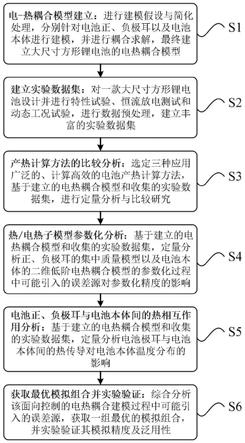
1.本发明属于电池技术领域,涉及一种方形锂电池电热耦合建模误差源分析方法。
背景技术:
2.准确且计算高效的电热耦合模拟对于电动车辆和智能电网储能系统的热安全和性能管理至关重要。电池的热过程通常包括产热、散热和热累积,现在已报道了很多电池系统的电热耦合模型。根据应用场景,电热耦合模型可分为面向控制的模型和面向设计的模型。其中,面向控制的模型由于能够在预测精度、计算复杂性和参数化难度之间取得良好折衷,已广泛应用于在线系统。但在模型假设和简化过程中,不可避免地会从数据采集、产热计算和传热模拟三个方面引入建模误差。
3.电池的电热耦合模拟通常需要采集电流、电压和温度在内的实验数据。众所周知,相比电流和电压数据,温度测量序列具有较大的测量噪声。评估不同程度的测量噪声对面向控制电热耦合模型的预测精度的影响显得很有必要。
4.面向控制的电热耦合模型的热源项通常由典型的bernardi产热公式计算。研究表明,如果电池因活性材料相变和电化学反应中锂离子浓度梯度引起的热效应不用考虑,那该模拟方法能够取得让人满意的精度。这个简化的产热模型包含不可逆热和可逆热两部分。其中,不可逆热的计算方式有两种:基于过电势的方法和基于等效内阻的方法。电池的等效内阻又可以通过几种典型的方法获得,例如,通过欧姆定律直接计算和基于等效电路模型的参数辨识获得。显然,这样就会组合出多种产热计算方法。虽然这些方法都足够计算高效,但是目前缺乏相关的比较研究,无法针对特定的电热模拟给出一种合适的产热计算方法。对于可逆热的计算,一般情况下它占总发热量的比重很小,并且只要提前获得熵热系数与荷电状态soc之间的函数关系,即通过插值或拟合技术进行计算。
5.电池的传热包括电池内部的热传导以及电池与外部环境之间的热交换(包括热对流和热辐射)。根据电池的产热假设,面向控制的电热模型可分为集中式产热模型和分布式产热模型。集中式产热模型,也称为热等效回路模型,类似于基于基尔霍夫定律推导的等效电路模型。虽然这些模型仅能获取单个位置的温度信息,但是它们计算高效且预测精度较高,目前已广泛用于各种几何形状电池系统的在线温度监测。对于分布式产热模型,它们通常由需要满足特定传热边界的能量守恒方程表示,可使用多种降阶技术进行求解,如多项式近似、二次假设、积分法近似、伽辽金近似和有限差分法等。与集中式产热模型相比,该类模型在增加少量计算成本的情况下能够获得更高的预测精度,并且能够获取详细的温度分布,从而实现更有效的电池热管理。对于上述传热模型,尽管它们的模型假设和简化各不相同,但它们都需要对模型进行参数化以确定未知参数。然而,目前鲜有研究报道分析影响模型参数化精度的可能因素。例如,如何优化温度传感器的布置方案以最小化模型参数化的误差,以及如何考虑电流倍率、外部冷却环境、工作温度和加载工况对模型参数的影响,都需要进一步研究。特别是对于方形电池,至少需要二维电热模型才能够准确捕捉电池的热动力学,这更凸显出温度传感器布置优化的重要意义。此外,若要建立准确的电热耦合模
型,还需要仔细考虑电池正、负极耳与电池本体间的热相互作用对大尺寸电池本体温度分布的影响。
6.基于此,本发明旨在通过详细分析面向控制的电热耦合模拟过程中可能出现的各种误差源,结合定量评估和纵横向对比分析,给出一组最优的模拟组合,实现大尺寸方形电池面向控制的电热耦合模拟在预测精度、计算复杂度和模型适用性多个方面的最佳折中。本发明的技术方案能够在很大程度上解决目前研究方案的遗留问题,为更准确、更实用的电热耦合模拟提供参考。
技术实现要素:
7.有鉴于此,本发明的目的在于提供一种方形锂电池电热耦合建模误差源分析方法。
8.为达到上述目的,本发明提供如下技术方案:
9.一种方形锂电池电热耦合建模误差源分析方法,该方法包括以下步骤:
10.s1:对大尺寸方形电池的产热、传热过程进行必要的建模假设及简化处理,针对电池的正、负极耳以及电池本体单独建模,建立面向控制的电热耦合模型;
11.s2:选择一款大尺寸方形锂电池,开展实验设计、进行实验并对电池数据进行必要的预处理,建立电池的特性试验、恒流工况以及动态工况数据集;
12.s3:综述现阶段计算高效的产热计算方法,选择应用广泛的产热计算方法作为分析对象,基于建立的电热耦合模型及收集的实验数据集,开展定量分析与比较研究;
13.s4:参数化电热耦合模型中的各热/电热子模型,定量分析其中可能引入的误差源;
14.s5:研究电池极耳与电池本体间的热相互作用,定量分析电池极耳与电池本体间的热传导对电池本体温度分布的影响;
15.s6:综合分析该面向控制的电热耦合建模过程中可能引入的误差源,获取一组最优的模拟组合,并实验验证其模拟精度及泛用性。
16.可选的,所述步骤s1中,针对电池的正、负极耳,考虑到极耳的材料特性以及较小的几何尺寸,建立集中质量模型来描述该区域的热行为;针对电池本体,建立一个二维低阶电热模型来描述该区域的热行为;针对电池本体与正、负极耳间的热相互作用,建立经验的传热模型来描述。
17.可选的,所述步骤s2中,设计及实施的实验包括电池的特性试验、恒流放电试验和动态工况试验,其中特性试验包括电池在不同温度下的静态容量测试和混合脉冲功率特性试验hppc,恒流放电测试包括不同倍率下的恒流放电测试,动态工况试验包括不同温度下的联邦城市行驶工况fuds和新标欧洲循环测试工况nedc。另外,对电池数据的预处理主要包括剔除异常数据、补充缺失数据和数据降噪,建立的实验数据集包括电流、电压和各测量点的温度数据。
18.可选的,所述步骤s3中,目前被广泛使用的产热计算方法有三种:基于过电势的方法和基于等效内阻的方法,其中基于等效内阻的方法根据等效内阻的获得方式又可分为电压差分法和基于等效电路模型的参数辨识法。
19.可选的,所述步骤s4中,电热耦合模型中各热/电热子模型的参数化是指正、负极
耳的集中质量热模型的参数化和电池本体的二维低阶电热耦合模型的参数化。在集中质量热模型的参数化过程中,考虑电池工作温度、外部冷却条件、电流倍率和加载工况对模型参数的影响;在二维低阶电热耦合模型的参数化过程中,重点考虑温度测点组合对模型参数化精度的影响。
20.可选的,所述步骤s5中,通过评估考虑和不考虑电池正、负极耳与电池本体间的热相互作用这两种情况下电热耦合模型的预测精度来定量分析电池极耳与电池本体间的热传导对电池本体温度分布的影响。
21.可选的,所述步骤s6中,以相对均方根误差rrmse作为评价指标,重点考虑电池的最高温度和最大温差的预测精度,综合分析面向控制的电热耦合模拟过程中所有可能的误差源,获取一组最优的模拟组合,然后在不同的工况场景下验证该最优模拟组合的预测精度及泛用性。
22.可选的,对于正、负极耳的集中质量热模型,其产热项仅用考虑欧姆产热;对于电池本体的二维低阶电热模型,其产热项基于典型的bernardi产热公式进行计算,考虑电池本体的产热包括可逆热和不可逆热。另外,对于电池本体的传热行为,使用二维能量守恒方程来描述,并利用切比雪夫
‑
伽辽金近似方法实现该二维偏微分方程的模型降阶,将其转化为若干常微分方程进行求解。对于正、负极耳与电池本体间的热流交换,使用一个经验的热传导方程来模拟,且需要将热流交换量按照热流传导距离合理地分配到每个离散单元。因为根据本发明的模型降阶方法,电池本体会被离散为若干单元。
23.可选的,在进行三种产热计算方法的模拟精度比较时,难以利用实验方法直接准确测取电池的产热量,导致直接比较产热计算方法时缺乏参考标准。为了解决该问题,本发明选择避开产热计算方法的直接比较,而是通过综合考虑产热计算方法以及其他影响电池电热耦合建模的因素,以最终模型的预测精度来间接评价这三种产热计算方法。该思路虽然无法准确知道哪种产热计算方法最能准确描述电池的真实产热,但是能够确定哪种产热计算方法最适用于当前的电热耦合模拟。
24.本发明的有益效果在于:
25.(1)针对大尺寸方形电池,本发明能够详细全面地分析面向控制的电热耦合模型在数据采集、产热计算和传热模拟阶段可能引入的误差源,通过定量评估和比较分析能够为电池系统提供一套最优的模拟组合,实现大尺寸方形电池面向控制的电热耦合模拟在预测精度、计算复杂度和模型适用性多个方面的最佳折中;
26.(2)本发明给出一套通用的针对大尺寸方形电池的计算高效电热耦合模拟的误差源分析框架,能够适用于各种电化学体系的软包电池和薄方型电池,也可以相似的思路应用于圆柱型电池面向控制的电热耦合建模过程中的误差源分析;
27.(3)无法准确测取电池在各种测试工况下的产热量,容易导致在进行产热计算方法的直接比较时缺乏参考值,但本发明巧妙地避开了产热计算精度的直接对比,而是通过综合考虑产热计算方法以及其他影响电池电热耦合建模的因素,以最终模型的预测精度来间接评价这三种产热计算方法。该思路能够确定哪种产热计算方法最适用于当前的电热耦合模拟。
28.本发明的其他优点、目标和特征在某种程度上将在随后的说明书中进行阐述,并且在某种程度上,基于对下文的考察研究对本领域技术人员而言将是显而易见的,或者可
以从本发明的实践中得到教导。本发明的目标和其他优点可以通过下面的说明书来实现和获得。
附图说明
29.为了使本发明的目的、技术方案和优点更加清楚,下面将结合附图对本发明作优选的详细描述,其中:
30.图1为本发明的总体流程图;
31.图2为本发明中大尺寸方形电池的散热条件以及温度传感器布置示意图;
32.图3为本发明中针对大尺寸方形电池的电热耦合模拟简图;
33.图4为本发明中电池正、负极耳与电池本体间热流交换的分配规则简图;
34.图5为本发明中切比雪夫
‑
伽辽金近似方法实现热能守恒方程模型降阶的流程图;
35.图6为本发明的实验设计说明图;
36.图7为本发明中一大尺寸方形电池计算高效的电热耦合模拟过程中可能出现的误差源分析框架。
具体实施方式
37.以下通过特定的具体实例说明本发明的实施方式,本领域技术人员可由本说明书所揭露的内容轻易地了解本发明的其他优点与功效。本发明还可以通过另外不同的具体实施方式加以实施或应用,本说明书中的各项细节也可以基于不同观点与应用,在没有背离本发明的精神下进行各种修饰或改变。需要说明的是,以下实施例中所提供的图示仅以示意方式说明本发明的基本构想,在不冲突的情况下,以下实施例及实施例中的特征可以相互组合。
38.其中,附图仅用于示例性说明,表示的仅是示意图,而非实物图,不能理解为对本发明的限制;为了更好地说明本发明的实施例,附图某些部件会有省略、放大或缩小,并不代表实际产品的尺寸;对本领域技术人员来说,附图中某些公知结构及其说明可能省略是可以理解的。
39.本发明实施例的附图中相同或相似的标号对应相同或相似的部件;在本发明的描述中,需要理解的是,若有术语“上”、“下”、“左”、“右”、“前”、“后”等指示的方位或位置关系为基于附图所示的方位或位置关系,仅是为了便于描述本发明和简化描述,而不是指示或暗示所指的装置或元件必须具有特定的方位、以特定的方位构造和操作,因此附图中描述位置关系的用语仅用于示例性说明,不能理解为对本发明的限制,对于本领域的普通技术人员而言,可以根据具体情况理解上述术语的具体含义。
40.请参阅图1,一种方形锂电池电热耦合建模误差源分析方法包括以下步骤:
41.s1:对大尺寸方形电池的产热、传热过程进行必要的建模假设及简化处理,针对电池的正、负极耳以及电池本体单独建模,建立面向控制的电热耦合模型;
42.s2:选择一款大尺寸方形锂电池,开展实验设计、进行实验并对电池数据进行必要的预处理,建立电池的特性试验、恒流工况、以及动态工况数据集;
43.s3:综述现阶段计算高效的产热计算方法,选择应用广泛的产热计算方法作为分析对象,基于建立的电热耦合模型及收集的实验数据集,开展定量分析与比较研究;
44.s4:参数化电热耦合模型中的各热/电热子模型,定量分析其中可能引入的误差源;
45.s5:研究电池极耳与电池本体间的热相互作用,定量分析电池极耳与电池本体间的热传导对电池本体温度分布的影响;
46.s6:综合分析该面向控制的电热耦合建模过程中可能引入的误差源,获取一组最优的模拟组合,并实验验证其模拟精度及泛用性。
47.请参阅图2,所述步骤s1中,假设大尺寸方形锂电池的温度分布仅存在于电池平面,四周与外部环境进行热交换,包括热对流和热辐射。另外,为了尽可能捕捉电池平面内的热行为,温度传感器布置方案考虑九个温度测点a
‑
i,对应所提出的电热耦合模型的输出t1‑
t9,可测取充足的温度数据用于后续的电热耦合建模、模型精度及有效性验证。
48.请参阅图3,针对电池的正、负极耳,考虑到极耳的材料特性以及较小的几何尺寸,建立集中质量模型来描述该区域的热行为;针对电池本体,建立一个二维低阶电热耦合模型来描述该区域的热行为;针对电池本体与正、负极耳间的热相互作用,建立经验的传热模型来描述。具体地,
49.对于正、负极耳的集中质量热模型,其通用表达式为:
[0050][0051]
其中ρ
t
、c
pt
、t
t
、q
t
、q
ct
、t
∞
分别为极耳的密度、比热容、温度、产热率、单位时间传导到电池本体的热量以及环境温度。热流交换量q
ct
可通过以下公式经验获得:
[0052]
q
ct
=h
ct
a
ct
(t
t
‑
t
m
)
[0053]
其中h
ct
、a
ct
、t
m
分别指描述接触内阻对传热限制影响的热接触系数、电池极耳与本体的接触面积和距离极耳位置最近的电池本体离散单元的温度。如图4,传导到电池本体的热量需要根据一定的分配规则将其分配给电池平面上的每个离散单元,依据的基本公式为:
[0054][0055]
其中q
ct,k
和β
ct
分别指分配到第k个离散单元上的热流量和调节因子,该因子用于确定该热流量对该离散单元温度变化的实际影响。坐标(x
t
,y
t
)和(x
i
,y
i
)分别指极耳在笛卡尔坐标系中的位置和第k个离散单元的位置。从该公式可知,热流量分配与热传导的距离成反比。
[0056]
产热项q
t
仅用考虑欧姆产热:
[0057]
q
t
=i2r
s,t
[0058]
其中极耳的等效内阻r
s,t
可通过实验数据辨识得到。
[0059]
对于电池本体,其温度分布服从笛卡尔坐标下的二维非稳态导热方程:
[0060]
ρc
p
d
t
t
‑
k
x
d
xx
t
‑
k
y
d
yy
t=q
[0061]
如图2,满足如下边界条件:
[0062]
在x=0和x=w处,
[0063]
在y=0和y=l处,其中,t为与位置和时间相关的温度函数,q为电池的单位体积产热率。数,q为电池的单位体积产热率。下标r、l、t和b分别表示电池的右、左、上、下边界。k
x
和k
y
分别指x和y方向上的非均一热导率。考虑到电池结构,在本发明中认为二者相等。x=[0,w],y=[0,l],其中w和l分别为电池的宽和长。ρ和c
p
分别为电池的体积平均密度和比热容。h
x
=[h
r
,
‑
h
l
]和h
y
=[h
t
,
‑
h
b
]分别为x和y方向上的等效散热系数。t
∞,x
=[t
r,∞
,t
l,∞
]和t
∞,y
=[t
t,∞
,t
b,∞
]分别为电池两个方向上的环境温度,在本发明的测试环境下可以假定二者相等。如表1,其产热项q基于典型的bernardi产热公式进行计算,考虑电池本体的产热包括可逆热和不可逆热。在本发明中考虑三种产热计算方法,通过横向对比分析选出最适合当前电热耦合模拟的产热计算方法。需要注意的是,在计算产热率q时,还需要考虑电池正、负极耳与电池本体间的热流在各离散单元上的分配。
[0064]
如图5,利用切比雪夫
‑
伽辽金近似方法可实现该二阶偏微分方程的模型降阶,将其转化为若干常微分方程进行求解。该建模方法能够在模型精度、计算复杂度和参数化难度间取得很好的折中,很有潜力应用于电池管理系统的在线温度监控和性能管理。
[0065]
请参阅图6,所述步骤s2中,设计及实施的实验包括电池的特性试验、恒流放电试验和动态工况试验,其中特性试验包括电池在不同温度下的静态容量测试和混合脉冲功率特性试验hppc,恒流放电测试包括不同倍率下的恒流放电测试,动态工况试验包括不同温度下的联邦城市行驶工况fuds和新标欧洲循环测试工况nedc。另外,对电池数据的预处理主要包括剔除异常数据、补充缺失数据和数据降噪,建立的实验数据集包括电流、电压和各测量点的温度数据。
[0066]
请参阅表1。
[0067]
表1目前应用广泛的产热计算公式
[0068][0069][0070]
所述步骤s3中,目前被广泛使用的产热计算方法有三种:基于过电势的方法和基
于等效内阻的方法,其中基于等效内阻的方法根据等效内阻的获得方式又可分为电压差分法和基于等效电路模型的参数辨识法。另外,在进行三种产热计算方法的模拟精度比较时,难以利用实验方法直接准确测取电池的产热量,导致在直接比较产热计算方法时缺乏参考标准。为了解决该问题,本发明选择避开产热计算方法的直接比较,而是通过综合考虑产热计算方法以及其他影响电池电热耦合建模的因素,以最终模型的预测精度来间接评价这三种产热计算方法。该思路虽然无法准确知道哪种产热计算方法最能准确描述电池的真实产热,但是能够确定哪种产热计算方法最适用于当前的电热耦合模拟。
[0071]
请参阅图7,所述步骤s4中,电热耦合模型中各热/电热子模型的参数化是指正、负极耳的集中质量热模型的参数化和电池本体的二维低阶电热耦合模型的参数化。在集中质量热模型的参数化过程中,考虑电池工作温度、外部冷却条件、电流倍率和加载工况对模型参数的影响;在二维低阶电热耦合模型的参数化过程中,重点考虑温度测点组合对模型参数化精度的影响。
[0072]
请参阅图7,所述步骤s5中,通过评估考虑和不考虑电池正、负极耳与电池本体间的热相互作用这两种情况下电热耦合模型的预测精度来定量分析电池极耳与电池本体间的热传导对电池本体温度分布的影响。
[0073]
请参阅图7,所述步骤s6中,以相对均方根误差rrmse作为评价指标,重点考虑电池的最高温度和最大温差的预测精度,综合分析面向控制的电热耦合模拟过程中所有可能的误差源,获取一组最优的模拟组合,然后在不同的工况场景下验证该最优模拟组合的预测精度及泛用性。
[0074]
最后说明的是,以上实施例仅用以说明本发明的技术方案而非限制,尽管参照较佳实施例对本发明进行了详细说明,本领域的普通技术人员应当理解,可以对本发明的技术方案进行修改或者等同替换,而不脱离本技术方案的宗旨和范围,其均应涵盖在本发明的权利要求范围当中。
再多了解一些
本文用于企业家、创业者技术爱好者查询,结果仅供参考。