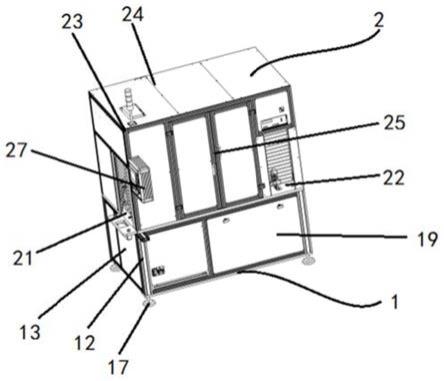
1.本发明涉及充磁设备的制造领域,更具体的说,它涉及一种充磁机。
背景技术:
2.充磁机结构较简单,实际上就是一个磁力极强的电磁铁,配备多种形状的铁块,作为附加磁极,以便与被充磁体形成闭合磁路,充磁时摆设好附加磁极和被充磁体,只要加上激磁电流瞬间即可完成。
3.随着电子设备的发展,各种磁铁设备的加工需求也日益增加,因此充磁机需要添加对应加工需求的加工工序和加工机构;工件在加工的过程中需要依次经过对应的机构,进而完成完整的加工工序;而这个加工的过程如果全程由人工进行操作的话,不仅充磁的质量以及效率低下,还容易出现安全隐患。
技术实现要素:
4.本发明克服了现有技术的不足,提供结构简单、设计合理、操作安全、高效率、高质量的一种充磁机。
5.为了解决上述技术问题,本发明的技术方案如下:
6.一种充磁机,包括供料组件、工件组装组件、工件加工组件、出料组件、机架部分和防护罩部分;所述供料组件、工件组装组件、工件加工组件和出料组件均设置于机架部分的设备装配板上,防护罩部分将其供料组件、工件组装组件、工件加工组件和出料组件包围;
7.所述供料组件包括送工件部分,在防护罩部分对应送工件部分的区域设置有供料开口,在防护罩部分对应出料组件的区域设置有出料开口;
8.所述供料组件还包括磁瓦供料部分,工件组装组件包括磁瓦分度机构、磁瓦运输部分和压磁瓦机构;所述磁瓦分度机构和磁瓦运输部分设置于磁瓦供料部分和送工件部分之间,且磁瓦分度机构设置于磁瓦运输部分和磁瓦供料部分之间;压磁瓦机构设置于送工件部分的上方;磁瓦供料部分将磁瓦运输到磁瓦分度机构内进行分度,磁瓦运输部分将成分度的磁瓦运输到送工件部分,通过压磁瓦机构将转子与磁瓦完成组装;
9.工件加工组件包括铁芯铆边部分、转子清洁部分、充磁部分和搬运部分;送工件部分、铁芯铆边部分、转子清洁部分、充磁部分和出料组件均设置于搬运部分的同一侧,并且处于同一直线上;所述送工件部分和出料组件设置于搬运部分的两端,铁芯铆边部分设置于送工件部分和转子清洁部分之间,充磁部分设置于转子清洁部分和出料组件之间;在搬运部分上设置有机械手移动板,机械手移动板位于送工件部分、铁芯铆边部分、转子清洁部分和充磁部分的上方,在机械手移动板上设置有四个上下抓料机构,并且分别对应送工件部分、铁芯铆边部分、转子清洁部分、充磁部分和出料组件;机械手移动板可在搬运气缸的作用下移动,机械手移动板的移动方向对应送工件部分、铁芯铆边部分、转子清洁部分、充磁部分和出料组件分布的形状,并在上下抓料机构的作用下,将送工件部分中的转子依次送入铁芯铆边部分、转子清洁部分、充磁部分进行加工,最后将加工后的转子放入出料组
件;
10.所述搬运部分包括搬运支架,所述搬运支架包括搬运固定板和搬运支柱,在搬运固定板的后表面上设置有第一搬运支座,搬运支柱的一端与第一搬运支座连接,搬运支柱的另一端设置有第二搬运支座,并通过第二搬运支座与设备装配板的上表面连接;所述机械手移动板设置于搬运固定板的另一表面上,在机械手移动板朝向搬运固定板的表面上设置有搬运滑轨,并在搬运滑轨上设置有搬运滑块,所述搬运滑块与搬运固定板连接;所述搬运气缸设置于搬运固定板上,在搬运固定板的上端面设置有搬运气缸座,搬运气缸的缸体与搬运气缸座连接,在搬运气缸的气缸臂上设置有搬运气缸连接件,且搬运气缸连接件与机械手移动板连接;上下抓料机构设置于机械手移动板远离搬运滑轨的表面,其包括垂直抓料气缸和手爪气缸,垂直抓料气缸的气缸臂与机械手移动板连接,手爪气缸设置于垂直抓料气缸的气缸臂上;
11.所述上下抓料机构包括第一上下抓料机构、第二上下抓料机构、第三上下抓料机构和第四上下抓料机构;
12.搬运气缸的气缸臂伸展时,第一上下抓料机构对应送工件部分,第二上下抓料机构对应铁芯铆边部分,第三上下抓料机构对应转子清洁部分,第四上下抓料机构对应充磁部分;
13.搬运气缸的气缸臂收拢时,第一上下抓料机构对应铁芯铆边部分,第二上下抓料机构对应转子清洁部分,第三上下抓料机构对应充磁部分,第四上下抓料机构对应充磁机的出料组件。
14.进一步的,所述磁瓦供料部分设置于搬运部分远离铁芯铆边部分、转子清洁部分、充磁部分的一侧,其包括磁瓦料盘,磁瓦料盘上设置有料盘槽,磁瓦设置于料盘槽内,料盘槽的开口朝向磁瓦分度机构,且磁瓦通过该开口进入磁瓦分度机构;磁瓦供料部分包括供料气缸,供料气缸将料盘槽内的磁瓦送入磁瓦分度机构;
15.磁瓦供料部分包括供料底板、供料电机和供料丝杆,所述磁瓦料盘、供料电机和供料丝杆设置于供料底板上,并且磁瓦料盘在供料电机和供料丝杆的带动下进行活动;在供料底板的上表面设置有供料导轨,并在供料导轨上设置有供料滑块,所述供料滑块与磁瓦料盘的下表面连接;所述供料电机设置于供料底板的下表面,供料丝杆设置于供料导轨之间;供料丝杆采用滚珠丝杆,其包括螺杆和螺母;在供料电机的输出端以及供料丝杆的螺杆靠近供料电机的一端均设置有同步轮,同步轮之间采用皮带连接和传动,并且在供料丝杆的同步轮和供料电机的同步轮上设置有将其两者以及皮带包围在内的皮带防护罩;供料丝杆的螺母与磁瓦料盘连接;在供料底板的上表面还设置有检测磁瓦料盘活动的供料光电传感器,并且在供料底板上还设置有传感器防护罩,传感器防护罩将供料光电传感器包围并保护;在供料底板下表面的四个角上还设置有供料支柱,供料支柱的一端与供料底板的下表面连接,供料支柱的另一端设置有安装座,并通过安装座与设备装配板连接;
16.所述磁瓦供料部分包括供料支架,供料气缸设置于供料支架上;所述供料支架呈“凵”字形,其包括第一供料直杆、第二供料直杆和第三供料直杆,第一供料直杆的一端以及第三供料直杆的一端分别与第二供料直杆的两端连接,第一供料直杆和第三供料直杆与第二供料直杆相互垂直,且第一供料直杆和第三供料直杆的朝向一致;第一供料直杆和第三供料直杆远离第二供料直杆的一端均设置有供料安装底板,并通过供料安装底板与设备装
配板连接;料盘槽设置于磁瓦料盘的上表面,第二供料直杆设置于磁瓦料盘的上方;所述供料气缸设置于第二供料直杆上,并且在供料气缸的气缸臂上设置有供料气缸活动块,在供料气缸活动块上设置有磁瓦横移推板,并在磁瓦横移推板上设置有磁瓦推头;供料气缸活动块的活动范围与料盘槽的设置形状对应,磁瓦推头将料盘槽内的磁瓦推入磁瓦分度机构;
17.所述磁瓦供料部分还包括磁瓦导入工装,所述磁瓦导入工装设置于磁瓦分度机构的上方;磁瓦导入工装包括磁瓦导入气缸和磁瓦导入块;所述磁瓦导入块设置于第一供料直杆上,且磁瓦导入块所在高度对应磁瓦料盘所在高度;在磁瓦导入块上设置有磁瓦导入槽,磁瓦导入槽设置于磁瓦导入块靠近料盘槽的一端,并且与料盘槽的开口对应;在磁瓦导入块的上表面以及下表面设置有对应磁瓦导入槽的导入块上开口和导入块下开口;
18.磁瓦导入气缸包括垂直导入气缸和水平导入气缸;所述垂直导入气缸通过导入气缸固定板固定在第二供料直杆上,在垂直导入气缸的气缸臂上设置有气缸接头,并在气缸接头内设置有磁瓦推条;所述磁瓦推条从导入块上开口进入磁瓦导入槽,并且可按照料盘槽的设置方向摆动;所述水平导入气缸设置在磁瓦导入块的外表面上,并且水平导入气缸的气缸臂穿过磁瓦导入块进入磁瓦导入槽;
19.在磁瓦导入块的外表面还设置有磁瓦导入传感器。
20.进一步的,所述磁瓦分度机构包括分度盘、分度轴、旋转分度电机和垂直分度气缸,分度盘处于设备装配板的上表面,旋转分度电机和垂直分度气缸处于设备装配板的下表面;分度轴的一端穿过设备装配板,通过夹箍与旋转分度电机的输出轴连接,所述分度盘设置于分度轴的另一端;磁瓦分度机构还包括导向座,所述导向座设置于设备装配板的上表面,并被分度轴穿过;
21.磁瓦分度机构包括分度移动板和分度安装板,分度移动板位于分度安装板的上方,并在分度安装板的上表面设置有分度导杆,分度导杆穿过分度移动板,且分度移动板沿分度导杆活动;所述旋转分度电机设置于分度移动板的下表面,并且旋转分度电机的输出轴穿过分度移动板与分度轴连接;垂直分度气缸的缸体与分度安装板连接,垂直分度气缸的气缸臂与分度移动板连接。
22.进一步的,所述磁瓦运输部分包括运输悬臂、磁瓦储存工装、垂直运输气缸和旋转运输气缸,磁瓦储存工装设置于运输悬臂上,运输悬臂被垂直运输气缸和旋转运输气缸带动;运输悬臂和垂直运输气缸处于设备装配板的上表面,旋转运输气缸处于设备装配板的下表面;所述磁瓦运输部分包括运输气缸座,所述旋转运输气缸设置于运输气缸座内;磁瓦运输部分包括旋转法兰盘,并在旋转法兰盘上设置有法兰轴承座,法兰轴承座与设备装配板装配;在旋转运输气缸的输出轴上设置有联轴器,并通过联轴器与旋转法兰盘的一端连接;磁瓦运输部分还包括运输导杆,所述运输悬臂被运输导杆穿过,并沿运输导杆活动;运输导杆的一端与旋转法兰盘连接,运输导杆的另一端与上盖连接;所述垂直运输气缸设置于上盖远离运输导杆的表面,并且垂直运输气缸的气缸臂穿过上盖与运输悬臂连接;
23.在运输悬臂的一端设置有悬臂装配孔,并在悬臂装配孔内设置有悬臂轴承,且运输导杆将悬臂轴承穿过;在运输悬臂的另一端设置有储存工装装配孔,磁瓦储存工装设置于储存工装装配孔内。
24.进一步的,所述压磁瓦机构包括顶板、压装电缸和下压部;所述压装电缸设置于顶
板的上表面,并且下压部置于顶板的下表面,压装电缸的输出轴穿过顶板与下压部连接;所述下压部包括电缸连接件、下压固定板、压力传感器、压力传感器固定座、推杆和推杆固定座;所述电缸连接件与压装电缸的输出轴连接,且电缸连接件远离压装电缸的一端与下压固定板的上表面连接;下压固定板的下表面与压力传感器固定座的一端连接,压力传感器固定座的另一端与推杆固定座连接;所述压力传感器设置于压力传感器固定座内,推杆设置于推杆固定座远离压力传感器固定座的一端;压磁瓦机构包括立柱,立柱的一端与顶板的下表面连接,立柱的另一端与设备装配板的上表面连接;
25.压磁瓦机构包括压装拖链和第一压装导杆;第一压装导杆的一端穿过顶板与下压固定板连接,在第一压装导杆的另一端设置有活动横杆;在顶板的上表面还设置有检测活动横杆活动的压装位移传感器;压装拖链的一端穿过顶板与下压固定板连接,压装拖链的另一端设置于压装拖链支架内,并在压装拖链支架内活动,压装拖链支架与顶板的上表面连接;压装电缸的输出轴、压装拖链和第一压装导杆的活动方向对应;
26.压磁瓦机构还包括第二压装导杆和压环,所述第二压装导杆的一端与下压固定板的下表面连接;压环被第二压装导杆穿过,并沿第二压装导杆活动;在第二压装导杆上套设有弹簧,弹簧的一端与压环连接,弹簧的另一端与下压固定板的下表面连接;在压环上设置有压环通过孔供推杆穿过进行压装。
27.进一步的,所述铁芯铆边部分包括滑槽座、铆压头组件和槽盘,其三者设置于设备装配板的上表面;在滑槽座的中间设置有铆边空间,在滑槽座上还设置有环绕铆边空间设置的铆边槽;所述铆压头组件设置于铆边槽内,并且各铆压头组件在槽盘的带动下同时进行朝向或远离铆边空间的活动;所述槽盘覆盖在滑槽座的上表面;在槽盘的中间设置有槽盘通孔,转子通过槽盘通孔进入铆边空间;铆边槽设置于滑槽座的上表面,槽盘将铆压头组件限定在铆边槽内,并且槽盘与铆压头组件接触;
28.所述铆压头组件包括铆压头、接触块和移动块,移动块设置于铆边槽内,铆压头设置于移动块朝向铆边空间的一端,接触块设置于移动块的上表面与槽盘接触;槽盘上设置有槽盘活动孔,所述槽盘活动孔环绕槽盘通孔设置,并且接触块设置于槽盘活动孔内;槽盘活动孔的两端分别为压迫端和放松端,压迫端至槽盘通孔中心点的距离大于放松端至槽盘通孔中心点的距离;各槽盘活动孔的放松端均处于对应顺时针方向的一侧;
29.铁芯铆边部分还包括铆边气缸和铆边外壳;在槽盘的外侧表面设置有槽盘连接块,槽盘连接块的一端与槽盘连接,槽盘连接块的另一端与铆边气缸的气缸臂连接,槽盘在铆边气缸的带动下进行活动;所述铆边外壳包括铆边底座和铆边盖板,在铆边底座内设置有滑槽座安装空间,铆边盖板将滑槽座安装空间封闭;所述滑槽座、铆压头组件和槽盘设置于滑槽座安装空间内;在铆边底座上还设置有铆边底座开口,铆边底座开口对应槽盘连接块的活动范围;铆边外壳和铆边气缸设置于设备装配板的上表面;
30.铁芯铆边部分还包括铆边顶升机构和顶升固定机构,铆边顶升机构和顶升固定机构设置于设备装配板的下表面;
31.铆边顶升机构包括顶升装配板和铆边顶升气缸;顶升装配板固定在设备装配板的下表面,在顶升装配板设置有对应铆边空间的顶升装配板通过孔;所述铆边顶升气缸设置于顶升装配板下表面,铆边顶升气缸通过气缸装配支柱与顶升装配板进行装配;铆边顶升气缸的气缸臂上设置有工件座,工件座在铆边顶升气缸的作用下穿过设备装配板进入铆边
空间支撑并顶升转子;
32.所述顶升固定机构设置于顶升装配板的下方,顶升固定机构包括顶升固定气缸,顶升固定气缸设置于顶升装配板通过孔的两侧;工件座将转子送入铆边空间时,固定气缸的气缸臂伸出,限定工件座的位置;在顶升装配板的下方还设置有用于限定顶升固定气缸的气缸臂活动方向的顶升固定座,在顶升固定座上设置有对应顶升固定气缸的气缸臂的豁口,且供顶升固定气缸的气缸臂通过。
33.进一步的,所述转子清洁部分包括防尘壳体和吸尘器,所述防尘壳体设置于设备装配板的上表面;在防尘壳体内设置有清洁空间,在设备装配板上设置有清洁通孔,防尘壳体设置于清洁通孔上方,并在清洁空间靠近设备装配板的一端设置有清洁开口,所述清洁开口与清洁通孔对应,吸尘器设置于设备装配板的下表面,吸尘器的吸尘口与清洁通孔对应;
34.所述防尘壳体包括第一防尘护罩和第二防尘护罩,清洁空间由第一防尘护罩和第二防尘护罩包围形成;
35.所述转子清洁部分话包括壳体控制气缸,所述壳体控制气缸采用阔型手指气缸,其包括两个伸展方向相反的气缸臂,第一防尘护罩与其中一个气缸臂连接,第二防尘罩与另外一个气缸臂连接。
36.进一步的,所述充磁部分固定在设备装配板的下表面,并在设备装配板对应充磁部分的区域设置有充磁开口;所述充磁部分包括充磁头和充磁壳体;所述充磁壳体内设置有充磁头安装空间,充磁头设置于充磁头安装空间内,且充磁头安装空间的上下端面均设置有开口;充磁头内设置有充磁空间,充磁空间的上下端分别设置有充磁上开口与充磁下开口;充磁上开口、充磁下开口以及充磁头安装空间上下端面的开口均与充磁开口对应;转子通过充磁上开口进入充磁空间;
37.所述充磁部分还包括充磁顶升部,所述充磁顶升部包括充磁顶升气缸和充磁顶升支架;所述充磁顶升支架包括充磁滑动板、充磁横板、充磁导杆和顶升轴;所述充磁导杆的一端与设备装配板的下表面连接,充磁导杆的一端的另一端与充磁横板的上表面连接;所述充磁滑动板被充磁导杆穿过,并沿充磁导杆活动;所述充磁顶升气缸的缸体与充磁横板连接,充磁顶升气缸的气缸臂穿过充磁横板与充磁滑动板连接;顶升轴设置于充磁滑动板的上表面,顶升轴的设置位置对应充磁下开口,并且通过充磁下开口进入充磁空间内支撑并顶升转子。
38.进一步的,所述出料组件包括出料气缸和出料承载座,出料气缸和出料承载座均设置于设备装配板的上表面;所述出料气缸的缸体与设备装配板的上表面连接,出料气缸的气缸臂与出料承载座连接;所述出料组件还包括出料限位部,所述出料限位部设置于出料气缸和出料承载座之间;所述出料限位部包括出料限位轴承座、出料导杆和气缸连接板;所述出料气缸的气缸臂与气缸连接板的一处表面连接,气缸连接板的另一处表面与出料导杆的一端连接,出料导杆的另一端与出料承载座连接;所述出料限位轴承座被出料导杆穿过,并且出料限位轴承座固定在设备装配板的上表面。
39.进一步的,所述机架部分包括机架支撑柱和机架盖板,并通过机架支撑柱和机架盖板包围形成机架空间;所述机架空间包括阀岛安装空间、电气装配空间和设备安装空间;充磁机的电气组件设置于电气装配空间内,充磁机的阀岛组件设置于阀岛安装空间内,旋
转分度电机、垂直分度气缸、旋转运输气缸、铆边顶升机构、顶升固定机构、吸尘器和充磁部分设置于设备安装空间内;在机架部分对应电气装配空间的区域设置有电气控制开关,在机架部分对应设备安装空间的区域设置有机架开门;设备装配板位于机架部分的上表面;在机架支撑柱底面的四个角上还设置地脚;
40.所述防护罩部分包括防护罩支撑柱和防护罩盖板,并通过防护罩支撑柱和防护罩盖板包围形成防护空间;在防护罩对应搬运部分两侧的位置设置有防护罩开门;所述防护罩开门包括防护罩前开门和防护罩后开门,其中防护罩前开门对应铁芯铆边部分、转子清洁部分、充磁部分所在一侧,防护罩后开门对应磁瓦供料部分所在一侧;在防护罩部分上还设置有设备控制开关。
41.本发明的有益效果是:
42.本发明通过供料组件、工件组装组件、工件加工组件和出料组件的配合实现了整体的自动化设置,进一步的提升了本发明的加工效率和加工质量;而防护罩部分将其供料组件、工件组装组件、工件加工组件和出料组件包围进一步的提升了本发明的安全使用性能。
43.防护罩部分所设置的供料开口和出料开口,使得本发明的供料和出料也同样可以采用自动化操作,在降低用人成本免除操作人员受伤风险的同时,提升了本发明的加工效率。
44.供料组件包括送工件部分和磁瓦供料部分,工件组装组件包括磁瓦分度机构、磁瓦运输部分和压磁瓦机构;磁瓦分度机构和磁瓦运输部分将磁瓦供料部分内的磁瓦带到送工件部分,并通过压磁瓦机构将磁瓦与转子进行组装;送工件部分和磁瓦供料部分在工件组装组件的作用下完成两种材料的组装,完成组装的转子再进入加工组件内进行加工,进而使得转子与磁瓦的装配过程更为便捷快速,且精度更高、效率更快。
45.在机械手移动板上设置有四个上下抓料机构,使得本发明在使用时能够同时搬运四个转子,进行下一步的加工或是将完成加工的转子取出,大大提升了本发明的工作效率。
附图说明
46.图1为本发明正面整体结构图。
47.图2为本发明反面整体结构图。
48.图3为设备装配板上所有组件的正面结构图。
49.图4为设备装配板上所有组件的反面结构图。
50.图5为磁瓦供料部分结构图。
51.图6为磁瓦供料部分侧面结构图。
52.图7为供料电机和供料丝杆连接处结构图。
53.图8为磁瓦导入工装正面结构图。
54.图9为磁瓦导入工装下表面结构图。
55.图10为送工件部分、磁瓦分度机构和磁瓦运输部分三者分布结构图。
56.图11为磁瓦分度机构结构图。
57.图12为磁瓦运输部分结构图。
58.图13为运输悬臂结构图。
59.图14为送工件部分未装配工件安装导套的结构图。
60.图15为工件安装导套剖面图。
61.图16为压磁瓦机构结构图。
62.图17为下压部结构图。
63.图18为送工件部分、铁芯铆边部分、转子清洁部分、充磁部分、搬运部分和出料组件的分布结构图。
64.图19为铁芯铆边部分结构图。
65.图20为滑槽座、铆压头组件、槽盘和铆边外壳的剖面图。
66.图21为滑槽座、铆压头组件和槽盘三者组合结构图。
67.图22为铆压头组件结构图。
68.图23为铆边顶升机构结构图。
69.图24为转子清洁部分结构图。
70.图25为转子清洁部分的下表面结构图。
71.图26为充磁部分的结构图。
72.图27为充磁壳体处的剖面图。
73.图28为搬运部分正面结构图。
74.图29为搬运部分反面结构图。
75.图30为出料组件结构图。
76.图中标号:
77.1.机架部分;2.防护罩部分;3.供料组件;4.工件组装组件;5.铁芯铆边部分;6.转子清洁部分;7.充磁部分;8.搬运部分;9.出料组件;11.设备装配板;12.机架支撑柱;13.机架盖板;14.阀岛安装空间;15.电气装配空间;16.设备安装空间;17.地脚;18.电气控制开关;19.机架开门;21.供料开口;22.出料开口;23.防护罩支撑柱;24.防护罩盖板;25.防护罩前开门;26.防护罩后开门;27.设备控制开关;31.送工件部分;32.磁瓦供料部分;35.磁瓦导入工装;41.磁瓦分度机构;42.磁瓦运输部分;44.压磁瓦机构;51.滑槽座;52.铆压头组件;53.槽盘;54.铆边气缸;55.铆边外壳;56.铆边顶升机构;57.顶升固定机构;61.防尘壳体;62.吸尘器;63.清洁空间;64.清洁通孔;65.清洁开口;66.第一防尘护罩;67.第二防尘护罩;68.壳体控制气缸;71.充磁开口;72.充磁头;73.充磁壳体;81.机械手移动板;83.搬运支架;84.搬运滑轨;85.搬运滑块;86.搬运气缸;91.出料气缸;92.出料承载座;93.出料限位部;94.出料限位轴承座;95.出料导杆;96.气缸连接板;309.工件安装空间;310.缓冲弹簧;311.送工件气缸;312.工件滑轨;313.送工件移动板;314.送工件滑块;315.工件移动板通孔;316.工件安装导套;317.送工件限位槽;318.送工件限位部;319.送工件限位块;320.送工件限位座;321.磁瓦料盘;322.料盘槽;323.供料气缸;324.供料底板;325.供料电机;326.供料丝杆;327.供料导轨;328.供料滑块;329.螺杆;330.螺母;331.同步轮;332.皮带;333.皮带防护罩;334.供料光电传感器;335.传感器防护罩;336.供料支柱;337.安装座;338.供料支架;339.第一供料直杆;340.第二供料直杆;341.第三供料直杆;342.供料安装底板;343.供料气缸活动块;344.磁瓦横移推板;345.磁瓦推头;346.料盘槽入口;351.磁瓦导入气缸;352.磁瓦导入块;353.磁瓦导入槽;354.导入块上开口;355.导入块下开口;356.垂直导入气缸;357.水平导入气缸;358.气缸接头;359.磁瓦推条;360.导入气缸固定
板;411.分度盘;412.分度轴;413.旋转分度电机;414.垂直分度气缸;415.夹箍;416.导向座;417.分度移动板;418.分度安装板;419.分度导杆;421.运输悬臂;422.磁瓦储存工装;423.垂直运输气缸;424.旋转运输气缸;425.运输气缸座;426.旋转法兰盘;427.法兰轴承座;428.联轴器;429.运输导杆;430.上盖;431.悬臂装配孔;432.悬臂轴承;433.储存工装装配孔;434.磁瓦储存空间;441.顶板;442.压装电缸;443.下压部;444.电缸连接件;445.下压固定板;446.压力传感器;447.压力传感器固定座;448.推杆;449.推杆固定座;450.立柱;451.压装拖链;452.第一压装导杆;453.活动横杆;454.压装位移传感器;455.压装拖链支架;456.第二压装导杆;457.压环;458.压环通过孔;511.铆边空间;512.铆边槽;521.铆压头;522.接触块;523.移动块;531.槽盘通孔;532.槽盘活动孔;533.压迫端;534.放松端;535.槽盘连接块;541.工件座;551.铆边底座;552.铆边盖板;553.滑槽座安装空间;554.铆边底座开口;561.顶升装配板;562.铆边顶升气缸;563.顶升装配板通过孔;564.气缸装配支柱;571.顶升固定气缸;572.顶升固定座;721.充磁空间;722.充磁上开口;723.充磁下开口;731.充磁头安装空间;741.充磁顶升气缸;743.充磁滑动板;744.充磁横板;745.充磁导杆;746.顶升轴;821.垂直抓料气缸;822.手爪气缸;823.第一上下抓料机构;824.第二上下抓料机构;825.第三上下抓料机构;826.第四上下抓料机构;831.搬运固定板;832.搬运支柱;833.第一搬运支座;834.第二搬运支座;861.搬运气缸座;862.搬运气缸连接件。
具体实施方式
78.下面结合附图和具体实施例对本发明进一步说明。应当说明的是,实施例只是对本发明的具体阐述,其目的是为了让本领域技术人员更好地理解本发明的技术方案,不应视为对本发明的限定。
79.实施例:
80.如图1-4所示,一种充磁机,包括供料组件3、工件组装组件4、工件加工组件、出料组件9、机架部分1和防护罩部分2;所述供料组件3、工件组装组件4、工件加工组件和出料组件9均设置于机架部分1的设备装配板11上,防护罩部分2将其供料组件3、工件组装组件4、工件加工组件和出料组件9包围;本发明通过供料组件3、工件组装组件4、工件加工组件和出料组件9的配合实现了整体的自动化设置,进一步的提升了本发明的加工效率和加工质量;而防护罩部分2将其供料组件3、工件组装组件4、工件加工组件和出料组件9包围进一步的提升了本发明的安全使用性能。
81.所述供料组件3包括送工件部分31,在防护罩部分2对应送工件部分31的区域设置有供料开口21,在防护罩部分2对应出料组件9的区域设置有出料开口22;供料开口21和出料开口22的设置使得本发明的供料和出料也同样可以采用自动化操作,在降低用人成本免除操作人员受伤风险的同时,提升了本发明的加工效率。
82.如图10所示,所述供料组件3还包括磁瓦供料部分32,工件组装组件4包括磁瓦分度机构41、磁瓦运输部分42和压磁瓦机构44;所述磁瓦分度机构41和磁瓦运输部分42设置于磁瓦供料部分32和送工件部分31之间,且磁瓦分度机构41设置于磁瓦运输部分42和磁瓦供料部分32之间;压磁瓦机构44设置于送工件部分31的上方;磁瓦供料部分32将磁瓦运输到磁瓦分度机构41内进行分度,磁瓦运输部分42将成分度的磁瓦运输到送工件部分31,通过压磁瓦机构44将转子与磁瓦完成组装;磁瓦分度机构41和磁瓦运输部分42将磁瓦供料部
分32内的磁瓦带到送工件部分31,并通过压磁瓦机构44将磁瓦与转子进行组装;送工件部分31和磁瓦供料部分32在工件组装组件4的作用下完成两种材料的组装,完成组装的转子再进入加工组件内进行加工,进而使得转子与磁瓦的装配过程更为便捷快速,且精度更高、效率更快。
83.如图18所示,工件加工组件包括铁芯铆边部分5、转子清洁部分6、充磁部分7和搬运部分8;送工件部分31、铁芯铆边部分5、转子清洁部分6、充磁部分7和出料组件均设置于搬运部分8的同一侧,并且处于同一直线上;所述送工件部分31和出料组件设置于搬运部分8的两端,铁芯铆边部分5设置于送工件部分31和转子清洁部分6之间,充磁部分7设置于转子清洁部分6和出料组件之间;在搬运部分8上设置有机械手移动板81,机械手移动板81位于送工件部分31、铁芯铆边部分5、转子清洁部分6和充磁部分7的上方,在机械手移动板81上设置有四个上下抓料机构,并且分别对应送工件部分31、铁芯铆边部分5、转子清洁部分6、充磁部分7和出料组件9;机械手移动板81可在搬运气缸86的作用下移动,机械手移动板81的移动方向对应送工件部分31、铁芯铆边部分5、转子清洁部分6、充磁部分7和出料组件9分布的形状,并在上下抓料机构的作用下,将送工件部分31中的转子依次送入铁芯铆边部分5、转子清洁部分6、充磁部分7进行加工,最后将加工后的转子放入出料组件9;在机械手移动板81上设置有四个上下抓料机构,使得本发明在使用时能够同时搬运四个转子,进行下一步的加工或是将完成加工的转子取出,大大提升了本发明的工作效率。
84.如图28-29所示,所述搬运部分8包括搬运支架83,所述搬运支架83包括搬运固定板831和搬运支柱832,在搬运固定板831的后表面上设置有第一搬运支座833,搬运支柱832的一端与第一搬运支座833连接,搬运支柱832的另一端设置有第二搬运支座834,并通过第二搬运支座834与设备装配板11的上表面连接;所述机械手移动板81设置于搬运固定板831的另一表面上,在机械手移动板81朝向搬运固定板831的表面上设置有搬运滑轨84,并在搬运滑轨84上设置有搬运滑块85,所述搬运滑块85与搬运固定板831连接;所述搬运气缸86设置于搬运固定板831上,在搬运固定板831的上端面设置有搬运气缸座861,搬运气缸86的缸体与搬运气缸座861连接,在搬运气缸86的气缸臂上设置有搬运气缸连接件862,且搬运气缸连接件862与机械手移动板81连接;上下抓料机构设置于机械手移动板81远离搬运滑轨84的表面,其包括垂直抓料气缸821和手爪气缸822,垂直抓料气缸821的气缸臂与机械手移动板81连接,手爪气缸822设置于垂直抓料气缸821的气缸臂上;
85.所述上下抓料机构包括第一上下抓料机构823、第二上下抓料机构824、第三上下抓料机构825和第四上下抓料机构826;
86.搬运气缸86的气缸臂伸展时,第一上下抓料机构823对应送工件部分31,第二上下抓料机构824对应铁芯铆边部分5,第三上下抓料机构825对应转子清洁部分6,第四上下抓料机构826对应充磁部分7;
87.搬运气缸86的气缸臂收拢时,第一上下抓料机构823对应铁芯铆边部分5,第二上下抓料机构824对应转子清洁部分6,第三上下抓料机构825对应充磁部分7,第四上下抓料机构826对应充磁机的出料组件。
88.如图5-7所示,磁瓦供料部分32设置于搬运部分8远离铁芯铆边部分5、转子清洁部分6、充磁部分7的一侧,其包括磁瓦料盘321,磁瓦料盘321上设置有料盘槽322,磁瓦设置于料盘槽322内,料盘槽322的开口朝向磁瓦分度机构41,且磁瓦通过该开口进入磁瓦分度机
构41;磁瓦供料部分32包括供料气缸323,供料气缸323将料盘槽322内的磁瓦送入磁瓦分度机构41;磁瓦供料部分32包括供料底板324、供料电机325和供料丝杆326,所述磁瓦料盘321、供料电机325和供料丝杆326设置于供料底板324上,并且磁瓦料盘321在供料电机325和供料丝杆326的带动下进行活动;在供料底板324的上表面设置有供料导轨327,并在供料导轨327上设置有供料滑块328,所述供料滑块328与磁瓦料盘321的下表面连接;所述供料电机325设置于供料底板324的下表面,供料丝杆326设置于供料导轨327之间;供料丝杆326采用滚珠丝杆,其包括螺杆329和螺母330;在供料电机325的输出端以及供料丝杆326的螺杆329靠近供料电机325的一端均设置有同步轮331,同步轮331之间采用皮带332连接和传动,并且在供料丝杆326的同步轮331和供料电机325的同步轮331上设置有将其两者以及皮带332包围在内的皮带防护罩333;供料丝杆326的螺母330与磁瓦料盘321连接;在供料底板324的上表面还设置有检测磁瓦料盘321活动的供料光电传感器334,并且在供料底板324上还设置有传感器防护罩335,传感器防护罩335将供料光电传感器334包围并保护;在供料底板324下表面的四个角上还设置有供料支柱336,供料支柱336的一端与供料底板324的下表面连接,供料支柱336的另一端设置有安装座337,并通过安装座337与设备装配板11连接;所述磁瓦供料部分32包括供料支架338,供料气缸323设置于供料支架338上;所述供料支架338呈“凵”字形,其包括第一供料直杆339、第二供料直杆340和第三供料直杆341,第一供料直杆339的一端以及第三供料直杆341的一端分别与第二供料直杆340的两端连接,第一供料直杆339和第三供料直杆341与第二供料直杆340相互垂直,且第一供料直杆339和第三供料直杆341的朝向一致;第一供料直杆339和第三供料直杆341远离第二供料直杆340的一端均设置有供料安装底板342,并通过供料安装底板342与设备装配板11连接;料盘槽322设置于磁瓦料盘321的上表面,第二供料直杆340设置于磁瓦料盘321的上方;所述供料气缸323设置于第二供料直杆340上,并且在供料气缸323的气缸臂上设置有供料气活动块343,在供料气活动块343上设置有磁瓦横移推板344,并在磁瓦横移推板344上设置有磁瓦推头345;供料气活动块343的活动范围与料盘槽322的设置形状对应,磁瓦推头345将料盘槽322内的磁瓦推入磁瓦分度机构41;所述料盘槽322设置于磁瓦料盘321的上表面,第二供料直杆340设置于磁瓦料盘321的上方,且供料气缸323设置于第二供料直杆340上,便于供料气缸323将磁瓦送入磁瓦分度机构41。
89.在本实施例中,在料盘槽322远离其开口的一端还设置有料盘槽入口346,料盘槽入口346使磁瓦推头345在供料气缸323的带动下进出料盘槽322;磁瓦设置于料盘槽322内,且磁瓦料盘321在供料电机325和供料丝杆326的带动下,将料盘槽322朝向供料气缸323方向推动;当磁瓦料盘321在活动时,磁瓦推头345位于料盘槽322外,当磁瓦料盘321到达预定位置时,磁瓦推头345由料盘槽入口346进入料盘槽322,将料盘槽322内的磁瓦推入磁瓦分度机构41,并沿进入路线退出料盘槽322。
90.如图8-9所示,所述磁瓦供料部分32还包括磁瓦导入工装35,所述磁瓦导入工装35设置于磁瓦分度机构41的上方;磁瓦导入工装35包括磁瓦导入气缸351和磁瓦导入块352;所述磁瓦导入块352设置于第一供料直杆339上,且磁瓦导入块352所在高度对应磁瓦料盘321所在高度;在磁瓦导入块352上设置有磁瓦导入槽353,磁瓦导入槽353设置于磁瓦导入块352靠近料盘槽322的一端,并且与料盘槽322的开口对应;在磁瓦导入块352的上表面以及下表面设置有对应磁瓦导入槽353的导入块上开口354和导入块下开口355;磁瓦导入气
缸351包括垂直导入气缸356和水平导入气缸357;所述垂直导入气缸356通过导入气缸固定板360固定在第二供料直杆340上,在垂直导入气缸356的气缸臂上设置有气缸接头358,并在气缸接头358内设置有磁瓦推条359;所述磁瓦推条359从导入块上开口354进入磁瓦导入槽353,并且可按照料盘槽322的设置方向摆动;所述水平导入气缸357设置在磁瓦导入块352的外表面上,并且水平导入气缸357的气缸臂穿过磁瓦导入块352进入磁瓦导入槽353;
91.在本实施例中,磁瓦从料盘槽322进入磁瓦分度机构41之前还需经过磁瓦导入工装35,并通过磁瓦导入工装35将磁瓦均匀的导入磁瓦分度机构41,便于压磁瓦机构44将转子与磁瓦进行组装;垂直导入气缸356和水平导入气缸357的设置使得磁瓦在其两者的作用下能够平稳且均匀的进入磁瓦分度机构41;磁瓦推条359不仅能够将磁瓦推入磁瓦分度机构41,磁瓦推条359还可按照料盘槽322的设置方向摆动,使得磁瓦导入工装35在同一时间只能导入一定数量的磁瓦,避免磁瓦导入工装35出现堵塞以及磁瓦导入不均匀的情况;在磁瓦导入块352的外表面还设置有磁瓦导入传感器,使得垂直导入气缸356和水平导入气缸357的活动更加精确。
92.如图11所示,磁瓦分度机构41包括分度盘411、分度轴412、旋转分度电机413和垂直分度气缸414,分度盘411处于设备装配板11的上表面,旋转分度电机413和垂直分度气缸414处于设备装配板11的下表面;分度轴412的一端穿过设备装配板11,通过夹箍415与旋转分度电机413的输出轴连接,所述分度盘411设置于分度轴412的另一端;磁瓦分度机构41还包括导向座416,所述导向座416设置于设备装配板11的上表面,并被分度轴412穿过;磁瓦分度机构41包括分度移动板417和分度安装板418,分度移动板417位于分度安装板418的上方,并在分度安装板418的上表面设置有分度导杆419,分度导杆419穿过分度移动板417,且分度移动板417沿分度导杆419活动;所述旋转分度电机413设置于分度移动板417的下表面,并且旋转分度电机413的输出轴穿过分度移动板417与分度轴412连接;垂直分度气缸414的缸体与分度安装板418连接,垂直分度气缸414的气缸臂与分度移动板417连接;所述分度盘411在旋转分度电机413的带动下对进入磁瓦分度机构41的磁瓦进行分度,分度盘411的所在高度在垂直分度气缸414的带动下变动,便于磁瓦运输部分42对磁瓦进行运输工作。
93.如图12-13所示,磁瓦运输部分42包括运输悬臂421、磁瓦储存工装422、垂直运输气缸423和旋转运输气缸424,磁瓦储存工装422设置于运输悬臂421上,运输悬臂421被垂直运输气缸423和旋转运输气缸424带动;运输悬臂421和垂直运输气缸423处于设备装配板11的上表面,旋转运输气缸424处于设备装配板11的下表面;所述磁瓦运输部分42包括运输气缸座425,所述旋转运输气缸424设置于运输气缸座425内;磁瓦运输部分42包括旋转法兰盘426,并在旋转法兰盘426上设置有法兰轴承座427,法兰轴承座427与设备装配板11装配;在旋转运输气缸424的输出轴上设置有联轴器428,并通过联轴器428与旋转法兰盘426的一端连接;磁瓦运输部分42还包括运输导杆429,所述运输悬臂421被运输导杆429穿过,并沿运输导杆429活动;运输导杆429的一端与旋转法兰盘426连接,运输导杆429的另一端与上盖430连接;所述垂直运输气缸423设置于上盖430远离运输导杆429的表面,并且垂直运输气缸423的气缸臂穿过上盖430与运输悬臂421连接;在运输悬臂421的一端设置有悬臂装配孔431,并在悬臂装配孔431内设置有悬臂轴承432,且运输导杆429将悬臂轴承432穿过;在运输悬臂421的另一端设置有储存工装装配孔433,磁瓦储存工装422设置于储存工装装配孔
433内。
94.运输悬臂421在磁瓦运输部分42的垂直运输气缸423和旋转运输气缸424的带动下调整磁瓦储存工装422所在的高度以及所处的位置,便于磁瓦的运输;当磁瓦供料部分32工作时,运输悬臂421将磁瓦储存工装422送至分度盘411上方与分度盘411接触,并且磁瓦储存工装422可以随分度盘411旋转,便于磁瓦均匀的进入磁瓦储存工装422的磁瓦储存空间434内;当磁瓦储存工装422完成磁瓦的储存后运输悬臂421在磁瓦运输部分42的垂直运输气缸423和旋转运输气缸424的带动下将磁瓦储存工装422送至送工件部分31的上方,并对应转子便于压磁瓦机构44将磁瓦与转子进行压装组合。
95.如图14-15所示,送工件部分31包括送工件气缸311、工件滑轨312和送工件移动板313,送工件气缸311、送工件滑轨312和送工件移动板313均设置于设备装配板11的上表面;送工件滑轨312上设置有送工件滑块314,送工件滑块314与送工件移动板313的下表面连接,送工件气缸311的缸体与设备装配板11连接,送工件气缸311的气缸臂与送工件移动板313连接;在送工件移动板313上还设置有工件移动板通孔315,并在工件移动板通孔315内设置有工件安装导套316,需要加工的转子设置于工件安装导套316内;工件安装导套316在送工件移动板313的带动下沿送工件滑轨312活动,使得送工件部分31可以将需要加工的转子送入对应位置,进一步的进行加工,相较于人工操作,在操作降低风险的同时还提升了加工效率;在设备装配板11设置有对应工件安装导套316活动范围的送工件限位槽317,工件安装导套316的一端在送工件限位槽317内活动;所述送工件部分31还包括送工件限位部318;所述送工件限位部318包括送工件限位块319和送工件限位座320,送工件限位块319设置于送工件移动板313的侧边,并且在送工件移动板313的带动下沿送工件滑轨312活动;所述送工件限位部318设置于设备装配板11的上表面,当送工件移动板313到达接收需要加工转子的区域时,送工件限位块319和送工件限位座320接触;所述送工件限位槽317和送工件限位部318设置使得送工件气缸311在运送需要加工的转子时能够更加精确,进而避免需要加工的转子因为放置不稳定,导致转子和磁瓦的组合工序出现问题;所述工件安装导套316内设置有工件安装空间309,转子设置于工件安装空间309内;在工件安装空间309内还设置有缓冲弹簧310,缓冲弹簧310的一端与工件安装空间309的内壁连接,缓冲弹簧310的另一端与转子接触;所述缓冲弹簧310避免了转子与磁瓦在压磁瓦机构44的作用下完成压装后出现位移且无法复位的情况,使得转子和磁瓦完成组合后能顺利的由搬运部分8送入铁芯铆边部分5。
96.如图16-17所示,压磁瓦机构44包括顶板441、压装电缸442和下压部443;所述压装电缸442设置于顶板441的上表面,并且下压部443置于顶板441的下表面,压装电缸442的输出轴穿过顶板441与下压部443连接;所述下压部443包括电缸连接件444、下压固定板445、压力传感器446、压力传感器固定座447、推杆448和推杆固定座449;所述电缸连接件444与压装电缸442的输出轴连接,且电缸连接件444远离压装电缸442的一端与下压固定板445的上表面连接;下压固定板445的下表面与压力传感器固定座447的一端连接,压力传感器固定座447的另一端与推杆固定座449连接;所述压力传感器446设置于压力传感器固定座447内,进而提升压磁瓦机构44压装时的精度,避免磁瓦或转子在压装过程中损坏;推杆448设置于推杆固定座449远离压力传感器固定座447的一端;压磁瓦机构44包括立柱450,立柱450的一端与顶板441的下表面连接,立柱450的另一端与设备装配板11的上表面连接;压磁
瓦机构44包括压装拖链451和第一压装导杆452;第一压装导杆452的一端穿过顶板441与下压固定板445连接,在第一压装导杆452的另一端设置有活动横杆453;在顶板441的上表面还设置有检测活动横杆453活动的压装位移传感器454,使得压磁瓦机构44对转子和磁瓦的压装更为精密;压装拖链451的一端穿过顶板441与下压固定板445连接,压装拖链451的另一端设置于压装拖链支架455内,并在压装拖链支架455内活动,压装拖链支架455与顶板441的上表面连接;压装电缸442的输出轴、压装拖链451和第一压装导杆452的活动方向对应;所述拖链的设置进一步的提升了压磁瓦机构44组装转子和磁瓦的精度;推杆448的数量与磁瓦储存空间434的对应,并且在压装电缸442的作用下将磁瓦储存空间434内的磁瓦压入转子。
97.压磁瓦机构44还包括第二压装导杆456和压环457,所述第二压装导杆456的一端与下压固定板445的下表面连接;压环457被第二压装导杆456穿过,并沿第二压装导杆456活动;在第二压装导杆456上套设有弹簧,弹簧的一端与压环457连接,弹簧的另一端与下压固定板445的下表面连接;在压环457上设置有压环通过孔458供推杆448穿过进行压装;所述压环457在推杆448与转子接触前,提前与转子接触,进而确保磁瓦压入转子的位置正确,而弹簧的设置使得压环457在确定转子压入位置后,能够使压环457沿第二压装导杆456回缩,避免损坏转子。
98.如图19-23所示,铁芯铆边部分5包括滑槽座51、铆压头组件52和槽盘53,其三者设置于设备装配板11的上表面;在滑槽座51的中间设置有铆边空间511,在滑槽座上还设置有环绕铆边空间设置的铆边槽;所述铆压头组件52设置于铆边槽512内,并且各铆压头组件52在槽盘53的带动下同时进行朝向或远离铆边空间511的活动;所述槽盘53覆盖在滑槽座51的上表面;在槽盘53的中间设置有槽盘通孔531,转子通过槽盘通孔531进入铆边空间511;铆边槽512设置于滑槽座51的上表面,槽盘53将铆压头组件52限定在铆边槽512内,并且槽盘53与铆压头组件52接触;所述铆压头组件52包括铆压头521、接触块522和移动块523,移动块523设置于铆边槽512内,铆压头521设置于移动块523朝向铆边空间511的一端,接触块522设置于移动块523的上表面与槽盘53接触;槽盘53上设置有槽盘活动孔532,所述槽盘活动孔532环绕槽盘通孔531设置,并且接触块522设置于槽盘活动孔532内;槽盘活动孔532的两端分别为压迫端533和放松端534,压迫端533至槽盘通孔531中心点的距离大于放松端534至槽盘通孔531中心点的距离;各槽盘活动孔532的放松端534均处于对应顺时针方向的一侧;铁芯铆边部分5还包括铆边气缸54和铆边外壳55;在槽盘53的外侧表面设置有槽盘连接块535,槽盘连接块535的一端与槽盘53连接,槽盘连接块535的另一端与铆边气缸54的气缸臂连接,槽盘53在铆边气缸54的带动下进行活动;所述铆边外壳55包括铆边底座551和铆边盖板552,在铆边底座551内设置有滑槽座安装空间553,铆边盖板552将滑槽座安装空间553封闭;所述滑槽座51、铆压头组件52和槽盘53设置于滑槽座安装空间553内;在铆边底座551上还设置有铆边底座开口554,铆边底座开口554对应槽盘连接块535的活动范围;铆边外壳55和铆边气缸54设置于设备装配板11的上表面;在本实施例中,铆边气缸54的气缸臂伸展时槽盘53沿顺时针转动,使得压迫端533与接触块522接触,进而使得铆压头521对磁瓦与转子进行铆压;当铆压完成后,铆边气缸54的气缸臂收缩时槽盘53沿逆时针转动,使得放松端534与接触块522接触,使得铆压头521远离转子。
99.铁芯铆边部分5还包括铆边顶升机构56和顶升固定机构57,铆边顶升机构56和顶
升固定机构57设置于设备装配板11的下表面;铆边顶升机构56包括顶升装配板561和铆边顶升气缸562;顶升装配板561固定在设备装配板11的下表面,在顶升装配板561设置有对应铆边空间511的顶升装配板通过孔563;所述铆边顶升气缸562设置于顶升装配板561下表面,铆边顶升气缸562通过气缸装配支柱564与顶升装配板561进行装配;铆边顶升气缸562的气缸臂上设置有工件座541,工件座541在铆边顶升气缸562的作用下穿过设备装配板11进入铆边空间511支撑并顶升转子;所述工件座541在铆边顶升气缸562作用下上升到能够接收未铆边的转子的位置,并且未铆边的转子在工件座541的支撑下到达铆边空间511进行铆边工序,转子完成铆边后通过工件座541将其送至上下抓料机构能够抓取的位置。
100.所述顶升固定机构57设置于顶升装配板561的下方,顶升固定机构57包括顶升固定气缸571,顶升固定气缸571设置于顶升装配板通过孔563的两侧;工件座541将转子送入铆边空间511时,固定气缸的气缸臂伸出,限定工件座541的位置;在顶升装配板561的下方还设置有用于限定顶升固定气缸571的气缸臂活动方向的顶升固定座572,在顶升固定座572上设置有对应顶升固定气缸571的气缸臂的豁口,且供顶升固定气缸571的气缸臂通过;当未铆边的转子在工件座541的支撑下到达铆边空间511内进行铆边工序时,所述顶升固定机构57的顶升固定气缸571的气缸臂与工件座541接触并限定工件座541位置,使得铆边效果更佳。
101.如图24-25所示,所述转子清洁部分6包括防尘壳体61和吸尘器62,所述防尘壳体61设置于设备装配板11的上表面;在防尘壳体61内设置有清洁空间63,在设备装配板11上设置有清洁通孔64,防尘壳体61设置于清洁通孔64上方,并在清洁空间63靠近设备装配板11的一端设置有清洁开口65,所述清洁开口65与清洁通孔64对应,吸尘器62设置于设备装配板11的下表面,吸尘器62的吸尘口与清洁通孔64对应;所述防尘壳体61包括第一防尘护罩66和第二防尘护罩67,清洁空间63由第一防尘护罩66和第二防尘护罩67包围形成;所述转子清洁部分6话包括壳体控制气缸68,所述壳体控制气缸68采用阔型手指气缸,其包括两个伸展方向相反的气缸臂,第一防尘护罩66与其中一个气缸臂连接,第二防尘罩与另外一个气缸臂连接;当完成铆边的转子进入第一防尘护罩66和第二防尘护罩67之间后,壳体控制气缸68将第一防尘护罩66和第二防尘护罩67闭合,使吸尘器62精确的对清洁空间63内的转子进行清洁,避免吸尘器62的吸尘范围过大导致吸尘的效果不佳。
102.如图26-27所示,所述充磁部分7固定在设备装配板11的下表面,并在设备装配板11对应充磁部分7的区域设置有充磁开口71;所述充磁部分7包括充磁头72和充磁壳体73;所述充磁壳体73内设置有充磁头安装空间731,充磁头72设置于充磁头安装空间731内,且充磁头安装空间731的上下端面均设置有开口;充磁头72内设置有充磁空间721,充磁空间721的上下端分别设置有充磁上开口722与充磁下开口723;充磁上开口722、充磁下开口723以及充磁头安装空间731上下端面的开口均与充磁开口71对应;转子通过充磁上开口722进入充磁空间721;所述充磁部分7还包括充磁顶升部,所述充磁顶升部包括充磁顶升气缸741和充磁顶升支架;所述充磁顶升支架包括充磁滑动板743、充磁横板744、充磁导杆745和顶升轴746;所述充磁导杆745的一端与设备装配板11的下表面连接,充磁导杆745的一端的另一端与充磁横板744的上表面连接;所述充磁滑动板743被充磁导杆745穿过,并沿充磁导杆745活动;所述充磁顶升气缸741的缸体与充磁横板744连接,充磁顶升气缸741的气缸臂穿过充磁横板744与充磁滑动板743连接;顶升轴746设置于充磁滑动板743的上表面,顶升轴
746的设置位置对应充磁下开口723,并且通过充磁下开口723进入充磁空间721内支撑并顶升转子;搬运部分8将清洁完成的转子送入充磁部分7,并且与顶升轴746接触,在顶升轴746的牵引下进入充磁空间721进行充磁工序;转子完成充磁后,再通过顶升轴746将其顶升到上下抓料机构可以抓取的区域,最后将其放入出料组件。
103.如图30所示,所述出料组件包括出料气缸91和出料承载座92,出料气缸91和出料承载座92均设置于设备装配板11的上表面;所述出料气缸91的缸体与设备装配板11的上表面连接,出料气缸91的气缸臂与出料承载座92连接;所述出料组件还包括出料限位部93,所述出料限位部93设置于出料气缸91和出料承载座92之间;所述出料限位部93包括出料限位轴承座94、出料导杆95和气缸连接板96;所述出料气缸91的气缸臂与气缸连接板96的一处表面连接,气缸连接板96的另一处表面与出料导杆95的一端连接,出料导杆95的另一端与出料承载座92连接;所述出料限位轴承座94被出料导杆95穿过,并且出料限位轴承座94固定在设备装配板11的上表面,进而限定出料导杆95的工作行程,防止其送出转子成品时出现偏移;充磁后的转子通过搬运部分8的搬运,放置在出料承载座92上,并且出料承载座92在出料气缸91的推动下将完成加工的转子送到出料开口22。
104.所述机架部分1包括机架支撑柱12和机架盖板13,并通过机架支撑柱12和机架盖板13包围形成机架空间;所述机架空间包括阀岛安装空间14、电气装配空间15和设备安装空间16;充磁机的电气组件设置于电气装配空间15内,充磁机的阀岛组件设置于阀岛安装空间14内,旋转分度电机413、垂直分度气缸414、旋转运输气缸424、铆边顶升机构56、顶升固定机构57、吸尘器62和充磁部分7设置于设备安装空间16内;在机架部分1对应电气装配空间15的区域设置有电气控制开关18,用于控制电气组件;在机架部分1对应设备安装空间16的区域设置有机架开门19,便于后期的检测和检修;设备装配板11位于机架部分1的上表面;在机架支撑柱12底面的四个角上还设置地脚17,便于本发明整体的放置;
105.所述防护罩部分2包括防护罩支撑柱23和防护罩盖板24,并通过防护罩支撑柱23和防护罩盖板24包围形成防护空间;在防护罩对应搬运部分8两侧的位置设置有防护罩开门;所述防护罩开门包括防护罩前开门25和防护罩后开门26;防护罩前开门25对应铁芯铆边部分5、转子清洁部分6、充磁部分7所在一侧,便于操作人员查看各部分的工作状态,也便于检修;防护罩后开门26对应磁瓦供料部分32所在一侧,在便于检修的同时使得磁瓦供料部分32添加磁瓦更加方便;在防护罩部分2上还设置有设备控制开关27,用于控制本发明。
106.充磁机的工作流程如下:
107.1.送工件部分31将需要加工的转子送到指定位置。
108.2.磁瓦运输部分42的运输悬臂421将磁瓦储存工装422运送到分度盘411上,磁瓦供料部分32工作将磁瓦均匀的装入磁瓦储存工装422内。
109.3.磁瓦运输部分42的运输悬臂421将装配了磁瓦的磁瓦储存工装422送至需要加工的转子所在位置的上方。
110.4.压磁瓦机构44将磁瓦从磁瓦储存工装422的磁瓦储存空间434压入转子,进而使转子和磁瓦完成组合。
111.5.搬运部分8将完成组合的转子和磁瓦送入铁芯铆边部分5,进行铆边。
112.6.搬运部分8将完成铆边的转子从铁芯铆边部分5送入转子清洁部分6,进行清洁。
113.7.搬运部分8将完成清洁的转子从铁芯铆边部分5送入充磁部分7,进行充磁。
114.8.最后搬运部分8将完成充磁的转子送入出料组件9,通过出料组件9将完成所有加工工序的转子送出充磁机。
115.值得说明的是,本发明的其他技术方案均属于现有技术,故不作赘述。
116.以上所述仅是本发明优选实施方式,应当指出,对于本技术领域的普通技术人员,在不脱离本发明构思的前提下,还可以做出若干改进和润饰,这些改进和润饰也应视为本发明保护范围。
再多了解一些
本文用于企业家、创业者技术爱好者查询,结果仅供参考。