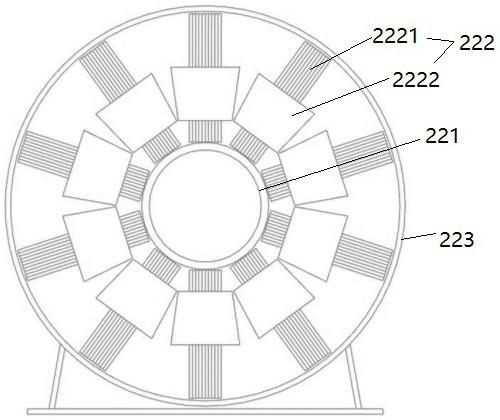
1.本发明涉及一种退磁装置,特别是涉及一种高密度多单元组合磁场退磁机。
背景技术:
2.钢管经磁粉探伤后通常具有剩磁,剩磁的存在会引起钢管焊接时产生飞弧,从而影响焊接质量,通过退磁工序,可以有效降低剩磁。
3.现有的退磁机多采用交流电框式线圈,如公开号为cn113035496a、cn112802653a的中国专利公开的技术方案都采用了框式线圈。当框式线圈用于退磁作业时,由于磁力线较为分散,存在很大漏磁,导致作用于钢管的磁力线强度较弱,经框式线圈退磁后的钢管剩磁仍然较高,严重影响焊接质量。
4.公开号为cn210073537u的中国专利公开了一种钢管退磁装置,使得退磁线圈与钢管间距离可调整,并通过钢管在轴向输送的同时进行自转而使上下两端的钢管退磁更彻底。
技术实现要素:
5.针对上述现有技术缺陷,本发明的任务在于提供一种高密度多单元组合磁场退磁机,解决钢管退磁后剩磁高的问题。
6.本发明技术方案如下:一种高密度多单元组合磁场退磁机,包括进料滚道、退磁机构和出料滚道,所述进料滚道和所述出料滚道驱动管件轴向运动以穿过所述退磁机构,所述退磁机构包括管件通道和若干并联工作的退磁线圈,所述管件通道供所述管件轴向穿过,所述退磁线圈周向分布于所述管件通道的四周,所述退磁线圈包括c形磁轭和线圈,所述c形磁轭包括两个侧边和连接边,两个所述侧边上分别绕设有所述线圈,所述c形磁轭的开口朝向所述管件通道设置,同一个所述退磁线圈的两个所述线圈处于所述管件通道的不同截面,所述截面垂直于所述管件通道的轴向。
7.进一步地,所述退磁线圈以所述管件通道的径向布置,所述c形磁轭的连接边平行于所述管件通道的轴线。
8.进一步地,所述线圈为锥形线圈,所述锥形线圈的匝数由靠近所述管件通道的一端向远离所述管件通道的一端增加。
9.进一步地,所述退磁线圈等分分布于所述管件通道的四周。
10.进一步地,所述退磁线圈设有8至12个。
11.进一步地,所述退磁机构包括升降机构,所述升降机构用于驱动所述退磁线圈和所述管件通道共同升降以调整所述管件通道的轴线与所述进料滚道及所述出料滚道的支撑面的相对高低。通过退磁线性和管件通道的高低调节,使得不同的管件在退磁时都能处于管件通道的中心位置,达到最佳的退磁效果。
12.进一步地,所述进料滚道和所述出料滚道均包括有滚轮和调速驱动机构,所述调速驱动机构用于驱动所述滚轮转动,所述滚轮的周面用于支承所述管件。调速驱动机构可
控制滚轮的转速从而调节管件的轴向输送速度,实现最佳的退磁效果。
13.进一步地,所述滚轮为中间低、两端高的v型滚轮。v型滚轮可减少管件在输送时的偏移,使得管件在通过退磁机构时位置稳定,保证退磁效果。
14.本发明与现有技术相比的优点在于:c形磁轭在管件通道周向布置且两个线圈处于不同截面,线圈产生的磁力线指向工件,使线圈空间磁力线集中作用于工件,增强了磁力线对工件(如钢管)的作用强度和深度,实现高纯净退磁。
15.退磁机构设置升降机构,调整退磁线圈及管件通道的上下高度,保证进料滚道、出料滚道上管件与管件通道的中心的对齐,由调速驱动机构根据管件的直径,控制进料滚道、出料滚道转速,实现不同直径管件的最佳退磁效果。
附图说明
16.图1为实施例的高密度多单元组合磁场退磁机的结构示意图。
17.图2为进料滚道和出料滚道结构示意图。
18.图3为退磁线圈结构示意图。
19.图4为退磁组件结构示意图(主视)。
20.图5为退磁组件结构示意图(侧视)。
21.图6为退磁线圈与管件的磁场示意图。
具体实施方式
22.下面结合实施例对本发明作进一步说明,但不作为对本发明的限定。
23.请结合图1至图5所示,本实施例所涉及的一种高密度多单元组合磁场退磁机包括进料滚道1、退磁机构2和出料滚道3。进料滚道1和出料滚道3分别设置在退磁机构2的两侧,待退磁的管件4由进料滚道1、出料滚道3承载并进行轴向输送,管件在进料滚道1的带动下,头端穿过退磁机构2后再由出料滚道3承载,并持续轴向运动至整个管件穿过退磁机构2完成退磁。
24.请结合图2所示,进料滚道1和出料滚道3都由若干个滚轮单元构成,滚轮单元可分为主动单元和被动单元,以主动单元为例,其包括滚轮5、减速箱6、调速驱动机构7。调速驱动机构7一般为电机,电机由变频器控制转速,再通过减速箱6与滚轮5的转轴连接。滚轮5的转轴通过支架设置在底座8上,滚轮5采用中间低、两端高的v型滚轮,管件在v型滚轮上输送时,保证管件4位置的稳定。主动单元上可设置滚道的启动控制器9,另外也可设置工件识别传感器10进行自动启停控制。被动单元则可仅设置v型滚轮,与主动单元间隔设置,达到充分支撑管件4的目的。主动单元与被动单元配合,使管件4以水平方向进行轴向的输送。
25.退磁机构2包括升降机构21及退磁组件22,升降机构21可以采用现有技术的电动、液压驱动的升降结构。由于待退磁的管件4的直径不同,因此管件4由进料滚道1和出料滚道3支承时,其中心高度会有所变化,为了使管件4中心能够与退磁组件22的中心对齐,升降机构21使退磁组件22的高度得以变化以适应不同直径的管件4,来提高退磁效果。
26.退磁组件22包括管件通道221和若干并联工作的退磁线圈222,退磁线圈22可设置8至12个,过少的退磁线圈222难以形成强度均匀的磁场,过多的退磁线圈222则难以有效布
置。如图4、图5所示,管件通道221处于中央供管件4轴向穿过,退磁线圈222周向等分分布于管件通道221的四周。请结合图3,退磁线圈222包括c形磁轭2221和锥形线圈2222,c形磁轭2221由多层硅钢片叠成,其包括两个侧边2221a和连接边2221b,两个侧边2221a上分别绕设有锥形线圈2222。c形磁轭2221的开口朝向管件221通道设置,退磁线圈222以管件通道221的径向布置,c形磁轭2221的连接边2221b平行于管件通道的轴线,使得同一个退磁线圈222的两个锥形线圈2222处于管件通道221的不同截面,截面垂直于管件通道221的轴向。也就是说单个退磁线圈222上的两个锥形线圈2222处于管件通道221的不同轴向位置,并且两个锥形线圈2222的连线与管件通道221的轴向平行。在退磁线圈222的最外围通过不锈钢制成环状壳体223以固定退磁线圈222。退磁线圈222形成的磁场及在管件4上作用的示意图如图6所示,退磁线圈222的并联是指所有的退磁线圈222的c形磁轭2221上靠近进料滚道1一端的锥形线圈2222所形成的磁场方向均相同,靠近出料滚道3一端的锥形线圈2222所形成的磁场方向也均相同并与靠近进料滚道1一端的锥形线圈2222所形成的磁场方向相反。如此设置的多个退磁线圈222,增强了磁力线对管件4的作用强度和深度,实现高纯净退磁。
27.以下实施例为本发明高密度多单元组合磁场退磁机进行钢管退磁作业的试验。
28.实施例1,c形磁轭2221结构尺寸为:a=220mm,b=140 mm,h=30 mm,硅钢片数量为10,锥形线圈尺寸:上底为φ40 mm,下底为φ80 mm,高度为100 mm,锥形线圈2222匝数为800。共设置10个退磁线圈222,相邻的退磁线圈222的夹角为36
°
,对规格为φ100
×
9000的钢管进行退磁作业,设置进料滚道1和出料滚道3的速度为115转/分,调整锥形线圈2222电流为6a,退磁后的钢管经测试剩磁为3.2gs。设置进料滚道1和出料滚道3的速度为10转/分时,退磁后的钢管经测试剩磁为3.1gs。设置进料滚道1和出料滚道3的速度为240转/分时,退磁后的钢管经测试剩磁为3.4gs。
29.实施例2,c形磁轭2221结构尺寸为:a=230mm,b=160 mm,h=30 mm,硅钢片数量为12,锥形线圈2222尺寸:上底为φ50 mm,下底为φ100 mm,高度为100 mm,锥形线圈2222匝数为1000。共设置12个退磁线圈222,相邻的退磁线圈222的夹角为30
°
,对规格为φ100
×
9000的钢管进行退磁作业,设置进料滚道1和出料滚道3的速度为115转/分,调整锥形线圈电流为4a,退磁后的钢管经测试剩磁为3.1gs。设置进料滚道1和出料滚道3的速度为10转/分时,退磁后的钢管经测试剩磁为3.0gs。设置进料滚道1和出料滚道3的速度为240转/分时,退磁后的钢管经测试剩磁为3.5gs。
再多了解一些
本文用于创业者技术爱好者查询,仅供学习研究,如用于商业用途,请联系技术所有人。