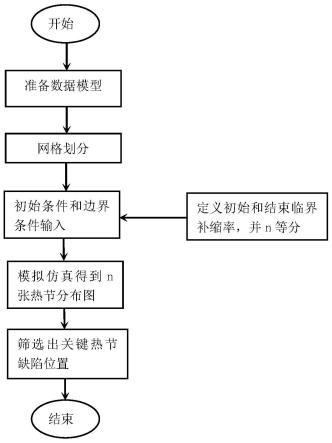
1.本发明涉及铸造,具体涉及一种基于铸造仿真软件预测实际铸件凝固缩孔缺陷的方法。
背景技术:
2.铸造过程计算机模拟仿真(简称cae)是学科发展的前沿领域,经过数十年的发展,诞生出了以德国magma为代表的优秀铸造模拟仿真软件;铸造生产正在由凭经验走向科学理论指导,指导工艺人员在实际铸造前对铸件可能出现的缺陷预测,在浇注前就采取措施以提升铸件质量,降低后期反复试模、修模成本。
3.但是金属凝固,尤其是宽结晶范围的合金凝固是涉及物理、流体、传热、冶金、力学等因素的复杂过程,以最为常见的凝固缩孔缺陷为例,即便是优秀的magma铸造模拟仿真软件也只能预测出可能产生的缺陷位置,实际铸造得到的铸件其缺陷可能有,也可能没有;同样的,作为铸造模拟仿真工程师经常碰到这样的困惑:模拟仿真分析出的热节或缩孔体积大小与其实际产生可能性、风险性并没有直接的关系(并非热节或缩孔体积越大,凝固缺陷出现可能性越大,风险越高),即存在这样的情况:热节或缩孔体积大的有可能实际铸件凝固缺陷风险性低,而热节或缩孔体积虽然小的位置,反而实际铸造出的铸件凝固缺陷风险性高。
4.另外,根据约翰
·
坎贝尔教授在《铸造原理》第二版中提到的,针对铸件凝固补缩,至少存在着五种机制在凝固过程中产生作用,分别是液态补缩、浆态补缩、枝晶间补缩、爆发时补缩、固态补缩,但并非这五种补缩机制在单一铸造中都会起作用。由此可见实际铸件凝固补缩的复杂性、阶段性、多样性的特征,但目前的模拟仿真软件所分析出的热节或缩孔结果都是在某一特定临界凝固补缩固相率条件下的结果,因此具有一定的片面性,并不能客观反映真实的铸造过程。
5.如果在实际浇注前,对模拟仿真分析出的所有凝固缩孔缺陷都进行优化、规避,无疑也会增加许多不必要的成本。因此,亟需一种在铸件开模前期就能基于模拟仿真软件精准预测铸件凝固缩孔缺陷的方法。
技术实现要素:
6.本发明的目的是提出一种基于铸造仿真软件预测实际铸件凝固缩孔缺陷的方法,以更精准的预测实际铸件凝固缩孔缺陷。
7.本发明所述的一种基于铸造仿真软件预测实际铸件凝固缩孔缺陷的方法,包括以下步骤:
8.s1:准备铸造模拟仿真分析所需的数据模型;
9.s2:将数据模型导入铸造仿真软件,进行网格剖分;
10.s3:设置材料物性参数和边界条件;
11.s4:定义初始临界补缩率f1和结束临界补缩率fn,在f1至fn之间等间隔取值,获得
f1、f2……fn
这n个临界补缩率;
12.s5:将f1、f2……fn
这n个临界补缩率分别带入到s3中进行模拟仿真,从后处理结果中得到同一铸件的n张热节分布图;
13.s6:将同一铸件的n张热节分布图进行比较,筛选出每张热节分布图中都存在热节缺陷的位置作为关键热节缺陷位置。
14.可选的,所述数据模型包括铸造模拟仿真分析所需的所有stl格式文件。
15.可选的,所述铸造仿真软件为magma软件。
16.可选的,f1、f2……fn
均为0到100%之间的数值。
17.可选的,(f
n-f1)/n≤5%。
18.本发明提出的方法可以尽可能准确的定位那些在实际浇注凝固过程中真正会产生凝固缩孔缺陷的位置,排除掉那些在实际浇注凝固过程中产生可能性极低的缺陷(虽然模拟仿真分析出其存在有热节缺陷),进而让铸造企业在铸件开模前期有针对性的进行优化,降低企业生产制造成本。
19.本发明提出的方法有以下有益效果:
20.1、弥补传统方法弊端,找到一套行之有效的方法评估模拟仿真分析出的凝固热节风险度高低,弥补了传统方法以模拟仿真热节或缩孔体积大小作为风险度高低的评估方法的弊端;
21.2、锁定缺陷准确度高,通过实际铸件开发案例,应用本发明所述的方法进行实际验证,凝固缺陷锁定准确度极高;
22.3、降本增效、节创价值高,基于本发明所述的方法,企业不必花费更多时间、金钱、精力去解决掉模拟仿真分析出的所有凝固热节缺陷,而是对真正风险高的地方有的放矢,既缩短了开发周期,又降低了生产制造成本。
附图说明
23.图1为具体实施方式中所述的基于铸造仿真软件预测实际铸件凝固缩孔缺陷的方法的流程图;
24.图2为具体实施方式中仿真得到的9张热节分布图;
25.图3为具体实施方式中所述的关键热节缺陷位置图;
26.图4为具体实施方式中所述的实际铸件内部凝固缩孔缺陷扫描结果。
具体实施方式
27.下面结合附图对本发明作进一步说明。
28.以某司开发的一款低压铸造三口集成排气缸盖为例进行说明,一种基于铸造仿真软件预测实际铸件凝固缩孔缺陷的方法,如图1所示,其步骤如下:
29.s1:准备铸造模拟仿真分析所需的数据模型,具体应包括实现完整铸造模拟仿真分析所需所有stl格式文件,如铸件、浇注系统、模具、砂芯和冷却管路等;
30.s2:将数据模型导入magma软件,进行网格剖分;
31.s3:按现场实际设置材料物性参数和边界条件;
32.s4:定义初始临界补缩率f1和结束临界补缩率fn,在f1至fn之间等间隔取值,获得
f1、f2……fn
这n个临界补缩率,在本实施例中,这里f1=30%,fn=70%,将30%至70%按照5%的间隔进行分解,得到30%、35%
……
70%这9个临界补缩率;
33.s5:将30%、35%
……
70%这9个临界补缩率分别带入到s3中进行模拟仿真,从后处理结果中得到如图2所示的同一铸件的9张热节分布图;
34.s6:将同一铸件的9张热节分布图进行比较,筛选出每张热节分布图中都存在热节缺陷的位置作为关键热节缺陷位置,得到如图3所示的关键热节缺陷位置图。
35.为了与实际铸造出的铸件凝固缺陷进行比对,利用工业ct机对实际铸件进行内部质量断层全扫描,实际铸件内部凝固缩孔缺陷扫描结果如图4所示,这与图3所示的经过筛选的模拟仿真结果高度一致。
36.通过上述的关键热节缺陷位置图,能够帮助工艺人员锁定那些实际铸造过程最有可能产生凝固缩孔缺陷的位置,针对性地指导结构或模具优化,并可以通过上述的基于铸造仿真软件预测实际铸件凝固缩孔缺陷的方法进一步进行验证方案的有效性,从而让问题在前期便暴露并加以解决。
37.在具体实施时,f1、f2……fn
均为0到100%之间的数值,f1大于0,fn小于100%。
38.在具体实施时,为保障输出足够数量的热节分布图,应使s4中的临界补缩率的取值间隔满足:(f
n-f1)/n≤5%。
39.在具体实施时,上述的基于铸造仿真软件预测实际铸件凝固缩孔缺陷的方法适用于重力铸造、低压铸造等这些凝固时间较长的铸造工艺方式,不适用于高压铸造等快速凝固冷却的特种铸造方式。
40.在具体实施时,上述的基于铸造仿真软件预测实际铸件凝固缩孔缺陷的方法适用于宽结晶范围的有色合金,如铝合金。
41.在具体实施时,采用的铸造仿真软件不限于magma软件,还可以采用其他的铸造仿真软件,例如procast、ekk和novacast。
再多了解一些
本文用于企业家、创业者技术爱好者查询,结果仅供参考。