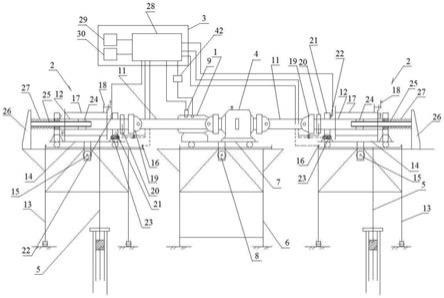
1.本发明涉及一种超长冲程采油系统及方法,特别涉及一种联动互平衡立式超长冲程采油系统及方法。
背景技术:
2.目前,低渗透石油资源广泛分布、储量大,根据相关部门开展的第三次油气评价结果,低渗透石油资源广泛分布在各大盆地,远景资源量为537
×
10λ8t,占全国石油远景资源总量的49%。中石油低渗透资源占到了其资源总量的65%以上;剩余石油资源中,低渗透石油资源量超过了75%,低渗透油田丛式井开发技术日渐成熟,中国石油每年新钻井数在2万口井左右,60%都是斜井,2000年以来仅长庆油田和大庆油田丛式井井组超过了7000个,以长庆油田为代表的“十多年来”95%以上产能建设采用丛式井组开发模式,累计减少用地40万亩,单井场组合8.7口井。
3.丛式井开发低渗透油田的技术优势如下:
4.节约土地资源减少开发难度、提高开采效率、提高经济效益;
5.工厂化钻、完井技术降低了投资;
6.工厂化储层整体套管压裂改造技术,实现了低渗透油田单井产量的最大化;
7.井站一体化建设优化简化地面集输流程;
8.为油井实现电子巡护、远程监控、智能管理开发生产管理新模式奠定了基础。
9.降低了低渗透油田的开发难度,提高了开采效率和经济效益;
10.目前开发低渗透油田采油技术,对丛式井开发仍采用游梁式抽油机或塔架式无游梁抽油机进行单机单井开发模式。设备成本高、钢材需求量大、系统效率低、能耗高等问题,与当下石油行业低油价、低产能的现状和降本增效的战略的实施形成了比较突出的矛盾,严重制约了低渗透油田的开发建设。因此,研究如何有效利用低渗透油田和丛式井自身的特点,研发与丛式井自身特点相对应的丛式井联动人工举升机械采油技术,实现通过一台电动机带动两口或数口井同时进行开采,从而有效实现节能降耗,提高系统效率,进而提高应用丛式井进行低渗透油田开发的经济效益,具有重要的意义。
11.另外,国外许多产油国都发现了低渗透油田,且丛式井钻井数量也逐渐增加。丛式井联动采油技术主要体现:在使用一台抽油机同时进行两口或数口井的开采,关注的重点:降低人力成本,针对抽油机的研究重点主要集中抽油机的模块化设计和数字化管理技术两方面。
12.国内单机多井联动采油技术:
13.主要时是双井抽油机和单机多井抽油机,塔架式一机双井抽油机与常规曲柄双向平衡游梁式双驴头双井抽油机,在投入成本、占地面积、生产参数调整、维护保养以及安全性等方面各有技术优势,也各自存在问题,具体如下:
14.一种丛式井载荷互平衡节能抽油系统,专利号:zl200920032163.2,存在问题:各井间平衡实现必须通过测试仪、计算机的分析计算确定各抽油机相位角,通过设定、调整各
抽油机的相位角实现各井之间平衡,此项操作繁杂、专业性强、实现困难,一旦某口井修井作业,开抽生产时,还需要上述操作。所以此种抽油机可操作性差,单井采油设备只是减少了一台电动机,而增加了一台传动箱,整体造价与常规抽油机相当。
15.丛式井多井柔性联动抽油机,专利号cn201120069943.1,从2012年开始,第一台样机在延长油田甘谷驿采油厂进行了现场试验。该机2012年完成室内试验后,在甘谷驿采油厂完成了现场试验。存在问题:作为主要受力元件的链条承受较大的油井载荷,频繁往复运动,对链条寿命影响较大,从现场使用情况看,整机可靠性较差,链条容易疲劳裂纹、断裂,寿命较短。
技术实现要素:
16.本发明的目的是为了解决现有的丛式井在生产过程中存在的诸多问题而提供的一种联动互平衡立式超长冲程采油系统及方法。
17.本发明提供的联动互平衡立式超长冲程采油系统包括有驱动电机、转向提升机构和控制机构,其中驱动电机通过传动变速机构与两个或数个转向提升机构相连接,驱动电机通过传动变速机构控制两个或数个转向提升机构的工作,每个转向提升机构均对应一个油井进行设置,每个转向提升机构均通过柔性抽油光杆与油井内的抽油杆连接并带动抽油泵的工作,控制机构与驱动电机相连接并控制驱动电机的工作。
18.驱动电机为变频调速电机,传动变速机构为一减速机,驱动电机和传动变速机构装配在第一桁架上,第一桁架上设置有滑轨,滑轨上装配有第一滑车,第一滑车能够沿滑轨进行移动,驱动电机和传动变速机构均装配在第一滑车上并与第一滑车同步进行移动,第一滑车的底部吊设有第一定向轮,通过第一定向轮能够使第一滑车沿第一桁架上设置的滑轨定向进行移动,驱动电机的尾轴上连接有电磁制动器,电磁制动器与控制机构相连接并由控制机构控制工作,第一桁架的底部装配有基础固定连接件,第一桁架能够通过基础固定连接件固定在基础上。
19.传动变速机构上连接有输入轴以及同转向提升机构数量相应的输出轴,传动变速机构通过输入轴与驱动电机的传动轴相连接,传动变速机构通过输出轴与转向提升机构的转轴相连接,传动变速机构上的输出轴带动转向提升机构的转轴同步进行转动。
20.每个转向提升机构均设在第二桁架上,第二桁架上也设置有滑轨,滑轨上装配有第二滑车,第二滑车能够在第二桁架上的滑轨上进行滑动,转向提升机构装配在第二滑车上并与第二滑车进行同步移动,第二滑车的底部吊设有第二定向轮,通过第二定向轮能够使第二滑车沿第二桁架上的滑轨定向进行移动,第二桁架上所设置的滑轨一端装配有行程开关,行程开关与控制机构相连接,行程开关能够把采集的数据实时传输给控制机构,转向提升机构包括有转轴和滚筒,滚筒套设在转轴上并与转轴同步进行转动,滚筒的一端装配有钳式制动器,通过钳式制动器能够控制滚筒的停止和转动,转轴的一端通过万向节联轴器与传动变速机构上的输出轴相连接,靠近万向节联轴器部位的转轴上装配有离合器,通过离合器控制转轴与输出轴的开合,转轴通过轴承和轴承座固接在第二滑车上的第一支座上,第一支座的一侧装配有编码器,第一支座的底部装配有荷载传感器,编码器和荷载传感器均与控制机构相连接,编码器和荷载传感器能够把采集的数据实时传输给控制机构,第二桁架的底部装配有滚轮,第二桁架能够在第二桁架的基础范围内进行移动。
21.转向提升机构的转轴为空心轴,空心轴内固连有螺母,螺母与转轴同步进行转动,螺母内螺接有丝杠,丝杠的外端固定在第二桁架上的第二支座上,在丝杠的导向作用下转向提升机构的转轴在转动过程中能够带动第一滑车和第二滑车分别沿第一桁架和第二桁架上的滑轨定向进行移动,丝杠的外端套设有伸缩套。
22.转向提升机构在传动变速机构的两侧对称装配有两个,传动变速机构两侧输出轴中心线与两个油井中心连线之间的夹角为≥5
°
并≤10
°
,两个油井井口之间的距离为5-8米,每个转向提升机构上的滚筒上均绕设有柔性抽油光杆,两个滚筒上的柔性抽油光杆进行反向缠绕,两个滚筒在进行同步转动过程中能够使反向缠绕的两部分柔性抽油光杆进行相向运动。
23.控制机构包括有可编程控制器plc、人机界面和远程数据传输单元,其中人机界面和远程数据传输单元均与可编程控制器plc相连接,可编程控制器plc与驱动电机相连接,可编程控制器plc与驱动电机的连接线路上装配有变频器,变频器接收可编程控制器plc的指令控制驱动电机的工作,可编程控制器plc还分别与行程开关、编码器、荷载传感器和电磁制动器相连接,行程开关、编码器和荷载传感器能够把采集的数据实时传输给可编程控制器plc,可编程控制器plc控制电磁制动器的工作,可编程控制器plc能够把采集的数据通过人机界面进行显示,人机界面用于设定工作参数和显示整个系统运行数据,远程数据传输单元由通讯设备、天线和备用电源组成,远程数据传输单元利用无线数据传输系统将载荷数据、位移数据、运行参数和故障报警数据信息发送到用户的手机或计算机终端上,同时用户也能够利用手机或计算机远程控制采油系统的运行。
24.转向提升机构中滚筒上绕设的柔性抽油光杆为钢丝绳,钢丝绳的下端与采油系统设置的内工作筒中的密封柱塞相连接,密封柱塞在钢丝绳的带动下进行上下运动进行抽油作业,内工作筒外套设有外工作筒,内工作筒和外工作筒之间形成有环形通道,外工作筒的顶部设置有油管四通,内工作筒插设在油管四通内,油管四通与内工作筒之间的环形空间内装配有回流单向阀,回流单向阀的入口与内工作筒的内腔相连通,回流单向阀的出口与油管四通相连通。
25.钢丝绳的下端与密封柱塞连接处装配有钢丝绳套接件,钢丝绳套接件的上部装配有钢丝绳回流光杆,油管四通的顶部连接有回流光杆盘根盒,回流光杆盘根盒内从上至下依次安装有钢丝绳刮油轮、盘根补偿弹簧和回流光杆盘根。
26.上述的驱动电机、行程开关、离合器、编码器、荷载传感器、钳式制动器、可编程控制器plc、人机界面和远程数据传输单元均为现有设备的组装,因此,具体型号和规格没有进行赘述。
27.本发明提供的联动互平衡立式超长冲程采油方法,其方法包括如下步骤:
28.第一步、根据油井给定的下泵深度和排液量进行采油系统的配置;
29.第二步、按照油田设计要求现场施工第一桁架和第二桁架的安装基础,然后将第一桁架和第二桁架进行安装,第一桁架和第二桁架安装完成后,将驱动电机和传动变速机构、转向提升机构分别装配到第一桁架和第二桁架上;
30.第三步、装配两个转向提升机构时,两个转向提升机构滚筒上缠绕的钢丝绳出绳方向不同,在系统装置现场安装时输出轴轴线与两口井井口中心连线成5
°‑
10
°
安装,两口井地面井口距离在5m-8m;
31.第四步、按照抽油泵冲程损失比率≤10%确定不同泵挂深度允许最小冲程长度,系统的提液量通过q=360πd^2η
×n×
s进行计算,对于给定排量的系统,增加抽油机的冲程和泵径能够降低抽油机的冲次,采用长冲程、低冲次和较大泵径的抽吸工艺,用一个动力源驱动两个转向提升机构进行采油生产,两口井的冲程、冲数一致,在长冲程、低冲数抽汲速度sn最大的情况下,仍无法满足其中某一口井的提液量需求时,两口井通过采取不同泵径生产,高产液量井采用较大泵径来满足提液需求;
32.第五步、系统装置平衡方式为利用两口井的井下杆柱载荷互为平衡,平衡率为90%及以上;
33.第六步、用一套动力源驱动两套转向提升机构进行油井采油生产,在投产进行调试时,逐一进行调试,调试时其中一口停留在上死点则另一口井必须停留在下死点,调试结束后将输出轴和滚筒转轴之间的离合器进行啮合;
34.第七步、用一套动力源驱动两套转向提升机构进行采油生产,其中某一口井修井作业时,通过输出轴和滚筒转轴之间的离合器将转轴和输出轴分离开来,并将装置移出距离井口700cm以上满足油井修井作业要求,另外一口井则保持正常工作生产而不受影响。
35.本发明的工作原理:
36.本发明提供的联动互平衡立式超长冲程采油系统及方法中的控制机构通过编码器和行程开关采集的位移信息通过控制机构的逻辑分析判断控制驱动电机正反向旋转带动传动变速机构双翼输出轴驱动两套转向提升机构中的滚筒进行正反向输出,缠绕在两滚筒上的钢丝绳随滚筒的正反向旋转做上下往复运动,由于两滚筒上缠绕的钢丝绳旋向相反,当其中之一为上行时则另一为下行,届时两口油井井下抽油杆载荷实现互平衡,并且能够保证钢丝绳始终位于井口的中心部位。
37.输出轴连接的两滚筒空心轴在转动过程中带动螺母和滚筒空心轴沿丝杠进行直线移动,驱动电机、滚筒和传动变速机构均分别固定在各机构小车底座上,螺母在进行直线移动时带动小车底座沿各自桁架平台轨道进行滑动,本发明设计为螺母每旋转一周小车行走距离为滚筒绳槽节距,滚筒上缠绕的钢丝绳牵引井下抽油杆和有杆抽油泵做往复运动,完成同一动力源驱动两口油井互平衡采油举升。
38.编码器装配在滚筒一侧轴承支座上,编码器的输出连接到控制机构内的可编程控制器plc上,在可编程控制器plc里对收到编码器的脉冲进行方向判断和累计计数,此计数的结果与缠绕在滚筒上的钢丝绳的长度成正比,也就是测出了钢丝绳上下冲程的位移长度,根据相应的逻辑关系控制驱动电机的正转或反转,实现抽油机上下冲程和滚筒同步排绳换向动作。
39.控制机构测量示功图时,从下死点行程开关接通,远程数据传输单元开始启动,荷载传感器开始检测油井上下冲程井下载荷的变化,载荷信号传送至可编程控制器plc,可编程控制器plc通过有线或无线通信模块发送数据给远程数据传输单元,编码器输出信号计算出的钢丝绳位移量和荷载传感器测得的井下载荷变化量配对,当一冲次周期结束时,载荷和位移关系曲线即油井示功图就测量完成。
40.人机界面与可编程控制器plc连接,用于设定工作参数和显示整个抽油机系统运行数据。远程数据传输单元和可编程控制器plc连接,可通过无线信号传输实现系统的远程操控。
41.本发明的有益效果:
42.本发明提供的联动互平衡立式超长冲程采油系统及方法能够有效利用低渗透油田和丛式井自身的特点,研发与丛式井自身特点相对应的丛式井联动人工举升机械采油技术,实现通过一台电动机带动两口或数口井同时进行开采,降低了设备成本,节约了大量钢材,有效实现节能降耗,提高系统效率,进而提高应用丛式井进行低渗透油田开发的经济效益,具有重要的意义。
43.本发明能够实现用一套动力源及传动变速系统同时驱动两口井,抽油机冲程长度只与滚筒钢丝绳在滚筒上缠绕的圈数和小车轴向移动距离有关,与抽油机其他机构参数无关,充分利用两井间的土地面积,两口油井井口有效距离在5-8m即可安装使用,减少了抽油机占地面积,立式结构减少了超长冲程抽油机井口支架和滑轮,三台小车在排绳换向牵引机构的驱动下沿桁架平台轨道在抽油泵上下往复运动的同时做同步轴向滑动,保证了钢丝绳做为抽油光杆始终位于井口中心部位;
44.本发明提供的技术方案利用两口悬点载荷实现上下冲程的互平衡,平衡率达到100%,节能效果更好,有效解决了超长冲程抽油机尤其是10型以上抽油机无平衡、节能效果差的技术瓶颈问题;
45.本发明提供的技术方案代替了游梁式抽油机四连杆和塔架式抽油机高高的塔架,利用滚筒的旋转运行特征实现原动机旋转运动转换为直线运动,缠绕的钢丝绳由于采用不同旋向缠绕,在滚筒同向旋转的情况下,实现两口油井井下有杆抽油泵上下往复相向运动,相向运动调整操作方便简单,抽油机能够在传动轴中心线和两口油井井口中心连线夹角σ≥5
°
并≤10
°
安装使用,同时采用电控和机械换向机电一体化设计,使抽油机的传动、转换机构更加简单,传动环节少,故障率低势必可靠耐用,维护容易。
46.本发明提供的技术方案实现了用石油专用钢丝绳替代现有的采取特殊工艺在钢丝绳主体外层整体包覆耐磨复合材料的钢丝绳做为抽油光杆成为可能,并在钢丝绳上设置有井下密封器,实现立式超长冲程(》10m)抽油机机型突破10型以上,解决了深井、中深井应用现有杆泵机械采油冲程损失大、效率低的问题,满足油层埋藏深、低渗难采储量的有效开发利用。
47.本发明采用智能控制 物联网的结合设计,使抽油机使用操作、采油生产管理简便容易;改变了传统的采油生产管理模式;
48.本发明提供的系统结构紧固、润滑点少,无需人工调平衡、调冲数换皮带轮,紧固、润滑保养智能提示管理,当其中的一口油井修井作业时,通过传动轴和滚筒轴之间的牙嵌式离合器即可将系统与其分离,则另一口井能够正常生产而不受其影响,调参方便,通过抽油机智能控制系统人机对话操作完成,不用调平衡、对防冲距、示功图自动测试,有效降低了工人的劳动强度和使用操作安全风险,优化简化了岗位操作人员结构。
49.抽油光杆使用的安全系数提高,按额定载荷计算抽油光杆安全使系数达到3.5以上,符合安全使用规范,而且机型能够达到10型以上,满足中深井和深井开发生产的需要。
50.本发明提供的系统有效延长了地面设备井下杆管的使用寿命,使悬点最大载荷减小,最小载荷增大,减小悬点载荷的波动,有效减轻径向偏磨力,有效降低抽油杆的疲劳损伤及偏磨程度,延长管杆寿命,同样降低了地面设备的运行磨损,延长了地面设备的使用寿命。
51.以油井日产量5吨,泵效60%计算,现有的游梁式抽油机的工作状态为:冲程4.2米、泵径32毫米、冲数2次/分钟,一天运行2880循环周期。本发明提供的系统工作状态为:冲程30米、泵径44毫米、冲数8次/小时,一天运行192循环周期。现有的游梁抽油机循环往复的次数是本发明提供的系统的15倍。
52.本发明提供的智能控制系统能够组成抽油机的闭环控制系统,有效解决机械采油两个能力的匹配问题:一是每天将有多少液体能够渗入到油井;二是渗入到油井的液量需要多大排量的抽汲参数组合将其举升到地面,实现本质节能。
附图说明
53.图1为本发明所述的采油系统主视图。
54.图2为本发明所述的采油系统俯视图。
55.图3为本发明所述的传动轴与两井口中心线夹角关系示意图。
56.图4为本发明所述的柔性抽油光杆与油井连接关系示意图。
57.图5为本发明所述的钢丝绳与密封柱塞连接关系示意图。
58.上图中的标注如下:
59.1、驱动电机
ꢀꢀ
2、转向提升机构
ꢀꢀ
3、控制机构
ꢀꢀ
4、传动变速机构
60.5、柔性抽油光杆
ꢀꢀ
6、第一桁架
ꢀꢀ
7、第一滑车
ꢀꢀ
8、第一定向轮
61.9、电磁制动器
ꢀꢀ
10、输入轴
ꢀꢀ
11、输出轴
ꢀꢀ
12、转轴
ꢀꢀ
13、第二桁架
62.14、第二滑车 15、第二定向轮 16、行程开关 17、滚筒
ꢀꢀ
18、钳式制动器
63.19、万向节联轴器
ꢀꢀ
20、离合器
ꢀꢀ
21、第一支座
ꢀꢀ
22、编码器
64.23、荷载传感器
ꢀꢀ
24、螺母
ꢀꢀ
25、丝杠
ꢀꢀ
26、第二支座
ꢀꢀ
27、伸缩套
65.28、可编程控制器 plc
ꢀꢀ
29、人机界面
ꢀꢀ
30、远程数据传输单元
66.31、内工作筒
ꢀꢀ
32、密封柱塞
ꢀꢀ
33、外工作筒
ꢀꢀ
34、油管四通
67.35、回流单向阀
ꢀꢀ
36、钢丝绳套接件
ꢀꢀ
37、钢丝绳回流光杆
68.38、回流光杆盘根盒
ꢀꢀ
39、钢丝绳刮油轮
ꢀꢀ
40、盘根补偿弹簧
69.41、回流光杆盘根
ꢀꢀ
42、变频器。
具体实施方式
70.请参阅图1至图5所示:
71.本发明提供的联动互平衡立式超长冲程采油系统包括有驱动电机1、转向提升机构2和控制机构3,其中驱动电机1通过传动变速机构4与两个或数个转向提升机构2相连接,驱动电机1通过传动变速机构4控制两个或数个转向提升机构2的工作,每个转向提升机构2均对应一个油井进行设置,每个转向提升机构2均通过柔性抽油光杆5与油井内的抽油杆连接并带动抽油泵的工作,控制机构3与驱动电机1相连接并控制驱动电机1的工作。
72.驱动电机1为变频调速电机,传动变速机构4为一减速机,驱动电机1和传动变速机构4装配在第一桁架6上,第一桁架6上设置有滑轨,滑轨上装配有第一滑车7,第一滑车7能够沿滑轨进行移动,驱动电机1和传动变速机构4均装配在第一滑车7上并与第一滑车7同步进行移动,第一滑车7的底部吊设有第一定向轮8,通过第一定向轮8能够使第一滑车7沿第一桁架6上设置的滑轨定向进行移动,驱动电机1的尾轴上连接有电磁制动器9,电磁制动器
9与控制机构3相连接并由控制机构3控制工作,第一桁架6的底部装配有基础固定连接件,第一桁架6能够通过基础固定连接件固定在基础上。
73.传动变速机构4上连接有输入轴10以及同转向提升机构2数量相应的输出轴11,传动变速机构4通过输入轴10与驱动电机1的传动轴相连接,传动变速机构4通过输出轴11与转向提升机构2的转轴12相连接,传动变速机构4上的输出轴11带动转向提升机构2的转轴12同步进行转动。
74.每个转向提升机构2均设在第二桁架13上,第二桁架13上也设置有滑轨,滑轨上装配有第二滑车14,第二滑车14能够在第二桁架13上的滑轨上进行滑动,转向提升机构2装配在第二滑车14上并与第二滑车14进行同步移动,第二滑车14的底部吊设有第二定向轮15,通过第二定向轮15能够使第二滑车14沿第二桁架13上的滑轨定向进行移动,第二桁架13上所设置的滑轨一端装配有行程开关16,行程开关16与控制机构3相连接,行程开关16能够把采集的数据实时传输给控制机构3,转向提升机构2包括有转轴12和滚筒17,滚筒17套设在转轴12上并与转轴12同步进行转动,滚筒17的一端装配有钳式制动器18,通过钳式制动器18能够控制滚筒17的停止和转动,转轴12的一端通过万向节联轴器19与传动变速机构4上的输出轴11相连接,靠近万向节联轴器19部位的转轴12上装配有离合器20,通过离合器20控制转轴12与输出轴11的开合,转轴12通过轴承和轴承座固接在第二滑车14上的第一支座21上,第一支座21的一侧装配有编码器22,第一支座21的底部装配有荷载传感器23,编码器22和荷载传感器23均与控制机构3相连接,编码器22和荷载传感器23能够把采集的数据实时传输给控制机构3,第二桁架13的底部装配有滚轮,第二桁架13能够在第二桁架13的基础范围内进行移动。。
75.转向提升机构2的转轴12为空心轴,空心轴内固连有螺母24,螺母24与转轴12同步进行转动,螺母24内螺接有丝杠25,丝杠25的外端固定在第二桁架13上的第二支座26上,在丝杠25的导向作用下转向提升机构2的转轴12在转动过程中能够带动第一滑车7和第二滑车14分别沿第一桁架6和第二桁架13上的滑轨定向进行移动,丝杠25的外端套设有伸缩套27。
76.转向提升机构2在传动变速机构4的两侧对称装配有两个,传动变速机构4两侧输出轴11中心线与两个油井中心连线之间的夹角为≥5
°
并≤10
°
,两个油井井口之间的距离为5-8米,每个转向提升机构2上的滚筒17上均绕设有柔性抽油光杆5,两个滚筒17上的柔性抽油光杆5进行反向缠绕,两个滚筒17在进行同步转动过程中能够使反向缠绕的两部分柔性抽油光杆5进行相向运动。
77.控制机构3包括有可编程控制器plc28、人机界面29和远程数据传输单元30,其中人机界面29和远程数据传输单元30均与可编程控制器plc28相连接,可编程控制器plc28与驱动电机1相连接,可编程控制器plc28与驱动电机1的连接线路上装配有变频器42,变频器42接收可编程控制器plc28的指令控制驱动电机1的工作,可编程控制器plc28还分别与行程开关16、编码器22、荷载传感器23和电磁制动器9相连接,行程开关16、编码器22和荷载传感器23能够把采集的数据实时传输给可编程控制器plc28,可编程控制器plc28控制电磁制动器9的工作,可编程控制器plc28能够把采集的数据通过人机界面29进行显示,人机界面29用于设定工作参数和显示整个系统运行数据,远程数据传输单元30由通讯设备、天线和备用电源组成,远程数据传输单元30利用无线数据传输系统将载荷数据、位移数据、运行参
数和故障报警数据信息发送到用户的手机或计算机终端上,同时用户也能够利用手机或计算机远程控制采油系统的运行。
78.转向提升机构2中滚筒17上绕设的柔性抽油光杆5为钢丝绳,钢丝绳的下端与采油系统设置的内工作筒31中的密封柱塞32相连接,密封柱塞32在钢丝绳的带动下进行上下运动进行抽油作业,内工作筒31外套设有外工作筒33,内工作筒31和外工作筒33之间形成有环形通道,外工作筒33的顶部设置有油管四通34,内工作筒31插设在油管四通34内,油管四通34与内工作筒31之间的环形空间内装配有回流单向阀35,回流单向阀35的入口与内工作筒31的内腔相连通,回流单向阀35的出口与油管四通34相连通。
79.钢丝绳的下端与密封柱塞32连接处装配有钢丝绳套接件36,钢丝绳套接件36的上部装配有钢丝绳回流光杆37,油管四通34的顶部连接有回流光杆盘根盒38,回流光杆盘根盒38内从上至下依次安装有钢丝绳刮油轮39、盘根补偿弹簧40和回流光杆盘根41。
80.上述的驱动电机1、行程开关16、离合器20、编码器22、荷载传感器23、钳式制动器18、可编程控制器plc28、人机界面29和远程数据传输单元30均为现有设备的组装,因此,具体型号和规格没有进行赘述。
81.本发明提供的联动互平衡立式超长冲程采油方法,其方法包括如下步骤:
82.第一步、根据油井给定的下泵深度和排液量进行采油系统的配置;
83.第二步、按照油田设计要求现场施工第一桁架6和第二桁架13的安装基础,然后将第一桁架6和第二桁架13进行安装,第一桁架6和第二桁架13安装完成后,将驱动电机1和传动变速机构4、转向提升机构2分别装配到第一桁架6和第二桁架13上;
84.第三步、装配两个转向提升机构2时,两个转向提升机构2滚筒17上缠绕的钢丝绳出绳方向不同,在系统装置现场安装时输出轴11轴线与两口井井口中心连线成5
°‑
10
°
安装,两口井地面井口距离在5m-8m。
85.第四步、按照抽油泵冲程损失比率≤10%确定不同泵挂深度允许最小冲程长度,系统的提液量通过q=360πd^2η
×n×
s进行计算,对于给定排量的系统,增加抽油机的冲程和泵径能够降低抽油机的冲次,采用长冲程、低冲次和较大泵径的抽吸工艺,用一个动力源驱动两个转向提升机构2进行采油生产,两口井的冲程、冲数一致,在长冲程、低冲数抽汲速度sn最大的情况下,仍无法满足其中某一口井的提液量需求时,两口井通过采取不同泵径生产,高产液量井采用较大泵径来满足提液需求;
86.第五步、系统装置平衡方式为利用两口井的井下杆柱载荷互为平衡,平衡率为90%及以上;
87.第六步、用一套动力源驱动两套转向提升机构2进行油井采油生产,在投产进行调试时,逐一进行调试,调试时其中一口停留在上死点则另一口井必须停留在下死点,调试结束后将输出轴11和滚筒17转轴12之间的离合器20进行啮合;
88.第七步、用一套动力源驱动两套转向提升机构2进行采油生产,其中某一口井修井作业时,通过输出轴11和滚筒17转轴12之间的离合器20将转轴12和输出轴11分离开来,并将装置移出距离井口700cm以上满足油井修井作业要求,另外一口井则保持正常工作生产而不受影响。
89.本发明的工作原理:
90.本发明提供的联动互平衡立式超长冲程采油系统及方法中的控制机构3通过编码
器22和行程开关16采集的位移信息通过控制机构3的逻辑分析判断控制驱动电机1正反向旋转带动传动变速机构4双翼输出轴11驱动两套转向提升机构2中的滚筒17进行正反向输出,缠绕在两滚筒17上的钢丝绳随滚筒17的正反向旋转做上下往复运动,由于两滚筒17上缠绕的钢丝绳旋向相反,当其中之一为上行时则另一为下行,届时两口油井井下抽油杆载荷实现互平衡,并且能够保证钢丝绳始终位于井口的中心部位。
91.输出轴11连接的两滚筒17空心轴在转动过程中带动螺母24和滚筒17空心轴沿丝杠25进行直线移动,驱动电机1、滚筒17和传动变速机构4均分别固定在各机构小车底座上,螺母24在进行直线移动时带动小车底座沿各自桁架平台轨道进行滑动,本发明设计为螺母24每旋转一周小车行走距离为滚筒17绳槽节距,滚筒17上缠绕的钢丝绳牵引井下抽油杆和有杆抽油泵做往复运动,完成同一动力源驱动两口油井互平衡采油举升。
92.编码器22装配在滚筒17一侧轴承支座上,编码器22的输出连接到控制机构3内的可编程控制器plc28上,在可编程控制器plc28里对收到编码器22的脉冲进行方向判断和累计计数,此计数的结果与缠绕在滚筒17上的钢丝绳的长度成正比,也就是测出了钢丝绳上下冲程的位移长度,根据相应的逻辑关系控制驱动电机1的正转或反转,实现抽油机上下冲程和滚筒17同步排绳换向动作。
93.控制机构3测量示功图时,从下死点行程开关16接通,远程数据传输单元30开始启动,荷载传感器23开始检测油井上下冲程井下载荷的变化,载荷信号传送至可编程控制器plc28,可编程控制器plc28通过有线或无线通信模块发送数据给远程数据传输单元30,编码器22输出信号计算出的钢丝绳位移量和荷载传感器23测得的井下载荷变化量配对,当一冲次周期结束时,载荷和位移关系曲线即油井示功图就测量完成。
94.人机界面29与可编程控制器plc28连接,用于设定工作参数和显示整个抽油机系统运行数据。远程数据传输单元30和可编程控制器plc28连接,可通过无线信号传输实现系统的远程操控。
再多了解一些
本文用于企业家、创业者技术爱好者查询,结果仅供参考。