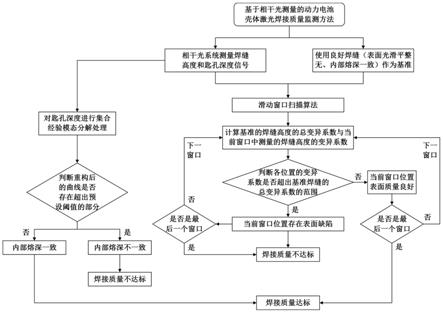
1.本发明属于质量监测领域,更具体地,涉及一种基于相干光测量的动力电池壳体激光焊接质量监测。
背景技术:
2.在动力电池模组的生产制造过程中,需要对电池壳体进行密封焊接,保证壳体良好的气密性,同时防止内部电解液的泄露,保障着电动汽车的安全性。目前,动力电池壳体选用材料一般为3系铝合金。激光焊接工艺以其焊缝窄、焊接速度快,焊接过程中产生的热量与热变形更低等特性对于电池壳体及其模组的连接具有良好的适用性,已经广泛应用在工厂动力电池壳体密封焊接。
3.但是激光焊接工艺在实际应用于动力电池壳体密封焊接过程中还存在诸多挑战。比如,方形密封壳体的板厚很薄,一旦焊接过程不稳定极易产生焊接缺陷,如表面凸起或塌陷、内部熔深不一致等,导致焊接质量下降,如果没有及时发现会造成严重的安全事故。例如,动力电池壳体在焊接后焊缝的表面质量是影响动力电池模组的服役寿命的重要因素,表面存在凸起等缺陷时会对电池模组其他部分产生剐蹭、碰撞的风险,而表面存在凹陷时会导致焊缝强度不足,因此在焊接过程中要严格控制表面质量;此外,动力电池的制造对良品率要求极高(单工序良品率≥99.8%),特别是壳体的焊接过程中焊缝下方由于熔深的存在产生的热扩散会对电池内部的电解液产生影响,而熔深又决定了焊缝强度进而对壳体的连接强度有极大影响,因此在焊接过程中也要严格控制熔深。目前,对于3系铝合金薄板激光焊接工艺机理国内外均有许多研究,但在实际的动力电池壳体激光焊接过程中,上述诸多问题难以通过工艺调整完全避免,缺乏动力电池壳体激光焊接质量实时监测的有效方法。
技术实现要素:
4.针对现有技术的以上缺陷或改进需求,本发明提供了一种动力电池壳体激光焊接质量的在线监测方法,对于监测并评估动力电池壳体激光焊接过程中的焊缝表面质量优劣与内部熔深一致性以保障焊接质量等具有重要的意义。
5.为实现上述目的,按照本发明的第一方面,提供了一种动力电池壳体激光焊接质量的在线监测方法,包括:
6.s1,基于相干光测量系统获取当前焊接过程中的焊缝高度h(t)及匙孔深度d(t);
7.s2,基于滑动窗口算法对h(t)进行扫描,计算滑动窗口i对应的焊缝高度的变异系数cvi,若|cvi|≤|cv
norm
|,则表面质量良好,否则所述滑动窗口处存在表面缺陷;其中,cv
norm
为基准焊缝的焊缝高度h(t)的总变异系数;
8.s3,对d(t)进行集合经验模态分解处理得到d(t)`,若d(t)`的波动在预设区间范围内,则内部熔深一致,否则内部熔深不一致;其中,为d(t)`的均值,μ和
s0分别为d(t)`的均值和标准差,d(t)`由将基准焊缝的匙孔深度d(t)进行集合经验模态分解处理得到的。
9.优选地,所述基准焊缝的焊缝高度波动范围不超过其平均值的5%,匙孔深度波动范围不超过其平均值的10%。
10.优选地,所述基准焊缝的焊缝高度的总变异系数cv
norm
的计算公式为:
[0011][0012]
其中,cv
norm
为基准焊缝的焊缝高度数据的总变异系数,hk(t)为各数据点,为所有数据的平均值。
[0013]
优选地,所述滑动窗口i对应的焊缝高度的变异系数cvi的计算公式为:
[0014][0015]
其中,为窗口中的各数据点,为每个窗口中的数据的平均值。
[0016]
优选地,所述动力电池壳体材料为铝合金。
[0017]
优选地,集合经验模态分解公式为:
[0018][0019]
其中,y(t)为待分解的原始信号,ci(t)为分解项中的第i个固有模函数,rn(t)为分解之后得到的余项,n为分解后得到的项的总个数。
[0020]
按照本发明的第二方面,提供了一种基于相干光测量的动力电池壳体激光焊接质量监测系统,包括:计算机可读存储介质和处理器;
[0021]
所述计算机可读存储介质用于存储可执行指令;
[0022]
所述处理器用于读取所述计算机可读存储介质中存储的可执行指令,执行如第一方面所述的方法。
[0023]
总体而言,通过本发明所构思的以上技术方案与现有技术相比,能够取得下列有益效果:
[0024]
1、本发明提供的基于相干光测量的动力电池壳体激光焊接质量监测方法,采用集成于激光头的相干光测量系统获取动力电池壳体激光焊接过程焊缝高度与匙孔深度信息,以良好焊缝(表面光滑平整、内部熔深一致)作为监测基准,实现对动力电池壳体激光焊接质量的在线监测。该方法为动力电池壳体激光焊接生产线质量监测提供了一种新的手段,能够避免繁琐的焊后检测,提高生产效率,具有灵活性高、鲁棒性好、可适用于不同工艺参数等优点。
[0025]
2、本发明提供的基于相干光测量的动力电池壳体激光焊接质量监测方法,计算简单,有利于实现完全自动化;借助相干光测量系统获取到焊缝高度信号与匙孔深度信号,进
而对动力电池壳体激光焊接过程的表面质量优劣与内部熔深一致性同步进行监测,综合判断焊接质量是否达标,对动力电池壳体安全保障具有重要意义。
附图说明
[0026]
图1为本发明实施例提供的基于相干光测量的动力电池壳体激光焊接质量监测方法流程示意图;
[0027]
图2为相干光测量系统的结构示意图;
[0028]
图3为本发明实施例提供的动力电池壳体激光焊接焊缝表面质量监测结果示意图之一;
[0029]
图4为本发明实施例提供的动力电池壳体激光焊接焊缝表面质量监测结果示意图之二;
[0030]
图5为本发明实施例提供的动力电池壳体激光焊接焊缝内部熔深监测结果示意图之一;
[0031]
图6为本发明实施例提供的动力电池壳体激光焊接焊缝内部熔深监测结果示意图之二;
[0032]
图7为本发明实施例提供的产品处理示意图。
具体实施方式
[0033]
为了使本发明的目的、技术方案及优点更加清楚明白,以下结合附图及实施例,对本发明进行进一步详细说明。应当理解,此处所描述的具体实施例仅仅用以解释本发明,并不用于限定本发明。此外,下面所描述的本发明各个实施方式中所涉及到的技术特征只要彼此之间未构成冲突就可以相互组合。
[0034]
本发明实施例提供一种基于相干光测量的动力电池壳体激光焊接质量监测方法,如图1所示,包括:
[0035]
s1,基于相干光测量系统获取当前焊接过程中的焊缝高度h(t)及匙孔深度d(t)。
[0036]
具体地,在步骤s1之前,首先基于相干光测量系统获取基准焊缝在焊接过程中的焊缝高度h(t)及匙孔深度d(t),根据h(t)计算基准焊缝的焊缝高度的总变异系数cv
norm
;对d(t)进行集合经验模态分解处理得到d(t)`。
[0037]
其中,所述基准焊缝的焊缝高度波动范围不超过其平均值的5%,匙孔深度波动范围不超过其平均值的10%。也即,所述基准焊缝定义为:表面质量要求为焊缝高度波动范围不超过其平均值的5%,内部熔深要求为熔深波动范围不超过其平均值的10%。
[0038]
本发明提出的监测方法所依靠的硬件系统为相干光测量系统,借助该系统能够获取动力电池壳体激光焊接过程焊缝高度、匙孔深度等特征信号。
[0039]
良好的动力电池壳体激光焊接工艺参数(激光功率、焊接速度、离焦量)的确定、基准焊缝的选取、处理算法的选择使用以及监测阈值的设置是本方法的关键点。
[0040]
优选地,所述动力电池壳体材料为铝合金。
[0041]
在基准焊缝所对应的良好工艺参数与较少的环境干扰的条件下进行3003铝合金激光焊接工艺实验,通过相干光测量系统获取基准焊缝在焊接过程中焊缝高度与匙孔深度沿焊缝长度方向变化的数据,作为后续动力电池壳体实际焊接过程中判断所监测的焊缝的
焊接质量是否达标的基准。
[0042]
进一步地,模拟实际动力电池壳体激光焊接过程中的焊接环境并且在焊前打磨3003铝合金薄板,用丙酮/酒精清洗表面,去除氧化膜与污渍,避免此类因素对焊接接头质量产生影响。
[0043]
其中,如图2所示,相干光测量系统集成于激光头上,在焊前将相干光测量系统中振镜摆动范围即从匙孔到后方焊缝的总测量范围设置为4mm,采样频率设置为1000hz。
[0044]
优选地,在步骤s1和获取基准焊缝在焊接过程中的焊缝高度h(t)及匙孔深度d(t)的过程中,相干光测量系统的参数设置相同。也即,在焊前将相干光测量系统中参数设置为与步骤s11中相同。
[0045]
具体地,在动力电池壳体实际焊接过程中,通过相干光测量系统在线获取当前所监测的焊接过程中焊缝高度与匙孔深度沿焊缝长度方向变化的数据。
[0046]
可以理解的是,焊缝高度沿焊缝长度方向变化的数据的纵坐标仍为h(t),横坐标为t与焊接速度的乘积,匙孔深度沿焊缝长度方向变化的数据的纵坐标仍为d(t),横坐标为t与焊接速度的乘积。
[0047]
s2,基于滑动窗口算法对h(t)进行扫描,计算滑动窗口i对应的焊缝高度的变异系数cvi,若|cvi|≤|cv
norm
|,则表面质量良好,否则所述滑动窗口处存在表面缺陷;其中,cv
norm
为基准焊缝的焊缝高度h(t)的总变异系数。
[0048]
优选地,所述基准焊缝的焊缝高度的总变异系数cv
norm
的计算公式为:
[0049][0050]
其中,cvi为焊接过程中各窗口位置处的焊缝高度数据的变异系数,cv
norm
为基准焊缝的焊缝高度数据的总变异系数,hk(t)为各数据点,为所有数据的平均值。
[0051]
优选地,所述滑动窗口i对应的焊缝高度的变异系数cvi的计算公式为:
[0052][0053]
其中,cv
norm
为基准焊缝的焊缝高度数据的总变异系数,为基准焊缝的焊缝高度数据的总变异系数,为窗口中的各数据点,为每个窗口中的数据的平均值。
[0054]
具体地,对所监测的动力电池壳体激光焊接过程中实时获得的焊缝高度数据采用滑动窗口算法进行扫描。
[0055]
分别计算所监测焊缝各个位置的窗口中焊缝高度数据的变异系数,并与基准焊缝的焊缝高度数据的总变异系数进行对比,如果所监测的焊缝各窗口位置中焊缝高度变异系数均未超出基准焊缝的焊缝高度的总变异系数的范围,则表面质量良好(焊缝不存在与电
池模组其它部分产生刮蹭、碰撞的风险,且保证了焊缝强度);否则在超出范围的窗口位置处存在表面缺陷(导致上述风险的存在或焊缝强度不足)。
[0056]
优选地,滑动窗口尺寸设置为10(每个窗口中包含10个数据点)、步长设置为10(每次向前移动10个数据点)。
[0057]
s3,对d(t)进行集合经验模态分解处理得到d(t)`,若d(t)`的波动在预设区间范围内,则内部熔深一致,否则内部熔深不一致;其中,为d(t)`的均值,μ和s0分别为d(t)`的均值和标准差,d(t)`由将基准焊缝的匙孔深度d(t)进行集合经验模态分解处理得到的。
[0058]
具体地,由于原始的匙孔深度数据震荡较大,难以提取有效特征,采用集合经验模态分解算法对其趋势项进行提取,趋势项中包含了局部特征,从而获得高信噪比、特征明显的匙孔深度数据,基于该数据进行内部一致性判断,从而提高监测精度。
[0059]
进一步地,集合经验模态分解算法是通过将白噪声均匀分布在整个时频空间,使时频空间被滤波器组分割成不同尺度成分,分解公式为:
[0060][0061]
其中,y(t)为待分解的原始信号,ci(t)为分解项中的第i个固有模函数,rn(t)为分解之后得到的余项,n为分解后得到的项的总个数。
[0062]
参数选择为:添加的白噪声的标准差与原始信号的标准差的比值为0.2、集合数量为100;集合经验模态分解将原始信号自适应地分为11个固有模函数和1个余项,其中将固有模函数1-6设置为高频分量,固有模函数7-11和余项设置为低频分量。使用6个低频分量来重构原始信号。
[0063]
具体地,对所监测的动力电池壳体激光焊接过程中实时获得的匙孔深度信号采用集合经验模态分解算法进行处理并重构信号。
[0064]
判断重构后的匙孔深度信号曲线是否存在超出预设阈值的部分,如果各位置均未超出,说明内部熔深一致(既不会由于焊缝某位置熔深过大而对焊缝下方电解液产生过量的热影响,也不会由于焊缝某位置熔深过小导致焊缝强度不足);否则内部熔深不一致(导致电解液受热超标或焊缝强度不足)。
[0065]
如果所监测焊缝的表面质量良好且内部熔深一致,则该动力电池壳体焊接质量达标;否则根据厂家具体要求进行后续处理。
[0066]
预设阈值计算公式为:
[0067][0068]
式中,th为用于监测当前焊接过程的内部熔深是否一致的阈值,如果所监测焊缝的各位置的匙孔深度均位于的范围之内,则内部熔深一致;否则不一致。为所监测焊缝的经集合经验模态分解重构后的匙孔深度数据的均值,μ为基准焊缝的经集合经验模态分解重构后的匙孔深度数据的均值,s0为基准焊缝的经集合经验模态分解重构后的匙孔深度数据的标准差。
[0069]
本发明公开的动力电池壳体激光焊接质量在线监测方法可以采用的数据处理算
法有多种,本发明所述的具体算法及流程只是其中一种,也可以根据不同的生产环境,进行具体的调整。
[0070]
下面以一个具体的例子对本发明提供的方法进一步进行说明。
[0071]
(1)进行动力电池壳体所用的3003铝合金薄板的激光焊接工艺实验,建立动力电池壳体焊接质量监测评估基准。实验前对3003铝合金薄板加工表面进行打磨,去除表面氧化膜,随后用丙酮/酒精清洗加工表面,去除金属表面残留污渍。
[0072]
需要说明的是实验采用2mm厚的3003铝合金薄板进行激光焊接实验,动力电池壳体的材料通常采用防锈性能好的3系铝合金,且焊接过程中对焊缝的表面质量和内部熔深控制有严格的要求。
[0073]
(2)打开相干光测量系统与激光器,在动力电池壳体的待焊位置处标定匙孔中心,在示教器上根据动力电池壳体的空间位置调整机器人位姿并设定激光功率、焊接速度,根据动力电池壳体外形设置焊接路径,在相干光测量系统用户界面设置参数如下:振镜摆动范围即从匙孔到后方焊缝的总测量范围设置为4mm,采样频率设置为1000hz。装夹工件,进行激光焊接工艺实验,获取到在良好工艺参数与较少环境干扰的条件下基准焊缝(焊缝表面成形光滑平整,内部熔深一致)的焊缝高度与匙孔深度随时间的变化数据。
[0074]
需要说明的是激光焊接工艺参数(例如:激光功率、焊接速度及离焦量)从实际动力电池壳体制造车间所用的焊接工艺参数范围中选择,得到表面质量良好(焊缝高度波动范围不超过其平均值的5%)且内部熔深一致(熔深波动范围不超过其平均值的10%)的基准焊缝,以监测用于动力电池壳体激光焊接的其它工艺参数下的焊接质量;或监测在基准焊缝的工艺参数下由于动力电池壳体所处加工环境异动或噪声干扰等偶然的非工艺因素导致的新焊接过程中的表面缺陷以及内部熔深不一致。
[0075]
需要说明的是相干光测量系统中的信号采集模块同轴集成于用于动力电池壳体焊接的激光头上,通过光学系统将发射出的相干测量光分为两束,分别到达动力电池壳体表面与测量位置(焊缝顶部或匙孔底部),并在动力电池壳体表面与测量位置反射回测量系统。其中到达测量位置的相干光通过摆动振镜间歇式周期性地到达焊缝顶部和匙孔底部其中的一处,实现前一时刻焊缝高度(或匙孔深度)的测量、当前时刻匙孔深度(或焊缝高度)的测量以及下一时刻焊缝高度(或匙孔深度)的测量。利用从动力电池壳体表面反射和从测量位置反射的两束相干光的光程差计算得到焊缝高度与匙孔深度的数值作为监测信号数据。具体工作原理如图2所示:根据参考光到参考镜的这段距离(l0 l4 l5)与所用时间t计算相干光的传输速度在动力电池壳体表面与焊缝表面被反射的两束测量相干光的光程差为干光的光程差为其中δt1为光程差对应的时间差,当焊缝表面高于动力电池壳体表面时,h为正值,当焊缝表面低于动力电池壳体表面时,h为负值;在匙孔底部与焊缝表面被反射的两束测量相干光的光程差为[(l0 l1 l3 d)-(l0 l1 l2 l3)]=d-l2=v
×
δt2,其中δt2为光程差对应的时间差。因此可以得到焊缝高度h与匙孔深度d的计算公式:
[0076][0077]
[0078]
(3)在动力电池壳体实际焊接过程中,通过相干光测量系统在线获取焊缝高度与匙孔深度沿焊缝长度方向(时间)的实时变化数据。
[0079]
需要说明的是相干光测量系统中振镜摆动范围即从匙孔到后方焊缝的总测量范围为4mm,焊缝高度采样频率为1000hz,匙孔深度采样频率为1000hz。
[0080]
(4)对所监测的动力电池壳体激光焊接过程中实时获得的焊缝高度数据采用滑动窗口算法进行扫描处理,通过滑动窗口将数据裁剪分组,以实现分组分段地对焊接过程进行监测,便于确定缺陷位置,计算量小,步骤简洁。窗口尺寸设置为10(每个窗口中包含10个数据点)、扫描步长设置为10(每次向前移动10个数据点)。
[0081]
(5)对当前位置的滑动窗口中的数据进行处理分析,计算该组数据的变异系数cvi,同时取基准焊缝高度数据,计算总变异系数cv
norm
,将cvi与cv
norm
的绝对值进行比较,如果该cvi的绝对值未超出cv
norm
的绝对值,则认为该位置处表面质量良好,结果如图3所示;否则该位置处存在表面缺陷,结果如图4所示。随后,依照上述步骤处理下一个滑动窗口中焊缝高度数据进行监测,依次循环,直到所监测的整条焊缝的每个焊接位置都被分析完,此时整个焊接过程也刚好完成。所监测的焊接过程中各窗口位置处的焊缝高度数据的变异系数计算公式为:
[0082]
式中,xj(t)为窗口中的各数据点。基准焊缝的焊缝高度样本数据的总变异系数计算公式为为各数据点。
[0083]
(6)对所监测的动力电池壳体激光焊接过程中实时获得的匙孔深度数据采用集合经验模态分解算法进行处理。通过将白噪声均匀分布在匙孔深度数据的整个时频空间,使匙孔深度信号在时频空间中被滤波器组分解成不同尺度成分,去掉其中高频噪声与细节成分并重构信号,获得高信噪比、特征明显的匙孔深度数据。分解公式为式中,y(t)为待分解的原始信号,ci(t)为分解项中的第i个固有模函数,rn(t)为分解之后得到的一个余项(残差项),n为分解后得到的项的总个数。
[0084]
参数选择为:添加的白噪声的标准差与原始信号的标准差的比值为0.2、集合数量为100;算法将原始信号自适应地分为11个固有模函数和1个余项,其中将固有模函数1-6设置为高频分量,固有模函数7-11和余项设置为低频分量。使用6个低频分量来重构原始信号。
[0085]
(7)计算基准焊缝的经集合经验模态分解重构后的匙孔深度数据的标准差s0和均值μ,将代表内部熔深一致的基准焊缝下的匙孔深度标准差s0映射至当前所监测的焊缝。根据所监测的焊接过程中实时获得的经集合经验模态分解重构后的匙孔深度数据的平均值经过计算得到该道焊缝重构后的匙孔深度波动的预设阈值th。判断该道焊缝的重构后的
匙孔深度信号曲线是否存在超出预设阈值th的部分,如果各位置均未超出,说明内部熔深一致,结果如图5所示;否则内部熔深不一致,结果如图6所示。所监测的每道焊缝重构后的匙孔深度波动的预设阈值计算公式为匙孔深度波动的预设阈值计算公式为
[0086]
(8)根据监测判断结果,做出相应的后续产品处理,如图7所示,需要说明的是,表中“正常”表示焊缝表面质量良好、内部熔深一致,即焊接质量达标;“一级缺陷”表示焊缝表面存在缺陷、内部熔深一致;“二级缺陷”表示焊缝表面质量良好、内部熔深不一致;三级缺陷表示焊缝表面存在缺陷同时内部熔深不一致。
[0087]
本监测方法普适性广、鲁棒性强,同样可以适用于其他工艺、环境下的动力电池壳体激光焊接质量实时监测。
[0088]
本实施例提出的产品后续处理方案仅为较佳处理方式之一,现场可以根据技工经验判断结果,进行其他最终处理。
[0089]
下面对本发明提供的基于相干光测量的动力电池壳体激光焊接质量监测系统进行描述,下文描述的基于相干光测量的动力电池壳体激光焊接质量监测系统与上文描述的基于相干光测量的动力电池壳体激光焊接质量监测方法可相互对应参照。
[0090]
本发明实施例提供一种基于相干光测量的动力电池壳体激光焊接质量监测系统,包括:计算机可读存储介质和处理器;
[0091]
所述计算机可读存储介质用于存储可执行指令;
[0092]
所述处理器用于读取所述计算机可读存储介质中存储的可执行指令,执行如上述任一实施例所述的方法。
[0093]
本领域的技术人员容易理解,以上所述仅为本发明的较佳实施例而已,并不用以限制本发明,凡在本发明的精神和原则之内所作的任何修改、等同替换和改进等,均应包含在本发明的保护范围之内。
再多了解一些
本文用于企业家、创业者技术爱好者查询,结果仅供参考。