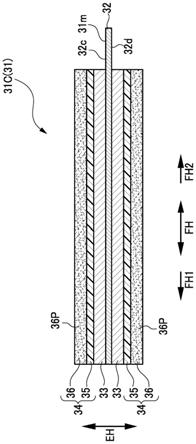
隔板一体电极板以及使用该隔板一体电极板的蓄电元件
1.本技术是2017年9月29日向中国国家专利局提出的申请号为201710906307.1、发明名称为“隔板一体电极板以及使用该隔板一体电极板的蓄电元件”这一申请的分案申请。
技术领域
2.本发明涉及在集电板上设置有活性物质层的电极板的活性物质层上一体地设置了隔板层的隔板一体电极板、以及使用了该隔板一体电极板的蓄电元件。
背景技术:
3.在一次电池、二次电池、电容器等蓄电元件中,在对置的电极板彼此之间形成夹持有离子能够透过的隔板(separator)的电极体。该情况下,还公知有在至少一方的电极板上一体地形成了隔板的隔板一体电极板。例如,专利文献1中公开了一种隔板是在正极板以及负极板的至少任意一方的被涂覆电极板的主面上涂覆形成的隔板层的电池、以及使将热塑性树脂的树脂粒子分散于溶剂而得到的绝缘糊剂(paste)涂覆于被涂覆电极板的主面并进行干燥来形成隔板层(树脂粒子层)的电池的制造方法。
4.专利文献1:日本特开2014-107035号公报
5.然而,当组装电池等蓄电元件时,要层叠很多电极板、或者反复卷绕一对电极板。此时,有在电极板彼此之间混入金属粉末等异物的情况。另外,也有这样的金属制的异物一旦熔解后,在负极析出并生长成树突状的情况。于是,有金属粉末或树突贯穿隔板层而使电极板间短路的情况。
6.然而,具有在电极板上涂覆上述的树脂粒子并进行干燥后的隔板层的隔板一体电极板中的隔板层与由多孔膜构成的隔板相比,针对由金属粉末或树突等异物造成的隔板层的贯穿的抵抗性往往较低。
技术实现要素:
7.本发明是鉴于这样的现状而完成的,提供虽然是将树脂粒子层设置在电极板上的隔板一体电极板但具有针对异物的贯穿的抵抗性良好的隔板层的隔板一体电极板、以及使用了该隔板一体电极板的蓄电元件。
8.本发明的一个方式是隔板一体电极板,具备:集电板;活性物质层,设置在上述集电板上;以及隔板层,设置于上述活性物质层上,且电解液中的离子能够透过该隔板层,其中,上述隔板层是聚酰亚胺层和聚烯烃粒子层层叠而成的隔板一体电极板,上述聚酰亚胺层设置在上述活性物质层上且由溶解于溶剂后析出的膜状的聚酰亚胺构成,上述聚烯烃粒子层设置在上述聚酰亚胺层上且熔点为140℃以下。
9.在上述的电极板中,由于除了聚烯烃粒子层以外,还具有机械强度优异而难以断裂的聚酰亚胺层,所以在与其他的电极板重叠的情况下,离子能够透过,并且能够抑制作为附着在聚烯烃粒子层上的异物的金属粉末或析出的金属生长成的树突等贯穿包括聚酰亚胺层的隔板层而电极板的活性物质层与配置在隔板层上的其他的电极板短路。
10.并且,聚烯烃树脂粒子的熔点是140℃以下。因此,在因电极间的短路等而电池异常发热、隔板层(聚烯烃粒子层)的温度成为140℃以上的高温的情况下,由于树脂粒子熔融而封堵电流的路径,所以能够切断流向电池的电流。
11.其中,作为聚烯烃树脂粒子,可举出由聚乙烯树脂(以下,也称为pe树脂)、聚丙烯树脂(以下,也称为pp树脂)、乙烯-丙烯共聚物树脂等构成的树脂粒子。作为该树脂粒子,例如可以使用单一种类的聚乙烯树脂粒子,但也能够混合使用熔点不同的聚乙烯树脂粒子,或者通过混合使用聚乙烯树脂粒子和聚丙烯树脂粒子而混合使用粒径、粒子形状不同的树脂粒子来进行混合并乳化聚合由此成为核-壳构造来进行使用等。
12.在上述的隔板一体电极板中,可以成为上述聚酰亚胺层具有10.0μm以下的厚度的隔板一体电极板。
13.如上所述,由于聚酰亚胺层由溶解于溶剂后析出的膜状的聚酰亚胺构成,所以聚酰亚胺层的离子透过性(或者作为其标准的耐透气性)容易比聚烯烃粒子层、独立的隔板所使用的聚乙烯单层的多孔膜或者(pe/pp/pe、pp/pe/pp等)3层构造的多孔膜、或者对它们涂覆了陶瓷粉末的耐热层而成的多孔膜中的离子透过性低(耐透气性的值容易变高)。
14.与此相对,在上述的电极板中,由于使聚酰亚胺层的厚度为10.0μm以下,所以整个隔板层能够确保与独立地作为隔板而使用的多孔膜所具有的离子透过性(作为典型例子而表示的关于由具有耐热层/pp/pe/pp的结构的多孔膜构成的隔板的、成为离子透过性的优劣的指标的耐透气性为260sec/100ml)相同程度或者更高的离子透过性(耐透气性)。
15.此外,形成在活性物质层上的聚酰亚胺层的厚度由三丰制测厚仪型号t212702来计测。
16.并且,在上述的隔板一体电极板中,可以是上述聚酰亚胺层具有6.0μm以下的厚度的隔板一体电极板。
17.在该电极板中,由于使聚酰亚胺层的厚度为6.0μm以下,所以整个隔板层能够进一步确保良好且适当的离子的透过。
18.在上述任一项所记载的隔板一体电极板中,可以是上述聚酰亚胺层具有0.5μm以上的厚度的隔板一体电极板。
19.如上所述,树脂粒子堆积而成的聚烯烃粒子层针对金属粉末或树突等的贯穿的抵抗性(作为其标准的后述的穿刺试验中的穿刺强度)容易比作为独立的隔板而使用的聚乙烯单层的多孔膜或者pe/pp/pe、pp/pe/pp等3层构造的多孔膜、或者在它们上涂覆了陶瓷粉末的耐热层的多孔膜中的针对贯穿的抵抗性低(穿刺强度也容易变低)。
20.与此相对,在上述的电极板中,由于将穿刺强度高的聚酰亚胺层的厚度确保为0.5μm以上的厚度,所以整个隔板层能够确保与独立地作为隔板而使用的多孔膜所具有的针对金属粉末等的贯穿的抵抗性(作为典型例子而表示的关于由具有耐热层/pp/pe/pp的结构的多孔膜构成的隔板的、穿刺试验中的穿刺强度为64mn(=6.5gf))相同程度或者更高的抵抗性(穿刺强度)。
21.此外,隔板一体电极板中的隔板层的穿刺试验的穿刺强度如以下那样进行评价。残留直径40mm的穿刺区域而从两面固定隔板一体电极板,将具有前端径300μm的半球状的前端部且由不锈钢材料构成的针按照以0.1mm/s的速度从隔板层侧刺入隔板一体电极板的穿刺区域的中心的方式使其前行,测量针与电极板导通的时刻下的负载,作为穿刺强度。
22.并且,在上述任一项所记载的隔板一体电极板中,可以是上述聚烯烃粒子层具有10~25μm的厚度的隔板一体电极板。
23.由于该电极板具备10μm以上的厚度的聚烯烃粒子层,所以在电池异常发热的情况下,聚烯烃粒子层的树脂粒子熔融而封堵空孔,能够可靠地切断在电池流动的电流。另一方面,因为使聚烯烃粒子层的厚度为25μm以下,所以能够减小隔板一体电极板的厚度和使用了该隔板一体电极板的电池的尺寸。
24.此外,形成在聚酰亚胺层上的聚烯烃粒子层的厚度也由上述的三丰制测厚仪型号t212702来计测。
25.并且,也可以成为具备电池壳体;收纳于上述电池壳体,且具有上述任一项所记载的隔板一体电极板的电极体;以及浸渍在上述电极体的电解液的蓄电元件。
26.在该电池中,电极体具有除了上述的聚烯烃粒子层以外还具有聚酰亚胺层的隔板一体电极板。因此,在电极体中,即使在该电极板和与其重叠的其他电极板之间混入有作为异物的金属粉末、由从其他的电极板析出的金属构成的树突延伸出来的情况下,离子也能够透过隔板层的聚酰亚胺层的,并且金属粉末、树突等难以贯穿。因此,能够成为有效地抑制了经由金属粉末、树突而该电极板的活性物质层与其他的电极板导通而短路的电池。
附图说明
27.图1是实施方式所涉及的锂离子二次电池的纵剖视图。
28.图2是表示实施方式所涉及的锂离子二次电池的电极体中的正极板和负极板的层叠状态的说明图。
29.图3是实施方式所涉及的隔板一体负极板的剖视图。
30.图4是对实施方式所涉及的隔板一体负极板的穿刺强度试验的试验方法进行说明的说明图。
31.图5是表示实施方式所涉及的负极板的制造以及电池的制造方法的流程图。
具体实施方式
32.(实施方式1)
33.以下,参照附图对本发明的实施方式进行说明。图1示出本实施方式所涉及的锂离子二次电池(以下,也简单地称为“电池”)1的纵剖视图。图2示出电池1中的电极体20中的正极板21以及负极板31的层叠状态。另外,图3示出本实施方式所涉及的负极板31(内侧负极板31c)的剖面构造。图4是测量该负极板31的隔板层34的穿刺强度的穿刺强度试验的试验方法的说明图。此外,以下将电池1的电池厚度方向bh、电池横向ch、电池纵向dh、层叠方向eh、层叠方向一侧eh1、层叠方向另一侧eh2、以及电极取出方向fh、第一取出侧fh1、第二取出侧fh2规定为图1、图2以及图3所示的方向来进行说明。
34.首先,电池1是被搭载于混合动力汽车、插电式混合动力汽车、电动汽车等车辆等的方型且封闭型的锂离子二次电池。电池1由电池壳体10、收纳于该内部的层叠型的电极体20、以及支承于电池壳体10的正极端子部件50和负极端子部件60等构成(参照图1)。另外,在电池壳体10内收纳有非水电解液(电解液)19,其一部分浸渍在电极体20内。
35.其中,电池壳体10是直六面体箱状且由金属(在本实施方式中为铝)构成。该电池
壳体10由仅上侧开口的有底方筒状的壳体主体部件11、和以封堵该壳体主体部件11的开口的形态焊接的矩形板状的壳体盖部件13构成。由铝构成的正极端子部件50以与壳体盖部件13绝缘的状态固定设置于壳体盖部件13。对该正极端子部件50而言,其一端在电池壳体10内与层叠型的电极体20中的正极板21的正极集电部21m连接并导通,另一方面,另一端贯穿壳体盖部件13而延伸到电池外部。另外,由铜构成的负极端子部件60以与壳体盖部件13绝缘的状态固定设置于壳体盖部件13。对该负极端子部件60而言,其一端在电池壳体10内与电极体20中的负极板31的负极集电部31m连接并导通,另一方面,另一端贯穿壳体盖部件13而延伸到电池外部。
36.电极体20(还参照图2)呈大致直六面体状,以正极板21以及负极板31的层叠方向eh与电池厚度方向bh一致、电极取出方向fh与电池横向ch一致的形态收纳于电池壳体10内。另外,将层叠方向eh中的图2中的上方作为一侧eh1,将下方作为另一侧eh2。并且,将电极取出方向fh中的图2中的左方作为第一取出侧fh1,将右方作为第二取出侧fh2。
37.该电极体20通过交替地在层叠方向eh层叠多个矩形状的正极板21以及多个矩形状的负极板31而成。各个正极板21均是通过在由矩形状的铝箔构成的正极集电箔22的两面(一侧面22c以及另一侧面22d)中的靠电极取出方向fh中的第二取出侧fh2的一部分(图2中为右侧)呈矩形地设置正极活性物质层23、23而成。并且,在正极活性物质层23、23上设置有耐热材料层24、24。其中,各正极板21的正极集电箔22中的靠第一取出侧fh1(图2中为左侧)的部位均不存在正极活性物质层23以及耐热材料层24,成为正极集电箔22露出的正极集电部21m。各个正极板21的正极集电部21m在层叠方向eh被束缚,焊接于上述的正极端子部件50。
38.正极板21所使用的正极集电箔22是厚度6~20μm(在本实施方式中具体为15μm)的压延铝箔。正极活性物质层23例如具有10~90μm(在本实施方式中具体为68μm)的厚度。作为锂离子二次电池用的正极活性物质,可例示能够吸留、释放li
离子的材料,例如licoo2、limno4、lini
x
mnycozo2、lini
x
coyalzo2、lifepo4等。在本实施方式中,正极活性物质层23除了lini
1/3
mn
1/3
co
1/3
o2以外,还包括作为导电材料的乙炔黑、以及粘合剂pvdf。另外,耐热材料层24例如具有2~8μm(在本实施方式中具体为5μm)的厚度。作为耐热材料层24所使用的耐热材料,可例示具有耐热性、耐电解液性的粒子,例如氧化铝粒子、勃姆石粒子、二氧化钛粒子、二氧化硅粒子。在本实施方式中,将中值粒径(d50%)1μm的氧化铝粒子与粘合剂cmc(羧甲基纤维素)一起涂覆并干燥而成。
39.接下来,对作为本实施方式所涉及的隔板一体电极板的负极板31进行说明。负极板31在电极体20中交替层叠的正极板21以及负极板31中被划分为位于层叠方向eh的一侧eh1的最外侧(图2中为最上端)的一侧负极板31a、位于层叠方向eh的另一侧eh2的最外侧(图2中为最下端)的另一侧负极板31b、以及位于它们中间的内侧负极板31c。
40.其中,图3所示的内侧负极板31c通过矩形状的负极集电箔32、和在该负极集电箔32中的靠第一取出侧fh1(图3以及图2中为左侧)的两面上呈矩形状地设置负极活性物质层33、33而成。另外,在负极活性物质层33、33上(层叠方向一侧eh1以及层叠方向另一侧eh2),隔板层34、34与负极活性物质层33、33一体地设置。另一方面,负极板31中的一侧负极板31a仅在负极集电箔32的另一侧面32d设置有负极活性物质层33以及隔板层34,另一侧负极板31b仅在负极集电箔32的一侧面32c设置有负极活性物质层33以及隔板层34。此外,各负极
板31的负极集电箔32中的靠第二取出侧fh2(图3中为右侧)的部位均不存在负极活性物质层33以及隔板层34,成为负极集电箔32露出的负极集电部31m。各个负极板31的负极集电部31m在层叠方向eh被束缚,焊接于上述的负极端子部件60。
41.负极板31所使用的负极集电箔32是厚度6~15μm(在本实施方式中具体为10μm)的铜箔。负极活性物质层33具有例如10~80μm(在本实施方式中具体为62μm)的厚度。作为锂离子二次电池用的负极活性物质,可例示能够吸留、释放li
离子的材料,例如天然石墨、人造石墨等石墨粒子、硬碳、软碳、li4ti5o
12
、li
4.4
si、li
4.4
ge等。在本实施方式中,负极活性物质层33除了天然石墨以外还具有导电材料的乙炔黑、粘合剂cmc。另外,隔板层34均由负极活性物质层33侧的聚酰亚胺层35和在其上形成的粒子层36构成。其中,聚酰亚胺层35例如具有0.2~15μm(在本实施方式中具体为5.0μm)的厚度,如后述那样,是由将暂且溶解于溶剂的聚酰亚胺树脂涂覆于负极活性物质层33并进行干燥而使其析出的聚酰亚胺树脂构成的膜状的层。另外,粒子层36例如具有10~25μm(在本实施方式中具体为15.0μm)的厚度,堆积由聚烯烃构成的树脂粒子36p,具体而言堆积由熔点132℃的聚乙烯构成的pe粒子36p而成。pe粒子是中值粒径(d50%)3μm的球状的粒子。
42.该隔板层34(聚酰亚胺层35以及粒子层36)作为在使用负极板31构成了li离子二次电池等蓄电元件的情况下,电解液中的li
离子等离子能够透过的隔板发挥作用。当对于本实施方式的隔板层34测量离子透过性的指标即耐透气性时,为45sec/100ml。
43.此外,对于设置在负极板31的隔板层34(聚酰亚胺层35以及粒子层36),无法直接测量其耐透气性。鉴于此,另外对铝网涂覆将后述的聚酰亚胺树脂溶解于溶剂而得到的聚酰亚胺糊剂并进行干燥,进而凹版涂覆分散有pe粒子的微粒子水分散体并进行干燥,来形成测量用隔板层。对于该测量用隔板层,使用依据jis p 8117:2009规定的gurley试验机(东洋精机制gurley式密度计)来测量耐透气性。
44.另外,当测量了负极板31的隔板层34的穿刺强度时,是114mn(=11.6gf)。隔板层34的穿刺强度的测量方法基于以下的方法(参照图4)。即,将负极板31以负极板31被平坦地拉伸的状态夹持在穿孔有直径d=40mm的贯通孔hd1h、hd2h的保持件hd1、hd2之间。另一方面,在图4中,在能够向下方移动的移动头mh经由测压元件(load cell)lc安装有挤压针nd。该挤压针nd的前端部nds为半径r=150μm的半球状。使该挤压针nd的前端部nds从与负极板31正交的方向(图4中为上方)朝向贯通孔hd1h、hd2h的中心以移动速度sp=0.1mm/分钟的速度移动。使用测压元件lc测量挤压针nd的前端部nds突破隔板层34而与负极板31的负极活性物质层33接触时的负载。挤压针nd的前端部nds与负极板31的负极活性物质层33的接触的判定如图4所示,在负极板31的负极集电箔32与挤压针nd之间设置电源ps以及电流计cm,将电流流过电流计cm的时机作为挤压针nd的前端部nds与负极板31的负极活性物质层33的接触的时机。
45.对于本实施方式的负极板31的隔板层34而言,为了用实际的电池系统评价其离子透过性以及绝缘特性,准备了仅在负极集电箔32的一侧设置了负极活性物质层33以及隔板层34的一侧负极板31a;和与上述的正极板21不同,仅在正极集电箔22的另一侧设置了正极活性物质层23以及耐热材料层24的另一侧正极板(未图示)。然后,使一对负极活性物质层33和正极活性物质层23经由隔板层34对置,并用层压材料包围,使电解液浸渍,从而形成了层压电池(laminate cell)。
46.对于该层压电池进行了充放电试验。即,在对层压电池进行了初始充电后,soc为50%,将1c放电、2c放电、5c放电分别进行10秒,根据放电时的电池电压的降低量δv1和放电电流(ma)测量了该层压电池的iv电阻值(mω)。该层压电池的iv电阻值为6.8mω。
47.另外,对于上述的层压电池,在初始充电中成为满充电后,(不施加负载等)放置7天,根据放置前后测量出的电池电压,测量由于该层压电池的自放电所造成的电压降低量δv2(mv)。该层压电池的电压降低量是δv2=6.3mv。
48.(实施例以及比较例)
49.接下来,对于实施方式所涉及的负极板31不变更隔板层34的总厚度(20μm),而使聚酰亚胺层35以及粒子层36的厚度不同的实施例1~8所涉及的负极板31、或者使用了该负极板31的层压电池,通过上述的方法来测量耐透气性、穿刺强度、iv电阻值、由自放电所造成的电压降低量。具体而言,在实施例1~8中,使隔板层34的厚度恒定为20μm,使聚酰亚胺层35的厚度为0.2μm、0.5μm、1.5μm、3.0μm、5.0μm、6.0μm、8.0μm、13.0μm。其中,上述的实施方式所涉及的负极板31与实施例5的负极板相当。
50.除此以外,作为比较例1,对于不形成聚酰亚胺层35而使整个隔板层34为粒子层36的隔板也进行了相同的评价。并且,作为比较例2,对于不是在负极活性物质层33一体地形成隔板层34而独立的隔板也同样进行了评价。其中,作为比较例2的独立的隔板,使用了在pp/pe/pp的3层构造的多孔膜的一方设置了耐热层的4层构造的隔板(宇部兴产制造)。该比较例2的隔板被作为锂离子二次电池用的隔板而使用,该隔板以及使用了该隔板的电池的特性可以作为对各实施例的负极板31中的隔板层34的特性优劣进行判断的一个基准而使用。表1示出关于各实施例以及比较例的结果。其中,各例的样本数均是三个。
51.表1
[0052][0053]
关于各实施例以及比较例,首先对负极板31的隔板层34的耐透气性进行研究。比较例2的隔板的耐透气性是260sec/100ml。与此相对,在隔板层34不设置聚酰亚胺层35而整体是粒子层36的比较例1的负极板的隔板层中,耐透气性为11sec/100ml,这表明透气性极好。可认为在堆积pe粒子而成的粒子层36中,由于在pe粒子彼此之间较多地形成有空间,所以透气性良好。另一方面,可知在实施例1~8的负极板31中,聚酰亚胺层35越厚(粒子层36
越薄),则耐透气性越上升、即隔板层34的透气性越降低。这是因为与堆积pe粒子而成的粒子层36相比,将暂且溶解于溶剂的聚酰亚胺树脂涂覆到负极活性物质层33并进行干燥而使其析出的聚酰亚胺层35在透气性上较差。特别是在使聚酰亚胺层35的厚度为13.0μm的实施例8中,耐透气性为265sec/100ml,与比较例2的隔板相比变低。但是,由于在该实施例8的隔板层34中,也能够得到与比较例2的隔板几乎相同程度的耐透气性,所以聚酰亚胺层35至少在厚度13μm以下的范围中,甚至更厚的范围中,也示出与其厚度对应的电解液中的离子能够透过的特性,能够作为隔板层34的一部分而使用。其中,若聚酰亚胺层的厚度超过6μm则耐透气性急剧地上升。可认为若聚酰亚胺层的厚度超过6μm,则由于聚酰亚胺树脂几乎覆盖负极活性物质层的整个表面,所以耐透气性变大。
[0054]
接下来,关于各实施例以及比较例,对负极板31的隔板层34的穿刺强度进行研究。比较例2的隔板的穿刺强度是64mn(=6.5gf)。其中,关于比较例2的隔板,是仅将该隔板夹持在上述的保持件hd1、hd2之间而测量出的值(参照图4)。与此相对,在隔板层34仅由粒子层36构成的比较例1中,穿刺强度是33mn,低于比较例2。可认为这是因为堆积pe粒子而成的粒子层36的各pe粒子容易活动,针对挤压针nd的穿刺的抵抗性低。另一方面,在实施例1~8的负极板31中,可知聚酰亚胺层35越厚,则穿刺强度越上升。另外,在使聚酰亚胺层35的厚度为0.5μm的实施例2中穿刺强度为64mn,与比较例2相同。在使聚酰亚胺层35的厚度比实施例2厚的实施例3~8中,得到更加良好的穿刺强度。可认为构成聚酰亚胺层35的聚酰亚胺树脂具有刚性强的分子结构,并且具有亚胺键强的分子间力,所以聚酰亚胺层35针对挤压针nd的前端部nds的穿刺而难以膜破裂,具有高的穿刺强度。
[0055]
接下来,关于各实施例以及比较例,对使用了各负极板以及上述的正极板的层压电池中的iv电阻值进行研究。使用了比较例2的隔板的层压电池的iv电阻值是7.2mω。与此相对,在比较例1的层压电池中,iv电阻值是2.5mω,可知与比较例2相比约为1/3。根据比较例1的耐透气性是低的值也可知,堆积pe粒子而成的粒子层36因为在pe粒子彼此之间较多地形成有空间而透气性良好,电解液中的离子(在各例中为li离子)容易透过粒子层36,iv电阻值变低。与此相对,在使用了实施例1~8的负极板31的层压电池中,可知聚酰亚胺层35越厚,iv电阻值越上升。特别是在使聚酰亚胺层35的厚度为6.0μm的实施例6的层压电池中,iv电阻值为7.2mω,与使用了比较例2的隔板的情况相同。另外,在实施例7、8的层压电池中,与使用了比较例2的隔板的情况相比,iv电阻值变高。可认为由于隔板层34中的聚酰亚胺层35的厚度过厚,所以隔板层34中的电解液中的li离子的透过性降低,iv电阻值上升。
[0056]
接下来,关于各实施例以及比较例,对关于使用了各负极板以及上述的正极板的层压电池的由于自放电所造成的电压降低量进行研究。使用了比较例2的隔板的层压电池的电压降低量是13.4mv。与此相对,在隔板层34仅由粒子层36构成的比较例1的层压电池中,产生异物短路而不能测量。根据该比较例1的负极板的穿刺强度低也可知,混入的金属粉末或生长成的树突容易贯穿隔板层34,在初始充电后的放置期间中,在正极板21与负极板31的负极活性物质层33之间产生短路。另一方面,在隔板层34设置了聚酰亚胺层35的实施例1~8的层压电池中,不产生如比较例1那样的短路。可认为由于存在聚酰亚胺层35,而防止了混入的金属粉末等突破隔板层34(聚酰亚胺层35)而在正极板21与负极板31的负极活性物质层33之间短路。另外,在实施例1~8中的聚酰亚胺层35的厚度是0.2~5.0μm的实施例1~5的层压电池中,可知聚酰亚胺层35越厚,电压降低量越减少。可认为这是因为聚酰
亚胺层35越厚,则越能够防止正负极间的微小短路。但是,在实施例5~8(聚酰亚胺层35的厚度为5.0~13.0μm)中,电压降低量不管聚酰亚胺层35的厚度如何都几乎为相同程度。可认为这是因为若聚酰亚胺层35的厚度为5.0μm(实施例5)以上,则聚酰亚胺层的厚度增加而导致的电压降低量的减少作用几乎为上限。
[0057]
根据这些结果可知,在隔板层34设置了聚酰亚胺层35的实施例1~8的任意一个负极板31中,电解液中的li离子能够透过隔板层34(聚酰亚胺层35),可发挥作为隔板的作用。因此,可知实施例1~8的负极板31均能够作为隔板一体负极板而使用。
[0058]
另外,通过设置聚酰亚胺层35,能够抑制附着在粒子层36上的金属粉末或析出的金属生长而成的树突等贯穿隔板层34而使得该负极活性物质层33和配置在隔板层34上的正极板21短路的情况。
[0059]
并且,本实施方式以及各实施例的负极板31的粒子层36所使用的树脂粒子36p的熔点是140℃以下的132℃。因此,由于在因电池1的正负极间的短路等而电池1异常发热、隔板层34(粒子层36)的温度变为140℃以上的高温的情况下,树脂粒子36p熔融而堵塞电流的路径,所以能够切断(shutdown)流向电池1的电流。
[0060]
并且,在实施例8的负极板31(聚酰亚胺层35的厚度13.0μm)中,与比较例2的隔板相比耐透气性较差,但在实施例7的负极板31(聚酰亚胺层35的厚度8.0μm)中,与比较例2的隔板相比为良好的耐透气性,从该情况可知,若使负极板31的聚酰亚胺层35的厚度为10.0μm以下的厚度,则能够得到与比较例2的隔板相比具有良好的耐透气性的负极板31。
[0061]
并且,实施例7、8的负极板31(聚酰亚胺层35的厚度为8.0μm、13.0μm)与其他的实施例相比,耐透气性高(透气度低),iv电阻值也不如比较例2的7.2mω。与此相对,在实施例1~6的负极板31(聚酰亚胺层35的厚度0.2μm~6.0μm)中,耐透气性、iv电阻值都与比较例2相同或者比它更好。从该情况可知,若使负极板31的聚酰亚胺层35的厚度为6.0μm以下的厚度,则能够得到iv电阻值与比较例2的隔板相同以下的良好的负极板31以及电池。
[0062]
并且,在比较例1以及实施例1的负极板31(聚酰亚胺层35的厚度0μm、0.2μm)中,穿刺强度低(33mn、50mn),不如比较例2的隔板的穿刺强度(64mn)。与此相对,在实施例2~8的负极板31(聚酰亚胺层35的厚度0.5μm~13.0μm)中,穿刺强度与比较例2相同或者更好。从该情况可知,若使负极板31的聚酰亚胺层35的厚度为0.5μm以上的厚度,则能够得到具有与比较例2的隔板相同以上的良好的穿刺强度的负极板31。
[0063]
并且,在各实施例1~7的负极板31中,具备厚度19.8~12.0μm的粒子层36。若粒子层36的厚度比10μm薄,则在电池1异常发热的情况下,存在当由粒子层36的聚烯烃(聚乙烯)构成的树脂粒子36p熔融而堵塞空孔时,可靠性较差的情况。另一方面,即使粒子层36的厚度比25μm厚,隔板层的切断功能也不会提高,反而电池的尺寸增大厚度变厚的量、成本增加等不良情况变多。与此相对,通过使粒子层36的厚度为10~25μm,由此在电池1异常发热的情况下粒子层36的树脂粒子36p熔融而堵塞空孔,能够可靠地切断在电池流动的电流。另一方面,也能够防止负极板以及电池的尺寸或成本的增加。
[0064]
接下来,对负极板31以及电池1的制造方法进行说明(参照图5)。首先,在“正极板形成工序s1”中,制造多个正极板21。即,将上述的正极活性物质、导电材料以及粘合剂与溶剂(nmp)一起混匀而制成正极糊剂。然后,通过模涂法将该正极糊剂涂覆到正极集电箔22的一侧面22c,并加热使其干燥,来形成正极活性物质层23。另外,在正极集电箔22的另一侧面
22d也同样地涂覆正极糊剂,并加热使其干燥,来形成正极活性物质层23。进而,之后在各正极活性物质层23上涂覆使氧化铝粒子和粘合剂分散于溶剂而得到的耐热材料糊剂并进行干燥来形成耐热材料层24。然后,通过加压辊压缩该正极板21,来提高正极活性物质层23的密度。由此,形成正极板21。
[0065]
并且,另外在“负极板形成工序s2”中制造多个负极板31。即,在“负极活性物质层形成工序s21”中,首先将上述的负极活性物质、导电材料、以及粘合剂与作为溶剂的水一起混匀而制成负极糊剂。然后,关于内侧负极板31c,反复进行朝向负极集电箔32的利用模涂法进行的负极糊剂的涂覆干燥而在负极集电箔32两面形成负极活性物质层33。关于一侧负极板31a,将上述的负极糊剂仅涂覆在负极集电箔32的另一侧面32d并使其干燥来形成负极活性物质层33。另外,关于另一侧负极板31b,将负极糊剂涂覆在负极集电箔32的一侧面32c并使其干燥来形成负极活性物质层33。关于各负极板31,通过加压辊进行压缩来提高负极活性物质层33的密度。
[0066]
接下来,在“聚酰亚胺层形成工序s22”中,在各个负极活性物质层33上形成聚酰亚胺层35。具体而言,将聚酰亚胺树脂溶解于溶剂而制成聚酰亚胺糊剂,涂覆在负极活性物质层33上并干燥使聚酰亚胺树脂析出,从而在负极活性物质层33上制成由聚酰亚胺树脂构成的膜状的聚酰亚胺层35。
[0067]
并且,在“粒子层形成工序s23”中,在各个聚酰亚胺层35上形成粒子层36。具体而言,首先使用反向微凹印在聚酰亚胺层35上涂覆以pe粒子分散于液体中的聚乙烯乳液为主要成分的微粒子水分散体(三井化学制chemipearl)并进行干燥,从而在聚酰亚胺层35上制成pe粒子堆积成的粒子层36。pe粒子的中值粒径(d50%)是3μm。这样,形成了负极板31(31a、31b、31c)。
[0068]
接下来,在“电极体形成工序s3”中形成电极体20。具体而言,交替地层叠多个正极板21以及负极板31。此时,在层叠方向eh的最一侧eh1(在图2中为最上端位置)配置一侧负极板31a,在层叠方向eh的最另一侧eh2(在图2中为最下端位置)配置另一侧负极板31b。
[0069]
接下来,在“组装工序s4”中组装电池1。具体而言,将正极端子部件50以及负极端子部件60分别固定设置于壳体盖部件13(参照图1)。并且,将正极端子部件50以及负极端子部件60分别焊接于电极体20。然后,将电极体20插入到壳体主体部件11内,用壳体盖部件13封堵壳体主体部件11的开口。然后,对壳体主体部件11和壳体盖部件13进行激光焊接来形成电池壳体10。然后,将非水电解液19从设置于壳体盖部件13的注液孔13h注射到电池壳体10内并使其浸渍在电极体20内,之后利用密封部件15密封注液孔13h。
[0070]
接下来,在进行“初始充电工序s5”之前,约束电池1。具体而言,用一对板状的按压夹具在电池厚度方向bh夹持电池壳体10中的最大面积且与电池厚度方向bh正交的2个对置的侧面,将电池1约束为沿电池厚度方向bh按压了的状态。其中,在本实施方式中,在这样约束了电池1的状态下进行以下说明的“初始充电工序s5”以及“短路检查工序s6”。
[0071]
在约束了电池1之后,在“初始充电工序s5”中对该电池1进行初始充电。具体而言,将充放电装置与电池1连接,并在室温(25
±
5℃)下通过恒流恒压充电(cccv充电)初始充电到4.2v。
[0072]
接下来,在“短路检查工序s6”中,将电池1放置在高温下陈化(ageing),并且,在室温下放置规定的放置时间,根据放置前后的电池电压获取由于自放电所造成的电压降低量
δv2,来检测该电池1的内部短路的有无。具体而言,首先将初始充电后的电池1放置在50~80℃的温度(在本实施方式中为60℃)下,在端子开放的状态下放置20个小时进行陈化。接下来,将电池1在室温(25
±
5℃)下放置7天,测量电压降低量δv2。
[0073]
然后,根据电压降低量δv2的大小来判定该电池1是否产生短路。具体而言,将该电池1的电压降低量δv2与基准电压降低量va比较,在电压降低量δv2大于基准电压降低量va的情况(δv2>va)下,判定为该电池1产生了内部短路(次品),废弃该电池1。另一方面,在该电池1的电压降低量δv2小于基准电压降低量va的情况(δv2≤va)下,将该电池1判定为正常(未产生内部短路的良品)。如此,电池1完成。
[0074]
以上,根据实施方式以及实施例对本发明进行了说明,但本发明并不局限于上述的实施方式等,当然能够在不脱离其主旨的范围内适当地进行变更来应用。
[0075]
在上述的实施方式以及实施例中,在负极板31设置了由聚酰亚胺层35和粒子层36构成的隔板层34,但也可以代替此而在正极板21设置由聚酰亚胺层和粒子层构成的隔板层。另外,也可以在负极板以及正极板双方设置由聚酰亚胺层和粒子层构成的隔板层。
[0076]
附图标记的说明
[0077]
1...锂离子二次电池(蓄电装置);19...非水电解液(电解液);20...电极体;21...正极板;22...正极集电箔;22c...一侧面;22d...另一侧面;23...正极活性物质层;24...耐热材料层;31...负极板(隔板一体负极板、隔板一体电极板);31a...一侧负极板;31b...另一侧负极板;31c...内侧负极板;32...负极集电箔;32c...一侧面;32d...另一侧面;33...负极活性物质层;34...隔板层;35...聚酰亚胺层;36...粒子层(聚烯烃粒子层);36p...树脂粒子(聚烯烃树脂粒子);eh...层叠方向;eh1...(层叠方向中的)一侧;eh2...(层叠方向中的)另一侧;fh...电极取出方向;fh1...(电极取出方向中的)第一取出侧;fh2...(电极取出方向中的)第二取出侧;s2...负极板形成工序;s21...负极活性物质层形成工序;s22...聚酰亚胺层形成工序;s23...粒子层形成工序;hd1、hd2...保持件;hd1h、hd2h...贯通孔;d...(贯通孔的)直径;nd...挤压针;nds(挤压针的)前端部;r...(前端部的)半径;lc...测压元件;mh...移动头;sp...移动速度;ps...电源;cm...电流计。
再多了解一些
本文用于企业家、创业者技术爱好者查询,结果仅供参考。