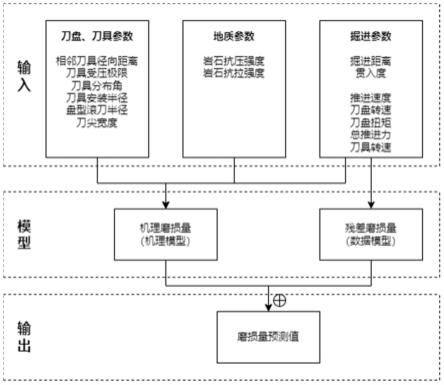
一种机理和数据联合驱动的tbm滚刀磨损预测方法
技术领域
1.本发明属于tbm掘进技术领域中的滚刀磨损量预测领域,具体涉及一种机理和数据联合驱动的tbm滚刀磨损预测方法。
背景技术:
2.刀盘刀具作为tbm的重要组成部分,在工作时具有负载巨大、变化范围宽、随机性强等特性,所以在施工作业中极易受损,滚刀磨损过大严重影响施工效率,而开仓换刀容易引发开挖面失稳、隧道坍塌等工程事故,增加了施工风险和成本。相关资料显示,刀具消耗的费用占总费用的二至三成,是配件耗用中所占消耗比例最大的一项,刀具检修及更换所用去的时长约占停机维护时长的三分之二,因此,在掘进过程中掌握刀具磨损状态就显得尤为关键。目前刀具的磨损检测方法并未实现自动化,在实际工程当中,大多数仍然采用定期停机人工检查的方式,传感器监测方法受限于过高的成本、有限的安装空间及恶劣的工作环境等条件。所以目前的研究集中于刀具的磨损预测方法,主要分为机理模型和数据模型,机理模型从刀具破岩时的力学分析或摩擦能角度出发,具有良好的可解释性和外推特性,数据模型则从地质参数或掘进参数(推进速度、刀盘转速、刀盘转矩、推进力等)的角度切入,充分挖掘掘进数据中的信息。
3.由于刀具与岩石相互作用机理相当复杂,大多数机理模型仅仅考虑单一的磨损机理,而忽视了磨损过程中其它磨损机理和它们之间的相互影响,往往导致模型的预测精度过低,无法很好应用于实际工程。而数据模型中所需要的大量地质信息也多依赖于地勘报告与人工测试,而缺乏理论机理的考虑,模型输入输出的关系往往与实际物理关系相矛盾,此外,数据模型完全取决于获得的数据性能,模型的可解释性和外推性差。
技术实现要素:
4.本发明的目的在于克服现有技术的不足,提出一种机理和数据联合驱动的tbm滚刀磨损预测方法。本发明提出的机理和数据联合驱动的滚刀磨损预测方法恰恰能综合现有两类模型的优点,为准确判断出滚刀的失效节点提供可靠参考。
5.本发明的技术方案如下:
6.本发明提供了一种机理和数据联合驱动的tbm滚刀磨损预测方法,其包括如下步骤:
7.1)计算刀盘滚刀所受垂直载荷f
nn
;
8.2)根据滚刀所受垂直载荷,计算由磨损机理引起的磨损量q
t
,所述由磨损机理引起的磨损量包括滚刀和硬岩摩擦引起的磨粒磨损量δ
abr
、硬质磨粒脱落引起的黏着磨损量δ
adh
、滚刀与岩土在交变接触应力作用下的疲劳磨损量δ
fat
;
9.3)构建并训练数据模型;所述数据模型以推进速度v、刀盘转速n、刀盘扭矩tc、总推进力f、滚刀转速ns作为输入,实际磨损量与由磨损机理引起的磨损量q
t
的差值为输出,采用历史数据进行训练;
10.4)建立tbm滚刀磨损预测模型,根据实时数据进行tbm刀盘每把滚刀实际磨损程度预测。
11.作为本发明的优选方案,所述步骤3)中,数据模型的训练,包括如下步骤:
12.步骤一:处理实际施工历史数据,包括筛除异常值、采用二值函数筛除非工作点,将时间序列数据转换为距离序列数据;
13.步骤二:选定数据模型,以推进速度v、刀盘转速n、刀盘扭矩tc、总推进力f、滚刀转速ns作为输入,实际磨损量与步骤2)计算得到的由磨损机理引起的磨损量q
t
的差值为输出进行模型训练;
14.步骤三:利用步骤一得到的距离序列数据对步骤二的数据模型进行训练。
15.与现有技术相比,本发明具有如下有益效果:
16.本发明提出的混合预测方法充分结合了理论机理模型和数据模型的各自优点,能够根据tbm规格参数和现场工程数据高精度的预测出每把滚刀的实际磨损程度,较纯数据模型有更好的泛化特性,较纯机理模型有更好的拟合精度,为现场操作人员掌握刀具信息提供帮助,为及时换刀提供数据依据,提升了滚刀的利用率和掘进机的工作效率。
附图说明
17.图1为本发明方法的总体流程框图;
18.图2为实施例中的420-444环49号滚刀的磨损量预测结果。
具体实施方式
19.下面结合具体实施方式对本发明做进一步阐述和说明。本发明中各个实施方式的技术特征在没有相互冲突的前提下,均可进行相应组合。
20.如图1所示为本发明方法的总体流程示意图,本发明方法为利用所构建的tbm滚刀磨损预测模型进行磨损预测,其中,tbm滚刀磨损预测模型包括机理模型和数据模型两部分。机理模型综合考虑磨粒磨损、黏着磨损和疲劳磨损等因素作用下的磨损机理,数据模型主要以现场tbm掘进参数为输入,基于机器学习模型构建,为理论计算公式补充详细的地质以及岩机相互作用信息。本发明提出的方法充分考虑了刀具磨损的实际理论机理以及现场数据信息,具有较高的预测精度,预测结果也符合实际的物理关系,可解释性和外推性也得到了极大的提升。
21.如图1所示,本发明方法的流程如下:
22.首先,计算滚刀所受垂直载荷f
nn
。
23.其次,分别计算由各类磨损机理引起的滚刀磨损量q
t
,包括滚刀和硬岩摩擦引起的磨粒磨损量δ
abr
,硬质磨粒脱落引起的黏着磨损量δ
adh
,滚刀与岩土在交变接触应力作用下的疲劳磨损量δ
fat
,其公式如下所示:
24.q
t
=aδ
abr
bδ
adh
cδ
fat
25.式中,q
t
为磨损机理引起的磨损量,a、b、c分别为磨粒磨损、黏着磨损、疲劳磨损的权重,由现场数据辨识得到。
26.最后,训练推进速度v、刀盘转速n、刀盘扭矩tc、总推进力f、滚刀转速ns作为输入,实际磨损量与机理磨损量差值为输出的数据模型,作为计算模型的有效补充。
27.本发明的tbm滚刀磨损预测模型如下式所示:
28.qi=aδ
abr
bδ
adh
cδ
fat
δ
29.式中,qi为刀盘上第i把滚刀掘进l后的总磨损量,单位mm;δ为数据模型计算得到的残差项,单位mm。
30.在本实施例中,计算公式如下,该计算模型为在科罗拉多矿业学院提出的力学模型(csm)基础上,利用相似计算,简化得到:
[0031][0032]
式中,c为无量纲参数;ψ为滚刀刀刃上的压力分布系数,通常范围在-0.2~0.2;s为相邻滚刀的刀间距,单位mm;r为盘型滚刀半径,单位mm;σc为岩石抗压强度,单位mpa;σ
t
为岩石抗拉强度,单位mpa;p为贯入度,单位mm;t为刀尖宽度,单位mm;β为刀具的分布角,单位rad。
[0033]
进一步的,所述磨粒磨损量δ
abr
计算公式如下:
[0034][0035]
式中,ni为第i把刀转过的圈数,其中l为tbm掘进距离,单位mm,ri为第i把刀的安装半径,单位mm,r为盘型滚刀半径,单位mm;k
abr
为磨料磨损系数,其中,θ为微量切削假说中的圆锥体的半角,单位rad,k为概率常数,取决于磨粒尺寸和材料特性等;σs为受压屈服极限,单位mpa;l为刀具一圈所走过的距离,单位mm。
[0036]
所述黏着磨损量δ
adh
计算公式如下:
[0037][0038]
式中,k
adh
为黏着磨损系数,取决于材料和摩擦条件。
[0039]
所述疲劳磨损量δ
fat
计算公式如下:
[0040][0041]
式中,k
fat
为疲劳磨损系数,k
fat
=1/n
fat
,其中n
fat
为产生疲劳破坏的应力循环数,即滚刀圈数。
[0042]
本发明的数据模型主要是利用掘进参数计算残差磨损量,即tbm滚刀磨损预测模型中的残差项。数据模型可以利用多元回归模型(mlr)、支持向量机回归模型(svr),反向传播神经网络(bpnn)等机器学习模型构建,模型训练可分为以下步骤:
[0043]
步骤一:处理实际施工数据,包括筛除异常值(本实施例采用隔离森林筛除异常值)、采用二值函数筛除非工作点,将时间序列数据转换为距离序列数据。
[0044]
所述二值函数用于判断某点是否处于掘进工作状态,表达式如下:
[0045]
[0046]
d=f(f)
·
f(v)
·
f(tc)
·
f(n)
[0047][0048]
式中,f(x)为二值函数,f为总推进力,v为推进速度,tc为刀盘扭矩,n为刀盘转速,d为状态判别函数。
[0049]
所述序列转换用到如下表达式:
[0050][0051]
式中,lj为某个采样周期内的掘进里程,vj表示某个采样时刻的推进速度,t
j 1-tj表示一个采样周期。
[0052]
步骤二:选定数据模型,以推进速度v、刀盘转速n、刀盘扭矩tc、总推进力f、滚刀转速ns作为输入,实际磨损量与机理磨损量差值为输出进行模型训练。
[0053]
步骤三:利用训练得到的数据模型,计算得到对应残差值。
[0054]
以下结合实施例对本发明的滚刀磨损计算方法的具体使用过程进行说明,来证明本发明的实用性与准确性。以某地铁工程49号刀在529-547环的掘进状态作为实施例。
[0055]
步骤一:将前所述各式经过代入化简,滚刀机理磨损量q
t
可通过如下表达式进行计算:
[0056][0057][0058]
式中,c为无量纲参数,此例取0.02;l为掘进距离,单位mm;ψ为滚刀刀刃上的压力分布系数,通常范围在-0.2~0.2,此例取0.1;s为相邻滚刀的刀间距,单位mm,此例取100;σs为受压屈服极限,单位mpa,此例取1853.85;σc为岩石抗压强度,单位mpa,此例中529环至547环包含微风化破碎岩、微风化板岩、中微风化破碎岩三种类型,抗压强度分别为46.4、54.6、41.9;σ
t
为岩石抗拉强度,单位mpa,是抗压强度的1/10;β为刀具的安装角度,单位rad;k
abr
为磨料磨损系数,此例取4.5
×
10-3
;ri为第i把刀的安装半径,单位mm,此例取4970;r为盘型滚刀半径,单位mm,此例取241.5;p为贯入度,单位mm;t为刀尖宽度,单位mm,此例取20;k
adh
为黏着磨损系数,取决于材料和摩擦条件,此例取k
adh
;k
fat
为疲劳磨损系数,k
fat
=1/n
fat
,其中n
fat
为产生疲劳破坏的应力循环数,即滚刀圈数;a、b、c分别为磨粒磨损、黏着磨损、疲劳磨损的权重系数,由现场数据拟合辨识得到,此例中a取0.8、b取0.14、c取0.06;
[0059]
将各确定参数代入后,可以得到机理磨损量q
t
与掘进距离l、贯入度p之间的数值关系,由此计算出529-547环每个点的机理磨损量。
[0060]
步骤二:以推进速度v、刀盘转速n、刀盘扭矩tc、总推进力f、刀具转速ns作为输入,实际磨损量与机理磨损量差值为输出训练数据模型。此实施例中,选用反向传播神经网络(bpnn)作为残差项的训练模型。
[0061]
1)针对现场施工数据,采用隔离森林筛除异常值、采用二值函数去除非工作点,将时间序列数据转换为距离序列数据。
[0062]
2)确定输入输出矢量,输入特征包括推进速度v、刀盘转速n、刀盘扭矩tc、总推进力f、刀具转速ns;实际磨损量与机理磨损量差值作为模型的输出。将49号刀80%的数据作为训练集对模型进行训练,20%数据作为模型的验证集,模型经过调优,包含四层隐藏层,各层包含8、10、12、14个神经元,采用adam优化器,在训练集上mae=0.39,rmse=0.53;验证集上mae=1.19,rmse=1.60。
[0063]
3)使用训练完成的数据模型,通过输入推进速度v、刀盘转速n、刀盘扭矩tc、总推进力f、刀具转速ns计算出每个点的残差值;
[0064]
步骤三:将步骤一、二的所得值相加计算出该点的磨损量,实现对磨损量的预测,最终49号刀在420-444环的预测结果如图2所示,对于工程中的其它掘进位置的磨损量可与本实施例类比进行计算。本发明充分结合了理论机理模型和数据模型的各自优点,能够根据tbm规格参数和现场工程数据高精度的预测出每把滚刀的实际磨损程度,较纯数据模型有更好的泛化特性,较纯机理模型有更好的拟合精度。
[0065]
以上所述实施例仅表达了本发明的几种实施方式,其描述较为具体和详细,但并不能因此而理解为对本发明专利范围的限制。应当指出的是,对于本领域的普通技术人员来说,在不脱离本发明构思的前提下,还可以做出若干变形和改进,这些都属于本发明的保护范围。因此,本发明的保护范围应以所附权利要求为准。
再多了解一些
本文用于创业者技术爱好者查询,仅供学习研究,如用于商业用途,请联系技术所有人。