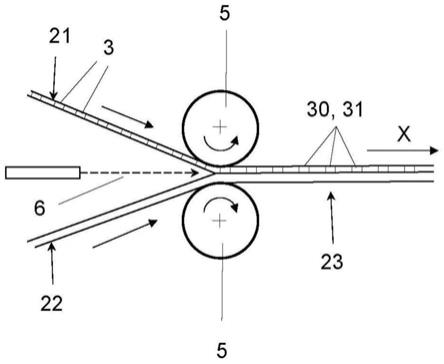
1.本发明涉及一种具有润滑凹穴的滑动元件的制造方法。
背景技术:
2.在运行表面上具有润滑凹穴的滑动元件用于在轴承表面上具有特别高负载的应用中。润滑凹穴可形成为运行表面中的凹槽或在滑动元件的整体厚度上延伸的小孔。穿孔衬套为这种滑动元件的一种示例。
3.某些铜合金具有优良的滑动性能,并且因此适合用作滑动轴承的运行表面材料。由于铜的金属价格高,由这些材料制成的单金属滑动轴承很昂贵。因此,通常使用复合材料,其中一种由铜材料构成的薄覆盖层施加到钢背。钢背具有明显大于该覆盖层的厚度。在运行中,钢背吸收了径向力,并且确保了轴承的机械稳定性。在滑动轴承的运行表面上由铜材料构成的覆盖层赋予轴承优异的滑动性能。对于这种复合材料的制造,已知多种方法,例如将铜材料熔化到钢背或包覆上。由这种复合材料构成的滑动轴承的运行表面可具有润滑凹穴。
4.文献de 10 2008 003 730 a1描述了这种两层的滑动元件,在这种情况下,第一层具有连续的小孔。这些小孔用作润滑容器。
5.文献us 6 095 690 a提出通过对双金属带材料的单面压纹在金属复合材料中引入润滑凹穴。从文献gb 1 454 385 a知晓了相同的方法。压纹过程中变形的材料仍保留在滑动元件中,并且无法回收。
6.作为替代方案,可以通过在复合材料中冲出小孔来制造润滑凹穴。然而,由此产生的冲孔余料不是一种类型,并且因此仅用相当大的努力才可回收。文献de 203 00 854 u1中公开了一种可通过这种方法制造的滑动轴承衬套。
技术实现要素:
7.本发明的目的是指定一种用于制造具有润滑凹穴的廉价滑动元件的经济方法。
8.本发明由权利要求1的特征限定。进一步的从属权利要求涉及本发明的有利实施例和发展。
9.本发明包括一种滑动元件的制造方法,其中,所述方法包括以下步骤:
10.a)提供具有厚度d1的第一带形或条形金属材料,其中,第一材料具有在第一材料的整个厚度d1上延伸的小孔,
11.b)提供具有厚度d2的第二带形或条形金属材料,
12.c)通过激光轧制包覆将第一带形或条形材料平面地连接到第二带形或条形材料,使得形成带形或条形复合材料,其具有纵向方向x和横向方向y,所述横向方向y相对于纵向方向x横向地定向,并且具有相对于纵向方向和横向方向垂直的厚度d,
13.d)环绕轴线a使所述复合材料弯曲,所述轴线平行于复合材料的横向方向y定向,使得形成弯曲的滑动元件,并且所述滑动元件在其运行表面上具有至少局部地由第一材料
的小孔形成的切口。
14.本发明涉及一种滑动元件的制造方法,所述滑动元件具有可用作润滑凹穴的切口。在该方法中,提供了第一带形或条形金属材料。第一材料具有宽度b1和厚度d1。厚度d1小于宽度b1。作为条形材料,所述第一材料具有限定的长度。作为带形材料,所述第一材料具有未限定的长度。第一材料可由轴承材料构成,特别地铜或铝合金。第一材料具有多个小孔,与穿孔板的情况一样,这些小孔在材料的整个厚度上延伸。第一材料因此被穿孔。
15.此外,提供了第二带形或条形金属材料。第二材料具有宽度b2和厚度d2。厚度d2小于宽度b2。作为条形材料,所述第二材料具有限定的长度。作为带形材料,所述第二材料具有未限定的长度。第二材料通常不同于第一材料。有利地选择具有高强度的有利材料用于第二材料。第二材料可特定地包括钢。第二金属材料的厚度d2优选地大于第一金属材料的厚度d1。第二材料的厚度d2特别优选地为第一材料的厚度d1的至少三倍。因此可以很经济地制造厚壁的滑动元件。
16.第一和第二材料通过激光轧制包覆彼此连接,使得形成一种带形或条形复合材料。在激光轧制包覆中,两种带形或条形材料在轧制支架的上游以平面的方式放置在一起,并且在进入轧制工具之前直接地通过激光辐射加热。由于加热,这两种材料之间的快速金属间扩散在轧制过程中发生,使得即使在轧制过程中变形程度很低的情况下,也制造了固体金属复合材料。可在文献de 44 29 913c1的教导基础上进行激光轧制包覆。
17.由此形成的复合材料具有纵向方向x和横向方向y。具有限定长度的条形复合材料由条形第一材料和条形第二材料制成。作为替代方案,带形复合材料由带形第一材料和带形第二材料制成。随后带形复合材料被切割成有限长度。由于在激光轧制包覆工艺中所需的变形程度很低,复合材料的厚度d仅略小于两种起始材料的厚度d1和d2之和。
18.通过绕平行于复合材料的横向方向定向的轴线使复合材料弯曲,由带形或条形复合材料制成了滑动元件。滑动元件具有外表面和内表面,其中之一作为运行表面。第一材料的小孔在复合材料的一侧上形成切口。因此,滑动轴承的运行表面具有至少局部地由第一材料的小孔形成的切口。这些切口可用作润滑凹穴。
19.该方法的特别优点在于,由于激光轧制包覆工艺中的低变形程度,起始材料的相应厚度几乎没有任何减少,并且第二材料的材料并没有被推入第一材料的小孔中,或在包覆工艺中仅被推到微不足道的程度。因此,就其原始形状和深度而言,第一材料的小孔基本保持不变。在需要更大变形程度的包覆方法中,情况并非如此。此外,可以通过第一材料的厚度d1调节由小孔形成的切口的深度。由于在激光轧制包覆的情况下,可以在很大范围内选择起始材料的厚度,因此可以制造一种复合材料,其具有实际上任何所需深度的润滑凹穴。
20.这种方法的进一步优点是,在包覆操作之前引入小孔,并且因此引入到单金属材料。由此产生的材料废料为一种类型,并且可在废料循环中容易回收。
21.在该方法的特定实施例中,第一材料的小孔可在两种材料的边界表面处由第二材料封闭。在这种情况下,在包覆工艺之后,所述小孔形成诸多在一侧敞开并且其呈现凹穴形式的切口,所述凹穴的深度仅在第一材料的厚度上延伸。
22.特别地,该复合材料可弯曲以形成衬套,即套筒形主体。在这种情况下,进行弯曲,使得复合材料的两端放置在一起,其中,形成了平行于弯曲轴线行进的对接接头。作为替代
方案,可使带形或条形复合材料弯曲以形成半壳,其围住约180
°
的角度。
23.优选地,进行弯曲,使得第一金属材料定位在滑动元件面对弯曲轴线a的表面上,即在衬套或半壳的内侧上。然后,衬套的内侧用作滑动元件的运行表面。
24.在本发明的优选地改进方案中,可以通过全平面的方式实现步骤c)中第一材料与第二材料的连接。为此,第一材料的宽度b1必须等于第二材料的宽度b2。因此形成的复合材料具有均匀的宽度b。最佳地利用了滑动元件的可用安装空间。
25.有利地,切口可以填充有润滑剂,特别地固体润滑剂。润滑剂改进了轴承的滑动性能。如果切口构造呈现凹穴的形式,所述切口在一侧上敞开并且其深度仅在第一材料的厚度d1上延伸,与具有在复合材料的整个厚度d上延伸的小孔的滑动元件的情况相比,填充切口需要明显更少的润滑剂。
26.在该方法的特定实施例的上下文中,第二材料可具有在第二材料的整个厚度上延伸的小孔。第二材料的切口导致明显地节省材料,以及因此降低滑动元件的重量。第二材料的切口可以在形状和尺寸方面与第一材料的切口等同,或者在形状和/或尺寸方面与第一材料的切口不同。
27.在本实施例的特定改进的上下文中,第一材料可连接到第二材料,使得第二材料的小孔与第一材料的小孔重合。在某种程度上,第一材料和第二材料的小孔一个放置在另一个上。换句话说,它们对准了。切口然后在复合材料的整个厚度d上延伸。由这种复合材料制成的滑动元件具有最大体积的润滑凹穴。
28.在本实施例的进一步具体改进的上下文中,第一材料可以连接到第二材料,使得第二材料的小孔相对于第一材料的小孔偏移地布置。然后,第一材料的小孔在两种材料的边界表面处由第二材料封闭。在这种情况下,在包覆工艺之后,第一材料的小孔形成切口,所述切口在一侧上敞开并且呈现凹穴的形式,其深度仅在第一材料的厚度d1上延伸。由这种复合材料制成的滑动元件具有最大的稳定性和很低的重量。特别地在本发明实施例的这种具体改进中,第二材料的切口可以在形状和/或尺寸方面与第一材料的切口不同。
29.关于第一材料的小孔相对于第二材料的小孔的定位,可以考虑在上述的两种特定改进之间的每种变型。特别地,可以连接这两种材料,使得第一材料的小孔与第二材料的小孔局部地重叠。
附图说明
30.关于根据本发明的方法的进一步技术特征和优点,在此明确地参考示例性实施例、附图,以及结合附图和示例性实施例的描述的解释。
31.参考附图的示意图更详细地解释了本发明的示例性实施例,
32.其中:
33.图1示出了具有小孔的第一材料,
34.图2示出了第二材料,
35.图3示意性地示出了激光轧制包覆工艺,
36.图4示出了复合材料,
37.图5示出了一种带有润滑凹穴的衬套,
38.图6示出了一种带有润滑凹穴的半壳,
39.图7示出了复合材料的一种特定实施例,
40.图8示出了复合材料的又一特定实施例,在所有附图中,相互对应的部件具有相同的附图标记。
41.附图标记列表
42.1 滑动元件
43.11 衬套
44.12 对接接头
45.13 半壳
46.14 运行表面
47.21 第一材料
48.22 第二材料
49.23 复合材料
50.3 小孔
51.30 切口
52.31 凹穴
53.4 小孔
54.5 轧制工具
55.6 激光束
56.a 轴线
57.b 宽度
58.d 厚度
59.x 纵向方向
60.y 横向方向
具体实施方式
61.图1示出了呈现具有宽度b1和厚度d1的带材料形式的第一材料21。该带形材料沿x方向在未限定的长度上延伸。沿y方向测量了宽度b1。沿垂直于x和y的方向测量了厚度d1。该材料具有多个小孔3。小孔3可具有如图示情况的圆形。其他形状,例如卵形、椭圆形、三角形或矩形也是可能的。
62.图2示出了呈现具有宽度b2和厚度d2的带材料形式的第二材料22。该带形材料沿x方向在未限定的长度上延伸。沿y方向测量了宽度b2。沿垂直于x和y的方向测量了厚度d2。在所示的情况下,第二材料22具体化为固体材料并且具有平面表面。不存在小孔或任何其他结构元件。
63.图3示意性地示出了激光轧制包覆工艺。工作方向从左到右。具有如图1所示的小孔3的第一材料21以实际上无限的带的形式进给到轧制设备,仅示出了所述轧制设备的两个相对旋转的轧制工具5。如图2所示的第二材料22也以实际上无限的带的形式进给到轧制设备。进给了这两种材料21、22,使得它们在轧制工具5的上游区域彼此平面的接触。直接在两种材料21、22进入轧制工具5的工作区域之前,两种材料21、22都通过激光束6加热。由于以这种方式实现的材料21、22的温度很高,在这两种材料21、22之间的快速金属间扩散在包
覆工艺期间发生。因此,在包覆工艺期间,为了在两种材料21、22之间获得足够牢固的材料接合连接,仅需要非常低的变形程度。由此制造的带形复合材料23因此在其一个表面上具有呈现凹穴31形式的切口30,所述切口在一侧上敞开,并且与第一材料21的小孔3相对应。
64.图4示出了制成的复合材料23。它由第一材料21和第二材料22构成。复合材料23的宽度b等于第一材料21的宽度b1,以及与其相等的第二材料22的宽度b2。复合材料的厚度d大致等于第一材料21的厚度d1和第二材料22的厚度d2之和。复合材料23在由第一材料21形成的表面上具有呈现凹穴31形式的多个切口30,所述切口在一侧上敞开。所述切口由第一材料21的小孔3制成,因为小孔3已经在一侧上被第二材料22封闭。
65.图5示出了一种呈现轧制衬套11形式的滑动元件1。为了制造衬套11,如图4所示的复合材料23已切割成与衬套11的外围对应的长度,并绕轴线a弯曲实际上360
°
。在复合材料23的两端之间保留很小的对接接头12。衬套11具有由第一材料21形成的作为运行表面14的内表面,以及由第二材料22形成的外表面。因此,运行表面14具有可填充有固体润滑剂的凹穴31。作为替代方案,复合材料23也可以弯曲,使得外表面由第一材料21形成,并且因此具有润滑凹穴31。
66.图6示出了呈现半壳13形式的滑动元件1。为了制造该半壳13,如图4所示的复合材料23已切割成与半壳13的外围对应的长度,并且已经绕轴线a弯曲了实际上180
°
。半壳13具有由第一材料21形成的作为运行表面14的内表面,以及由第二材料22形成的外表面。运行表面14因此具有可填充有固体润滑剂的凹穴31。作为替代方案,复合材料23也可以弯曲,使得外表面由第一材料21形成,并且因此具有润滑凹穴31。
67.图7示意性地示出了复合材料23的特定实施例的侧视图。不仅第一材料21具有小孔,而且第二材料22还具有小孔4,所述小孔4具有与第一材料的小孔3相同的形状和尺寸。第一材料21已经连接到第二材料22,使得第二材料22的小孔4与第一材料的小孔3重合。以这种方式,形成了切口30,所述切口以不变的形状和尺寸在复合材料23的整个厚度上延伸。作为润滑剂容器,这些切口30具有润滑剂的最大体积。
68.图8示意性地示出了复合材料23的又一特定实施例的侧视图。不仅第一材料21具有小孔,而且第二材料22也具有小孔4。第一材料21已经连接到第二材料22,使得第二材料22的小孔4相对于第一材料21的小孔3偏移地布置。与如图4所示的复合材料23的情况一样,第一材料21的小孔3在两种材料21、22的边界表面处由第二材料22封闭,使得在一侧上敞开的呈现凹穴31形式的切口30在由第一材料21形成的复合材料23的表面中形成。
再多了解一些
本文用于企业家、创业者技术爱好者查询,结果仅供参考。