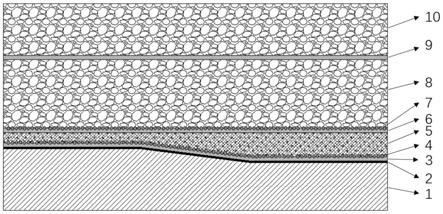
1.本发明涉及桥面工程技术领域,特别是涉及一种高耐久不等厚钢桥面铺装结构的施工方法。
背景技术:
2.随着我国快速的经济增长与科技进步,实现跨江跨海交通的需求日益增加,大跨径公路钢桥的建设迅猛发展,我国钢桥面铺装材料与技术也从直接引进国外成熟铺装结构与工艺的初始阶段过渡到以自主研发为主的创新阶段。
3.环氧沥青混凝土具有优异的路用性能,是大跨径钢桥面铺装的常用材料。由于钢桥面铺装的服役环境异于普通沥青道面,且公路钢桥承担着繁重的交通荷载作用,钢桥面铺装对铺装材料的要求尤为严苛。国内现有钢桥面铺装中主要采用日本taf的三组分环氧沥青与美国chemo的双组份环氧沥青,而国产环氧沥青混凝土刚自主研发成功,在施工方面尚少有成功的应用实例。
4.近年来,国内外设计的钢桥为了保证钢桥u肋传力,避免u肋上下错位衔接时出现局部应力集中现象,顶层钢板的板厚变化采用了内对齐的形式,使得钢桥面的顶层钢板具有了不等厚的特点,同时为了保证钢桥面铺装上表面的平整度,铺装厚度只能随钢板厚度的变化而作出相应的调整。相对于等厚钢桥面铺装,不等厚钢桥面板在厚度变化区域,存在大量锐角和棱边,防腐涂装比较困难,传统的防水黏层洒布工艺也难以确保不等厚铺装防水黏层的均匀性,会直接影响防水黏层的粘结力,导致铺装出现脱层等病害;其次,传统的混凝土摊铺及碾压工艺也难以满足不等厚铺装的施工质量要求,极易出现集料破碎、开裂等路面病害。不等厚钢桥面板属于新型钢桥结构,暂无针对性的钢桥面铺装结构,亟待不等厚钢桥面铺装结构的提出,以实现不等厚钢桥的推广与应用。此外,需根据不等厚铺装结构性能特点,提出具有针对性的施工方法。
技术实现要素:
5.基于此,本发明的目的在于,提供一种高耐久不等厚钢桥面铺装结构的施工方法,其可有效提高施工质量与施工效率,显著降低不等厚钢桥面国产环氧沥青混凝土铺装出现开裂、脱层等路面病害的可能性,同时,降低环境污染与材料损耗,施工损耗率由12%降低到3%,具有显著的社会经济效应。
6.具体技术方案为:
7.一种高耐久不等厚钢桥面铺装结构的施工方法,所述施工方法包括如下步骤:
8.步骤一,对不等厚钢桥面板(1)进行清洁及喷砂除锈作业:采用打磨机对钢桥面板(1)的厚度变化区域及无法用移动式自动无尘打砂机除锈的边角或凹坑部位进行人工打磨;
9.步骤二,防锈层(2)布设:在步骤一所述喷砂除锈作业结束后2~6h内进行防锈层(2)的布设,防锈层的布设中每道漆膜与前道漆膜需设有1/4~1/3的重叠;防锈层(2)厚度
为60~80μm;采用拉拔试验装置对防锈层的强度进行检测,当拉拔强度达到7.5mpa时,方可进行下一工序的作业;
10.步骤三,防水黏层(3)洒布:洒布粘结料为树脂类粘结料,用量为0.55~0.95kg/m2;洒布次数为1~3次;
11.步骤四,底碎石层(4)布设:将碎石预加热至120~135℃,再进行底碎石层(4)的布设;碎石用量范围为1.3~1.7kg/m2;
12.步骤五,整平层(5)铺设:使用环氧乳化沥青砂浆进行铺设,当所述运料车进入施工作业面后,控制运料车车厢的倾斜角度在35~65
°
,使环氧乳化沥青砂浆依靠自流平性质铺设,要求铺设厚度保持均匀;整平层(5)厚度根据钢板的不等厚情况进行调整,其最小厚度不小于5mm,最大厚度不超过30mm;
13.步骤六,下粘结层(6)洒布:洒布粘结料为树脂类粘结料,用量为0.65~0.85kg/m2;洒布次数为1~2次;
14.步骤七,下碎石层(7)布设:将碎石预加热至120~135℃,再进行下碎石层(7)的布设;碎石用量为1.1~1.6kg/m2;
15.步骤八,结构层(8)摊铺:采用沥青混凝土摊铺机双机联铺的摊铺组合方式进行摊铺作业,各摊铺机的纵向间距为5m~15m,摊铺速度为1.0m/min~1.5m/min;碾压过程分为初压、复压、终压三个阶段,初压采用胶轮压路机碾压3~5遍,复压采用钢轮压路机碾压4~6遍,终压采用胶轮压路机碾压2~4遍、钢轮压路机碾压3~5遍;初压作业最低温度为155℃,复压作业最低温度为110℃,终压作业最低温度为90℃;所述结构层(8)厚度为40mm;
16.步骤九,上粘结层(9)洒布:洒布粘结料为树脂类粘结料,用量为0.45~0.75kg/m2;洒布次数为1~3次;
17.步骤十,磨耗面层(10)摊铺:采用沥青混凝土摊铺机双机联铺的摊铺组合方式进行摊铺作业,各摊铺机的纵向间距为5m~15m,摊铺速度为1.0m/min~1.5m/min;碾压过程分为初压、复压、终压三个阶段,初压采用胶轮压路机碾压3~5遍,复压采用钢轮压路机碾压4~6遍,终压采用胶轮压路机碾压2~4遍、钢轮压路机碾压3~5遍;初压作业最低温度为165℃,复压作业最低温度为120℃,终压作业最低温度为100℃;所述磨耗面层(10)厚度为30~40mm。
18.本发明根据钢桥面桥面板不等厚的特点,考虑到铺装结构与钢桥面板的变形协调性、铺装结构层间粘结性及铺装结构整体的力学稳定性,提出三层桥面铺装结构施工方法,即在不等厚钢桥面板(1)与结构层(8)间先加设整平层(5),在整平层(5)上进行结构层(8)及磨耗面层(10)等的施工,则本发明施工方法获得的铺装结构从下至上依次为防锈层(2)、防水黏层(3)、底碎石层(4)、整平层(5)、下粘结层(6)、下碎石层(7)、结构层(8)、上粘结层(9)与磨耗面层(10)。所述防水黏层(3)、下粘结层(6)与上粘结层(9)材料使用树脂类粘结料,所述结构层(8)与磨耗面层(10)材料使用国产环氧沥青混凝土。通过本发明施工方法获得的铺装结构整体性好,层与层之间粘结性能良好,拥有良好的水稳定性、低温抗裂性与高温稳定性,铺装层与不等厚钢桥面板的变形协调性较好,耐久性强,面层集料不易脱落,减振降噪效果良好。
19.本发明施工方法提出“不等厚钢桥面板喷砂打磨 国产树脂类粘结料两次洒布 国产环氧沥青混凝土时温调度、科学碾压”的处理方案,极大地提高了国产树脂类粘结料洒布
的均匀性和经济性,降低了国产树脂类粘结料的粘结失效风险,减少铺装不等厚和混凝土温度不稳定带来的施工干扰;提高混凝土的施工质量,减少混凝土的废弃;提高了碾压质量,避免铺装厚度偏大区域碾压不密实、厚度偏小区域过压以至集料破碎现象的发生,在整体上实现了安全、高效施工。
20.本发明施工方法所采用的不等厚钢桥面板喷砂除锈、打磨、环氧富锌漆喷涂、国产树脂类粘结料洒布、国产环氧沥青混凝土生产、运输、调度、摊铺、碾压、维养等施工技术的工艺比较成熟,可操作性强,作业人员容易掌握,易于推广。
21.进一步地,所述步骤一中喷砂除锈作业带需重叠5-10cm,不等厚钢桥面板(1)锋利的边角必须处理成半径2mm以上的圆角。
22.进一步地,步骤一中所述打磨机为手提式打磨机。
23.进一步地,所述防锈层(2)采用树脂类富锌漆进行防腐涂刷,所述树脂类富锌漆包含双酚a型树脂、细铝粉及改性胺类曼尼希碱,且双酚a型树脂、细铝粉及改性胺类曼尼希碱的质量比为1:4:0.8~1.4。
24.进一步地,所述防水黏层(3)的树脂类粘结料采用双酚a型树脂作为主剂,采用改性胺类曼尼希碱作为固化剂,且双酚a型树脂与改性胺类曼尼希碱的质量比为1:0.7~1.3。
25.进一步地,所述下粘结层(6)的树脂类粘结料采用双酚a型树脂作为主剂,采用改性胺类曼尼希碱作为固化剂,且双酚a型树脂与改性胺类曼尼希碱的质量比为1:1.1~1.4。
26.进一步地,所述上粘结层(9)的树脂类粘结料采用双酚a型树脂作为主剂,采用改性胺类曼尼希碱作为固化剂,且双酚a型树脂与改性胺类曼尼希碱的质量比为1:1.2~1.5。
27.进一步地,所述防水黏层(3)、下粘结层(6)及上粘结层(9)均采用双组分一体化智能洒布车进行作业,总洒布量应满足防水黏层(3)、下粘结层(6)及上粘结层(9)的设计用量。
28.所述防水黏层(3)、下粘结层(6)及上粘结层(9)均采用树脂类粘结料材料涂刷,防水黏层(3)中树脂类粘结料由主剂双酚a型树脂与固化剂按1:0.7~1.3的比例调配而成,下粘结层(6)中树脂类粘结料由主剂双酚a型树脂与固化剂按1:1.1~1.4的比例调配而成,上粘结层(9)中树脂类粘结料由主剂双酚a型树脂与固化剂按1:1.2~1.5的比例调配而成;树脂类粘结料材料中固化剂为改性胺类曼尼希碱固化剂;对于防水黏层(3),根据研究结果确定0.55~0.95kg/m2的国产树脂类粘结料洒布量和两次洒布的施工工艺,可明显提高国产树脂类粘结料洒布的均匀性和经济性,降低国产树脂类粘结料的粘结失效风险,对于下粘结层(6),其国产树脂类粘结料撒布量为0.65~0.85kg/m2,上粘结层(9)的树脂粘结料撒布量为0.45~0.75kg/m2。
29.所述防水黏层(3)、下粘结层(6)与上粘结层(9)洒布时边角与凹坑部分应当采用人工涂刷,漏洒或少洒的地方应及时纠正;不宜逆风作业,洒布后的区域做好保护措施,避免污染;若洒布的国产树脂粘结料遭受雨淋,待雨停后,立即用吹风机吹干,树脂粘结料的表面,进行粘结强度检测,若不满足要求,需进行返工处理。
30.进一步地,所述防水黏层(3)、下粘结层(6)与上粘结层(9)中树脂类粘结料的制备方法为:将所述双酚a型树脂主剂升温到50~60℃,所述改性胺类曼尼希碱固化剂升温到40~50℃,然后按照所述防水黏层(3)、下粘结层(6)与上粘结层(9)树脂类粘结料中主剂与固化剂的质量比将主剂与固化剂混合,搅拌3~4min使其充分混合均匀,得防水黏层(3)、下粘
结层(6)与上粘结层(9)中所述树脂类粘结料。
31.进一步地,所述改性胺类曼尼希碱包含甲醛、壬基酚以及间笨二甲胺,且甲醛、壬基酚以及间笨二甲胺的质量比为1:1.2:1.3。
32.进一步地,所述改性胺类曼尼希碱的合成方法为:按比例称取甲醛、壬基酚以及间笨二甲胺进行反应,反应温度90℃,反应时间2h,脱水压力为0.0098mpa。
33.在树脂及粘结材料选择方面,常规胺类固化剂具有毒性大,固化配比苛刻、使用时间短、固化产物脆性大等缺陷,且施工后对周围环境存在明显的不利影响。本发明采用化学工程中的曼尼希反应对固化剂进行改性从而达到减轻毒性,增强力学机械性能的作用,以此固化剂形成的树脂类粘结料具有环保,粘结性强,密水性好,成膜速度快等特点,并在实际工程中得到了良好的验证,提高了工程经济性,符合环保理念,具有较好的社会经济效益。
34.进一步地,所述底碎石层(4)中碎石选自玄武岩或辉绿岩石料中的至少一种,石料粒径尺寸范围为2.36~4.75mm。
35.进一步地,所述下碎石层(7)中碎石选自玄武岩或辉绿岩石石料中的至少一种,石料粒径分布为1.18~4.75mm。
36.进一步地,所述底碎石层(4)、下碎石层(7)均采用碎石洒布车进行洒布作业。
37.进一步地,所述整平层(5)的环氧乳化沥青砂浆包含石灰岩矿粉、水、消泡剂、铝粉、石英砂、环氧树脂及乳化改性沥青,且石灰岩矿粉、水、消泡剂、铝粉、石英砂、环氧树脂及乳化改性沥青的质量比为390:530:12:0.06:75:440~500;所述乳化改性沥青包含乳化沥青与固化剂,且乳化沥青与固化剂的质量比为15:20~40。所述环氧乳化沥青砂浆中环氧树脂的掺量根据室内路用性能检测试验结果确定为5%,此时砂浆的抗压强度和粘结强度较大,且具有较好的低温抗裂性,且此环氧树脂含量下砂浆制备的成本较低,节省了工程成本,具有较好的经济性。
38.进一步地,所述环氧乳化沥青砂浆的制备方法为:先将石英砂、环氧树脂及乳化改性沥青混合搅拌3~4min,然后依次加入石灰岩矿粉、水、消泡剂、铝粉,搅拌2~3min至均匀,得所述环氧乳化沥青砂浆。
39.进一步地,所述消泡剂为磷酸三丁酯。
40.进一步地,所述石英砂粒径范围为0.32~4.75mm。
41.进一步地,所述结构层(8)的环氧沥青混凝土包含环氧沥青结合料与集料,且环氧沥青结合料与集料的质量比为6.4~7.0:100;所述环氧沥青结合料包含双酚a型环氧树脂主剂和含有固化剂的基质沥青,且双酚a型环氧树脂主剂与含有固化剂的基质沥青的质量比为10:20~30;所述含有固化剂的基质沥青中,固化剂与基质沥青的质量比为6.5:20~30;所述集料包含玄武岩集料以及矿粉填料。所述集料包含粗集料和细集料,所述粗、细集料采用玄武岩,其性质致密、耐磨,与环氧沥青结合料的粘结性好、集料形状均为立方体,不含针片状集料。
42.进一步地,所述磨耗面层(10)的环氧沥青混凝土包含环氧沥青结合料与集料,且环氧沥青结合料与集料的质量比为6.7~7.1:100;所述环氧沥青结合料包含双酚a型环氧树脂主剂与含有固化剂的基质沥青,且双酚a型环氧树脂主剂与含有固化剂的基质沥青的质量比为10:20~30;所述含有固化剂的基质沥青包含固化剂与基质沥青,且固化剂与基质
沥青的质量比为6.2:15~25;所述集料包含玄武岩集料以及矿粉填料。所述粗集料和细集料,所述粗、细集料采用玄武岩,其性质致密、耐磨,与环氧沥青结合料的粘结性好、集料形状均为立方体,不含针片状集料。
43.进一步地,所述固化剂选自甲基四氢苯酐、葵二酸中的至少一种。
44.进一步地,所述结构层(8)与磨耗面层(10)用环氧沥青混凝土的制备方法为:先将双酚a型环氧树脂主剂和固化剂在拌合楼存储罐中分别循环加热至85~95℃与50℃~60℃,基质沥青加热至145~155℃,集料及矿粉加热至185~195℃;将基质沥青与固化剂混合,搅拌30~40s,之后加入双酚a型环氧树脂,搅拌35~40s,制得环氧沥青结合料;然后将环氧沥青结合料加入至结构层(8)、磨耗面层(10)相对应的玄武岩集料中拌合30~40s;拌合完成后再加入石灰岩矿粉,拌合30~40s,配置得到结构层(8)、磨耗面层(10)所需的环氧沥青混凝土。
45.所述结构层(8)、磨耗面层(10)摊铺时铺装厚度偏大区域,初压时胶轮压路机多碾压1遍,且适当降低压路机行驶速度,厚度偏小区域,复压的钢轮压路机严禁启动振动模式;厚度变化区域,严禁压路机长时间停留;摊铺过程中如果突然遇雨,立即停止施工,并清除未压实成型的混凝土,未铺混凝土必须全部予以废弃。
46.本发明施工方法获得的高耐久不等厚钢桥面铺装结构能够较好地适应钢桥面受力情况复杂、交通荷载重、环境因素影响大等不利条件,充分考虑了由于钢板厚度不均可能引发铺装层受力不平衡的情况以及层间的粘结性,对不等厚钢桥面板和结构层之间做了加设整平层(5)的设计保证铺装面层厚度及受力均匀,在防水黏层(3)上布设底碎石层(4)、在下粘结层(6)上布设下碎石层(7),以增加层间粘结力,保证铺装层的粘结强度及整体协调性,可有效防止由于不等厚钢桥面板和铺装层间的变形不连续导致的脱空,脱层现象。对于防水黏层(3)、下粘结层(6)及上粘结层(9)中树脂类粘结料的使用,从力学强度和经济性方面对固化剂进行斟酌考虑,采用了一种新颖的改性胺类固化剂,提高了工程经济性,符合环保理念,具有较好的社会经济效益。
47.本发明施工方法充分考虑由于钢板厚度不均可能引发铺装层受力不平衡的情况以及层间的粘结性,在不等厚钢桥面板上采用环氧乳化沥青砂浆作为整平层(5),保证了铺装面层施工时下部结构的平整性,防水黏层(3)、下粘结层(6)及上粘结层(9)所用的树脂类粘结料采用改性胺类曼尼希碱固化剂,国产环氧沥青结合料的固化剂采用甲基四氢苯酐或葵二酸,所用的环氧沥青混凝土nea-10的集料公称最大粒径分别为9.5mm,结构层(8)用国产环氧沥青结合料与集料的质量比为6.4~7.0:100,磨耗面层(10)用国产环氧沥青结合料与集料的质量比为6.4~7.1:100,铺装面层的厚度为40mm(结构层)与30~40mm(磨耗面层);最终获得的铺装结构其抗压强度及抗拉强度均较大,渗水系数较好,耐久性优良,同时兼具抗滑、防水、低温抗裂性与高温稳定性等性能。
48.相比常用的钢桥面铺装结构,本发明施工方法获得的铺装结构防水黏层(3)、下粘结层(6)及上粘结层(9)采用改性胺类曼尼希碱固化剂,并从工程经济性的角度出发,考虑防水黏层(3)、下粘结层(6)及上粘结层(9)的性能区别使用不同量的固化剂,利用该材料制成的树脂类粘结料,其粘结强度大,其性能满足长期使用的要求,同时也兼具优异的抗滑与防水性能,克服了传统胺类固化剂中挥发性强,毒性较大、固化配比苛刻、使用时间短、固化产物脆性大等缺陷,提升了工程的社会经济效益,符合现代社会环保工程的理念。
附图说明
49.图1为本发明施工方法获得的不等厚钢桥面铺装结构的结构示意图。
50.图中:1-不等厚钢桥面板、2-防锈层、3-防水黏层、4-底碎石层,5-整平层、6-下粘结层、7-下碎石层、8-结构层、9-上粘结层、10-磨耗面层。
具体实施方式
51.本发明下列实施例中未注明具体条件的实验方法,通常按照常规条件,或按照制造厂商所建议的条件。实施例中所用到的各种常用化学试剂,均为市售产品。
52.除非另有定义,本发明所使用的所有的技术和科学术语与属于本发明的技术领域的技术人员通常理解的含义相同。本发明的说明书中所使用的术语只是为了描述具体的实施例的目的,不用于限制本发明。
53.本发明的术语“包括”和“具有”以及它们任何变形,意图在于覆盖不排他的包含。例如包含了一系列步骤的过程、方法、装置、产品或设备没有限定于已列出的步骤或模块,而是可选地还包括没有列出的步骤,或可选地还包括对于这些过程、方法、产品或设备固有的其它步骤。
54.本发明的术语“包括”和“具有”以及它们任何变形,意图在于覆盖不排他的包含。例如包含了一系列步骤的过程、方法、装置、产品或设备没有限定于已列出的步骤或模块,而是可选地还包括没有列出的步骤,或可选地还包括对于这些过程、方法、产品或设备固有的其它步骤。
55.在本发明中提及的“多个”是指两个或两个以上。“和/或”,描述关联对象的关联关系,表示可以存在三种关系,例如,a和/或b,可以表示:单独存在a,同时存在a和b,单独存在b这三种情况。字符“/”一般表示前后关联对象是一种“或”的关系。
56.以下结合具体实施例对本发明作进一步详细的说明。
57.实施例1
58.本实施例施工方法获得的不等厚钢桥面用铺装结构如图1所示。在不等厚钢桥面板1上设置防锈层2、防水黏层3、底碎石层4、整平层5、下粘结层6、下碎石层7、结构层8、上粘结层9与磨耗面层10;防锈层2和整平层5之间通过防水黏层3粘结,并且加铺底碎石层4保证粘结强度;整平层5和结构层8之间通过下粘结层6粘结,并且加铺下碎石层7保证粘结强度;结构层8通过上粘结层9和磨耗面层10粘结;对于钢桥面中不等厚区域,其不等厚钢桥面板厚度变化以1:8的坡度放坡过渡,钢板厚度沿纵桥向共设有16处不等厚过渡区,其厚度变化以跨中横截面对称,本实施例不等厚钢桥面板一侧的厚度如表1所示。
59.表1不等厚钢箱梁桥一侧的钢板厚度
[0060][0061]
所述防锈层2采用树脂类富锌漆进行喷涂作业,树脂类富锌漆成分主要由双酚a型树脂、细铝粉及改性胺类曼尼希碱按质量比1:4:1混合而成,树脂类富锌漆技术要求如表2所示。
[0062]
表2防锈层用树脂类富锌漆技术要求
[0063][0064]
所述防水黏层3、下粘结层6和上粘结层9均采用国产树脂类粘结料铺设,防水黏层3中,国产树脂类粘结料由双酚a型树脂和固化剂以1:1.1的比例混合调配而成,下粘结层6和上粘结层9中,国产树脂类粘结料由双酚a型树脂和固化剂以1:1.2的比例混合调配而成,固化剂均采用改性胺类曼尼希碱,防水黏层3的国产树脂类粘结料用量为0.8kg/m2,下粘结层6的国产树脂类粘结料用量为0.7kg/m2,上粘结层9的国产树脂类粘结料用量为0.5kg/m2;双酚a型树脂和国产树脂类粘结料的技术要求分别满足表3和表4。
[0065]
表3双酚a型树脂的技术要求
[0066]
检测指标技术要求试验方法含水率/%≤0.09astm d 1744比重(23℃)1.10~1.20astm d 1475粘度(23℃)/mpa
·
s140~180astm d 445闪点/℃≥230astm d 92酸值/mgkoh/g≤2gb/t 258颜色(gardner)≤4astm d 1544外观淡黄偏透明目视10
[0067]
表4国产树脂类粘结料的技术要求
[0068][0069]
整平层4所用的环氧乳化沥青材料由石灰岩矿粉、水、消泡剂、铝粉、石英砂、环氧树脂及乳化改性沥青混合而成,其质量比为390:530:12:0.06:75:460。钢板及整平层整体厚度为41mm(钢板最厚处为36mm,此时砂浆厚度为5mm,钢板最薄处为16mm,此时砂浆厚度为25mm)。
[0070]
所述结构层8与磨耗面层10均采用国产环氧沥青混凝土(nea-10)铺设,其主要由国产环氧沥青结合料、粗集料、细集料以及矿粉填料组成,其中国产环氧沥青结合料由环氧沥青主剂(采用双酚a型环氧树脂),固化剂(采用甲基四氢苯酐),和70#基质沥青组成,结构层8与磨耗面层10所用国产环氧沥青混凝土(nea-10)主剂与添加固化剂后的基质沥青质量比均为10:25,固化剂和基质沥青的质量比分别为6.5:25与6.5:20。粗、细集料采用玄武岩,其性质致密、耐磨,与国产环氧沥青结合料的粘结性好、集料形状均为立方体,不含针片状集料,国产环氧沥青混凝土(nea-10)公称粒径最大为9.5mm,矿质填料为石灰石矿粉,玄武岩集料与矿粉填料按100:3配置而成,铺装结构中结构层8的厚度为40mm,磨耗面层10的厚度为30mm。双酚a型环氧树脂、基质沥青、玄武岩粗集料、细集料和矿质填料的技术要求分别满足表5、表6、表7、表8,表9,国产环氧沥青结合料的技术要求满足表10,nea-10级配满足表11。
[0071]
表5双酚a型环氧树脂技术要求
[0072]
检测指标技术要求试验方法粘度(23℃)/mpa
·
s130~180astm d 445含水量/%≤0.05astm d 1744比重(23℃)1.10~1.20astm d 1475环氧当量/1g190~200astm d 1652闪点/℃≥220astm d 92外观淡黄偏透明目视
[0073]
表6 70#基质沥青技术要求
[0074][0075]
表7玄武岩粗集料技术要求
[0076][0077]
表8玄武岩细集料技术要求
[0078][0079]
表9矿粉技术要求
[0080][0081]
表10国产环氧沥青结合料(采用甲基四氢苯酐)技术要求
[0082][0083]
表11国产环氧沥青混凝土nea-10集料级配技术要求
[0084][0085]
所述结构层8与磨耗面层10的国产环氧沥青混凝土制备方法为:先将环氧树脂主剂和固化剂在拌合楼存储罐中分别循环加热至85~95℃与50℃~60℃,基质沥青加热至145~155℃,集料及矿粉加热至185~195℃;混合基质沥青与固化剂,搅拌35s,之后加入环氧树脂,搅拌40s,制得国产环氧沥青结合料,后将环氧沥青结合料加入至结构层8、磨耗面层10相对应的玄武岩集料中拌合35s;拌合完成后再加入石灰岩矿粉,拌合35s,配置得到结构层8、磨耗面层10所需国产环氧沥青混凝土,本方案国产环氧沥青混凝土nea-10的集料级配如表12所示。
[0086]
表12实施例1中国产环氧沥青混凝土nea-10集料级配
[0087][0088]
钢桥面铺装复合结构的路用性能技术要求见表13所示:
[0089]
表13钢桥面铺装复合结构路用性能技术要求
[0090][0091]
基于上述设计,本实施例一种高耐久不等厚钢桥面铺装结构的施工方法采用如下
步骤:
[0092]
步骤一,对不等厚钢桥面板1进行清洁及喷砂除锈作业,采用手提式打磨机对钢桥面板1的厚度变化区域及无法用移动式自动无尘打砂机除锈边角或凹坑部位进行人工打磨;喷砂除锈作业带需重叠10cm,不等厚钢桥面板1锋利的边角必须处理到半径2mm以上的圆角;
[0093]
步骤二,检验钢桥面板1表面处理是否合格,在4h内进行防锈层2的布设;采用拉拔试验装置对防锈层的强度进行检测,当拉拔强度达到7.5mpa及以上时,方可进行下一工序的作业;防锈层的布设中,涂层需分布均匀,不产生流挂、漏喷、干喷、龟裂等缺陷,每道漆膜与前道漆膜需设有1/3的重叠;
[0094]
步骤三,防水黏层3国产树脂类粘结料的洒布采用双组分一体化智能洒布车进行作业,洒布次数为2次,单次洒布量为0.4kg/m2;边角与凹坑部分应当采用人工涂刷,漏洒或少洒的地方应及时纠正;不宜逆风作业,洒布后的区域做好保护措施,避免污染;若洒布的国产树脂粘结料遭受雨淋,待雨停后,立即用吹风机吹干,树脂粘结料的表面,进行粘结强度检测,若不满足要求,需进行返工处理;
[0095]
步骤四,将碎石预加热至130℃,再进行底碎石层4的布设;采用碎石洒布车进行洒布作业;
[0096]
步骤五,根据实际情况合理安排整平层5环氧乳化沥青砂浆运料车的数量及路径,当运料车进入施工作业面后,控制运料车车厢的倾斜角度在50
°
,使环氧乳化沥青砂浆依靠自流平性质铺设,要求铺设厚度保持均匀;
[0097]
步骤六,下粘结层6所用国产树脂类粘结料采用双组分一体化智能洒布车进行洒布铺设,洒布次数为2次,单次洒布量为0.35kg/m2;边角与凹坑部分应当采用人工涂刷,漏洒或少洒的地方应及时纠正;不宜逆风作业,洒布后的区域做好保护措施,避免污染;若洒布的国产树脂粘结料遭受雨淋,待雨停后,立即用吹风机吹干,树脂粘结料的表面,进行粘结强度检测,若不满足要求,需进行返工处理;
[0098]
步骤七,将碎石预加热至130℃,再进行下碎石层7的布设;采用碎石洒布车进行洒布作业;
[0099]
步骤八,对结构层8进行施工作业时需根据国产环氧沥青混凝土(nea-10)的施工容留时间与机械设备供给情况安排施工组织,保证料车调度、摊铺设备摊铺与压路机碾压高效有序进行;采用沥青混凝土摊铺机双机联铺的摊铺组合方式进行摊铺作业,各摊铺机的纵向间距为10m,摊铺速度为1.2m/min;碾压过程分为初压、复压、终压三个阶段,初压采用胶轮压路机碾压4遍,复压采用钢轮压路机碾压5遍,终压采用胶轮压路机碾压3遍、钢轮压路机碾压4遍;初压作业最低温度为155℃,复压作业最低温度为110℃,终压作业最低温度为90℃;铺装厚度偏大区域,初压时胶轮压路机多碾压1遍,且适当降低压路机行驶速度,厚度偏小区域,复压的钢轮压路机严禁启动振动模式,厚度变化区域,严禁压路机长时间停留;摊铺过程中如果突然遇雨,立即停止施工,并清除未压实成型的混凝土,未铺混凝土必须全部予以废弃;
[0100]
步骤九,上粘结层9所用国产树脂类粘结料采用双组分一体化智能洒布车进行洒布铺设,洒布次数为2次,单次洒布量为0.25kg/m2;边角与凹坑部分应当采用人工涂刷,漏洒或少洒的地方应及时纠正;不宜逆风作业,洒布后的区域做好保护措施,避免污染;若洒
布的国产树脂粘结料遭受雨淋,待雨停后,立即用吹风机吹干,树脂粘结料的表面,进行粘结强度检测,若不满足要求,需进行返工处理;
[0101]
步骤十,对磨耗面层10进行施工作业时需根据国产环氧沥青混凝土(nea-10)的施工容留时间与机械设备供给情况安排施工组织,保证料车调度、摊铺设备摊铺与压路机碾压高效有序进行;采用沥青混凝土摊铺机双机联铺的摊铺组合方式进行摊铺作业,各摊铺机的纵向间距为10m,摊铺速度为1.2m/min;碾压过程分为初压、复压、终压三个阶段,初压采用胶轮压路机碾压4遍,复压采用钢轮压路机碾压5遍,终压采用胶轮压路机碾压3遍、钢轮压路机碾压3遍;初压作业最低温度为165℃,复压作业最低温度为120℃,终压作业最低温度为100℃;铺装厚度偏大区域,初压时胶轮压路机多碾压1遍,且适当降低压路机行驶速度,厚度偏小区域,复压的钢轮压路机严禁启动振动模式,厚度变化区域,严禁压路机长时间停留;摊铺过程中如果突然遇雨,立即停止施工,并清除未压实成型的混凝土,未铺混凝土必须全部予以废弃。
[0102]
实施例2
[0103]
本实施例不等厚钢桥面用铺装结构应用的场景中,除磨耗面层所用环氧沥青混凝土nea-10的集料级配、钢板厚度变化情况和铺装层厚度与实施例1存在区别外,其余各项包括所用材料、施工工艺等均与实施例1保持一致。
[0104]
表14不等厚钢箱梁桥一侧钢板厚度
[0105][0106][0107]
所述防锈层2采用树脂类富锌漆进行喷涂作业,树脂类富锌漆成分主要由双酚a型树脂、细铝粉及改性胺类曼尼希碱按质量比1:4:1.1混合而成,树脂类富锌漆技术要求如表15所示。
[0108]
表15防锈层用树脂类富锌漆技术要求
[0109][0110]
所述防水黏层3、下粘结层6和上粘结层9均采用国产树脂类粘结料铺设,防水黏层3、下粘结层6和上粘结层9中,国产树脂类粘结料均由双酚a型树脂和固化剂以1:1.2的比例混合调配而成,固化剂均采用改性胺类曼尼希碱,防水黏层3的国产树脂类粘结料用量为0.85kg/m2,下粘结层6的国产树脂类粘结料用量为0.65kg/m2,上粘结层9的国产树脂类粘结料用量为0.45kg/m2;双酚a型树脂和国产树脂类粘结料的技术要求分别满足表16和表17。
[0111]
表16双酚a型树脂技术要求
[0112]
检测指标技术要求试验方法含水率/%≤0.1astm d 1744比重(23℃)1.10~1.20astm d 1475粘度(23℃)/mpa
·
s150~180astm d 445闪点/℃≥230astm d 92酸值/mgkoh/g≤2gb/t 258颜色(gardner)≤4astm d 1544外观淡黄偏透明目视
[0113]
表17国产树脂类粘结料技术要求
[0114][0115]
整平层4所用的环氧乳化沥青材料由石灰岩矿粉、水、消泡剂、铝粉、石英砂、环氧树脂及乳化改性沥青混合而成,其质量比为390∶530∶12∶0.06∶75∶480。钢板及整平层整体厚度为55mm(钢板最厚处为42mm,此时砂浆厚度为13mm,钢板最薄处为25mm,此时砂浆厚度为30mm)。
[0116]
所述结构层8与磨耗面层10均采用国产环氧沥青混凝土(nea-10)铺设,其主要由国产环氧沥青结合料、粗集料、细集料以及矿粉填料组成,其中国产环氧沥青结合料由环氧
沥青主剂(采用双酚a型环氧树脂)、固化剂(采用葵二酸)、和70#基质沥青组成,结构层8与磨耗面层10所用国产环氧沥青混凝土(nea-10)主剂与添加固化剂后的基质沥青质量比均为10∶25,固化剂和基质沥青的质量比分别为6.5∶30与6.5∶25。粗、细集料采用玄武岩,其性质致密、耐磨,与国产环氧沥青结合料的粘结性好、集料形状均为立方体,不含针片状集料,国产环氧沥青混凝土(nea-10)公称粒径最大为9.5mm,矿质填料为石灰石矿粉,玄武岩集料与矿粉填料按100∶3配置而成,铺装结构中结构层8的厚度为40mm,磨耗面层10的厚度为35mm。双酚a型环氧树脂、基质沥青、玄武岩粗集料、细集料和矿质填料的技术要求分别满足表18、表19、表20、表21、表22,国产环氧沥青结合料的技术要求满足表23,nea-10级配满足表24。
[0117]
表18双酚a型环氧树脂技术要求
[0118]
检测指标技术要求试验方法粘度(23℃)/mpa
·
s140~180astm d 445含水量/%≤0.06astmd 1744比重(23℃)1.12~1.20astmd 1475环氧当量/1g190~200astmd 1652闪点/℃>220astm d 92外观淡黄偏透明目视
[0119]
表19 70#基质沥青技术要求
[0120][0121]
表20玄武岩粗集料技术要求
[0122][0123]
表21玄武岩细集料技术要求
[0124][0125]
表22矿粉技术要求
[0126][0127]
表23国产环氧沥青结合料(采用葵二酸)技术要求
[0128][0129]
表24国产环氧沥青混凝土nea-10集料级配技术要求
[0130]
筛孔尺寸(mm)13.29.54.752.361.180.60.30.150.075通过百分率(%)10095~10065~8550~7039~5528~4021~3214~237~14
[0131]
所述结构层8与磨耗面层10的国产环氧沥青混凝土的制备方法为:先将环氧沥青主剂和固化剂在拌合楼存储罐中分别循环加热至85~95℃与50℃~60℃,基质沥青加热至145~155℃,集料及矿粉加热至185~195℃;混合基质沥青与固化剂,搅拌30~40s,之后加入环氧树脂,搅拌35~40s,制得国产环氧沥青结合料,后将环氧沥青结合料加入至结构层8、磨耗面层10相对应的玄武岩集料中拌合30~40s;拌合完成后再加入石灰岩矿粉,拌合30~40s,配置得到结构层8、磨耗面层10所需国产环氧沥青混凝土,本方案国产环氧沥青混凝土nea-10的集料级配如表25所示。
[0132]
表25实施例2中国产环氧沥青混凝土nea-10集料级配
[0133][0134]
钢桥面铺装复合结构的路用性能技术要求见表26所示:
[0135]
表26钢桥面铺装复合结构路用性能技术要求
[0136][0137]
实施例1和实施例2的不等厚钢桥面铺装结构的性能检测结果如表27所示:
[0138]
表27不等厚钢桥面铺装结构的性能检测结果
[0139][0140]
注:对比例为一种钢桥面板等厚情况下常用的双层环氧沥青混凝土铺装结构,所用铺装材料为nea10(结构层) nea10(磨耗面层)。
[0141]
根据表27所示试验结果可知,本发明施工方法获得的不等厚钢桥面铺装结构各项力学性能指标均满足现行相关规范中的技术要求,且其各项性能较常规钢桥面铺装结构具有显著优势,说明所述铺装结构对钢桥面板不等厚的情况有良好的应用效果。本发明不等厚铺装结构的防水黏层、下粘结层及上粘结层采用改性胺类曼尼希碱作为固化剂,该固化剂明显提高了树脂类材料的粘结性能,将不等厚钢桥面板1、整平层5、结构层8与磨耗面层10粘结为牢固整体;不等厚钢桥面板1与整平层5间布设的底碎石层4、整平层5与结构层8间布设的下碎石层7可增大不等厚铺装结构的层间粘结力,进一步提高了不等厚铺装结构的粘结性能,可有效防止由于钢桥面板与铺装层产生不连续变形导致的脱层,脱空等病害,使得不等厚铺装结构成为牢固的复合粘结体系。
[0142]
综合实施例所示的性能指标可知,本发明施工方法获得的不等厚铺装结构的抗疲劳性能优异,且线收缩系数更小,即间距优良的耐久性能与协同变形能力;更大的摩擦系数与构造深度代表该不等厚铺装结构具有出色的抗滑与阻水性能;路用性能试验结果显示该不等厚铺装结构的高温抗变形及低温抗开裂性能也表现优异。
[0143]
以对比例作为对照,本发明不等厚铺装结构施工方法机械化程度高、操作难度低,且施工结束后所需的养护期短,可更快地投入服役运营;此外,该不等厚铺装结构的维养频次与维养成本也明显低于对比例,即与不等厚钢桥面板间具备优异的匹配性。所述施工方法采用“不等厚钢桥面板喷砂打磨 国产树脂类粘结料两次洒布 国产环氧沥青混凝土时温调度、科学碾压”的处理方案,减少铺装不等厚和混凝土温度不稳定带来的施工干扰,提高混凝土的施工质量及碾压质量,减少混凝土的废弃且避免铺装厚度偏大区域碾压不密实、厚度偏小区域过压以至集料破碎现象的发生,在整体上实现了安全、高效施工,以此方式施工成型的铺装结构,不仅施工过程简易,节省成本,且其铺装结构在长时间内也将处于合格的工作状态,不需要进行大规模的结构重建,维养成本较低,具有良好的社会经济效益。
[0144]
以上所述实施例仅表达了本发明的几种实施方式,其描述较为具体和详细,但并不能因此而理解为对发明专利范围的限制。应当指出的是,对于本领域的普通技术人员来说,在不脱离本发明构思的前提下,还可以做出若干变形和改进,这些都属于本发明的保护范围。
再多了解一些
本文用于企业家、创业者技术爱好者查询,结果仅供参考。