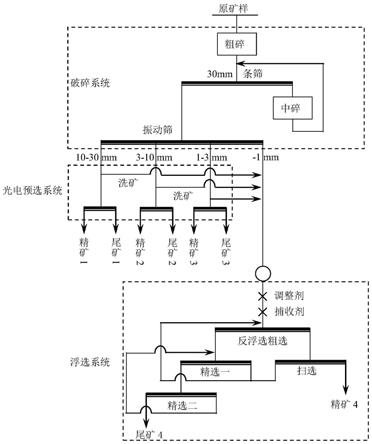
1.本发明涉及冶金化工技术领域,尤其涉及一种用于氧化铜矿石预选脱钙的选矿方法。
背景技术:
2.行业内针对氧化铜矿物常采用浮选、酸浸、生物浸出等工艺回收该类氧化铜资源。浮选工艺是最常见的工艺之一,但由于氧化铜矿物的天然可浮性较差,在浮选过程中要加入大量的活化剂及捕收剂,药剂成本较高,同时铜的综合回收率不高,造成资源的浪费。酸浸、生物浸出等工艺处理氧化铜矿时,一般原矿品位较高,湿法浸出铜综合回收率可达90%以上。我国氧化铜资源大多品位较低,矿物组成复杂,原矿中有部分脉石矿物会影响铜的综合回收率。氧化铜矿原矿铜品位在1.5%以下时,直接进行浮选或者浸出时,成本高、回收率低、经济效益差。我国西北地区、西南地区氧化铜资源丰富,但脉石矿物多为碳酸盐型矿物,在浸出过程中酸耗大,成本高,在浸出过程中会产生大量的气泡,且反应时间较长,影响铜的浸出率,同时会污染现场劳动环境,存在安全隐患。为解决生产存在的问题,改善作业环境,提高铜浸出率,开展低品位大理岩型氧化铜矿石预选脱钙的研究,对提高资源利用率,消除安全隐患,减少碳排放具有重要意义。
技术实现要素:
3.本发明要解决的技术问题是针对现有技术存在的问题,提供一种更为经济高效、可改善作业环境、能提高铜浸出率、可简化工艺流程的低品位大理岩型氧化铜矿石预选脱钙的选矿方法。
4.为解决上述技术问题,本发明采用如下技术方案:一种低品位大理岩型氧化铜矿石预选脱钙的选矿方法,该低品位大理岩型氧化铜矿石含铜0.9-1.5%,直接进行浮选或者浸出,成本高,回收率低,经济效益差。选矿设备包括有破碎系统、光电预选系统及浮选系统,选矿过程按以下步骤进行,
5.1)采用破碎系统对原矿进行粗碎,粗碎后的产品进入中碎,中碎后的产品进行三层振动筛,破碎不达标的矿物返回中碎系统,形成闭路碎矿;经过筛分后得到原矿1、原矿2、原矿3和原矿4;
6.2)将原矿1、原矿2、原矿3进行分选,经给料系统分别给入洗矿系统后,冲干净原矿表面的粉矿,粉矿与原矿4合并为原矿5;经洗矿系统处理后的原矿1-3进入颜色识别系统,分为绿色的孔雀石和白色的大理岩矿物,识别后的矿物进入喷气执行系统,将绿色的孔雀石与白色的大理岩矿物区分开来,得到精矿1、精矿2、精矿3和尾矿1、尾矿2、尾矿3;
7.3)原矿5进行采用浮选系统进行分离,将矿石磨细,得到磨矿矿浆,加水调节矿浆浓度为28-33%;
8.4)往步骤3)得到的磨矿矿浆添加调整剂,调整剂为碳酸钠,作用时间为2~3分钟;加入捕收剂,作用时间为4~5分钟,进行反浮选粗选,得到反浮选粗精矿和反浮选尾矿;
9.5)将步骤4)得到的反浮选尾矿扫选两次,扫选中矿返回到粗选,扫选尾矿即为精矿4;
10.6)将步骤4)得到的反浮选粗精矿精选两次,第一次精选中矿返回到粗选,第二次精选中矿返回到第一次精选,第二次精选精矿即为尾矿4。
11.在步骤1)中,筛孔尺寸分别为30mm、10mm、3mm、1mm, 30mm粒级的矿物返回中碎系统,形成闭路碎矿,经过筛分后得到10-30mm的原矿1,3-10mm的原矿2,1-3mm的原矿3,-1mm的原矿4。
12.所述光电预选系包括振动给料系统、洗矿系统、颜色识别系统和喷气执行系统。
13.在步骤4)中添加的捕收剂为油酸、油酸钠、苯甲羟肟酸中的一种或两种或三种药剂组合。
14.本发明通过将原矿进行破碎后,对粗粒级矿物采用运行成本更低的光电预选系统,利用孔雀石与大理岩型脉石矿物颜色差异的特点,将大理岩型脉石矿物预先抛除。对于光电预选难以处理的细粒级矿物,采用浮选抛除大理岩型脉石矿物,减少进入湿法系统的大理岩矿物。采用该选矿方法,大理岩型脉石矿物抛除率可达到75%以上,铜品位可富集4倍以上,减少后续工艺的浸出成本,提高入选品位,对同类型矿山均有借鉴意义。
附图说明
15.图1为本发明工艺流程图。
具体实施方式
16.下面结合附图通过具体实施例对本发明做进一步说明:
17.实施例1,本实施例以西南地区某大理岩型氧化铜矿石为例,原矿含铜0.93%,铜氧化率80%以上,铜矿物主要为孔雀石,脉石矿物主要为方解石,其中方解石含量80%以上。
18.按照工艺流程图1,对原矿进行破碎,经筛分后分为10-30mm的原矿1,3-10mm的原矿2,1-3mm的原矿3,-1mm的原矿4,对原矿1、原矿2、原矿3进入光电预选系统,冲干净原矿表面的粉矿,粉矿与原矿4合并为原矿5,洗矿水循环利用。经洗矿系统处理后的原矿1-3进入颜色识别系统,分为绿色的孔雀石和白色的大理岩矿物,识别后的矿物进入喷气执行系统,将绿色孔雀石与白色大理岩矿物区分开来,得到精矿1、精矿2、精矿3和尾矿1、尾矿2、尾矿3。
19.粉矿与原矿4合并后进行磨细,得到磨矿矿浆,加入碳酸钠,作用时间为2~3分钟,加入油酸,作用时间为4~5分钟,进行反浮选粗选,得到反浮选粗精矿和反浮选尾矿。反浮选尾矿扫选两次,扫选中矿返回到粗选,扫选尾矿即为精矿4。反浮选粗精矿精选两次,第一次精选中矿返回到粗选,第二次精选中矿返回到第一次精选,第二次精选精矿即为尾矿4。结果如下表所示:
20.实施例1试验结果/%
21.产品名称产率铜品位回收率精矿15.865.3833.98精矿23.274.4715.76
精矿34.554.9924.47精矿40.7321.3316.78尾矿133.500.082.89尾矿226.300.102.83尾矿315.500.111.84尾矿410.290.131.44原矿100.000.93100.00
22.实施例2,本实施例以西藏某大理岩型氧化铜矿石为例,原矿含铜1.874%,铜氧化率85%以上,铜矿物主要为孔雀石,脉石矿物主要为方解石,其中方解石含量75%以上。
23.按照工艺流程图1,对原矿进行破碎,经筛分后分为10-30mm的原矿1,3-10mm的原矿2,1-3mm的原矿3,-1mm的原矿4,对原矿1、原矿2、原矿3进入光电预选系统,冲干净原矿表面的粉矿,粉矿与原矿4合并为原矿5,洗矿水循环利用,经洗矿系统处理后的原矿1-3进入颜色识别系统,分为绿色的孔雀石和白色的大理岩矿物,识别后的矿物进入喷气执行系统,将绿色孔雀石与白色大理岩矿物区分开来,得到精矿1、精矿2、精矿3和尾矿1、尾矿2、尾矿3。
24.粉矿与原矿4合并后进行磨细,得到磨矿矿浆,加入碳酸钠,作用时间为2~3分钟,加入油酸,作用时间为4~5分钟,进行反浮选粗选,得到反浮选粗精矿和反浮选尾矿。反浮选尾矿扫选两次,扫选中矿返回到粗选,扫选尾矿即为精矿4。反浮选粗精矿精选两次,第一次精选中矿返回到粗选,第二次精选中矿返回到第一次精选,第二次精选精矿即为尾矿4。
25.实施例二试验结果/%
26.产品名称产率铜品位回收率精矿110.355.88532.51精矿27.684.61818.93精矿35.245.66415.84精矿43.4715.6629.00尾矿124.210.0750.97尾矿213.520.0680.49尾矿320.340.0971.05尾矿415.190.1501.22原矿100.001.874100.00
27.采用该发明,低品位大理岩型氧化铜矿石经过预选后,大理岩型脉石矿物抛除率可达到75%以上,铜品位可富集4倍以上,尾矿中损失的铜品位较少,铜资源得到充分的利用。
28.以上已将本发明做一详细说明,以上所述,仅为本发明之较佳实施例而已,当不能限定本发明实施范围,即凡依本技术范围所作均等变化与修饰,皆应仍属本发明涵盖范围内。
再多了解一些
本文用于企业家、创业者技术爱好者查询,结果仅供参考。