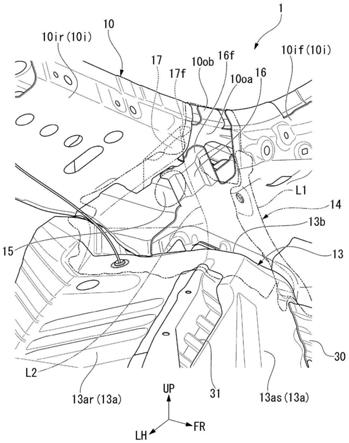
1.本发明涉及一种车体后部结构。
背景技术:
2.作为车辆的车体后部结构,已知有下述结构,即:从车体左右的后部向车顶侧部延伸的后柱(rear pillar)、与覆盖车体左右的后避震器(rear damper)的上部区域的避震器外壳(damper housing)之间由角撑(gusset)连结(例如参照专利文献1)。
3.专利文献1所记载的车体后部结构将车外侧的柱外件(pillar outer)与车内侧的柱内件(pillar inner)相互结合而形成闭合截面结构的后柱,将大致u字状的截面沿上下方向连续的角撑的上端部接合于后柱的下部区域。角撑的下端部结合于避震器外壳。而且,在后柱的闭合截面内,以与角撑的前壁和后壁的位置匹配的方式安装有一对隔板(bulk head,补强壁)。
4.所述车体后部结构中,从后避震器输入至避震器外壳的上下方向的负荷通过角撑及隔板由后柱支撑。
5.[现有技术文献]
[0006]
[专利文献]
[0007]
[专利文献1]日本专利第6402250号公报
技术实现要素:
[0008]
[发明所要解决的问题]
[0009]
专利文献1所记载的车体后部结构中,在后柱的闭合截面内,以与角撑的前壁和后壁的位置匹配的方式安装有一对隔板。隔板通过焊接等而接合于后柱的内表面。因此,将隔板安装于后柱的内表面的作业困难。
[0010]
而且,专利文献1所记载的车体后部结构中,在将隔板焊接固定于后柱的内表面的情况、或将后柱的柱外件焊接固定于避震器外壳的车外侧的上方伸出壁等的情况下,需要在后柱设置焊接作业用的多个开口。此时,为了避免由开口导致的后柱的刚性降低而必须追加补强构件。
[0011]
因此,本发明欲提供一种车体后部结构,可确保后柱的充分刚性且实现制造的容易化。
[0012]
[解决问题的技术手段]
[0013]
本发明的车体后部结构为了解决所述问题,采用以下结构。
[0014]
即,本发明的车体后部结构的特征在于包括:后柱(例如实施方式的后柱10),从车体左右的后部向车顶侧部延伸,将车外侧的柱外件(例如实施方式的柱外件10o)与车内侧的柱内件(例如实施方式的柱内件10i)相互接合而形成闭合截面;避震器外壳(例如实施方式的避震器外壳13),覆盖后避震器的上部区域;以及角撑(例如实施方式的角撑14),将所述避震器外壳与所述后柱连结,所述柱内件以所述避震器外壳的顶壁(例如实施方式的顶
壁13b)的上方位置为界分离为前侧内板与后侧内板而构成,在所述前侧内板与所述后侧内板之间配置有远离部(例如实施方式的远离部15),在所述前侧内板和所述后侧内板的面向所述远离部的端缘,形成有以截面大致l字状折曲且对与所述柱外件之间的闭合截面进行补强的隔板部(例如实施方式的隔板部16、隔板部17),所述角撑的上部以堵塞所述远离部的方式结合于所述前侧内板和所述后侧内板。
[0015]
所述车体后部结构中,在制造时,在柱内件的前侧内板和后侧内板预先形成隔板部,在此状态下将前侧内板和后侧内板结合于柱外件。然后将角撑结合于避震器外壳和后柱,利用角撑的上部来堵塞前侧内板与后侧内板的远离部。通过采用所述车体后部结构,从而可确保后柱的充分刚性且实现制造的容易化。
[0016]
所述隔板部也可结合于所述柱外件。
[0017]
此时,与柱内件一体形成的隔板部在面向远离部的位置结合于柱外件,因而可获得牢固的后柱的截面。而且,柱内件的远离部由角撑的上部堵塞,因而可进一步提高后柱的刚性。
[0018]
所述角撑的上部也可结合于所述柱内件的与车宽方向大致正交的面。
[0019]
此时,从后避震器输入的上下方向的输入负荷通过角撑的上部由柱内件作为剪切负荷而接住。因此,后避震器的支撑刚性提高,车辆的操控稳定性提高。
[0020]
所述柱外件也可在与所述柱内件的远离部对应的位置的、车宽方向内侧的端部,具有与车宽方向大致正交地延伸的凸缘部(例如实施方式的凸缘部10ob),所述角撑结合于所述柱外件的所述凸缘部、和所述避震器外壳的与车宽方向大致正交的面。
[0021]
此时,从后避震器输入的上下方向的输入负荷通过角撑而传递至柱内件和柱外件。此时,从避震器外壳输入至角撑的负荷作为剪切负荷而由角撑接住,从角撑输入至柱内件及柱外件的负荷作为剪切负荷而由柱内件和柱外件接住。因此,在采用所述结构的情况下,可提高后避震器的支撑刚性,进一步提高车辆的操控稳定性。
[0022]
所述角撑也可包含经前后分割的多个角撑板(例如实施方式的前角撑板14f、后角撑板14r)。
[0023]
此时,可将各角撑板分别结合于后柱或避震器外壳等,因而可容易且准确地进行角撑的结合作业。
[0024]
也可在一个所述角撑板形成有堵塞部(例如实施方式的凸缘部14b),此堵塞部将所述前侧内板与所述后侧内板的侧面之间的由所述远离部形成的间隙堵塞。
[0025]
此时,前侧内板与后侧内板的侧面之间的间隙由一个角撑板的堵塞部堵塞,因而可进一步提高前侧内板与后侧内板的结合部的强度。
[0026]
所述柱外件也可横跨所述远离部而结合于所述后侧内板和所述前侧内板,并且前部侧分支为向前方延伸的前方伸出部(例如实施方式的前方伸出部10of)与向车宽方向内侧延伸的内侧伸出部(例如实施方式的内侧伸出部10og),所述前方伸出部结合于车顶侧梁(例如实施方式的车顶侧梁11),所述内侧伸出部结合于后车顶拱门(例如实施方式的后车顶拱门12)。
[0027]
此时,可使从后避震器输入至避震器外壳的负荷经由角撑及后柱分散至车顶侧的结构体。因此,在采用本结构的情况下,可提高后避震器的支撑刚性,进一步提高车辆的操控稳定性。
[0028]
所述角撑也可具有大致u字状的截面沿上下方向连续的u字状截面部(例如实施方式的u字状截面部14a),所述前侧内板和所述后侧内板的各所述隔板部以与所述u字状截面部的前侧的棱线(例如实施方式的棱线l1)和后侧的棱线(例如实施方式的棱线l2)的各伸出方向匹配的方式配置。
[0029]
此时,通过使后柱的前后的隔板部与角撑的前后的棱线的伸出方向匹配,从而角撑与后柱的结合体的强度及刚性提高。由此,可利用强度及刚性高的角撑与后柱的结合体来稳定地支撑从后避震器输入至避震器外壳的负荷。
[0030]
也可在所述避震器外壳,以与所述u字状截面部的前侧的棱线和后侧的棱线的各伸出方向匹配的方式,安装有前侧补强构件(例如实施方式的前侧补强构件30)和后侧补强构件(例如实施方式的后侧补强构件31)。
[0031]
此时,可利用强度及刚性高的避震器外壳、角撑及后柱的结合体来稳定地支撑从后避震器输入至避震器外壳的负荷。
[0032]
所述避震器外壳也可具有从所述顶壁的车宽方向外侧的端部向上方伸出的接合凸缘(例如实施方式的接合凸缘13c),所述柱外件具有从车宽方向外侧抵接于所述接合凸缘并接合于所述接合凸缘的接合壁(例如实施方式的接合壁10oe),关于所述柱内件,下壁设定得低于所述接合凸缘的上端部,并且在所述接合凸缘的车宽方向内侧位置配置有前后宽度较所述接合凸缘更宽的所述远离部。
[0033]
此时,可使后柱的截面低且小型,并且可在将后柱组装于避震器外壳时,使柱外件的接合壁从车宽方向外侧大致水平地移动并触碰避震器外壳的接合凸缘,将接合壁与接合凸缘容易地焊接固定。此时,柱内件虽然下壁低于接合凸缘的上端部,但在柱内件上的与接合凸缘对应的位置(接合凸缘的车宽方向内侧位置)配置有远离部,因而可避免柱内件与接合凸缘发生干扰。
[0034]
[发明的效果]
[0035]
本发明在前侧内板和后侧内板的面向远离部的端缘折曲地形成有隔板部,因而可在后柱的内侧容易地形成对后柱的闭合截面进行补强的隔板部。
[0036]
而且,本发明中,设于柱内件的远离部由结合于后柱的角撑的上部堵塞,因而可在组装角撑之前的状态下,通过远离部容易地进行柱外件与其他构件的焊接作业等。
[0037]
因此,在采用本发明的情况下,可确保后柱的充分刚性,并且实现车体后部的制造的容易化。
附图说明
[0038]
图1为表示实施方式的车辆的后部的立体图。
[0039]
图2为从车内侧观看实施方式的车辆的图1的ii部的立体图。
[0040]
图3为从图2去掉了角撑的车辆的立体图。
[0041]
图4为从图2的iv箭视方向观看实施方式的车辆的立体图。
[0042]
图5为从图4去掉了角撑的车辆的立体图。
[0043]
图6为沿着图2的vi-vi线将一部分截断的车辆的局部截面立体图。
[0044]
图7为在沿着图2的vi-vi线的截面上重叠记载以往例的组装形态的图。
[0045]
[符号的说明]
[0046]
10:后柱
[0047]
10o:柱外件
[0048]
10ob:凸缘部
[0049]
10oe:接合壁
[0050]
10of:前方伸出部
[0051]
10og:内侧伸出部
[0052]
10i:柱内件
[0053]
10if:前侧内板
[0054]
10ir:后侧内板
[0055]
13b:顶壁
[0056]
11:车顶侧梁
[0057]
12:后车顶拱门
[0058]
13:避震器外壳
[0059]
13c:接合凸缘
[0060]
14:角撑
[0061]
14a:u字状截面部
[0062]
14b:凸缘部(堵塞部)
[0063]
15:远离部
[0064]
16、17:隔板部
[0065]
30:前侧补强构件
[0066]
31:后侧补强构件
[0067]
l1:前侧的棱线
[0068]
l2:后侧的棱线
具体实施方式
[0069]
以下,基于附图对本发明的实施方式进行说明。此外,在附图的适当部位,标注有指代车辆的前方的箭头fr、指代车辆的上方的箭头up、及指代车辆的左侧方的箭头lh。
[0070]
图1为从左斜上方观看本实施方式的车辆1的后部的骨架部的立体图,图2为从车内侧的后斜下方观看图1的ii部的立体图。
[0071]
实施方式的车辆1在车体后部的左右两侧,配置有从后部侧向车顶侧部向斜上方延伸的后柱10。如图1所示,后柱10的前端侧接合于车体左右的车顶侧梁(roof side rail)11和后车顶拱门(rear roof arch)12。
[0072]
在左右的后柱10的靠上部的部分的下方侧,配置有避震器外壳13,此避震器外壳13覆盖车辆左右的后避震器(未图示)的上部区域。避震器外壳13包括水平截面为大致帽状的本体部13a、及覆盖本体部13a的上端侧且支撑未图示的后避震器的上端部的顶壁13b(参照图3、图5)。
[0073]
与避震器外壳13的顶壁13b相连的、本体部13a的上端部分通过角撑14而连结于后柱10。角撑14具有大致u字状的截面沿上下方向连续的u字状截面部14a。u字状截面部14a的下端部分接合于避震器外壳13的本体部13a的上部区域。在u字状截面部14a的上端部,延伸
设置有接合于后柱10的凸缘部14b、凸缘部14c、凸缘部14d。避震器外壳13的本体部13a的上端部与后柱10由角撑14连结。
[0074]
图3为从图2去掉了角撑14的立体图。而且,图4为车辆1的图2的iv箭视图,图5为从图4去掉了角撑14的立体图。
[0075]
角撑14包括:后角撑板14r,下端部接合于避震器外壳13的本体部13a的后壁13ar和侧壁13as;以及前角撑板14f,下端部接合于避震器外壳13的本体部13a的前壁13af和侧壁13as的靠前部的部分。即,角撑14包含多个角撑板。在后角撑板14r的上端部形成有凸缘部14b、凸缘部14c,在前角撑板14f的上端部形成有凸缘部14d。
[0076]
后柱10包括位于车外侧的柱外件10o及位于车内侧的柱内件10i。关于后柱10,将柱外件10o与柱内件10i相互接合而形成在车体前后方向连续的闭合截面。
[0077]
如图3、图5所示,柱内件10i以避震器外壳13的顶壁13b的上方位置为界分离为前侧内板10if与后侧内板10ir而构成。在前侧内板10if与后侧内板10ir之间配置有远离部15。
[0078]
在前侧内板10if的面向远离部15的后侧的端缘,形成有向上方侧以大致l字状折曲且对与柱外件10o之间的闭合截面进行补强的隔板部16。同样地,在后侧内板10ir的面向远离部15的前侧的端缘,形成有向上方侧以大致l字状折曲且对与柱外件10o之间的闭合截面进行补强的隔板部17。在各隔板部16、17的前端部,延伸设置有向远离部15的方向折曲的接合凸缘16f、接合凸缘17f。各接合凸缘16f、17f接合于柱外件10o的内侧面。
[0079]
图6为将避震器外壳13、后柱10及角撑14的结合体沿着图2的vi-vi线截断的局部截面立体图,图7为在避震器外壳13、后柱10及角撑14的结合体的沿着图2的vi-vi线的截面图上,以假想线重叠记载以往例的组装形态的图。
[0080]
如图7所示,柱内件10i(后侧内板10ir、前侧内板10if)的将远离部15除外的部位呈具有下述部分的截面形状:内侧壁10ia,从车宽方向内侧的端部向铅垂上方延伸;下壁10ib,从内侧壁10ia的下端大致水平地向车宽方向外侧延伸;外侧壁10ic,一边从下壁10ib的车宽方向外侧的端部向车宽方向外侧倾斜一边向上方延伸;以及外凸缘10id,从外侧壁10ic的上端部向车宽方向外侧延伸。
[0081]
而且,柱外件10o的远离部15的附近部呈具有下述部分的截面形状:上壁10oa,大致水平地延伸;凸缘部10ob,从上壁10oa的车宽方向内侧的端部向铅垂上方折曲并延伸;外侧壁10oc,从上壁10oa的车宽方向外侧的端部向铅垂下方折曲并延伸;延长壁10od,从外侧壁10oc的下端向车宽方向外侧延伸;以及接合壁10oe,从延长壁10od的车宽方向外侧的端部向下方折曲并延伸。凸缘部10ob在柱外件10o的车宽方向内侧的端部,与车宽方向大致正交地延伸。
[0082]
关于柱内件10i与柱外件10o,将柱内件10i的内侧壁10ia的上缘部与柱外件10o的凸缘部10ob接合,并且将柱内件10i的外凸缘10id与柱外件10o的延长壁10od。
[0083]
柱外件10o横跨远离部15而结合于后侧内板10ir和前侧内板10if。而且,柱外件10o如图1所示,前部侧分支为向前方延伸的前方伸出部10of与向车宽方向内侧延伸的内侧伸出部10og。前方伸出部10of结合于车顶侧梁11,内侧伸出部10og结合于后车顶拱门12。
[0084]
此处,角撑14的上部的后侧的凸缘部14c如图2所示那样向后方折曲并延伸,角撑14的上部的前侧的凸缘部14d如图4所示那样向前方折曲并延伸。后侧的凸缘部14c接合于
后侧内板10ir的下壁中的、远离部15的前侧的缘部,前侧的凸缘部14d接合于前侧内板10if的下壁中的、远离部15的后侧的缘部。
[0085]
而且,角撑14的上部的中央的凸缘部14b以大致直线状向上方延伸。中央的凸缘部14b以前后横跨后侧内板10ir与前侧内板10if的内侧壁中的、由远离部15形成的间隙的方式,接合于后侧内板10ir的前缘部和前侧内板10if的后缘部。中央的凸缘部14b如上文所述,一体地形成于后角撑板14r的上部。
[0086]
本实施方式中,中央的凸缘部14b构成堵塞前侧内板10if与后侧内板10ir的侧面之间的间隙的堵塞部。而且,后侧内板10ir与前侧内板10if的内侧壁向铅垂上方延伸,凸缘部14b(角撑14的上部)所接合的面设为与车宽方向大致正交的面。
[0087]
而且,如图3、图5所示,在由远离部15所形成的、前侧内板10if与后侧内板10ir的侧面之间的间隙中,柱外件10o的车宽方向内侧的凸缘部10ob露出。角撑14的中央的凸缘部14b的上缘部分也接合于柱外件10o的凸缘部10ob。
[0088]
另一方面,角撑14的下缘部接合于避震器外壳13的侧壁13as的与车宽方向大致正交的面。
[0089]
此处,角撑14的u字状截面部14a在侧壁与前壁的交界部配置有大致沿上下方向延伸的前侧的棱线l1,在侧壁与后壁的交界部同样地配置有大致沿上下方向延伸的后侧的棱线l2。后柱10的前后的隔板部16、17如图3、图5所示,以与角撑14的前后的棱线l1、l2匹配的方式形成。
[0090]
而且,在避震器外壳13的本体部,以与角撑14的前后的棱线l1、l2的各伸出方向匹配的方式,安装有前侧补强构件30和后侧补强构件31。前侧补强构件30具有与角撑14的前侧的棱线l1的延伸方向匹配的棱线,后侧补强构件31具有与角撑14的后侧的棱线l2的延伸方向匹配的棱线。
[0091]
而且,如图6、图7所示,避震器外壳13的顶壁13b朝向车宽方向外侧向上方倾斜。在顶壁13b的车宽方向外侧的端部,延伸设置有向铅垂上方延伸的接合凸缘13c。柱外件10o的车宽方向外侧的接合壁10oe从车宽方向外侧抵接于接合凸缘13c,在此状态下接合壁10oe通过焊接而结合。
[0092]
在将后柱10组装于避震器外壳13的上部的情况下,以柱内件10i的下壁10ib的高度低于接合凸缘13c的上端部的方式,使后柱10从避震器外壳13的车宽方向外侧位置直接向车宽方向内侧移动。此时,在柱内件10i中的与接合凸缘13c对应的前后位置,配置有前后宽度较接合凸缘13c更宽的远离部15,因此即便使后柱10向车宽方向内侧水平地移动,也可避免柱内件10i的内侧壁10ia或下壁10ib等与避震器外壳13的接合凸缘13c发生干扰。这样,若后柱10在车宽方向移动某程度,则柱外件10o的接合壁10oe抵接于避震器外壳13的接合凸缘13c的车外侧面,由此进行定位。柱外件10o的接合壁10oe与避震器外壳13的接合凸缘13c在此状态下经焊接固定。而且,随后角撑14的上部焊接固定于后柱10。
[0093]
此外,图7中,以假想线来表示未在柱内件设有远离部的、以往例的后柱10c的情况的组装形态。
[0094]
以往例的后柱10c的情况下,在将后柱10c安装于避震器外壳13的上部时,如图7中的箭头所示,使后柱10c从避震器外壳13的车宽方向外侧的上方位置向车宽方向内侧且向下方移动。由此,避免柱内件的内侧壁或下壁与避震器外壳13的接合凸缘13c发生干扰。这
样,柱内件10i的下壁10ib移动至较接合凸缘13c的上端部更靠内侧下方时,使后柱10在车宽方向内水平地移动。然后,柱外件的接合壁抵接于避震器外壳13的接合凸缘13c的车外侧面时,将柱外件的接合壁与避震器外壳13的接合凸缘13c焊接固定。
[0095]
上文所述的本实施方式的结构中,在将后柱10c安装于避震器外壳13的上部时,不需要下述活动,即:使后柱10c从避震器外壳13的车宽方向外侧的上方位置向车宽方向内侧且向下方移动。
[0096]
如以上那样,本实施方式的车体后部结构在柱内件10i的前侧内板10if和后侧内板10ir的面向远离部15的端缘,折曲地形成有隔板部16、隔板部17,因而可在后柱10的内侧容易地形成对后柱10的闭合截面进行补强的隔板部16、隔板部17。即,在采用本实施方式的车体后部结构的情况下,可在制造时,在柱内件10i的前侧内板10if和后侧内板10ir预先形成隔板部16、隔板部17,在此状态下将前侧内板10if和后侧内板10ir结合于柱外件10o。
[0097]
而且,本实施方式的车体后部结构中,设于柱内件10i的远离部15由结合于后柱10的角撑14的上部堵塞,因而可在组装角撑14之前的状态下,通过远离部15容易地进行柱外件10o与其他构件的焊接作业等。因此,在采用本实施方式的车体后部结构的情况下,可确保后柱10的充分刚性并且实现车体后部的制造的容易化。
[0098]
而且,本实施方式的车体后部结构中,与柱内件10i一体形成的隔板部16、隔板部17在面向远离部15的位置结合于柱外件10o,因而可获得牢固的后柱10的截面。而且,柱内件10i的远离部15由角撑14的上部堵塞,因而可进一步提高后柱10的刚性。
[0099]
而且,本实施方式的车体后部结构中,角撑14的上部结合于柱内件10i的与车宽方向大致正交的面,因而可通过角撑14的上部利用柱内件10i将从后避震器输入的上下方向的输入负荷作为剪切负荷而接住。因此,在采用本结构的情况下,可提高后避震器的支撑刚性,提高车辆的操控稳定性。
[0100]
尤其本实施方式的车体后部结构中,角撑14的上部也结合于柱外件10o的与车宽方向大致正交地延伸的凸缘部10ob,因而可不仅利用柱内件10i而且也利用柱外件10o将从后避震器输入的上下方向的输入负荷作为剪切负荷而接住。因此,在采用本结构的情况下,可提高后避震器的支撑刚性,进一步提高车辆的操控稳定性。
[0101]
而且,本实施方式的车体后部结构中,角撑14包含经前后分割的后角撑板14r和前角撑板14f。此时,可将各角撑板分别结合于后柱10或避震器外壳13等,因而可容易且准确地进行角撑14的结合作业。
[0102]
进而,本实施方式的车体后部结构中,在其中一个角撑板(后角撑板14r)设有凸缘部14b(堵塞部),此凸缘部14b(堵塞部)将前侧内板10if与后侧内板10ir的侧面之间的由远离部15形成的间隙堵塞。因此,可进一步提高前侧内板10if与后侧内板10ir的结合部的强度。
[0103]
而且,本实施方式的车体后部结构中,柱外件10o的前方伸出部10of结合于车顶侧梁11,柱外件10o的内侧伸出部10og结合于后车顶拱门12。因此,可使从后避震器输入至避震器外壳13的负荷经由角撑14和后柱10分散于车顶侧的结构体进行支撑。因此,在采用本结构的情况下,可提高后避震器的支撑刚性,进一步提高车辆的操控稳定性。
[0104]
而且,本实施方式的车体后部结构中,以前侧内板10if和后侧内板10ir的隔板部16、隔板部17与角撑14的前后的棱线l1、l2的伸出方向匹配的方式进行配置。因此,可提高
角撑14与后柱10的结合体的强度及刚性。因此,在采用本结构的情况下,可利用强度及刚性高的角撑14与后柱10的结合体来稳定地支撑从后避震器输入至避震器外壳13的负荷。
[0105]
进而,本实施方式的车体后部结构中,以与角撑14的前后的棱线l1、l2的伸出方向匹配的方式,将前侧补强构件30和后侧补强构件31安装于避震器外壳13。因此,可利用强度及刚性高的避震器外壳13、角撑14及后柱10的结合体来稳定地支撑从后避震器输入至避震器外壳13的负荷。
[0106]
而且,本实施方式的车体后部结构中,柱外件10o包括从车宽方向外侧抵接并接合于避震器外壳13的接合凸缘13c的接合壁10oe,柱内件10i的下壁10ib设定得低于接合凸缘13c的上端部。而且,在避震器外壳13的接合凸缘13c的车宽方向内侧位置,配置有前后宽度较接合凸缘13c更宽的、柱内件10i的远离部15。因此,可使后柱10的截面低且小型,并且可在将后柱10组装于避震器外壳13时,使柱外件10o的接合壁10oe从车宽方向外侧大致水平地移动并触碰避震器外壳13的接合凸缘13c,将接合壁10oe与接合凸缘13c容易地焊接固定。
[0107]
即,本实施方式的车体后部结构中,在柱内件10i上的与接合凸缘13c对应的位置(接合凸缘13c的车宽方向内侧位置),配置有前后宽度较接合凸缘13c更宽的远离部15,因而可在后柱10的组装时,不导致柱内件10i与接合凸缘13c的干扰而将接合壁10oe与接合凸缘13c容易地焊接固定。
[0108]
此外,本发明不限定于所述实施方式,可在不偏离其主旨的范围内进行各种设计变更。
再多了解一些
本文用于企业家、创业者技术爱好者查询,结果仅供参考。