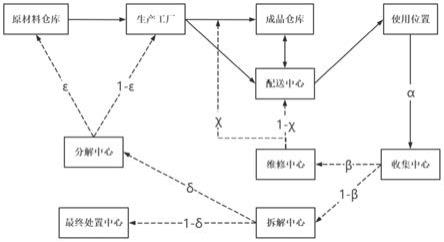
1.本发明属于工业工程领域的一种产品价值链优化处理方法,具体是一种不确定环境下产品价值链模式的多阶段优化配置方法。
背景技术:
2.由于资源短缺和环境恶化,政府、企业和学术机构越来越重视产品生命周期的管理。正如papageorgiou(2009)所述,人们对闭环价值链的设计与规划问题的兴趣越来越大,其旨在收集和再利用报废产品,并将环境问题与旧产品价值恢复相关的商业机会联系起来。salema等人(2010)提出了一个多周期、多产品网络模型,用于同时设计和规划具有反向流动的价值链,其中在正向和反向两个方向上都考虑了两层网络。后来,达斯和乔杜里(2012)发布了一个闭环价值链网络模型,其中根据被退回的产品的三个预先定义的质量水平来选取重新制造的方案。然而,在实际生产环境中需要从更广泛的角度研究闭环价值链的设计与规划问题。例如,将通用网络纳入不确定条件下建模的经济和环境问题的考虑范畴(paksoy等人(2011),zeballos等人(2012))。目前的研究工作旨在减少这种差距,并在考虑网络经济与环境成本的确定性与不确定性条件下研究通用的闭环价值链网络模型结构。
3.目前在确定性环境下,多产品价值链的优化策略已趋于成熟。而在不确定环境下,例如原材料数量和使用位置需求水平不确定情况下,对于不确定性进行建模,目前还没有较为有效的建模方式。另外目前的不确定性建模基本采用两阶段优化模型,无法适用各类产品在多个时间段中表现形式复杂多样的情况,并且大多不允许在各个时间段内进行决策修正。因此在实际生产环境中,应用价值局限性较高,无法实现最大化回收产品的数量,优化结果精确度较低。
技术实现要素:
4.鉴于以上所述现有技术的缺点,本发明的目的在于提供一种新的不确定环境下产品价值链的优化配置方法。这种新型优化方法可以实现在每个时间段内的优化,以此实现网络的动态特性,这是确定性公式和两阶段模型所不具备的优势。
5.本发明通过在产品价值链网络上完成不确定性随机建模,获得产品价值链网络模型,使用基于多阶段随机混合整数线性规划优化产品价值链网络模型,从而获得产品价值链的最佳拓扑结构,进而实施到产品运输和仓储中。
6.本发明采取以下技术方案:
7.s1:构建包含10个节点的多周期、多产品的产品价值链网络模型;
8.s2:根据产品价值链网络模型建立基于多阶段随机混合整数线性规划的目标函数和约束条件,进而优化获得产品价值链的最优配置,将最优配置施加到各个节点和节点间实现最优产品的运输和储存。
9.所述的产品价值链网络模型是由节点和边构成,节点代表产品价值链中具体的独立单元,边代表了节点之间的关系,具体为离散事件,离散事件是指一个节点到另一个节点
的触发行为,设置每种离散事件发生的给定概率作为不确定性参数,所有具有不确定参数的离散事件构成了不确定性环境。
10.具体的产品价值链网络模型中包含一组用于描述离散事件的不确定性参数。
11.如图1所示,所述产品价值链网络模型中的十个节点分别为原材料仓库is、生产工厂if、成品仓库iw、配送中心i
dc
、使用位置ic、收集中心i
cc
、拆解中心id、维修中心i
rc
、最终处置中心i
fd
和分解中心i
dp
;
12.产品的正向生产流程包括了原材料仓库is、生产工厂if、成品仓库iw、配送中心i
dc
、使用位置ic的五个节点的关系,原材料仓库is发出原材料到生产工厂if,由生产工厂if生产出产品运输到成品仓库iw和配送中心i
dc
进行存储,成品仓库iw和配送中心i
dc
之间存在产品运输,配送中心i
dc
中的产品向使用位置ic进行运输;
13.本发明在原有产品的正向生产流程,增设了产品的反向生产流程的模型。
14.产品的反向生产流程还包括了收集中心i
cc
、拆解中心id、维修中心i
rc
、最终处置中心i
fd
和分解中心i
dp
,使用过的产品从使用位置被退回收集运送到收集中心,收集中心的一部分使用过的产品运送到维修中心进行维修翻新处理,收集中心的另一部分使用过的产品运送到拆解中心进行拆解,维修中心将修理后的一部分产品运送到配送中心,维修中心将修理后的另一部分产品运送到成品仓库,拆解中心将拆解产品获得的一部分模块或者组件运送到分解中心进行进一步分解,拆解中心将拆解产品获得的另一部分模块或者组件运送到最终处置中心进行最终处置,分解中心将将分解模块和组件获得的一部分元件或者零部件运送到原材料仓库,分解中心将将分解模块和组件获得的另一部分元件或者零部件运送到生产工厂。
15.拆解中心是对损坏严重而无法维修的产品进行拆分为模块和组件,分解中心是对损坏严重而无法维修的模块和组件进行进一步元件或者零部件的分解。最终处置中心对拆解后的模块和组件进行垃圾处理。
16.如图1所示,实线表示产品的正向生产流程,虚线表示本发明所增设的产品的反向生产流程。
17.所述的原材料仓库is、生产工厂if、成品仓库iw、配送中心i
dc
、使用位置ic、收集中心i
cc
、拆解中心id、维修中心i
rc
、最终处置中心i
fd
和分解中心i
dp
的各个节点均包含多个实体,多个实体地点不同。例如维修中心i
rc
由很多个实体,在某处有一个作为维修中心i
rc
的实体,在另一处也有一个作为维修中心i
rc
的实体。
18.设置以下节点间的不确定性参数,在优化过程中根据不确定性参数进行优化求解:使用过的产品从使用位置被退回收集运送到收集中心的退货率为α,收集中心的一部分使用过的产品运送到维修中心进行维修翻新处理的维修比例为β,收集中心的另一部分使用过的产品运送到拆解中心进行拆解的拆解比例为1-β,维修中心将修理后的另一部分产品运送到成品仓库的坏修比例χ,维修中心将修理后的一部分产品运送到配送中心的良修比例1-χ,拆解中心将拆解产品获得的一部分模块或者组件运送到分解中心进行进一步分解的分解比例为δ,拆解中心将拆解产品获得的另一部分模块或者组件运送到最终处置中心进行最终处置的坏品比例为1-δ,分解中心将分解模块和组件获得的一部分元件或者零部件运送到原材料仓库的比例为ε,分解中心将分解模块和组件获得的另一部分元件或者零部件运送到生产工厂的比例为1-ε。
19.本发明在所述不确定性环境下,采用多阶段方法允许在每个时间段内修改优化,即修改不确定性参数以实现目标。
20.目标函数包含两个连续变量用于表示在指定时间与指定方案下两节点间产品的运输数量和存储数量、一个半连续变量用于表示在任意方案下指定时间与指定运输模式下两节点间产品的运输数量以及一个数值变量用于表示节点中的实体数量。
21.本发明充分考虑未来事件可能产生的需求和供应状态变动和最小化产品价值链网络的总成本,以实现最小化原材料消耗、储存、运输的预期成本和排放,并同时最大化回收产品的数量的目标,建立以下目标函数及其约束条件:
[0022][0023]
约束条件:
[0024][0025][0026][0027][0028][0029][0030]
其中:
[0031]
x
ijprts
是第一连续变量,表示在指定时间段t和指定方案s中从节点i运输到节点j的产品p的数量;
[0032]zipts
是第二连续变量,表示节点i在指定时间段t和指定方案s中存储的产品数量;
[0033]
yi为数值变量,表示节点i所包含中的实体数量;
[0034]
x
ijrts
是半连续变量,代表边对应的节点i在运输模式r、时间段t和方案s 的情况下向节点j运送的产品的数量;
[0035]
p表示产品的序号,pr表示产品的集合;
[0036]
r表示运输模式的序号,tr表示运输模式的集合;
[0037]
t表示时间段的序号,t表示所有时间长;
[0038]
s表示方案,sc代表所有方案的集合,pbs代表方案s属于集合sc的概率;
[0039]
每种产品在不同网络结构下都有不同的需求与供应状态,具体体现在:当采取不
同的网络结构,会改变产品的生产成本(包含运输、采购、储存、设施和co2排放等各项成本)而最终影响产品价格,产品价格最终导致产品的需求发生变动。而不同的网络结构也会影响产品的供应状态,例如当各节点的实体数目越多,产品的反向生产流程各节点的处理速度也越快,相应地产品供应水平也随之提高。以ed代表产品所有需求状态的集合,es代表产品所有供应状态的集合。ed∈ed代表某种具体的需求状态,es∈es代表某种具体的供应状态。
[0040]
所述的方案具体指不同的预设条件,比如各个节点预设有多少个实体数目,以及时间预设的不同的不确定性参数。
[0041]
i、j表示节点的序号,i代表所有节点的集合,i∈i代表某一节点;
[0042]
a代表节点之间所有的边集合,dst
ij
代表节点之间边的距离,具体指节点对应实体之间的实际距离;
[0043]cijrt
代表一条边在运输模式r、时间段t的情况下的运输成本;
[0044]eijrt
代表一条边在运输模式r、时间段t的情况下的采购成本;
[0045]
pc
pt
表示产品p在时间段t下的价值增益,表示任意供应状态和需求状态;
[0046]uipt
代表在时间段t的情况下产品p在节点i的存储成本;
[0047]
stc
ipt
代表在时间段t的情况下产品p在节点i的设施成本;
[0048]zipts
代表在时间段t、方案s的情况下产品p在节点i的存储数量;
[0049]
fcci代表节点i的co2排放成本;
[0050]
ω
st
表示在时间段t发生在方案s的离散事件es∈es和ed∈ed;
[0051]dipted
表示在时间段t、产品需求量ed情况下产品p在节点i的需求下限;
[0052]
rmn
iptes
代表在时间段t、产品供应量es情况下产品p在节点i的供应量最小值;
[0053]
rmx
iptes
代表在时间段t、产品供应量es情况下产品p在节点i的供应量最大值;
[0054]
所述的运输模式r分为陆运、海运、空运。
[0055]
然后通过优化求解目标函数获得各个节点间的第一连续变量x
ijprts
、第二连续变量z
ipts
、半连续变量x
ijrts
以及每个节点的数值变量yi,即确定了各个节点的实体数目、制造的产品以及运输、存储和回收的数量,根据第一连续变量x
ijprts
、第二连续变量z
ipts
、数值变量yi、半连续变量x
ijrts
对产品的运输和储存进行配置。
[0056]
在优化求解过程中,每个节点i到每个节点j之间的产品运输关系和过程根据产品价值链网络模型和不确定性参数进设置。
[0057]
目标函数中,第一项表示考虑所有时间段,对于每种运输方式和产品类型,节点之间边a上的运输和排放成本;第二项特指从原材料仓库运输到工厂的产品(原材料)的采购成本;第三项表示所有实体、产品和时间段的存储成本;第四项表示通过将回收的产品/材料引入前向网络获得的价值增益。第五项表示开放/使用设施的成本,与方案无关。
[0058]
不等式(2)表示规定的周期内需求量合格的最低水平,并考虑特定事件 ed∈ed(d
ipted
)。不等式(3)和(4)限制了在时间t发生事件es∈es时原材料的最大和最小供应能力。上述约束条件确保闭环供应链中每种产品的流量守恒、所有相关节点的加工和存储能力以及不同运输模式的运输承载量。
[0059]
本发明将完整的时间规划范围被划分为多个时间段(t),每个时间段内:
[0060]
向使用位置供应来自仓库和配送中心的多种产品;原材料仓库和工厂从分解中心接收旧产品的可重复使用部分;仓库和配送中心从维修中心获取维修产品;回收产品与新产品一视同仁;任何一对节点之间的运输操作都可以使用不同的运输模式(tr)来执行;网络结构中的产品(pr)根据其回收等级进行分组(例如完全可重复使用、部分可重复使用和不可重复使用)。
[0061]
不确定性与需求(d)和原材料供应有关,原材料供应量受到人为规定的最小值(rmn)和最大值(rmx)约束。节点之间的距离(dst)和运输模式级别是已知且固定的。运输、采购、储存、设施和估计的co2排放成本(分别为c、 e、u、stc和fcc)以及回收产品的单位价值增益(pc)也是确定性的。并考虑到未来事件可能导致的需求和供应状态(ed和es)。
[0062]
本发明主要是解决在原材料数量和使用位置需求水平不确定的环境下产品价值链的设计和规划问题。针对一些具有实际意义的方案,例如在不同运输方式下运营和环境成本的限制方案,以及生产、分配和储存的容量限制方案。
[0063]
本发明相较于传统方法和配置,计算复杂度更低,并且能够保证优化结果具有良好的精确度。
[0064]
本发明的有益效果为:
[0065]
1、传统优化方法往往需要多个离散的方案加以近似,以此实现随机变量的概率分布,而随着优化结果精确度的提升,所需近似的方案数会呈现几何式增长,导致计算复杂度急剧提升。本发明利用产品价值链网络模型严格限制了方案数,显著地降低了计算复杂度,并且采用多阶段优化配置方法来保证优化结果具有较高精确度,得益于其高精度特性,不再像传统优化方法仅能作为参考。
[0066]
2、在这项工作中,引入了多阶段优化配置方法来处理产品价值链的设计和规划问题。通过产品价值链网络模型的参数和情景分析,构建对应产品价值链网络,例如价值链网络各节点实体的数目,以及实体之间实际距离,以及预估各种网络所带来的价值增益。并且提前预估不同网络结构对产品所带来的影响,根据不同时期的不同目标,可以更有目的性地去调整产品价值链网络。而人工规划和设计网络结构,只能通过后续结果来倒推网络结构合理性再做出对应调整,其具有滞后性。突出使用多阶段优化配置方法对产品价值连的设计和规划的好处。
[0067]
3、传统优化方法例如确定性公式以及两阶段模型获得的网络模型仅适用于其预设的确定参数。而实际生产中,产品价值链网络需要跟随时间实现动态调整,例如需要加大网络的供应量,应尽量减小网络的供应量以及减小整体网络的生产成本。这种新型优化方法可以实现在每个时间段内修改决策,以此实现网络的动态特性,这是确定性公式和两阶段模型所不具备的优势。
附图说明
[0068]
为了进一步阐述本发明所描述的内容,下面结合附图对本发明的具体实施方式作进一步详细的说明。应当理解,这些附图仅作为典型示例,而不应看作是对本发明的范围的限定。
[0069]
图1为产品价值链网络结构图。
具体实施方式
[0070]
以下通过特定的具体实例说明本发明的实施方式,本领域技术人员可由本说明书所揭晓的内容轻易地了解本发明的其他优点与功效。本发明还可以通过另外不同的具体实施方式加以实施或应用,本说明书中的各项细节也可以基于不同观点与应用,在没有背离本发明的精神下进行各种修饰和改变。
[0071]
本发明的实施例具体实现过程描述如下:
[0072]
产品价值链网络结构由3个原材料仓库(s1,s2,s3)、3个生产工厂(f1,f2,f3)、 1个成品仓库(w1)、2个配送中心(dc1,dc2)、5个使用位置、2个收集中心(cc1,cc2)、 2个拆解中心(d1,d2)、1个维修中心(rc1)、2个分解中心(dp1,dp2)、1个最终处置中心(fd1)组成。网络中的产品按回收率被分为3组:回收率为100%、50%和 0%的产品(分别对应完全可重复使用、部分可重复使用和不可重复使用)。新产品和回收利用重新制造出的产品之间没有区别。
[0073]
运输系统包含陆运、海运、空运三种运输模式。使用过的产品从使用位置被退回收集运送到收集中心的退货率为α,收集中心的一部分使用过的产品运送到维修中心进行维修翻新处理的维修比例为β,维修中心将修理后的另一部分产品运送到成品仓库的坏修比例χ,拆解中心将拆解产品获得的一部分模块或者组件运送到分解中心进行进一步分解的分解比例为δ,分解中心将分解获得的一部分元件或者零部件运送到原材料仓库的比例为ε。每种模式都有固定单位的二氧化碳排放量和运输成本。假定产品通过反向生产流程的参数为:α=0.7,β=0.4,χ=0.7,ε=0.7,δ={(δ
p1
,δ
p2
,δ
p3
)=(0,0.7,1)}。
[0074]
在这项工作中,原材料供应(es)和需求(ed)的不确定性分别通过三个可能值来近似:es1、es2和es3,以及ed1、ed2和ed3。因此供应状态与需求状态两两组合将有9种方案,并假定两年时间作为实验方法考虑的总时间,将其(24*30 天)分成9段,每段80天作为多阶段优化配置方法作用的时间范围,最终获得 81种方案数。
[0075]
该公式在具有amd ryzen 8 4800h 2.90ghz和16gb ram内存的工作站上求解,间隙容限为0.01%。
[0076]
多阶段优化配置方法(spa)的优势评估是针对确定性方法(da)进行的,其中考虑了预期的需求和原材料供应。此外,还考虑了反向生产流程中的不同处理的替代方案。表1和表2中描述了参数α和ε对da和spa的结果。
[0077]
表1不同案例研究的在单一变量α下的最佳网络结构
[0078] dadaspaspaspaspa实体α=0.7α=1α=0.7α=0.8α=0.9α=1s1******s2
ꢀꢀ
****s3******f1**
ꢀꢀꢀꢀ
f2******f3
ꢀꢀ
****w1******dc1******
dc2
ꢀꢀ
****cc1 * ***cc2* ****rc1******d1******d2 **
ꢀꢀꢀ
dp1
ꢀꢀ
****dp2******fd1******
[0079]
注:未选中部分代表该实体未选用
[0080]
表2不同案例研究的在单一变量ε下的最佳网络结构
[0081] daspaspaspa实体ε=1ε=0.8ε=0.9ε=1s1****s2 ***s3****f1*
ꢀꢀꢀ
f2****f3 ***w1****dc1****dc2 ***cc1
ꢀꢀꢀ
*cc2****rc1****d1****d2 ** dp1 ***dp2****fd1****
[0082]
注:未选中部分代表该实体未选用
[0083]
表3价值增益和成本分析表
[0084][0085][0086]
应用于该问题的线性规划公式包含16个二元变量、20779个半连续变量、 89926个连续变量和71679个约束。另一方面,确定性方法包含16个二元变量、 469个半连续变量、2022个连续变量和1639个约束。鉴于相似类型实例的spa 和da的模型维度相同,两种模型分组计算并记录平均计算工作量。结果显示spa的计算量明显更大,需要1800秒的cpu计算时间才能获得最佳解决方案,对比da只需要5秒的cpu计算时间。
[0087]
从结果可以看出,与确定性解决方案(da)相比,多阶段优化配置方法(spa) 适用于更多的网络结构实体并获得了更大的目标函数值。在α=0.7的情况下, da的目标值为3.2306
×
e-9,而spa的目标值为4.0965
×
e-9。spa解决方案比da获得的解决方案的结果高出26.8%。这是因为spa获得了所有组合方案的最佳解决方案,而da的解决方案是基于不确定参数中期望值的单一方案。此外,由于受限所选工厂的生产能力,da的网络结构是不可行的。
[0088]
与参考案例(α=0.7)相比,随着退货率α的增加(从0.7到1),spa 获得的网络结构中收集中心的实体数量提高至两个,以应对提升的退货率,但对应地需要减少一个拆解中心来达到平衡。
[0089]
当产品的可重复使用部分的比率ε增加时,也会出现类似的情况。然而,对于ε=1,原材料成本增加,减少,因为当回收产品完全由原材料仓库再加工时,公司获得的收入减少。通过与da的对比可以看出,spa可以获得产品流量和实体数量更高的解决方案。
[0090]
在spa方案中发现包含3个原材料仓库以及两个生产工厂f2和f3的优化方案是适应不确定环境下产品价值链的关键要素,但这在确定性方案中没有观察到。
[0091]
由上述实施例可知,本发明对比于确定性环境下方案能更好的获得更优的优化策略方案,并且spa方案在每个时间段内允许修改决策,实现了价值链网络的动态特性。
[0092]
上述具体实施例仅例式性说明本发明的原理与其功效,并非用于限制本发明。任
何熟悉此技术的人士皆可在不违背本发明的精神及范畴下,对上述实施例进行修饰或改变。因此,凡在未脱离本发明所揭示的精神与技术思想下所完成的一切等效修饰或改变,仍应由本发明的权利要求所涵盖。
再多了解一些
本文用于企业家、创业者技术爱好者查询,结果仅供参考。