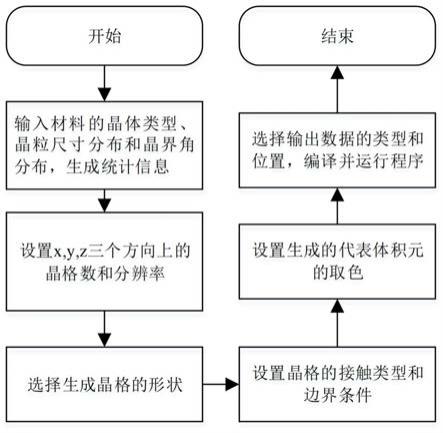
1.本发明涉及零件疲劳寿命的的研究,具体涉及一种样件在承受多轴载荷时其疲劳寿命 预测的方法。
背景技术:
2.材料或工件在变动的应力或应变重复作用下发生的破坏称为疲劳失效;据统计,机械 构件在工作中发生的疲劳失效,占全部力学失效的50%-90%,是机械结构和部件最常见的一 种失效形式。由于实际工况的复杂性和表面缺陷的存在,构件往往会受到多个方向载荷的影 响,即可将其归为多轴疲劳问题。但由于多轴疲劳的复杂性,在工程实际中往往将其简化为 单轴疲劳的形式来处理,这会导致预测的疲劳寿命与真实寿命之间相差过大,降低疲劳寿命 预测的参考价值。因此,寻找更准确更有效的多轴疲劳寿命预测方法仍然是当前工程中的主 要课题。目前也有一些学者提出了多轴疲劳寿命的预测方法:专利cn201810253959.4公开了 一种基于临界平面法的多轴疲劳寿命预测模型,即通过分析其危险截面得到等效应力和等效 应变继而预测其疲劳寿命;专利cn202110067336.x公开了一种基于单个缺陷的多轴疲劳寿 命预测方法,通过其同样缺陷下的单轴拉伸载荷和纯扭载荷下的应力-寿命数据,来预测多 轴疲劳寿命;专利cn201710078178.1公开了一种基于等温疲劳和蠕变疲劳的多轴热机械疲劳 寿命预测方法,通过循环载荷下的热机械疲劳损伤来预测样件的疲劳寿命。但是这些疲劳寿 命预测方法还存在以下不足:
①
未考虑样件晶体结构对疲劳寿命的影响,准确度不高;
②
预 测公式参数的确定需要大量的实验,成本较高;
③
未考虑非比例强化等异相加载带来的影响, 导致误差较大;
④
只能预测固定载荷形式下的疲劳,具有一定的局限性。这给多轴疲劳寿命 预测带来巨大挑战和不便。
技术实现要素:
3.本发明所要解决的技术问题是指提出一种预测样件多轴疲劳寿命的方法,本方法通过 对材料进行拉伸和疲劳实验,来拟合其晶体塑性参数,继而预测其在多轴载荷下疲劳寿命。
4.为解决以上技术问题,本发明采用如下的技术方案,本发明采用如下步骤:
①
以样件表层电子背散射衍射(ebsd)数据生成代表体积元;
②
建立材料晶体塑形有限元模型并进行疲劳试验;201建立该材料的晶体塑性本构方程:f=fef
p
ꢀꢀ
(1)式中f为变形梯度张量,f
p
为塑性变形梯度张量,fe为弹性变形梯度张量,l
p
为中间构型 塑性速度梯度,为剪切应变率,s
α
和m
α
分别为滑移系α的滑移方向和滑移面法向上的 单位矢量;
202确定剪切应变率为:式中为参考应变率,τ
α
为滑移系α上的解析剪应力,g
α
为滑移系α上的滑移系统阻力, m为速率灵敏度参数;203确定滑移系统阻力g
α
为:为:式中为滑移系α的初始阻力,为滑移系α的阻力率,q
sl
为潜硬化与自硬化之比,δ
αr
为 克罗内克函数符号,hr为材料的潜在硬化模量;204确定潜在硬化模量hr为:式中h0为初始硬化模量,τs为饱和应力,τ0为初始临界分解剪应力,n为硬化指数;205在常温下对待测试材料进行单轴拉伸试验以及两种不同加载下的疲劳实验,并使用引伸 计记录疲劳过程中的应力和应变,得到拉伸曲线、滞回曲线以及该载荷下的疲劳寿命;重复 步骤201-204模拟单轴拉伸试验以及两种不同加载下的疲劳实验,得到拉伸曲线,循环软化 曲线和滞回曲线;
③
输入样件所承受的多轴载荷,并预测样件的疲劳寿命;301执行步骤
②
中的方法,输入样件所承受的疲劳载荷,利用建立的晶体塑形有限元模型模 拟裂纹萌生初期的疲劳响应,并按式(7)和式(8)计算塑性应变能:拟裂纹萌生初期的疲劳响应,并按式(7)和式(8)计算塑性应变能:式中,σ(t)、ε(t)、τ(t)和γ(t)分别为t时刻模拟的代表体积元的轴向应力、轴向应变、剪切 应力和剪切应变;302利用式(9)和式(10)拟合得到的轴向塑性应变能和剪切塑性应变能曲线,并求得k1和k2的值;的值;式中k1为影响轴向塑性应变能增长速率的因子,k2为影响剪切塑性应变能增长速率的因子, c1和c2为轴向应变能和剪切应变能初值;303根据式(11)获得k
c2
的值:k
c2
=k
12
3k
12
ꢀꢀ
(11)
5.进一步地,步骤
①
包括:101在样件表面线切割部分材料,制样并拍摄ebsd图像,获取样件的晶粒类型,晶粒尺寸 分布和晶界角分布等晶体数据;102设置待生成的代表体积元的晶格数和分辨率并生成样件代表体积元模型。
6.进一步地,步骤
③
包括:将步骤
②
中实验所得的两种载荷下疲劳寿命以及其各自k
c2
的值带入式(10)中进行计算,求得 c和r:lg(nf)=ck
c2
r
ꢀꢀ
(12)式中nf为其多轴疲劳寿命,k
c2
为预测多轴疲劳寿命的因素,c和r为拟合线性函数的参数; 将需要预测的样件所承受的疲劳载荷仿真所求得k
c2
值带入式(10),预测其疲劳寿命nf。
7.与现有技术相比,本发明具有如下优点:本发明通过拍摄样件表层ebsd图像,获取 了材料的真实晶体数据,并用其生成的代表体积元来建立多轴疲劳寿命预测模型,大大提高 了模型的精度;本发明晶体塑性参数的确定仅需进行一次简单拉伸和两次不同载荷下的疲劳 实验,即可通过仿真拟合求得,既减少了进行纳米压痕和霍普金斯压杆等复杂的实验的花费, 又避免了尺寸效应,增加了参数的准确性;本发明可预测拉伸、扭转和剪切等多种复杂载荷 谱下的疲劳寿命,应用范围较广。
附图说明
图1为9310钢ebsd数据;图2为代表体积元建立流程;图3为9310钢代表体积元模型;图4为多轴疲劳实验载荷;图5为单轴拉伸应力应变曲线;图6为拉扭复合疲劳下的滞回曲线;图7为9310钢塑性应变能的实验结果及仿真预测曲线;
具体实施方式
8.下面结合附图和具体的实例对本发明进行详细说明,其主要步骤如下:
①
以样件表层电子背散射衍射(ebsd)数据生成代表体积元:101给定所需预测疲劳寿命的材料为齿轮钢9310,取其表层材料制样,并扫描获取其ebsd 数据,并计算其晶粒尺寸分布曲线和晶界角分布曲线,如图1所示。102按如图2所示的流程建立9310钢的代表体积元模型:输入晶体类型为体心立方,并输入 101所得的晶粒尺寸分布曲线和晶界角分布曲线,生成统计信息;输入x,y,z三个方向的晶格 数和分辨率分别为30、30、30、10、10和10;设置晶格形状为立方体;设置接触类型和边界 条件为立方接触;晶格取色选择黑白。103生成如图3所示的代表体积元以及对应的其晶体数据。
②
建立材料晶体塑形有限元模型并进行疲劳试验:201在有限元中,利用式(1)-(6)建立9310钢的晶体塑性本构方程:
f=fef
p
ꢀꢀ
(1)式中,f为变形梯度张量,f
p
为塑性变形梯度张量,fe为弹性变形梯度张量,l
p
为中 间构型塑性速度梯度,为剪切应变率,s
α
和m
α
分别为滑移系α的滑移方向和滑移面法 向上的单位矢量。进一步地,剪切应变率可由式(3)表示:式中,为参考应变率,τ
α
为滑移系α上的解析剪应力,g
α
为滑移系α上的滑移系统 阻力,m为应变率敏感性指数。进一步地,滑移系统阻力g
α
可由式(4)和式(5)求得:可由式(4)和式(5)求得:式中,为滑移系α的初始阻力,为滑移系α的阻力率,q
sl
为潜硬化与自硬化之比, δ
αr
为克罗内克函数符号,hr为材料的潜在硬化模量。进一步地,潜在硬化模量hr可由式(6)求得:式中,h0为初始硬化模量,τs为饱和应力,τ0为初始临界分解剪应力,n为硬化指数。202在常温下对9310钢样件进行拉伸试验以及两种不同相位角下的拉扭多轴疲劳实验,具体 参数如下:轴向为应力控制幅值为300mpa的载荷,径向为应变控制幅值为3
°
的载荷,应 力比r=-1,频率f=1hz,相位角分别为0
°
和45
°
,载荷曲线如图4所示。图4中横坐标 轴t(s)表示时间,单位为秒,左侧纵坐标axial stress为轴向应力,torsional shear angle为扭 转剪切角。进一步地,在实验过程中使用引伸计采集样件实验过程中的应力应变响应和滞回曲线, 如图5,图6所示,同时确定0
°
同相加载下样件的疲劳寿命n
f1
=13734cyc,45
°
异相加载 下样件的疲劳寿命n
f2
=8784cyc。203将步骤
①
生成的代表体积元导入有限元中,输入初始9310钢晶体塑性参数值,如表1所 示;然后用建立的程序模拟202中进行的拉伸试验以及不同相位角下的拉扭复合多轴疲劳实 验,得到其应力应变曲线;然后通过不断调整输入的材料晶体塑性参数值来拟合实验得到的 数据,最终确定9310钢晶体塑性有限元模型的参数,如表2所示。表1 9310钢初始晶体塑性参数
表2 9310钢拟合晶体塑性参数
③
输入样件所承受的多轴载荷,并预测样件的疲劳寿命: 301在有限元中输入步骤
②
中已进行疲劳实验的样件所承受的载荷以及需要预测的样件所承 受的疲劳载荷(如表3所示),利用建立的晶体塑形有限元模型模拟其裂纹萌生初期(即前 1000个循环载荷)下的的疲劳响应,并根据式(8)和式(9)计算其塑性应变能。表3仿真模拟的疲劳载荷表3仿真模拟的疲劳载荷表3仿真模拟的疲劳载荷式中,σ(t)、ε(t)、τ(t)和γ(t)分别为t时刻模拟的代表体积元的轴向应力、轴向应变、 剪切应力和剪切应变。302利用式(9)和式(10)去拟合仿真得到的轴向塑性应变能和剪切塑性应变能曲线,如图7所 示,并求得所拟合参数的值,如表4所示。示,并求得所拟合参数的值,如表4所示。
式中,k1为影响轴向塑性应变能增长速率的因子,k2为影响剪切塑性应变能增长速率的 因子,c1和c2为轴向应变能和剪切应变能初值。表4不同载荷拟合的参数进一步地,根据式(11)求得k
c2
的值:k
c2
=k
12
3k
12
ꢀꢀ
(11)进一步地,将步骤
②
中实验所得的两种载荷(即载荷1和载荷2)下疲劳寿命以及其各 自k
c2
的值带入式(10)中进行计算,求得c和r:lg(nf)=ck
c2
r
ꢀꢀ
(12)式中,nf为其多轴疲劳寿命,k
c2
为预测多轴疲劳寿命的因素,c和r为拟合线性函数 的参数。303进一步地,由302求得c=20.7702,r=3.6376,将需要预测的样件所承受的疲劳载荷仿 真所求得k
c2
值带入式(10),即可预测其疲劳寿命nf。
9.通过以上计算分析后,预测了90
°
异相加载和180
°
同相加载下9310钢样件的疲劳寿 命,通过与真实疲劳寿命对比,最大误差为8.17%,具体结果如表5所示:表5表5
10.以上所述实施方式仅为本发明的优选实施例,而并非本发明可行实施的穷举。对于本 领域一般技术人员而言,在不背离本发明原理和精神的前提下对其所作出的任何显而易见的 改动,都应当被认为包含在本发明的权利要求保护范围之内。
再多了解一些
本文用于企业家、创业者技术爱好者查询,结果仅供参考。