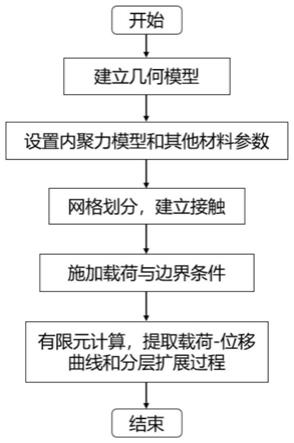
1.本发明涉及复合材料模拟技术领域,具体而言涉及一种引入分层损伤的复合材料弯曲失效模拟方法,适用于航空航天等领域的复合材料弯曲失效过程的研究与预测。
背景技术:
2.航空发动机是在高温、高压、高速旋转的恶劣环境条件下长期可靠工作的复杂热力机械,新一代航空发动机的高性能指标对材料提出了更高的要求。陶瓷基复合材料具有耐高温、高比强度、低热膨胀系数等优点,是未来航空发动机热端部件的首选材料。
3.连续纤维增韧陶瓷基复合材料从根本上克服了陶瓷脆性大的缺点。相较于碳纤维,sic纤维在高温下具有更好的抗氧化性。因此平纹编织sic/sic是未来航空发动机高温构件的理想材料。
4.目前专家学者对平纹编织复合材料进行了大量的力学研究,包括拉伸、压缩、剪切和模态分析,实现了相关试验的数值模拟,然而对于平纹编织sic/sic弯曲行为研究较少,目前尚没有考虑分层的弯曲失效模拟方法。
5.航空发动机的热端部件(如调节片和涡轮叶片等)承受温度和压力作用,表现为弯曲载荷作用于梁结构。由于平纹编织材料的层间强度较低,容易发生分层破坏,所以有必要对平纹编织sic/sic梁在弯曲载荷作用下的分层行为进行研究。
技术实现要素:
6.本发明针对现有技术中的不足,提供一种引入分层损伤的复合材料弯曲失效模拟方法,适用于工程应用,可以对复合材料结构的弯曲失效模式进行有效的分析和预测,保障结构安全性。
7.为实现上述目的,本发明采用以下技术方案:
8.一种引入分层损伤的复合材料弯曲失效模拟方法,所述模拟方法包括以下步骤:
9.s1,根据复合材料梁弯曲试验,建立复合材料弯曲几何模型,根据实际铺层厚度对几何体划分铺层;
10.s2,建立内聚力模型,选择内聚力模型的本构关系,设置相关内聚力模型参数,设置复合材料铺层单元和夹具的材料参数;
11.s3,采用六面体单元对几何模型进行网格划分,对铺层间设置内聚力接触,建立有限元模型;复合材料梁与夹具之间采用摩擦接触,复合材料铺层之间采用内聚力接触;
12.s4,根据复合材料结构的弯曲受载形式,确定边界条件和施加载荷;
13.s5,对有限元模型进行计算,获取计算结果:计算弯曲强度,提取载荷-位移曲线,获得复合材料的分层裂纹扩展过程。
14.为优化上述技术方案,采取的具体措施还包括:
15.进一步地,步骤s1中,所述复合材料弯曲几何模型包括划分铺层的复合材料梁和夹具模型。
16.进一步地,步骤s2中,设置复合材料铺层单元的材料参数的过程包括:
17.采用双线性本构模型,通过dcb试验和mmb试验获得的复合材料i型、ii型断裂能、法向应力和剪切应力极限,计算包括界面初始刚度、界面强度在内的反映界面行为的各项参数。
18.进一步地,步骤s2中,建立内聚力模型,选择内聚力模型的本构关系,设置相关内聚力模型参数,设置复合材料铺层单元的材料参数的过程包括以下步骤:
19.s21,设所述内聚力模型的本构关系为:
20.p=knun(1-dn)
ꢀꢀꢀ
(1);
[0021][0022]
其中,p是法向内聚力,kn是法向刚度,dn是与界面相对位移相关的损伤系数,un,,分别表示界面法向相对位移、界面法向初始损伤时的位移和法向完全破坏时的位移;
[0023]
s22,根据j积分定义,三角形oac的面积为纯拉伸性的临界断裂能:
[0024][0025]
其中,g
cn
为i型临界断裂能,σ
max
表示界面初始损伤时的应力;
[0026]
s23,综合考虑拉伸与剪切耦合的混合型内聚力模型,初始损伤位移为完全破坏位移的一半,采用二次断裂能失效准则判断界面损伤萌生:
[0027][0028]
进一步地,步骤s4中,根据复合材料结构的弯曲受载形式,确定边界条件和施加载荷的过程包括:
[0029]
设有限元模型的x面和y面为对称面,分别限制x方向和y方向位移;压头与支撑为高温合金材料,只建立半圆柱体,分别施加向下的位移载荷与固定约束,夹具与试件之间建立接触对。
[0030]
进一步地,步骤s5中,复合材料的弯曲强度计算公式为:
[0031][0032]
式中,su为弯曲强度,单位为mpa;pu为峰值载荷,单位为n;l为四点弯曲支撑跨度,单位为mm;b为试件宽度,单位为mm;d为试件厚度,单位为mm。
[0033]
本发明的有益效果是:
[0034]
本发明的引入分层损伤的复合材料弯曲失效模拟方法,不但可以计算平纹编织sic/sic复合材料的弯曲强度,而且可以对分层损伤裂纹的萌生与扩展过程进行分析,获取弯曲过程中的载荷-位移曲线。
附图说明
[0035]
图1是本发明实施例的引入分层损伤的复合材料弯曲失效模拟方法流程图。
[0036]
图2是本发明实施例的试件有限元模型图。
[0037]
图3是试验载荷位移曲线和是否考虑分层扩展的有限元模拟结果对比图。
[0038]
图4是考虑分层损伤的裂纹扩展过程。
具体实施方式
[0039]
现在结合附图对本发明作进一步详细的说明。
[0040]
需要注意的是,发明中所引用的如“上”、“下”、“左”、“右”、“前”、“后”等的用语,亦仅为便于叙述的明了,而非用以限定本发明可实施的范围,其相对关系的改变或调整,在无实质变更技术内容下,当亦视为本发明可实施的范畴。
[0041]
图1是本发明实施例的引入分层损伤的复合材料弯曲失效模拟方法流程图。参见图1,该复合材料弯曲失效模拟方法的具体步骤如下:
[0042]
步骤1,根据复合材料梁弯曲试验,建立试件和夹具的几何模型,根据实际铺层厚度对几何体划分铺层。当试件及夹具为对称结构时,建立1/4模型进行计算。
[0043]
步骤2,建立内聚力模型,选择内聚力模型的本构关系,设置相关内聚力模型参数,分别设置复合材料铺层单元和夹具的材料参数。采用双线性本构模型,通过dcb试验和mmb试验获得的复合材料i型、ii型断裂能、法向应力和剪切应力极限,计算界面初始刚度、界面强度等反映界面行为的参数。
[0044]
示例性地,步骤s2中,建立内聚力模型,选择内聚力模型的本构关系,设置相关内聚力模型参数,设置复合材料铺层单元的材料参数的过程包括以下步骤:
[0045]
s21,设所述内聚力模型的本构关系为:
[0046]
p=knun(1-dn)
ꢀꢀꢀ
(1);
[0047][0048]
其中,p是法向内聚力,kn是法向刚度,dn是与界面相对位移相关的损伤系数,un,,分别表示界面法向相对位移、界面法向初始损伤时的位移和法向完全破坏时的位移。
[0049]
s22,根据j积分定义,三角形oac的面积为纯拉伸性的临界断裂能:
[0050][0051]
其中,g
cn
为i型临界断裂能,σ
max
表示界面初始损伤时的应力。
[0052]
s23,综合考虑拉伸与剪切耦合的混合型内聚力模型,初始损伤位移为完全破坏位移的一半,采用二次断裂能失效准则判断界面损伤萌生:
[0053][0054]
步骤3,采用六面体单元对试件几何模型进行网格划分,建立有限元模型。复合材料梁与夹具之间采用摩擦接触,复合材料铺层之间采用内聚力接触。
[0055]
步骤4,根据复合材料结构的弯曲受载形式,确定边界条件和施加载荷。如图2所示,有限元模型的x面和y面为对称面,分别限制x方向和y方向位移。压头与支撑为高温合金
材料,只建立半圆柱体,分别施加向下的位移载荷与固定约束,夹具与试件之间建立接触对。
[0056]
步骤5,对有限元模型进行计算,获取计算结果。计算弯曲强度,提取载荷-位移曲线,获得复合材料的分层裂纹扩展过程。
[0057]
示例性地,步骤s5中,复合材料的弯曲强度计算公式为:
[0058][0059]
式中,su为弯曲强度,单位为mpa;pu为峰值载荷,单位为n;l为四点弯曲支撑跨度,单位为mm;b为试件宽度,单位为mm;d为试件厚度,单位为mm。
[0060]
计算获得的载荷-位移曲线如图3所示,分层裂纹扩展过程如图4所示。采用内聚力模型模拟分层损伤获得的载荷-位移曲线与试验曲线吻合度很好,验证了考虑分层损伤的复合材料弯曲失效模拟方法预测的准确性。
[0061]
以上仅是本发明的优选实施方式,本发明的保护范围并不仅局限于上述实施例,凡属于本发明思路下的技术方案均属于本发明的保护范围。应当指出,对于本技术领域的普通技术人员来说,在不脱离本发明原理前提下的若干改进和润饰,应视为本发明的保护范围。
再多了解一些
本文用于企业家、创业者技术爱好者查询,结果仅供参考。