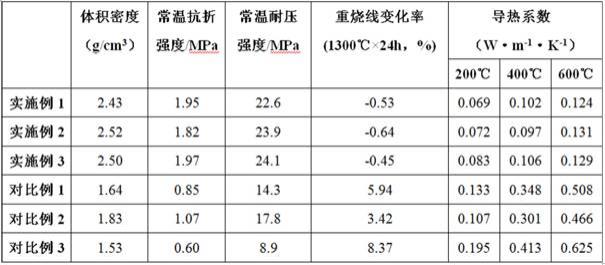
1.本发明涉及一种致密钙长石质耐火材料的制备方法,属于耐火材料领域。
背景技术:
2.钙长石具有高熔点(1550℃)、低介电常数、低热膨胀系数、低导热系数等特性,因此用作耐火材料不仅具有优异的耐高温和隔热性能,还具备很好的抗含碳还原气氛作用、抗热冲击性能、抗水蒸气腐蚀性能、体积稳定性和电绝缘性,能广泛应用于多种高温工业环境。由于钙长石与钠长石呈完全类质同象存在,纯净的钙长石很少富集成矿,因此工业上所采用的钙长石均为人工合成。通常,钙长石质耐火材料是由含有氧化钙、氧化硅和氧化铝的如球状粘土、石英、长石、方解石等各种天然原料的混合物,通过混合烧结而成。近年来,工业废弃物的再生利用成为热点,工业制造过程中产生的残留物作为耐火材料的替代原材料,如何再利用已成为一个重要问题。已有研究主要利用工业含钙废物,如石灰泥、方解石废物、蛋壳废物、粉煤灰、钢渣、高炉渣、再生纸加工残渣和石膏模废物等作为钙源制备钙长石质耐火材料。
3.然而,轻质多孔隔热耐火材料是近年钙长石质耐火材料的研发重点品种,多作为隔热层材料,钙长石质耐火材料的致密性和机械强度限制了其作为用耐火工作衬应用,无法充分发挥其低导热等特性。因此,为充分发掘钙长石质耐火材料在高温工业中的应用价值,支撑高温工业“双碳”行动,亟需研发能用于高温工业炉热面的高强度致密钙长石质耐火材料。
4.中国专利cn114195532a公开了一种气孔均匀的钙长石轻质耐火材料及其制备方法,通过调整不同原料的混合顺序,先加入煤矸石类粉料、叶腊石,再加入耐火黏土、碳酸钙,最后加入高铝水泥、促凝剂、发泡剂,可以有效调整料浆的状态,使料浆在浇注后的坯体中气泡分布更加均匀,进而有利降低产品的导热系数。该专利得到的耐火材料耐压强度低,导热系数过高,不适合高温工业领域的节能环保。
5.中国专利cn114195550a公开了一种闭孔结构的钙长石耐火材料及其制备方法,该专利中的轻质钙长石耐火材料,具有特定微观结构,且具有钙长石和莫来石复合晶相,并以钙长石相作为主晶相,晶相占比达到90%以上;具有闭孔结构,其孔径分布均匀,具有特定的孔径尺寸分布范围(孔径大小500~700微米,孔径分布均匀)。该专利得到的耐火材料,耐压强度低,抗折强度差,导热系数较高,不适合耐火工作衬应用要求。
6.以上可以看到,钙长石质耐火材料仍存在耐压强度低,抗折强度差,导热系数高等问题,难以在高温工业中得到普遍应用。
技术实现要素:
7.针对上述现有技术存在的不足,本发明提供一种致密钙长石质耐火材料的制备方法,实现以下发明目的:制备出体积密度高,耐压强度高,抗折强度高,导热系数低,重烧线变化率低的致密钙长石质耐火材料。
8.为实现上述发明目的,本发明采取以下技术方案:一种致密钙长石质耐火材料的制备方法,包括混合粉体制备、混合粉体预处理、制浆、造粒、压制成型、烧结。
9.以下是对上述技术方案的进一步改进:步骤1、混合粉体制备将糖厂工业滤饼渣粉、焦宝石粉、有机硅钙肥、硅铝酸钠粉末、铝酸钙粉末、硅酸钙粉末混合后,球磨成平均粒径10~25微米的混合粉末,得到混合粉体;所述糖厂工业滤饼渣粉、焦宝石粉、有机硅钙肥、硅铝酸钠粉末、铝酸钙粉末、硅酸钙粉末的质量比为30~50:40~70:30~45:1~5:2~6:2~9;所述糖厂工业滤饼渣粉,其平均粒径为10~15微米,cao含量为46~60wt%;所述焦宝石粉,其平均粒径为110~150微米,sio2含量为45~55wt%,al2o3含量为40~50wt%;所述有机硅钙肥,其平均粒径为500~1000微米,sio2含量为25~45wt%,cao含量为36~50wt%;所述硅铝酸钠粉末的平均粒径为20~60微米;所述铝酸钙粉末的平均粒径为15~55微米;所述硅酸钙粉末的平均粒径为25~65微米。
10.步骤2、混合粉体预处理将四(三乙醇胺)锆酸酯、2-丁氧基乙醇磷酸酯、硬脂酸、三聚氰胺搅拌溶解于乙酸乙酯中,控温50~70℃,搅拌速度1800~2600转/分下,将混合粉体缓慢加入其中,搅拌1~3小时后,过滤,滤出的固体粉末在70~90℃下烘干1~2小时,得到预处理的混合粉体;所述四(三乙醇胺)锆酸酯、2-丁氧基乙醇磷酸酯、硬脂酸、三聚氰胺、乙酸乙酯、混合粉体的质量比为1~1.5:0.5~1.3:2~4:3~7:90~120:30~50。
11.步骤3、制浆将磷酸硅、偏硅酸钠、十二烷基硫酸钠、去离子水混合成溶液,5500~8500转/分搅拌速度下,向溶液中缓慢加入预处理的混合粉体,加料完毕后,继续搅拌3~6小时后出料得到料浆;所述磷酸硅、偏硅酸钠、十二烷基硫酸钠、去离子水、预处理的混合粉体的质量比为0.5~1.5:8~15:0.5~1:100~150:35~50。
12.步骤4、造粒对料浆进行喷雾造粒,进口温度控制为110~140℃,出口温度控制为70~95℃,得到粒料;所述粒料的粒径为20~46微米。
13.步骤5、压制成型将粒料放入模具中,在25~50mpa下压制成型,得到生胚。
14.步骤6、烧结将生胚于80~140℃下干燥10~19小时后,以2~5℃/min速率升温至1200~1400℃,恒温煅烧2~5小时,然后冷却至室温得到致密钙长石质耐火材料。
15.与现有技术相比,本发明取得以下有益效果:
1、本发明制备出了体积密度高,耐压强度高,抗折强度高,导热系数低,重烧线变化率低的致密钙长石质耐火材料;2、本发明制备出的致密钙长石质耐火材料,体积密度为2.43~2.52g/cm3,常温抗折强度为1.82~1.97mpa,常温耐压强度为22.6~24.1mpa,重烧线变化率为-0.45~-0.64%,200℃、400℃、600℃下导热系数分别为0.069~0.083w
·
m-1
·
k-1
、0.097~0.106 w
·
m-1
·
k-1
、0.124~0.131 w
·
m-1
·
k-1
;3、本发明通过添加微米级硅铝酸钠粉末、铝酸钙粉末、硅酸钙粉末来促进糖厂工业滤饼渣粉、焦宝石粉、有机硅钙肥三种主原料的烧结致密度,最终提高了耐火材料的体积密度;4、本发明通过对混合粉体进行预处理,来抑制制浆步骤中的粉体团聚现象,提高了压制成型过程中生胚的密实度,最终提高了耐火材料烧结体的各项性能;5、本发明用磷酸硅、偏硅酸钠作为粘结剂,提高了造粒过程所得粒料的滑动性,使压制成型过程能够得到密实度更高的生胚,进而提高了最终成品的各项性能。
具体实施方式
16.以下对本发明的优选实施例进行说明,应当理解,此处所描述的优选实施例仅用于说明和解释本发明,并不用于限定本发明。
17.实施例1:一种致密钙长石质耐火材料的制备方法包括以下步骤:1、混合粉体制备将糖厂工业滤饼渣粉、焦宝石粉、有机硅钙肥、硅铝酸钠粉末、铝酸钙粉末、硅酸钙粉末混合后,球磨成平均粒径15微米的混合粉末,得到混合粉体;所述糖厂工业滤饼渣粉、焦宝石粉、有机硅钙肥、硅铝酸钠粉末、铝酸钙粉末、硅酸钙粉末的质量比为40:60:40:3:4:6;所述糖厂工业滤饼渣粉,其平均粒径为12微米,cao含量为52wt%;所述焦宝石粉,其平均粒径为130微米,sio2含量为50wt%,al2o3含量为45wt%;所述有机硅钙肥,其平均粒径为800微米,sio2含量为30wt%,cao含量为45wt%;所述硅铝酸钠粉末的平均粒径为35微米;所述铝酸钙粉末的平均粒径为40微米;所述硅酸钙粉末的平均粒径为40微米。
18.2、混合粉体预处理将四(三乙醇胺)锆酸酯、2-丁氧基乙醇磷酸酯、硬脂酸、三聚氰胺搅拌溶解于乙酸乙酯中,控温60℃,搅拌速度2200转/分下,将混合粉体缓慢加入其中,搅拌2小时后,过滤,滤出的固体粉末在80℃下烘干1.5小时,得到预处理的混合粉体;所述四(三乙醇胺)锆酸酯、2-丁氧基乙醇磷酸酯、硬脂酸、三聚氰胺、乙酸乙酯、混合粉体的质量比为1.2:1:3:5:110:40。
19.3、制浆将磷酸硅、偏硅酸钠、十二烷基硫酸钠、去离子水混合成溶液,7000转/分搅拌速度下,向溶液中缓慢加入预处理的混合粉体,加料完毕后,继续搅拌4小时后出料得到料浆;
所述磷酸硅、偏硅酸钠、十二烷基硫酸钠、去离子水、预处理的混合粉体的质量比为1:12:0.8:130:45。
20.4、造粒对料浆进行喷雾造粒,进口温度控制为120℃,出口温度控制为80℃,得到粒料;所述粒料的粒径为30微米。
21.步骤5、压制成型将粒料放入模具中,在40mpa下压制成型,得到生胚。
22.6、烧结将生胚于120℃下干燥15小时后,以3℃/min速率升温至1300℃,恒温煅烧3.5小时,然后冷却至室温得到致密钙长石质耐火材料。
23.实施例2:一种致密钙长石质耐火材料的制备方法包括以下步骤:1、混合粉体制备将糖厂工业滤饼渣粉、焦宝石粉、有机硅钙肥、硅铝酸钠粉末、铝酸钙粉末、硅酸钙粉末混合后,球磨成平均粒径10微米的混合粉末,得到混合粉体;所述糖厂工业滤饼渣粉、焦宝石粉、有机硅钙肥、硅铝酸钠粉末、铝酸钙粉末、硅酸钙粉末的质量比为30:40:30:1:2:2;所述糖厂工业滤饼渣粉,其平均粒径为10微米,cao含量为46wt%;所述焦宝石粉,其平均粒径为110微米,sio2含量为45wt%,al2o3含量为40wt%;所述有机硅钙肥,其平均粒径为500微米,sio2含量为25wt%,cao含量为36wt%;所述硅铝酸钠粉末的平均粒径为20微米;所述铝酸钙粉末的平均粒径为15微米;所述硅酸钙粉末的平均粒径为25微米。
24.2、混合粉体预处理将四(三乙醇胺)锆酸酯、2-丁氧基乙醇磷酸酯、硬脂酸、三聚氰胺搅拌溶解于乙酸乙酯中,控温50℃,搅拌速度1800转/分下,将混合粉体缓慢加入其中,搅拌1小时后,过滤,滤出的固体粉末在70℃下烘干1小时,得到预处理的混合粉体;所述四(三乙醇胺)锆酸酯、2-丁氧基乙醇磷酸酯、硬脂酸、三聚氰胺、乙酸乙酯、混合粉体的质量比为1:0.5:2:3:90:30。
25.3、制浆将磷酸硅、偏硅酸钠、十二烷基硫酸钠、去离子水混合成溶液,5500转/分搅拌速度下,向溶液中缓慢加入预处理的混合粉体,加料完毕后,继续搅拌3小时后出料得到料浆;所述磷酸硅、偏硅酸钠、十二烷基硫酸钠、去离子水、预处理的混合粉体的质量比为0.5:8:0.5:100:35。
26.4、造粒对料浆进行喷雾造粒,进口温度控制为110℃,出口温度控制为70℃,得到粒料;所述粒料的粒径为20微米。
27.5、压制成型将粒料放入模具中,在25mpa下压制成型,得到生胚。
28.6、烧结将生胚于80℃下干燥10小时后,以2℃/min速率升温至1200℃,恒温煅烧2小时,然后冷却至室温得到致密钙长石质耐火材料。
29.实施例3:一种致密钙长石质耐火材料的制备方法包括以下步骤:1、混合粉体制备将糖厂工业滤饼渣粉、焦宝石粉、有机硅钙肥、硅铝酸钠粉末、铝酸钙粉末、硅酸钙粉末混合后,球磨成平均粒径25微米的混合粉末,得到混合粉体;所述糖厂工业滤饼渣粉、焦宝石粉、有机硅钙肥、硅铝酸钠粉末、铝酸钙粉末、硅酸钙粉末的质量比为50:70:45:5:6:9;所述糖厂工业滤饼渣粉,其平均粒径为15微米,cao含量为60wt%;所述焦宝石粉,其平均粒径为150微米,sio2含量为55wt%,al2o3含量为50wt%;所述有机硅钙肥,其平均粒径为1000微米,sio2含量为45wt%,cao含量为50wt%;所述硅铝酸钠粉末的平均粒径为60微米;所述铝酸钙粉末的平均粒径为55微米;所述硅酸钙粉末的平均粒径为65微米。
30.2、混合粉体预处理将四(三乙醇胺)锆酸酯、2-丁氧基乙醇磷酸酯、硬脂酸、三聚氰胺搅拌溶解于乙酸乙酯中,控温70℃,搅拌速度2600转/分下,将混合粉体缓慢加入其中,搅拌3小时后,过滤,滤出的固体粉末在90℃下烘干2小时,得到预处理的混合粉体;所述四(三乙醇胺)锆酸酯、2-丁氧基乙醇磷酸酯、硬脂酸、三聚氰胺、乙酸乙酯、混合粉体的质量比为1.5:1.3:4:7:120:50。
31.3、制浆将磷酸硅、偏硅酸钠、十二烷基硫酸钠、去离子水混合成溶液,8500转/分搅拌速度下,向溶液中缓慢加入预处理的混合粉体,加料完毕后,继续搅拌6小时后出料得到料浆;所述磷酸硅、偏硅酸钠、十二烷基硫酸钠、去离子水、预处理的混合粉体的质量比为1.5:15:1:150:50。
32.4、造粒对料浆进行喷雾造粒,进口温度控制为140℃,出口温度控制为95℃,得到粒料;所述粒料的粒径为46微米。
33.5、压制成型将粒料放入模具中,在50mpa下压制成型,得到生胚。
34.6、烧结将生胚于140℃下干燥19小时后,以5℃/min速率升温至1400℃,恒温煅烧5小时,然后冷却至室温得到致密钙长石质耐火材料。
35.对比例1:实施例1基础上,将硅铝酸钠粉末、铝酸钙粉末、硅酸钙粉末等量替换为焦宝石粉步骤1中,实施例1基础上,将3份硅铝酸钠粉末、4份铝酸钙粉末、6份硅酸钙粉末等量替换为13份焦宝石粉,其它操作同于实施例1;
步骤2、3、4、5、6操作同于实施例1。
36.对比例2:实施例1基础上,不进行混合粉体预处理步骤混合粉体制备操作同于实施例1的步骤1;不进行混合粉体预处理步骤;制浆步骤中,实施例1基础上,将45份预处理的混合粉体等量替换为45份混合粉体,其它操作同于实施例1的步骤3;造粒、压制成型、烧结三个步骤的操作同于实施例1的步骤4、5、6。
37.对比例3:实施例1基础上,制浆步骤中将磷酸硅、偏硅酸钠替换为聚乙烯醇步骤1、2操作同于实施例1;步骤3中,实施例1基础上,将1份磷酸硅、12份偏硅酸钠等量替换为13份聚乙烯醇;所述聚乙烯醇的分子量为5325g/mol;步骤4、5、6操作同于实施例1。
38.性能测试:按下述相关标准,对实施例1、2、3和对比例1、2、3得到的致密钙长石质耐火材料进行性能测试;1、根据gb/t2998-2001测试体积密度;2、按照gb/t3997.2-1998测试抗折强度、耐压强度;3、按照gb/t3997.1-1998测试重烧线变化率;4、按照yb/t4130-2005测试导热系数;以上测试结果见下表:对比例1中不加入硅铝酸钠粉末、铝酸钙粉末、硅酸钙粉末,得到的耐火材料体积密度相比实施例1、2、3下降显著,进而影响到产品的其它性能;对比例2中不进行混合粉体预处理,同样引起耐火材料体积密度的下降及其它性能的降低;对比例3中,粘结剂磷酸硅、偏硅酸钠替换为聚乙烯醇,耐火材料的体积密度下降最大,可见无机粘结剂相对有机粘结剂有显著的积极效果。
再多了解一些
本文用于企业家、创业者技术爱好者查询,结果仅供参考。