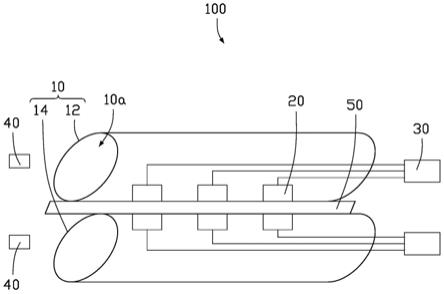
1.本发明涉及压膜机技术领域,尤其涉及一种压膜机和一种压膜机的控制方法。
背景技术:
2.目前,电子产品逐步向着短/小/轻薄发展,对应设备的精度及稳定性要求越来越高,为了防止生产出不良产品,需定期对设备能力进行检核。其中,压力均匀性是压膜机稳定性的监控指标之一,压力不均匀直接影响到产品的开短路功能性报废。
3.现有的压膜机压力均匀性测试的作业方式为:在基板(如,裸铜板)上下表面贴附感压纸,当基板经过上下压膜辊后,加压加热辊提供压力及温度给压膜辊,使贴附于基板上的感压纸发生变色(如,感压纸产生红色痕迹),通过量测变色区域的宽度,监控压膜机的压力均匀性。一般地,每周都需对压膜机压力进行测试一次,以保证压膜机压力均匀性稳定,方可进行生产。
4.因此,现有的压膜机及其压力检测方法,浪费感压纸,且操作不便捷,需要人员去计算判定,时效性差。
技术实现要素:
5.本发明实施例提供一种压膜机,其包括:
6.压膜辊,所述压膜辊为空心的,其定义有一容置空间,以及
7.压力传感器,位于所述容置空间内并固定连接于所述压膜辊上,以用于测试待压膜的基板与所述压膜辊接触时的压力值。
8.该压膜机,通过在压膜辊内设置压力传感器,可实时监控压膜辊与基板接触时的压力值。如此,避免了压感纸的浪费,也无需每周都要提前排配人员去检测,节省了人力及时间。并且,压力传感器可实时地监控压膜辊在工作过程中的压力变化,时效性快。
9.本发明实施例还提供一种压膜机的控制方法,用于控制上述的压膜机,其包括:
10.接收并发送所述压力传感器测试的压力值;
11.判断所述压力值是否超出预设的压力范围;以及
12.当所述压力值超出预设的压力范围时,控制所述压膜机停机。
13.该压膜机的控制方法,可实时监控压膜辊与基板接触时的压力值,并进行比较判断该压力值是否出现异常以及时暂停压膜过程。如此,避免了压感纸的浪费,也无需每周都要提前排配人员去检测,节省了人力及时间。并且,压力传感器可实时地监控压膜辊在工作过程中的压力变化,时效性快。
附图说明
14.图1为本发明一实施例的压膜机的结构示意图。
15.图2为压力传感器与压膜辊的连接示意图。
16.图3为本发明另一实施例的压膜机的结构示意图。
17.图4为本发明一实施例的压膜机的控制方法的流程示意图。
18.主要元件符号说明
19.压膜机
ꢀꢀꢀꢀꢀꢀꢀꢀꢀꢀꢀꢀꢀꢀꢀꢀꢀ
100
20.压膜辊
ꢀꢀꢀꢀꢀꢀꢀꢀꢀꢀꢀꢀꢀꢀꢀꢀꢀ
10
21.容置空间
ꢀꢀꢀꢀꢀꢀꢀꢀꢀꢀꢀꢀꢀꢀꢀ
10a
22.上压膜辊
ꢀꢀꢀꢀꢀꢀꢀꢀꢀꢀꢀꢀꢀꢀꢀ
12
23.下压膜辊
ꢀꢀꢀꢀꢀꢀꢀꢀꢀꢀꢀꢀꢀꢀꢀ
14
24.安装孔
ꢀꢀꢀꢀꢀꢀꢀꢀꢀꢀꢀꢀꢀꢀꢀꢀꢀ
16
25.压力传感器
ꢀꢀꢀꢀꢀꢀꢀꢀꢀꢀꢀꢀꢀ
20
26.螺栓孔
ꢀꢀꢀꢀꢀꢀꢀꢀꢀꢀꢀꢀꢀꢀꢀꢀꢀ
22
27.第一预紧工装
ꢀꢀꢀꢀꢀꢀꢀꢀꢀꢀꢀ
242
28.第二预紧工装
ꢀꢀꢀꢀꢀꢀꢀꢀꢀꢀꢀ
244
29.螺栓
ꢀꢀꢀꢀꢀꢀꢀꢀꢀꢀꢀꢀꢀꢀꢀꢀꢀꢀꢀ
26
30.螺杆
ꢀꢀꢀꢀꢀꢀꢀꢀꢀꢀꢀꢀꢀꢀꢀꢀꢀꢀꢀ
262
31.螺母
ꢀꢀꢀꢀꢀꢀꢀꢀꢀꢀꢀꢀꢀꢀꢀꢀꢀꢀꢀ
264
32.数据采集器
ꢀꢀꢀꢀꢀꢀꢀꢀꢀꢀꢀꢀꢀ
30
33.基板
ꢀꢀꢀꢀꢀꢀꢀꢀꢀꢀꢀꢀꢀꢀꢀꢀꢀꢀꢀ
50
34.如下具体实施方式将结合上述附图进一步说明本发明。
具体实施方式
35.为了能够更清楚地理解本发明的上述目的、特征和优点,下面结合附图和具体实施例对本发明进行详细描述。需要说明的是,在不冲突的情况下,本技术的实施例及实施例中的特征可以相互组合。
36.在下面的描述中阐述了很多具体细节以便于充分理解本发明,所描述的实施例仅是本发明一部分实施例,而不是全部的实施例。基于本发明中的实施例,本领域普通技术人员在没有做出创造性劳动前提下所获得的所有其他实施例,都属于本发明保护的范围。
37.除非另有定义,本文所使用的所有的技术和科学术语与属于本发明的技术领域的技术人员通常理解的含义相同。本文中在本发明的说明书中所使用的术语只是为了描述具体的实施例的目的,不是旨在于限制本发明。
38.图1为本发明一实施例的压膜机100的结构示意图。如图1所示,压膜机100包括压膜辊10以及压力传感器20。其中,所述压膜辊10为空心的,其定义有一容置空间10a。压力传感器20位于所述容置空间10a内并固定连接于所述压膜辊10上,以用于测试待压膜的基板50与所述压膜辊10接触时的压力值。
39.该压膜机100,通过在压膜辊10内设置压力传感器20,可实时监控压膜辊10与基板50接触时的压力值。在压膜过程中,如没有异常点则压膜辊10表面各点收到的压力较为均匀,若有异常点(如异物、粉尘颗粒、铜颗粒等)则压膜过程中压膜辊10受到的压力会发生变化,形成压力异常点。
40.该压膜机100,通过设置压力传感器20,可实时地监控压膜辊10在工作过程中的压力变化,无需每周都要提前排配人员去检测,节省了人力及时间,也无需浪费感压纸,节约
了压感纸的使用成本。且压力传感器20可实时地监控压膜辊10在工作过程中的压力变化,时效性快,可快速发现问题以及时根据压力异常点进行调整,进而保证产品的品质稳定性。再者,该压膜辊10为空心的,通过将压力传感器20设置于压膜辊10内,压膜机100的结构更紧凑。
41.请继续参阅图1,所述压膜辊10包括相对设置的上压膜辊12和下压膜辊14。所述上压膜辊12和所述下压膜辊14内均包括间隔设置的多个所述压力传感器20。
42.图1中,所述上压膜辊12和所述下压膜辊14内分别设置有三个所述压力传感器20,即,对应基板50的上下表面分别对应三个位置量测压力值的变化。于其他实施例中,压力传感器20的数量不限于三个。
43.图1中,位于所述上压膜辊12内的多个所述压力传感器20和位于所述下压膜辊14内的多个所述压力传感器20一一对准设置。基板50的上下表面的压力量测点的位置大致对称。
44.于其他实施例中,上压膜辊12内压力传感器20和下压膜辊14内的多个所述压力传感器20也可采用其他排布设置。例如,图3中,位于所述上压膜辊12内的多个所述压力传感器20和位于所述下压膜辊14内的多个所述压力传感器20相互交错设置。上压膜辊12内的每一压力传感器20的投影位于下压膜辊14内相邻的两个压力传感器20之间,如此,使得沿基板50的宽度方向可以有更多量测点。
45.于一实施例中,所述压力传感器20的可耐温度为-20℃至120℃,其能够量测的最小压力值为1n。其中,所述压膜机100可设置压力传感器20的量测压力的范围,例如,其量测范围为40n至60n。
46.请继续参阅图1,所述压膜机100还包括数据采集器30。该数据采集器30位于压膜辊10外。每一压力传感器20均电性连接至所述数据采集器30。数据采集器30用于接收和处理每一压力传感器20量测的压力值。
47.于一实施例中,数据采集器30的数量为二。上压膜辊12内的压力传感器20和下压膜辊14内的压力传感器20分别电性连接至不同的数据采集器30。
48.于一实施例中,所述压膜机100还包括电性连接所述数据采集器30的控制器(图未示)。所述控制器接收所述数据采集器30的信号后,判断压力传感器20量测的所述压力值是否超出预设的压力范围。如果所述压力值超出预设的压力范围,则该控制器控制所述压膜机100停机。
49.于一实施例中,所述控制器可以为,但不限于,可编程逻辑控制器(programmable logic controller,plc)。
50.于一实施例中,预设的压力范围包括两个临界点(压力值的上限值和下限值)。该压力值的上限值和下限值为经过长期测试得到的压膜无异常情况下的正常压力范围的上下限。该预设的压力范围可以提前导入压膜机100的程序中。在压膜工艺中,若压力传感器20检测的压力值大于所述上限值或小于所述下限值时,控制器控制压膜机100停机,以进入待检查状态,等待人员维修完毕,待人工开启后,再次进入正常生产状态。
51.请继续参阅图1,所述压膜机100还包括光电开关,所述光电开关电性连接所述控制器。所述数据采集器30包括放大器,所述放大器电性连接所述压力传感器20和所述控制器。所述放大器可用于对接收到的压力信号进行放大处理。所述控制器还用于接收所述光
电开关发出的信号,以控制所述放大器复位,从而使所述压力传感器20周期性检测压力。图1中,光电开关的数量为二,其分别针对上压膜辊12和下压膜辊14设置。
52.如图2所示,压力传感器20中部定义有贯穿其相对两表面的螺栓孔22,以使所述压力传感器20和压膜辊10通过螺栓26实现固定连接。图2中,所述压力传感器20的相对两侧分别设置有预紧工装24。螺栓26包括螺杆262和螺母264。压膜辊10对应设置压力传感器20的位置开设有安装孔16。第一预紧工装242开设有凹槽,螺杆262的一端与位于凹槽内的螺母264紧固。螺杆262的另一端依次穿过第一预紧工装242、压力传感器20、第二预紧工装244以及压膜辊10而与另一螺母264紧固。
53.于其他实施例中,压力传感器20和压膜辊10可采用其他连接,例如,螺钉连接,焊接或铆接等。
54.于一实施例中,所述上压膜辊12和所述下压膜辊14的长度可以为660mm,外径50mm,内径48mm,压力传感器20为圆环状,其外径为12mm,内径为4mm,厚度3mm,但不限于此。
55.在压膜辊10转动的过程中,当压力传感器20与待压膜的基板50平行时(即,压力传感器20感测压力的表面与基板50的表面平行时,或者说,压膜辊10安装有压力传感器20的位置与基板50接触时),压力传感器20会受到基板50的压力,并将该压力值发送至数据采集器30,数据采集器30接收并处理该压力值,并将其发送给控制器。其中,压膜辊10旋转一周,光电开关保持开关一次,控制器命令数据采集器30中的放大器复位(数据清零),然后压膜辊10再进行下一周的运转。如此,使得压力传感器20可以周期性检测压力。
56.于一实施例中,所述数据采集器30还包括滤波模块(图未示)以及模数转换模块(图未示)等。其中,放大器和滤波模块电性连接,滤波模块和模数转换模块电性连接。滤波模块用于对压力信号进行滤波处理,模数转换模块用于对压力信号进行模数转换处理。
57.于一实施例中,所述压膜机100还包括报警单元(图未示)。所述报警单元与所述控制器电性连接。在所述压力值超出预设的压力范围时,报警单元发出报警提示,以提示人员及时排查异常及异常位置。其中,报警提示可以为响铃警报、红灯警报灯,以使压膜异常问题尽快被知晓并及时得到处理,进而提高压膜过程的生成效率。
58.于一实施例中,压膜机100电性连接至电脑。压膜机100包括操作面板,在该操作面板上,具有按键,可以设定时间间隔,以定期监控压膜机100的压力的变化值。其中,压力传感器20测得的压力数据可存储于电脑,并自动导入数据系统内,该数据系统可以生成压力的变化趋势图,通过观察该压力的变化趋势图,可以直观的观测到压膜机100是否有异常,进而及时有效的进行异常处理,保证机台的稳定性。
59.于一实施例中,该压膜机100用于电路板(如高密度互连电路板、印刷电路板等)的生成过程中。在电路板生成图形线路过程中,均需要进行表面压膜处理。其中,图形线路压膜工艺是表面压膜处理的重要步骤之一。其主要是利用压膜机100的包胶滚轮(即,压膜辊10外面包覆一层胶层)对电路板进行预热处理,温度可在100℃(其可根据板厚及散热设计而定),使电路板的表面温度达到压膜生成温度,干膜贴附电路板表面后受高温影响,充分释放干膜流动性和贴合性,使干膜更好的发挥表面贴合和封孔能力,以便于对电路板进行附着和封孔。其中,压膜机100在进行干膜压贴时,需要根据生产参数对压膜机100的包胶滚轮进行压力设定,以适应不同板厚和不同结构的电路板生产条件。其中,压力参数是指电路板(或其基板50,比如裸铜板)正反两面受包胶滚轮的压力值,而该压力值主要受到电路板
表面洁净度和板材本体结构的影响。在生产过程中,例如空气中的灰尘、药水残留等均会对压膜品质造成影响。
60.该压膜机100,通过在其压膜辊10内设置压力传感器20,测试电路板或其基板50与压膜辊10接触时的压力值,并进行比较判断该压力值是否处于预定的压力范围内,从而对表面异常的基板50及时暂停其压膜过程,进而避免了批量性的不良压膜板的产出,以降低报废率,提高电路板的良品率及生成效率。
61.图4为本发明一实施例的压膜机100的控制方法的流程示意图,其用于控制上述的压膜机100。如图4所示,该控制方法包括以下步骤。
62.步骤s1:接收并发送所述压力传感器20测试的压力值。
63.具体地,数据采集器30接收并处理所述压力传感器20测试的压力值信号,对其放大、滤波、模数转换等处理。然后,将其发送给控制器。
64.步骤s2:判断所述压力值是否超出预设的压力范围。
65.具体地,控制器接收来自数据采集器30的压力信号,并判断该压力值是否在预定的压力范围内。
66.步骤s3:当所述压力值超出预设的压力范围时,控制所述压膜机100停机。
67.具体地,控制器若判断压力值不在预设的压力范围内,控制压膜机100停机。
68.于一实施例中,步骤s3还包括当所述压力值超出预设的压力范围时,报警单元发出报警提示。
69.该压膜机100的控制方法,可实时监控压膜辊10与基板50接触时的压力值,并进行比较判断该压力值是否出现异常以及时暂停压膜过程,时效性好,进而避免批量性的不良压膜板的产出,降低报废率,提高压膜产品的良品率及生产效率。
70.以上实施方式仅用以说明本发明的技术方案而非限制,尽管参照较佳实施方式对本发明进行了详细说明,本领域的普通技术人员应当理解,可以对本发明的技术方案进行修改或等同替换,而不脱离本发明技术方案的精神和范围。
再多了解一些
本文用于企业家、创业者技术爱好者查询,结果仅供参考。