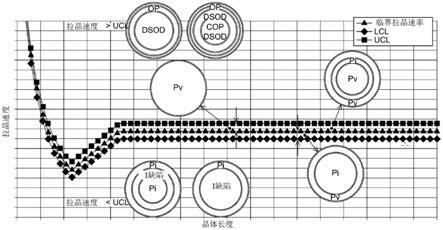
使用连续柴可斯基方法生长氮掺杂单晶硅锭的方法以及通过此方法生长的单晶硅锭
1.相关申请案的交叉参考
2.本技术案主张两者在2019年9月13日申请的第16/569,949号及第16/570,010号美国非临时专利申请案的优先权,且所述申请案的全部公开内容特此以其全文引用的方式并入。
技术领域
3.本公开的领域涉及一种使用连续柴可斯基方法生长单晶硅锭的方法及一种通过此方法生长的单晶硅锭。
背景技术:
4.单晶硅(其是用于制造半导体电子组件的大多数工艺的起始材料)通常由柴可斯基(“cz”)方法制备。在此方法中,将多晶硅装料到坩埚中且熔融多晶硅,使一种晶与熔融硅接触,且通过缓慢提取来生长单晶体。在完成颈部的形成之后,通过(例如)降低拉晶速率及/或熔体温度来扩大晶体的直径,直到达到所要或目标直径。接着,通过控制拉晶速率及熔体温度同时补偿降低熔体液位来生长具有大致恒定直径的晶体的圆柱形主体。在生长工艺将近结束时但在坩埚清空熔融硅之前,晶体直径通常经逐渐减小以形成呈端锥的形式的尾端。端锥通常通过提高拉晶速率及供应到坩埚的热来形成。当直径变得足够小时,晶体与熔体分离。
5.柴可斯基生长技术包含分批柴可斯基方法及连续柴可斯基方法。在分批cz中,将单个多晶装料装载到坩埚中,单一装料足以生长单晶硅锭,此后坩埚基本上耗尽硅熔体。在连续柴可斯基(ccz)生长中,可将多晶硅连续或周期性添加到熔融硅以在生长工艺期间补充熔体,因此,可在生长工艺期间可从单个坩埚拉制多个锭。
6.为实施ccz工艺,传统分批柴可斯基生长室及设备经修改以包含用于在不负面影响生长锭的性质的情况下依连续或半连续方式进给额外多晶硅到熔体的构件。随着种晶从熔体连续生长,将固体多晶硅(例如粒状多晶硅)添加到熔体以补充熔体。添加到熔体的额外固体多晶硅的进给速率通常经控制以维持工艺参数。为减少此补充活动对同时晶体生长的负面影响,传统石英坩埚通常经修改以提供其中补给添加材料的外或环形熔融区及从其拉制硅锭的内生长区。这些区彼此流体流动连通。
7.现代微电子装置的不断缩减大小给基本上由原生微缺陷的大小及分布确定的硅衬底的质量带来挑战性限制。形成于由柴可斯基(cz)工艺及浮区(fz)工艺生长的硅晶体中的大多数微缺陷是硅的本质点缺陷的聚结物——空位及自身间隙(或简称间隙)。
8.一系列研究已证实间隙聚结物以两种形式存在:球状间隙丛集,称为b漩涡缺陷(或b缺陷);及错位环,称为a漩涡缺陷(或a缺陷)。后来发现的空位聚结物(称为d缺陷)已被识别为八面体空隙。沃罗科夫(voronkov)基于晶体生长条件来提供硅晶体中观察到的微缺陷分布的被广泛接受解释。根据沃罗科夫模型或理论,熔体/晶体界面附近的温度场驱动点
缺陷的重组以提供其从熔体/晶体界面(其中点缺陷以其相应平衡浓度存在)扩散到晶体块中的驱动力。通过扩散及对流两者的点缺陷的运输与其重组之间的相互作用确定超出远离界面的短距离(称为重组长度)的点缺陷浓度。通常,空位浓度与超出重组长度的间隙浓度(称为过量点缺陷浓度)之间的差保持基本上远离晶体的横向表面固定。在快速拉晶中,除靠近充当点缺陷的槽或源的晶体的横向表面的区域之外,由其超出重组长度扩散所致的点缺陷的空间再分布一般不重要。因此,如果超出重组长度的过量点缺陷浓度是正的,那么空位保持过量,且聚结以在较低温度形成d缺陷。如果过量点缺陷浓度是负的,那么间隙保持主要点缺陷,且聚结以形成a缺陷及b缺陷。如果过量点缺陷浓度低于某一检测阈值,那么不形成可检测微缺陷。因此,通常,原生微缺陷的类型仅由超出重组长度确定的过量点缺陷浓度确定。确定过量点缺陷浓度的工艺称为初始结合且主要点缺陷种类称为结合主要点缺陷。结合点缺陷的类型由拉晶速率(v)与界面附近的轴向温度梯度的量值(g)的比率确定。在较高v/g处,点缺陷的对流主导其扩散,且空位保持结合主要点缺陷,因为界面处的空位浓度高于间隙浓度。在较低v/g处,扩散主导对流以允许快速扩散间隙随着主要点指向结合。在接近其临界值的v/g处,两个点缺陷以非常低及相当的浓度结合以彼此相互消除且因此抑制任何微缺陷在较低温度的潜在形成。所观察的空间微缺陷分布通常可由g的径向非均匀性及v的轴向变动引起的v/g变动解释。径向微缺陷分布的显著特征是通过氧与相对较低结合空位浓度的区域中的空位的相互作用形成的氧化物微粒(在略高于临界v/g的小v/g范围内)。这些微粒形成可由热氧化显露为osf(氧化诱发迭差)环的窄空间带。通常,osf环标记空位主导及间隙主导的相邻晶体区域之间的边界,称为v/i边界。
9.然而,在许多现代工艺中,依较低速率生长的cz晶体中的微缺陷分布受晶体块中的点缺陷的扩散(包含由晶体的横向表面诱发的扩散)影响。因此,cz晶体中的微缺陷分布的准确量化优选地结合轴向及径向的2维点缺陷扩散。仅量化点缺陷浓度场可定性地捕获cz晶体中的微缺陷分布,因为所形成的微缺陷的类型由其直接确定。然而,为更准确量化微缺陷分布,需要捕获点缺陷的聚结。通常,通过解耦合点缺陷的初始结合与微缺陷的后续形成来量化微缺陷分布。此方法忽略成核区域附近的主要点缺陷从较高温度的区域(其中微缺陷密度可忽略)到较低温度的区域(其中微缺陷以较高密度存在且消耗点缺陷)的扩散。替代地,基于预测晶体中的每个位置处的微缺陷群体的大小分布的严格数值模拟从数值上看很昂贵。
10.空位与间隙主导材料之间的转变发生于v/g的临界值(其当前约为2.5
×
10-5
cm2/sk)处。如果v/g的值超过临界值,那么空位是主要本质点缺陷,且其浓度随v/g增大而增大。如果v/g的值小于临界值,那么硅自身间隙是主要本质点缺陷,且其浓度随v/g减小而增大。因此,工艺条件(例如生长速率(其影响v)及热区配置(其影响g))可经控制以确定单晶硅内的本质点缺陷是否将主要为空位(其中v/g一般大于临界值)或自身间隙(其中v/g一般小于临界值)。
11.聚结缺陷形成一般发生于两个步骤中。首先,发生缺陷“成核”,其是本质点缺陷在给定温度过饱和的结果;如果高于此“成核阈值”温度,那么本质点缺陷保持可溶于硅晶格中。聚结本质点缺陷的成核温度大于约1000℃。
12.一旦达到此“成核阈值”温度,那么本质点缺陷聚结,即,发生这些点缺陷从硅晶格的“固溶体”析出。只要其中存在本质点缺陷的锭的部分的温度保持高于第二阈值温度(即,“扩散率阈值”),那么本质点缺陷将继续通过硅晶格扩散。如果低于此“扩散率阈值”温度,那么本质点缺陷无法再在商业上可行的时段内移动。
13.当锭保持高于“扩散率阈值”温度时,空位或间隙本质点缺陷通过硅晶格扩散到其中已分别存在聚结空位缺陷或间隙缺陷的位点以引起给定聚结缺陷的大小生长。生长发生的原因事故这些聚结缺陷位点基本上充当“槽”以由于聚结的更有利能态而吸引及收集本质点缺陷。
14.空位型缺陷经辨识为例如d缺陷、流动图案缺陷(fpd)、栅极氧化物完整性(goi)缺陷、晶体导致微粒(cop)缺陷、晶体导致光点缺陷(lpd)及由红外光散射技术(例如扫描红外线显微术及激光断层扫描)观察到的特定类别的体缺陷的可观察晶体缺陷的来源。氧或二氧化硅的丛集还存在于过量空位的区域中。一些这些丛集保持较小且相对无应变以基本上对由此硅制备的大部分装置无害。一些这些丛集足够大以充当环氧化诱发迭差(oisf)的核。可推测此特定缺陷由存在过量空位催化的先前有核氧聚结物促进。在存在适度空位浓度的情况下,氧化物丛集主要形成于低于1000℃的cz生长中。
15.与自身间隙有关的缺陷相对较少研究。其一般被视为低密度的间隙型错位环或网络。此类缺陷不造成栅极氧化物完整性故障(重要晶片性能指标),但其被广泛认为是通常与电流泄漏问题相关联的其它类型的装置故障的原因。
16.据此应注意,一般来说,硅晶格中呈间隙形式的氧通常被视为硅的点缺陷而非本质点缺陷,而硅晶格空位及硅自身间隙(或简称间隙)通常被视为本质点缺陷。因此,基本上所有微缺陷一般可被描述为聚结点缺陷,而d缺陷(或空隙)及a缺陷及b缺陷(即,间隙缺陷)可更具体描述为聚结本质点缺陷。通过吸收空位来形成氧丛集;因此,氧丛集可被视为空位及氧两者的聚结物。
17.应进一步注意,柴可斯基硅中的此空位及自身间隙聚结点缺陷的密度在历史上已在约1
×
103/cm3到约1
×
107/cm3的范围内,而氧丛集的密度在约1
×
108/cm3到约1
×
10
10
/cm3之间变动。因此,聚结本质点缺陷对于装置制造商具有日益剧增的重要性,因为此类缺陷会严重影响复杂及高度集成电路的生产中的单晶硅材料的良率潜力。
18.鉴于上文,在许多应用中,硅晶体(其随后被切割成硅晶片)的部分或全部优选地基本上无这些聚结本质点缺陷。迄今为止,已报告用于生长基本上无缺陷硅晶体的若干方法。一般来说,所有这些方法涉及控制比率v/g以确定存在于生长cz单晶硅晶体中的本质点缺陷的初始类型及浓度。然而,另外,此类方法可涉及控制晶体的后续热历程以允许延长扩散时间以抑制晶体内的本质点缺陷的浓度且因此基本上限制或避免晶体的部分或全部中形成聚结本质点缺陷。(见(例如)第6,287,380号、第6,254,672号、第5,919,302号、第6,312,516号及第6,328,795号美国专利,所述专利的全部内容以引用的方式并入本文中。)然而,替代地,此类方法可涉及快速冷却硅(rcs)生长工艺,其中接着控制晶体的后续热历程以通过目标成核温度快速冷却晶体的至少一部分以控制聚结本质点缺陷形成于所述部分中。这些方法中的一或两者还可包含允许生长晶体的至少一部分以保持高于成核温度达一延长时段以在通过目标成核温度快速冷却晶体的此部分之前减小本质点缺陷的浓度以因此基本上限制或避免晶体内形成聚结本质点缺陷。(见(例如)第2003/0196587号美国公开专利申请案,所述案的全部内容以引用的方式并入本文中。)此外,已开发通过同时控制固化锭的冷却速率及界面附近的轴向温度梯度(g)的径向变动来减少或消除从锭的中心到边
缘的聚结点缺陷的方法。(见(例如)第8,673,248号美国专利,所述专利的全部内容以引用的方式并入本文中。)
19.满足缺乏聚结点缺陷(例如晶体导致微坑(cop))的制造商要求的抛光硅晶片可指称中性硅或完美硅。完美硅晶片优选地在许多半导体应用中作为替代(例如)较高外延沉积晶片的较低成本抛光晶片。在过去20年期间,许多硅晶片供货商已开发200mm及300mm直径两者的无缺陷及无cop晶片产品以主要销售给市场内对成本压力通常更敏感的存储器(dram/nand/flash)市场。从光点散射(lls)与栅极氧化物强度(goi)的可接受位准来说,随着客户应用装置节点缩小,可接受缺陷率的工业标准已在此期限内演进。例如,工业无cop规格已一度在不超过0.12um大小处小于数百。更近标准需要在不超过0.026um大小处小于20个cop以符合完美硅。作为另一实例,mos晶体管中的goi的过去标准是≤8mv(b模式)处95%。当前,规格移动到10mv到12mv处的99%(d模式)。除此要求之外,需要随装置节点缩小而改进通常由bmd密度(体微缺陷)及bmd大小分布测量的跨晶片的径向氧析出以避免处理期间的衬底滑移或会影响装置微影期间的图案化叠加的翘曲。随着这些规格收紧(lls、goi、bmd均匀性等等),无缺陷及cop硅生长的控制窗已显著缩小以显著降低工艺的晶体产量。这是因为可接受带结构窗(其可直接转化成工艺操作窗)已与规格随时间变换。
20.本节希望向读者介绍可与下文将描述及/或主张的本公开的各种方面有关的各种技术方面。可认为此讨论有助于向读者提供背景信息以促进本公开的各种方面的较佳理解。因此,应理解,这些陈述应鉴于此解读,而非被承认为现有技术。
技术实现要素:
21.本公开的方面是针对一种通过连续柴可斯基方法制备单晶硅锭的方法,所述方法包括:将多晶硅的初始装料添加到坩埚,所述初始装料进一步包括氮源;加热包括多晶硅的所述初始装料及所述氮源的所述坩埚以引起硅熔体形成于所述坩埚中,所述硅熔体包括熔融硅的初始容积且具有初始熔体高度液位;使硅种晶与硅熔体接触;抽取所述硅种晶以生长颈部部分,其中在所述颈部部分的生长期间依颈部部分拉晶速率抽取所述硅种晶,且其中所述颈部部分具有至少约1
×
10
13
个原子/cm3的颈部部分氮浓度;抽取所述硅种晶以邻近于所述颈部部分生长向外扩口晶种锥,其中在所述向外扩口晶种锥的生长期间依晶种锥拉晶速率抽取所述硅种晶,且其中所述向外扩口晶种锥具有至少约1
×
10
13
个原子/cm3的向外扩口晶种锥氮浓度;及抽取所述硅种晶以邻近于所述向外扩口晶种锥生长所述单晶硅锭的主体,其中在所述单晶硅锭的所述主体的生长期间,所述硅熔体包括熔融硅的容积及熔体高度液位,且其中所述单晶硅锭的所述主体具有至少约1
×
10
13
个原子/cm3的主体氮浓度;其中所述单晶硅锭的所述主体依初始可变主体拉晶速率及恒定主体拉晶速率生长,其中所述单晶硅锭的所述主体在所述单晶硅锭的所述主体的长度的小于约20%内依所述初始可变主体拉晶速率生长且在生长期间在所述单晶硅锭的所述主体的所述长度的至少约30%内依所述恒定主体拉晶速率生长;且其中将多晶硅连续进给或周期性进给到所述坩埚以借此补充熔融硅的容积且借此在所述单晶硅锭的所述主体的生长期间维持所述坩埚中的熔体高度液位,且将所述氮源连续进给或周期性进给到所述坩埚以借此补充氮量。
22.在另一方面中,本公开是针对一种单晶硅锭,其具有主体部分,其中所述主体部分具有圆周边缘、平行于所述圆周边缘具有轴向长度的中心轴线及从所述中心轴线延伸到所
述圆周边缘的半径,其中在所述单晶硅锭的所述主体的轴向长度的至少60%、所述单晶硅锭的所述主体的轴向长度的至少70%或所述单晶硅锭的所述主体的轴向长度的至少80%上从所述主体的任何部分切割的晶片以通过射哥蚀刻(secco-etching)技术的不可检测fpd(通过射哥蚀刻技术的流动图案缺陷)及dsod(电击穿之后的直接表面氧化物缺陷微粒计数)及零i缺陷(a缺陷)为特征。
23.在另一方面中,本公开是针对一种单晶硅锭,其具有主体部分,其中所述主体部分具有圆周边缘、平行于所述圆周边缘具有轴向长度的中心轴线及从所述中心轴线延伸到所述圆周边缘的半径,其中所述主体部分包括具有在所述单晶硅锭的所述主体的轴向长度的至少40%、所述单晶硅锭的所述主体的轴向长度的至少50%、所述单晶硅锭的所述主体的轴向长度的至少60%、所述单晶硅锭的所述主体的轴向长度的至少70%或所述单晶硅锭的所述主体的轴向长度的至少80%上变动不超过平均主体氧浓度以上20%且不小于所述平均主体氧浓度以下20%的主体氧浓度的间隙氧。
24.在另一方面中,本公开是针对一种单晶硅锭,其具有主体部分,其中所述主体部分具有圆周边缘、平行于所述圆周边缘具有轴向长度的中心轴线及从所述中心轴线延伸到所述圆周边缘的半径,其中所述主体部分包括具有在所述单晶硅锭的所述主体的轴向长度的至少40%、所述单晶硅锭的所述主体的轴向长度的至少50%、所述单晶硅锭的所述主体的轴向长度的至少60%、所述单晶硅锭的所述主体的轴向长度的至少70%或所述单晶硅锭的所述主体的轴向长度的至少80%上变动不超过一平均主体氮浓度以上20%且不小于所述平均主体氮浓度以下20%的主体氮浓度的氮。
25.在另一方面中,本公开是针对一种单晶硅锭,其具有主体部分,其中所述主体部分具有圆周边缘、平行于所述圆周边缘具有轴向长度的中心轴线及从所述中心轴线延伸到所述圆周边缘的半径,其中所述主体部分进一步包括:其中所述主体部分具有在所述单晶硅锭的所述主体的轴向长度的至少40%、所述单晶硅锭的所述主体的轴向长度的至少50%、所述单晶硅锭的所述主体的轴向长度的至少60%、所述单晶硅锭的所述主体的轴向长度的至少70%或所述单晶硅锭的所述主体的轴向长度的至少80%上变动不超过平均主体电阻率以上20%且不小于所述平均主体电阻率以下20%的电阻率。
26.存在相对于本公开的上述方面所提及的特征的各种改进。进一步特征还可并入本公开的上述方面中。这些改进及额外特征可个别或以任何组合存在。例如,下文相对于本公开的说明实施例的任何者所讨论的各种特征可单独或以任何组合并入到本公开的上述方面的任何者中。
附图说明
27.图1a(早期本体生长)、1b(中期本体生长)及1c(后期本体生长)说明示范性分批柴可斯基工艺期间随晶体长度而变化的熔体容积或深度及坩埚位置。
28.图2a是描绘实现由示范性分批cz工艺生长的锭中的足够缺陷率控制所需的拉晶速率的恒定改变的曲线图。
29.图2b是描绘归因于由示范性分批cz工艺生长的锭中的偏析系数效应的氮掺杂浓度的改变的曲线图。
30.图3是描绘使用外加磁场实现由示范性分批cz工艺生长的锭中的足够缺陷率控制
所需的拉晶速率分布的曲线图。
31.图4a是描绘实现由根据本公开的方法的示范性连续cz工艺生长的锭中的足够缺陷率控制所需的拉晶速率分布的曲线图。
32.图4b是比较由示范性分批cz工艺生长的锭与由根据本公开的方法的示范性连续cz工艺生长的锭之间的氮掺杂浓度的曲线图。
33.图5描绘适合于根据本公开的方法的示范性连续cz工艺的示范性坩埚配置。
34.图6a、6b及6c说明根据本公开的方法的示范性连续cz工艺中的熔体液位及锭生长。
35.图7是描绘用于生长由根据本公开的方法的示范性连续cz工艺生长的锭的氮源添加到熔体协议的曲线图。
36.图8a及8b说明在由根据本公开的方法的示范性连续cz工艺生长锭期间施加于硅熔体的磁场。
37.对应元件符号指示所有图式中的对应部分。
具体实施方式
38.在本公开的背景中,“完美硅”是指柴可斯基生长单晶硅锭或从在满足或超过perfect silicon
tm
(sunedison semiconductor有限公司)的标准的条件下生长的柴可斯基生长单晶硅锭切割的单晶硅晶片。这些标准包含满足或超过聚结缺陷、dsod(直接表面氧化物缺陷)、cop(晶体导致微坑或微粒)、d缺陷及i缺陷等等的工业规格的锭,或从锭切割的晶片。例如,“完美硅”晶片可是以通过射哥蚀刻技术的不可检测fpd(通过射哥蚀刻技术的流动图案缺陷)及dsod(电击穿之后的直接表面氧化物缺陷微粒计数)及零i缺陷(a缺陷)为特征。射哥蚀刻包括施加碱性重铬酸盐及氢氟酸的稀释水溶液以适当显露硅的各种结晶(100)、(111)及(110)面中的错位及其它晶格缺陷。蚀刻呈出线列(低角度晶粒边界)及滑移线两者。本公开的方法实现单晶硅锭的生长,单晶硅锭包括完美硅,例如在单晶硅锭的主体的长度的至少约70%(例如单晶硅锭的主体的长度的至少约80%,或甚至单晶硅锭的主体的长度的至少约90%)上,从此锭切割的晶片。在一些实施例中,在单晶硅锭的主体的长度的至少约60%、单晶硅锭的主体的长度的至少约70%(例如单晶硅锭的主体的长度的至少约80%)或甚至单晶硅锭的主体的长度的至少约90%上,从所生长的锭切割的晶片是以通过射哥蚀刻技术的不可检测fpd(通过射哥蚀刻技术的流动图案缺陷)及dsod(电击穿之后的直接表面氧化物缺陷微粒计数)及零i缺陷(a缺陷)为特征。在一些实施例中,在单晶硅锭的主体的长度的至少约60%、单晶硅锭的主体的长度的至少约70%(例如单晶硅锭的主体的长度的至少约80%)或甚至超过单晶硅锭的主体的长度的至少约90%上,从所生长的锭切割的晶片是以在≤8mv(b模式)处95%或更大(优选地99%或更大)及/或10mv到12mv(d模式)处95%或更大(优选地99%或更大)的mos晶体管中的goi良率(即,无故障)为特征。在一些实施例中,在单晶硅锭的主体的长度的至少约60%、单晶硅锭的主体的长度的至少约70%(例如单晶硅锭的主体的长度的至少约80%)或甚至单晶硅锭的主体的长度的至少约90%上,从所生长的锭切割的晶片通过不超过0.026um大小处小于20个cop以符合完美硅。
39.在生长单晶硅锭的常规分批柴可斯基工艺中,晶体熔体/界面及热条件两者归因于锭生长期间的硅熔体的消耗及坩埚位置的可变性而随增大锭长度连续变动。图1中可看
见熔体耗乏及坩埚移动的描绘。图1a(早期本体生长)、1b(中期本体生长)及1c(后期本体生长)说明分批cz工艺期间随晶体长度而变化的熔体液位及坩埚高度。由于熔体条件(例如质量及高度液位)及坩埚位置在分批工艺期间连续改变,因此最小化缺陷率所需的v/g比(生长速率v/轴向温度梯度g)在晶体长度内连续改变以变动晶体的质量。为维持所要质量以满足工艺窗内的规格,需要根据位置来连续控制调整若干参数。这些参数包含坩埚旋转速率(c/r)、晶种旋转速率(s/r)、晶种提升速率(s/l)、加热器功率、反射器高度等等。见图2a,其是描绘实现由示范性分批cz工艺生长的锭中的足够缺陷率控制所需的拉晶速率的恒定改变的曲线图。由三角形(
‑‑‑▲‑‑‑
)界定的线是实现临界v/g值的不断改变的临界拉晶速率。拉晶速率可在由方形(
‑‑‑■‑‑‑
)标记的上临界拉晶速率(“ucl”)及由菱形(
‑‑‑◆‑‑‑
)标记的下临界拉晶速率(“lcl”)内变动,且仍实现可接受缺陷率控制。这三个线指示可产生完美硅的拉晶速度。在上拉晶速度界限及下拉晶速度界限内,可产生具有变化主导本质点缺陷的完美硅。例如,在外加拉晶速度受控于由图2a(及图3及4)中的三角形及方形标记的线之间时产生空位主导(“pv”)硅,及在外加拉晶速度受控于由图2a(及图3及4)中的三角形及菱形标记的线之间时产生间隙主导(“pi”)硅。在图2a(及图3及4)所描绘的实例中,可在锭生长的早期及中期部分生长具有空位主导点缺陷的完美硅,如由标记为“pv”的锭横截面的表示所展示。图2a描绘锭是从中心到边缘的空位主导。在图2a所描绘的实例中,于后期生长中,锭以空位主导点缺陷及间隙主导点缺陷的区域(如标记为“pi”的横截面区域中所表示)为特征。例如,可生长从中心到小于整个锭的半径的径向长度间隙主导的锭,其由到锭的边缘的空位主导材料的带包围。仍在后期区域中,锭的横截面展示由间隙主导材料的带包围的中心中的空位主导材料,所述带在边缘处由空位主导材料的另一带包围。这些描绘仅供说明且不希望限制本公开的方法。完美硅(即,无可检测聚结点缺陷的锭及从锭切割的晶片)源自由锭的拉晶速率部分地适当控制过量点缺陷(空位及间隙硅)。本质点缺陷(例如空位及间隙)发生于由柴可斯基方法生长的锭中。此类缺陷的存在不影响是否完美。确切来说,完美硅经特征化为无聚结点缺陷,例如cop、dsod及i缺陷。
40.图2a(及图3及4)还指示可导致锭在任何晶体长度处在临界v/g的上限及下限外依据拉晶速度而变化的聚结缺陷。可在超过上临界拉晶速率(v/g高于临界v/g)时发生的缺陷包含dsod(直接表面氧化物缺陷)或cop(晶体导致微坑或微粒)。可在拉晶速率低于下临界拉晶速率(v/g低于临界v/g)时发生的缺陷包含i缺陷。其中发生这些缺陷的带也展示于锭横截面中。在其中主导过量点缺陷是空位的区域中,空位缺陷的聚结物在cz硅晶生长及冷却期间通过空位的凝聚及析出来形成例如cop、dsod的体缺陷。在其中主导过量点缺陷是间隙硅原子的区域中,间隙硅原子聚结以通过聚结/析出间隙硅且冲压出错位来形成例如i缺陷的体缺陷。v/g的任何小偏差将通过聚结空位或间隙硅原子来形成缺陷。
41.除衬底缺陷率控制之外,晶片强度是例如flash装置的特定应用的另一重要变量,其中归因于装置的垂直堆叠,较高晶片强度是有利的。在一些技术中,晶片强度由氧析出及本质吸除的操纵提供。例如,增加晶片中的氧含量是操纵氧析出的主要方式。除氧含量操纵之外或替代氧含量操纵,熔体及从熔体生长的锭可掺杂有例如氮的杂质,其可操纵cop大小及bmd密度两者。氮掺杂还可提供较大完美硅质量窗对无氮掺杂材料。归因于偏析系数效应,氮掺杂可在生长期间轴向偏析。氮偏析系数低于1且已报告为约7
×
10-4
。因此,氮在生长期间不优先分配到锭中,其引起熔体中的氮含量在拉锭工艺期间增加以借此沿生长单晶硅
锭的轴向长度增加氮含量。见图2b,其是描绘氮浓度的增大的曲线图,氮浓度可从锭生长的开始到锭生长的结束增大多达7倍或更大,锭生长可沿使用图1a到1c中所描绘的熔体条件及图2a中所描绘的工艺条件根据分批柴可斯基方法制备的晶体的轴向长度发生。归因于生长期间随多晶硅被消耗的晶体位置的改变的氮轴向变动及变化晶体/熔体界面及热条件(见图1a到1c)是轴向维持良好ps质量的障碍,除非其在生长期间通过不断调谐晶体生长条件来补偿。由此,v/g在晶体长度上连续改变,其可借此变动晶体的质量。
42.可施加磁场(例如水平或尖点)以更改坩埚内的熔体流动图案且实现晶体/熔体界面的形状及高度的增强控制,其借此增强质量控制。然而,拉晶速率及其它参数仍必须经变动以实现可接受缺陷率控制,如图3中所示范。图3是描绘使用外加磁场实现由示范性分批cz工艺生长的锭中的足够缺陷率控制所需的拉晶速率分布的曲线图。由三角形(
‑‑‑▲‑‑‑
)界定的线是实现临界v/g值的临界拉晶速率,其在单晶硅锭的生长期间视需要连续变动。拉晶速率可在由方形(
‑‑‑■‑‑‑
)标记的上临界拉晶速率(“ucl”)及由菱形(
‑‑‑◆‑‑‑
)标记的下临界拉晶速率(“lcl”)内变动且仍实现可接受缺陷率控制。单晶硅锭的横截面中的本质点缺陷及聚结点缺陷的区域基本上如上文图2a的描述中所描述。
43.根据本公开的方法,在实现在生长期间保持基本上恒定的熔体深度(即,熔融硅的高度液位)及热条件的条件下由连续柴可斯基(ccz)方法生长单晶硅锭,因为熔体随其被消耗而连续补充。在一些实施例中,维持熔融硅的基本上恒定高度液位能够使坩埚维持固定位置。一旦v/g由适当热区配置固定,那么工艺窗将在晶体长度的实质部分上固定(即,无控制调整)。一旦设置工艺条件(s/r、功率、气流及压力、磁通量密度、尖点或hmcz mgp位置),那么气流及/或腔室压力及c/r用于控制氧含量。因此,本公开的方法实现由连续柴可斯基(ccz)方法生长单晶硅锭,其中拉晶速度在锭的实质长度的生长期间恒定,且根据此方法的生长锭在锭的轴向长度的实质部分上具有均匀及可接受缺陷率控制、oi均匀性、bmd均匀性及氮含量均匀性。
44.在将所要条件设置为稳定状态之后,产生在整个晶体长度中具有所要缺陷率控制的单晶硅锭的拉晶速率将恒定以归因于过程控制而比常规cz工艺显著减少生产中的质量损失。图4a是根据本公开的示范性连续柴可斯基生长方法期间依据单晶硅锭的轴向长度而变化的拉晶速率的曲线图。如图4a中所展示,在单晶硅锭的主体部分的生长的实质部分上维持恒定拉晶速率。由三角形(
‑‑‑▲‑‑‑
)界定的线是实现临界v/g值的临界拉晶速率,其具有初始变化区域,接着单晶硅锭的主体部分的生长的实质部分上的恒定拉晶速率的区域。拉晶速率可在由方形(
‑‑‑■‑‑‑
)标记的上临界拉晶速率(“ucl”)及由菱形(
‑‑‑◆‑‑‑
)标记的下临界拉晶速率(“lcl”)内变动且仍实现可接受缺陷率控制。单晶硅锭的横截面中的本质点缺陷及聚结点缺陷的区域基本上如上文图2a的描述中所描述。
45.在根据本公开的方法的ccz工艺中,多晶硅进给与晶体生长连续,借此使熔体容积维持基本上相同于初始装料熔体深度,不管晶体长度如何。由于熔体高度由生长晶体重量与连续进给的多晶硅之间的质量平衡控制,因此熔体及生长晶体中的热条件在整个轴向生长中不改变。随后,一旦所要晶体/熔体界面由例如磁场、c/r及s/r、拉晶速率、加热器功率等等的参数确定及固定,那么缺陷质量及oi控制将在整个晶体轴向生长中维持恒定。此外,因为热条件及晶体/熔体界面在晶体生长期间固定,所以可在准稳定状态控制中在整个晶体长度上使用给定hz及晶体/熔体界面的恒定拉晶速率。
46.根据本公开的方法,适合于实现满足缺陷率控制的要求的单晶硅锭的生长的热条件由热区配置设置。生长方法是连续柴可斯基方法。因此,炉室包括用于连续进给多晶硅的构件,例如进给管。添加到坩埚的固体多晶硅通常为粒状多晶硅,但可使用块状多晶硅,且其使用经优化以与粒状多晶硅一起使用的多晶硅进给器来进给到坩埚中。块状多晶硅通常具有3毫米到45毫米之间的大小(例如最大尺寸),且粒状多晶硅通常具有400微米到1400微米之间的大小。粒状多晶硅具有包含归因于较小大小而提供进给速率的容易及精确控制的若干优点。然而,归因于化学汽相沉积工艺或用于其生产中的其它制造方法,粒状多晶硅的成本通常高于块状多晶硅的成本。块状多晶硅具有较便宜且鉴于其较大大小而实现较高进给速率的优点。加热单元、冷却套的位置及功率控制的操作经调整以适应多晶硅进给器。
47.图5中展示具有将熔体分离成不同熔体区的多个堰(20、30、40)或流体屏障的坩埚10的描绘。在所说明的实施例中,坩埚组合件10包含界定硅熔体的内熔体区22的第一堰20(广义来说,流体屏障)。内熔体区22是单晶硅锭50从其生长的生长区域。第二堰30界定硅熔体的中间熔体区32。最后,第三堰40界定硅熔体的外熔体区42。进给管(图中未展示)在锭的生长期间依足以维持基本上恒定熔体高度液位及容积的速率将多晶硅(其可呈粒状、块状或粒状及块状的组合)进给到外熔体区42中。第一堰20、第二堰30及第三堰40各自具有大体上环形形状,且其内界定有至少一开口以容许熔融硅径向向内地朝向内熔体区22的生长区域流动。图5中所描绘的坩埚配置是示范性的且适合于实施本公开的工艺。可在不背离本公开的范围的情况下使用适合于ccz的其它配置。例如,坩埚10可缺乏第二堰30及/或可缺乏第三堰40。
48.一般通过将多晶硅装载到坩埚中以形成初始硅装料来形成锭从其抽拉的熔体。一般来说,初始装料介于约100千克到约400千克的多晶硅之间(例如介于约100千克到约300千克的多晶硅之间或介于约100千克到约200千克的多晶硅之间),其可呈粒状、块状或粒状及块状的组合。初始装料的质量取决于所要晶体直径及hz设计。初始装料不反映晶体的长度,因为多晶硅在晶体生长期间连续进给。例如,如果多晶硅连续进给且腔室高度足够高,那么晶体长度可延伸到2000mm、3000mm或甚至4000mm长。坩埚可具有图5中所描绘的配置或适合于ccz生长的另一配置。可使用多晶硅的各种源,其包含(例如)通过在流体化床反应器中热分解硅烷或卤代硅烷产生的粒状多晶硅或西门子(siemens)反应器中产生的多晶硅。
49.在一些实施例中,熔体进一步装有氮源,使得根据本公开的方法生长的单晶硅锭掺杂有氮。在一些实施例中,氮源是固体氮源,例如氮化硅。氮化硅可具有化学式si
x
ny,其中x及y两者是1或x及y中的一或两者大于1。可使用任何形式的氮化硅,其中si3n4是最常见及稳定。氮化硅可呈粒状或粉末的形式。在一些实施例中,氮源是在其表面上具有氮化硅膜的硅晶片。氮化硅膜可通过化学汽相沉积来沉积于硅晶片上以在晶片的一或两侧上沉积(例如)0.5微米到10微米厚膜,例如约1微米厚膜。硅晶片可整体添加或其可压碎成小件。在一些实施例中,氮源是氮氧化硅玻璃。在一些实施例中,氮掺杂可通过掺杂有例如氮气(n2)的含氮气体来完成。为形成初始装料,氮源可在使用固体源时直接添加到多晶硅装料。随着单晶硅锭生长,周期性或连续添加氮源以维持单晶硅锭的每一部分中的氮的均匀浓度。
50.本公开的方法在生长单晶硅锭的每一部分(包含单晶硅锭的颈部部分、向外扩口晶种锥部分及主体)中实现均匀氮浓度。在一些实施例中,生长单晶硅锭的每一部分中的氮浓度是至少约1
×
10
13
个原子/cm3,例如介于约1
×
10
13
个原子/cm3到约1
×
10
15
个原子/cm3之
间,或介于约1
×
10
13
个原子/cm3到约1.5
×
10
14
个原子/cm3之间,或介于约5
×
10
13
个原子/cm3到约1
×
10
14
个原子/cm3之间。优选地,单晶硅锭的轴向长度上的氮浓度的变动不超过设置点或平均氮浓度以上20%且不小于设置点或平均氮浓度以下20%。更优选地,单晶硅锭的轴向长度上的氮浓度的变动不超过设置点或平均氮浓度以上10%且不小于设置点或平均氮浓度以下10%。甚至更优选地,单晶硅锭的轴向长度上的氮浓度的变动不超过设置点或平均氮浓度以上5%且不小于设置点或平均氮浓度以下5%。例如,如果设置点(即,目标)氮浓度是7
×
10
13
个原子/cm3,那么单晶硅锭的整个轴向长度中的氮浓度优选地介于约5.67
×
10
13
个原子/cm3到约8.47
×
10
13
个原子/cm3之间,更优选地介于约6.3
×
10
13
个原子/cm3到约7.7
×
10
13
个原子/cm3之间,且甚至更优选地介于约6.65
×
10
13
个原子/cm3到约7.35
×
10
13
个原子/cm3之间。见图4b,其是描绘可通过在根据本公开的方法的示范性连续柴可斯基生长期间周期性或连续添加氮来实现的氮浓度均匀性(由空心圆
○
标记的线)的曲线图。均匀性可与分批生长工艺期间观察到的增大氮浓度(由实心圆
●
标记的线)比较。还见图2c。优选地,在锭的所有部分(包含颈部部分、向外扩口晶种锥及主体)的生长期间实现均匀氮浓度。在一些实施例中,在单晶硅锭的主体的轴向长度的至少40%、单晶硅锭的主体的轴向长度的至少50%、单晶硅锭的主体的轴向长度的至少60%、单晶硅锭的主体的轴向长度的至少70%或单晶硅锭的主体的轴向长度的至少80%或单晶硅锭的主体的轴向长度的至少90%的生长期间实现均匀氮浓度。
51.一旦将多晶硅及氮源添加到坩埚以形成装料,那么将装料加热到高于硅的约熔融温度的温度(例如约1412℃)以熔融装料且借此形成包括熔融硅的硅熔体。硅熔体具有熔融硅的初始容积且具有初始熔融高度液位,且这些参数由初始装料的大小确定。在一些实施例中,将包括硅熔体的坩埚加热至少约1425℃、至少约1450℃或甚至至少约1500℃的温度。硅熔体进一步包括足以给予锭的颈部部分至少约1
×
10
13
个氮原子/cm3的氮掺杂浓度的氮源。在一些实施例中,硅熔体进一步包括足以给予锭的颈部部分约1
×
10
13
个原子/cm3到约1
×
10
15
个原子/cm3之间或约1
×
10
13
个原子/cm3到约1.5
×
10
14
个原子/cm3之间或约5
×
10
13
个原子/cm3到约1
×
10
14
个原子/cm3之间的氮掺杂浓度的氮源。
52.一般来说,对单晶硅锭的电阻率无约束。因此,单个单晶硅锭的电阻率是基于本公开的结构的最终用途/应用的要求。因此,电阻率可从毫欧姆或更小变动到百万欧姆或更大。在一些实施例中,坩埚掺杂有p型或n型掺杂物。适合掺杂物包含硼(p型)、镓(p型)、磷(n型)、锑(n型)及砷(n型)。基于从单晶硅锭切割的晶片的所要电阻率来选择掺杂浓度。
53.在一些实施例中,根据本公开的方法拉制的单晶硅锭具有相对较低最小体电阻率,例如低于约100ohm-cm、低于约50ohm-cm、低于约1ohm-cm、低于约0.1ohm-cm或甚至低于约0.01ohm-cm。在一些实施例中,单晶硅锭具有相对较低最小体电阻率,例如低于约100ohm-cm或介于约1ohm-cm到约100ohm-cm之间。低电阻率晶片可包括电活性掺杂物,例如硼(p型)、镓(p型)、磷(n型)、锑(n型)及砷(n型)。在一些实施例中,将掺杂物添加到坩埚中的初始装料且通过在晶体生长期间连续或周期性添加掺杂物来维持电阻率均匀性。
54.在一些实施例中,单晶硅锭具有相对较高最小体电阻率。电活性掺杂物(例如硼(p型)、镓(p型)、铝(p型)、铟(p型)、磷(n型)、锑(n型)及砷(n型))可以一般非常低的浓度添加到坩埚。cz生长的硅晶片可在从约600℃到约1000℃的范围内的温度经受热退火以消除由晶体生长期间结合的氧引起的热施体。在一些实施例中,单晶硅锭具有至少100ohm-cm、至
少约500ohm-cm、至少约1000ohm-cm或甚至至少约3000ohm-cm的最小体电阻率,例如介于约100ohm-cm到约100,000ohm-cm之间,或介于约500ohm-cm到约100,000ohm-cm之间,或介于约1000ohm-cm到约100,000ohm-cm之间,或介于约500ohm-cm到约10,000ohm-cm之间,或介于约750ohm-cm到约10,000ohm-cm之间,介于约1000ohm-cm到约10,000ohm-cm之间,介于约2000ohm-cm到约10,000ohm-cm之间,介于约3000ohm-cm到约10,000ohm-cm之间,或介于3000ohm-cm到约5,000ohm-cm之间。在一些实施例中,单晶硅锭可包括p型掺杂物,例如硼、镓、铝或铟。在一些实施例中,单晶硅锭可包括n型掺杂物,例如磷、锑或砷。在一些实施例中,将掺杂物添加到坩埚中的初始装料且通过在晶体生长期间连续或周期性添加掺杂物来维持电阻率均匀性。例如,在一些实施例中,主体部分具有在单晶硅锭的主体的轴向长度的至少40%、单晶硅锭的主体的轴向长度的至少50%、单晶硅锭的主体的轴向长度的至少60%、单晶硅锭的主体的轴向长度的至少70%或单晶硅锭的主体的轴向长度的至少80%或单晶硅锭的主体的轴向长度的至少90%上变动不超过平均主体电阻率以上20%且不小于平均主体电阻率以下20%的电阻率。在一些实施例中,主体部分具有在单晶硅锭的主体的轴向长度的至少40%、单晶硅锭的主体的轴向长度的至少50%、单晶硅锭的主体的轴向长度的至少60%、单晶硅锭的主体的轴向长度的至少70%或单晶硅锭的主体的轴向长度的至少80%或单晶硅锭的主体的轴向长度的至少90%上变动不超过平均主体电阻率以上10%且不小于平均主体电阻率以下10%的电阻率。在一些实施例中,主体部分具有在单晶硅锭的主体的轴向长度的至少40%、单晶硅锭的主体的轴向长度的至少50%、单晶硅锭的主体的轴向长度的至少60%、单晶硅锭的主体的轴向长度的至少70%或单晶硅锭的主体的轴向长度的至少80%或单晶硅锭的主体的轴向长度的至少90%上变动不超过平均主体电阻率以上5%且不小于平均主体电阻率以下5%的电阻率。
55.一旦液化装料以形成包括熔融硅的硅熔体,那么降低硅种晶以接触熔体。接着,从熔体抽取硅种晶且使硅附接到硅种晶(即,种晶部分及颈部52,参考图5)以借此在熔体的表面附近或熔体的表面处形成熔体-固体界面。形成颈部部分的初始拉晶速度一般较高。在一些实施例中,硅种晶及颈部部分依至少约1.0mm/分钟的颈部部分拉晶速率(例如介于约1.5mm/分钟到约6mm/分钟之间,例如介于约3mm/分钟到约5mm/分钟之间)抽取。在一些实施例中,硅种晶及坩埚在相反方向上旋转,即,逆向旋转。逆向旋转实现硅熔体中的对流。晶体的旋转主要用于提供对称温度分布、抑制杂质的角变动及还控制晶体熔体界面形状。在一些实施例中,硅种晶依约5rpm到约30rpm之间、或约5rpm到约20rpm之间、或约8rpm到约20rpm之间或约10rpm到约20rpm之间的速率旋转。在一些实施例中,坩埚依约0.5rpm到约10rpm之间、或约1rpm到约10rpm之间、或约4rpm到约10rpm之间或约5rpm到约10rpm之间的速率旋转。在一些实施例中,种晶依比坩埚快的速率旋转。在一些实施例中,种晶依比坩埚的旋转速率高至少1rpm(例如高至少约3rpm或高至少约5rpm)的速率旋转。通常,晶体旋转速率高于坩埚旋转速率以促进晶体中的掺杂浓度的良好径向均匀性。在一些实施例中,硅种晶及坩埚在相反方向上旋转,即,逆向旋转。
56.一般来说,颈部部分具有约10毫米到约700毫米之间、约30毫米到约700毫米之间、约100毫米到约700毫米之间、约200毫米到约700毫米之间或约300毫米到约700毫米之间的长度。在一些实施例中,颈部部分具有约10毫米到约100毫米之间(例如约20毫米到约50毫米之间)的长度。在一些实施例中,颈部部分具有约350毫米到约550毫米之间的长度。在一
些实施例中,颈部部分具有约450毫米到约550毫米之间的长度。然而,颈部部分的长度可在这些范围外变动。在一些实施例中,颈部部分具有约1毫米到约10毫米之间、约2.5毫米到约6.5毫米之间(例如约3毫米到约6毫米之间)的直径。由于硅熔体掺杂有氮,因此锭的颈部部分52掺杂有氮。在一些实施例中,颈部部分52具有至少约1
×
10
13
个原子/cm3的颈部部分氮浓度。在一些实施例中,颈部部分52具有约1
×
10
13
个原子/cm3到约1
×
10
15
个原子/cm3之间、或约1
×
10
13
个原子/cm3到约1.5
×
10
14
个原子/cm3之间或约5
×
10
13
个原子/cm3到约1
×
10
14
个原子/cm3之间的氮浓度。优选地,颈部部分的轴向长度上的氮浓度的变动不超过设置点或平均氮浓度以上20%且不小于设置点或平均氮浓度以下20%。更优选地,颈部部分的轴向长度上的氮浓度的变动不超过设置点或平均氮浓度以上10%且不小于设置点或平均氮浓度以下10%。甚至更优选地,颈部部分的轴向长度上的氮浓度的变动不超过设置点或平均氮浓度以上5%且不小于设置点或平均氮浓度以下5%。
57.在形成颈部之后,生长邻近于颈部52的向外扩口晶种锥部分54,参考图5。一般来说,拉晶速率从颈部部分拉晶速率减小到适合于生长向外扩口晶种锥部分的速率。例如,向外扩口晶种锥的生长期间的晶种锥拉晶速率介于约0.5mm/min到约2.0mm/min之间,例如约1.0mm/min。在一些实施例中,向外扩口晶种锥54具有约100毫米到约400毫米之间(例如约150毫米到约250毫米之间)的长度。向外扩口晶种锥54的长度可在这些范围外变动。在一些实施例中,向外扩口晶种锥54生长到约为150mm、至少约150毫米、约200mm、至少约200毫米、约300mm、至少约300mm、约450mm或甚至至少约450mm的终端直径。向外扩口晶种锥54的终端直径一般等于单晶硅锭的主体的恒定直径的直径。根据本公开的方法,锭的向外扩口晶种锥54掺杂有氮。在一些实施例中,向外扩口晶种锥54具有至少约1
×
10
13
个原子/cm3的向外扩口晶种锥氮浓度。在一些实施例中,向外扩口晶种锥54具有约1
×
10
13
个原子/cm3到约1
×
10
15
个原子/cm3之间、或约1
×
10
13
个原子/cm3到约1.5
×
10
14
个原子/cm3之间或约5
×
10
13
个原子/cm3到约1
×
10
14
个原子/cm3之间的氮浓度。优选地,向外扩口晶种锥54中的氮浓度的变动不超过设置点氮浓度以上约20%且不小于设置点氮浓度以下20%。更优选地,向外扩口晶种锥54中的氮浓度的变动不超过设置点氮浓度以上约10%且不小于设置点氮浓度以下10%。甚至更优选地,向外扩口晶种锥54中的氮浓度的变动不超过设置点氮浓度以上约5%且不小于设置点氮浓度以下5%。再次参考图4b,在锭的所有部分(包含向外扩口晶种锥)的生长期间根据本公开的示范性方法优选地实现氮浓度均匀性。
58.在形成颈部及邻近于颈部部分的向外扩口晶种锥之后,生长邻近于锥部分具有恒定直径的主锭体56。主体56的恒定直径部分具有圆周边缘、平行于圆周边缘的中心轴线,及从中心轴线延伸到圆周边缘的半径。中心轴线还穿过锥部分及颈部52。主锭体的直径可变动,且在一些实施例中,直径可为约150mm、至少约150毫米、约200mm、至少约200毫米、约300mm、至少约300mm、约450mm,或甚至至少约450mm。在一些实施例中,单晶硅锭的主体最终生长为至少约1000毫米长,例如至少1100毫米长,例如至少1200毫米长,例如至少1400毫米长,例如至少1500毫米长,例如至少1700毫米长、或至少1900毫米长、或至少2000毫米长、或至少2200毫米、或至少约3000毫米长或至少约4000毫米长。根据本公开的方法,锭的主体56经掺杂有氮。在一些实施例中,主体56具有至少约1
×
10
13
个原子/cm3的主体氮浓度。在一些实施例中,主体56具有约1
×
10
13
个原子/cm3到约1
×
10
15
个原子/cm3之间、或约1
×
10
13
个原子/cm3到约1.5
×
10
14
个原子/cm3之间,或约5
×
10
13
个原子/cm3到约1
×
10
14
个原子/cm3之间
的氮浓度。优选地,主体56中的氮浓度的变动不超过设置点氮浓度以上约20%且不小于设置点氮浓度以下20%。更优选地,主体56中的氮浓度的变动不超过设置点氮浓度以上约10%且不小于设置点氮浓度以下10%。甚至更优选地,主体56中的氮浓度的变动不超过设置点氮浓度以上约5%且不小于设置点氮浓度以下5%。再次参考图4b,在锭的所有部分(包含主体部分)的生长期间,根据本公开的示范性方法优选地实现氮浓度均匀性。在一些实施例中,主体包括具有在单晶硅锭的主体的轴向长度的至少40%、单晶硅锭的主体的轴向长度的至少50%、单晶硅锭的主体的轴向长度的至少60%、单晶硅锭的主体的轴向长度的至少70%,或单晶硅锭的主体的轴向长度的至少80%,或单晶硅锭的主体的轴向长度的至少90%上变动不超过平均主体氮浓度以上20%且不小于平均主体氮浓度以下20%的主体氮浓度的氮。在一些实施例中,主体包括具有在单晶硅锭的主体的轴向长度的至少40%、单晶硅锭的主体的轴向长度的至少50%、单晶硅锭的主体的轴向长度的至少60%、单晶硅锭的主体的轴向长度的至少70%,或单晶硅锭的主体的轴向长度的至少80%,或单晶硅锭的主体的轴向长度的至少90%上变动不超过平均主体氮浓度以上10%且不小于平均主体氮浓度以下10%的主体氮浓度的氮。在一些实施例中,主体包括具有在单晶硅锭的主体的轴向长度的至少40%、单晶硅锭的主体的轴向长度的至少50%、单晶硅锭的主体的轴向长度的至少60%、单晶硅锭的主体的轴向长度的至少70%,或单晶硅锭的主体的轴向长度的至少80%,或单晶硅锭的主体的轴向长度的至少90%上变动不超过平均主体氮浓度以上5%且不小于平均主体氮浓度以下5%的主体氮浓度的氮。
59.图4a说明根据本公开的方法的一些实施例的用于拉制单晶硅锭的主体的示范性及非限制性拉晶速率协议。如从示范性说明明白,在单晶硅锭的主体的生长的重要部分中,拉晶速率从相对较高拉晶速率下降到最小拉晶速率,且接着上升到恒定拉晶速率。根据本公开的工艺,选择拉晶速率以实现完美硅,即,以缺乏选自聚结缺陷、dsod(直接表面氧化物缺陷)、cop(晶体导致微坑)、d缺陷及i缺陷等等的可检测聚结缺陷为特征的硅。初始高拉晶速率可介于约0.5mm/min到约2.0mm/min之间(例如约1.0mm/min),接着,在增大到约0.4mm/min到约0.8mm/min之间、约0.4mm/min到约0.7mm/min之间或约0.4mm/min到约0.65mm/min之间的恒定拉晶速率之前减小到可低到约0.4mm/min或甚至低到约0.3mm/min的拉晶速率。
60.图6a、6b及6c中描绘适合于实施本公开的方法的炉室100内的热区配置的示范性及非限制性说明。其它热区配置适合于实施本公开的方法。热区配置包含冷却套102、反射器104、侧面加热器106及底部加热器108。生长晶体直径及弯月面的形状及高度由位于顶部窗的摄影机(图中未图画)监测。从摄影机获得的数据能够回馈到侧面加热器106及底部加热器108。在晶体生长期间,可调整加热器之间的功率分配以实现熔体/固体界面的均匀性,即,维持弯月面的所要形状及高度。反射器104会将热通量从包含加热器及坩埚的炉的热部分反射到熔体。反射器104减少从炉的热部分到冷部分(由冷却套102维持)的热传递且借此维持炉的这两个区域之间的分离。反射器有助于控制轴向及径向温度梯度,其驱使熔融硅固化及结晶为生长锭。
61.图6a、6b及6c描绘分别对应于图4a中所展示的拉晶速率的区域的第一步骤、第二步骤及第三步骤。即,图6a中所描绘的第一步骤对应于其中拉晶速率较高且减小到图4a中的最小值的区域。图6b中所描绘的第二步骤对应于其中拉晶速率处于最小值且增大到图4a中的恒定拉晶速率的区域。图6c中所描绘的第三步骤对应于图4a中的恒定拉晶速率的区
域。在每一步骤期间,熔体110保持根据本公开的实施例的恒定熔体容积及熔体高度液位,因为多晶硅在锭112的生长期间连续进给到熔体中(见图5)。
62.以可变拉晶速率为特征的生长单晶硅锭的主体的初始区域可涵盖单晶硅锭的主体的总长度的小于约20%。在一些实施例中,可变拉晶速率范围可涵盖单晶硅锭的主体的长度的约5%到约20%之间,例如单晶硅锭的主体的长度的约5%到约15%之间或单晶硅锭的主体的长度的约10%到约15%之间。在可变拉晶速率条件下生长的单晶硅锭的主体的长度的百分比部分取决于锭的主体的总长度。例如,在可变速率条件下拉制的锭的主体的长度可在约50mm到约200mm之间、约100mm到约200mm之间(例如约150mm到约200mm之间)变动。如果在可变速率条件下生长200mm且锭的主体的总长度是1400mm,那么主体的约14%在可变速率条件下生长,而对2200mm的总主体长度来说,主体的仅约9%在可变速率条件下生长。
63.在可变拉晶速率条件下生长主体的初始区域之后,在恒定拉晶速率下生长主体的剩余部分。在一些实施例中,锭的主体在单晶硅锭的主体的长度的至少约30%(例如单晶硅锭的主体的长度的至少约50%、单晶硅锭的主体的长度的至少约70%、单晶硅锭的主体的长度的至少约80%或甚至单晶硅锭的主体的长度的至少约90%)的生长期间依恒定主体拉晶速率生长。在一些实施例中,恒定主体拉晶速率介于约0.4mm/min到约0.8mm/min之间、约0.4mm/min到约0.7mm/min之间或约0.4mm/min到约0.65mm/min之间。
64.在单晶硅锭的主体的生长期间,将多晶硅(即,粒状、块状或粒状及块状的组合)添加到熔融硅以借此实现熔融硅的恒定容积及恒定熔体高度液位。根据本公开的方法,在单晶硅锭的主体的轴向长度的实质部分的生长期间维持基本上恒定熔体容积实现依恒定拉晶速率实现单晶硅锭的主体的轴向长度的实质部分上的高锭质量。不管晶体长度如何,恒定熔体容积能够维持恒定晶体/熔体界面且因此维持锭的主体的实质部分上的均匀晶体质量。因此,在一些实施例中,熔融硅的容积在单晶硅锭的主体的至少约90%的生长期间变动不超过约1.0容积%,或在单晶硅锭的主体的至少约90%的生长期间变动不超过约0.5容积%,或甚至在单晶硅锭的主体的至少约90%的生长期间变动不超过0.1容积%。换句话说,在一些实施例中,熔体高度液位在单晶硅锭的主体的至少约90%的生长期间变动小于约 /-0.5毫米。
65.在单晶硅锭的主体的生长期间,熔体进一步装有氮源,使得根据本公开的方法生长的单晶硅锭掺杂有氮。在一些实施例中,氮源是固体氮源,例如氮化硅。氮化硅可呈粉末的形式。在一些实施例中,氮源是在其表面上具有氮化硅膜的硅晶片。氮化硅膜可通过化学汽相沉积来沉积于硅晶片上以将(例如)0.5微米到10微米(例如约1微米)厚膜沉积于晶片的两侧上。硅晶片可整体添加或其可压碎成小件。在一些实施例中,氮源是氮氧化硅玻璃。在一些实施例中,氮掺杂可通过掺杂有例如氮气(n2)的含氮气体来完成。在锭的生长期间,根据本公开的方法,氮源可与多晶硅一起添加到第三堰40,如图5中所描绘。
66.本公开的方法适合于在单晶硅锭的颈部部分、晶种锥及主体部分的生长期间实现轴向均匀氮浓度。见图4b,其用于描绘可通过根据本公开的连续柴可斯基技术在锭的生长期间连续或周期性添加氮来实现的均匀性。克服常见于氮掺杂单晶硅锭中的偏析的均匀性由将氮源连续或周期性添加到熔体的自动掺杂系统实现。氮源可在锭(包含颈部部分、晶种锥及主体部分中的每一者)的生长期间连续或周期性添加。在一些实施例中,为了均匀性及
容易处理,优选地周期性添加氮源,例如在锭生长期间的轴向长度的每25mm、50mm、75mm或100mm中。在锭的生长期间,还优选地周期性添加氮源(例如在锭生长期间的轴向长度的每25mm、50mm、75mm或100mm中)以促进在锭的轴向长度的生长期间取得完美硅。
67.在一些实施例中,氮源以每50mm的单晶硅锭的主体的轴向长度约1毫克氮到约100毫克氮之间、或每50mm的单晶硅锭的主体的轴向长度约1毫克氮到约25毫克氮之间或每50mm的单晶硅锭的主体的轴向长度约2毫克氮到约15毫克氮之间的量连续进给或周期性进给到坩埚。在一些实施例中,氮源是氮化硅,其可作为粉末添加。在一些实施例中,氮化硅在单晶硅锭的主体的生长期间以每50mm的单晶硅锭的主体的轴向长度约2.5毫克氮化硅到约250毫克氮化硅之间、或每50mm的单晶硅锭的主体的轴向长度约5毫克氮化硅到约100毫克氮化硅或每50mm的单晶硅锭的主体的轴向长度约10毫克氮化硅到约50毫克氮化硅之间的量连续进给或周期性进给到坩埚。在一些示范性实施例中,每50mm的具有约310毫米的标称直径的主体的轴向长度可添加约10毫克到约50毫克之间(例如约25毫克)的氮化硅。所添加的氮化硅的量可取决于锭的标称直径而按比例增加或减少。例如,每50mm的具有约150毫米的标称直径的主体的轴向长度可添加约1毫克到约10毫克之间(例如约5毫克或约6毫克)的氮化硅。在又一实例中,每50mm的具有约450毫米的标称直径的主体的轴向长度可添加约25毫克到约75毫克之间(例如约45毫克到约60毫克之间)的氮化硅。图7中描绘显示依据单晶硅锭的轴向长度而变化的氮化硅的总添加的示范性进给协议。
68.在一些实施例中,在生长期间添加氮源以实现约1
×
10
13
个原子/cm3到约1
×
10
15
个原子/cm3之间、或约1
×
10
13
个原子/cm3到约1.5
×
10
14
个原子/cm3之间或约5
×
10
13
个原子/cm3到约1
×
10
14
个原子/cm3之间的主体氮浓度。在一些实施例中,在生长期间添加氮源以在单晶硅锭的主体的轴向长度的至少40%、单晶硅锭的主体的轴向长度的至少50%、单晶硅锭的主体的轴向长度的至少60%、单晶硅锭的主体的轴向长度的至少70%或单晶硅锭的主体的轴向长度的至少80%或单晶硅锭的主体的轴向长度的至少90%或甚至单晶硅锭的主体的整个轴向长度上实现约5
×
10
13
个原子/cm3到约1
×
10
14
个原子/cm3的主体氮浓度。
69.在一些实施例中,在生长期间添加氮源以实现约1
×
10
13
个原子/cm3到约1.5
×
10
14
个原子/cm3之间或约5
×
10
13
个原子/cm3到约1
×
10
14
个原子/cm3之间的主体氮浓度,且其中主体氮浓度在单晶硅锭的主体的轴向长度的至少40%、单晶硅锭的主体的轴向长度的至少50%、单晶硅锭的主体的轴向长度的至少60%、单晶硅锭的主体的轴向长度的至少70%或单晶硅锭的主体的轴向长度的至少80%或单晶硅锭的主体的轴向长度的至少90%或甚至单晶硅锭的主体的整个轴向长度上变动不超过设置点或平均主体氮浓度以上20%且不小于设置点或平均主体氮浓度以下20%。更优选地,主体56中的氮浓度的变动在单晶硅锭的主体的轴向长度的至少40%、单晶硅锭的主体的轴向长度的至少50%、单晶硅锭的主体的轴向长度的至少60%、单晶硅锭的主体的轴向长度的至少70%或单晶硅锭的主体的轴向长度的至少80%或单晶硅锭的主体的轴向长度的至少90%或甚至单晶硅锭的主体的整个轴向长度上不超过设置点氮浓度以上约10%且不小于设置点氮浓度以下10%。甚至更优选地,主体56中的氮浓度的变动在单晶硅锭的主体的轴向长度的至少40%、单晶硅锭的主体的轴向长度的至少50%、单晶硅锭的主体的轴向长度的至少60%、单晶硅锭的主体的轴向长度的至少70%或单晶硅锭的主体的轴向长度的至少80%或单晶硅锭的主体的轴向长度的至少90%或甚至单晶硅锭的主体的整个轴向长度上不超过设置点氮浓度以上约5%且不
小于设置点氮浓度以下5%。
70.在一些实施例中,在生长期间添加氮源以实现约5
×
10
13
个原子/cm3到约1
×
10
14
个原子/cm3之间的主体氮浓度,且其中主体氮浓度在单晶硅锭的主体的轴向长度的至少40%、单晶硅锭的主体的轴向长度的至少50%、单晶硅锭的主体的轴向长度的至少60%、单晶硅锭的主体的轴向长度的至少70%或单晶硅锭的主体的轴向长度的至少80%上变动不超过设置点或平均主体氮浓度以上20%且不小于设置点或平均主体氮浓度以下20%。更优选地,主体56中的氮浓度的变动在单晶硅锭的主体的轴向长度的至少40%、单晶硅锭的主体的轴向长度的至少50%、单晶硅锭的主体的轴向长度的至少60%、单晶硅锭的主体的轴向长度的至少70%或单晶硅锭的主体的轴向长度的至少80%或单晶硅锭的主体的轴向长度的至少90%或甚至单晶硅锭的主体的整个轴向长度上不超过设置点氮浓度以上约10%且不小于设置点氮浓度以下10%。甚至更优选地,主体56中的氮浓度的变动在单晶硅锭的主体的轴向长度的至少40%、单晶硅锭的主体的轴向长度的至少50%、单晶硅锭的主体的轴向长度的至少60%、单晶硅锭的主体的轴向长度的至少70%或单晶硅锭的主体的轴向长度的至少80%或单晶硅锭的主体的轴向长度的至少90%或甚至单晶硅锭的主体的整个轴向长度上不超过设置点氮浓度以上约5%且不小于设置点氮浓度以下5%。
71.另外,根据本公开的工艺,可将磁场施加于包括硅熔体的坩埚。可施加尖点或水平磁场以设置适当晶体/熔体界面,即,弯月面的形状及高度。磁场主要用于固定所要晶体/熔体界面形状及高度,且控制氧含量oi是次要目的。
72.可通过在单晶硅锭的主体的生长期间将磁场施加于硅熔体来增强熔体流动及熔体/固体界面的形状及因此锭的质量的控制。在一些实施例中,外加磁场在单晶硅锭的主体的生长的至少约70%或单晶硅锭的主体的生长的至少约70%到约90%之间期间维持基本上恒定熔体/固体界面分布。磁场施加电磁力,其影响硅熔体流动,因此影响熔体中的热传递。其改变晶体/熔体界面的分布及生长晶体的温度,其是完美硅的关键控制参数。
73.磁场影响锭中的氧含量及均匀性。锭中的氧源来自石英坩埚壁的溶解、无熔体表面处的蒸发siox(g)(由熔体流动动力学控制)及到生长晶体正面中的结合。磁场影响生长期间的对流熔体流动,其可影响氧蒸发及结合。随时间递增结合到单晶硅锭中的氧的变动由熔体中的氧的扩散及对流根据以下方程式控制:
[0074][0075]
c是固化硅中的氧浓度,t是时间,v是对流速度(熔体流动速度),rho(ρ)是硅熔体的密度,是梯度(d/dx)。外加磁场影响熔体速度(v)及熔体中的氧浓度的梯度由于磁场导致稳定状态熔体流动,因此将氧oi结合到锭中是时间常数,其提高径向及轴向氧浓度均匀性。source项从以下两个参数导出:石英(sio2)坩埚的溶解,其产生氧(si(l) sio2(s)
→
siox(g));及蒸发,其从熔体移除(消散)氧(siox(g))。在分批cz工艺中,此source项不恒定。相反地,其取决于晶体长度,因为熔体质量随晶体生长而减小。当锭已生长其本体长度的实质部分时,剩余熔体容积较低,使得与坩埚接触的硅熔体量减少,其因此导致从坩埚结合到熔体中的氧的较低浓度。因此,如果其它项(扩散、对流、蒸发)恒定,那么结合到固化硅晶体中的氧减少。无熔体表面(熔体与气体之间的接触表面)面积影响siox(g)的蒸发速率。归因于图1c中所展示的坩埚的形状,分批cz工艺中的小熔体质量具有相对
较小表面积。siox(g)的较少蒸发意味着更多氧结合到固化硅晶体中。根据本公开的方法,熔体质量维持恒定,因为多晶硅随晶锭生长而添加。因此,所有源项(通过sio2坩埚溶解到熔体中来产生氧及通过无熔体表面蒸发siox(g)气体)是恒定的。因此,扩散及对流项影响固化硅晶体的氧。外加磁场使熔体流动更稳定(即,熔体流动是恒定的,如作为非时变稳定条件),因此结合氧在锭的整个长度的生长期间在轴向及径向方向上均匀及稳定。在一些实施例中,间隙氧可以约4ppma到约18ppma之间的浓度结合到锭中。在一些实施例中,间隙氧可以约10ppma到约35ppma之间的浓度结合锭中。在一些实施例中,锭包括具有不大于约15ppma或不大于约10ppma的浓度的氧。间隙氧可根据semi mf 1188-1105测量。在一些实施例中,主体间隙氧浓度在单晶硅锭的主体的轴向长度的至少40%、单晶硅锭的主体的轴向长度的至少50%、单晶硅锭的主体的轴向长度的至少60%、单晶硅锭的主体的轴向长度的至少70%或单晶硅锭的主体的轴向长度的至少80%或单晶硅锭的主体的轴向长度的至少90%上变动不超过平均主体氧浓度以上20%且不小于平均主体氧浓度以下20%。在一些实施例中,主体间隙氧浓度在单晶硅锭的主体的轴向长度的至少40%、单晶硅锭的主体的轴向长度的至少50%、单晶硅锭的主体的轴向长度的至少60%、单晶硅锭的主体的轴向长度的至少70%或单晶硅锭的主体的轴向长度的至少80%或单晶硅锭的主体的轴向长度的至少90%上变动不超过平均主体氧浓度以上10%且不小于平均主体氧浓度以下10%。在一些实施例中,主体间隙氧浓度在单晶硅锭的主体的轴向长度的至少40%、单晶硅锭的主体的轴向长度的至少50%、单晶硅锭的主体的轴向长度的至少60%、单晶硅锭的主体的轴向长度的至少70%或单晶硅锭的主体的轴向长度的至少80%或单晶硅锭的主体的轴向长度的至少90%上变动不超过平均主体氧浓度以上5%且不小于平均主体氧浓度以下5%。
[0076]
在一些实施例中,在单晶硅锭的主体的生长期间将水平磁场施加于硅熔体。图8a中说明此水平场,其描绘叠加于图5中所描绘的坩埚及生长锭上的水平磁场。通过将保持硅熔体的坩埚放置于常规电磁铁200的极之间来实现存在水平磁场时的晶体生长。在一些实施例中,水平磁场在熔体区域中可具有约0.2特斯拉到约0.4特斯拉之间的磁通量密度。在给定强度下,熔体中的磁场变动小于 /-约0.03特斯拉。施加水平磁场导致沿轴向方向(在与流体运动相反的方向上)的劳伦兹(lorentz)力,相反力驱动熔体对流。因此,抑制熔体中的对流,且界面附近的晶体中的轴向温度梯度增大。接着,熔体-晶体界面向上移动到晶体侧以适应界面附近的晶体中的增大轴向温度梯度且来自坩埚中的熔体对流的贡献减小。
[0077]
在一些实施例中,在单晶硅锭的主体的生长期间将尖点磁场施加于硅熔体。图8b中说明尖点磁场,其描绘叠加于图5中所描绘的坩埚及生长锭上的尖端磁场。尖点磁场具有两个控制参数,即,磁通量密度及磁场形状。尖点磁场施加熔体的最近表面处的水平(径向)磁场分量与锭的轴线附近的熔体中的较深处的垂直(轴向)磁场的组合。尖点磁场使用载送相反方向上的电流的对亥姆霍兹(helmholtz)线圈产生。因此,在垂直地沿锭轴线的两个磁场之间的中间位置,磁场彼此抵消以形成等于或接近零的垂直磁场分量。例如,尖点磁通量密度在轴向方向上通常为0特斯拉到约0.2特斯拉。径向方向上的磁通量密度一般高于垂直方向上的磁通量密度。例如,尖点磁通量密度在径向位置中通常介于约0t到约0.6t之间(例如介于约0.2t到约0.5t之间),其取决于径向位置。径向尖点磁场约束熔体的流动以借此稳定熔体。换句话说,施加径向尖点磁场诱发邻近于其中发生晶体生长的固体-液体界面的部分处的对流且抑制熔体的剩余部分的对流以借此充当用于实现均匀氧气分布的有效方法。
热熔体对流可同时由无熔体表面及熔体坩埚界面处的尖点磁场局部及独立控制。此能够仅通过磁通量密度来控制生长晶体中的氧浓度,不管晶体旋转速度如何。如果存在轴向或径向磁场,那么经由控制晶体旋转速度来实现氧浓度的控制。施加尖点磁场可实现包括小于在无外加磁场的情况下生长的锭的氧含量(例如不大于约15ppma或不大于约10ppma)的锭上的生长。间隙氧可根据semi mf1188-1105测量。
[0078]
本公开的方法能够通过连续柴可斯基方法来生长满足或超过完美硅的工业规格的单晶硅锭。促成完美硅晶体的生长的因子包含确定生长完美硅的临界拉晶速度、维持单晶硅锭的主体的生长的实质部分上的临界速度处的恒定拉晶速度及施加磁场以维持熔体/固体界面的形状及高度。一旦确定拉晶速度及磁场的配置,那么可归因于连续添加多晶硅而依恒定速率维持拉晶速度以维持恒定熔体容积及熔体高度液位。因此,不同于常规锭生长方法,拉晶速度在锭的生长的实质部分上恒定。鉴于由本文所公开的方法实现的工艺控制,本公开的方法能够在单晶硅锭的主体的长度的至少约70%上(例如在单晶硅锭的主体的长度的至少约80%上或在甚至单晶硅锭的主体的长度的至少约90%上)生长包括完美硅的单晶硅锭。
[0079]
如本文所使用,术语“约”、“实质上”、“基本上”及“近似”在结合尺寸、浓度、温度或其它物理或化学性质或特性的范围使用时意味着涵盖可存在于性质或特性的范围的上限及/或下限中的变动,其包含(例如)源自舍入、测量方法或其它统计变动的变动。
[0080]
当引入本公开或其实施例的元件时,冠词“一”及“所述”希望意味着存在元件中的一或多者。术语“包括”、“包含”、“含有”及“具有”希望具包含性且意味着可存在除所列元件之外的额外元件。使用指示特定定向(例如“顶部”、“底部”、“侧”等等)的术语是为了方便描述且不要求描述项的任何特定定向。
[0081]
由于可在不背离本公开的范围的情况下对上述构造及方法进行各种改变,因此预期以上描述中所含及附图中所展示的所有事项应被解译为意在说明而非限制。
再多了解一些
本文用于企业家、创业者技术爱好者查询,结果仅供参考。