且于第五加药管线上设置有阀门;该加气絮凝装置可将被输送入其内部的废液进行微泡破胶、曝气氧化、絮凝及沉降处理后通过管线输送入强化絮凝分离装置内部,强化絮凝分离装置可将被输送入其内部的废液进行溶气气浮、浮油收集、化学氧化、加药澄清、絮凝、斜板沉降及再次浮油收集后通过排水管排出。据此,通过将加气絮凝装置与强化絮凝分离装置的串联应用,可对预处理装置的整体结构进行优化,从而减小预处理装置的整体规模,并能够确保废液处理工艺的高效运行;另外,通过控制各条加药管线上的阀门,可使预处理装置实现多级加药混凝、多级氧化及加药澄清的流程工艺,以满足不同性质废液的处置需要。
7.作为本技术方案的另一种实施,该加气絮凝装置包括:外筒体、处理液排管、内筒体、气泡液进管、进水环管、至少一条气泡发生器管路及泥渣排管;其中,外筒体呈胶囊状且竖直向设置,外筒体的上端部开设有与外界相通的排气孔,外筒体的下端部的中心位置开设有通口以及围绕通口开设有至少一个处理液出口,该至少一个处理液出口连接处理液排管;内筒体与外筒体共轴线且由数根支撑杆固定连接于内筒体外侧面及外筒体内侧面之间而使内筒体被设置于外筒体内部,且内筒体外侧面与外筒体内侧面之间间隔有间距,以此形成沉降空间;该内筒体由上至下包括圆筒段、收腰段及漏斗段,圆筒段的上端部为开放式的敞口,圆筒段的内侧面间隔环设有双层的导流结构,导流结构是由数个均匀间隔设置于圆筒段内侧面上的横向截面呈等腰三角形的导流器构成,且导流器横向截面的两条等腰边呈内凹圆弧状,并且上层导流结构的导流器是与下层导流结构的导流器相错开的,收腰段结合于圆筒段的下端部,且收腰段中间部位的直径小于其上、下端部的直径,漏斗段结合于收腰段的下端部,且漏斗段的直径由上至下渐小,漏斗段的下端部对应通口位置开设有通孔,气泡液进管穿设密封结合于通口,且气泡液进管的上端部与通孔连通,气泡液进管的下端部位于通口外侧且为封闭状;进水环管环设固定于外筒体外侧面的上部,且进水环管上开设有进水孔以通过管线连接管道混合器的输出端,进水环管上还开设有至少一个废液输出口,气泡液进管上对应至少一个废液输出口而开设有至少一个废液输入口,且于至少一
个废液输出口至至少一个废液输入口间接设至少一条气泡发生器管路,并于气泡发生器管路上设置有气泡发生器;气泡液进管的底部还开设有排渣口,排渣口连接泥渣排管。以此,使得加气絮凝装置内部结构紧凑,废液处理效率高,可对被输送入其内部的废液进行微泡破胶、曝气氧化、旋流和涡流絮凝及沉降工艺。
8.作为本技术方案的另一种实施,该强化絮凝分离装置由其进水端至其出水端方向包括:接触室、两个油渣室、分隔室、第一混合室、第一反应室、第二混合室、第二反应室、斜板沉降室及清水室;接触室连接废液进水管,两个油渣室分别设置于接触室的两侧,分离室设置于接触室相对于废液进水管的另一侧,且分离室与接触室和两个油渣室之间是以上端部朝向分离室倾斜设置的隔板所区隔的,于接触室上方且与隔板上端部高度相同的位置处装设有第一收油槽,第一收油槽的两端分别与两个油渣室的上部相通,废液由接触室经溢流进入分离室,分离室的底部形成有第一污泥斗,第一污泥斗装设有排泥管,第一混合室、第一反应室及第二混合室是并排设置于分离室相对于隔板的另一侧,且分离室与第一混合室通过流道连通,第一混合室与第一反应室通过流道连通,第一反应室与第二混合室通过流道连通,并且于第一混合室及第二混合室均装设有搅拌装置,第二反应室设置于并排设置的第一混合室、第一反应室及第二混合室的另一侧,且第二反应室与第二混合室通过流道连通,第二反应室的底部形成有第二污泥斗,第二污泥斗装设有排泥管,斜板沉降室设置于第二反应室的另一侧,且第二反应室与斜板沉降室通过流道连通,斜板沉降室上方装设有第二收油槽,清水室设置于斜板沉降室的另一侧,废液由斜板沉降室经溢流进入清水室,清水室连接排水管,第三、第五加药管线均连接第一反应室,第四加药管线连接第二反应室。以此,使得强化絮凝分离装置内部结构紧凑,废液处理效率高,可对被输送入其内部的废液进行浮油收集、化学氧化、加药澄清、絮凝、斜板沉降及再次浮油收集工艺。
9.作为本技术方案的另一种实施,该废液来水管线、废液进水管及排水管上均设置有取样口,并且于清水室连接有回流管,回流管通过溶气泵与接触室的回流口连接。以此,可根据处理后废液检测的达标情况,对未达到排放标准的废液通过回流管与溶气泵重新回流至接触室重复进行强化絮凝分离处理,同时还能对废液进行溶气气浮处理。
10.作为本技术方案的另一种实施,该第一加药装置为混凝剂加药装置,该第二加药装置为絮凝剂加药装置、该第三加药装置为次氯酸钠加药装置。
11.作为本技术方案的另一种实施,该提升泵的泵出端至管道混合器的输入端的管线上连接有第一分支旁路,该管道混合器的输出端至加气絮凝装置的进水端的管线上连接有第二分支旁路,该加气絮凝装置的出水端至强化絮凝分离装置的进水端的管线上连接有第三分支旁路,该第一、第二及第三分支旁路上均设置有阀门并且第一、第二及第三分支旁路彼此连通。以此,可实现油气田复杂废液多功能预处理装置的流程超越,根据废液的成分及性质,通过第一、第二及第三分支旁路上阀门的控制而选择从管道混合器、加气絮凝装置或强化絮凝分离装置开始进行废液的处理;另外,流程超越还可便于对管道混合器、加气絮凝装置及相关管线装置的检修与维护。
12.作为本技术方案的另一种实施,该提升泵、管道混合器、加气絮凝装置、强化絮凝分离装置、第一加药装置、第二加药装置、第三加药装置及连接管线等为橇装化设置。以此,便于油气田复杂废液多功能预处理装置的运输,从而适用于边远区块零散废液的就地处理。
13.为了解决上述技术问题,本技术方案还提供了一种油气田复杂废液的预处理方法,方法步骤包括:加药混合步骤:废液由第一加药装置加入混凝剂后进入管道混合器进行混合;加药预絮凝步骤:经混合后的废液由管道混合器输出并由第二加药装置加入絮凝剂;加气絮凝步骤:废液进入加气絮凝装置,于微泡发生与空化氧化区由气泡发生器向废液中注入空气以进行微泡破胶及曝气氧化反应;之后废液由下至上依序进入旋流絮凝反应区及涡流絮凝反应区进行絮凝反应,且絮凝产生的沉淀物经由泥渣排管排出;之后废液进入沉降区进行沉降,经沉降后的废液由加气絮凝装置的处理液排管输出;强化絮凝分离步骤:废液进入强化絮凝分离装置,于接触区利用收油槽对废液上层的浮油进行第一次浮油收集;之后废液经溢流进入分离区进行沉降且沉降产生的沉淀物经由排泥管排出;之后废液经流道依序进入第一混合区、第一反应区及第二混合区,第一及第二混合区均设置有搅拌装置以对废液进行搅拌,于第一反应区由第三加药装置向废液中加入次氯酸钠进行化学氧化反应,同时由第一加药装置向废液中加入混凝剂进行澄清反应;之后废液经流道由第二混合区进入第二反应区,并由第二加药装置向废液中加入絮凝剂进行絮凝反应且絮凝产生的沉淀物经由排泥管排出;之后废液经流道进入斜板沉降区进行斜板沉降,同时于斜板沉降区利用收油槽对废液上层的浮油进行第二次浮油收集;之后废液经溢流进入清水区;预处理废液排出步骤:清水区连接有排水管,以将预处理后的废液排出。
14.据此,该预处理方法可实现多级加药混凝、微泡破胶、絮凝、多级氧化、沉降及加药澄清的工艺,不仅使废液处理流程得到优化,而且确保废液处理的高效性,并可以满足不同性质废液的处置需求。
15.作为本技术方案的另一种实施,于预处理废液排出步骤前还增设有回流强化絮凝分离步骤:于清水区的排水管处设置有取样口,当从取样口检测的废液未达标时,将清水区的废液通过回流管及溶气泵回流至接触区进行溶气气浮反应并且再次执行强化絮凝分离步骤,直到取样口检测的废液达标时再执行预处理废液排出步骤。以此,通过溶气气浮反应可提高废液处理的效率,而重复执行强化絮凝分离步骤可确保废液在排放时达到排放标准。
16.作为本技术方案的另一种实施,于加药混合步骤前还增设有废液处理流程超越步骤:于废液来水管线和加气絮凝装置的处理液排管上均设置有取样口,并且于废液来水管线、加气絮凝装置的进水端的管线和处理液排管上分别连接有具有阀门的分支旁路管线,且各分支旁路管线彼此连通,通过从各取样口检测的废液的达标情况,以对各分支旁路管线上的阀门进行关闭或开启操作,从而选择从加药混合步骤、加气絮凝步骤或强化絮凝分离步骤中任一个步骤开始执行油气田复杂废液的预处理操作。以此,可视废液的成分及性质,选择处理步骤的起点,从而简化处理流程并节约能耗;另外,流程超越还可便于对管道混合器或加气絮凝装置及相关管线装置的检修与维护。
附图说明
17.图1为本发明油气田复杂废液多功能预处理装置一实施例的示意图;
图2为本发明中加气絮凝装置的侧面剖视图;图3为本发明中强化絮凝分离装置的侧面剖视图;图4为本发明中强化絮凝分离装置的俯视图;图5为本发明油气田复杂废液多功能预处理装置另一实施例的示意图。
18.附图中的符号说明:1 废液来水管线;2 提升泵;3 管道混合器;4 加气絮凝装置;41 外筒体;411 排气孔;412 通口;413 处理液出口;414 处理液排管;415 支撑杆;42 内筒体;421 圆筒段;4211 敞口;4212 导流器;422 收腰段;423 漏斗段;424 通孔;43 气泡液进管;431 泥渣排管;44 进水环管;441 进水孔;45 气泡发生器管路;451 气泡发生器;5 强化絮凝分离装置;51废液进水管;52 接触室;521 隔板;522 第一收油槽;523 油渣室;53 分隔室;531 第一污泥斗;532 排泥管;54 第一混合室;541 搅拌装置;55 第一反应室;56 第二混合室;561 搅拌装置;57 第二反应室;571 第二污泥斗;572 排泥管;58 斜板沉降室;581 第二收油槽;59 清水室;591 回流管;592 溶气泵;6 第一加药装置;61 第一加药管线;62 第三加药管线;7 第二加药装置;71 第二加药管线;72 第四加药管线;8 第三加药装置;81 第五加药管线;9 阀门;10 排水管;11 取样口;12 第一分支旁路;13 第二分支旁路;14 第三分支旁路。
具体实施方式
19.有关本发明的详细说明及技术内容,配合图式说明如下,然而所附图式仅提供参考与说明用,并非用来对本发明加以限制。
20.如图1所示,为本发明油气田复杂废液多功能预处理装置一实施例的示意图。该油气田复杂废液多功能预处理装置包括:提升泵2、管道混合器3、加气絮凝装置4、强化絮凝分离装置5、第一加药装置6、第二加药装置7及第三加药装置8。其中,废液来水管线1连接提升泵2的泵入端,提升泵2的泵出端通过管线连接管道混合器3的输入端,管道混合器3的输出端通过管线连接加气絮凝装置4的进水端,加气絮凝装置4的出水端通过管线连接强化絮凝分离装置5的进水端,强化絮凝分离装置5的出水端连接排水管10。第一加药装置6通过第一加药管线61连接管道混合器3的输入端的管线且于第一加药管线61上设置有阀门9,第二加药装置7通过第二加药管线71连接管道混合器3的输出端的管线且于第二加药管线71上设置有阀门9,第一加药装置6还通过第三加药管线62连通强化絮凝分离装置5的第一反应室55(结合图4所示)且于第三加药管线62上设置有阀门9,第二加药装置7还通过第四加药管线72连通强化絮凝分离装置5的第二反应室57(结合图4所示)且于第四加药管线72上设置有阀门9,第三加药装置8通过第五加药管线81连通强化絮凝分离装置5的第一反应室55且于第五加药管线81上设置有阀门9。该加气絮凝装置4可将被输送入其内部的废液进行微泡破胶、曝气氧化、絮凝及沉降处理后通过管线输送入强化絮凝分离装置5内部。强化絮凝分离装置5可将被输送入其内部的废液进行溶气气浮、浮油收集、化学氧化、加药澄清、絮凝、斜板沉降及再次浮油收集后通过排水管10排出。
21.具体而言,如图2所示,于本实施例中,该加气絮凝装置4包括:外筒体41、处理液排管414、内筒体42、气泡液进管43、进水环管44、至少一条气泡发生器管路45及泥渣排管431。其中,外筒体41呈胶囊状且竖直向设置,外筒体41的上端部开设有与外界相通的排气孔
411,外筒体41的下端部的中心位置开设有通口412以及围绕通口412开设有至少一个处理液出口413,该至少一个处理液出口413连接处理液排管414。内筒体42与外筒体41共轴线且由数根支撑杆415固定连接于内筒体42外侧面及外筒体41内侧面之间而使内筒体42被设置于外筒体41内部,且内筒体42外侧面与外筒体41内侧面之间间隔有间距,以此形成沉降空间。该内筒体42由上至下包括圆筒段421、收腰段422及漏斗段423,其中,圆筒段421的上端部为开放式的敞口4211,圆筒段421的内侧面间隔环设有双层的导流结构,导流结构是由数个均匀间隔设置于圆筒段421内侧面上的横向截面呈等腰三角形的导流器4212构成,且导流器4212横向截面的两条等腰边呈内凹圆弧状,并且上层导流结构的导流器4212是与下层导流结构的导流器4212相错开的;收腰段422结合于圆筒段421的下端部,且收腰段422中间部位的直径小于其上、下端部的直径;漏斗段423结合于收腰段422的下端部,且漏斗段423的直径由上至下渐小,漏斗段423的下端部对应通口412位置开设有通孔424,气泡液进管43穿设密封结合于通口412,且气泡液进管43的上端部与通孔424连通,气泡液进管43的下端部位于通口412外侧且为封闭状。进水环管44环设固定于外筒体41外侧面的上部,且进水环管44上开设有进水孔441以通过管线连接管道混合器的输出端,进水环管44上还开设有至少一个废液输出口(图未标示),气泡液进管43上对应至少一个废液输出口而开设有至少一个废液输入口(图未标示),且于至少一个废液输出口至至少一个废液输入口间接设至少一条气泡发生器管路45,并于气泡发生器管路45上设置有气泡发生器451。气泡液进管43的底部还开设有排渣口(图未标示),排渣口连接泥渣排管431。通过上述结构,废液经进水孔441进入进水环管44内,并经至少一条气泡发生器管路45注入至内筒体42下部的漏斗段423,在此过程中,气泡发生器管路45中的气泡发生器451将外界空气引入至管路中进行微泡造泡,以对废液微泡破胶及曝气氧化,进入漏斗段423的废液在液流流向的作用下进行旋流絮凝,之后经收腰段422对液流稳定后,废液进入圆筒段421并经其内部的双层导流结构而进行涡流絮凝,旋流和涡流絮凝所产生的沉淀物通过气泡液进管43底部的排渣口排出,絮凝后的废液经圆筒段421上部的敞口4211溢流至内、外筒体42、41间形成的沉降空间进行沉淀,同时废液中释放出的气体通过排气孔411排出,经沉降后的废液通过处理液出口413经处理液排管414输入至下一个处理装置。以此,使得加气絮凝装置内部结构紧凑,废液处理效率高,可对被输送入其内部的废液进行微泡破胶、曝气氧化、旋流和涡流絮凝及沉降工艺。
22.如图1、3及4所示,于本实施例中,该强化絮凝分离装置5由其进水端至其出水端方向包括:接触室52、两个油渣室523、分隔室53、第一混合室54、第一反应室55、第二混合室56、第二反应室57、斜板沉降室58及清水室59。其中,接触室52连接废液进水管51,两个油渣室523分别设置于接触室52的两侧,分离室53设置于接触室52相对于废液进水管51的另一侧,且分离室53与接触室52和两个油渣室523之间是以上端部朝向分离室53倾斜设置的隔板521所区隔的,于接触室52上方且与隔板521上端部高度相同的位置处装设有第一收油槽522,第一收油槽522的两端分别与两个油渣室523的上部相通。废液由接触室52经溢流进入分离室53,分离室53的底部形成有第一污泥斗531,第一污泥斗531装设有排泥管532。第一混合室54、第一反应室55及第二混合室56是并排设置于分离室53相对于隔板521的另一侧,且分离室53与第一混合室54通过流道(图未标示)连通,第一混合室54与第一反应室55通过流道连通,第一反应室55与第二混合室56通过流道连通,并且于第一混合室54及第二混合室56均装设有搅拌装置541、561。第二反应室57设置于并排设置的第一混合室54、第一反应
室55及第二混合室56的另一侧,且第二反应室57与第二混合室56通过流道连通,第二反应室57的底部形成有第二污泥斗571,第二污泥斗571装设有排泥管572。斜板沉降室58设置于第二反应室57的另一侧,且第二反应室57与斜板沉降室58通过流道连通,斜板沉降室58上方装设有第二收油槽581。清水室59设置于斜板沉降室58的另一侧,废液由斜板沉降室58经溢流进入清水室59,清水室59连接排水管10。第三、第五加药管线62、81均连接第一反应室55,第四加药管线72连接第二反应室57。通过上述结构,废液经废液进水管51进入至接触室52并通过溢流流至分离室53,在此溢流过程中,废液上层的浮油通过第一收油槽522被收集并被排入至接触室52两侧的油渣室523,废液于分离室53进行沉降,沉降后的沉淀物淤积于第一污泥斗531中并通过静压作用由排泥管532排出,之后废液经流道依序进入第一混合室54、第一反应室55及第二混合室56,于第一、第二混合室54、56废液可由搅拌装置541、561充分搅拌以提升相关反应的效果,而于第一反应室55则由第一和第三加药装置6、8对废液中投加药物以进行化学氧化及澄清反应,废液经投药搅拌后经流道进入第二反应室57并由第二加药装置7向废液中投加药物以进行絮凝处理,絮凝所产生的沉淀物淤积于第二污泥斗571中并通过静压作用由排泥管572排出,与此同时废液也进入斜板沉降室58进行沉降,沉降后的沉淀物同样也会淤积于第二污泥斗571中由排泥管572排出,此后废液经溢流由斜板沉降室58进入至清水室59并通过排水管10排出。以此,使得强化絮凝分离装置内部结构紧凑,废液处理效率高,可对被输送入其内部的废液进行浮油收集、化学氧化、加药澄清、絮凝、斜板沉降及再次浮油收集工艺。
23.另外,结合图1所示,于该废液来水管线1、废液进水管51及排水管10上可均设置有取样口11,以便对各处理阶段的废液进行成分及性质检测。并且还可于清水室59连接有回流管591,回流管591通过溶气泵592与接触室52的回流口(图未标示)连接,以此可根据处理后废液检测的达标情况,对未达到排放标准的废液通过回流管与溶气泵重新回流至接触室重复进行强化絮凝分离处理,同时还能对废液进行溶气气浮处理。
24.于本实施例中,该第一加药装置可为混凝剂加药装置,该第二加药装置可为絮凝剂加药装置、该第三加药装置可为次氯酸钠加药装置。
25.如图5所示,于本发明油气田复杂废液多功能预处理装置的另一实施例中,可于提升泵2的泵出端至管道混合器3的输入端的管线上连接有第一分支旁路12,于管道混合器3的输出端至加气絮凝装置4的进水端的管线上连接有第二分支旁路13,于加气絮凝装置4的出水端至强化絮凝分离装置5的进水端的管线上连接有第三分支旁路14,该第一、第二及第三分支旁路12、13、14上均设置有阀门9并且第一、第二及第三分支旁路12、13、14彼此连通。以此可实现油气田复杂废液多功能预处理装置的流程超越,根据废液的成分及性质,通过第一、第二及第三分支旁路上阀门的控制而选择从管道混合器、加气絮凝装置或强化絮凝分离装置开始进行废液的处理;另外,流程超越还可便于对管道混合器、加气絮凝装置及相关管线装置的检修与维护。
26.本发明的油气田复杂废液多功能预处理装置中的提升泵、管道混合器、加气絮凝装置、强化絮凝分离装置、第一加药装置、第二加药装置、第三加药装置及连接管线等装置可为橇装化设置(图未标示),以此便于装置的运输,从而适用于边远区块零散废液的就地处理。
27.结合上述预处理装置,本发明还提供了一种油气田复杂废液的预处理方法,该预
处理方法的步骤包括:加药混合步骤:废液由第一加药装置加入混凝剂后进入管道混合器进行混合;加药预絮凝步骤:经混合后的废液由管道混合器输出并由第二加药装置加入絮凝剂;加气絮凝步骤:废液进入加气絮凝装置,于微泡发生与空化氧化区由气泡发生器向废液中注入空气以进行微泡破胶及曝气氧化反应;之后废液由下至上依序进入旋流絮凝反应区及涡流絮凝反应区进行絮凝反应,且絮凝产生的沉淀物经由泥渣排管排出;之后废液进入沉降区进行沉降,经沉降后的废液由加气絮凝装置的处理液排管输出;强化絮凝分离步骤:废液进入强化絮凝分离装置,于接触区利用收油槽对废液上层的浮油进行第一次浮油收集;之后废液经溢流进入分离区进行沉降且沉降产生的沉淀物经由排泥管排出;之后废液经流道依序进入第一混合区、第一反应区及第二混合区,第一及第二混合区均设置有搅拌装置以对废液进行搅拌,于第一反应区由第三加药装置向废液中加入次氯酸钠进行化学氧化反应,同时由第一加药装置向废液中加入混凝剂进行澄清反应;之后废液经流道由第二混合区进入第二反应区,并由第二加药装置向废液中加入絮凝剂进行絮凝反应且絮凝产生的沉淀物经由排泥管排出;之后废液经流道进入斜板沉降区进行斜板沉降,同时于斜板沉降区利用收油槽对废液上层的浮油进行第二次浮油收集;之后废液经溢流进入清水区;预处理废液排出步骤:清水区连接有排水管,以将预处理后的废液排出。
28.据此,该预处理方法可实现多级加药混凝、微泡破胶、絮凝、多级氧化、沉降及加药澄清的工艺,不仅使废液处理流程得到优化,而且确保废液处理的高效性,并可以满足不同性质废液的处置需求。
29.上述预处理方法中,还可于预处理废液排出步骤前增设回流强化絮凝分离步骤:于清水区的排水管处设置有取样口,当从取样口检测的废液未达标时,将清水区的废液通过回流管及溶气泵回流至接触区进行溶气气浮反应并且再次执行强化絮凝分离步骤,直到取样口检测的废液达标时再执行预处理废液排出步骤。以此,通过溶气气浮反应可提高废液处理的效率,而重复执行强化絮凝分离步骤可确保废液在排放时达到排放标准。
30.上述预处理方法中,还可于加药混合步骤前增设废液处理流程超越步骤:于废液来水管线和加气絮凝装置的处理液排管上均设置有取样口,并且于废液来水管线、加气絮凝装置的进水端的管线和处理液排管上分别连接有具有阀门的分支旁路管线,且各分支旁路管线彼此连通,通过从各取样口检测的废液的达标情况,以对各分支旁路管线上的阀门进行关闭或开启操作,从而选择从加药混合步骤、加气絮凝步骤或强化絮凝分离步骤中任一个步骤开始执行油气田复杂废液的预处理操作。以此,可视废液的成分及性质,选择处理步骤的起点,从而简化处理流程并节约能耗;另外,流程超越还可便于对管道混合器或加气絮凝装置及相关管线装置的检修与维护。
31.本发明通过将加气絮凝装置与强化絮凝分离装置的串联应用,可对预处理装置的整体结构进行优化,从而减小预处理装置的整体规模,并能够确保废液处理工艺的高效运行;另外,通过控制各条加药管线上的阀门,可使预处理装置实现多级加药混凝、多级氧化及加药澄清的流程工艺,以满足不同性质废液的处置需要。
32.以上仅为本发明的较佳实施例,并非用以限定本发明的专利范围,其他运用本发
明的专利构思所做的等效变化,均应属于本发明的专利保护范围。
再多了解一些
本文用于企业家、创业者技术爱好者查询,结果仅供参考。