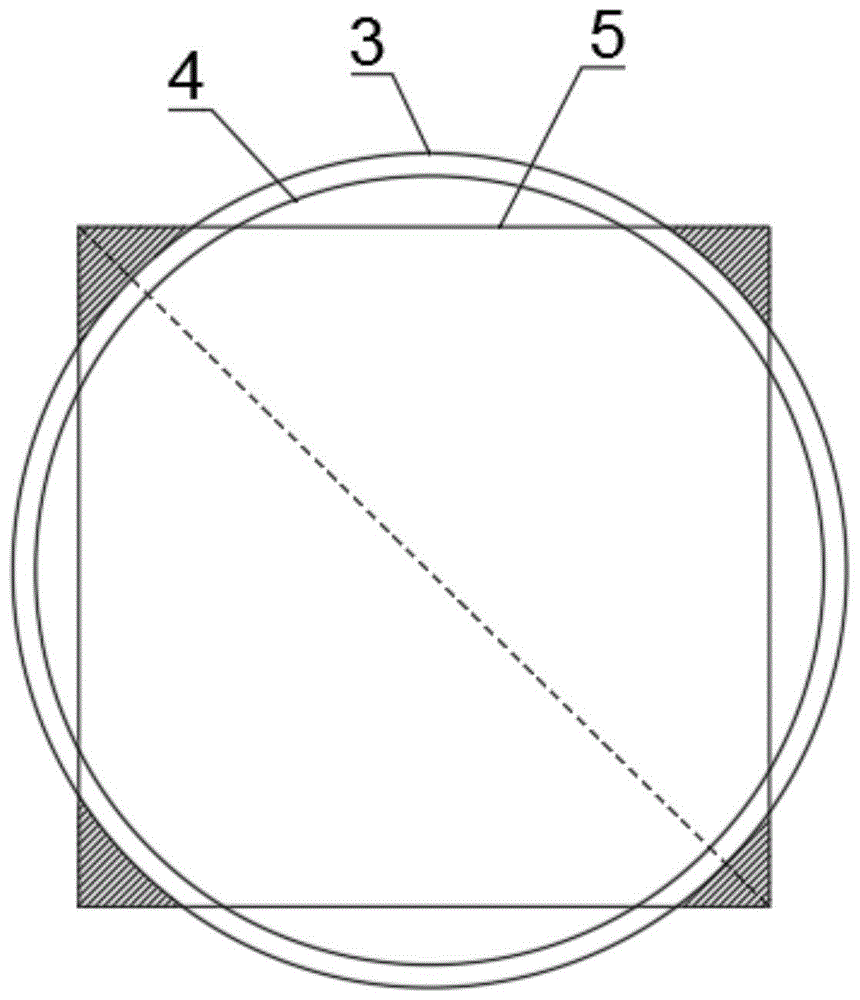
本发明涉及印刷电路板领域,具体涉及一种塔式PCB板及其缝合方法。
背景技术
随着电子行业的高速发展,由于塔式线路板占用空间小等优点,在制造行业已得到广泛应用。目前国内PCB板已逐渐趋于标准化,在当下塔式线路板的质量主要受到缝合工艺的限制,如何实现线路板的有效缝合,成为保证塔式线路板质量的关键。
传统的线路板缝合是将已焊接好的上、下线路板借助工装叠合在一起,再将缝合针插入线路板缝合孔内,如手工焊、浸焊或波峰焊等。
但采用此种方式有诸多缺点:
首先是手工焊,焊接时线路板受热不均易导致严重变形,线路板部分位置插件、链接件较多,本身加工中也存在一定的变形,为了保证线路板的有效缝合,需要在其附近增加缝合工艺,但由于缝合孔与插件之间间隙小,操作员在焊锡时电烙铁无法深入缝合针位置,线路板得不到有效缝合,出现虚焊、堆焊、漏焊、有锡珠、短路等不良缺陷,即使已完成焊锡,但由于受热、受力不均等,线路板间也存在变形、错位等缺陷,严重影响安装工艺,
其次是浸焊,相较于手工焊,浸焊有较大的优点,不管是人工成本还是材料成本都较手工成本低,可以浸锡各种电路板,对原件管脚尺寸和电路板形状基本没有限制,但在塔式线路板的缝合上其使用缺点也是较为明显:
1.浸锡效果无法保证一致,主要表现在三方面:
a.在浸锡过程中浸锡角度和浸锡时间都不能保证一致,会造成短路和虚焊等情况;
b.在浸锡过程中容易使元件倾斜和脱落,由于受热不均容易导致缝合板变形,达不到缝合的效果;
c.人工浸锡使很多焊锡附着在管脚,造成焊锡浪费;
2.浸锡效率不高,人非机器,容易疲劳,工作时间越长效率越低,特别是要保证缝合板在浸锡时不至于出现严重变形,对人员的操作手法和持久耐力上有着较高的需求。
3.对操作人员有专门的要求,浸锡手法熟练,经验比较丰富,所以一般要求此类人员能够稳定长久的工作下去,如果一朝离开就可能会影响生产。
4.为满足较高的导电性、稳定性、抗腐蚀性、抗拉和抗疲劳、机械强度、低成本等需求,普遍采用有铅焊料,但铅对人类的生活环境的污染太大,对人体的伤害是非常严重的。
然后是波峰焊,相较于前面两种波峰焊有较突出的优点,可实现均匀焊接,但主要用在插接件的焊接,且预烘温度90-1000℃,波峰焊温度220-2400℃,对焊接PCB板和插件的耐高温性要求较高,且根据需求不同,需要使用不同的波峰焊,对于成本投入也要求较高。
综上问题点,使得塔式线路板的焊接操作不便,生产成本居高不下,合格率得不到提升的尴尬境地。
技术实现要素:
本发明所要解决的技术问题是目前塔式线路板的焊接操作不便,生产成本居高不下,合格率得不到提升,目的在于提供一种塔式PCB板及其缝合方法,采用本方案,能确保PCB板的有效缝合,避免产生上下PCB板变形错位等不良情况,同时还能满足焊锡从缝合孔渗透到PCB板的另一侧,确保另一侧焊接无漏焊、虚焊、堆焊等不良现象。
本发明通过下述技术方案实现:
一种塔式PCB板,包括PCB板本体,所述PCB板本体包括上层板和下层板,还包括方针;
所述PCB板本体上开有多个焊接缝合孔和固定缝合孔,所述焊接缝合孔和固定缝合孔中均可插入方针并进行缝合,用于固定上层板和下层板;所述焊接缝合孔与固定缝合孔均和方针间隙配合,所述方针的截面对角线长度均大于焊接缝合孔和固定缝合孔的孔径,所述固定缝合孔的孔径小于焊接缝合孔的孔径。
相对于现有技术中,目前塔式线路板的焊接操作不便,生产成本居高不下,合格率得不到提升的问题,本方案通过印刷机将锡膏分别印刷到PCB板的上、下板的铜箔上,将完成插片、贴片的PCB板组合在一起,再将方针插入线路板上,将插有方针的线路板经过回流焊实现焊锡,最终完成线路板的缝合,该方式缝合的线路板变形小,线路板受到的机械伤害小、热变形小,且成品缝合位置锡膏能均匀分布,不存在漏焊、虚焊、堆锡的缺陷;具体的,其中PCB板本体包括有上层板和下层板,上层板和下层板的铜箔上均通过印刷机印刷有锡膏,其中上层板和下层板之间叠放,保持塔式PCB板重叠位置固定不变,在此基础上,开始插入缝合针,即方针;在PCB本体上开有多个焊接缝合孔和固定缝合孔,即上层板和下层板上均开有缝合孔,两板之间的缝合孔相对应,使方针能通过缝合孔贯穿上层板和下层板,用于缝合固定;其中固定缝合孔与焊接缝合孔均和方针之间能实现间隙配合,即两者之间留有空隙,能在焊接PCB板本体时,位于上层板和下层板上侧面的锡膏,能融化并通过空隙有效渗透到另一侧,实现焊接固定;进一步的,其中所述方针的截面对角线长度均大于焊接缝合孔和固定缝合孔的孔径,能保证焊接缝合孔与固定缝合孔均和方针的四角有固定重合部分,避免在回流焊机内,锡膏融化时,方针由于自身重力从PCB板上掉落,造成缝合失败;进一步的,固定缝合孔的孔径小于焊接缝合孔的孔径,使方针和固定缝合孔之间的重合部分更多,用于固定上层板和下层板,实现机械定位,保证PCB板在焊接时的位置固定,确保较小的形变量;通过上述几种方式配合,使成品缝合位置的锡膏能均匀分布,不存在焊锡堆积现象;待焊接完成后即可得到缝合完好的线路板,通过该方式,能杜绝漏焊、虚焊、堆锡等现象的产生。
进一步优化,多个所述焊接缝合孔均布于PCB板本体的周边和中部;用于加固线路板的缝合。
进一步优化,多个所述固定缝合孔均布于PCB板的边角和中部;用于在焊接前,实现对上层板和下层板的位置进行加固。
进一步优化,所述PCB板本体边角处均设有支撑柱,所述支撑柱连接上层板和下层板;用于固定上层板和下层板之间间距,在插入方针时,能支撑PCB板。
进一步优化,所述焊接缝合孔和方针之间的缝隙含有缕空;用于焊接时,使锡膏能顺利通过渗透方式到达另一侧位置。
进一步优化,一种塔式PCB板的缝合方法,包括以下步骤:
第一步:将锡膏均匀布局于上层板和下层板上表面的焊盘上;
第二步:将上层板和下层板塔式重叠;
第三步:重叠后,在固定缝合孔中插入方针,进行缝合;
第四步:然后在焊接缝合孔中插入方针,进行缝合;
第五步:焊接PCB板本体,完成PCB板本体的固定。
进一步优化,所述上层板与下层板的正面均印刷有锡膏,所述锡膏均布于焊接缝合孔和固定缝合孔的焊盘上;用于使PCB板成品的缝合位置,锡膏能均匀分布。
进一步优化,所述上层板和下层板之间采用回流焊焊接固定。
进一步优化,采用人工或缝合机,将所述方针插入焊接缝合孔和固定缝合孔中,并进行缝合。
进一步优化,在将上层板和下层板塔式重叠前,需在上层板和下层板之间的四角安装支撑柱。
本发明与现有技术相比,具有如下的优点和有益效果:
本发明提供了一种塔式PCB板及其缝合方法,采用本方案,能确保PCB板的有效缝合,避免产生上下PCB板变形错位等不良情况,同时还能满足焊锡从缝合孔渗透到PCB板的另一侧,确保另一侧焊接无漏焊、虚焊、堆焊等不良现象;该方式缝合的线路板变形小,线路板受到的机械伤害小、热变形小,线路板正、反两面都无气孔,无堆焊,无虚焊,PCB板的缝合位置正反面锡膏分布均匀。
附图说明
为了更清楚地说明本发明示例性实施方式的技术方案,下面将对实施例中所需要使用的附图作简单地介绍,应当理解,以下附图仅示出了本发明的某些实施例,因此不应被看作是对范围的限定,对于本领域普通技术人员来讲,在不付出创造性劳动的前提下,还可以根据这些附图获得其他相关的附图。在附图中:
图1为本发明提供的一种塔式PCB板的结构示意图;
图2为本发明提供的一种塔式PCB板的侧视图;
图3为本发明提供的一种塔式PCB板-焊接缝合孔、固定缝合孔与方针的配合图。
附图中标记及对应的零部件名称:
1-上层板,2-下层板,3-焊接缝合孔,4-固定缝合孔,5-方针,6-支撑柱。
具体实施方式
为使本发明的目的、技术方案和优点更加清楚明白,下面结合实施例和附图,对本发明作进一步的详细说明,本发明的示意性实施方式及其说明仅用于解释本发明,并不作为对本发明的限定。
实施例1:
本实施例提供了一种塔式PCB板,如图1-图3所示,包括PCB板本体,所述PCB板本体包括上层板1和下层板2,还包括方针5;
所述PCB板本体上开有多个焊接缝合孔3和固定缝合孔4,所述焊接缝合孔3和固定缝合孔4中均可插入方针5并进行缝合,用于固定上层板1和下层板2;所述焊接缝合孔与固定缝合孔均和方针间隙配合,所述方针的截面对角线长度均大于焊接缝合孔和固定缝合孔的孔径,所述固定缝合孔的孔径小于焊接缝合孔的孔径。
相对于现有技术中,目前塔式线路板的焊接操作不便,生产成本居高不下,合格率得不到提升的问题,本方案通过印刷机将锡膏分别印刷到PCB板的上、下板的铜箔上,将完成插片、贴片的PCB板组合在一起,再将方针插入线路板上,将插有方针的线路板经过回流焊实现焊接,最终完成线路板的缝合,该方式缝合的线路板变形小,线路板受到的机械伤害小、热变形小,且成品缝合位置焊锡能均匀分布,不存在漏焊、虚焊、堆锡的缺陷;具体的,其中PCB板本体包括有上层板和下层板,上层板和下层板的铜箔上均通过印刷机印刷有锡膏,其中上层板和下层板之间叠放,保持塔式PCB板重叠位置固定不变,在此基础上,开始插入缝合针,即方针;在PCB本体上开有多个焊接缝合孔和固定缝合孔,即上层板和下层板上均开有缝合孔,两板之间的缝合孔相对应,使方针能通过缝合孔贯穿上层板和下层板,用于缝合固定;其中固定缝合孔与焊接缝合孔均和方针之间能实现间隙配合,即两者之间留有空隙,能在焊接PCB板本体时,位于上层板和下层板上侧面的锡膏,能融化并通过空隙有效渗透到另一侧,实现焊接固定;进一步的,其中所述方针的截面对角线长度均大于焊接缝合孔和固定缝合孔的孔径,能保证焊接缝合孔与固定缝合孔均和方针的四角有固定重合部分,避免在回流焊机内,锡膏融化时,方针由于自身重力从PCB板上掉落,造成缝合失败;进一步的,固定缝合孔的孔径小于焊接缝合孔的孔径,使方针和固定缝合孔之间的重合部分更多,用于固定上层板和下层板,实现机械定位,保证PCB板在焊接时的位置固定,确保较小的形变量;通过上述几种方式配合,使成品缝合位置的锡膏能均匀分布,不存在焊锡堆积现象;待焊接完成后即可得到缝合完好的线路板,通过该方式,能杜绝漏焊、虚焊、堆锡等现象的产生。
本实施例中,多个所述焊接缝合孔3均布于PCB板本体的周边和中部;为加固线路板的缝合,本方案中,由于PCB板周边位置受力较多,且焊接缝合孔3和方针5重合部分较少,对PCB板的伤害小,因此在PCB板本体的周边和中部可均布有多个焊接缝合孔3,通过方针5缝合,实现对PCB板周边和中部位置的缝合加固。进一步优化的,其中设置在PCB板本体周边的多个焊接缝合孔3,应采用阵列方针5的方式用于加固线路板的缝合,其中阵列方针5的方式多种,如矩形阵列、路径阵列等等。
本实施例中,多个所述固定缝合孔4均布于PCB板的边角和中部;为在焊接PCB板前,对上层板1和下层板2的位置进行加固,本方案中,由于固定缝合孔4与方针5的重合部分更多,但对PCB板的伤害更大,因此,固定缝合孔4只需在四角和中部共五个点位,由5个固定缝合孔4设置于PCB板的边角和中部位置,靠固定缝合孔4维持上下板的拼装,实现对PCB板四角和中心位置进行固定。
本实施例中,所述PCB板本体边角处均设有支撑柱6,所述支撑柱6连接上层板1和下层板2;为固定上层板1和下层板2之间间距的作用,在插入方针5时,能支撑PCB板,本方案中,在PCB板本体边角处均设有支撑柱6,其中支撑柱6是起到支撑上层板1和下层板2的作用,在插入方针5时,能支撑PCB板,进一步减少形变量,其中支撑柱6上有卡扣,能固定在下层板2的安装孔上。
本实施例中,所述焊接缝合孔3和方针5之间的缝隙含有缕空;在焊接时,为使锡膏能顺利通过渗透方式到达另一侧位置,本方案中,在焊接缝合孔3和方针5之间的缝隙含有一定的缕空,其中焊接缝合孔3和方针5之间的间隙不易过大,否则会导致锡焊漏到PCB板另一侧,在PCB板另一侧形成漏焊或虚焊的情况。
实施例2:
本实施例在实施例1的基础上进一步优化,提供了一种塔式PCB板的缝合方法,包括以下步骤:
第一步:将锡膏均匀布局于上层板1和下层板2上表面的焊盘上;
第二步:将上层板1和下层板2塔式重叠;
第三步:重叠后,在固定缝合孔4中插入方针5,进行缝合;
第四步:然后在焊接缝合孔3中插入方针5,进行缝合;
第五步:使用回流焊焊接PCB板本体,完成PCB板本体的固定。
本实施例中,所述上层板1与下层板2的正面均印刷有锡膏,所述锡膏均布于焊接缝合孔3和固定缝合孔4的焊盘上;用于使PCB板成品的缝合位置,锡膏能均匀分布。
本实施例中,所述上层板1和下层板2之间采用回流焊焊接固定;
本实施例中,采用人工或缝合机,将所述方针5插入焊接缝合孔3和固定缝合孔4中,并进行缝合;本方案中,能通过将组合好的PCB板放入缝合机自动插入方针5,或放置在插方针5的工装上手动插入方针5,将完成方针5插入的PCB板放入回流焊实现焊接,待焊接完成后即可得到缝合好的线路板。
本实施例中,在将上层板1和下层板2塔式重叠前,需在上层板1和下层板2之间的四角安装支撑柱6;其中支撑柱6是起到支撑上层板1和下层板2的作用,在插入方针5时,能支撑PCB板,进一步减少形变量,其中支撑柱6上有卡扣,能固定在下层板2的安装孔上。
本方案具体工作原理:首先通过印刷机印刷,此时锡膏被均匀布局于PCB板的正面缝合孔的焊盘上,然后在上层板1上安装支撑柱6,在支撑柱6上带有卡扣,可固定在下层板2的安装孔上,用于支撑上层板1和下层板2,并在上层板1和下层板2上分别完成插件和贴片的安装,其中下层板2的插件对穿上层板1还可以起到固定相对位置的效果,然后叠放PCB板,将上层板1和下层板2进行叠放,保持塔式PCB板重叠位置固定不变,这是除对PCB板尺寸及精度要求外的,保证塔式PCB板有效缝合的先决条件;然后开始插缝合针,通过人工或缝合机,首先在固定缝合孔4处插入方针5,并进行缝合,保证PCB班在焊接时位置固定,确保较小的变形量,实现机械定位;然后在焊接缝合孔3处插入方针5,并进行缝合,此时焊接缝合孔3和方针5之间过盈配合,留有空隙,便于锡焊渗透到另一侧,使焊锡均匀分布;然后将完成方针5插入的PCB板放入回流焊实现焊接,待焊接完成后即可得到缝合好的线路板。
实施例3:
本实施例在实施例2的基础上进一步优化,提供了一种具体实施方式。
缝合前工艺:
首先通过印刷机印刷,锡膏被均匀布局于PCB板的正面缝合孔的焊盘上,锡膏厚度:0.5mm;完成PCB板插件、贴片,并完成上下PCB板的重叠组合,并固定好,待后续缝合。
缝合工艺:
第一步:首先是叠放PCB板,保持塔式PCB板重叠位置固定不变,这是除对PCB板尺寸及精度要求外的,保证塔式PCB板有效缝合的先决条件。
第二步:插缝合针,人工或缝合机插方针5,都应遵循以下内容:
材料:1.5*1.5mm方针5,厚度1.6mm一致的上下层PCB板。为保证PCB板在焊接时位置固定,确保较小的变形量,首先需要进行机械定位,(下板四角和中部共设有固定缝合孔45个,和多个焊接缝合孔3,且PCB板正反面都有焊盘)。
具体缝合工艺:将组合好的PCB板放入缝合机自动插入方针5,或放置在插方针5的工装上手动插入方针5,先插固定缝合孔4,再插焊接缝合孔3。将完成方针5插入的PCB板放入回流焊实现焊接,待焊接完成后即可得到缝合好的线路板。
在支撑柱6附近的固定缝合孔4内,首先插入缝合针。
方针5固定在PCB板上,同时方针5与缝合孔间有一定的镂空,这样处于PCB板上侧锡膏在熔化后可有效地渗透到另一侧,且不存在焊锡堆积的现象,具体尺寸选择见下表:
常用(铜)方针与刚性PCB板(铜箔厚0.3)配合孔径参数表 单位:mm
同时在线路板外部受力较多的部位采用阵列方针5的方式以加固线路板的缝合,该方式缝合的线路板变形小,线路板受到的机械伤害小、热变形小,且成品缝合位置锡膏能均匀分布,不存在漏焊、虚焊、堆锡的缺陷。在过回流焊时,缝合孔径与方针5的间隙过大容易导致焊锡漏到PCB板一侧,在PCB板一侧形成漏焊或虚焊的情况。线路板正、反两面都无气孔,无堆焊,无虚焊,焊锡分布均匀。
以上所述的具体实施方式,对本发明的目的、技术方案和有益效果进行了进一步详细说明,所应理解的是,以上所述仅为本发明的具体实施方式而已,并不用于限定本发明的保护范围,凡在本发明的精神和原则之内,所做的任何修改、等同替换、改进等,均应包含在本发明的保护范围之内。
本文用于企业家、创业者技术爱好者查询,结果仅供参考。