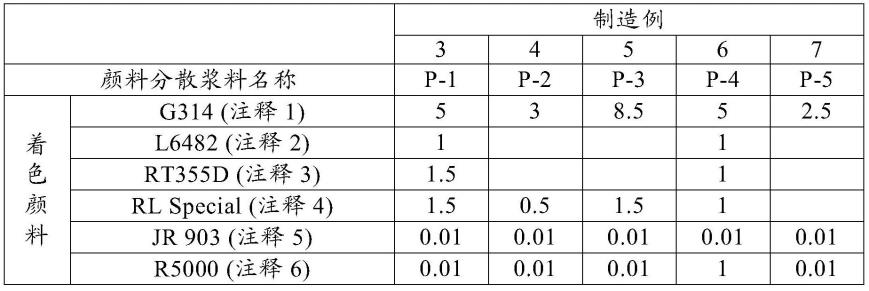
1.相关专利申请的交叉引用本技术要求2019年11月22日提交的第2019-211244号日本专利申请的优先权(其全部公开内容通过引用并入本说明书中)。本发明涉及一种多层涂膜形成方法。
背景技术:
2.对于诸如汽车的工业产品的外部颜色,用户高度要求彩度高和暗度(深邃感)优异的涂料颜色作为有奢华感和吸引性优异的涂料颜色。
3.作为获得这种彩度高和暗度优异的涂料颜色的方法,已经公开了一种多层涂膜形成方法,所述方法包括依次涂装第一着色涂料、具有透明度的第二着色涂料和透明涂料。
4.例如,专利文献1(ptl1)公开了一种用于形成具有复杂外观设计的多层涂膜的方法,其包括以下步骤:将包含着色成分和/或效应材料的第一涂料涂装至被涂物的表面以形成第一涂膜,在不使第一涂膜受热固化的情况下将包含基于涂料的树脂固体含量的0.01重量%至1重量%含量的着色成分的第二涂料涂装至第一涂膜以形成第二涂膜,并且在使第二涂膜不受热固化的情况下将透明涂料涂装至第二涂膜以形成透明涂膜。然而,尽管通过该方法获得的涂膜具有高彩度,但暗度不足;另外有时观察到因膜厚度变化而引起的颜色不均匀性和颜色变化。引文列表专利文献
5.ptl 1:jp2001-314807a
技术实现要素:
要解决的技术问题
6.本发明的目的是提供一种多层涂膜形成方法,所述方法能够消除上述缺陷并形成彩度高、暗度优异、因膜厚度变化而引起的颜色不均匀性降低和颜色变化降低的多层涂膜。解决问题的方案
7.本发明包括如下各项中陈述的主题(技术方案)。项1.多层涂膜形成方法,其包括步骤(1):涂装包含效应颜料和着色颜料的第一着色涂料(x)以形成第一着色涂膜,步骤(2):将包含着色颜料的第二着色涂料(y)涂装至所述第一着色涂膜以形成第二着色涂膜,步骤(3):将透明涂料(z)涂装至所述第二着色涂膜以形成透明涂膜,以及步骤(4):分别或同时加热在所述步骤(1)中形成的所述第一着色涂膜、在所述步骤(2)中形成的所述第二着色涂膜和在所述步骤(3)中形成的所述透明涂膜以固化这些涂膜;
其中,所述第一着色涂膜的明度l
*
值为30至60,所述第二着色涂膜在400nm以上且700nm以下的波长处的透光率为10%以上且小于30%,并且作为所述第一着色涂膜的l*c*h颜色空间图中的色相角h值(h(x))与所述多层涂膜的l*c*h颜色空间图中的色相角h值(h(s))之间的差|h(x)-h(s)|为0至30。项2.如项1所述的多层涂膜形成方法,其中通过所述多层涂膜形成方法获得的所述多层涂膜在l*c*h颜色空间图中的色相角h值(h(s))为225至315。项3.如项1或2所述的多层涂膜形成方法,其中所述第一着色涂料(x)中的着色颜料和所述第二着色涂料(y)中的着色颜料包含酞菁颜料。项4.如项1至3中任一项所述的多层涂膜形成方法,其中包含在所述第一着色涂料(x)中的所述效应颜料包含着色铝颜料。项5.如项1至4中任一项所述的多层涂膜形成方法,其中所述第二着色涂料(y)包含颜料质量浓度(本文中也称为“pwc”:颜料重量浓度)为0.1%至10%的所述着色颜料。项6.如项1至5中任一项所述的多层涂膜形成方法,其中所述第二着色涂料(y)还包含效应颜料。项7.如项6所述的多层涂膜形成方法,其中所述第二着色涂料(y)包含颜料质量浓度为1.2%至5%的所述效应颜料。发明的有益效果
8.基于本发明的多层涂膜形成方法能够形成一种彩度高、暗度优异、因膜厚度变化而引起的颜色变化降低和颜色不均匀性降低的多层涂膜。
具体实施方式
9.步骤(1)基于本发明的方法,在步骤(1)中,首先涂装第一着色涂料(x)以形成第一着色涂膜。第一着色涂料(x)是赋予遮盖力并确定所得多层涂膜的色相的涂料。第一着色涂料(x)包含效应颜料和着色颜料。
10.第一着色涂膜的特征在于在l*c*h颜色空间中具有为30至60的明度l
*
。
11.l*c*h颜色空间(l*c*h表色系)是l
*a*b*
颜色空间(l*a*b*表色系)的极坐标版本,其在1976年由国际照明委员会标准化,并且也在jisz8781-4(2013)中采用。l
*
值表示明度。c
*
值表示彩度(色度),其是距起始点的距离。h值表示在l
*a*b*
颜色空间中从a
*
红色方向上的轴设为0
°
开始的并且在色相方面逆时针方向移动的色相角。
12.在本说明书中,明度l
*
、彩度c
*
和色相角h是由用配备有积分球的分光光度计测量的反射率(模式不包括镜面反射光)计算的值。
13.配备有积分球的分光光度计的实例包括cr-400和cr-410(商品名,由konica minolta,inc.制造)。
14.第一着色涂膜的l*c*h颜色空间中的明度l
*
的上限没有特别限制,只要其为60或更小即可。例如,上限优选为50或更小,更优选为45或更小。第一着色涂膜的l*c*h颜色空间中的明度l
*
的下限没有特别限制,只要其为30或更大即可,例如优选为32或更大,更优选为35或更大。第一着色涂膜的明度l
*
优选为32至50,更优选为35至45。从诸如改善所得多层涂
膜的彩度和暗度以及抑制颜色不均匀性和因膜厚度变化而引起的颜色变化的观点出发,第一着色涂膜优选具有在上述范围的明度l
*
值。
15.此外,从例如抑制因膜厚度变化而引起的颜色变化的观点出发,第一着色涂膜的色相角h值(h(x))优选为225至315,更优选为240至310,并且进一步优选为255至305。
16.作为包含在第一着色涂料(x)中的效应颜料的实例包括铝颜料、气相沉积金属片颜料和干涉颜料。其中,从所得多层涂膜的暗度等观点出发,铝颜料是优选的。铝颜料优选为鳞片状的铝片颜料。这些颜料可以适当地单独使用或者组合两种或更多种使用。
17.铝颜料通常通过在研磨液体介质的存在下在球磨机或磨碎机中使用研磨助剂来粉碎和研磨铝来制造。研磨助剂的实例包括:高级脂肪酸(例如油酸、硬脂酸、异硬脂酸、月桂酸、棕榈酸和肉豆蔻酸)以及脂肪族胺、脂肪族酰胺和脂肪族醇。研磨液体介质的实例包括脂肪族烃,例如矿油精。
18.根据研磨助剂的类型,铝颜料被大致分类为漂浮型铝颜料和非漂浮型铝颜料。添加至涂料组合物中的漂浮型铝颜料在通过涂装涂料组合物形成的涂膜的表面上取向(漂浮),从而提供具有强金属感的成品,同时表现出热反射和防锈效果。因此,漂浮型铝颜料经常用于罐、导管、管道和屋顶以及用于各种建筑材料。从所得多层涂膜的暗度等观点出发,第一着色涂料(x)优选包含非漂浮型铝颜料。
19.关于尺寸,从所得多层涂膜的暗度的观点出发,铝颜料优选具有在5至30μm的平均粒径。平均粒径更优选地为7至25μm,并且特别优选地为8至23μm。厚度优选为0.05至5μm。本文所用的“平均粒径”是指使用microtrack mt3300粒径分布分析仪(商品名,由nikkiso co.,ltd.制造)通过激光衍射散射测量的以体积加权粒径分布计的中值尺寸。如本文所用的“厚度”被定义为通过使用显微镜观察含有铝颜料的涂膜横截面并使用图像处理软件测量厚度且计算100个或更多个颗粒的测量值所求得的平均值。
20.当第一着色涂料(x)包含铝颜料时,铝颜料的颜料质量浓度没有特别限制,并且在优选的实施方式中,从所得多层涂膜的暗度的观点出发,基于第一着色涂料(x)的固体含量,铝颜料的颜料质量浓度是1%至50%,优选3%至40%,并且进一步优选5%至20%。
21.从抑制颜色不均匀性和抑制因所得多层涂膜的膜厚度变化而引起的颜色变化的观点出发,优选使用着色铝颜料作为上述铝颜料中的至少一种。
22.作为使用的着色铝颜料典型的是在作为基材的铝片表面涂装有着色层的颜料。
23.着色铝颜料的实例包括:所包含铝片的表面通过具有一个或多个双键和两个或更多个羧基的热聚合物(所述热聚合物通过一种或多种含双键的羧酸的热聚合获得)化学吸附有着色颜料而成的颜料;以及所包含铝片的表面化学吸附有着色颜料并且进而通过由可自由基聚合的不饱和羧酸和包含三个或更多个可自由基聚合的双键的单体形成的聚合物包覆在所述铝片上而成的颜料。
24.在此,可自由基聚合的不饱和羧酸表示具有一个或多个可自由基聚合的不饱和基团的羧酸。如本文所用,可自由基聚合的不饱和基团意指可以经历自由基聚合的不饱和基团。这种可聚合不饱和基团的实例包括乙烯基和(甲基)丙烯酰基。
25.在此,着色颜料决定着色铝颜料的色相。使用的着色颜料可以适当选自已知的有机颜料或无机颜料。使用的着色颜料的具体实例包括:有机颜料,例如偶氮颜料、喹吖啶酮颜料、二酮吡咯并吡咯颜料、苝颜料、紫环酮颜料、苯并咪唑酮颜料、异吲哚啉颜料、异吲哚
啉酮颜料、金属螯合物偶氮颜料、酞菁颜料、蒽醌颜料、二噁嗪颜料、还原颜料和靛蓝颜料。其中,从所得多层涂膜的色相和彩度的观点出发,优选使用酞菁颜料。
26.除了包含其表面涂装有着色颜料的铝片的颜料以外,使用的着色铝颜料还可以是包含其表面通过气相方法或液相方法涂装有金属氧化物如氧化铁的铝片的颜料。
27.关于尺寸,从抑制因膜厚度变化而引起的颜色变化和抑制所得多层涂膜的颜色不均匀性的观点出发,着色铝颜料优选具有5至30μm的平均粒径。平均粒径更优选地为7至25μm,并且特别优选地为8至23μm。厚度优选为0.05至5μm。
28.当第一着色涂料(x)包含铝颜料时,铝颜料的颜料质量浓度没有特别限制,并且在优选的实施方式中,从抑制颜色不均匀性和抑制因所得多层涂膜的膜厚度变化而引起的颜色变化的观点出发,基于第一着色涂料(x)的固体含量,着色铝颜料的颜料质量浓度为0.1%至30%,优选0.5%至20%,进一步优选1%至10%。
29.此外,从改善所得多层涂膜的彩度和暗度、抑制因膜厚度变化而引起的颜色变化和抑制颜色不均匀性的观点出发,优选组合使用着色铝颜料和非着色铝颜料作为铝颜料。
30.当组合使用着色铝颜料和非着色铝颜料作为铝颜料时,着色铝颜料和非着色铝颜料的比例没有特别限制。在优选的实施方式中,从改善所得多层涂膜的彩度和暗度、抑制颜色不均匀性和抑制因膜厚度变化而引起的颜色变化的观点出发,着色铝颜料与非着色铝颜料的质量比为95/5至1/99,优选90/10至10/90,进一步优选80/20至10/90。
31.气相沉积金属片颜料通常通过在基材上气相沉积金属膜、剥离基材并且然后研磨气相沉积金属膜来获得。基底材料的实例包括膜。
32.上述金属的材料没有特别限制。实例包括铝、金、银、铜、黄铜、钛、铬、镍、镍铬和不锈钢。其中,从例如易得性和易操作性的观点出发,铝或铬是特别优选的。通过气相沉积铝作为金属材料获得的气相沉积铝片颜料可以用作铝颜料。
33.干涉颜料是通常通过用具有不同折射率的金属氧化物涂装透明或半透明片状基材(例如天然云母、合成云母、玻璃、二氧化硅、氧化铁、氧化铝和各种金属氧化物)的表面所获得的效应颜料。干涉颜料可以单独使用或者组合两种或更多种使用。
34.天然云母是通过将云母从矿石中粉碎获得的片状基材。合成云母是通过加热诸如sio2、mgo、al2o3、k2sif6或na2sif6的工业材料,在约1500℃的高温下熔化材料并且冷却熔体用于结晶来合成。当与天然云母相比时,合成云母含有较少量的杂质并且具有更均匀的尺寸和厚度。合成云母基材的具体实例包括氟金云母(kmg3alsi3o
10
f2)、钾四硅云母(kmg
2.5
alsi4o
10
f2)、钠四硅云母(namg
2.5
alsi4o
10
f2)、na带云母(namg2lisi4o
10
f2)和lina带云母(limg2lisi4o
10
f2)。
35.用于涂装基材的金属氧化物的实例包括氧化钛和氧化铁。干涉颜料根据金属氧化物的厚度的差异表现各种不同的干涉色。
36.干涉颜料的具体实例包括以下描述的金属氧化物涂装的云母颜料、金属氧化物包覆的氧化铝片颜料、金属氧化物涂装的玻璃片颜料和金属氧化物涂装的二氧化硅片颜料。
37.金属氧化物涂装的云母颜料是通过用金属氧化物涂装天然云母或合成云母基材的表面所获得的颜料。
38.金属氧化物包覆的氧化铝片颜料是通过用金属氧化物涂装氧化铝片状基材的表面所获得的颜料。氧化铝片是指通常透明且无色的片状(薄的)氧化铝。氧化铝片不一定仅
由氧化铝组成,并且可以含有其它金属氧化物。
39.金属氧化物涂装的玻璃片颜料是通过用金属氧化物涂装片状玻璃基材的表面所获得的颜料。金属氧化物涂装的玻璃片颜料具有光滑的基材表面,这导致强烈的光反射。
40.金属氧化物涂装的二氧化硅片颜料是通常通过用金属氧化物涂装片状二氧化硅所获得的颜料,所述片状二氧化硅是具有光滑表面和均匀厚度的基材。
41.作为包含在第一着色涂料(x)中的着色颜料的实例包括:氧化钛颜料、氧化铁颜料、钛黄颜料、偶氮颜料、喹吖啶酮颜料、二酮吡咯并吡咯颜料、苝颜料、紫环酮颜料、苯并咪唑酮颜料、异吲哚啉颜料、异吲哚啉酮颜料、金属螯合物偶氮颜料、酞菁颜料、蒽醌颜料、二噁嗪颜料、还原颜料、靛蓝颜料和碳黑颜料。这些着色颜料可以单独使用或者组合两种或更多种使用。其中,从所得多层涂膜的色相和彩度的观点出发,优选使用酞菁颜料。
42.从所得多层涂膜的色相和彩度的观点出发,基于第一着色涂料(x)的固体含量,第一着色涂料(x)中包含的着色颜料的颜料质量浓度为1%至50%,优选3%至40%,并且进一步优选5%至20%。
43.第一着色涂料(x)通常可以包含树脂成分作为媒介物(展色剂)。作为树脂成分,优选使用热固性树脂组合物。其具体实例包括:热固性树脂组合物,其包含具有可交联官能团(例如羟基)的基体树脂(例如丙烯酸树脂、聚酯树脂、醇酸树脂和氨基甲酸酯树脂)以及交联剂(例如三聚氰胺树脂、脲树脂和多异氰酸酯化合物及其封端的多异氰酸酯化合物)。这种热固性树脂组合物在使用前溶解或分散在溶剂如有机溶剂和/或水中。树脂组合物中基体树脂和交联剂的比例没有特别限制。基于总基体树脂固体含量,交联剂通常以10至100质量%,优选20至80质量%,更优选30至60质量%使用。
44.第一着色涂料(x)可以任选地进一步适当地包含:溶剂,例如水或有机溶剂;用于涂料的各种添加剂,例如流变调节剂、颜料分散剂、抗沉降剂、固化催化剂、消泡剂、抗氧化剂和紫外线吸收剂;以及体质颜料。
45.第一着色涂料(x)可以通过诸如静电涂装、空气喷射涂装和无空气喷射涂装的方法来涂装。第一着色涂膜的膜厚度没有特别限制,并且从改善彩度和暗度以及抑制所得多层涂膜的颜色不均匀性的观点出发,基于固化涂膜,优选为约1至40μm,更优选为3至30μm,进一步优选为约5至20μm。
46.第一着色涂料(x)的固体含量没有特别限制,例如为10质量%至65质量%,优选15质量%至55质量%,更优选20质量%至50质量%。此外,优选的是,用水和/或有机溶剂将第一着色涂料(x)的粘度适当地调节至适于涂装的范围,其通常为500至5000mpa
·
s,所述粘度如使用b型粘度计以6rpm的旋转速度在20℃下测量的。
47.在涂装如下所述的第二着色涂料(y)之前,可以在使得涂膜基本上不固化的加热条件下对第一着色涂膜进行预热、吹气等。预热在优选40至100℃,更优选50至90℃,并且进一步优选60至80℃的温度下进行优选30秒至15分钟,更优选1至10分钟,并且进一步优选2至5分钟。吹气可以例如通过将加热至常温或25℃至80℃的温度的空气吹至被涂物的涂装表面上30秒至15分钟来进行。
48.步骤(2)基于本发明的方法,然后将第二着色涂料(y)涂装至在步骤(1)中形成的第一着色涂膜以形成第二着色涂膜。第二着色涂料(y)是增强彩度并改善所得多层涂膜的暗度的涂
料。第二着色涂料(y)包含作为必要成分的着色颜料。
49.所述第二着色涂膜在400nm以上且700nm以下的波长处的透光率为15%以上且小于30%。当透光率为15%或更高时,所得多层涂膜具有优异的彩度。此外,当透光率小于30%时,所得多层涂膜具有优异的暗度。特别地,从所得多层涂膜的彩度和暗度的观点出发,第二着色涂膜优选具有在400nm以上且700nm以下的波长处17%至29%、更优选20%至28%的透光率。
50.如本文所用,第二着色涂膜在400nm以上且700nm以下的波长处的透光率可以通过以下方法测量。
51.首先,将第二着色涂料(y)涂装至聚丙烯板,然后固化。接着,剥离并收集固化涂膜,并且用分光光度计测量在400nm以上且700n m以下的波长处的透光率。在本发明中,“在400nm以上且700nm以下的波长处的透光率”是指在400nm以上且700nm以下的波长处的透光率的平均值。分光光度计可以是例如uv-2700(商品名,由shimadzu corporation制造)。
52.作为包含在第二着色涂料(y)中的着色颜料的实例包括:无机颜料,例如复合氧化物颜料,例如氧化钛颜料、氧化铁颜料和钛黄;有机颜料,例如偶氮颜料、喹吖啶酮颜料、二酮吡咯并吡咯颜料、苝颜料、紫环酮颜料、苯并咪唑酮颜料、异吲哚啉颜料、异吲哚啉酮颜料、金属螯合物偶氮颜料、酞菁颜料、蒽醌颜料,二噁嗪颜料、还原颜料和靛蓝颜料;以及炭黑颜料。这些着色颜料可以单独使用或者组合两种或更多种使用。其中,从所得多层涂膜的色相和彩度的观点出发,优选使用酞菁颜料。
53.作为包含在第二着色涂料(y)中的着色颜料的颜料质量浓度没有特别限制,并且在优选的实施方式中,从所得多层涂膜的彩度和暗度的观点出发,基于第二着色涂料(y)的固体含量,为0.1%至10%,优选1%至9%,并且更优选3%至8%。
54.优选第二着色涂料(y)还包含效应颜料。
55.这里使用的效应颜料可以是在上述步骤(1)的描述中提到的任何效应颜料。
56.从抑制所得多层涂膜的颜色不均匀性的观点出发,效应颜料优选为干涉颜料,更优选为金属氧化物包覆的氧化铝片颜料。
57.关于尺寸,从抑制所得多层涂膜的颜色不均匀性的观点出发,效应颜料优选具有5至30μm的平均粒径。平均粒径更优选地为7至25μm,并且特别优选地为8至23μm。厚度优选为0.05至5μm。
58.当第二着色涂料(y)包含效应颜料时,效应颜料的颜料质量浓度没有特别限制,并且在优选的实施方式中,从抑制所得多层涂膜的颜色不均匀性的观点出发,基于第二着色涂料(y)的固体含量,效应颜料的颜料质量浓度为1.2%至5%,优选1.3%至4%,更优选1.5%至3%。
59.第二着色涂料(y)通常可以包含树脂成分作为展色剂。作为树脂成分,优选使用热固性树脂组合物。其具体实例包括热固性树脂组合物,其包含具有可交联官能团(例如羟基)的基体树脂(例如丙烯酸树脂、聚酯树脂、醇酸树脂和氨基甲酸酯树脂)以及交联剂(例如三聚氰胺树脂、脲树脂和多异氰酸酯化合物及其封端的多异氰酸酯化合物)。这种热固性树脂组合物在使用前溶解或分散在溶剂如有机溶剂和/或水中。树脂组合物中基体树脂和交联剂的比例没有特别限制。基于总基体树脂固体含量,交联剂通常以10至100质量%,优选20至80质量%,更优选30至60质量%使用。
60.若需要,第二着色涂料(y)可以进一步适当地包含:溶剂,例如水或有机溶剂;用于涂料的各种添加剂,例如流变调节剂、颜料分散剂、抗沉降剂、固化催化剂、消泡剂、抗氧化剂和紫外线吸收剂;以及体质颜料。
61.第二着色涂料(y)可以通过诸如静电涂装、空气喷射涂装和无空气喷射涂装的方法来涂装。第二着色涂膜的膜厚度没有特别限制,并且在优选的实施方式中,从所得多层涂膜的彩度和暗度的观点出发,基于固化涂膜,为约1至30μm,更优选约3至20μm,进一步优选约5至15μm。
62.第二着色涂料(y)的固体含量没有特别限制,并且在优选的实施方式中,为10质量%至65质量%,优选15质量%至55质量%,并且进一步优选20质量%至50质量%。此外,优选的是,用水和/或有机溶剂将第二着色涂料(y)的粘度适当地调节至适于涂装的范围,其通常为500至5000mpa
·
s,如使用b型粘度计以6rpm的旋转速度在20℃下测量的。
63.在涂装如下所述的透明涂料(z)之前,可以在涂膜基本上不固化的加热条件下对第二着色涂膜进行预热、吹气等。预热在优选40至100℃,更优选50至90℃,并且进一步优选60至80℃的温度下进行优选30秒至15分钟,更优选1至10分钟,并且进一步优选2至5分钟。吹气可以例如通过将加热至常温或25℃至80℃的温度的空气吹至被涂物的涂装表面上30秒至15分钟来进行。
64.步骤(3)基于本发明的方法,将透明涂料(z)涂装至通过涂装如上所述的第二着色涂料(y)获得的第二着色涂膜上,以形成透明涂膜。
65.用于基于本发明的方法的透明涂料(z)可以是任何已知的透明涂料。具体实例包括形成无色或着色的透明涂膜的液体或粉末状透明涂料,其包含由基体树脂和交联剂组成的树脂成分作为必要成分以及任选的成分如涂料添加剂和溶剂(例如水或有机溶剂)。
66.基体树脂的实例包括:具有可交联官能团(例如羟基、羧基、硅烷醇基和环氧基)的树脂,例如丙烯酸树脂、聚酯树脂、醇酸树脂、氟树脂、氨基甲酸酯树脂和含硅树脂。交联剂的实例包括:具有与基体树脂的官能团反应的官能团的化合物或树脂,例如三聚氰胺树脂、脲树脂、多异氰酸酯化合物、封端多异氰酸酯化合物、环氧化合物或树脂、含羧基的化合物或树脂、酸酐和含烷氧基甲硅烷基的化合物或树脂。
67.树脂成分中基体树脂和交联剂的比例没有特别限制。通常,基于基体树脂的总固体含量,使用的交联剂的量为10质量%至100质量%,优选20质量%至80质量%,更优选30质量%至60质量%。
68.透明涂料(z)可以任选地包含:溶剂如水和有机溶剂;以及涂料添加剂,例如固化催化剂、消泡剂、紫外线吸收剂、流变调节剂和抗沉降剂。
69.透明涂料(z)也可以适当地包含着色颜料至达到不损害涂膜的透明度的程度。使用的着色颜料可以是用于油墨或涂料的已知颜料,并且这些颜料可以单独使用或者组合两种或更多种使用。尽管使用的着色颜料的量例如根据使用的着色颜料的类型而变化,但基于透明涂料中树脂成分的总固体含量,着色颜料的量通常为30质量%或更少,优选为0.05质量%至20质量%,更优选为0.1质量%至10质量%。
70.透明涂料(z)可以通过诸如静电涂装、空气喷射涂装和无空气喷射涂装的方法来涂装。透明涂膜的膜厚度没有特别限制,并且在优选实施方式中,基于固化涂膜,为约10至
60μm,更优选约15至50μm,进一步优选约20至40μm。
71.透明涂料(z)的固体含量没有特别限制,并且在优选的实施方式中,为10质量%至65质量%,优选15质量%至55质量%,并且进一步优选20质量%至50质量%。此外,优选的是,用水和/或有机溶剂将透明涂料(z)的粘度适当地调节至适于涂装的范围,其通常为约15至60秒,特别是约20至50秒,如使用第4号福特杯粘度计在20℃测量的。
72.步骤(4)基于本发明的方法,分别或同时加热在步骤(1)中形成的第一着色涂膜、在步骤(2)中形成的第二着色涂膜和在步骤(3)中形成的透明涂膜以固化这些膜。
73.特别地,从例如节能的观点出发,优选同时加热第一着色涂膜、第二着色涂膜和透明涂膜。
74.加热可以用已知技术进行,例如热风炉、电炉或红外引导加热炉。加热温度优选为70℃至150℃,并且更优选为80℃至140℃。加热时间没有特别限制,并且优选为约10至40分钟、更优选为约20至30分钟。
75.基材应用本发明方法的基材可以是任何基材。实例包括:由金属形成的构件,例如铁、锌、铝或镁;由这些金属的合金形成的构件;镀有这些金属的构件,或这些金属沉积在其上的构件;以及由例如各种材料的玻璃、塑料或泡沫形成的构件。特别地,构成车体的钢和塑料材料是合适的,钢是特别合适的。这些构件可以任选地进行处理,例如脱脂或表面处理。
76.其上形成底涂膜和/或中间涂膜的这些构件也可以用作基材。在本发明中,优选使用这些基材。
77.将底涂膜涂装至构件的表面以遮盖构件的表面,或者赋予构件防腐性和防锈性。底涂膜可以通过涂装底涂涂料并将其固化而形成。这种底涂涂料可以是任何底涂涂料;并且可以是已知的涂料,例如电沉积涂料或溶剂型底漆。
78.将中间涂膜应用于基底,以遮盖构件或基底的表面,例如底涂膜,增强底涂膜与顶涂膜之间的粘合,或者赋予涂膜抗崩裂性。中间涂膜可以通过将中间涂料涂装至基底的表面(例如构件的表面或底涂膜)并固化涂料来形成。使用的中间涂料可以是任何已知的中间涂料。例如,可以优选使用包含热固性树脂组合物和着色颜料的有机溶剂型中间涂料或水性中间涂料。
79.当在本发明的方法中使用其上形成有底涂膜和/或中间涂膜的构件作为基材时,通过预先加热固化底涂膜和/或中间涂膜,然后可以涂装步骤(1)的第一着色涂料(x)。第一着色涂料(x)也可以与未固化的底涂膜和/或中间涂膜一起涂装。特别地,从节能的观点出发,第一着色涂料(x)优选在中间涂膜未固化的情况下涂装。
80.多层涂膜的形成基于本发明的方法,通过进行以下步骤(1)至(4)形成多层涂膜:步骤(1):涂装包含效应颜料和着色颜料的第一着色涂料(x)以形成第一着色涂膜,步骤(2):将包含着色颜料的第二着色涂料(y)涂装至所述第一着色涂膜以形成第二着色涂膜,步骤(3):将透明涂料(z)涂装至所述第二着色涂膜以形成透明涂膜,以及
步骤(4):分别或同时加热在所述步骤(1)中形成的所述第一着色涂膜、在所述步骤(2)中形成的所述第二着色涂膜和在所述步骤(3)中形成的所述透明涂膜以固化这些涂膜。第一着色涂膜的明度l
*
值为30至60,第二着色涂膜在400nm以上且700nm以下的波长处的透光率为15%以上且小于30%,并且作为第一着色涂膜的l*c*h颜色空间图中的色相角h值(h(x))与多层涂膜的l*c*h颜色空间图中的色相角h值(h(s))之间的差|h(x)-h(s)|为0至30。因此,该方法可以形成彩度高、暗度优异、因膜厚度变化而引起的颜色变化降低并且颜色不均匀性降低的多层涂膜。
81.当作为第一着色涂膜的l*c*h颜色空间图中的色相角h值(h(x))与多层涂膜的l*c*h颜色空间图中的色相角h值(h(s))之间的差|h(x)-h(s)|为30或更小时,所得多层涂膜具有减少的因膜厚度变化而引起的颜色变化和减少的颜色不均匀性。
82.对于作为第一着色涂膜的l*c*h颜色空间图中的色相角h值(h(x))与多层涂膜的l*c*h颜色空间图中的色相角h值(h(s))之间的差|h(x)-h(s)|的上限,没有特别限制,只要其为30或更小即可。上限优选为25或更小,更优选为20或更小,进一步优选为15或更小。对于作为第一着色涂膜的l*c*h颜色空间图中的色相角h值(h(x))与多层涂膜的l*c*h颜色空间图中的色相角h值(h(s))之间的差|h(x)-h(s)|的下限,没有特别限制,例如为0.1或更大,0.2或更大,0.3或更大,或者0.5或更大。此外,作为第一着色涂膜的l*c*h颜色空间图中的色相角h值(h(x))与多层涂膜的l*c*h颜色空间图中的色相角h值(h(s))之间的差|h(x)-h(s)|,其优选为0至25,更优选为0至20,并且进一步优选为0至15。从抑制因膜厚度变化而引起的颜色变化和抑制所得多层涂膜的颜色不均匀性的观点出发,作为第一着色涂膜的l*c*h颜色空间图中的色相角h值(h(x))与多层涂膜的l*c*h颜色空间图中的色相角h值(h(s))之间的差|h(x)-h(s)|优选在上述范围。
83.多层涂膜的l*c*h颜色空间图中的色相角h值(h(s))优选为225至315,更优选为240至310,并且进一步优选为255至305。
84.第一着色涂膜的l*c*h颜色空间图中的色相角h值(h(x))和多层涂膜的l*c*h颜色空间图中的色相角h值(h(s))可以通过调节用于形成多层涂膜的第一着色涂料(x)、第二着色涂料(y)和透明涂料中包含的颜料的类型和量来调节(通过小规模实验来进行)。
85.因此,基于本发明的多层涂膜形成方法可以适合应用于各种工业产品,特别是车体的外部板上形成多层涂膜。
86.下面,参考实施例和比较例更详细地描述本发明。然而,本发明不局限于这些实施例。应注意,“份”和“%”以质量为基准,并且膜厚度以固化涂膜为基准。实施例
87.[1]基材的制备用elecron gt-10阳离子电沉积涂料(商品名,由关西涂料株式会社制造,封端多异氰酸酯化合物用作环氧树脂聚胺类阳离子树脂中的固化剂)通过电沉积涂装经脱脂并且用磷酸锌处理的钢板((jisg3141,尺寸为400mm
×
300mm
×
0.8mm),使得涂膜基于固化涂膜具有20μm的膜厚度。将所得膜在170℃下加热20分钟以通过交联固化来形成电沉积涂膜。
[0088]
通过使用空气喷射用wp-523h n-5.5(商品名,关西涂料株式会社,水性中间涂料,所获得的中间涂膜具有55的明度l
*
)涂装在钢板上获得的电沉积涂膜以使得膜厚度基于固化涂膜为30μm,并且使其静置3分钟,随后在80℃下预热3分钟,从而形成未固化的中间涂
膜。该板被确定为基材。
[0089]
[2]涂料的制备含羟基的丙烯酸树脂(a)的制造制造例1将70.7份去离子水和0.52份aqualon kh-10(商品名,由dks co.,ltd.制造,乳化剂,活性成分97%)置于配有温度计、恒温器、搅拌器、回流冷凝器和滴液漏斗的反应容器中,然后在氮气流中混合并搅拌,然后加热至80℃。随后,将如下所述的整个单体乳液的1%和5份的6%过硫酸铵水溶液引入到反应器容器中,并将混合物在80℃下保持15分钟。此后,将剩余的单体乳液在3小时内滴加至保持在相同温度的反应容器。在完成逐滴添加后,将混合物熟化1小时。此后,在将40份5%的2-(二甲基氨基)乙醇水溶液逐渐添加至反应容器中的同时,将反应产物冷却至30℃并排出,同时通过100目尼龙布过滤,从而获得固体浓度为45%的含羟基的丙烯酸树脂乳液(a)。所获得的含羟基的丙烯酸树脂具有43mg koh/g的羟值和12mg koh/g的酸值。
[0090]
单体乳液:在搅拌下混合50份去离子水、10份苯乙烯、40份甲基丙烯酸甲酯、35份丙烯酸乙酯、3.5份甲基丙烯酸正丁酯、10份甲基丙烯酸2-羟乙酯、1.5份丙烯酸、1.0份aqualon kh-10和0.03份过硫酸铵,从而获得单体乳液。
[0091]
含羟基的聚酯树脂溶液(b)的制造制造例2将174份三羟甲基丙烷、327份新戊二醇、352份己二酸、109份间苯二甲酸和101份1,2-环己烷二甲酸酐放置在配备有温度计、恒温器、搅拌器、回流冷凝器和水分离器的反应容器中,并且将温度在3小时内从160℃升高至230℃。此后,将温度保持在230℃,同时用水分离器蒸馏出所产生的冷凝水,以使反应进行直至酸值达到3mgkoh/g或更小。将59份偏苯三酸酐添加至该反应产物,在170℃下进行加成反应,持续30分钟,然后冷却至50℃或更低。将与酸基等当量的2-(二甲基氨基)乙醇添加至其中以中和反应产物,并且然后逐渐添加去离子水,由此获得固体浓度为45%的含羟基的聚酯树脂溶液(b)。所获得的含羟基的聚酯树脂具有128mg koh/g的羟值、35mg koh/g的酸值和13000的重均分子量。
[0092]
颜料分散浆料(p-1)至(p-5)的制造制造例3将56份(固体含量:25份)在制造例2中获得的含羟基的聚酯树脂溶液(b)、5份氯化铜花青蓝g-314(商品名,酞菁蓝颜料,由sanyo color works ltd.制造)、1份paliogen blue l6482(商品名,还原类蓝颜料,由basf制造)、1.5份magenta brt-355-d(商品名,喹吖啶酮红色颜料,由basf制造)、1.5份hostaperm violet rl special(商品名,二噁嗪颜料,由clariant制造)、0.01份titanix jr-903(商品名,无机钛白色颜料,由tayca corporation制造)、0.01份raven 5000ultra iii beads(商品名,炭黑颜料,由columbian carbon co.制造)和5份去离子水混合,并用2-(二甲基氨基)乙醇将混合物调节至ph 8.0。随后,将所得混合物置于广口玻璃瓶中,并向其中添加作为分散介质的玻璃珠(直径:约1.3mm)。将瓶气密密封,并用涂料搅拌器将混合物分散30分钟,从而获得颜料分散浆料(p-1)。
[0093]
制造例4至7
除了施用下表1中所示的配方,重复制造例3的操作从而获得颜料分散浆料(p-2)至(p-5)。表1中所示的配方基于固体质量表示。
[0094]
表1
[0095]
g314(注释1):酞菁蓝颜料,商品名:氯化铜青蓝g-314,由sanyo color works ltd.制造l6482(注释2):还原类蓝色颜料,商品名:paliogen blue l6482,由basf制造rt355d(注释3):喹吖啶酮红色颜料,商品名:magenta b rt-355-d,由basf制造rl special(注释4):二噁嗪颜料,商品名:hostaperm violet rl special,由clariant制造jr903(注释5):无机钛白颜料,商品名:titanix jr903,由tayca corporation制造r5000(注释6):炭黑颜料,商品名:raven 5000ultra iii beads,由columbian carbon co.制造
[0096]
效应颜料分散液(r-1)至(r-5)的制造制造例8将4.1份(固体含量:3份)gx-180a(商品名,铝颜料膏,由asahi kasei metals corporation制造,金属含量:74%)、7.8份(固体含量:6份)gx-3108(商品名,铝颜料膏,由asahi kasei metals corporation制造,金属含量:77%)、2份(固体含量:2份)friend color d9452bl(商品名,着色铝颜料,由toyo aluminium k.k.制造)、将35份2-乙基-1-己醇、8份(固体含量:4份)下述含磷酸基团的树脂溶液(c)和0.2份2-(二甲基氨基)乙醇在搅拌混合容器中均匀混合,从而获得效应颜料分散液(r-1)。
[0097]
含磷酸基团的树脂溶液(c):将含有27.5份甲氧基丙醇和27.5份异丙醇的组合溶剂放置在配备有温度计、恒温器、搅拌器、回流冷凝器和滴液漏斗的反应容器中,并且加热至110℃。将包含25份苯乙烯、27.5份甲基丙烯酸正丁酯、20份丙烯酸异硬脂酯(商品名,由osaka organic chemical industry ltd.制造,丙烯酸支链高级烷基酯)、7.5份丙烯酸4-羟基丁酯、15份下述含磷酸基团的可聚合单体、12.5份2-甲基丙烯酰氧基乙酸磷酸酯、10份异丁醇和4份过氧辛酸叔丁酯的混合物(121.5份)在4小时内添加至组合溶剂中。向其中进一步滴加包含0.5份过氧辛酸叔丁酯和20份异丙醇的混合物持续1小时,然后在搅拌下熟化1小时,从而获得固体浓度为50%的含磷酸基团的树脂溶液(c)。该树脂由于磷酸基团而具有83mgkoh/g的酸值,29mgkoh/g的羟值和10000的重均分子量。
[0098]
含磷酸基团的可聚合单体:将57.5份单丁基磷酸酯和41份异丁醇放置在配备有温
度计、恒温器、搅拌器、回流冷凝器和滴液漏斗的反应容器中,并且加热至90℃。然后在2小时内滴加42.5份甲基丙烯酸缩水甘油酯,然后在搅拌下熟化1小时。此后,添加59份异丙醇,由此获得具有50%固体浓度的含磷酸基团的可聚合单体溶液。所得单体的基于磷酸基团的酸值为285mgkoh/g。
[0099]
制造例9至12除了施用下表2中所示的配方以外,重复制造例8的操作从而获得效应颜料分散液(r-2)至(r-5)。表2中所示的配方基于固体质量表示。
[0100]
表2
[0101]
第一着色涂料(x-1)至(x-6)的制造制造例13将70.02份在制造例3中获得的颜料分散浆料(p-1)、57.1份在制造例8中获得的效应颜料分散液(r-1)、44.4份(固体含量:20份)在制造例1中获得的含羟基的丙烯酸树脂乳液(a)、60份(固体含量:21份)ucoat ux-8100(商品名,氨基甲酸酯乳液,由sanyo chemical industries,ltd.制造,固体含量:35%)和37.5份(固体含量:30份)cymel 325(商品名,三聚氰胺树脂,由nihon cytec industries inc.制造,固体含量:80%)均匀混合。随后,将uh-752(商品名,由adeka corporation制造,增稠剂)、2-(二甲基氨基)乙醇和去离子水添加至所获得的混合物中,从而获得具有8.0的ph、25%的涂料固体含量和3000mpa
·
s的粘度的第一着色涂料(x-1),所述粘度是使用b型粘度计在20℃下以6rpm的旋转速度测量的。
[0102]
制造例14至18除了施用下表3中所示的配方以外,重复制造例13的操作从而获得粘度为3000mpa
·
s的第一着色涂料(x-2)至(x-6),所述粘度是使用b型粘度计在20℃下以6rpm的旋转速度测量的。
[0103]
第一着色涂膜的评估用cr-400(商品名,由konica minolta,inc.制造)评估由获得的第一着色涂料(x-1)至(x-6)形成的第一着色涂膜的明度l
*
和色相角h值(h(x))。通过使用迷你钟(mini bell)型旋转静电涂装器在20℃的机房温度和75%的湿度下将第一着色涂料(x-1)至(x-6)中的每一种涂装至在上述[1]部分中获得的基材上,使得基于固化涂膜的膜厚度为8μm,使膜在室温下静置3分钟,然后在热空气循环烘箱中在140℃下加热膜30分钟,从而获得第一着色涂膜。表3还示出了评估结果。
[0104]
表3
[0105]
含羟基的丙烯酸树脂乳液(d)的制造制造例19将130份去离子水和0.52份aqualon kh-10置于配备有温度计、恒温器、搅拌器、回流冷凝器和滴液漏斗的反应容器中,并且在氮气流中搅拌并混合,然后加热至80℃。随后,将下述单体乳液(1)的总量的1%和5.3份的6%过硫酸铵水溶液置于反应容器中并在80℃下保持15分钟。此后,将剩余的单体乳液(1)在3小时内逐滴添加至保持在相同温度的反应容器中。在完成逐滴添加后,将混合物熟化1小时。随后,在1小时内滴加以下单体乳液(2),然后熟化1小时。此后,在将40份5%二甲基乙醇胺水溶液逐渐添加至反应容器中的同时,将反应产物冷却至30℃并排出,同时通过100目尼龙布过滤,从而获得固体浓度为30%的含羟基的丙烯酸树脂乳液(d)。所获得的含羟基的丙烯酸树脂具有25mg koh/g的羟值和33mg koh/g的酸值。
[0106]
单体乳液(1):将42份去离子水、0.72份aqualon kh-10、2.1份亚甲基双丙烯酰胺、2.8份苯乙烯、16.1份甲基丙烯酸甲酯、28份丙烯酸乙酯和21份丙烯酸正丁酯在搅拌下进行混合,由此获得单体乳液(1)。
[0107]
单体乳液(2):将18份去离子水、0.31份aqualon kh-10、0.03份过硫酸铵、5.1份甲基丙烯酸、5.1份2-羟乙基丙烯酸酯、3份苯乙烯、6份甲基丙烯酸甲酯、1.8份丙烯酸乙酯和9份丙烯酸正丁酯在搅拌下进行混合,由此获得单体乳液(2)。
[0108]
含羟基的聚酯树脂溶液(e)的制造制造例20将109份三羟甲基丙烷、141份1,6-己二醇、126份六氢邻苯二甲酸酐和120份己二酸置于配有温度计、恒温器、搅拌器、回流冷凝器和水分离器的反应容器中,并且在3小时内加热以将温度从160℃升高到230℃,随后在230℃下缩合反应4小时。随后,为了将羧基添加至所得的缩合反应产物中,还添加38.3份偏苯三酸酐,并且使得混合物在170℃下反应30分钟。然后用2-乙基-1-己醇稀释反应产物,从而获得固体浓度为70%的含羟基的聚酯树脂溶液(e)。所获得的含羟基的聚酯树脂具有150mg koh/g的羟值、46mg koh/g的酸值和6400的重均分子量。
[0109]
颜料分散浆料(p-6)至(p-9)的制造制造例21
将35.7份(固体含量:25份)在制造例20中获得的含羟基的聚酯树脂溶液(e)、7.5份氯化铜青蓝g-314(商品名,酞菁蓝颜料,由sanyo color works ltd.制造)、0.01份raven 5000ultra iii beads(商品名,炭黑颜料,由columbian carbon co.制造)、5份去离子水混合,并用2-(二甲基氨基)乙醇将混合物调节至ph 8.0。随后,将所得混合物置于广口玻璃瓶中,并且添加作为分散介质的玻璃珠(直径:约1.3mm)。将瓶气密密封,并用涂料振荡器将混合物分散30分钟,从而获得颜料分散浆料(p-6)。
[0110]
制造例22至24除了施用下表4中所示的配方以外,重复制造例21的操作从而获得颜料分散浆料(p-7)至(p-9)。表4中所示的配方基于固体质量表示。
[0111]
表4
[0112]
效应颜料分散液(r-6)至(r-7)的制造制造例25将2份xirallic t60-23 wnt galaxy blue(商品名,氧化钛涂装的氧化铝氧化物片,由merck&co.,inc.制造)、10份2-乙基-1-己醇、4份(固含量:2份)含磷酸基团的树脂溶液(c)和0.1份2-(二甲基氨基)乙醇在搅拌混合容器中均匀混合,从而获得效应颜料分散液(r-6)。
[0113]
制造例26将2份pyrisma t40-23 sw color space blue(商品名,氧化钛涂装的云母片,由merck&co.,inc.制造)、10份2-乙基-1-己醇、4份(固含量:2份)含磷酸基团的树脂溶液(c)和0.1份2-(二甲基氨基)乙醇在搅拌混合容器中均匀混合,从而获得效应颜料分散液(r-7)。
[0114]
第二着色涂料(y-1)至(y-6)的制造制造例27将48.21份在制造例21中获得的颜料分散浆料(p-6)、16.1份在制造例25中获得的效应颜料分散液(r-6)、73.3份(固体含量:22份)在制造例19中获得的含羟基的丙烯酸树脂乳液(d)、60份(固体含量:21份)ucoat ux-8100(商品名,氨基甲酸酯乳液,由sanyo chemical industries,ltd.生产,固体含量:35%)和37.5份(固体含量:30份)的cymel 325(商品名:三聚氰胺树脂,由nihon cytec industries inc.制造,固体含量:80%)均匀混合。随后,将uh-752(商品名,由adeka corporation制造,增稠剂)、2-(二甲基氨基)乙醇和去离子水添加至所获得的混合物中,从而获得具有8.0的ph、25%的涂料固体含量和3000mpa
·
s的粘度的第二着色涂料(y-1),所述粘度如在20℃下和以6rpm的旋转速度用b型粘度计测量的。
[0115]
制造例28至32除了施用下表5中所示的配方以外,重复制造例27的操作从而获得粘度为
3000mpa
·
s的第二着色涂料(y-2)至(y-6),所述粘度是使用b型粘度计在20℃下和以6rpm的旋转速度测量的。
[0116]
第二着色涂膜的评估用uv-2700(商品名,由shimadzu corporation制造)评估以上获得的第二着色涂料(y-1)至(y-6)的第二着色涂膜的离型膜,并且获得400nm以上且700nm以下的波长处的透光率。第二着色涂膜的离型膜通过以下方式获得:将第二着色涂料(y-1)至(y-6)中的每一种涂装至聚丙烯板,使得通过使用迷你钟型旋转静电涂装器在200℃的室温和75%的湿度下使膜在室温下静置3分钟,然后在热空气循环烘箱中在140℃下加热膜30分钟,然后剥离,基于固化涂膜的膜厚度为10μm。表5还示出了评估结果。
[0117]
表5
[0118]
[iii]测试板的制备测试板的制备实施例1至8和比较例1至4用第一着色涂料(x)涂装在20℃的机房温度和75%的湿度下用迷你钟型旋转静电涂装器将上述[2]部分中制备的第一着色涂料(x-1)至(x-6)中的一种涂装至上述[1]部分中制备的基材上,使得涂膜基于固化涂膜具有8μm的厚度。然后使涂膜在室温下静置3分钟,从而获得未固化的第一着色涂膜。
[0119]
用第二着色涂料(y)涂装在20℃的机房温度和75%的湿度下用迷你钟型旋转静电涂装器将上述[2]部分中制备的第二着色涂料(y-1)至(y-6)中的一种涂装至未固化的第一着色涂膜,使得涂膜基于固化涂膜具有10μm的厚度。使涂膜在室温下静置3分钟,然后在80℃下预热3分钟,从而获得未固化的第二着色涂膜。
[0120]
用透明涂料(z)涂装在20℃的机房温度和75%的湿度下用迷你钟型旋转静电涂装器将透明涂料(z)(magicron kino-1210,商品名,由关西涂料株式会社制造,丙烯酸树脂,环氧可固化的溶剂型顶涂透明涂料)涂装至未固化的第二着色涂膜,使得涂膜基于固化涂膜具有35μm的膜厚度。然后使涂膜在室温下静置7分钟;然后在热空气循环烘箱中在140℃下加热30分钟以通过同时干燥固化由中间涂膜、第一着色涂膜、第二着色涂膜和透明涂膜组成的多层涂膜,从
而制备测试板1。
[0121]
以与制备测试板1相同的方式获得测试板2,但将基于固化涂膜的第二着色涂膜的膜厚度改变为9μm。
[0122]
以与制备测试板1相同的方式获得测试板3,但将基于固化涂膜的第二着色涂膜的膜厚度改变为11μm。
[0123]
涂膜的评估通过以下方法评估以上述方式获得的测试板上的涂层膜的外观。表6和表7示出了结果。
[0124]
色相角h值(h(s))用cr-400(商品名,由konica minolta,inc.制造)测量每个测试板1的色相角h值。
[0125]
彩度c
*
值用cr-400(商品名,由konica minolta,inc.制造)测量每个测试板1的c
*
值。较高的c
*
值表示较高程度的彩度。55或更高的值被认为是可接受的(合格)。
[0126]
暗度c
*
/l
*
值通过用cr-400(商品名,由konica minolta,inc.制造)测量彩度c
*
值和明度l
*
值,并且将c
*
值除以l
*
值(c
*
值/l
*
值)来评估每个测试板1。c
*
值/l
*
值的较大值表示较高程度的暗度。1.8或更高的值被认为是可接受的(合格)。
[0127]
因膜厚度变化而引起的颜色变化用cr-400(商品名,由konica minolta,inc.制造)评估每个测试板2和每个测试板3的δe
*
值。根据下式计算δe
*
值。较小的δe
*
值表示因膜厚度变化而引起的颜色变化(较小)越良好。1.5或更小的值被认为是可接受的(合格)。δe={(δl
*
)2 (δa
*
)2 (δb
*
)2}
1/2
δl
*
:测试板2与测试板3之间的l
*
值的差,δa
*
:测试板2与测试板3之间的a
*
值的差,δb
*
:测试板2与测试板3之间的b
*
值的差。
[0128]
颜色不均匀性目视评估每个测试板的颜色不均匀性。s和a被认为是可接受的。s:几乎没有观察到颜色不均匀性,并且涂膜具有极好的外观。a:轻微观察到颜色不均匀性,但涂膜具有优异的外观。b:观察到颜色不均匀,并且涂膜具有稍微差的外观。c:大量地观察到颜色不均匀性,并且涂膜具有差的外观。
[0129]
色相差:|h(x)-h(s)|计算第一着色涂膜的l*c*h颜色空间图中的色相角h值(h(x))与多层涂膜的l*c*h颜色空间图中的色相角h值(h(s))之间的差(即|h(x)-h(s)|)。
[0130]
表6
[0131]
表7
再多了解一些
本文用于企业家、创业者技术爱好者查询,结果仅供参考。