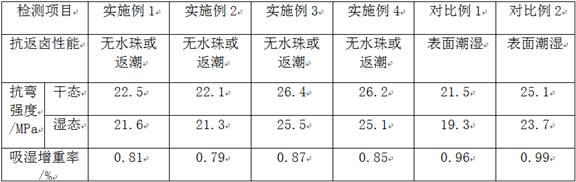
1.本发明涉及建筑装饰技术领域,具体地涉及一种自修复玻镁板的制备方法。
背景技术:
2.玻镁板是一种以氧化镁和氯化镁为主要材料制造的建筑板材,可用作墙板、吊顶板、防火板、防水板、包装箱等,可替代木质胶合板做墙裙、门窗、板门板、家具等,也可根据需要表面涂调和漆、清水漆,并可加工成各种类型的板面,还可用于地下室、矿井等潮湿环境的工程,和多种保温材料复合使用,制成复合保温板材。
3.玻镁板在应用过程中常常会遇到吸潮返卤的问题,出现吸潮返卤现象后,玻镁板表面会变得潮湿,严重情况下玻镁板还会变形、开裂,导致玻镁板质量出现严重缺陷。造成返卤现象的主要原因通常是玻镁板中游离的氯离子含量较高,由于玻镁板微观结构上存在大量孔隙,水蒸气被吸收至孔隙内部后,在高湿高温的环境当中氯离子很容易从晶体中发生位移,通过制品内部的毛细孔道迁移出来,不断聚集,这些盐类物质有吸潮性,不断吸附空气中的水份,导致制品表面潮湿。一些厂家利用硫酸镁来代替氯化镁进行玻镁板生产,以改善返卤问题,但该方法会导致生产成本明显提高,降低市场竞争力。
4.为了控制玻镁板的成本以及提高玻镁板的性能,现有技术中多采用抗返卤剂来解决氯化镁玻镁板的返卤问题。目前市面上的抗返卤剂基本是通过在体系中形成膜或胶体来堵断玻镁板中的游离氯离子通过毛细通道迁移至玻镁板表面来实现抗返卤效果。例如申请号为cn201810097575.8的专利文件提供了一种抗返卤氯氧镁水泥及其制备方法,该方法利用表面活性剂修饰的超薄类水滑石纳米片作为抗返卤剂, ldh纳米片具有超薄结构,分散后具有较大的比表面积,能够有效捕捉水泥材料中游离的氯离子,形成氯离子插层的ldh,避免氯离子迁移到水泥表面造成返卤。上述方案在一定程度上可以改善返卤问题,但玻镁板不可避免地仍会残留有未被封闭的毛细通道,这些毛细通道会导致玻镁板的内部形成侵蚀,降低玻镁板的使用寿命。
技术实现要素:
5.为了解决上述问题,本发明提供了一种自修复玻镁板的制备方法,以改善现有玻镁板容易出现返卤现象的问题,实现延长使用寿命、增加结构强度的目的。
6.为了实现上述目的,本发明采用了以下技术方案:一种自修复玻镁板的制备方法,包括以下步骤:s1、取硅藻土载体置于带有真空泵的容器中,再向容器加入巴氏芽孢杆菌菌液,对容器进行抽真空处理使巴氏芽孢杆菌吸附于硅藻土载体中,再将吸附有巴氏芽孢杆菌的硅藻土置于烘箱中烘干处理,得到载菌硅藻土;s2、将包括载菌硅藻土、微生物矿化底物、氯化镁、氧化镁和无机矿物填料在内的制备原料搅拌混合,得到第一混合料;所述的微生物矿化底物包含乳酸钙;s3、取通过步骤s2中方法制得的第一混合料,向其中加入聚苯颗粒并搅拌混合,得
到第二混合料;s4、取通过步骤s2中方法制得的第一混合料,加水搅拌至胶质状态,得到浆料;s5、向模具板上铺涂浆料并辊压形成底料层,再在底料层表面铺涂第二混合料并辊压形成轻质芯层,最后在轻质芯层表面再次铺涂浆料并辊压形成装饰面层,得到具有三层结构的雏形板;s6、雏形板经压实、养护后得到自修复玻镁板。
7.巴氏芽孢杆菌是一种好氧微生物,当接触水分和空气时,能够摄入乳酸钙并且将乳酸钙转化为碳酸钙沉淀,同时巴氏芽孢杆菌生命活动过程中产生的二氧化碳也会使体系中的钙离子转化为碳酸钙沉淀。当玻镁板成型后,其微观结构上具有大量的毛细通道,这些毛细通道会吸收外界的水蒸气,若不进行抗返卤处理,则生产玻镁板时氯化镁带来的游离氯离子会因为水蒸气产生的潮湿环境通过毛细通道逐渐迁移至玻镁板表面,在玻镁板表面形成盐结晶,这些盐结晶通常具有潮吸特性,进一步导致玻镁板表面长期处于潮湿状态,最终使玻镁板强度下降,使用寿命更短。而本发明则在玻镁板的制备原料中添加有巴氏芽孢杆菌,当水蒸气和空气通过毛细通道进入玻镁板内部时,在潮湿环境下休眠的巴氏芽孢杆菌被激活,巴氏芽孢杆菌通过生命活动逐渐产生碳酸钙沉淀,最终将毛细通道堵塞,阻止水蒸气的进入以及氯离子的向外迁移。现有技术中一般采用抗返卤剂来阻止水蒸气和氯离子通过毛细通道,缺点在于抗返卤剂并不能保证对每一处毛细通道均形成阻断效果,只能减少毛细通道的生成或者减少游离氯离子向表面迁移的概率,玻镁板在成型过程中不可避免地仍会形成部分未被阻断的毛细通道。而本发明利用了微生物的自身特性,当微生物因为毛细通道吸收的水蒸气而激活后,便会开始进行生命活动生成碳酸钙沉淀将该毛细通道阻塞,因此当微生物在玻镁板中基本均匀分布时,大多毛细孔道均会因为微生物的矿化作用被碳酸钙堵塞。从另一角度,即使少量毛细孔道未分布有微生物,当毛细孔道内部因为水蒸气变得湿润而产生内部侵蚀时,当侵蚀部分接触到微生物后,微生物会产生碳酸钙沉淀而阻碍侵蚀的进一步发生,保证玻镁板内部结构的稳定性。
8.此外,玻镁板在长时间使用后以及面临强震动、强风等环境时,可能会出现微裂纹等结构性损伤,此外玻镁板养护成型过程中也可能因为各部分硬化不均匀而产生内应力并导致微裂纹的产生,当微裂纹出现后水蒸气会通过裂纹进入至玻镁板内部,此时抗卤剂无法阻止水蒸气与游离氯离子接触,裂缝内部会形成潮湿环境,从而进一步加剧结构损伤,导致玻镁板强度大幅下降。本发明提供的玻镁板可以利用微生物的生命活动产生碳酸钙沉淀将这些微裂纹修补,降低玻镁板的结构损伤,延长玻镁板的使用寿命以及提高玻镁板的结构强度。
9.综上,本发明的“自修复”包含两方面,其一是利用微生物的矿化作用产生碳酸钙沉淀来修复玻镁板成型过程中微观角度产生的大量毛细孔道,阻止水蒸气的进入和氯离子的向外迁移,避免返卤现象的出现,同时当内部侵蚀出现后微生物产生的碳酸钙沉淀可以阻碍侵蚀的进一步发生;其二是当玻镁板宏观角度因为结构损伤产生微裂纹时,微生物可以产生碳酸钙沉淀来填补这些微裂纹,避免裂纹的进一步扩大,保证玻镁板的结构强度。
10.进一步地,所述的微生物矿化底物还包含硝酸钙和尿素。
11.进一步地,所述的微生物矿化底物中各组分的配比为:尿素3~6份、硝酸钙30~60份、乳酸钙100~150份。
12.进一步地,步骤s2中所述的制备原料还包括hpmc、减水剂、粉煤灰和聚丙烯纤维。
13.进一步地,步骤s2中所述的无机矿物填料为膨胀珍珠岩。
14.进一步地,步骤s2中所述的第一混合料中各组分的配比为:载菌硅藻土100-300份、微生物矿化底物140~200份、氯化镁75~150份、氧化镁150~300份、无机矿物填料20~50份。
15.进一步地,步骤s3中所述的第一混合料中各组分的配比为:载菌硅藻土100-300份、微生物矿化底物140~200份、氯化镁75~150份、氧化镁150~300份、无机矿物填料20~50份、聚苯颗粒20~60份。
16.进一步地,步骤s1中,抽真空处理过程中温度控制为-4~0℃,真空负压大小控制为0.55~0.56mpa。
17.进一步地,步骤s1中,烘干处理过程温度控制为37~43℃。
18.进一步地,步骤s5中,所述雏形板的装饰面层表面还压贴有装饰膜层。
19.本发明还提供了另一种自修复玻镁板的制备方法,包括以下步骤:s1、取硅藻土载体置于带有真空泵的容器中,再向容器加入巴氏芽孢杆菌菌液,对容器进行抽真空使巴氏芽孢杆菌吸附于硅藻土载体中,再将吸附有巴氏芽孢杆菌的硅藻土置于烘箱中烘干处理,得到载菌硅藻土;s2、将包括载菌硅藻土、微生物矿化底物、氯化镁、氧化镁和无机矿物填料在内的制备原料搅拌混合,得到第一混合料;所述的微生物矿化底物包含乳酸钙;s3、取通过步骤s2中方法制得的第一混合料,向其中加入聚苯颗粒并搅拌混合,得到第二混合料;s4、取通过步骤s2中方法制得的第一混合料,加水搅拌至胶质状态,得到浆料;s5、向模具板上铺涂浆料并辊压形成底料层,在底料层表面铺设玻纤布形成第一加强层,在第一加强层表面铺涂第二混合料并辊压形成轻质芯层,在轻质芯层表面铺设玻纤布形成第二加强层,最后在第二加强层表面再次铺涂浆料形成装饰面层,得到具有五层结构的雏形板;s6、雏形板经压实、养护后得到自修复玻镁板。
20.综上所述,应用本发明方案可以取得以下有益效果:1、本发明通过向玻镁板生产原料中添加载菌硅藻土,使生产得到的玻镁板在强风、强震等使用环境下容易出现的裂纹能够自行修复,达到提高玻镁板的结构强度、延长玻镁板的使用寿命的目的。
21.2、本发明过向玻镁板生产原料中添加载菌硅藻土,使玻镁板在成型养护过程中因为各部分的硬化速率不完全一致可能会导致产生微裂缝,此时菌体可以在微裂缝处生成碳酸钙沉淀实现填补效果,提高玻镁板结构强度。
22.3、玻镁板在成型过程中通常会形成大量毛细孔道,水蒸气进入毛细孔道后容易造成返卤现象,本发明添加的载菌硅藻土可以通过生成碳酸钙沉淀来阻断毛细通道,避免水蒸气进入玻镁板内部,从而减少返卤现象的发生。
具体实施方式
23.下面结合实施例对本发明作进一步说明。
24.实施例1一种自修复玻镁板的制备方法,包括以下步骤:s1、载菌硅藻土的试制过程为:巴氏芽孢杆菌菌液低温-4℃~0℃下放置12小时后,取再生骨料载体置于负压真空泵,再加入巴氏芽孢杆菌菌液,启动真空泵使再生骨料载体对菌液进行吸附,真空负压为0.6mpa,吸附时间为30min,然后转移至烘箱内恒温40℃烘干24小时,即得到载菌硅藻土;s2、按顺序向混料机中添加粉煤灰40份、乳酸钙125份、载菌硅藻土200份、聚丙烯纤维2份、hpmc2份、减水剂4份、膨胀珍珠岩30份、尿素3份、硝酸钙40份、氯化镁110份、氧化镁220份,混料机搅拌速度1000转/min,搅拌10分钟,得到第一混合料,待用;s3、取步骤s2中制得的第一混合料380份投入至搅拌机中,向其中加入聚苯颗粒25份,搅拌速度300转/min,搅拌5分钟,得到第二混合料,待用;s4、取经步骤s3后剩余第一混合料,向其中加入水260份,搅拌至胶质状态,得到浆料;s5、在涂有脱模剂的模具板上铺涂一半的步骤s4中制得的浆料,并进行辊压处理形成底料层;在底料层表面铺涂第二混合料,并进行辊压处理形成轻质芯层;在轻质芯层表面铺涂另一半的浆料,并进行辊压处理形成装饰面层,从而得到具有三层结构的雏形板;s6、将雏形板在温度20~30℃、湿度50%~70%的环境下放置24h后进行脱模处理,随后将雏形板送至养护房在常温下进行14天养护处理,即得到自修复玻镁板。
25.实施例2一种自修复玻镁板的制备方法,包括以下步骤:s1、载菌硅藻土的试制过程为:巴氏芽孢杆菌菌液低温-4℃~0℃下放置12小时后,取再生骨料载体置于负压真空泵,再加入巴氏芽孢杆菌菌液,启动真空泵使再生骨料载体对菌液进行吸附,真空负压为0.6mpa,吸附时间为30min,然后转移至烘箱内恒温40℃烘干24小时,即得到载菌硅藻土;s2、按顺序向混料机中添加粉煤灰45份、乳酸钙130份、载菌硅藻土220份、聚丙烯纤维1份、hpmc 1份、减水剂3份、膨胀珍珠岩25份、尿素3份、硝酸钙35份、氯化镁120份、氧化镁240份,混料机搅拌速度1000转/min,搅拌10分钟,得到第一混合料,待用;s3、取步骤s2中制得的第一混合料400份投入至搅拌机中,向其中加入聚苯颗粒20份,搅拌速度300转/min,搅拌5分钟,得到第二混合料,待用;s4、取经步骤s3后剩余第一混合料,向其中加入水270份,搅拌至胶质状态,得到浆料;s5、在涂有脱模剂的模具板上铺涂一半的步骤s4中制得的浆料,并进行辊压处理形成底料层;在底料层表面铺涂第二混合料,并进行辊压处理形成轻质芯层;在轻质芯层表面铺涂另一半的浆料,并进行辊压处理形成装饰面层,从而得到具有三层结构的雏形板;s6、将雏形板在温度20~30℃、湿度50%~70%的环境下放置24h后进行脱模处理,随后将雏形板送至养护房在常温下进行14天养护处理,即得到自修复玻镁板。
26.实施例3一种自修复玻镁板的制备方法,包括以下步骤:s1、载菌硅藻土的试制过程为:巴氏芽孢杆菌菌液低温-4℃~0℃下放置12小时
后,取再生骨料载体置于负压真空泵,再加入巴氏芽孢杆菌菌液,启动真空泵使再生骨料载体对菌液进行吸附,真空负压为0.6mpa,吸附时间为30min,然后转移至烘箱内恒温40℃烘干24小时,即得到载菌硅藻土;s2、按顺序向混料机中添加粉煤灰40份、乳酸钙125份、载菌硅藻土200份、聚丙烯纤维2份、hpmc2份、减水剂4份、膨胀珍珠岩30份、尿素3份、硝酸钙40份、氯化镁110份、氧化镁220份,混料机搅拌速度1000转/min,搅拌10分钟,得到第一混合料,待用;s3、取步骤s2中制得的第一混合料380份投入至搅拌机中,向其中加入聚苯颗粒25份,搅拌速度300转/min,搅拌5分钟,得到第二混合料,待用;s4、取经步骤s3后剩余第一混合料,向其中加入水260份,搅拌至胶质状态,得到浆料;s5、在涂有脱模剂的模具板上铺涂一半的步骤s4中制得的浆料,并进行辊压处理形成底料层;通过第一放卷设备在底料层表面覆盖一层玻纤布形成第一加强层,并辊压处理使底料层和第一加强层复合;在第一加强层表面铺涂第二混合料,并进行辊压处理形成轻质芯层;通过第二放卷设备在轻质芯层表面覆盖一层玻纤布形成第二加强层,并辊压处理;在第二加强层表面铺涂另一半的浆料,并进行辊压处理形成装饰面层,从而得到具有五层结构的雏形板;s6、将雏形板在温度20~30℃、湿度50%~70%的环境下放置24h后进行脱模处理,随后将雏形板送至养护房在常温下进行14天养护处理,即得到自修复玻镁板。
27.实施例4一种自修复玻镁板的制备方法,包括以下步骤:s1、载菌硅藻土的试制过程为:巴氏芽孢杆菌菌液低温-4℃~0℃下放置12小时后,取再生骨料载体置于负压真空泵,再加入巴氏芽孢杆菌菌液,启动真空泵使再生骨料载体对菌液进行吸附,真空负压为0.6mpa,吸附时间为30min,然后转移至烘箱内恒温40℃烘干24小时,即得到载菌硅藻土。
28.s2、按顺序向混料机中添加粉煤灰45份、乳酸钙130份、载菌硅藻土220份、聚丙烯纤维1份、hpmc 1份、减水剂3份、膨胀珍珠岩25份、尿素3份、硝酸钙35份、氯化镁120份、氧化镁240份,混料机搅拌速度1000转/min,搅拌10分钟,得到第一混合料,待用;s3、取步骤s2中制得的第一混合料400份投入至搅拌机中,向其中加入聚苯颗粒20份,搅拌速度300转/min,搅拌5分钟,得到第二混合料,待用;s4、取经步骤s3后剩余第一混合料,向其中加入水270份,搅拌至胶质状态,得到浆料;s5、在涂有脱模剂的模具板上铺涂一半的步骤s4中制得的浆料,并进行辊压处理形成底料层;通过第一放卷设备在底料层表面覆盖一层玻纤布形成第一加强层,并辊压处理使底料层和第一加强层复合;在第一加强层表面铺涂第二混合料,并进行辊压处理形成轻质芯层;通过第二放卷设备在轻质芯层表面覆盖一层玻纤布形成第二加强层,并辊压处理;在第二加强层表面铺涂另一半的浆料,并进行辊压处理形成装饰面层,从而得到具有五层结构的雏形板;s6、将雏形板在温度20~30℃、湿度50%~70%的环境下放置24h后进行脱模处理,随后将雏形板送至养护房在常温下进行14天养护处理,即得到自修复玻镁板。
29.对比例1s1、按顺序向混料机中添加粉煤灰40份、乳酸钙125份、再生骨料200份、聚丙烯纤维2份、hpmc2份、减水剂4份、膨胀珍珠岩30份、尿素3份、硝酸钙40份、氯化镁110份、氧化镁220份,混料机搅拌速度1000转/min,搅拌10分钟,得到第一混合料,待用;s2、取步骤s4中制得的第一混合料380份投入至搅拌机中,向其中加入聚苯颗粒25份,搅拌速度300转/min,搅拌5分钟,得到第二混合料,待用;s3、取经步骤s5后剩余第一混合料,向其中加入水260份,搅拌至胶质状态,得到浆料;s4、在涂有脱模剂的模具板上铺涂一半的步骤s3中制得的浆料,并进行辊压处理形成底料层;在底料层表面铺涂第二混合料,并进行辊压处理形成轻质芯层;在轻质芯层表面铺涂另一半的浆料,并进行辊压处理形成装饰面层,从而得到具有三层结构的雏形板。
30.s5、将雏形板在温度20~30℃、湿度50%~70%的环境下放置24h后进行脱模处理,随后将雏形板送至养护房在常温下进行14天养护处理,即得到自修复玻镁板。
31.对比例2s1、按顺序向混料机中添加粉煤灰40份、乳酸钙125份、再生骨料200份、聚丙烯纤维2份、hpmc2份、减水剂4份、膨胀珍珠岩30份、尿素3份、硝酸钙40份、氯化镁110份、氧化镁220份,混料机搅拌速度1000转/min,搅拌10分钟,得到第一混合料,待用;s2、取步骤s4中制得的第一混合料380份投入至搅拌机中,向其中加入聚苯颗粒25份,搅拌速度300转/min,搅拌5分钟,得到第二混合料,待用;s3、取经步骤s5后剩余第一混合料,向其中加入水260份,搅拌至胶质状态,得到浆料;s4、在涂有脱模剂的模具板上铺涂一半的步骤s3中制得的浆料,并进行辊压处理形成底料层;通过第一放卷设备在底料层表面覆盖一层玻纤布形成第一加强层,并辊压处理使底料层和第一加强层复合;在第一加强层表面铺涂第二混合料,并进行辊压处理形成轻质芯层;通过第二放卷设备在轻质芯层表面覆盖一层玻纤布形成第二加强层,并辊压处理;在第二加强层表面铺涂另一半的浆料,并进行辊压处理形成装饰面层,从而得到具有五层结构的雏形板;s5、将雏形板在温度20~30℃、湿度50%~70%的环境下放置24h后进行脱模处理,随后将雏形板送至养护房在常温下进行14天养护处理,即得到自修复玻镁板。
32.将上述实施例1~4所得玻镁板与对比例1、2的玻镁板进行检测,具体检测如下:1、抗吸潮返卤性:按照jc688,在玻镁板上任意切下150mm
×
150mm试板3块,放入相对湿度为90%,温度为35℃的恒温恒湿箱中24h后,取出观察试板有无水珠或返潮;2、干、湿态抗弯强度:在玻镁板上任意切下尺寸250mm
×
250mm试板6块,养护14天后,取其中的3块在抗弯强度仪上测试抗弯强度,另3块试板浸水48h后测试湿态抗弯强;3、吸湿增重率:切取玻镁板尺寸为100mm
×
100mm的试板3块,将试板放入温度为20℃,相对湿度为97%的玻璃干燥器(底部盛水)中,通过称重,测试试板在玻璃干燥器中24h后的吸湿增重率。
33.结果如表1所示。
34.表1:
由上表可知,本发明实施例提供的玻镁板因为载菌硅藻土的添加,毛细孔道被活性菌体生产的碳酸钙封堵,使得玻镁板具有较好的抗吸潮返卤性,且毛细通道被碳酸钙封堵后也会使玻镁板的吸湿增重率相对较低,因此玻镁板在潮湿环境下具有更强的耐久性。此外,实施例中的玻镁板的抗弯强度也略高于对比例,因此玻镁板运输和使用过程中不易出现变形、开裂等问题,其原因可能是在养护成型过程中活性菌体能够用碳酸钙对玻镁板内部潜在在的微裂缝进行填充,提高局部结构强度。
35.最后所应说明的是,以上实施例仅用以说明本发明的技术方案而非限制,尽管参照本发明实施例进行了详细说明,本领域的普通技术人员应当理解,对本发明的技术方案进行修改或者等同替换,都不脱离本发明的技术方案的精神和范围,其均应涵盖本发明的权利要求保护范围中。
再多了解一些
本文用于企业家、创业者技术爱好者查询,结果仅供参考。