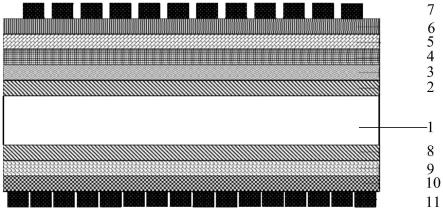
1.本实用新型涉及太阳能电池制备技术领域,尤其涉及一种异质结太阳能电池。
背景技术:
2.光伏发电技术是当前最具潜力的可持续发展能源之一,近些年出现最多的硅基太阳能电池已成为主流,但随着多次的技术革新,目前市场占比最大的perc电光电池转换效率以及降本空间已到极限,因此需要发展一种更为高效、低成本的太阳电池满足市场的需要。异质结(hjt)太阳能电池技术由于其双面性能、低工作温度系数和相对简单的制造工艺,在提升转换效率和向大规模生产升级方面都显示出了巨大的潜力。
3.目前异质结太阳能电池制备方法为:将n型硅片进行清洗、制绒,然后分别在硅片正背面沉积非晶硅薄膜,在硅片一侧非晶薄膜上沉积n型掺杂非晶硅,在硅片另一侧非晶硅薄膜上沉积p型掺杂非晶硅,形成pn结。异质结太阳能电池较高的转换效率主要来源于电池较高的开路电压,这是由于其内部非晶硅钝化效果优异,氢化非晶硅有效地减少了硅基悬挂键,降低了界面态缺陷密度。但目前的异质结太阳能电池的短路电流偏低,这是由于其内部非晶硅钝化层较厚,且带隙较窄,对太阳光的有效利用率偏低,以至于其光学性能较差,同时非晶硅薄膜与tco以及电池表面电极接触电阻整体偏高,这也最终导致其短路电流偏低的问题。
技术实现要素:
4.为解决上述技术问题,本实用新型提供一种异质结太阳能电池。本实用新型技术方案如下:
5.一种异质结太阳能电池,其包括n型单晶硅片,所述n型单晶硅片正面依次沉积有正面本征非晶硅薄膜、本征微晶硅薄膜、n型掺杂微晶硅氧薄膜、n型掺杂微晶硅薄膜、正面tco膜层和正面金属栅线层,所述n型单晶硅片背面依次沉积有背面本征非晶硅薄膜、p型掺杂非晶硅薄膜、背面tco膜层和背面金属栅线层。
6.可选地,所述正面本征非晶硅薄膜的沉积厚度为1-15nm。
7.可选地,所述本征微晶硅薄膜的沉积厚度为0.2-5nm。
8.可选地,所述n型掺杂微晶硅氧薄膜的沉积厚度为3-20nm。
9.可选地,所述n型掺杂微晶硅薄膜的沉积厚度为1-10nm。
10.可选地,所述背面本征非晶硅薄膜的沉积厚度为1-15nm。
11.可选地,所述p型掺杂非晶硅薄膜的沉积厚度为2-10nm。
12.可选地,所述正面tco膜层的沉积厚度为70-130nm。
13.可选地,所述背面tco膜层的沉积厚度为70-120nm。
14.上述所有可选地技术方案均可任意组合,本实用新型不对一一组合后的结构进行详细说明。
15.借由上述方案,本实用新型的有益效果如下:
16.通过设置n型掺杂微晶硅氧薄膜来与正面tco膜层匹配,可以有效增加带隙宽度,提高300-1200波段的太阳光利用率,同时降低了寄生吸收,并且通过引入n型掺杂微晶硅氧薄膜,可有效地降低薄膜折射率,增强表面光照利用率,通过配合正面tco膜层有效地降低了接触电阻,提高载流子的迁移率,从而可以明显地增加异质结太阳能电池的短路电流,从而提升异质结太阳能电池的转化效率。
17.上述说明仅是本实用新型技术方案的概述,为了能够更清楚了解本实用新型的技术手段,并可依照说明书的内容予以实施,以下以本实用新型的较佳实施例并配合附图详细说明如后。
附图说明
18.图1是本实用新型的结构示意图。
19.图2是常规异质结太阳能电池的结构示意图。
具体实施方式
20.下面结合附图和实施例,对本实用新型的具体实施方式作进一步详细描述。以下实施例用于说明本实用新型,但不用来限制本实用新型的范围。
21.如图1所示,本实用新型提供的异质结太阳能电池,其包括n型单晶硅片1,所述n型单晶硅片1正面依次沉积有正面本征非晶硅薄膜2、本征微晶硅薄膜3、n型掺杂微晶硅氧薄膜4、n型掺杂微晶硅薄膜5、正面tco膜层6和正面金属栅线层7,所述n型单晶硅片1背面依次沉积有背面本征非晶硅薄膜8、p型掺杂非晶硅薄膜9、背面tco膜层10和背面金属栅线层11。
22.可选地,所述正面本征非晶硅薄膜2的沉积厚度为1-15nm。
23.可选地,所述本征微晶硅薄膜3的沉积厚度为0.2-5nm。
24.可选地,所述n型掺杂微晶硅氧薄膜4的沉积厚度为3-20nm。
25.可选地,所述n型掺杂微晶硅薄膜5的沉积厚度为1-10nm。
26.可选地,所述背面本征非晶硅薄膜8的沉积厚度为1-15nm。
27.可选地,所述p型掺杂非晶硅薄膜9的沉积厚度为2-10nm。
28.可选地,所述正面tco膜层6的沉积厚度为70-130nm。
29.可选地,所述背面tco膜层10的沉积厚度为70-120nm。
30.制备上述异质结太阳能电池的主要步骤为:
31.步骤1,对n型单晶硅片1进行去损伤层,清洗表面脏污,并进行制绒,使n型单晶硅片1表面形成金字塔结构,过程使用化学品为氢氧化钾、双氧水、盐酸、氢氟酸和制绒添加剂。
32.步骤2,对步骤1制绒清洗后的n型单晶硅片1正面沉积正面本征非晶硅薄膜2,沉积厚度为1-15nm,使用设备为板式rf-pecvd(等离子体化学气相沉积),使用气体为sih4和h2。
33.步骤3,对步骤2后n型单晶硅片1沉积本征微晶硅薄膜3,沉积厚度为0.2-5nm,使用气体为sih4和h2,体系控制h2:sih4为100-250:1。
34.步骤4,对步骤3后n型单晶硅片1沉积n型掺杂微晶硅氧薄膜4,沉积厚度为3-20nm,使用气体为sih4、h2、ph3和co2,体系控制h2:sih4为100-250:1,ph3掺杂浓度为2%-8%,co2掺杂浓度为20%-70%。
35.步骤5,对步骤4后n型单晶硅片1沉积n型掺杂微晶硅薄膜5,沉积厚度为1-10nm,使用气体sih4、h2和ph3,体系控制h2:sih4为100-250:1,ph3掺杂浓度3%-10%。
36.步骤6,对步骤5后n型单晶硅片1进行翻片,在n型单晶硅片1另一侧沉积背面本征非晶硅薄膜8,沉积厚度为1-15nm,使用气体sih4和h2。
37.步骤7,对步骤6后硅片沉积p型掺杂非晶硅薄膜9,沉积厚度为2-10nm,使用气体sih4、h2、b2h6,b2h6掺杂比例为1.5%-6%。
38.步骤8,对步骤7后n型单晶硅片1通过pvd设备磁控溅射法在n型单晶硅片1正面(n面)和背面(p面)分别沉积正面tco膜层6和背面tco膜层10,n面使用高晶化率靶材ito,沉积厚度为70-130nm,p面使用常规靶材,沉积厚度为70-120nm。
39.步骤9,对步骤8后n型单晶硅片1进行双面金属化丝网印刷,形成正面金属栅线层7和背面金属栅线层11,退火15-30min,得到成品异质结太阳能电池。
40.本实用新型通过引入n型掺杂微晶硅氧薄膜4来与正面tco膜层6匹配,使得载流子的迁移率明显提高,降低了tco薄膜电阻,也降低了与金属栅线之间的接触电阻,扩大了光学带隙,增加了300-1200nm波段的光照利用率,同时降低了寄生吸收,大幅提升了异质结太阳能电池的光学性能。
41.为说明本实用新型实施例提供的异质结太阳能电池的有益效果,下面提供如下对比例和实验例。
42.对比例:
43.如图2所示,其为另一种异质结太阳能电池的结构示意图。该异质结太阳能电池包括硅片200,依次沉积在硅片200正面的正面本征非晶硅201、n型掺杂非晶硅薄膜202、正面tco薄膜203和正面金属栅极204,以及依次沉积在硅片200背面的背面本征非晶硅205、p型掺杂非晶硅206、背面tco薄膜207和背面金属栅极208。
44.该种异质结太阳能电池的制备工艺为:
45.步骤21,对硅片200进行去损伤层,清洗表面脏污,并进行制绒,使硅片200表面形成金字塔结构,过程使用化学品为氢氧化钾、双氧水、盐酸、氢氟酸、制绒添加剂。
46.步骤22,对步骤21制绒清洗后的硅片200正面沉积正面本征非晶硅201,沉积厚度7nm,使用设备为板式rf-pecvd(等离子体化学气相沉积),使用气体sih4、h2。
47.步骤23,对步骤22后硅片沉积n型掺杂非晶硅薄膜202,沉积厚度5nm,使用气体sih4、h2、ph3,ph3掺杂比例3%。
48.步骤24,对步骤23后硅片200进行翻片,在硅片200另一侧沉积背面本征非晶硅205,沉积厚度8nm,使用气体sih4、h2。
49.步骤25,对步骤24后硅片200沉积p型掺杂非晶硅206,沉积厚度6nm,使用气体sih4、h2、b2h6,b2h6掺杂比例2%。
50.步骤26,对步骤25后硅片200借助pvd设备进行磁控溅射在硅片正背面分别沉积正面tco薄膜203和背面tco薄膜207,沉积厚度110nm。
51.步骤27,对步骤26后硅片进行金属化丝网印刷,形成正面金属栅极204和背面金属栅极208,退火25min,得到成品电池片。
52.实验例:
53.实验例的异质结太阳能电池的结构如图1所示,其为本实用新型实施例提供的异
质结太阳能电池,其制备工艺为:
54.步骤31,对n型单晶硅片1进行去损伤层,清洗表面脏污,并进行制绒,使硅片表面形成金字塔结构,过程使用化学品为氢氧化钾、双氧水、盐酸、氢氟酸、制绒添加剂。
55.步骤32,对步骤31制绒清洗后的n型单晶硅片1正面沉积正面本征非晶硅薄膜2,沉积厚度4nm,使用设备为板式rf-pecvd(等离子体化学气相沉积),使用气体sih4、h2。
56.步骤33,对步骤32后n型单晶硅片1沉积本征微晶硅薄膜3,沉积厚度1nm,使用气体sih4、h2,体系控制h2:sih4为150:1。
57.步骤34,对步骤33后n型单晶硅片1沉积n型掺杂微晶硅氧薄膜4,沉积厚度15nm,使用气体sih4、h2、ph3、co2,体系控制h2:sih4为150:1,ph3掺杂浓度2%,co2掺杂浓度30%。
58.步骤35,对步骤34后n型单晶硅片1沉积n型掺杂微晶硅薄膜5,沉积厚度3nm,使用气体sih4、h2、ph3,体系控制h2:sih4为150:1,ph3掺杂浓度3%。
59.步骤36,对步骤35后n型单晶硅片1进行翻片,在n型单晶硅片1另一侧沉积背面本征非晶硅薄膜8,沉积厚度10nm,使用气体sih4、h2。
60.步骤37,对步骤36后n型单晶硅片1沉积p型掺杂非晶硅薄膜9,沉积厚度5nm,使用气体sih4、h2、b2h6,b2h6掺杂比例1.5%。
61.步骤38,对步骤37后n型单晶硅片1通过pvd设备磁控溅射法在n型单晶硅片1正面(n面)和背面(p面)分别沉积正面tco膜层6和背面tco膜层10,正面tco膜层6使用高晶化率靶材ito(in2o3:sno2=99:1wt%),沉积厚度120nm,p面使用常规靶材,沉积厚度110nm。
62.步骤39,对步骤38后n型单晶硅片1进行金属化丝网印刷,形成正面金属栅线层7和背面金属栅线层11,退火25min,得到成品异质结太阳能电池。
63.将本实用新型提供的异质结太阳能电池(图1对应的异质结电池)与图2所对应的异质结太阳能电池进行实验,得到如下表一所示的实验结果:
64.表一
65.分组对比例实验例isc0.0000.058-0.070
66.表一中,isc为短路电流,对比实验例和对比例的短路电流差异。实验组相较于对比例isc可提升58-70ma。由此可得,通过n型掺杂微晶硅氧薄膜4和正面tco膜层6的匹配,使得本实用新型实施例提供的异质结太阳能电池有效提升了光学带隙,增加了光照利用率,同时降低了寄生吸收,有效增加了载流子的迁移率,降低了接触电阻,进而提升了电池的短路电流,提高了电池的转换效率。
67.以上所述仅是本实用新型的优选实施方式,并不用于限制本实用新型,应当指出,对于本技术领域的普通技术人员来说,在不脱离本实用新型技术原理的前提下,还可以做出若干改进和变型,这些改进和变型也应视为本实用新型的保护范围。
再多了解一些
本文用于创业者技术爱好者查询,仅供学习研究,如用于商业用途,请联系技术所有人。