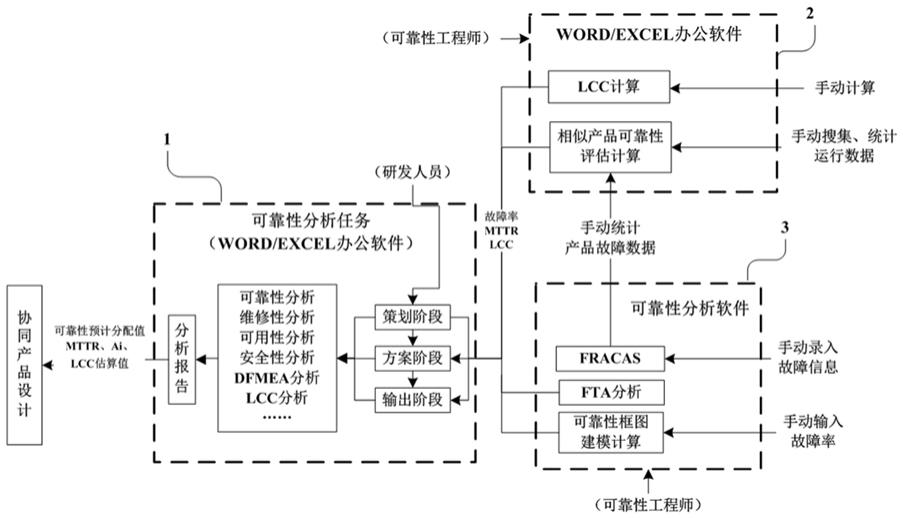
1.本发明涉及研发、生产和运维过程中的可靠性技术,一种面向产品协同设计的可靠性数据、模型及方法的集成系统。
背景技术:
2.随着高铁飞速发展,轨道交通装备产品可靠性已成为铁路安全运行的关注点,高可靠性的产品是需要制造企业有效实施可靠性系统工程才能保证的。国内轨道交通行业于引20世纪90年代引入可靠性系统工程,中车集团和运营部门均不同程度地应用了可靠性技术,然而成功实施可靠性系统工程的关键是要结合产品特点选取合适的可靠性技术,并融入企业数字化环境和管理中形成技术集成应用模式。因此,开展具有企业特色的可靠性技术集成应用方法研究,对保可靠性系统工程的实施效果及提升产品可靠性具有重要意义。
3.当前国内大多制造型企业对产品的全寿命周期数据收集不完整,各部门之间数据及业务独立,设计部门和运维部门也存在脱节,因此导致产品的设计、制造、生产、运行及维护各个阶段的数据没有形成完成的链条及完整的闭环,无法支撑产品的高质量设计改进和健康运行;另一方面,由于可靠性数据的不完整,导致可靠性技术和方法没有有效的集成和管理,导致各个业务流之间传递不顺畅、功能模块不完善等。其可靠性技术集成应用方法主要是对可靠性技术、工具和方法的软件引进或开发,针对融合企业产品协同设计过程、全寿命周期可靠性数据及可靠性分析工具自主开发的集成应用方法研究还很少,且缺乏此类方法的理论指导,不能支撑轨道交通制造企业高效实施可靠性系统工程的要求。
4.图1为现有轨道交通装备产品制造企业的可靠性技术集成应用方案。1为研发人员执行的可靠性分析任务,是由可靠性工程师事先将可靠性技术标准中要求转化为分析表格模板及企业相应管理流程文件,指导研发人员进行产品可靠性分析。为了支撑可靠性分析任务,需利用word/excel办公软件2和可靠性专业软件3,进行参数算法嵌入、相似产品可靠性评估计算、fracas管理、绘制可靠性框图、建模计算等操作,并将结果反馈至可靠性分析任务1中,由于可靠性专业软件和办公软件无法自动获取产品数据,其分析所用数据来源均需要手动搜集、整理及录入。
5.现有技术的缺点1)缺乏产品全寿命周期可靠性数据集成及应用,包括故障数据、运行数据、故障率、维修性数据、lcc数据等分散在不同部门,人员需花费大量精力收集及统计数据,且缺乏对产品可靠性的持续评估及监控。
6.2)人员不能便捷地应用rams/lcc分析方法,仅通过标准宣贯,不能使人员熟练掌握各阶段的分析项点及输出内容,不清楚可靠性/维修性预计分配方法、全寿命周期费用(lcc)计算方法、rams/lcc分析中的逻辑关联性等,造成可靠性分析精力多花费在可靠性审查和文件纠错上。
7.3)可靠性分析滞后于产品研发节点,虽在研发各阶段规定了rams/lcc分析项点及审查要求,但人为管控方式效果不佳,多数产品可靠性分析未在相应策划、方案、输出等节
点进行,部分产品甚至到结项阶段才开展。
技术实现要素:
8.本发明针对现有技术方案缺乏企业数据支持及应用不便捷高效的缺点,形成一种面向产品协同设计的可靠性数据、模型及方法的集成系统,解决产品全寿命周期各阶段数据分散独立不集中的问题,同时基于本可靠性技术集成管理方法开发形成的动态数据库也可以把各阶段的可靠性技术和计算方法融合贯通,实现支持产品全寿命周期可靠性数据的集成及关联调用、支持可靠性分析方法及模型的工具化开发、支持在协同产品设计过程中智能推送应用。
9.本发明所述方案如下:一种面向产品协同设计的可靠性数据、模型及方法的集成系统,包括基于企业研发平台建立的协同产品设计的可靠性分析流程及应用界面,基于企业知识平台建立的可靠性分析工具模块,基于企业大数据平台建立的动态可靠性数据库,以及产品业务系统;企业研发平台与企业知识平台双向通讯连接,企业大数据平台与企业知识平台以及产品业务系统双向通讯连接,企业知识平台与产品业务系统单向通讯连接;所述可靠性分析流程及应用界面是在企业研发平台上利用知识推送技术建立,用于在不同设计阶段向研发人员推送相匹配的可靠性知识、分析模板及可靠性分析工具模块的应用链接;通过推送的应用链接进入企业知识平台,根据产品特点选定并利用任务流功能组合多种可靠性分析工具形成可靠性分析工具模块,再依据可靠性分析工具模块中的任务流程提示执行产品可靠性分析任务,同时将动态可靠性数据库与可靠性分析工具模块进行系统对接,支持可靠性分析工具模块应用中实时调取数据;动态可靠性数据库系统利用数据库技术搭建,具备产品全寿命周期数据集成及自动运算功能,通过与可靠性分析工具模块与产品业务系统的双向传输接口开发,实现从产品业务系统提取原始数据支持可靠性分析工具模块的应用,同时可靠性分析工具模块应用后的分析结果回传可靠性分析流程及应用界面和产品业务系统指导产品优化改进,形成产品可靠性技术集成应用及全寿命周期数据闭环反馈。
10.本发明的有益效果:实现支持产品全寿命周期可靠性数据的集成及关联调用、支持可靠性方法及模型的工具化开发、支持能在协同产品设计过程中自动推送应用,实现可靠性技术融入企业产品数字集成环境后的信息交互与逻辑协调,为轨道交通装备产品制造企业可靠性系统工程的有效实施提供一种便捷高效的可靠性数据、模型及方法的集成应用方法(模式),从而支撑企业产品可靠性持续提升。
附图说明
11.图1现有可靠性技术集成应用方案。
12.图2面向产品协同设计的可靠性数据、模型及方法的集成应用方案。
13.图3协同产品设计的可靠性工作流程及项点。
14.图4可靠性分析工具示意图。
15.图5可靠性分析工具模块工作流程图。
16.图6可靠性分析工具模块在知识工程系统的应用界面。
17.图7动态可靠性数据库架构示意图。
18.图8故障率算法流程图。
具体实施方式
19.本发明是一种适用于轨道交通装备产品制造企业数字化环境的可靠性数据、模型及方法的集成应用方法(系统),图2为本发明提出的技术方案,主要由可靠性分析流程及应用界面1,可靠性分析工具模块2,动态可靠性数据库3、产品业务系统4组成。
20.在企业研发平台上(如plm系统)利用知识推送技术,建立起协同产品设计的可靠性分析流程及应用界面1,用于在不同设计阶段向研发人员推送相匹配的可靠性知识、分析模板及可靠性分析工具模块2的应用链接,研发人员通过推送的应用链接进入企业知识平台(如知识工程系统),根据产品特点选定并利用任务流功能组合多种可靠性分析工具(提前利用程序封装技术开发的定制化应用工具)形成可靠性分析工具模块2,再依据可靠性分析工具模块2中的任务流程提示执行产品可靠性分析任务,同时将动态可靠性数据库3与可靠性分析工具模块2进行系统对接,支持可靠性分析工具模块2应用中实时调取数据。
21.利用数据库技术搭建具备产品全寿命周期数据集成及自动运算的动态可靠性数据库3,通过与可靠性分析工具模块2与产品业务系统4(如mro、erp、qms、lims系统等)的双向传输接口开发,实现从产品业务系统4提取原始数据支持可靠性分析工具模块2的应用,同时可靠性分析工具模块2应用后结果回传可靠性分析流程及应用界面1和产品业务系统4指导产品优化改进。从而形成便捷高效地产品可靠性技术集成应用及全寿命周期数据闭环反馈,指导产品的高质量正向设计开发。
具体实施例
22.本发明提出的技术方案涉及在企业现有的多个平台上进行功能模块开发,实施路径如下:实施例1:协同产品设计的可靠性流程开发在plm系统的产品设计全过程中嵌入可靠性分析任务,包括策划阶段制定rams计划、输入阶段评估相似产品、预计本产品可靠性、维修性指标及定性分析、方案阶段实施dfmeca及可靠性设计、输出阶段措施落实等,并利用plm系统信息化推送手段,在设计阶段推送相应的可靠性分析模板、分析工具及知识(标准、规范)如图3。图中可知,所述可靠性分析流程及应用界面1中的设计阶段分为策划阶段、输入阶段、方案阶段和输出阶段,策划阶段的任务为确定rams/lcc管理计划;输入阶段的任务为rams/lcc初步分析,推送的可靠性分析工具(封装程序)为ram预计分配的设计工具;方案阶段的任务为dfmeca分析和rams/lcc分析与设计,上述两个任务对应推送的可靠性分析工具(封装程序)分别是dfmeca分析的设计工具和rams/lcc分析的设计工具;输出阶段的任务分别为rams&lcc分析报告、dfmeca表和rams/lcc分析结论,各任务相应推送的可靠性分析工具(封装程序)分别为dfmeca分析的设计工具以及rams&lcc分析的设计工具。
23.可靠性分析流程及应用界面1中各个设计阶段还输出与各任务对应的文件/资料/记录、推送与各任务对应的分析文件模板以及知识,所述知识包括各种生产标准和规范。
24.实施例2:可靠性分析工具模块开发1)选定适合企业产品设计过程的可靠性分析方法,利用程序封装技术开发为可便
捷应用的可靠性分析工具,包含可靠性、维修性、安全性、lcc方面共16个分析工具如图4,应用界面如图6。可靠性分析工具模块2中提前利用程序封装技术开发多种定制化应用工具,所述应用工具包括可靠性指标换算、隐患登记册、lcc分析、修复性维修分析、可靠性预计与分配、设计潜在失效模式、影响及危害性分析(dfmeca)和预防性维修分析;lcc分析包括购置费提取或计算、维修费计算、耗能费计算和报废处置费计算;可靠性预计与分配包括相似产品预计法、相似产品 专家评分预计法、评分预计法、元器件计数预计法、评分分配法、比例组合分配法。
25.2)针对每个设计阶段可靠性分析具有继承性的特点,利用知识工程系统的任务流功能,开发可靠性分析工具自由组合和中间数据传输功能,形成可靠性分析工具模块工作流程,如图5所示。可靠性分析工具模块2执行产品可靠性分析任务的流程如下:通过可靠性分析流程及应用界面1中的各设计阶段推送的应用链接进入可靠性分析工具模块2,应用可靠性建模预计工具分析后得到ram(可靠性、可用性及可维修性)预计结果和潜在故障,其中ram预计结果单独生成rams(可靠性、可用性、可维修性及安全性)初步分析结果并反馈至可靠性分析流程及应用界面1中的输入阶段;ram预计结果同时输入至cm(修复性维修)分析工具、pm(预防性维修)分析工具和退役处置分析工具,应用这三个工具分析后分别得到故障维修费、维护检修费和报废处置费,并输入至lcc(全寿命周期费用)分析工具;潜在故障输入至dfmeca(设计失效模式、影响及安全性分析)工具,应用dfmeca工具分析得到ram措施反馈至可靠性分析流程及应用界面1中的方案阶段;应用dfmeca工具还得到r1/r2类风险并输入至hla(危害分析)工具;最后所有分析工具输出的结果存储并得到故障率、mttr(平均维修时间)、ai(可用度)、lcc和可靠性措施建议,进而得到rams&lcc分析报告并反馈至可靠性分析流程及应用界面1、动态可靠性数据库3和产品业务系统4。
26.实施例3:动态可靠性数据库系统开发对企业各系统中大量设计制造、运营维护数据,采用复杂算法对大量数据进行挖掘,进而发现数据间隐藏的模式、关联、异常及结构,建立产品可靠性分析模型和动态数据库,以数据库为基础建立数据可视化展示、可靠性知识推送等功能,如图7。
27.动态可靠性数据库3包括原始数据库、模型算法库、统计数据库和分析结果库;动态可靠性数据库3从产品业务系统4同步采集结构化、半结构化和非结构化可靠性数据,存储至原始数据库;模型算法库对数据进行分析处理,并通过统计数据库将可靠性分析工具模块2分析所需数据同步输出至可靠性分析工具模块2的动态可靠性数据模块存储。
28.产品业务系统4包括mro(产品保养、维修及运行管理系统)、erp(资源计划管理系统)、qms(质量管理系统)、lims(试验室信息管理系统)、wms(仓库管理系统)、plm(产品生命周期管理系统);原始数据库从上述各系统中同步采集数据。
29.分析结果库接收来自可靠性分析工具模块2的分析结果,迭代更新后输入统计数据库。
30.基于可靠性参数类别和企业数据来源,并结合协同产品设计的可靠性分析需求,将rams/lcc参数算法进行分类如表1。
31.以轨道交通产品故障率参数计算为例,根据企业可靠性数据实际情况,制定了基于erp出厂日期、基于mro配属上下车日期、上下车里程的三种算法。其计算精度是递增关系,设置默认使用erp数据计算,通过增加判断条件,当mro系统数据完整后,再启用基于mro系统数据的算法,并将计算结果同时存入动态可靠性数据库,供可靠性分析平台提取调。以轨道交通产品故障率算法流程为例如图8所示。
32.动态可靠性数据库在计算轨道交通产品故障率参数时,采用如下方案:首先提取可靠性数据,并存入原始数据库;可靠性数据包括嵌入的产品层级表、mro每条故障数据、erp每台产品每次出厂日期、mro每台产品配属上下车日期/里程;采用基于erp出厂日期、基于mro配属上下车日期、基于mro配属上下车里程的三种算法计算得到累计运行时间/里程并求和,同时得到故障次数求和,并将结果存入统计数据库,统计数据库按照嵌入的公式计算故障率;设置默认使用erp数据计算,通过增加判断条件,当mro系统数据完整后,再启用基于mro系统数据的算法。
33.本发明的创新点:1、本发明基于产品协同设计理念提出的一种可靠性数据、模型及方法的集成应用系统。本发明支持产品全寿命周期可靠性数据的集成及关联调用、支持可靠性分析方法及模型的工具化开发、支持能在协同产品设计过程中自动推送应用。
34.2、本发明结合企业数字化环境的可靠性动态数据库搭建方法及应用方法研究,智能提取业务系统中可靠性数据,各环节嵌入模型算法不仅可以对可靠性相关参数智能计算,而且还能支持各阶段数据及计算结果的传递、迭代更新及各业务系统间信息智能互通。
35.3、本发明提出自带动态可靠性数据库的可靠性分析工具开发与集成方法。利用编程技术封装选定的多种可靠性分析计算方法,并能组合形成可靠性分析工具包嵌入各阶段可靠性业务管理系统,同时也可以智能实时调用动态可靠性数据库支持可靠性分析工具包的应用。
再多了解一些
本文用于企业家、创业者技术爱好者查询,结果仅供参考。