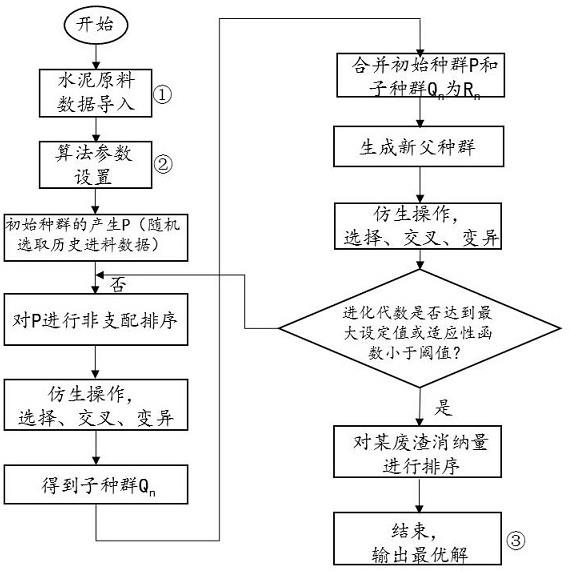
1.本发明属于固体废物资源化利用领域,尤其是一种基于仿生算法的固体废物优先消纳驱动的水泥配料方法。
背景技术:
2.近年来,随着我国城镇固废和大宗工业固体废物产生量的迅猛增长,这些固废用于水泥回转窑协同处理处置受到越来越多的关注,生活垃圾、城镇污泥和一般工业固废的协同处置量也日益上升,其中危险固体废弃物的水泥窑协同处置量更是占据了危废焚烧处置量的45%以上。
3.以工业固体废弃物的水泥回转窑协同处置为例,近年来通过对各种工业废渣的原料成分以及物理、化学特性进行深入分析,发现工业固废可以作为原料用于烧制水泥。以聚氯乙烯废渣为例的生产废渣水泥工艺,其主要是以电石渣作为主要钙质原料,再适量添加各种另类钙质、粘土质、铁质类废渣进行全废渣水泥熟料的煅烧,进而利用脱硫灰或柠檬酸渣替代天然石膏,粉煤灰、煤矸石、石灰石碎屑做混合材生产全废渣硅酸盐水泥,经过不断调整设计方案,合理搭配原料和进行产前试验、类比筛选、工艺选定,并进行初步均化,分类存储、有效计量、生产制备、例行监控和两磨一烧的工艺流程后,制得合格的水泥成品,成功地获得符合国家水泥标准的全废渣硅酸盐水泥熟料和全废渣硅酸盐水泥。这些全废渣原料主要来源于一些化工产业、电石产业、热电产业、生化公司等上游产业所产生的工业固废,如:电石渣、电石炉收尘灰、石灰渣、石灰石碎屑、净化灰等钙质原料,粉煤灰、炉渣、煤矸石等粘土质原料,硫酸渣、铜渣、铁质尾矿等校正原料,脱硫石膏、柠檬酸渣等缓凝剂原料。与传统水泥工艺相比,全废渣水泥原料种类多、成分复杂,且废渣的量随着上游企业的运行情况波动很大,同时导致生产出来的水泥性能、质量参差不齐,这是水泥生料配料的一个巨大挑战。
4.在水泥进料配比的领域中,水泥生料配料常常采用的是excel人工试算表格方法,主要是利用三率值的约束条件来计算水泥配伍;在excel中也可以使用线性/非线性规划模块进行优化求解,但实际情况中常常遇到该方法无法求到最优解的情况。同时,掺入固体废物后水泥工艺的原料组分和种类比普通硅酸盐水泥更复杂,虽然经过了技术人员多年的探索,已经积累了一些废渣水泥原料配料的实践经验,但采用excel表格进行水泥原料的配伍计算的方法效率较低,且不能很好地解决原料波动较大的情况下废渣的进料配料比和水泥产品质量参差不齐的问题。虽然已有采用遗传算法用于传统硅酸盐水泥原料配比优化控制的相关报道,但仍然存在不少问题。此前报道的遗传算法多应用于传统硅酸盐水泥配料方法优化中,主要是针对原料简单的传统水泥生产工艺的;而通过excel线性/非线性规划得出的一批解中,有时某库存量大的固废原料消纳量较小,难以满足最大量消纳电石渣等大宗工业固废的需求。
5.本发明中引举的案例中采用的则是一种基于以非支配排序多目标优化为代表的进化算法,非支配排序多目标进化算法常被用于寻求有多个目标函数最优解的问题之中,
所选择的这种算法,与普通遗传算法不同的点主要在于:(1)采用快速非支配排序的方法,使计算复杂度大大降低;(2)定义了拥挤度和拥挤度比较算子,替代了需要指定的共享半径,使准pareto域中的个体能扩展到整个pareto域,且均匀分布,保持了种群的多样性;(3)引入了精英策略,扩大了采样空间,防止了最佳个体的丢失,提高了算法的运算速度。
6.该算法常常用于优化多目标问题,其优化效果将大大升高。此前还未出现将此算法应用于成分复杂的工业固废水泥原料配伍计算之中的案例,本发明是首次将这种仿生算法程序应用于废渣原料水泥工艺的原料配比优化问题之中。但是若简单地将此算法应用于成分更复杂的工业固废水泥原料的配伍计算之中尚存在诸多技术问题。为此,本发明针对固废原料特点将这种仿生算法的程序进一步改进后,成功地实现含废渣水泥工艺的原料配比的仿生优化。
技术实现要素:
7.本发明是提供一种基于仿生算法的固体废物优先消纳驱动的水泥配料方法,解决采用工业废渣为原料生产水泥时进料波动大、生产水泥质量不稳定和三率值计算方法不完善的问题。具体来说包括以下步骤:步骤1,选取若干组固废原料生产水泥的数据,该数据包括固废原料的种类、固废原料的关键组成参数以及其中主要的五种氧化物cao、al2o3、fe2o3、sio2以及so3的含量占比,包括每种废渣的占总进料的含量百分比,整合这些数据,把固废原料成分数据整合成属性矩阵,各原料的进料比作为待优化向量。具体来说即是进料的所有种类为矩阵块a,a为一个5
×
n的矩阵。例如矩阵a的第一列为电石渣,第二列为拌合料,后面列次依次为其他固体废物等。向量表示水泥生料中各原料的进料百分比,向量表示的是水泥进料中五种氧化物的总量,公式如下:
·
=
ꢀꢀꢀꢀꢀꢀꢀꢀꢀꢀꢀꢀ
a
ꢀꢀꢀꢀꢀꢀꢀꢀꢀꢀꢀꢀꢀꢀꢀꢀ
其中,c1表示电石渣中cao的质量百分含量,c2表示拌合料中cao的质量百分含量,依此类推;s1表示电石渣中sio2的质量百分含量,s2表示拌合料中sio2的质量百分含量,依此类推;f1表示电石渣中fe2o3的质量百分含量,f2表示拌合料中fe2o3的质量百分含量,依此类推;a1表示电石渣中al2o3的质量百分含量,a2表示拌合料中al2o3的质量百分含量,依
此类推;s1表示电石渣中so3的质量百分含量,s2表示拌合料中so3的质量百分含量,依此类推。
8.优选地,以某批次的水泥进料为例:表1 某批次水泥进料氧化物含量及比例种类(wt%)caosio2fe2o3al2o3so3进料占比电石渣68.323.380.511.870.4840.27拌合料86.273.700.700.700.5025.10粉煤灰10.0049.847.7017.911.297.28炉渣7.9048.207.4316.000.454.44钢渣44.6116.7018.494.430.416.78硅粉0.3194.520.240.460.494.15硅石7.5644.897.5615.930.217.00焚烧灰渣26.0326.958.378.965.544.99整合转换成为属性矩阵,即是:
·
=通过将近几年的历史进料数据编写成属性矩阵,后续算法迭代计算求最优解过程中,会随机使用这些历史数据作为初猜值。
9.步骤2,优选地,选择以非支配排序多目标遗传算法为代表的仿生算法,根据固废原料特点并对其进行改进,通过此仿生算法优化计算求得最优的若干种固废原料比。在算法设置过程中,把水泥的期望三率值(石灰饱和系数kh或lsf、硅率sm和铝率im)当作适应度函数,据此来评价产生的固废原料配比解的适应性(即计算得到的实际三率值越接近期望三率值,则对应的固废原料配比解在此算法中具有越强的适应性)。输入期望三率值后,以此为适应度函数来进行新一轮的种群生长和筛选,通过约束表征期望三率值和实际三率值之间偏差的四个目标函数,,,,求解一批满足四个目标函数的最优解。其中kh*(或lsf*)、sm*、im*为预期三率值,kh(或lsf)、sm、im为实际三率值。
10.废渣水泥工艺中三率值采用的计算公式为:废渣水泥工艺中三率值采用的计算公式为:废渣水泥工艺中三率值采用的计算公式为:
以期望三率值和由最终优化解得到的若干固体废渣进料配比通过三率值公式计算得到的实际三率值之间的偏差作为目标函数,,,,目标函数写为:目标函数写为:目标函数写为:目标函数写为:目标函数写为:或其中,,,分别为目标函数,,,的权重因子,且远大于,,。为了均衡地约束三率值,优选地,设定,,,,保证y1,y2,y3和y4均趋于0。在满足,,,的前提下,权重因子的进一步增大可以使得,,可以更加均衡地趋近于0,优选地,是、、的5~15倍,、、三者之间的比例是0.5~3,加大的数值,从而整体三率值都能均衡地接近期望三率值。在水泥的实际生产中,当水泥的性能对某个三率值的影响较为敏感时,可在算法设置里修改该三率值约束函数前的权重因子,以动态地衡量其对水泥配比的影响。比起传统水泥配料方法中计算三率值的约束条件(取三率值差的平方和),这种方法可以使实际三率值kh(或lsf)、sm、im无限接近期望三率值kh*(或lsf*)、sm*、im*,且能科学衡量某一敏感率值对水泥配比的影响。
11.将历史数据和期望三率值导入算法,编码成位串产生初始种群,经过非支配排序和仿生操作、遗传变异生成子种群q
n
,将子代种群和父代种群合并为r
n
,经过非支配排序和拥挤度计算产生新父种群,再继续遗传进化生成新的子代种群,采用最优个体保留机制,直至进化代数达到最大设定值或适应度函数小于阈值,通过设置最优前端个体系数,优选地设置为0.2~0.5,得到一批最优解。
12.步骤3,对步骤2中得到的满足目标函数,,,的一批最优解,按照某废渣最大程度消纳的目标函数来排序,取靠前的该组解。对产生的新一代符合条件的群体设置合适的最优前端个体系数,优选地设为0.2~0.5,由此会得到一批pareto最优解。将这些
pareto最优解按照有最大程度消纳需求的某种固体废渣的量(比如电石渣的优先消纳量)从高至低依次排序,取排靠前的这组最优解,作为最终满足我们目标函数的所寻求的最终解。
13.优选地,以步骤1提到的某批次水泥厂固体废渣的进料成分(表2)为例详解本发明求解水泥配料方法的流程步骤。
14.表2 某批次水泥进料氧化物含量及比例种类(wt%)caosio2fe2o3al2o3so3进料占比电石渣68.323.380.511.870.4840.27拌合料86.273.700.700.700.5025.10粉煤灰10.0049.847.7017.911.297.28炉渣7.9048.207.4316.000.454.44钢渣44.6116.7018.494.430.416.78硅粉0.3194.520.240.460.494.15硅石7.5644.897.5615.930.217.00焚烧灰渣26.0326.958.378.965.544.99拟满足的期望三率值依次为kh*=0.88,sm*=2.15,im*=1.45,并以电石渣为最大程度废渣消纳量的目标来进行水泥配料。
15.以此基于仿生算法的非支配排序的多目标进化算法求得各固体废渣进料配比最优解为:电石渣:50.0576%,拌合料:16.0989%,粉煤灰:2.4237%,炉渣:3.5862%,钢渣:5.8345%,硅粉:4.6222%,硅石:11.4113%,焚烧灰渣:6.0386%。
16.对应的三率值为,kh=0.88187,sm=2.1506,im=1.4451,非常接近期望三率值kh*=0.88,sm*=2.15,im*=1.45。
17.步骤4,求得的最优解用于指导实际废渣水泥工艺生料配比。本发明的水泥进料配料方法不仅适用于固体废渣水泥的原料配比,同时也适用于传统硅酸盐水泥等水泥生产工艺的原料配比优化。
18.在此背景下,本发明结合水泥企业在过往几年实际操作过程中积累的工业固废水泥原料进料配比数据作为初猜值,利用以非支配排序的多目标进化算法为代表的仿生算法建立废渣水泥工艺原料进料配比模型,用此仿生算法优化模型来求解均衡地趋近期望三率值、并同时实现以电石渣为代表的库存压力较大的固废原料优先消纳从而实现最优水泥含废渣的原料配比。
19.本专利发明基于一种仿生算法的以固体废物消纳驱动的非支配排序的多目标进化算法来优化全废渣水泥配料,得到的水泥原料配比既能较均衡地尽量满足预期三率值,又可以满足尽可能多地消纳库存压力较大的固体废渣的目标,与人工试错法、excel线性/非线性求解法和传统的遗传算法计算相比,具有效率高,精度大等优点,不仅适用于固体废渣水泥的原料配比,亦适用于传统硅酸盐水泥等水泥生产工艺的原料配比优化,在水泥工业具有较为广泛的应用前景。
附图说明
20.图1为基于仿生算法的固体废物优先消纳驱动的水泥配料算法流程图;图2为基于仿生算法的固体废物优先消纳驱动的水泥配料优化系统的用户交互界面和优化结果展示示意图;图3为非支配排序分层示意图,对应中间图的rank histogram;图4为pareto前沿面的示意图(上端第一个图);其中图1中
①
、
②
、
③
算法步骤,与图2中软件界面中
①
、
②
、
③
功能区域及控件按钮一一对应。
具体实施方式
21.参照说明书附图图1,一种基于仿生算法的固体废物优先消纳驱动的水泥配料方法,优选地,以表2中的废渣水泥生料进料的成分为例。
22.选择表2中的废渣水泥生料进料的成分,也即发明内容步骤1中提及的属性矩阵。
23.优选地,进行算法参数设置,设置目标石灰饱和系数kh*=0.89,目标硅率sm*=2.1,目标铝率im*=1.4,具体实施案例如下。
24.(1)本发明仿生算法求解水泥配比的详细计算过程
①
启动水泥配料程序,进行初始参数的初始化:导入水泥进料各组分的氧化物含量数据,例如:表3 水泥进料各组分的氧化物含量种类(wt%)caosio2fe2o3al2o3so3电石渣68.323.380.511.870.48拌合料86.273.700.700.700.50粉煤灰10.0049.847.7017.911.29炉渣7.9048.207.4316.000.45钢渣44.6116.7018.494.430.41硅粉0.3194.520.240.460.49硅石7.5644.897.5615.930.21焚烧灰渣26.0326.958.378.965.54
②
经过算法处理,整合成属性矩阵:通过将近几年的历史进料数据编写成属性矩阵,其中表4为列举的部分历史进料(废渣进料百分比),后续算法迭代计算求最优解过程中,会随机使用这些历史数据作为初猜值。
25.·
=
表4 水泥生料配料的部分历史进料数据
种类进料占比历史数据1(wt%)进料占比历史数据2(wt%)进料占比历史数据3(wt%)进料占比历史数据4(wt%)进料占比历史数据5(wt%)电石渣40.2739.7140.8739.1737.34拌合料25.1025.4226.9325.6128.73粉煤灰7.287.348.137.346.09炉渣4.444.514.104.825.29钢渣6.786.617.076.626.69硅粉4.154.233.914.524.27硅石7.006.706.597.057.87焚烧灰渣4.994.934.254.625.24
导入水泥的期望三率值(石灰饱和系数kh或lsf、硅率sm和铝率im):kh*=0.88,sm*=2.15,im*=1.45,作为适应度函数。
26.导入所用煤的各种性质:烧成热耗3014 kj/kg、煤热值 27010 kj/kg、煤灰份 12.28%。
27.设置合适的遗传算法的参数:包括最优个体比例 0.3(即30%)、种群大小200、进化的代数300、重复进行遗传算法模拟的重复次数3次,以第一个原料(电石渣)为优先消纳对象,与期望值间的最大允许方差0.03(即3%))。
28.③
算法将上述属性矩阵转化二进制字符串,字符串组合为初始种群p,设种群规模为200,列举部分个体编码如下:l1=10010101l2=01001011l3=01011001l4=10100001
……………………
l
197
=01101101l
198
=10110000l
199
=00111000l
200
=11110000
④
对规模为200的种群p进行非支配排序和拥挤度计算,即通过非支配排序算法对p进行分层后,进行拥挤度计算,如说明书附图图3所示:种群p被分为9个层次,第一级非支配层个数为60个,第二级非支配层个数为30个,第三级非支配层为25个
……
第九级非支配层个数为7个。由此,整个种群被分层,同时算法会对每个个体进行与目标函数之间的距离和计算即拥挤度计算,这样每个个体拥有非支配层此和拥挤度这两个属性。如此降低算法计算的复杂度。
29.⑤
对种群p进行仿生操作,选择、交叉、变异等,如:通过仿生算法带有的精英策略,选择出拥挤度度较大的且处于较优的非劣等级个体,设置最优前沿系数为0.3,则选择出60个个体,下面举例列举前4个个体进行交叉、变异的说明。
30.l1=1001 0101
ꢀꢀꢀꢀ
l2=0100 1011
ꢀꢀꢀ
l3=0101 1001
ꢀꢀꢀ
l4=1010 0001经过交叉后得到的新的可能的种群有:100110111001100110010001010001010100100101000001010101010101101101010001101001011010101110101001再经过变异(某些位点由1
→
0或由0
→
1)后,得到的新的可能的子种群q
n
有:100110111001100110010001110110110001100110100001
………………
010001010100100101000001110001010000100101001001
………………
010101010101101101010001010111011101101101010011
………………
101001011010101110101001101011011110101110001001
………………⑥
将p和qn合并为rn,依次重复
④
、
⑤
仿生操作,直至达到算法迭代次数或满足终止阈值。
31.⑦
将产生的满足期望三率值的一批最优解(pareto前沿面绘图,参见说明书附图图4)按照优先消纳某固废要求对消纳量高低进行排序,算法选择最佳解,输出为废渣配比,列举部分pareto最优解如表5:表5 仿生算法水泥配比解由表5中列举的部分pareto最优解,从
①
至
⑤
依次按照电石渣的消纳量从高到低排序,为了满足优先消纳电石渣的目标,选择解
①
。
32.⑧
以此基于仿生算法的非支配排序的多目标进化算法求得各固体废渣进料配比最优解为:表6 仿生算法水泥配比最优解对应的实际三率值为,kh=0.88187,sm=2.1506,im=1.4451,非常接近期望三率值kh*=0.88,sm*=2.15,im*=1.45。
33.(2)人工试错法、excel线性/非线性规划计算算法与本发明仿生算法求解水泥配比案例对比。
34.①
以人工手算试错法来计算水泥配比:列出约束条件,即,
解此五元一次方程组,有无数解,取一组解,如表7所示:表7 人工试错法水泥配料解人工试错法就是解此五元一次方程组的过程,但是过程很繁琐,不够简便,且常常出现无解的情况。
35.②
以excel表格线性/非线性规划模块通过约束期望三率值和实际三率值相等,并利用三率值计算公式进行求解,发现满足约束条件的解有多个,随机举例,如表8所示:表8 excel线性/非线性规划法水泥配料解1在上述实施案例中,通过excel表格设定期望三率值和实际三率值相等的约束条件,得到的水泥配料比部分见上表,其中列举的
①
、
②
、
③
的解能满足此条件,除了解
①
较能符合基于水泥厂的废渣堆量的消纳需求;解
②
和
③
均含有某项原料配料为0的情况,且电石渣的消纳量过少,不满足实际需求。
36.③
当废渣原料的进料成分发生改变时,excel线性/非线性规划求得的解还会出现无解的情况。
37.优选地,以表9的进料成分为例:表9 某批次水泥进料氧化物含量种类(wt%)caosio2fe2o3al2o3so3电石渣58.323.380.511.870.48拌合料62.2121.020.700.700.50粉煤灰11.0052.847.7014.212.10炉渣7.9056.259.4115.871.48钢渣15.2113.6355.245.680.61硅粉0.1195.210.150.460.21硅石3.2662.124.218.250.36焚烧灰渣26.0326.958.378.965.54
优选地,设定期望三率值kh*=0.89,sm*=2.1,im*=1.4,用此方法进行水泥配比求解,见表10。
38.表10 excel线性/非线性规划法水泥配料解2由上述实施案例,在表9的进料成分下,期望三率值只能满足其中两个,其中kh*=kh=0.89,sm*=sm=2.1,im=1.35≠1.4= im*,可见在用excel求解水泥配料比的过程中,某些进料成分数据会使得求到的解是无效的,不能全部满足所有约束条件(即寻不到解),此外,进料配比中电石渣的含量高达69.58%,并不符合实际情况。
39.④
本发明仿生算法对表9进料成分下的以电石渣为最大消纳量废渣进行水泥进料的配比,见表11。
40.表11 仿生算法水泥配料解由上述实施案例,在表9的进料情况下,用excel线性/非线性规划法求解水泥配料寻不到解。而本发明仿生算法可以解决在用excel线性/非线性规划法求解水泥配料时无法满足三率值kh、sm和im均接近kh*、sm*和im*的问题,且能得到一个较为合理的废渣进料配比。
41.(3)传统遗传算法与本发明仿生算法求解水泥原料配比案例对比。
42.①
以普通遗传算法求得的水泥配料(不设置某固体废渣优先消纳目标的情况)用普通遗传算法产生的解是算法系统从随机初始值进行优化后的可能解,常常有多个近似解,例如将期望三率值输入计算模型后,得到8种工业废渣的配料比,一些典型的解见表12。
43.表12 遗传算法水泥配料解由上述实施案例,各解的kh、sm、im值大致可以满足kh*=kh=0.89,sm*=sm=2.1,im*=im=1.4的目标。解
①
和
②
中,可以看到电石渣和拌合料的进料比差别很大,解
②
和
③
比较可以观察到焚烧灰渣与硅石这两项的差别也较大,难以得到稳定生产需要的最佳配比数据。
44.列举两个以传统遗传算法得到的电石渣进料情况波动较大的水泥配比解,见表13。
45.表13 遗传算法水泥配料解由上述实施案例,解
①
和
②
中可见所有进料项的配比差别均较大,以此方法进行水泥配比的计算,各固废原料配比波动较大。对于我们的废渣水泥生产工艺来说,也不能实现水泥原料堆场里库存压力大的废渣的优先消纳目标和稳定生产。
46.②
优选地,以电石渣的最大程度为消纳量来进行此全工业废渣的水泥进料配比优化。以本发明基于仿生算法的非支配排序多目标进化算法求得兼顾趋近期望三率值和最大库存量废渣消纳量的唯一最优解,见表14。
47.表14 仿生算法水泥配料解由上述实施案例,实际计算出的三率值kh=0.89076,sm=2.0998,im=1.3985和期望三率值kh*=0.89,sm*=2.1,im*=1.4的误差很小,且各废渣进料不存在0%的情况,符合实际。与传统简单遗传算法计算得到的表4中各废渣原料进料相比较而言,可以采用历史进料数据作为初猜值,进料范围稳定,符合废渣堆量的实际情况,在本案例中可以实现以电石渣为主要消纳废渣的配料目标。
48.(4)传统遗传算法与本发明仿生算法求解水泥原料配比计算过程对比。
49.①
传统遗传算法计算案例。
50.优选地,以表2的进料组分为属性矩阵,设定期望三率值kh*=0.89,sm*=2.1,im*=1.4,设定遗传算法的最大迭代次数为300次。
51.以传统遗传算法算出的水泥配料比及计算时间和收敛时的迭代次数见表15。
52.表15 遗传算法水泥配料解和出解时间在上述实施例中,以传统遗传算法得出的水泥配比kh=0.88994,sm=2.1001,im=1.4002和期望三率值kh*=0.89,sm*=2.1,im*=1.4基本上相等,整个计算过程消耗118s,达到设定的最大遗传迭代次数300次,但仍小于收敛条件,结束计算,计算收敛。
53.②
本发明仿生算法计算案例。
54.优选地,以表2中的进料成分为例。
55.优选地,设定期望三率值kh*=0.89,sm*=2.1,im*=1.4,设定仿生算法的最大迭代次数为300次。
56.以本发明仿生算法算出的水泥配料比及计算时间和收敛时的迭代次数见表16。
57.表16 仿生算法水泥配料解和出解时间在上述实施例中,以传统遗传算法得出的水泥配比kh=0.89021,sm=2.99007,im=1.39913和期望三率值kh*=0.89,sm*=2.1,im*=1.4基本上相等,得到的最优解水泥配料比即是历史进料数据的配比。整个计算过程消耗30.8s,迭代至80次,计算达到收敛条件。
58.对比传统遗传算法和仿生算法,传统遗传算法采用的是随机数据为初猜值,据表14,计算时间和迭代次数较长才达到收敛。而本发明算法采用历史进料数据为初始种群,当期望三率值与进料数据计算出来的三率值相近时,历史进料数据可作初猜值,可以使得计算时间大大减小,并在较少的迭代次数内完成适应度函数迭代的收敛。
59.(5)用本发明的仿生算法计算传统硅酸盐水泥、水泥协同处置污泥和焚烧飞灰的进料配比案例。
60.①
用本发明算法程序对传统硅酸盐水泥原料配比方法的计算案例如下:设置期望三率值kh*=0.89,sm*=2.5,im*=1.5,得到的最优解见表17。
61.表17 仿生算法传统水泥配料解
序号/种类(%)石灰石黏土砂岩铁矿渣焚烧灰渣khsmim
①
80.0512.026.551.382.120.889612.501231.50014
由上述实施案例可见,kh、sm和im非常接近kh*、sm*和im*值,说明同样适用于传统硅酸盐水泥原料的配置。
62.②
用该算法对水泥协同处置制革污泥进行配料计算案例如下:某制革污泥中,各氧化物的比例为cao:12.81%,al2o3:5.69%,fe2o3:4.51%,sio2:3.85%,so3:0.35%。
63.传统硅酸盐水泥原料中掺入制革污泥后水泥制备的期望三率值为kh*=0.89,sm*=2.1,im*=1.4的配比方案见表18。
64.表18 仿生算法掺制革污泥水泥配料解
序号/种类(%)石灰石黏土砂岩铜渣制革污泥khsmim
①
86.822.749.120.820.50.890242.102321.49987
由上述实施案例可见,kh、sm和im非常接近kh*、sm*和im*值,本发明中基于仿生算法的水泥配料方法同样适用于水泥协同处置污泥。
65.③
用该算法对水泥协同处置焚烧飞灰进行配料计算案例如下:焚烧飞灰属于危废的一种,其处置方式之一就是掺入到水泥原料中进行协同处置。优选地,某生活垃圾焚烧飞灰中,各氧化物的比例为cao:10.95%,al2o3:23.19%,fe2o3:6.62%,sio2:42.22%,so3:4.22%。
66.以传统硅酸盐水泥原料掺入制革污泥的期望三率值为kh*=0.89,sm*=2.1,im*=1.4的配比方案见表19。
67.表19 仿生算法掺生活垃圾焚烧飞灰水泥配料解
序号/种类(%)石灰石石英砂页岩铜渣生活垃圾焚烧飞灰khsmim
①
82.909.990.002.105.010.890642.099571.50002
由上述实施案例可见,kh、sm和im非常接近kh*、sm*和im*值,本发明中基于仿生算法的水泥配料方法同样适用于水泥协同处置生活垃圾焚烧飞灰(危废)。
68.本领域的技术人员容易理解,以上所述仅为本发明的较佳实施例而已,并不用以限制本发明,凡在本发明的精神和原则之内所作的任何修改、等同替换和改进等,均应包含在本发明的保护范围之内。
再多了解一些
本文用于企业家、创业者技术爱好者查询,结果仅供参考。