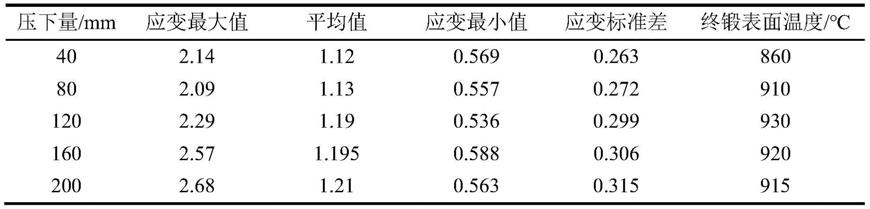
1.本发明属于钛合金加工技术领域,具体涉及一种基于数值模拟的钛合金锻造工艺优化方法。
背景技术:
2.钛合金由于其密度小、比强度高、耐热性好以及较好的低温性能等特点,已经在航空、航天、舰船及医疗等领域获得广泛应用。
3.传统工艺对钛合金锻造过程关键参数的确定往往是基于经验或实物检验测定。经验往往不针对具体材料与锻坯外形尺寸等,对锻造参数的确定存在较大随意性和偏差;而通过实物检验测定需实施物料的解剖分析,效率低且成本高。另外对于不同尺寸的坯料,也没有一个标准的工艺参数制定准则。
4.钛合金是一种对温度和应变非常敏感的材料,不同于传统金属材料,如钢铁,自古以来有“趁热打铁”之说。而对于钛合金,由于其热导率较低,变形过程产生的温升来不及散失,会导致坯料组织过烧,从而产生热裂、组织异常等缺陷,因此,工程中提出“控温打钛”。且随着坯料尺寸的增大,变形的不均匀性增大。
5.钛合金的加热和变形及其均匀性受温度场和应变场影响,表现在工件锻造过程中需对以下参数进行控制:加热温度、变形量(镦粗和拔长)、变形速率(镦粗和拔长)、变形方式(变形组合方式)。上述参数耦合作用,影响材料变形过程中的组织演化,进而影响最终组织的形态和力学性能。这是一个极其复杂的过程,很难通过有限数量的工艺试验来充分掌握。
6.锻造过程数值模拟技术,能够借助少量的试验测试,实现材料加热、变形和组织演变过程的预测,已经成为金属热加工工艺研究中一项重要的辅助手段,近年来得以快速发展并得到广泛应用。
7.有鉴于此,本发明人研究设计了一种基于数值模拟的钛合金锻造工艺优化方法,用以解决上述技术问题。
技术实现要素:
8.本发明的目的在于克服上述现有技术的缺点,提供一种基于数值模拟的钛合金锻造工艺优化方法,该方法基于材料在不同变形阶段建立本构方程,利用有限元计算方法得出坯料的温度场与应变场分布,根据锻坯尺寸和环境条件确定加热、冷却时间,再通过计算机数值模拟技术对坯料锻造过程中的温度场、应变场、再结晶与晶粒分布进行了准确的预测,结合锻坯锻造组合方式设计,可以快速有效的确定钛合金加工过程中的关键工艺参数,从而提高工艺制定的合理性、可靠性与工艺实施过程的稳定性。
9.本发明的目的是通过以下技术方案来实现的:
10.一种基于数值模拟的钛合金锻造工艺优化方法,建立材料在不同锻造阶段的本构方程;根据待加工材料的热物理性能参数、再结晶及晶粒长大动力学和冷却介质的换热系
数作为初始条件和边界定义,利用有限元计算方法得出锻坯的温度场与应变场分布,并根据物料尺寸确定加热、冷却时间和变形参数,从而实现锻造工艺的优化;
11.所述的热物理性能参数包括:密度、热传导系数、比热容;
12.所述的再结晶及晶粒长大动力学参数包括:温度、变形量、变形速率、变形组合方式。
13.进一步地,所述的有限元计算方法,采用但不限于有限元软件forge实现。
14.进一步地,基于hansel
‑
spittel模型采用forge软件描述材料在不同温度、不同应变速率、不同变形量条件下的流变行为;
15.获得材料在单相区和两相区的本构方程:
16.单相区材料本构方程:
[0017][0018]
双相区材料本构方程:
[0019][0020]
进一步地,所述的有限元计算方法,通过对物料加热过程、冷却过程、镦粗过程、拔长过程进行数值模拟分析,获取钛合金物料在锻造过程中各个部位的温度场与应变场分布数据。
[0021]
进一步地,所述冷却过程中,当钛合金物料处于开坯和成型阶段时,采用水冷方式冷却物料;当接近成品阶段时,采用空冷方式以保证产品质量。
[0022]
进一步地,所述镦粗过程和拔长过程中,镦粗锻比设定为1.5~1.9;镦粗速度设定为20mm/s~60mm/s;拔长压下量设定在80mm~160mm之间。
[0023]
进一步地,镦拔采用换向方式。
[0024]
进一步地,锻坯的单火次变形应不多于两镦两拔。
[0025]
与现有技术相比,本发明提供的技术方案包括以下有益效果:
[0026]
本发明基于数值模拟的钛合金锻造工艺优化方法,借助有限元模拟软件与常规实验,获得了钛合金(具体为ti6al4v)材料在加热和锻造变形过程中的温度场和应变场分布,快速、有效的确定了钛合金锻造过程中的加热、冷却和变形参数,提出了优化方案,提高了钛合金材料锻造工艺制定过程中的合理性、可靠性与经济性。
附图说明
[0027]
图1为本发明基于数值模拟的钛合金锻造工艺优化方法流程图;
[0028]
图2为实施例中计算得出的ti6al4v合金热传导系数和比热容随温度变化示意图;
[0029]
图3为实施例中坯料心部温度与加热时间和炉温的关系曲线图;
[0030]
图4冷却方式与冷却时间的关系曲线图;
[0031]
图5为实施例中坯料在不同变形速率条件下晶粒尺寸分布图;
[0032]
图6为实施例中坯料直镦直拔和换向镦拔心部截面应变分布图。
具体实施方式
[0033]
为使本发明的目的、技术方案和优点更加清楚明了,下面通过附图中示出的具体实施例来描述本发明。但是应该理解,这些描述只是示例性的,而并非限制本发明的范围。此外,在以下说明中,省略了对公知结构和技术的描述,以避免不必要的混淆本发明的概念。
[0034]
本实施例以直径为φ920mm的ti6al4v(tc4)钛合金铸锭开坯和锻造过程为例,该坯料初始截面尺寸大(大于621000mm2),初始晶粒为200mm柱状晶,最终产品为长条形矩形截面(截面积小于137000mm2)锻坯,长度大于3300mm,晶粒尺寸约30μm呈球状或短棒状且均匀不连续分布,实现该坯料的组织细化和均匀变形难度较大。通过数值模拟确定并优化工艺参数,包括以下步骤:
[0035]
步骤一、确定材料热变形过程中的本构方程
[0036]
为了更好描述材料的变形过程,采用gleeble热压缩试验获得ti6al4v(tc4)钛合金材料在不同应变、不同应变速率、不同温度下的应力应变数据。再对这些数据进行数学拟合处理,基于hansel
‑
spittel模型描述材料在不同温度、不同应变速率、不同变形量条件下的本构模型。分别获得ti6al4v(tc4)钛合金材料在单相区(>t
βtrans
)和两相区(<t
βtrans
)的本构方程如下:
[0037]
单相区材料本构方程:
[0038][0039]
双相区材料本构方程:
[0040][0041]
步骤二、确定材料的热物理性能参数
[0042]
借助材料热力学计算软件jmatpro对ti6al4v(tc4)钛合金材料的各项热物理性能参数进行计算,包括密度、热传导系数、比热容,由于这些参数是与温度相关的,实际计算出的一条性能参数与温度的曲线,如图2列出了计算得出的热传导系数与比热容随温度变化的关系图;对于tc4钛合金在变形过程中的热传导系数、辐射系数可以基于现有的大量参考文献,也可以根据实际生产的数据逆向反推有限模拟合理的热力学参数,比如生产实际积累大量不同规格材料加热到不同温度的热透时间,可以用专业锻造软件forge模拟上述锻坯加热过程,反复调教换热系数,使得模拟结果与实际结果相吻合,这样可以获得比较符合实际情况的换热系数。
[0043]
步骤三、确定加热、冷却和变形参数及变形方式对锻造过程温度场、应变场、再结晶及晶粒分布的关系
[0044]
运用有限元计算方法进行模拟,通过对本实施例物料加热过程、冷却过程、镦粗过程、拔长过程进行数值模拟分析,获取物料在锻造过程中各个部位的温度场与应变场分布数据,具体过程如下:
[0045]
1)物料加热过程中,热透时间受物料尺寸、炉子设定温度的影响,如图3所示,当炉温接近设定温度时(10℃以内),升温缓慢且很难达到设定值(低于设置温度1~3℃),适当提高设定温度能有效缩短加热过程的高温停留时间;
[0046]
2)本实施例分别对锻造中间坯采用水冷或空冷进行分析,如图4所示,同等坯料温度条件下,水冷比空冷节约一半的冷却时间,但在水冷条件下,材料各部分温度梯度较大,会产生较大的残余应力。为了加快生产流程和细化晶粒,开坯和成型火次以外的其他火次可以采用水冷方式进行冷却;
[0047]
3)镦粗过程中,镦粗锻比影响锻坯动态再结晶体积分数和晶粒尺寸,当锻比为1.5时,锻坯心部动态再结晶呈现明显区域分布,心部平均晶粒尺寸为280~320μm,随锻比增加至1.9,锻坯心部平均晶粒尺寸为200~240μm,在工艺允许范围内适当增加镦粗锻比有利于坯料锻透性提高和晶粒尺寸细化。另外如图5所示,镦粗速率影响变形抗力和晶粒分布,当镦粗速度从20mm/s上升到60mm/s时(对应的坯料中心截面的应变速率为0.02~0.1s
‑1之间),材料的变形抗力峰值应力从1133吨增加至1341吨,锻造能耗增加,平均晶粒尺寸分布区域化趋势明显;但变形速率在20~60mm/s范围内变化时,对材料变形均匀性影响不明显,但镦粗速率过低会导致镦粗时间增加;
[0048]
4)拔长过程中,如下表一所示,拔长压下量影响坯料的变形均匀性及微观组织演变。随着拔长压下量增加,应变的最大值和平均值不断增加,应变标准差也不断增大,变形不均匀程度加剧,平均晶粒尺寸减小。设置变形温度为1100℃,压机速率40mm/s,初始晶粒尺寸1000μm的坯料,在单次压下量小于40mm时,坯料无法锻透;压下量大于160mm时,坯料表面在砧子交界处出现折叠损伤。压下量从80mm增加到160mm对平均晶粒尺寸影响不明显,因此,在工艺允许范围内,适当提高拔长压下量有利于细化晶粒,提高锻坯的整体性能;
[0049]
表1不同压下量坯料应变场参数及表面终锻温度
[0050][0051]
值得注意的是,本实施例在进行数值模拟过程中,发现换向镦拔有利于提升坯料的变形均匀性。具体如图6所示,换向镦拔有利于提升坯料端部变形量,相比于直镦直拔,换向镦拔可将应变分布标准差从0.79降低至0.68,提升了变形均匀性和组织均匀性。
[0052]
最后,验证了火次与镦拔次数影响坯料的应变场和温度场分布的情况,具体数据如下表2所示,1火内完成的镦拔次数影响坯料的应变场和温度场分布,镦拔次数增加,应变场和温度场的不均匀性增加。一火完成三镦三拔坯料表面温度下降较多,应变和温度分布不均匀性最大,坯料表面质量差,需增加打磨工序;三火完成三镦三拔表面成形质量最好,温度和应变的标准差最小,但是加热次数多会影响生产效率。综合考虑锻造成本和成形质量,应选择每火次完成两镦两拔。
[0053]
表2不同镦拔方案参量数值统计
[0054][0055]
步骤四、获得优化的锻造工艺流程及工艺参数
[0056]
本实施例为厚大截面坯料的锻造工艺和参数优化,本实施例初始材料为大规格ti6al4v铸锭,目标为经过充分和均匀变形的长、薄特征锻坯。经本实施获悉:1、钛合金材料的加热和冷却过程受环境影响,不同冷却方式影响坯料的温度场和应力场分布从而影响产品质量,钛合金开坯阶段,残余应力也可以通过后序锻造过程释放,采用水冷方式冷却物料,可以加快生产流程和细化晶粒,接近成品阶段应采用空冷方式以保证产品质量;2、变形量和变形速率通过影响变形过程中的温度场和应变场而对物料的变形均匀性和平均晶粒尺寸及分布产生影响,镦粗锻比为1.9时,物料心部平均晶粒尺寸约200~240μm,在工艺范围内应适当增加镦粗锻比,可以提高物料锻透性;拔长压下量在80mm~160mm之间,平均晶粒尺寸变化不大,可适当提高拔长压下量以便细化晶粒;镦粗速度20mm/s~60mm/s(对应的物料中心截面的应变速率为0.02s
‑
1~0.1s
‑
1)可以实现物料较均匀变形;3、提高锻坯的整体性能变形方式和变形组合方式,影响坯料的变形均匀性和组织均匀性,单火次变形应不多于两镦两拔。
[0057]
以上内容是结合具体的优选实施方式对本发明所作的进一步详细说明,不能认定本发明的具体实施只局限于这些说明。对于本发明所属技术领域的普通技术人员来说,在不脱离本发明构思的前提下,还可以做出若干简单推演或替换,都应当视为属于本发明的保护范围。
再多了解一些
本文用于企业家、创业者技术爱好者查询,结果仅供参考。