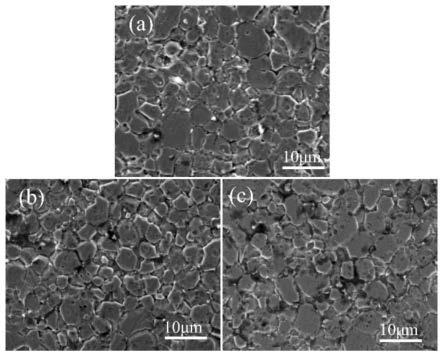
一种高性能薄片r-t-b稀土永磁体的制备方法
技术领域
1.本发明涉及一种高性能薄片r-t-b稀土永磁体的制备方法,属于稀土磁体领域。
背景技术:
2.晶界扩散能够在基本不降低r-t-b磁体剩磁的情况下显著的提高磁体的矫顽力,因此采用晶界扩散技术可以制备高剩磁、高矫顽力的r-t-b稀土永磁体。晶界扩散前磁体基体要经过机加工处理,这导致磁体表面存在油污、锈斑和表面氧化层等缺陷。为保证扩散源涂层与基体的结合强度以及扩散后磁体磁性能的提升效果需要对磁体进行表面处理,在实际生产过程中通常采用酸洗的方式去除磁体表面油污、锈斑和氧化层。
3.r-t-b稀土永磁体主要由主相r2t
14
b和晶界富r相组成,由于晶界富r相的电负性更高,在酸洗时会优先腐蚀。经过酸洗后磁体表面会出现宏观腐蚀深度小于晶界相腐蚀深度的腐蚀形貌,导致主相晶粒间具有一定宽度和深度的间隙。通过控制酸洗工艺使酸洗后主相晶粒间存在合适深度的间隙能够确保磁体表面氧化层被充分去除。此外,主相晶粒间合适深度的间隙能够提高晶界扩散源涂层与磁体基体的结合力,防止磁体在转运过程中因受力而导致晶界扩散源涂层从磁体表面脱落。但是当腐蚀量过大时,主相晶粒间的间隙会加深,这会造成磁体表层主相晶粒与磁体基体的结合力减弱,磁体表面结构呈疏松状态。当晶界扩散源涂层覆盖在这层疏松层上时,由于磁体表层晶粒与基体的结合力减弱,磁体转运过程中受力时容易导致磁体表层晶粒和附在其上的晶界扩散源涂层一起脱落。此外,晶界扩散过程中处于熔融状态的晶界富r相是原子扩散的快速通道。晶界富r相腐蚀量太大时,晶界扩散源涂层与磁体的晶界富r相间存在较大间隙,阻碍扩散源原子的晶界扩散过程,降低晶界扩散效率。从而导致扩散源在磁体表面堆积,诱发体扩散的产生,最终降低扩散磁体的磁性能。
4.在实际生产过程中,通过pvd后,在进行高温晶界扩散时,磁体由于表面活性较高,磁体间低熔点金属互熔而经常产生粘片的现象,会造成磁片在分开过程由于剧烈碰撞产生缺角,并使磁片外观尺寸变差,产品合格率降低,增加废片率,增大了损耗成本。
5.通过调控磁体酸洗工艺,使磁体表层晶界富r相有合适的腐蚀深度,能够充分去除磁体表面氧化层,提高磁体的晶界扩散效果。此外,磁体表层晶界富r相合适的腐蚀深度能够提高晶界扩散源涂层与磁体基体的结合强度,减少磁体转运过程中扩散源涂层从磁体表面脱落的情况,从而提高最终产品性能的一致性,提高产品的合格率。通过加入低浓度酸性表面钝化剂使得磁体表面形成钝化薄膜,防止磁体在进行扩散时效处理时产生粘片现象。
技术实现要素:
6.针对r-t-b稀土永磁体酸洗不充分时磁体表面氧化层去除不彻底,晶界扩散源涂层与基体的结合力弱;酸洗时间太长时晶界富r相腐蚀深度增大,虽然晶界扩散源涂层与磁体表面的结合力增强但磁体表层主相晶粒与基体的结合力减弱,扩散源涂层容易随磁体表面主相晶粒脱落而导致产品性能一致性低、扩散后磁性能低和产品合格率低的不足,本发
明提供了一种高性能薄片r-t-b稀土永磁体的制备方法。
7.本发明采用的技术方案如下:
8.一种高性能薄片r-t-b稀土永磁体的制备方法,所述方法包含以下步骤:
9.(1)将磁体基体加工成厚度为0.5~10.0mm的磁片,在室温条件下将磁片置于酸洗液中超声酸洗10~180s,随后用清水超声清洗1~5min后烘干,所述酸洗液为含有0.1~5vol%酸性表面钝化液和1.0~10vol.%硝酸的水溶液;得到酸洗处理后的磁片;
10.(2)在酸洗处理后的磁片表面沉积重稀土元素扩散层;
11.(3)表面沉积扩散源的磁片进行晶界扩散处理,制得所述高性能薄片r-t-b稀土永磁体。
12.所述步骤(1)中,所述酸性表面钝化液为不锈钢酸洗钝化液。不锈钢酸洗钝化液通常是以环保无机酸氧化剂为主剂、添加羟基酸化合物高效缓蚀剂和抑雾剂等复配而成,采用市售的不锈钢酸洗钝化液即可。本发明优选采用广东凯盟钝化防锈技术有限公司的酸洗钝化液id4008或dh365h。
13.所述步骤(1)中的酸洗过程为在室温条件下将磁片置于酸性表面钝化液浓度为0.1~5vol%和硝酸浓度为1~4vol.%的酸洗液中超声酸洗100~180s;或为在室温条件下将磁片置于酸性表面钝化液浓度为0.1~5vol%和硝酸浓度为4~8vol.%的酸洗液中超声酸洗50~100s;或为在室温条件下将磁片置于酸性表面钝化液浓度为0.1~5vol%和硝酸浓度为8~10vol.%的酸洗液中超声酸洗10~50s。
14.酸洗液中酸性表面钝化液浓度为0.1~5vol%和硝酸浓度为1vol.%时,超声酸洗180s;酸洗液中酸性表面钝化液浓度为0.1~5vol%和硝酸浓度为4vol.%时,超声酸洗100s;酸洗液中酸性表面钝化液浓度为0.1~5vol%和硝酸浓度为8vol.%时,超声酸洗50s;酸洗液中酸性表面钝化液浓度为0.1~5vol%和硝酸浓度为10vol.%的酸洗液中超声酸洗10s。
15.所述磁片酸洗前后表面维氏硬度满足1.05≤h1/h2≤1.25,h1为酸洗前磁片表面维氏硬度,h2为酸洗后磁片表面维氏硬度;
16.所述酸洗处理后的磁片中,表面晶界富r相腐蚀深度为0.1~0.4倍磁体表面两主相晶界深度。
17.所述步骤(1)中的磁体基体通过真空感应熔炼甩带、氢破、气流磨、取向成型、等静压、真空烧结、高温一级时效和低温二级时效制得。采用本领域公知的制备方法制备得到磁体基体。
18.一般采用机加工的方式将磁体基体加工成厚度为0.5~10.0mm的磁片。
19.所述步骤(2)中,优选采用蒸镀、磁控溅射或多弧离子镀膜的方式在酸洗处理后的磁片表面沉积重稀土元素扩散层。
20.所述步骤(2)中,重稀土元素扩散层的厚度优选为3~100μm。
21.所述步骤(2)中,重稀土扩散源为纯重稀土元素金属、重稀土元素氢化物或重稀土元素与其他金属元素的合金,所述重稀土元素为dy、tb或ho中的至少一种。
22.所述步骤(2)中,优选在磁体垂直于取向方向的表面覆盖重稀土扩散源,在磁体不垂直于取向方向的表面优选不覆盖重稀土扩散源。
23.所述步骤(3)中,晶界扩散的扩散温度为800~1000℃,保温时间为5~25h,保温结
束后冷却至200℃以下后再升温至400~650℃,保温2~10h,制得所述高性能薄片r-t-b稀土永磁体。
24.所述步骤(3)中,晶界扩散处理达到扩散温度后炉内绝对真空度为10-2
~10-5
pa。
25.本发明采用真空感应熔炼甩带、氢破、气流磨、取向成型、等静压、真空烧结、高温一级时效和低温二级时效制备基体磁体。采用机加工的方式将基体磁体加工成厚度为0.5~10.0mm的磁片,在室温条件下将磁片置于酸性表面钝化液浓度为0.1~5vol%和硝酸浓度为1.0~10.0vol.%水溶液中超声酸洗10~180s,随后用清水超声清洗1~5min后烘干。采用蒸镀、磁控溅射或多弧离子镀膜的方式在磁片表面沉积厚度为3~100μm的重稀土元素扩散层,然后进行晶界扩散处理。扩散温度为800~1000℃,保温时间为5~25h,保温结束后冷却至200℃以下后再升温至400~650℃,保温2~10h,制得高性能薄片r-t-b稀土永磁体。
26.磁体经机加工后表面会存在较多的油污、锈斑和氧化层,这些表面杂质会影响晶界扩散源涂层与磁体的结合力,也会降低晶界扩散对矫顽力的提升效果。因此磁体表面沉积扩散源涂层前一般会采用酸洗的方法进行表面处理。酸洗时控制磁体的腐蚀量非常重要。当酸洗时间太短、磁体表层腐蚀量太少时,虽然可以通过目视的方法保证磁体表面油污和锈斑被充分去除,但是很难确保磁体表面氧化层被彻底清除。表面氧化层会阻碍重稀土原子的晶界扩散过程,最终影响磁体的磁性能。同时,当磁体表面的腐蚀量较小时,磁体表面比较光滑,晶界扩散源涂层与磁体基体的结合力较弱。在后续产品转运过程中,磁体受力时晶界扩散源涂层容易从磁体表面脱落。
27.晶界富r相的电负性较主相更高,提高酸浓度或延长酸洗时间时,晶界富r相会优先腐蚀。经酸洗后磁体表面会出现宏观腐蚀深度小于晶界富r相腐蚀深度的腐蚀形貌,导致主相晶粒间具有一定宽度和深度的间隙。通过增大磁体表面的腐蚀量可以保证磁体表面的氧化层彻底去除。此外,主相晶粒间存在较大深度的间隙能够提高晶界扩散源涂层与磁体基体的结合力,防止磁体在转运过程中晶界扩散源涂层从磁体表面脱落。在实际生产过程中,通过pvd后再进行扩散的磁体由于表面活性较高,磁体间低熔点金属互熔而产生粘片的现象,会造成磁片在分开过程由于剧烈碰撞产生缺角,并使磁片外观尺寸变差。磁体晶界富r相腐蚀量会进一步增加时,磁体表层主相晶粒与基体的结合力减弱,导致磁体表层的主相晶粒容易脱落。因此虽然主相晶粒间一定深度的间隙有利于提高扩散源涂层与磁体表面的结合力,但由于磁体表层主相晶粒与基体的结合力减弱,磁体受力时晶界扩散源涂层容易随着表层主相晶粒一起脱落。导致晶界扩散后磁体的磁性能较差,合格率较低。
28.此外,晶界扩散过程中熔融的晶界富r相是原子扩散的快速通道,当主相晶粒间存在太大深度的间隙时,晶界扩散源涂层与磁体表层晶界富r相的距离较大,会影响晶界扩散速率,导致晶界扩散源在磁体表面大量堆积,诱发体扩散的产生,降低磁体扩散后的磁性能。本发明通过实验发现,当酸洗后磁体表面晶界富r相的腐蚀深度为0.1~0.4倍磁体表面两主相晶界深度时能够充分去除磁体表面氧化层,同时主相晶粒间该深度范围的间隙能够增强晶界扩散源涂层与磁体表面的结合力。此外,剩余的晶界富r相可以保证磁体表面主相晶粒与基体的结合力,确保晶界扩散源涂层不会因磁体表层主相晶粒受力而随同其一起脱落。实现既能够提高生产效率,又能够提高磁体的晶界扩散效果的目的。
29.在实际生产中如果采用金相或sem观察晶界富r相的腐蚀深度时,由于操作较为繁琐,会严重影响生产效率。本发明通过实验发现磁体晶界富r相的腐蚀深度与磁体表面的维
氏硬度存在显著联系。当磁体表面晶界富r相的腐蚀深度小于0.1倍的磁体表面两主相晶界深度时,酸洗前后磁体表面维氏硬度满足1.0≤h1/h2≤1.05;当磁体表面晶界富r相的腐蚀深度为0.1~0.4倍的表面两主相晶界深度时,酸洗后磁体的表面维氏硬度满足1.05≤h1/h2≤1.25;当磁体表面晶界富r相的腐蚀深度大于0.4倍的表面两主相晶界深度时,酸洗后磁体的表面维氏硬度满足h1/h2》1.25,其中h1为酸洗前磁体表面维氏硬度,h2为酸洗后磁体表面维氏硬度。因此,在实际生产过程中,可以通过磁体表面硬度变化来表征晶界富r相的腐蚀程度,实现合理控制晶界富r相腐蚀深度的同时提高生产效率。
30.磁体酸洗时,酸的浓度和酸洗时间会影响磁体腐蚀速度,因此需要对两者进行调控从而控制表层晶界富r相的腐蚀深度。本发明中采用在室温条件下将磁片置于酸性表面钝化液浓度为0.1~5vol%和硝酸浓度为1~4vol.%的酸洗液中超声酸洗100~180s;或为在室温条件下将磁片置于酸性表面钝化液浓度为0.1~5vol%和硝酸浓度为4~8vol.%的酸洗液中超声酸洗50~100s;或为在室温条件下将磁片置于酸性表面钝化液浓度为0.1~5vol%和硝酸浓度为8~10vol.%的酸洗液中超声酸洗10~50s,保证磁体表层晶界富r相合适的腐蚀深度。
31.为保证晶界扩散源涂层与基体的结合力,本发明优选采用蒸镀、磁控溅射或多弧离子镀膜的方式在磁片表面沉积厚度为3~100μm的重稀土元素扩散层,重稀土扩散源为纯重稀土元素金属、重稀土元素氢化物或重稀土元素与其他金属元素的合金,所述重稀土元素为dy、tb或ho中的至少一种。r-t-b磁体晶界扩散存在各向异性,即沿着磁体取向方向的扩散速率较高,而沿垂直于磁体取向方向的晶界扩散速率较低。在本发明中,为了保证晶界扩散后磁体的矫顽力增量,垂直于磁体取向方向的表面必须涂覆晶界扩散源。虽然磁体其他表面涂覆晶界扩散源同样能够提高磁体的矫顽力,但由于该方向上晶界扩散速率较慢,会诱发体扩散的产生,导致磁体剩磁降低量增加。因此在本发明中优选磁体其他表面不沉积晶界扩散源层。
32.本发明的有益效果在于:通过控制酸洗工艺,将磁体表层晶界富r相的腐蚀深度控制在0.1~0.4倍的表面两主相晶界深度,保证机加工后磁体表面油污、锈斑和氧化层能彻底去除,同时确保磁体表层剩余晶界r相与晶界扩散源涂层的连续性,从而提高磁体的晶界扩散效果。酸洗后磁体表面主相晶粒间合适深度的腐蚀间隙能够增强晶界扩散源涂层与磁体的结合力,确保磁体转运过程中晶界扩散源涂层不会因受力从磁体表面脱落,获得高性能、高一致性、高合格率的产品。此外,本发明通过建立磁体表面维氏硬度与晶界富r相腐蚀深度的关系,可以采用酸洗前后磁体表面硬度变化表征磁体表层晶界富r相的腐蚀深度,简化测试流程,显著提高生产效率。通过加入低浓度酸性表面钝化剂使得磁体表面形成钝化薄膜,防止磁体在进行高温晶界扩散和时效处理时产生粘片现象。
附图说明
33.图1为实施例一中不同磁体酸洗后表面sem二次电子像,图中(a)、(b)、(c)分别为实验no.1、实验2no.和实验no.4磁体酸洗后表面sem二次电子像。
34.图2为磁体表面晶界富r相不同腐蚀深度时晶界扩散源涂层与基体结合情况的示意图,其中(a)、(b)、(c)分别为磁体表面晶界富r相腐蚀深度低于本发明推荐范围、处于本发明推荐范围和高于本发明推荐范围时晶界扩散源涂层与基体结合情况的示意图。
35.图3为实施例二中不同磁体酸洗后表面sem二次电子像,图中(a)、(b)、(c)分别为实验no.10~实验no.12磁体酸洗后表面sem二次电子像。
36.图4为实施例四中不同磁体酸洗后表面sem二次电子像,图中(a)、(b)、(c)分别为实验no.16~实验no.18磁体酸洗后表面sem二次电子像。
具体实施方式
37.下面结合具体实施例对本发明的技术方案进行进一步说明,但本发明的保护范围不限于此。
38.采用真空感应熔炼甩带、氢破、气流磨、取向成型、等静压、真空烧结、高温一级时效和低温二级时效制备基体磁体。
39.采用机加工的方式将磁体基体加工成厚度为0.5~10.0mm的磁片,在室温条件下将磁片置于酸洗液中超声酸洗10~180s,随后用清水超声清洗1~5min后烘干,所述酸洗液为添加0.1~5vol%酸性表面钝化液和1.0~10vol.%硝酸的水溶液。
40.采用蒸镀、磁控溅射或多弧离子镀膜的方式在磁片表面沉积厚度为3~100μm的重稀土元素扩散层。重稀土扩散源为纯重稀土元素金属、重稀土元素氢化物或重稀土元素与其他金属元素的合金,重稀土元素为dy、tb或ho中的至少一种。磁体垂直于取向方向的表面必须沉积重稀土元素晶界扩散源,磁体其他表面优选为不沉积重稀土元素晶界扩散源。
41.将沉积了扩散源涂层的磁体加热到800~1000℃,进行晶界扩散处理。达到最高温度后炉内真空度应高于10-2
pa,保温5~25h。保温结束后冷却至200℃以下,再升温至400~650℃,保温2~10h,制得高性能薄片r-t-b稀土永磁体。
42.采用喷砂工艺对最终磁体进行表面处理,去除表面残留的扩散源涂层后采用nim磁性能测试设备测量磁体磁性能,采用icp测量磁体成分。采用维氏硬度计测量酸洗前后磁体表面维氏硬度,采用sem观察磁体表面腐蚀形貌,采用激光共聚焦显微镜测量磁体表面晶界富r相的腐蚀深度。采用百格实验测试晶界扩散源涂层与磁体基体的结合力,每个实验组测试20只产品的结合力,以扩散源涂层脱落面积《5%作为合格标准,计算合格率。
43.实施例一:
44.将成分为nd
23
pr7b
0.95
ga
0.15
cu
0.15
zr
0.2
fe
68.55
(质量比)配料后采用真空感应熔炼甩带、氢破、气流磨、取向成型、等静压、真空烧结、高温一级时效和低温二级时效制备基体磁体。
45.采用机加工的方式将磁体基体加工成长
×
宽
×
高为10mm
×
10mm
×
3mm的磁片,高度方向为磁体取向方向。在室温条件下将磁片置于添加不同比例酸性表面钝化液和硝酸的酸洗液中超声酸洗80s,随后用清水超声清洗1min后烘干。采用的酸性表面钝化液为广东凯盟钝化防锈技术有限公司生产的酸洗钝化液id4008。
46.采用多弧离子镀膜的方式在磁片垂直于取向方向的表面沉积厚度为10μm的纯tb扩散源层,其他表面不沉积重稀土元素扩散源。
47.将沉积了扩散源涂层的磁体加热到910℃,进行高温晶界扩散。达到最高温度后炉内绝对真空度为10-2
pa~10-5
pa,保温10h。保温结束后以不低于80℃/min的冷速冷却至磁体温度低于200℃。随后将磁体加热至520℃,保温3h。保温完成后以不低于80℃/min的冷速冷却至低于200℃。
48.采用喷砂工艺对最终磁体进行表面处理,去除表面残留的扩散源涂层后采用nim磁性能测试设备测量磁体磁性能,采用icp测量磁体成分。采用维氏硬度计测量酸洗前后磁体表面维氏硬度,采用sem观察磁体表面腐蚀形貌,采用激光共聚焦显微镜测量磁体表面晶界富r相的腐蚀深度。激光共聚焦显微镜测量材料表面微区的粗糙度,从粗糙度检测得到两主相晶界深度。采用百格实验测试晶界扩散源涂层与磁体基体的结合力,每个实验组测试20只产品的结合力,以扩散源涂层脱落面积《5%作为合格标准,计算合格率。
49.实验no.1~实验no.9酸洗时的硝酸浓度、酸洗表面钝化剂的体积浓度最终磁体tb含量、磁体室温(20℃)磁性能如表1所示:
50.表1
[0051][0052]
从表1数据可知,硝酸浓度、酸洗表面钝化剂的体积浓度处于本发明推荐范围内时(0.1~5vol%酸性表面钝化液和1.0~10vol.%硝酸),经过晶界扩散后磁体tb含量较高,剩磁和矫顽力均处于较高水平。当硝酸浓度、酸洗表面钝化剂的体积浓度在本发明推荐范围外时,由于磁体表面氧化层清除不彻底、晶界富r相腐蚀深度太大或磁片表面钝化膜厚度较厚,影响晶界扩散效果,导致磁体的磁性能较差。
[0053]
从实验no.1、实验no.2和实验no.4磁体酸洗后表面sem二次电子像可以看出,当磁体酸洗时间固定为80s,酸浓度低于本发明推荐范围(硝酸浓度推荐4~8vol%)内时(实验no.1),磁体表面的腐蚀量较小;酸浓度高于本发明推荐范围内时,磁体表面腐蚀较为严重,不但晶界富r相有较大的腐蚀深度,磁体表面主相晶粒也存在严重腐蚀;酸浓度处于本发明推荐范围内时,磁体晶界富r相有比较合适的腐蚀深度,同时磁体表层主相晶粒未发生明显腐蚀。
[0054]
另外,从实验no.2、no.6、no.7、no.8和no.9可以看出当酸性表面钝化液含量在本发明推荐范围内时(0.1~5vol%酸性表面钝化液),虽然相对于不添加酸性表面钝化液,略微降低了磁片的扩散效果,但是对磁片的磁性能影响不大;但相对于不添加酸性表面钝化液的实验no.6,其他实验组磁片在扩散时效后未产生粘片现象,而实验no.6组磁片在扩散时效后产生较严重的粘片,不利于磁片分离,产生了大量废品。但是当酸性表面钝化液含量超过本发明推荐范围内时,如实验no.9,表面钝化液浓度为10%,超出范围,实验结果显示,磁片表面晶粒钝化膜较厚,显著降低了磁体的扩散效果,使磁体性能大大降低。
[0055]
采用激光共聚焦显微镜测试磁体表面晶界富r相的腐蚀深度,采用维氏硬度计测试磁体的硬度,实验no.1~实验no.9磁体酸洗前后表面维氏硬度变化以及酸洗后磁体表面
晶界富r相腐蚀深度如表2所示:
[0056]
表2
[0057][0058][0059]
本发明通过测量磁体表面层主相晶粒的平均尺寸,以磁体表层主相平均晶粒尺寸作为表面两主相晶界深度。从表2数据可以看出,当磁体的表面晶界富r相腐蚀深度在0.1~0.4倍的表面两主相晶界深度时,由于主相晶粒间的晶界富r相一定程度上被腐蚀,主相晶粒间的结合力被削弱,因此磁体表面维氏硬度有一定程度的降低,酸洗前后磁体表面维氏硬度比h1/h2在1.05~1.25之间。当磁体表面晶界富r相的腐蚀深度小于0.1倍的表面两主相晶界深度时,由于晶界富r相的腐蚀量较少,磁体表面维氏硬度变化不大,酸洗前后磁体表面维氏硬度比在h1/h2《1.05。当磁体表面晶界富r相腐蚀量进一步加深时,磁体表层主相晶粒间的结合力被进一步减弱,受力时更容易发生碎裂,表面维氏硬度也进一步降低,酸洗前后磁体表面维氏硬度h1/h2》1.25。另外,当酸洗钝化液含量超过本发明推荐范围内时(实验no.9),虽然磁片表面的腐蚀深度降低,但是磁片表面晶粒钝化膜厚度较厚,加上酸洗使得晶粒间富r相缺失,使得表面晶粒之间结合力下降,因此降低了磁体的硬度值。
[0060]
可见磁体表面晶界富r相的腐蚀深度与磁体表面的维氏硬度存在较大的关联性,因此在本发明中可以通过酸洗前后磁体表面的维氏硬度变化表征磁体酸洗程度。
[0061]
实验no.1、实验no.2、实验no.4和实验no.5磁体经酸洗、沉积晶界扩散源涂层后的百格实验合格率结果如表3所示:
[0062]
表3
[0063]
实验no.合格率192.3%299.5%495.8%589.2%
[0064]
从表3数据可以看出,当磁体表面晶界富r相的腐蚀深度超过本发明的推荐范围时,磁体表面晶界扩散源涂层与基体的结合力降低,体现在百格实验中次品的合格率降低。
[0065]
磁体表面晶界富r相腐蚀深度低于本发明推荐范围、处于本发明推荐范围和高于本发明推荐范围时晶界扩散源与基体结合情况的示意图如图2所示,图2可以看出,当磁体表面晶界富r相的腐蚀深度较小时(《0.1倍表面两主相晶界深度),磁体表面较为光滑,此时
晶界扩散源涂层只能贴附在磁体表面,与基体的结合力较小,因此在进行百格实验或磁体受力时晶界扩散源涂层易从磁体表面脱落。当磁体表面晶界富r相存在合适的腐蚀深度时(0.1~0.4倍表面两主相晶界深度),部分晶界扩散源涂层会进入主相晶粒的间隙中,增强晶界扩散源与磁体表面的结合力,因此扩散源涂层不易脱落。而当磁体表层晶界富r相的腐蚀深度太大时(》0.4倍表面两主相晶界深度),虽然此时晶界扩散源涂层与磁体表面的结合力增强,但由于磁体表层主相晶粒与磁体基体的结合力减弱,导致磁体表层主相晶粒易从磁体基体脱落,附在磁体表层的晶界扩散源涂层也随之脱落。
[0066]
磁体表面晶界富r相的腐蚀深度对晶界扩散效果同样存在显著影响,当磁体表层晶界富r相的腐蚀深度<0.1倍表面两主相晶界深度时,由于磁体表面的腐蚀量太小,表面氧化层去除不干净。磁体表面的氧化层,尤其是存在于磁体晶界富r相的氧化物会对晶界扩散起到强烈的阻碍作用,降低晶界扩散效率。重稀土元素在磁体表面大量堆积会诱发体扩散的产生,使得最终磁体的矫顽力增量降低,剩磁下降量增大。当磁体表层晶界富r相的腐蚀深度》0.4倍表面两主相晶界深度时,主相晶粒间存在较深的间隙。此时晶界扩散源涂层与磁体剩余晶界富r相间的距离较大,如图2(c)所示。晶界扩散源涂层与磁体晶界富r相间的不连续也会阻碍原子扩散,降低晶界扩散效果,诱发体扩散的产生,从而降低磁体磁性能。当磁体表层晶界富r相的腐蚀深度为0.1~0.4倍表面两主相晶界深度时,既能够充分去除磁体表面氧化层,又能够保证晶界富r相与晶界扩散源涂层的连续性,从而保证晶界扩散后磁体的磁性能。
[0067]
本发明通过调控酸洗工艺,将磁体表层晶界富r相的腐蚀深度控制在0.1~0.4倍的表面两主相晶界深度,可以保证磁体表面氧化层被充分去除,又能够保证磁体表层剩余晶界r相与晶界扩散源涂层的连续性,从而提高磁体的晶界扩散效果。此外,磁体表层晶界富r相合适的腐蚀深度能够增强晶界扩散源涂层与磁体表面的结合力,防止磁体受力时晶界扩散源涂层从磁体表面脱落而造成产品性能一致性变差,合格率降低。同时本发明发现,酸洗时磁体表面晶界富r相的腐蚀深度与磁体表面维氏硬度存在较大的关联性。因此通过测试酸洗前后磁体表面维氏硬度变化可以表征晶界富r相的腐蚀深度,从而简化测试流程,提高生产效率。此外,随着酸浓度升高,磁体的腐蚀速度加快,控制晶界富r相腐蚀深度的难度增加,因此在本发明中酸洗液合适的硝酸浓度为1.0~10.0vol.%。
[0068]
实施例二:
[0069]
将成分为nd
23
pr7b
0.95
ga
0.15
cu
0.15
zr
0.2
fe
68.55
(质量比)配料后采用真空感应熔炼甩带、氢破、气流磨、取向成型、等静压、真空烧结、高温一级时效和低温二级时效制备基体磁体。
[0070]
采用机加工的方式将磁体基体加工成长
×
宽
×
高为10mm
×
10mm
×
3mm的磁片,高度方向为磁体取向方向。在室温条件下将磁片置于添加1.0vol%酸洗表面钝化剂和5.0vol.%硝酸的水溶液中超声酸洗不同时间,随后用清水超声清洗1min后烘干。采用的酸性表面钝化液为广东凯盟钝化防锈技术有限公司生产的酸洗钝化液id4008。
[0071]
采用多弧离子镀膜的方式在磁片垂直于取向方向的表面沉积厚度为10μm的纯tb扩散源层,其他表面不沉积重稀土元素扩散源。
[0072]
将沉积了扩散源涂层的磁体加热到910℃,进行高温晶界扩散。达到最高温度后炉内绝对真空度为10-2
pa~10-5
pa,保温10h。保温结束后以不低于80℃/min的冷速冷却至磁
体温度低于200℃。随后将磁体加热至520℃,保温3h。保温完成后以不低于80℃/min的冷速冷却至低于200℃。
[0073]
采用喷砂工艺对最终磁体进行表面处理,去除表面残留的扩散源涂层后采用nim磁性能测试设备测量磁体磁性能,采用icp测量磁体成分。采用维氏硬度计测量酸洗前后磁体表面维氏硬度,采用sem观察磁体表面腐蚀形貌,采用激光共聚焦显微镜测量磁体表面晶界富r相的腐蚀深度。采用百格实验测试晶界扩散源涂层与磁体基体的结合力,每个实验组测试20只产品的结合力,以扩散源涂层脱落面积《5%作为合格标准,计算合格率。
[0074]
实验no.10~实验no.12酸洗时间、最终磁体tb含量、磁体室温(20℃)磁性能如表4所示:
[0075]
表4
[0076]
实验no.酸洗时间(s)tb含量(wt.%)br(kgs)hcj(koe)10200.2214.2520.8 11800.2514.3322.1 122000.2114.1920.7
[0077]
从表4数据可知,对于实验no.11,当酸洗工艺处于本发明推荐范围内(50~100s)时,经过晶界扩散后磁体tb含量较高,剩磁和矫顽力均处于较高水平。当酸洗工艺超过本发明推荐范围内时,由于磁体表面氧化层去除不彻底(实验no.10)或晶界富r相腐蚀深度太大(实验no.12),影响晶界扩散效果,导致磁体的磁性能较低。
[0078]
实验no.10~实验no.12磁体酸洗后表面sem二次电子像如图3(a)~(c)所示。当硝酸浓度为5vol.%,对应酸洗时间低于本发明推荐范围内时,磁体表层的腐蚀量较少;当酸洗时间高于本发明推荐范围时,磁体表面腐蚀严重,不但晶界富r相有较大的腐蚀深度,磁体表面主相晶粒也存在严重腐蚀;当酸洗时间处于本发明推荐范围内时,磁体表层晶界富r相有比较合适的腐蚀深度,同时磁体表层主相晶粒未发生明显腐蚀。
[0079]
实验no.10~实验no.12磁体酸洗前后表面维氏硬度变化以及酸洗后磁体表面晶界富r相的腐蚀深度、百格实验的合格率如表5所示。
[0080]
表5
[0081][0082]
当酸洗时间在本发明推荐范围内时,磁体表面晶界富r相的腐蚀深度在0.1~0.4倍的表面两主相晶界深度,酸洗前后磁体表面维氏硬度比h1/h2在1.05~1.25之间。此时能够保证磁体表面氧化层充分去除的同时增强晶界扩散源涂层与磁体表面的结合力,防止磁体在受力时晶界扩散源涂层从磁体表面脱落造成产品合格率低的不足。
[0083]
在本实施例中,当腐蚀时间较短时,磁体表层晶界富r相的腐蚀深度<0.1倍表面两主相晶界深度时,由于磁体表层的腐蚀量太小,表面氧化层去除不干净。表面氧化层会对晶界扩散起到强烈的阻碍作用,降低磁体的晶界扩散效率。重稀土元素在磁体表面大量堆积会诱发体扩散的产生,使得最终磁体的矫顽力增量降低,剩磁下降量增大。当磁体表层晶
界富r相的腐蚀深度》0.4倍表面两主相晶界深度时,主相晶粒间存在较深的间隙。此时晶界扩散源涂层与磁体剩余晶界富r相间存在较大间隙。晶界扩散源涂层与磁体晶界富r相间的不连续也会阻碍原子扩散,降低晶界扩散效果,诱发体扩散的产生,从而降低磁体磁性能。当磁体表层晶界富r相的腐蚀深度为0.1~0.4倍表面两主相晶界深度时,既能够充分去除磁体表面氧化层、保证扩散源涂层与磁体表面的结合力,又能够保证磁体表层剩余晶界富r相与晶界扩散源涂层的连续性,从而保证晶界扩散后磁体的磁性能。
[0084]
在本发明中为了更加精确控制晶界富r相的腐蚀深度,采用的硝酸浓度为1.0~10.0vol.%。且随着腐蚀时间的延长晶界富r相的腐蚀量也相应的增大。因此针对不同的酸浓度需要合理调控腐蚀时间。本发明中酸浓度为1~4vol.%时,在室温条件下磁体酸洗时间为100~180s;酸浓度为4~8vol.%时,在室温条件下磁体酸洗时间为50~100s;酸浓度为8~10vol.%时,在室温下磁体酸洗时间为10~50s,从而保证磁体表层晶界富r相合适的腐蚀深度。
[0085]
实施例三:
[0086]
将成分为nd
22.5
pr
7.5
dy
1.0b0.95
al
0.5
cu
0.15
ga
0.15
zr
0.1
fe
67.15
(质量比)配料后采用真空感应熔炼甩带、氢破、气流磨、取向成型、等静压、真空烧结、高温一级时效和低温二级时效制备基体磁体。
[0087]
采用机加工的方式将磁体基体加工成长
×
宽
×
高为10mm
×
10mm
×
3mm的磁片,高度方向为磁体取向方向。在室温条件下将磁片置于添加1.0vol%酸洗表面钝化剂和5.0vol.%硝酸的水溶液中超声酸洗80s,随后用清水超声清洗1min后烘干。采用的酸性表面钝化液为广东凯盟钝化防锈技术有限公司生产的酸洗钝化液dh365h。
[0088]
实验no.13采用多弧离子镀膜的方式在磁体垂直于取向方向的两个表面沉积厚度10μm的纯tb扩散源层,其他表面不沉积重稀土元素扩散源。实验no.14磁体用多弧离子镀膜的方式在磁体所有表面沉积厚度为10μm的纯tb扩散源层。
[0089]
将沉积了扩散源涂层的磁体加热到890℃,进行高温晶界扩散。达到最高温度后炉内绝对真空度为10-2
pa~10-5
pa,保温10h。保温结束后以不低于80℃/min的冷速冷却至磁体温度低于200℃。随后将磁体加热至510℃,保温3h。保温完成后以不低于80℃/min的冷速冷却至低于200℃。
[0090]
采用喷砂工艺对最终磁体进行表面处理,去除表面残留的扩散源涂层后采用nim磁性能测试设备测量磁体磁性能,采用icp测量磁体成分。
[0091]
实验no.13和实验no.14最终磁体成分及磁性能如表6所示。
[0092]
表6
[0093]
实验no.tb含量(wt.%)br(kgs)hcj(koe)130.2314.221.7 140.3113.422.3
[0094]
r-t-b磁体晶界扩散存在较强的各向异性,沿取向方向的晶界扩散速率大于沿垂直于取向方向的晶界扩散速率。在本发明中,实验no.13磁体在垂直于取向方向的两个表面沉积晶界扩散源,结合酸洗工艺去除磁体表面氧化层能够保证晶界扩散后磁体有较高的矫顽力增量,同时扩散后剩磁下降量也较低。当磁体平行于取向方向的表面也沉积晶界扩散源时,由于沿垂直于磁体取向方向的晶界扩散速率较低,虽然经酸洗后磁体表面的氧化层
得到充分去除,但较低的晶界扩散速率导致重稀土元素在磁体表面堆积,促进了体扩散的进行。因此实验no.14磁体经过扩散后磁体的矫顽力增量较实验no.13虽然有所升高,但剩磁降低量明显增大。因此本发明中,优选垂直于磁体取向方向的两个表面需要涂覆晶界扩散源涂层,而平行于磁体取向方向的表面不沉积晶界扩散源。
[0095]
实施例四:
[0096]
将成分为nd
22.5
pr
7.5
dy
1.0b0.95
al
0.5
cu
0.15
ga
0.15
zr
0.1
fe
67.15
(质量比)配料后采用真空感应熔炼甩带、氢破、气流磨、取向成型、等静压、真空烧结、高温一级时效和低温二级时效制备基体磁体。
[0097]
采用机加工的方式将磁体基体加工成长
×
宽
×
高为10mm
×
10mm
×
3mm的磁片,高度方向为磁体取向方向。在室温条件下将磁片置于添加1.0vol%酸洗表面钝化剂和5.0vol.%不同种类酸的水溶液中超声酸洗80s,随后用清水超声清洗1min后烘干。采用的酸性表面钝化液为广东凯盟钝化防锈技术有限公司生产的酸洗钝化液id4008。
[0098]
采用多弧离子镀膜的方式在磁片垂直于取向方向的表面沉积厚度为10μm的纯tb扩散源层,其他表面不沉积重稀土元素扩散源。
[0099]
将沉积了扩散源涂层的磁体加热到890℃,进行高温晶界扩散。达到最高温度后炉内绝对真空度为10-2
pa~10-5
pa,保温10h。保温结束后以不低于80℃/min的冷速冷却至磁体温度低于200℃。随后将磁体加热至510℃,保温3h。保温完成后以不低于80℃/min的冷速冷却至低于200℃。
[0100]
采用喷砂工艺对最终磁体进行表面处理,去除表面残留的扩散源涂层后采用nim磁性能测试设备测量磁体磁性能,采用icp测量磁体成分,采用sem观察磁体表面形貌。
[0101]
实验no.15~实验no.18酸种类、最终磁体tb含量、磁体室温(20℃)磁性能如表7所示:
[0102]
表7
[0103]
实验no.酸类型tb含量(wt.%)br(kgs)hcj(koe)15硝酸0.2414.321.9 16盐酸0.2314.119.4 17硫酸0.2314.119.8 18草酸0.1914.220.0
[0104]
从表7数据可知,采用不同种类的酸进行磁体表面酸洗后最终磁体的磁性能存在较大差别。采用硝酸作为酸洗液时,晶界扩散后磁体的矫顽力增量大,剩磁也处于较高水平。而当采用盐酸、硫酸和草酸作为酸洗液时,晶界扩散后磁体的矫顽力增量较低,剩磁也明显降低。
[0105]
测试磁体在不同酸溶液中酸洗5分钟后磁体的失重,结果如表8所示。
[0106]
表8
[0107]
实验no.失重mg/cm2150.105160.317170.325180.051
[0108]
从表8数据可知,采用硫酸或盐酸作为酸洗液时,磁体腐蚀速度大约为采用硝酸时的3倍。这导致采用硫酸或盐酸作为酸洗液时磁体的晶界富r相腐蚀太快,工艺过程难以控制。腐蚀后磁体表面剩余晶界富r相的量较少,晶界扩散源涂层与磁体表面剩余晶界富r相的距离较大。阻碍了重稀土原子的晶界扩散作用,促进体扩散的进行,从而导致最终磁体的矫顽力增量降低,剩磁下降量增大。
[0109]
同时从表7数据可以看出,采用盐酸作为酸洗液时,磁体的矫顽力增量要明显低于其他种类的酸。这是由于盐酸中的氯离子半径小,渗透性强,渗入磁体的晶界富r相中会产生锈点,严重阻碍重稀土元素沿晶界扩散速率,因此采用盐酸作为酸洗液时磁体的磁性能会显著降低。
[0110]
实验no.16~实验no.18磁体酸洗后表面sem二次电子像如图4所示,从不同酸酸洗后磁体表面sem二次电子像可以看出,磁体经盐酸和硫酸腐蚀后磁体表面的腐蚀深度非常大,磁体表层主相晶粒间的晶界富r相基本被完全腐蚀,同时磁体表层主相晶粒也发生明显腐蚀。采用草酸作为酸洗液时磁体表面的腐蚀效果较弱,草酸在磁体表面产生了类似钝化的作用。这对氧化层的清洗效果较弱,不利于氧化层的去除。在磁体表面氧化层和草酸钝化作用下,晶界扩散效率明显降低,扩散后磁体磁性能也降低。因此在本发明中优选采用硝酸作为酸洗液。
再多了解一些
本文用于创业者技术爱好者查询,仅供学习研究,如用于商业用途,请联系技术所有人。