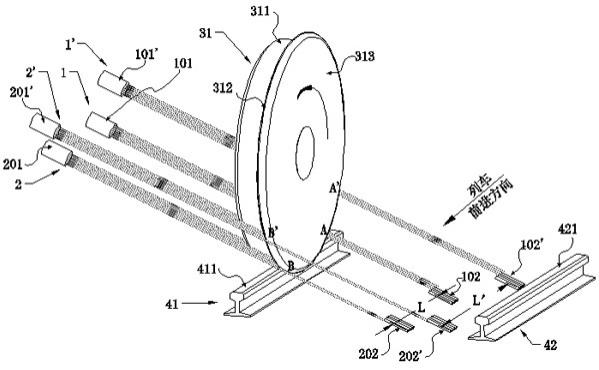
1.本发明属于轨道车辆在线安全运行检测技术领域,特别是一种车轮轮缘顶点圆弦长和直径的在线检测技术。
背景技术:
2.轨道交通在当今世界已经成为主要的运输系统和交通工具,如何保证有轨列车在运行中安全行驶是一个必须面对的重要课题,其中车辆运行状态监测特别是走行部的在线监测是保证列车安全运行的一个主要环节。
3.本发明提供一种车轮轮缘顶点圆弦长和直径的在线检测系统,其目的是让车辆运营单位能够通过本发明获得的检测数据,进一步获知在线列车走行部的重要部件
----
车轮的主要尺寸及其变化,如踏面直径、踏面磨耗程度、不圆度等,为列车运行安全评估以及轮对维修计划提供依据。目前类似的技术有:现有技术1,由广州微予易数据技术有限公司申请的专利文件《基于二维激光位置检测技术的车轮尺寸检测方法和系统》,申请号为 201811486232.7;现有技术2,由南京睿速轨道交通科技有限公司申请的专利文件《一种城轨列车车轮轮缘顶点圆直径的检测方法及其系统》,申请号为201610365665.1;现有技术3,由广州微易轨道交通科技有限公司申请的专利文件《一种检测列车车轮不圆度的方法》,申请号为201910548893.6;现有技术4,由广州市奥特创通测控技术有限公司与余原生申请的专利文件《一种智能车轮在线运动数据采集装置》,申请号为201821002970.5。
4.现有技术1与2公开的技术均是由布局于上宽下窄梯形四个顶点位的四个激光发射装置从轨内侧(轨外侧)向轨外侧(或轨内侧)发出的四道线激光被经过的车轮切割,利用切割车轮轮缘的两条弦长及其该两弦长之间距离推算出轮缘顶点圆直径和其它指标参数;现有技术3公开的技术是利用布置在车轮前进路上以两个线激光为一组的m(m≥2)组检测点测量车轮轮缘m个弦长,来推算同一车轮的m个直径进一步地评价其不圆度,从上述三件现有技术文献中可知,其中所述的轮缘顶点圆弦长测量计算是一个重要的不可少的步骤,而它的测量计算则是由测同一弦长的两个激光发射装置(或接受装置)的安装距离加一个由该两线激光被切割的时间差与车轮通过此处的平均速度的乘积而得,本领域技术人员都知道:列车沿轨道运动时轮轨关系非常复杂,因为车轮锥形踏面与导轨轨顶面滚动接触,其前行过程受迫于诸多因素,轮对在轨道上除了滚动前行还有沿钢轨的蠕滑运动,特别是还存在横移和摇头运动,即车轮在钢轨上具体表现为沿钢轨横向、纵向滑动,虽然这个滑动出现的很短暂,但会使此时的车轮前行的瞬间速度变化很大,致使上述三件现有技术中所计算的平均速度的准确度下降,导致推算的车轮轮缘直径乃至后续的其它尺寸数据出现较大的误差;现有技术4公开的是一种智能车轮在线运动数据采集装置,其技术特征是在单轨一侧由多个沿行车方向平行排列的直射光源向单轨另一侧对准直射光源排布的光纤传感器发射光束,利用车轮依次切割光束时多个光纤传感器接收的时序信号完成判断列车车轮到来位置、到来时刻、测量和计算行驶过程的实时速度以及实时加速度。
技术实现要素:
5.车轮在轨道上行驶过程中其轮缘是不被磨耗和损坏的,轮缘顶点圆在一个轮对镟修周期内是不变的,所以在所有轮对尺寸在线检测中,有关车轮在线检测的项目都以轮缘顶点圆的弦长作为基础数据,它的检测精度会直接影响其它指标的检测精度,为提高列车轮对尺寸在线检测系统的检测精度,克服现有技术1~3的缺陷,本发明解决的技术问题是在与现有技术1~4使用环境不变的条件下,能够对一个个通过的车轮检测出一条或多条或高准确度的车轮轮缘顶点圆弦长,为车轮的主要尺寸计算提供准确的轮缘顶点圆弦长数据。
6.本发明利用光纤直接耦合光源技术,定距测量方法,对现有技术4进行深度创新,在列车运行轨道线上合理布置至少两组光纤传感器组和对应直射光源,能对经过的低、中、高速运动列车的各个车轮轮缘顶点圆弦长进行检测。
7.光纤直接耦合光源,光纤平端面直接对准光源发光面,当某范围波长的光直射光纤的端部时,光纤可以接收到光束并能在光纤里传播,本发明采用的是光纤直接空间耦合光源技术;本发明采用的定距测量方法是指:在一个固定长度一端或两端放置检测游标尺(或检测探头),用于与该固定长度差不多长的多个物体进行测量,物体的一端与固定长度的一端对齐,只进行测量物体的另一端与这个固定长度的另一端的差值就可以完成该物体的测量。
8.本发明首先提供的是一种车轮轮缘顶点圆弦长在线检测系统,然后在该系统基础上增加一组或多组采集信号单元,并合理设置这些采集信号单元的位置,达到对车轮轮缘周向多次或车轮轮缘同时多条的弦长检测,从而完成轮对尺寸的其它指标检测,如车轮的不圆度检测、轮缘顶点圆直径检测等。
9.本发明系统现场的采集信号单元布置均以轨顶平面和轨内侧为基准,所述轨顶平面为两轨道轨顶共面,所述轨内侧是指轨道内道轨向内的一侧在轨平面以下16mm处。
10.所述的一种车轮轮缘顶点圆弦长的在线检测系统,如图1,包含:工控机、显示器、电源模块、智能控制器、至少两组采集信号单元;其中,电源模块负责各设备匹配供电,智能控制器通过信号线连接并接收各组采集信号单元上传的数据信号,数据分析处理后的再通过电缆线上传到工控机,数据以报表或文字或图形的方式在显示器上呈现给用户,其特征在于:所述的各组采集信号单元均由光纤传感器组、光源组组成,所述的光纤传感器组包含单条光纤的单条光纤传感器或包含n(n》1的自然数)条光纤沿车轮行驶方向线性排列形成的光纤阵列传感器,其安装在轨道内道轨内侧轨顶平面下方且接收光束方向对于车轮轮背面垂直向上;所述的光源组至少有一只直射光源,安装在轨道外侧轨顶平面上方且正对所述光纤传感器组发射光束,其发射的光束为平行或接近平行的光束,照射面能覆盖所述光纤传感器组的所有光纤并使各条光纤接收到光束;如图2所述光纤传感器组相对于轨顶平面的安装高度v、仰角α及距道轨内侧的距离u能使得该光纤传感器组的所有光纤接收的光束仅被经过的列车车轮轮缘前弧截断和车轮轮缘后弧还原接通;所述两组采集信号单元沿轨道行车方向以一个设定的距离l且对于轨顶平面不限于等高的平行布置:第一位采集信号单元、第二位采集信号单元,如图1和4所述的距离l可以使得在一定范围内任一直径车轮行驶通过时,所述第一位采集信号单元的所有光纤被车轮阻挡的原接收光束随着该车轮的离开依次全部由该车轮轮缘后弧还原接通所用的时间段与所述第二位采集信号的所有光纤原接收的光束随着该车轮的进入被该车轮轮缘前弧依次全部截断所用的时间段有重合
时间段t
1-t2或重合时刻点t
00
。
11.作为对本发明的优化,如图2,所述第一位采集信号单元的光纤传感器组和第二位采集信号单元的光纤传感器组有相等的所述安装高度v、仰角α及距轨内侧的距离u,且所述第一位采集信号单元与所述第二位采集信号单元的光纤传感器组不同时为单条光纤传感器。
12.利用本发明进行检测,其弦长计算可以是多种方法,对于对本发明的进一步优化,其弦长计算这样进行:所述智能控制器包含有数据处理程序,先对所述系统的每组采集信号单元建立以横轴表示时间纵轴表示距离的时间-距离坐标系,当本组采集信号单元中所述光纤传感器组为光纤阵列传感器时,所述光纤阵列传感器的第一条光纤位置设定为坐标系原点,其余的第二条至第n条光纤按与第一条光纤的距离依次在所述纵轴上标记,进一步地,所述数据处理程序还包含至少记录所有光纤的接收光束被每个车轮轮缘前弧截断和轮缘后弧还原接通的时刻点,并把这些时刻点在所述的横轴上一一对应标记,即在时间-距离坐标系里形成能反映车轮轮缘前弧或后弧通过每条光纤的位移与通过该光纤的时间点一一对应的车轮轮缘前弧或后弧的一个个实时位置坐标点,把单个车轮的轮缘前弧或后弧的实时位置坐标点依次用光滑曲线连起来即形成一条反映该车轮轮缘前弧或后弧向前移动的时间-位移曲线,进一步地,所述的数据处理程序还包含对相邻两个采集信号单元的时间-距离坐标系里的时间-位移曲线进行比较,并找出同一车轮的轮缘前弧和后弧向前移动过程中存在的所述的重合时间段t
1-t2,如图7、13、14在所述的重合时间段t
1-t2中任取一个时刻点ti,以ti为横轴值在相关的两个时间-位移曲线找出时刻ti对应纵轴的距离值s
1i
和s
2i
,再结合所述的距离l计算出这个车轮一条没有速度影响的轮缘前弧到后弧的轮缘顶点圆弦长ab,即:弦长ab=l-s
1i
s
2i
;如图8当本组采集信号单元中所述光纤传感器组为单条光纤传感器时,用车轮轮缘前弧进入或后弧离开而截断或还原接通该单条光纤传感器接收光束的时刻点t
00
在相邻采集信号单元的时间-位移曲线里找出时刻点t
00
对应纵轴的距离值,结合所述的距离l计算出该车轮一条没有速度影响的轮缘顶点圆弦长ab。
13.利用本发明还可以通过如下设置完成对车轮的不圆度检测:如图9,在本发明基础上沿轨道行车方向在所述的第二采集信号单元的前方,以与所述的第一采集信号单元或第二采集信号单元相同的所述安装高度v、仰角α及距轨内侧的距离u、且按所述距离l相等的间距、同向的依次增加布置五组所述采集信号单元:第三位采集信号单元、第四位采集信号单元、第五位采集信号单元、第六位采集信号单元、第七位采集信号单元,利用每相邻两组采集信号单元测量一条轮缘顶点圆弦长,获得车轮滚动一周左右的六条轮缘顶点圆弦长,比较这些弦长,用其差值来判定该车轮踏面圆的不圆度程度。
14.利用本发明还可以通过如下设置完成对车轮的轮缘顶点圆直径检测:如图10,在本发明基础上沿轨道行车方向且在所述第一位采集信号单元和第二位采集信号单元的上方或下方排列的另两组所述采集信号单元:第一副位采集信号单元和第二副位采集信号单元,且:所述的第一位采集信号单元、第二位采集信号单元、第一副位采集信号单元、第二副位采集信号单元等四组采集信号单元的位置按上宽下窄的梯形顶点布置;列车经过时,对于同一车轮,所述第一副位采集信号单元的所有光纤被车轮阻挡的原接收光束随着该车轮的离开依次全部由该车轮轮缘后弧还原接通所用的时间段、所述第二副位采集信号的所有光纤原接收的光束随着该车轮的进入被该车轮轮缘前弧依次全部截断所
用的时间段以及所述的重合时间段t
1-t2三者之间有重合时间段t1’-
t2’
;如图11所述第一位采集信号单元和第二位采集信号单元检测轮缘顶点圆弦长ab的同时,所述第一副位采集信号单元和所述第二副位采集信号单元也检测到同轮的轮缘顶点圆弦长cd,且所述轮缘顶点圆弦长cd与所述轮缘顶点圆弦长ab平行,由弦长ab和cd结合两弦的间距
△
h,根据圆的相关几何关系即可以算出车轮轮缘顶点圆直径。
15.利用本发明还可以通过如下另一种设置完成对车轮的轮缘顶点圆直径检测:在本发明基础上在位于所述第一位采集信号单元或第二位采集信号单元的上方或下方的另一组所述采集信号单元:副位采集信号单元;列车经过时,对于同一车轮,所述副位采集信号单元的所有光纤被车轮阻挡的原接收光束随着该车轮的离开依次全部由该车轮轮缘后弧还原接通所用的时间段,或者是,所述副位采集信号单元的所有光纤原接收的光束随着该车轮的进入被该车轮轮缘前弧依次全部截断所用的时间段、第一位采集信号单元的所有光纤被车轮阻挡的原接收光束随着该车轮的离开依次全部由该车轮轮缘后弧还原接通所用的时间段、第二位采集信号的所有光纤原接收的光束随着该车轮的进入被该车轮轮缘前弧依次全部截断所用的时间段三者之间有重合时间段t1
’-
t2’;这样,如图12,所述第一位采集信号单元和第二位采集信号单元检测轮缘顶点圆弦长ab的同时,所述副位采集信号单元也检测到同轮的轮缘顶点圆上的第三点c’,检测出了轮缘顶点圆的三个点的相对位置,根据不在同一条直线上的三个点确定一个圆的定律,即可以推算出此车轮的轮缘顶点圆直径。
16.在本发明所有方案中,所述采集信号单元中的光纤传感器组和光源组的安装位置可以互换,且不影响检测效果;所述光纤阵列传感器中相邻的光纤间距越小,即本发明系统的检测精度越高。
附图说明
17.图1:系统示意图;图2:采集信号单元安装截面图图3:车轮将进入弦长检测区立体示意图;图4:正在检测弦长立体示意图;图5:被检测到的车轮轮缘弦长示意图;图6:两组光纤传感器组关系示意图一;图7:两组光纤传感器组关系示意图二;图8:两组光纤传感器组关系示意图三;图9:系统检测车轮不圆度示意图;图10:系统检测车轮轮缘顶点圆直径立体示意图;图11:被检测到的车轮轮缘两条弦长示意图;图12:被检测到的车轮轮缘一条弦长和第三点示意图;图13:时间-位移曲线比较图一;图14:时间-位移曲线比较图二;图15:系统检测车轮轮缘顶点圆直径示意图。
18.其中:1-第一位采集信号单元, 2-第二位采集信号单元, 3-第三位采集信号单
元,4-第四位采集信号单元
…
,101-第一位采集信号单元的光源组,102-第一位采集信号单元的光纤传感器组,103-第一位采集信号单元的光束,201-第二位采集信号单元的光源组,202-第二位采集信号单元的光纤传感器组,203-第二位采集信号单元的光束,31-车轮,311-车轮踏面,312-轮缘顶点圆,313-车轮轮背面,41-道轨,411-轨顶,42-另一道轨,421-另一轨轨顶,1021-第一位采集信号单元的光纤阵列传感器中第一条光纤,1022-第一位采集信号单元的光纤阵列传感器中第二条光纤,以此类推,2021-第二位采集信号单元的光纤阵列传感器中第一条光纤,2022-第二位采集信号单元的光纤阵列传感器中第二条光纤,依次类推,1
’-
第一副位采集信号单元,2
’-
第二副位采集信号单元,101
’-
第一副位采集信号单元的光源组,102
’-
第一副位采集信号单元的光纤传感器组,103
’-
第一副位采集信号单元的光束,201
’-
第二副位采集信号单元的光源组,202
’-
第二副位采集信号单元的光纤传感器组,203
’-
第二副位采集信号单元的光束。
具体实施方式
19.以下列举五个实施例进行进一步地说明,所列举的实施例并不限定本发明的其它实施方式。
20.实施例一,一种车轮轮缘顶点圆弦长的在线检测系统,如图1,包含:工控机、显示器、电源模块、智能控制器、以及沿轨道行车方向排列的两组采集信号单元:第一位采集信号单元1和第二位采集信号单元2;其中,电源模块负责各设备匹配供电,智能控制器通过信号线连接并接收各组采集信号单元上传的数据信号,数据分析处理后的再通过电缆线上传到工控机,数据以报表或文字或图形的方式在显示器上呈现给用户;如图3、4所述的采集信号单元1由光纤传感器组102、光源组组101成,所述的采集信号单元2由光纤传感器组202、光源组组201成,如图7所述的光纤传感器组102是由4条光纤1021、1022、1023、1024沿车轮行驶方向依次线性排列形成的光纤阵列传感器,所述的光纤传感器组202是4条光纤2021、2022、2023、2024沿车轮行驶方向依次线性排列形成的光纤阵列传感器,两者安装距离l,均安装在轨道内道轨41内侧轨顶平面411下方且接收光束方向对于车轮31轮背面313垂直向上;所述的光源组101或201至少有一只直射光源,安装在轨道外道轨41外侧轨顶平面411上方且正对所述光纤传感器组102或202,其发射的光束103或203为平行或接近平行的光束,照射面覆盖所述的光纤传感器组102并能使4条正对的光纤1021、1022、1023、1024接收到光束;如图2所述光纤传感器组102或202距轨顶平面41的安装高度v、关于轨顶平面41的仰角α及距道轨41内侧的距离u均一致,并且能使得在列车通过时,光纤传感器组102或202接收的光束103或203仅是被列车的车轮31截断或还原接通而不受其它部件影响,如图4即所述光束203中被光纤接收的光束随车轮31进入被截断时与所述轮缘顶点圆312相交于b点,所述光束103中被光纤接收的光束随车轮31离开被还原接通时与所述轮缘顶点圆312相交于a点;根据列车实际情况,本实施实例设定对轨顶平面411下6mm~轨顶平面上90mm范围的平行于轨顶平面411的轮缘顶点圆312的弦长进行检测,即图5中的h为-6mm~90mm,如下设计可以使得所述a点通过第一位采集信号单元1的所有光纤时所用的时间段与所述b点通过所述所第二位采集信号单元2的所有光纤用的时间段有重合时间段t
1-t2:针对车轮31踏面311直径为760mm~840mm的车轮31轮缘顶点圆312弦长ab检测,所述采集信号单元1和2之间的距离l设计为352.0mm~613.0mm的某一值,针对车轮31踏面311直径为1150mm~1250mm的机车车轮
轮缘顶点圆312弦长ab检测,所述距离l设计为428.5mm~758.5mm中的某一值;所述光纤传感器组102、202中光纤阵列传感器里各相邻光纤间距相等且均设计为10.00~12.00mm或12.00mm~13.00mm或13.00mm~15mm的某一值。
21.本系统包含有数据处理程序,如图7、12、13所示,对所述采集信号单元1建立以横轴表示时间纵轴表示距离的时间-距离坐标系,其中,所述光纤传感器组102的第一条光纤1021位置设定为坐标系原点,其余的光纤1022、1023、1024按与第一条光纤1021的距离s11、s12、s13、s14依次在所述纵轴上标记,也对所述采集信号单元2建立以横轴表示时间纵轴表示距离的时间-距离坐标系,其中,所述光纤传感器组202的第一条光纤2021位置设定为坐标系原点,其余的光纤2022、2023、2024按与第一条光纤2021的距离s21、s22、s23、s24依次在所述纵轴上标记,系统运行后,所述系统数据处理程序至少记录所述光纤2021、2022、2023、2024接收的光束被车轮31轮缘前弧截断的时刻点t21、t22、t23、t24,即所述b点经过所述光纤2021、2022、2023、2024的时刻点,以及,所述光纤1021、1022、1023、1024接收的光束被车轮31轮缘后弧还原接通的时刻点t11、t12、t13、t14,即所述a点经过所述光纤1021、1022、1023、1024的时刻点;并把这些时刻点对应的赋予各自坐标系的时间轴上,即形成车轮31通过所述光纤传感器组202时所述轮缘前弧b点的位移与时间曲线s
t2
和车轮31通过所述光纤传感器组102时所述轮缘后弧a点的位移与时间曲线s
t1
,进一步地,对所述位移曲线s
t1
和s
t2
进行比较,找出同一车轮31的轮缘b点和a点向前移动过程中存在的所述的重合时间段t
1-t2,在所述的重合时间段t
1-t2中任取一个时刻点ti,以ti为横轴值在所述的时间-位移曲线s
t1
和s
t2
中找出时刻ti对应纵轴的距离值s
1i
和s
2i
,那么,该车轮31的轮缘顶点圆312所述的弦长ab=所述距离l s
2i
-ꢀs1i
。
22.实施例二,一种车轮轮缘顶点圆弦长的在线检测系统,如图8所示,在实施例1基础上把所述的光纤传感器组202的光纤阵列传感器改变为单条光纤传感器2021,那么与实施例1不同的是:所述距离l定义为所述光纤1021与单条光纤2021之间的距离;所述光纤2021接收的光束被车轮31轮缘前弧截断的时刻只有一个时刻点t
00
,通过如下设计使得所述时刻点t
00
处于所述的时刻点t11和t14范围之内:所述光纤传感器组102里各相邻光纤间距相等且为20.00mm~22.00mm的某一值,所述的距离l设计为382.0mm~643.0mm某一值时用于车轮31踏面311直径为760mm~840mm的、距轨顶平面-6mm~90mm范围的轮缘顶点圆弦长ab检测,所述的距离l设计为458.5mm~788.5mm某一值时用于车轮31踏面311直径为1150mm~1250mm的机车车轮且距轨顶平面-6mm~90mm范围的轮缘顶点圆弦长ab检测。用时刻点t
00
在所述的位移与时间曲线s
t1
上找出对于的s
1i
,那么,该车轮31的轮缘顶点圆312所述弦长ab=所述距离l
ꢀ-ꢀs1i
。
23.实施例三,一种车轮轮缘顶点圆弦长的在线检测系统,用于评价车轮31踏面311不圆度的设计,其特征是:如图9,在实施例1或2基础上沿轨道行车方向在所述的第二采集信号单元的前方,以与所述的第一采集信号单元或第二采集信号单元相同的所述安装高度v、仰角α及距轨内侧的距离u、且按所述距离l相等的间距、同向的依次增加布置五组所述采集信号单元:第三位采集信号单元、第四位采集信号单元、第五位采集信号单元、第六位采集信号单元、第七位采集信号单元,那么,每相邻两组采集信号单元会测量一条轮缘顶点圆弦长,即所述采集信号单元1和2检测弦长ab、所述采集信号单元2和3检测弦长bc、所述采集信号单元3和4检测弦长cd、所述采集信号单元4和5检测弦长cd,依次类推获得车轮滚动一周
左右的六条轮缘顶点圆弦长,比较这些弦长,用其差值来判定该车轮踏面圆的不圆度程度;对于同一个车轮,轮缘顶点圆与踏面圆是同心的,而且顶点圆在行驶中不被磨耗与损坏,其直径2r在轮对镟修周期内是一不变量,如图5所示,在保证所述光纤传感器组与道轨相对位置不变情况下,如果对于同一车轮本系统能测出不同的弦长,则反映该弦长在轮缘顶点圆的弦中心距h发生了变化,也就是该弦长在轨顶平面的高度h有了差异,此处踏面圆不圆所致。
24.实施例四,一种车轮轮缘顶点圆直径的在线检测系统,如图10,15所示,在实施实例1所述的一种车轮轮缘顶点圆弦长的在线检测系统基础上,增加两组所述的采集信号单元:第一副位采集信号单元1’和第二副位采集信号单元2’,所述第一副位采集信号单元1’位于所述第一位采集信号单元1的上方,所述第二副位采集信号单元2’位于第二位采集信号单元2的上方,且:所述的第一位采集信号单元1、第二位采集信号单元2、第一副位采集信号单元1’、第二副位采集信号单元2’等四组采集信号单元的光纤传感器组均不为单条光纤传感器且其位置投影到车轮轮背面上看是按上宽下窄的梯形顶点布置,安装仰角相同都为α。列车经过时,对于同一车轮,所述第一副位采集信号单元1’的光纤传感器组102
’ꢀ
所有光纤被车轮31阻挡的原接收光束随着该车轮的离开依次全部由该车轮轮缘后弧还原接通所用的时间段、所述第二副位采集信号2’的光纤传感器组202’的所有光纤原接收的光束随着该车轮的进入被该车轮轮缘前弧依次全部截断所用的时间段以及实施实例1所述的重合时间段t
1-t2三者之间有重合时间段t1’-
t2’
,如图10、11,所述第一位采集信号单,1和第二位采集信号单元2检测轮缘顶点圆弦长ab的同时,所述第一副位采集信号单元1’和所述第二副位采集信号单元2’根据距离l’和检测到的点a’和b’的位移也检测到同轮的轮缘顶点圆弦长a’b’,且所述轮缘顶点圆弦长a’b’与所述轮缘顶点圆弦长ab平行,由弦长ab和a’b’结合两弦的间距
△
h,根据圆的相关几何关系即可以算出车轮轮缘顶点圆直径2r;如图15,所述两弦的间距
△
h =(u’*tanα-v’)-(u*tanα-v)。
25.实施例五,一种车轮轮缘顶点圆直径的在线检测系统,本实施例是在实施例四基础上去掉所述第二副位采集信号单元2’,只用所述采集信号单元1、2、1’完成车轮31的顶点圆312直径检测,那么如图12,本实施例测得所述顶点圆312的不在同一直线上的三个点a、b、c’,因为所述采集信号单元1、2、1’之间安装距离已知,则:所述c’点与所述a点的竖向距离
△
h为已知,而所述c’点与所述a点的水平距离c由采集信号单元1、1’测得,这样所述三个点a、b、c’的位置被确定,从而推算出对应的唯一几何圆。
再多了解一些
本文用于企业家、创业者技术爱好者查询,结果仅供参考。