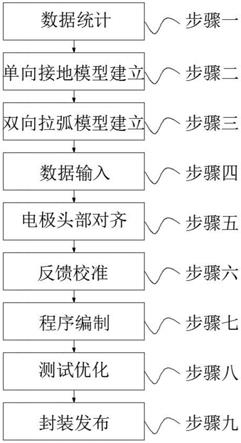
一种软件补偿的lf炉电极自动对齐方法
技术领域
1.本发明涉及lf炉技术领域,具体为一种软件补偿的lf炉电极自动对齐方法。
背景技术:
2.在lf炉外精炼的生产过程中,电极是重要的工艺设备,负责温度的控制,在电极加热升温的过程中,由于电极使用过程中消耗不同,造成长度存在一定差距,在每次升温结束后,三相电极头部位置平齐,但电极抬升过程中由于升降机构的限位位置固定,到达电极上限位时,三相电极头部长短不一;
3.在升温点弧的过程中,最长的电极先接触钢水,当第二长的电极也接触钢水,开始两相拉弧,待第三根电极接触钢水开始三相拉弧,点弧过程结束,由于电极头部位置长短不一,造成点弧时间过长,电极消耗增加,电能浪费,升温及造渣周期延长,在点弧之前自动调整对齐三相电极头部成为亟待解决的问题;
4.目前国内大部分冶金企业的lf工序普遍采用手动控制对齐,根据工人的目视参考进行人工操作,自动化程度低,控制精度低,责任心不强的岗位人员经常不进行对齐操作,造成电极过度消耗,点弧周期长,由于两相电极长时间拉弧对三相电网造成较大的冲击,对于中性点不接地的tt系统,偶尔会造成保护装置动作,无法升温,高压真空断路器触电老化严重等一系列问题,因此研制lf炉电极自动对齐方法对于提高点弧速度,提升自动化程度,降低电极消耗,减少lf炉对电网的冲击具有很重要的意义。
技术实现要素:
5.本发明的目的在于提供一种软件补偿的lf炉电极自动对齐方法,以解决上述背景技术中提出的问题。
6.为实现上述目的,本发明提供如下技术方案:一种软件补偿的lf炉电极自动对齐方法,包括以下步骤:步骤一,数据统计;步骤二,单相接地模型建立;步骤三,双相拉弧模型建立;步骤四,数据输入;步骤五,电极头部对齐;步骤六,反馈校准;步骤七,程序编制;步骤八,测试优化;步骤九,封装发布;
7.其中在上述步骤一中,首先对现场的工艺参数及设备参数进行统计,对副边电流、电压、比例阀输出历史操作数据进行数据分析,数据分析后备用;
8.其中在上述步骤二中,根据步骤一中统计分析的数据建立带有滤波器的中性点不直接接地电网的小电流接地识别模型,其识别函数为:
[0009][0010]
并且其中ua、ub和uc分别为三相副边电压;
[0011]
其中在上述步骤三中,根据步骤一中得出的副边电流的变化,建立双相拉弧识别模型,其特征函数为:
[0012][0013]
并且其中ia、ib和ic为三相副边电流,为三相平均电流;
[0014]
其中在上述步骤四中,当步骤二和步骤三中的模型建立完成后,采集副边电压电流比例阀的信号输入,随后根据步骤一中的模型识别单相接地,记录参考时间,根据步骤三中的模型识别双相拉弧,记录参考时间,继而识别三相拉弧,记录参考时间,随后根据单相电极接地,双相拉弧,三相拉弧的时间差计算出三相电极头部之间的位置关系,将位置关系输入到电极对齐补偿模型中;
[0015]
其中在上述步骤五中,当步骤四中的数据输入到电极对齐补偿模型中之后,开始升温时先将三相电极同步降至经验值升温准备区域,然后根据对齐补偿模型对电极头部最高和次高的电极进行分别下降补偿,来实现电极头部的平齐;
[0016]
其中在上述步骤六中,测量步骤五中使用补偿模型对齐之后的三个电极头是否对齐,如果对齐则进入下一步,如果没有对齐,则测量出误差数据,将误差数据手动标定反馈到电极对齐补偿模型中,对模型进行修正,直至三个电机头部完全对齐为止;
[0017]
其中在上述步骤七中,利用编程软件将上述算法在一级电极调节plc系统中编程实现,程序下载运行;
[0018]
其中在上述步骤八中,对步骤七中编制完成的程序进行测试,排除异常情况,随后对程序进行现场调试,分析误差原因,根据分析的原因进行程序优化;
[0019]
其中在上述步骤九中,当步骤八中的程序优化完成后,进行程序封装发布,从而得到软件补偿的lf炉电极自动对齐的程序。
[0020]
优选的,所述步骤二中,当得出的x超过3时,系统识别为单相接地。
[0021]
优选的,所述步骤三中,当得出的x超过0.5时,系统识别为双相拉弧。
[0022]
优选的,所述步骤三中,积分时间常数为1.4秒。
[0023]
优选的,所述步骤四中,由于比例调节阀存在温度漂移和零点漂移,为保证发明取得良好效果,需每月对三相电极进行同步校准。
[0024]
优选的,所述步骤六中,利用激光测距仪进行测量。
[0025]
与现有技术相比,本发明的有益效果是:
[0026]
1.本发明在不增加硬件投资的前提下,软件算法实现了lf钢包精炼炉的三相电极自动对齐,提升了自动化程度,无需人工干预,为智能炼钢提供了重要保证,减少了误操作情况的发生,大大降低了人工成本;
[0027]
2.本发明lf炉点弧对电网的非线性冲击大幅改善,三相副边电压平衡度提高,显著降低了电极消耗和电耗,起弧快速平稳,电极折断现象极少发生,减少热停时间,大幅缩短了点弧时间,进而缩短了冶炼周期,减少了过程温降,杜绝了两相拉弧电能的浪费,有效的延长了设备的使用寿命;
[0028]
3.本发明通过人工标定误差,随后将误差数据反馈到电极对齐补偿模型中,从而实现对电极对齐补偿模型的优化,大大降低了电极对齐补偿模型的误差,有利于提高对齐的精准度。
附图说明
[0029]
图1为本发明的方法流程图;
[0030]
图2为本发明的技术方案流程图;
[0031]
图3为本发明的系统原理框图;
[0032]
图4为实施例中原设计精炼炉点弧时间实时曲线图;
[0033]
图5为实施例中应用本发明后的点弧时间实时曲线图。
具体实施方式
[0034]
下面将结合本发明实施例中的附图,对本发明实施例中的技术方案进行清楚、完整地描述,显然,所描述的实施例仅仅是本发明一部分实施例,而不是全部的实施例。基于本发明中的实施例,本领域普通技术人员在没有做出创造性劳动前提下所获得的所有其他实施例,都属于本发明保护的范围。
[0035]
请参阅图1-5,本发明提供的一种实施例:一种软件补偿的lf炉电极自动对齐方法,包括以下步骤:步骤一,数据统计;步骤二,单相接地模型建立;步骤三,双相拉弧模型建立;步骤四,数据输入;步骤五,电极头部对齐;步骤六,反馈校准;步骤七,程序编制;步骤八,测试优化;步骤九,封装发布;
[0036]
其中在上述步骤一中,首先对现场的工艺参数及设备参数进行统计,对副边电流、电压、比例阀输出历史操作数据进行数据分析,数据分析后备用;
[0037]
其中在上述步骤二中,根据步骤一中统计分析的数据建立带有滤波器的中性点不直接接地电网的小电流接地识别模型,其识别函数为:
[0038][0039]
当得出的x超过3时,系统识别为单相接地,并且其中ua、ub和uc分别为三相副边电压;
[0040]
其中在上述步骤三中,根据步骤一中得出的副边电流的变化,建立双相拉弧识别模型,其特征函数为:
[0041][0042]
当得出的x超过0.5时,系统识别为双相拉弧,并且其中ia、ib和ic为三相副边电流,为三相平均电流,积分时间常数为1.4秒;
[0043]
其中在上述步骤四中,当步骤二和步骤三中的模型建立完成后,采集副边电压电流比例阀的信号输入,且由于比例调节阀存在温度漂移和零点漂移,为保证发明取得良好效果,需每月对三相电极进行同步校准,随后根据步骤一中的模型识别单相接地,记录参考时间,根据步骤三中的模型识别双相拉弧,记录参考时间,继而识别三相拉弧,记录参考时间,随后根据单相电极接地,双相拉弧,三相拉弧的时间差计算出三相电极头部之间的位置关系,将位置关系输入到电极对齐补偿模型中;
[0044]
其中在上述步骤五中,当步骤四中的数据输入到电极对齐补偿模型中之后,开始升温时先将三相电极同步降至经验值升温准备区域,然后根据对齐补偿模型对电极头部最
高和次高的电极进行分别下降补偿,来实现电极头部的平齐;
[0045]
其中在上述步骤六中,利用激光测距仪进行测量,测量步骤五中使用补偿模型对齐之后的三个电极头是否对齐,如果对齐则进入下一步,如果没有对齐,则测量出误差数据,将误差数据手动标定反馈到电极对齐补偿模型中,对模型进行修正,直至三个电机头部完全对齐为止;
[0046]
其中在上述步骤七中,利用编程软件将上述算法在一级电极调节plc系统中编程实现,程序下载运行;
[0047]
其中在上述步骤八中,对步骤七中编制完成的程序进行测试,排除异常情况,随后对程序进行现场调试,分析误差原因,根据分析的原因进行程序优化;
[0048]
其中在上述步骤九中,当步骤八中的程序优化完成后,进行程序封装发布,从而得到软件补偿的lf炉电极自动对齐的程序。
[0049]
本发明应用前后100炉次随机提取的对比过程数据如下表:
[0050]
方法应用前的过程数据:
[0051]
炉号牌号钢种点弧时间电流不平衡度两相拉弧时长2165140sphce44074029.40.223.22155011q235be33024018.60.212.32115015bg380cle33020039.50.213.22155065q355be330470211.70.194.52165168scga440e220850110.30.232.42165161hc340lae220900110.20.223.32115053spht2e331570110.30.214.32165188ss400e331520111.20.332.22155083q355de33066019.70.271.3215519245e33061019.50.223.3
[0052]
方法应用后的过程数据:
[0053]
[0054][0055]
数据表明,本专利应用以前,平均点弧时间为10.04秒,平均起弧电流不平衡度23.1%,平均两相拉弧时长为3秒,本专利应用以后,平均点弧时间为3.67秒,平均起弧电流不平衡度15.5%,平均两相拉弧时长为0.3秒,原设计精炼炉点弧时间实时曲线图见图4,由图可知专利应用前的点弧实时曲线,其点弧时间为10秒,应用本发明后的点弧时间实时曲线图见图5,由图可知,专利应用后的点弧实时曲线,其点弧时间为2.5秒,发明方法应用点弧过程时间明显缩短,现场观察电极晃动幅度小,三相电压电流平衡度好,对电网的非线性冲击小,使用效果较好。
[0056]
基于上述,本发明的优点在于,本发明在不增加硬件投资的前提下,软件算法实现了lf钢包精炼炉的三相电极自动对齐,提升了自动化程度,无需人工干预,为智能炼钢提供了重要保证,减少了误操作情况的发生,大大降低了人工成本,同时lf炉点弧对电网的非线性冲击大幅改善,三相副边电压平衡度提高,显著降低了电极消耗和电耗,起弧快速平稳,电极折断现象极少发生,减少热停时间,大幅缩短了点弧时间,进而缩短了冶炼周期,减少了过程温降,杜绝了两相拉弧电能的浪费,有效的延长了设备的使用寿命,通过人工标定误差,随后将误差数据反馈到电极对齐补偿模型中,从而实现对电极对齐补偿模型的优化,大大降低了电极对齐补偿模型的误差,有利于提高对齐的精准度。
[0057]
对于本领域技术人员而言,显然本发明不限于上述示范性实施例的细节,而且在不背离本发明的精神或基本特征的情况下,能够以其他的具体形式实现本发明。因此,无论从哪一点来看,均应将实施例看作是示范性的,而且是非限制性的,本发明的范围由所附权利要求而不是上述说明限定,因此旨在将落在权利要求的等同要件的含义和范围内的所有变化囊括在本发明内。不应将权利要求中的任何附图标记视为限制所涉及的权利要求。
再多了解一些
本文用于企业家、创业者技术爱好者查询,结果仅供参考。