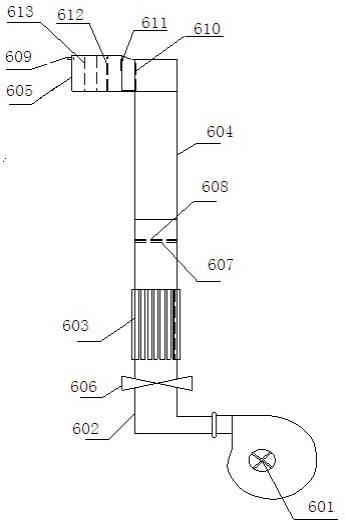
1.本发明属于聚酯纤维技术领域,涉及一种多异形丝的生产设备。
背景技术:
2.聚酯纤维是目前我国生产量和消费量最大的纺织纤维,具有极大的应用前景。但是,目前我国的高档涤纶产品、新型差别化功能性聚酯纤维的自产能力缺口较大,与国际先进技术尚有一定的差距,因此,聚酯生产企业应以差别化聚酯纤维为源头,通过研发一些典型的高附加值的功能与高性能化聚酯新产品,来提升我国纺织品的附加值和国际竞争力,全面实现产业升级,达到提升整个行业技术水平的目的。
3.目前市场上羊毛是珍贵的纺织原料之一。由于价格昂贵量少,远远不能满足市场日益增长的需求。因此,各厂家都致力于化纤仿毛的研发和应用。仿毛织物用聚酯纤维常规使用涤纶加弹丝、涤纶网络丝或各种异形截面聚酯纤维为原料织成的具有呢绒风格的织物和中长仿毛织物,其价格低于同类毛织物产品。其中以异形截面聚酯纤维织成的织物,既具有尼龙的手感丰满蓬松、弹性好的特性,又具备涤纶坚牢耐用、易洗快干、平整挺括、不易变形、不易起毛、起球等特点。
4.而在聚酯纤维生产中,对于多异形丝来说,表面积大容易散热,丝条各个方向冷却速率有差异,因此对环吹风冷却装置要求比较高。如果采用普通的外环吹风冷却设备,要求具有较高的冷却风冷却丝条,才能保持多异形丝的异形度,但风速过大导致初生纤维冷却过快,纤维分子结构不均匀,纺丝张力升高,拉伸后容易产生单丝断裂,且风速过大,熔体细流向中心偏移,产生粘连。对于吹风筒滤芯来说,过短达不到冷却成形要求,过长吹出的风容易发生气流紊乱,引起丝束抖动,且采用外环吹风冷却,风速在达到丝束中心时,存在风速降低,冷却效果减弱的现象,丝条达不到均匀冷却,集束时单丝间易于粘着而产生毛丝,制得的纤维截面异形度差。
5.因此,研究一种多异形丝的生产设备以解决多异形丝难以均匀冷却,制得的纤维截面异形度差具有十分重要的意义。
技术实现要素:
6.为了克服现有设备和技术的不足,本发明提供一种多异形丝的生产设备。
7.为达到上述目的,本发明采用的技术方案如下:一种多异形丝的生产设备,包括喷丝板和环吹风冷却装置,喷丝板为环形结构;环吹风冷却装置包括圆柱筒状的外环吹风滤芯、圆柱筒状的内环吹风滤芯、内环吹送风管和外环吹装置;外环吹装置、外环吹风滤芯和内环吹风滤芯都位于喷丝板的下方且与其间隔一定的距离,外环吹风滤芯位于外环吹装置内且外环吹装置与外环吹风滤芯的中空部分相对的区域为空心区域,内环吹风滤芯位于外环吹风滤芯内且二者共轴,内环吹风滤芯与喷丝板共轴,内环吹风滤芯的外径与喷丝板的内径相同,外环吹风滤芯的内径与喷丝板的外径相
同;内环吹送风管穿入内环吹风滤芯内,用于为内环吹风滤芯提供风速为0.5~0.7m/s、温度为t1℃、相对湿度为75~85%的冷却风;外环吹装置用于为外环吹风滤芯提供风速为0.5~0.7m/s、温度为t2℃、相对湿度为75~85%的冷却风,t
1=
t2,取值范围为20~24℃;冷却成形是熔体纺丝的重要过程之一,冷却条件中风速、风温、相对湿度三个因素对纺程上熔体细流的流变特性有很大的影响;以风速对纤维成形影响最大,过大或过小的吹风速度均会使条干不匀率增大,当内外环吹风风速过大时,湍动因素增加,而空气流动因素的任何湍动必将引起丝条震荡或飘荡,当振动振幅达到一定数值,就会传递到凝固区上方,使初生丝条干不均,风速过小时,丝条出环吹风室后受外界气流干扰的因素增强,以及丝条凝固点速度的减慢,使丝条飘忽、振动的因素增加,使初生丝条干不匀率变大;当内外环吹风滤芯风速控制在0.5~0.7m/s时,条干不匀率低;环吹风风温在20~24℃时,对丝条的张力和纤维的性质几乎没有影响,但当温度波动范围增加时,容易引起单丝间冷却长度的偏差,将影响纤维的条干不匀率,动态热拉伸应力的不均率,使纤维染色均匀性差,毛丝多,生产稳定性差等;在纺丝过程中水蒸气向聚酯熔体内部扩散的速率为10-9
~10-10
cm2/s,聚酯的平衡吸湿约为0.4%,因此刚纺出的单丝在60~300s之内即快速完成吸湿,对冷却吹风要求有恒定的相对湿度;随着冷却风相对湿度的提高,它的比热容和热容量将会增加,热吸收量随之增加;从而使冷却风在吸收同样的热量时温升低,能保证冷却吹风温度的相对稳定性,提高冷却效果;同时高的含湿量可减小丝条在纺丝中产生静电,减少丝条抖动或跳动,但过高的相对湿度会造成操作条件恶化和设备的锈蚀,因此冷却吹风的相对湿度不能太高,控制在75~85%较好;外环吹风向内吹风冷却丝条时,风速逐渐递减,外圈丝束均匀冷却,内环吹风向外依次吹向内圈丝束,风速逐渐递减,内外圈丝束均得到均匀冷却;外环吹送风风速和内环吹送风风速可以相同也可以不同,根据喷丝孔的排布方式可以灵活调整,当内圈孔排布密集或孔数较多时,内环吹送风风速高于外环吹送风风速,内圈孔排布少时,内环吹送风风速低于外环吹送风风速。
8.作为优选的技术方案:如上所述的一种多异形丝的生产设备,喷丝板的内径为45~50mm,外径为85~105mm,如此设计有利于提高喷丝孔喷丝的稳定性,减少孔道紊流产生短片段的不均匀;喷丝板上喷丝孔的数量为24~144,呈同心圆分布;喷丝孔包括导流孔、过渡孔和微孔,喷丝孔的深度为20~30mm(即为喷丝板厚度);微孔的截面形状为三角形、三叶形、十字形、w形、多c形、多h形、多叶形或错位丰字形,微孔的深度为0.27~0.70mm;错位丰字形由丰字形错位形成,丰字形由三条左侧横条、一条中间竖条和三条右侧横条组成,三条左侧横条等间距排列且间距为d,三条右侧横条等间距排列且间距为d,错位是指三条右侧横条下移d/2;内环吹风滤芯的内径为30~35mm,外环吹风滤芯的外径为100~120mm。
9.如上所述的一种多异形丝的生产设备,内环吹风滤芯由圆柱筒状的多孔板、圆柱筒状的不锈钢烛芯风筒和环形密封垫组成,不锈钢烛芯风筒位于多孔板内且二者共轴,多
孔板和不锈钢烛芯风筒的顶端和底端均通过环形密封垫相连;外环吹风滤芯的结构同内环吹风滤芯;外环吹风滤芯和内环吹风滤芯均可以周期更换清洗,重复使用。
10.如上所述的一种多异形丝的生产设备,外环吹风滤芯与内环吹风滤芯的顶端齐平,与喷丝板的距离为30~50mm;外环吹风滤芯的底端向下延伸形成无孔筒i,内环吹风滤芯的底端向下延伸形成无孔筒ii,无孔筒i与无孔筒ii的作用是延长丝条冷却时间,避免外界环境风对丝条的干扰;外环吹风滤芯和内环吹风滤芯的高度h1相等均为200~300mm,无孔筒i与无孔筒ii的高度h2相等均为50~60mm,h1与h2的比例为4~6:1。
11.如上所述的一种多异形丝的生产设备,多异形丝的生产设备还包括纺丝箱体、纺丝组件和缓冷区,内环吹送风管穿过纺丝箱体、纺丝组件和缓冷区穿入内环吹风滤芯内。
12.如上所述的一种多异形丝的生产设备,内环吹送风管位于纺丝箱体、纺丝组件和缓冷区内的长度段均采用海泡石保冷隔热材料制成,导热系数大约为0.045w/m
·
k,其特点是导热系数小,抗老化,轻质阻燃,在350℃高温下,结构不发生变化。
13.如上所述的一种多异形丝的生产设备,外环吹装置包括顺序连接的风机、送风管一、送风软管、送风管二和环吹风箱,送风软管的存在不仅可以避免风箱在送风压力的作用下产生震动,影响环吹风冷却,起到减震的作用,而且维修拆装方便,如果风阀控制装置坏,可以拆掉送风软管与送风管一连接处检查风阀;环吹风箱内设有多孔板一、整流板和多孔板二;外环吹风滤芯位于环吹风箱内,环吹风箱与送风管二的连接口记为接口c,多孔板一、整流板和多孔板二位于外环吹风滤芯以及接口c之间,整流板位于多孔板一与多孔板二之间;多孔板一和多孔板二,实现了对进入环吹滤芯的风速进行整流的目的,从而避免进入环吹滤芯的冷却风过于紊乱;整流板可以对经过多孔板一的冷却风进行缓冲和进一步整流,消除冷却风的紊乱;此装置解决了风箱内因气流紊乱,从而导致各滤芯内风速不一致的问题。
14.如上所述的一种多异形丝的生产设备,多孔板一与多孔板二的表面均匀分布圆形风孔,开孔率为80~90%;多孔板一与多孔板二的上端和下端均与环吹风箱焊接连接;整流板为1~1.5mm厚度的不锈钢板;整流板的高度小于多孔板一与多孔板二,整流板的上端与环吹风箱焊接连接。
15.如上所述的一种多异形丝的生产设备,多孔板一上风孔的直径为6mm,相邻两风孔的间距为4mm;多孔板二上风孔的直径为4mm,相邻两风孔的间距为3mm。
16.如上所述的一种多异形丝的生产设备,送风管一上设有风阀,风阀上设有调节风速的0~100%开度值,通过调节风阀的开度调整进入环吹风箱的风速;送风管二内设有过滤整流装置,过滤整流装置包括设于下层的钢丝网以及固定在钢丝网上的无纺布,钢丝网的设置可以提供过滤整流装置的稳定性,避免无纺布在冷却风的作用下变形;钢丝网和无纺布具有吸尘作用,在喷丝板面清洁时,可以更换清洗,保证冷却风的质量。
17.如上所述的环吹风箱上设有风速检测点,风速检测点处设有smc单向阀的快插接头,正常生产时,可以通过风速检测点检测风速是否正常,以满足初生纤维冷却的工艺条件。
18.如上所述的一种多异形丝的生产设备,外环吹装置中的送风管一和送风管二均为圆柱形中空腔;外环吹风自风机吹向送风管道时,经过两次分配,在静压室形成两次静压,以满足工艺冷却风的要求;第一分配是指冷却风从风机吹出后,自送风管一进入送风软管,
再进入送风管二内,由于送风管二内设有钢丝网和无纺布,在其阻力的作用下,使进入送风管二的冷却风在钢丝网和无纺布下方产生湍流效应,从而使得冷却风在送风管二钢丝网下方形成静压室,使得从钢丝网和无纺布中吹出的风速均匀、稳定;第二次分配是指从钢丝网和无纺布过滤整流中垂直向上吹出的风进入送风管二上方,再依次经过多孔板和整流板,最终水平的吹向环吹风风箱中,再由环吹风风箱中的滤芯水平吹向经喷丝板孔喷出的丝条;由于送风管二后设有多孔板和整流板的阻力作用,从而使得从钢丝网和无纺布中吹出的冷却风在送风管二上方形成静压室,从而使冷却风更加稳定的进入环吹风箱中,由多孔板和整流板整流;此工艺冷却风的特点为:冷却风由风机吹入送风管一,气流经过两次转弯,风速达到均匀去向一致后水平进入环吹风箱中,再经环吹风箱中的外环吹风滤芯水平吹向丝条进行冷却。
19.有益效果(1)本发明的一种多异形丝的生产设备,从喷丝板微孔中喷出的丝条经内外环吹风均匀冷却,纤维截面形状保持好,提高了纤维的异形度。
20.(2)本发明采用的外环吹送风风速和内环吹送风风速可以根据喷丝孔的排布方式可以灵活调整,当内圈孔排布密集或孔数较多时,内环吹送风风速高于外环吹送风风速,内圈孔排布少时,内环吹送风风速低于外环吹送风风速。而且可以减小环吹风的出风量,防止喷丝板板面受环吹风影响,板面温度降低,出现注头、滴丝等异常,提高生产稳定性和产品质量。
附图说明
21.图1为工艺路线图;图2为喷丝板进料面图;图3为喷丝板出丝面图;图4为喷丝板喷丝孔图;图5为喷丝孔微孔截面图;图6为缓冷区装置图;图7为上油装置图;图8为上油装置底座图;图9为上油装置的喷嘴座背面平面图;图10为上油装置的喷嘴座背面立体图;图11为上油装置的喷嘴座正视图;图12为上油装置的压盖图i;图13为上油装置分解图;图14为上油装置的压盖图ii;图15为内环吹风滤芯图;图16为外环吹风装置图;图17为多孔板图;图18为整流板图;图19为上油嘴集油槽示意图;
图20为实施例6的三角形微孔截面图;图21为实施例7的三叶形微孔截面图;图22为实施例8的十字形微孔截面图;图23为实施例9的w形微孔截面图;图24为实施例10的多c圆环形微孔截面图;图25为实施例11的多h形微孔截面图;图26为实施例12的五叶形微孔截面图;其中,1-纺丝箱体,2-纺丝组件,3-缓冷区,4-内环吹送风管,5-内环吹风滤芯,501-多孔板,502-不锈钢烛芯风筒,503-环形密封垫,601-风机,602-送风管一,603-送风软管,604-送风管二,605-环吹风箱,606-风阀,607-钢丝网,608-无纺布,609-快插接头,610-多孔板一,611-整流板,612-多孔板二,613-外环吹风滤芯,7-冷却单元,8-稳压单元,9-丝条,10-上油装置,11-甬道,12-分流孔,13-预网络器,14-牵伸热辊,15-定型热辊,16-主网络器,17-卷绕机,181-气相热媒进气孔,182-气相热媒回流孔,19-圆柱形通孔,20-锁扣,21-喷丝板,22-导流槽,23-导流孔,24-过渡孔,25-微孔,26-中间竖条,27-弧形条,28-上油管,29-快插i,30-不锈钢杆,301-进油通道,31-定位孔,32-o型圈i,33-压空管,34-快插ii,35-进油凹槽,36-进气凹槽,37-进油孔,38-进气孔,39-气流缓冲孔,40-定位螺孔,41-出油孔,42集油槽,43-喷气孔,44-凹槽i,45-凹槽ii,46-底座,47-喷嘴座,48-压盖i,49-压盖ii。
具体实施方式
22.下面结合具体实施方式,进一步阐述本发明。应理解,这些实施例仅用于说明本发明而不用于限制本发明的范围。此外应理解,在阅读了本发明讲授的内容之后,本领域技术人员可以对本发明作各种改动或修改,这些等价形式同样落于本技术所附权利要求书所限定的范围。
23.一种多异形丝的生产设备,如图1~19所示,包括纺丝箱体1;纺丝箱体1采用气相热媒加热和保温,气相热媒由热媒蒸发器提供,热媒蒸发器内设有一个u型管热交换器,u型管热交换器采用液相热媒加热,液相热媒由热媒站供应;纺丝箱体1内设有用于计量熔体的计量泵,计量泵的下方设有用于挤出熔体的纺丝组件2,纺丝组件2内设有环形结构的喷丝板21,喷丝板21内设有喷丝孔;喷丝板21上喷丝孔的数量为24~144,喷丝孔的深度为20~30mm,喷丝孔包括微孔25,位于微孔25的上方、共轴且自上而下顺序连接的导流槽22、导流孔23和过渡孔24;导流槽22和导流孔23构成的整体呈喇叭状,导流槽22的上端即为喇叭的大端;喷丝板21的一端面为熔体进料面,另一端面为喷丝面,导流槽22的上端位于熔体进料面上,微孔25的下端位于喷丝面上;微孔25的深度为0.27~0.70mm;微孔25的下端记为d,d在喷丝面上呈同心圆分布,同心圆由n个圆构成,n为3~6,同心圆的圆心为喷丝面的中心;相邻两圆上的d错位排列,同一圆上分布m个d,同一圆上的m个d对应的微孔25与同一个环形的导流槽22连接;同心圆中最外部的圆对应的导流槽22记为第一导流槽,第一导流槽的上端的内侧边缘与熔体进料面的外侧边缘之间的距离为6~10mm;同心圆中最内部的圆对应的导流槽22记为第n导流槽,第
n导流槽的上端的内侧边缘与熔体进料面的内侧边缘之间的距离为5~8mm;导流槽22的槽深为1.5~2.5mm,环形的导流槽22的上端记为u,u呈环形,该环形的内侧边缘为圆形a,外侧边缘为花瓣形,花瓣形由m个形状和尺寸相同的半圆相互连接而成,所有相邻的两个半圆的连接点连接形成一个与圆形a同心的圆形b,圆形a和圆形b的半径差为1.9~2.1mm;导流孔23在熔体进料面上的正投影呈圆形,该圆形同时与所述半圆和所述圆形a相切;微孔25的横截面主体呈错位丰字形;错位丰字形由丰字形错位形成;丰字形由三条左侧横条、一条中间竖条和三条右侧横条组成;中间竖条的上端融合标准三叶形,下端融合等腰三角形,中间竖条为两条短边位于上下侧、两条长边位于左右侧的长方形;上端融合标准三叶形即标准三叶形的一叶与长方形完全重合且该叶的中心轴与长方形的长对称轴重合,同时标准三叶形的中心点与长方形的上短边的中点重合,标准三叶形即三叶的叶长l3相等都为0.2~0.3mm、叶宽相等都为0.1~0.18mm、相邻两叶的中心轴线的夹角都为120
°
的三角形;下端融合三角形即等腰三角形的两腰分别经过长方形的两条长边,等腰三角形的顶点位于长方形的长对称轴上,同时等腰三角形的中心点与长方形的下短边的中点重合;等腰三角形的中心点与等腰三角形底边端点的距离l2为0.15~0.18mm;三条左侧横条等间距排列且间距为d,三条右侧横条等间距排列且间距为d;错位是指三条右侧横条下移d/2;三条左侧横条和三条右侧横条的尺寸相同,远离中间竖条的一端与中间竖条的竖直对称轴的距离l4为0.25~0.35mm,沿竖直方向的宽度w2为0.06~0.08mm,l4/w2>4.0;中间竖条沿竖直方向的长度l1为0.45~0.60mm,沿水平方向的宽度w1为0.12~0.15mm,l1/w1>3.0;每条左侧横条的左端都与一条位于其上方的弧形条连接成j形钩,每条右侧横条的右端都与一条位于其下方的弧形条连接成j形钩,各j形钩的钩尖与其主体部分的水平对称轴的距离h都相等,t=h/l4,0.16﹤t<0.5;喷丝板21的下方设有缓冷区3,缓冷区为设置在立方体内的圆柱形通孔19,设有圆柱形通孔的立方体由对称的两部分用锁扣20可拆卸连接而成,每部分都为中空结构,每部分的顶部设有气相热媒进气孔181,底部设有气相热媒回流孔182;缓冷区3的下方设有环吹风冷却装置,环吹风冷却装置包括圆柱筒状的外环吹风滤芯613、圆柱筒状的内环吹风滤芯、内环吹送风管4和外环吹装置;内环吹风滤芯5由圆柱筒状的多孔板501、圆柱筒状的不锈钢烛芯风筒502和环形密封垫503组成,不锈钢烛芯风筒502位于多孔板501内且二者共轴,多孔板501和不锈钢烛芯风筒502的顶端和底端均通过环形密封垫503相连;外环吹风滤芯613的结构同内环吹风滤芯;内环吹风滤芯的外径与喷丝板21的内径相同,为45~50mm,外环吹风滤芯613的内径与喷丝板21的外径相同,为85~105mm;内环吹风滤芯的内径为30~35mm,外环吹风滤芯613的外径为100~120mm;外环吹装置包括顺序连接的风机601、送风管一602、送风软管603、送风管二604和环吹风箱605;送风管一602和送风管二604均为圆柱形中空腔;环吹风箱605内设有多孔板一610、整流板611和多孔板二612,环吹风箱605上设有风速检测点,检测点上设有安装在环
吹风箱605上的快插接头609;送风管一602上设有风阀606,风阀606上设有调节风速的0~100%开度值,通过调节风阀的开度调整进入环吹风箱的风速;送风管二604内设有过滤整流装置,过滤整流装置包括设于下层的钢丝网607以及固定在钢丝网607上的无纺布608;多孔板一610与多孔板二612的表面均匀分布圆形风孔,开孔率为80~90%;多孔板一610上风孔的直径为6mm,相邻两风孔的间距为4mm;多孔板二612上风孔的直径为4mm,相邻两风孔的间距为3mm;多孔板一610与多孔板二612的上端和下端均与环吹风箱605焊接连接;整流板611为1~1.5mm厚度的不锈钢板;整流板611的高度小于多孔板一610与多孔板二612,整流板611的上端与环吹风箱605焊接连接;外环吹风滤芯613位于环吹风箱605内,环吹风箱605与送风管二604的连接口记为接口c,多孔板一610、整流板611和多孔板二612位于外环吹风滤芯613以及接口c之间,整流板611位于多孔板一610与多孔板二612之间;外环吹装置、外环吹风滤芯613和内环吹风滤芯都位于喷丝板21的下方且与其间隔一定的距离,外环吹装置与外环吹风滤芯613的中空部分相对的区域为空心区域,内环吹风滤芯位于外环吹风滤芯613内且二者共轴,内环吹风滤芯与喷丝板21共轴;外环吹风滤芯613与内环吹风滤芯的顶端齐平,与喷丝板21的距离为30~50mm,为冷却单元7;外环吹风滤芯613的底端向下延伸形成稳压单元8的无孔筒i,内环吹风滤芯的底端向下延伸形成无孔筒ii;外环吹风滤芯613和内环吹风滤芯的高度h1相等均为200~300mm,无孔筒i与无孔筒ii的高度h2相等均为50~60mm,h1与h2的比例为4~6:1;内环吹送风管4穿过纺丝箱体1、纺丝组件2和缓冷区3穿入内环吹风滤芯内,用于为内环吹风滤芯提供风速为0.5~0.7m/s、温度为20~24℃、相对湿度为75~85%的冷却风;内环吹送风管4位于纺丝箱体1、纺丝组件2和缓冷区3内的长度段均采用海泡石保冷隔热材料制成;外环吹装置用于为外环吹风滤芯613提供风速为0.5~0.7m/s、温度为20~24℃、相对湿度为75~85%的冷却风;环吹风冷却装置的下方设有上油装置10,上油装置10包括块体、上油管28、压空管33、底座46、快插i29、不锈钢杆30、快插ii 34和压盖ii 49;块体由左右相对的喷嘴座47和压盖i 48组成,压盖ii 49与压盖i 48背离喷嘴座47的表面连接,压盖ii 49背离压盖i 48的表面为弧面,压盖i 48面向喷嘴座47的表面的一边设为坡道结构;压盖ⅰ、压盖ⅱ与喷嘴座47等长,压盖ⅰ或压盖ⅱ的宽度与喷嘴座47的宽度之比为2:3;喷嘴座47和压盖i 48都为立方体结构;喷嘴座47背离压盖i 48的表面上设有上下两个圆柱形的凹槽,上凹槽的直径为4~6mm,下凹槽的直径为6~8mm;上凹槽的中心设有一直径为1~2mm的进油孔37;上凹槽内设有一层60~80目过滤网片,用于过滤油剂中的杂质过滤;下凹槽的中心设有一直径为2~3mm的进气孔38;下凹槽内进气孔38的一侧设有一个长方形气流缓冲孔39,压盖i 48上设有一个用于与气流缓冲孔39连通且形状和尺寸同气流缓冲孔39的通孔;底座46为立方体结构,底座46上设有直径为6~8mm的上螺纹孔、直径为8~10mm的下螺纹孔、o型圈ⅰ32、o型圈ⅱ、直径为4~6mm的上通孔、直径为6~8mm的下通孔、进油凹槽35和
进气凹槽36;不锈钢杆30的一端插入底座46的上螺纹孔内与其螺纹连接,同时与固定在底座46的上螺纹孔内的o型圈ⅰ32接触,底座46的上螺纹孔、上通孔和进油凹槽35顺序连接,底座46的进油凹槽35与喷嘴座47的上凹槽相对;快插ii 34插入底座46的下螺纹孔内与其螺纹连接,同时与固定在底座46的下螺纹孔内的o型圈ii接触,底座46的下螺纹孔、下通孔和进气凹槽顺序连接,底座46的进气凹槽与喷嘴座47的下凹槽相对;块体内设有丝条通道,丝条通道为横截面呈圆形、自上端至中间尺寸递减且自中间至下端尺寸递增的通孔,由左右对称的凹槽i 44和凹槽ii 45组成;凹槽i 44设置在喷嘴座47上且槽口位于喷嘴座47面向压盖i 48的表面上,凹槽ii 45设置在压盖i 48上且槽口位于压盖i 48面向喷嘴座47的表面上;凹槽i 44由上部分、中间部分、下部分组成,凹槽i 44的上部分与下部分为对称结构,长度都为15~20mm,最小直径都为2~5mm,最大直径都为4~8mm;上油管28依次经过快插i29、不锈钢杆30和底座46后,通过进油孔37、一设置在喷嘴座47内的出油孔41与喷嘴座47上的凹槽i 44的上部分连接;压空管33用于提供5~8bar的气流,依次经过快插ii 34和底座46后,通过进气孔38、一设置在喷嘴座47内的喷气孔43与喷嘴座47上的凹槽i 44的下部分连接;凹槽i 44上与上油管28连接的点记为接点a,凹槽i 44上与压空管33连接的点记为接点b,接点a与凹槽i 44的上端的距离为凹槽i 44的上部分长度的30%~40%,接点b与凹槽i 44的下端的距离为凹槽i 44的下部分长度的40%~50%;凹槽i 44的中间部分为圆柱状结构,直径同凹槽i 44的上部分的最小直径,长度为8~10mm;凹槽i 44的中间部分设有16~20个自上而下等间距排列且环绕丝条通道的中心轴设置的集油槽42,间距为0.5mm;集油槽42的槽体部分,深度为1~2mm,宽度为2~3mm;集油槽42的槽体外边沿中与丝条通道中的丝条接触的边为齿条状,相邻的集油槽42的齿条错开分布;各集油槽42中齿条的齿数为15~20个,齿槽宽w0为0.3~0.5mm,齿的高度h0为0.5~1.0mm;底座46、喷嘴座47、压盖i 48和压盖ii 49上均设有上下两个定位螺孔40,底座46、喷嘴座47、压盖i 48和压盖ii 49通过与定位螺孔40配合的定位螺钉固定为一体;不锈钢杆30的外表面设有定位孔31,上油装置10通过不锈钢杆30上的定位孔31固定在纺丝上油架上;上油装置10的下方设有甬道11,甬道11的底端设有分流孔12,甬道11的下方设有预网络器13,预网络器13的下方设有牵伸热辊14,牵伸热辊14的侧方设有定型热辊15,定型热辊15的下方设有主网络器16,主网络器16的下方设有卷绕机17。
24.使用本发明的一种多异形丝的生产设备的具体工艺过程为:聚酯输送的熔体经纺丝箱体1内计量泵精确计量后,由纺丝组件2过滤、喷丝孔喷出丝条9至缓冷区3缓冷,再经冷却单元7的内环吹风滤芯5和外环吹风滤芯613吹出的工艺风冷却后,至稳压单元8内延缓丝条冷却时间,经过上油装置10上油后,进入稳定丝条的甬道11经过分流孔12至预网络器13进一步匀化丝条上油,再经牵伸热辊14和定型热辊15牵伸定型,主网络器16网络后至卷绕机17卷绕成型。
25.实施例1一种多异形丝的生产设备,包括纺丝箱体;
纺丝箱体采用气相热媒加热和保温,气相热媒由热媒蒸发器提供,热媒蒸发器内设有一个u型管热交换器,u型管热交换器采用液相热媒加热,液相热媒由热媒站供应;纺丝箱体内设有用于计量熔体的计量泵,计量泵的下方设有用于挤出熔体的纺丝组件,纺丝组件内设有环形结构的喷丝板,喷丝板内设有喷丝孔;喷丝板上喷丝孔的数量为24,喷丝孔的深度为30mm,喷丝孔包括微孔,位于微孔的上方、共轴且自上而下顺序连接的导流槽、导流孔和过渡孔;导流槽和导流孔构成的整体呈喇叭状,导流槽的上端即为喇叭的大端;喷丝板的一端面为熔体进料面,另一端面为喷丝面,导流槽的上端位于熔体进料面上,微孔的下端位于喷丝面上;微孔的深度为0.7mm;微孔的下端记为d,d在喷丝面上呈同心圆分布,同心圆由n个圆构成,n为3,同心圆的圆心为喷丝面的中心;相邻两圆上的d错位排列,同一圆上分布m个d,同一圆上的m个d对应的微孔与同一个环形的导流槽连接;同心圆中最外部的圆对应的导流槽记为第一导流槽,第一导流槽的上端的内侧边缘与熔体进料面的外侧边缘之间的距离为10mm;同心圆中最内部的圆对应的导流槽记为第n导流槽,第n导流槽的上端的内侧边缘与熔体进料面的内侧边缘之间的距离为8mm;导流槽的槽深为2.5mm,环形的导流槽的上端记为u,u呈环形,该环形的内侧边缘为圆形a,外侧边缘为花瓣形,花瓣形由m个形状和尺寸相同的半圆相互连接而成,所有相邻的两个半圆的连接点连接形成一个与圆形a同心的圆形b,圆形a和圆形b的半径差为1.9mm;导流孔在熔体进料面上的正投影呈圆形,该圆形同时与所述半圆和所述圆形a相切;微孔的横截面主体呈错位丰字形;错位丰字形由丰字形错位形成;丰字形由三条左侧横条、一条中间竖条和三条右侧横条组成;中间竖条的上端融合标准三叶形,下端融合等腰三角形,中间竖条为两条短边位于上下侧、两条长边位于左右侧的长方形;上端融合标准三叶形即标准三叶形的一叶与长方形完全重合且该叶的中心轴与长方形的长对称轴重合,同时标准三叶形的中心点与长方形的上短边的中点重合,标准三叶形即三叶的叶长l3相等都为0.3mm、叶宽相等都为0.12mm、相邻两叶的中心轴线的夹角都为120
°
的三角形;下端融合三角形即等腰三角形的两腰分别经过长方形的两条长边,等腰三角形的顶点位于长方形的长对称轴上,同时等腰三角形的中心点与长方形的下短边的中点重合;等腰三角形的中心点与等腰三角形底边端点的距离l2为0.18mm;三条左侧横条等间距排列且间距为d,三条右侧横条等间距排列且间距为d;错位是指三条右侧横条下移d/2;三条左侧横条和三条右侧横条的尺寸相同,远离中间竖条的一端与中间竖条的竖直对称轴的距离l4为0.35mm,沿竖直方向的宽度w2为0.08mm;中间竖条沿竖直方向的长度l1为0.6mm,沿水平方向的宽度w1为0.14mm;每条左侧横条的左端都与一条位于其上方的弧形条连接成j形钩,每条右侧横条的右端都与一条位于其下方的弧形条连接成j形钩,各j形钩的钩尖与其主体部分的水平对称轴的距离h都相等,t=h/l4,t为0.45;喷丝板的下方设有缓冷区,缓冷区为设置在立方体内的圆柱形通孔,设有圆柱形通孔的立方体由对称的两部分用锁扣可拆卸连接而成,每部分都为中空结构,每部分的顶
部设有气相热媒进气孔,底部设有气相热媒回流孔;缓冷区的下方设有环吹风冷却装置,环吹风冷却装置包括圆柱筒状的外环吹风滤芯、圆柱筒状的内环吹风滤芯、内环吹送风管和外环吹装置;内环吹风滤芯由圆柱筒状的多孔板、圆柱筒状的不锈钢烛芯风筒和环形密封垫组成,不锈钢烛芯风筒位于多孔板内且二者共轴,多孔板和不锈钢烛芯风筒的顶端和底端均通过环形密封垫相连;外环吹风滤芯的结构同内环吹风滤芯;内环吹风滤芯的外径与喷丝板的内径相同,为45mm,外环吹风滤芯的内径与喷丝板的外径相同,为85mm;内环吹风滤芯的内径为30mm,外环吹风滤芯的外径为100mm;外环吹装置包括顺序连接的风机、送风管一、送风软管、送风管二和环吹风箱;送风管一和送风管二均为圆柱形中空腔;环吹风箱内设有多孔板一、整流板和多孔板二,环吹风箱上设有风速检测点,检测点上设有安装在环吹风箱上的快插接头;送风管一上设有风阀,风阀上设有调节风速的0~100%开度值,通过调节风阀的开度调整进入环吹风箱的风速;送风管二内设有过滤整流装置,过滤整流装置包括设于下层的钢丝网以及固定在钢丝网上的无纺布;多孔板一与多孔板二的表面均匀分布圆形风孔,开孔率为90%;多孔板一上风孔的直径为6mm,相邻两风孔的间距为4mm;多孔板二上风孔的直径为4mm,相邻两风孔的间距为3mm;多孔板一与多孔板二的上端和下端均与环吹风箱焊接连接;整流板为1.5mm厚度的不锈钢板;整流板的高度小于多孔板一与多孔板二,整流板的上端与环吹风箱焊接连接;外环吹风滤芯位于环吹风箱内,环吹风箱与送风管二的连接口记为接口c,多孔板一、整流板和多孔板二位于外环吹风滤芯以及接口c之间,整流板位于多孔板一与多孔板二之间;外环吹装置、外环吹风滤芯和内环吹风滤芯都位于喷丝板的下方且与其间隔一定的距离,外环吹装置与外环吹风滤芯的中空部分相对的区域为空心区域,内环吹风滤芯位于外环吹风滤芯内且二者共轴,内环吹风滤芯与喷丝板共轴;外环吹风滤芯与内环吹风滤芯的顶端齐平,与喷丝板的距离(即缓冷区高度)为50mm;外环吹风滤芯的底端向下延伸形成无孔筒i,内环吹风滤芯的底端向下延伸形成无孔筒ii;外环吹风滤芯和内环吹风滤芯的高度h1相等均为300mm,无孔筒i与无孔筒ii的高度h2相等均为50mm,h1与h2的比例为6:1;内环吹送风管穿过纺丝箱体1、纺丝组件和缓冷区穿入内环吹风滤芯内,用于为内环吹风滤芯提供风速为0.5m/s、温度为20℃、相对湿度为85%的冷却风;内环吹送风管位于纺丝箱体、纺丝组件和缓冷区内的长度段均采用海泡石保冷隔热材料制成;外环吹装置用于为外环吹风滤芯提供风速为0.7m/s、温度为20℃、相对湿度为75%的冷却风;环吹风冷却装置的下方设有上油装置,上油装置包括块体、上油管、压空管、底座、快插i、不锈钢杆、快插ii和压盖ii;块体由左右相对的喷嘴座和压盖i组成,压盖ii与压盖i背离喷嘴座的表面连接,压盖ii背离压盖i的表面为弧面,压盖i面向喷嘴座的表面的一边设为坡道结构;压盖ⅰ、压盖ⅱ与喷嘴座等长,压盖ⅰ或压盖ⅱ的宽度与喷嘴座的宽度之比为2:3;喷嘴座和压盖i都为立方体结构;喷嘴座背离压盖i的表面上设有上下两个圆柱形
的凹槽,上凹槽的直径为4mm,下凹槽的直径为6mm;上凹槽的中心设有一直径为1mm的进油孔;上凹槽内设有一层60目过滤网片,用于过滤油剂中的杂质过滤;下凹槽的中心设有一直径为2mm的进气孔;下凹槽内进气孔的一侧设有一个长方形气流缓冲孔,压盖i上设有一个用于与气流缓冲孔连通且形状和尺寸同气流缓冲孔的通孔;底座为立方体结构,底座上设有直径为6mm的上螺纹孔、直径为8mm的下螺纹孔、o型圈ⅰ、o型圈ⅱ、直径为4mm的上通孔、直径为6mm的下通孔、进油凹槽和进气凹槽;不锈钢杆的一端插入底座的上螺纹孔内与其螺纹连接,同时与固定在底座的上螺纹孔内的o型圈ⅰ接触,底座的上螺纹孔、上通孔和进油凹槽顺序连接,底座的进油凹槽与喷嘴座的上凹槽相对;快插ii插入底座的下螺纹孔内与其螺纹连接,同时与固定在底座的下螺纹孔内的o型圈ii接触,底座的下螺纹孔、下通孔和进气凹槽顺序连接,底座的进气凹槽与喷嘴座的下凹槽相对;块体内设有丝条通道,丝条通道为横截面呈圆形、自上端至中间尺寸递减且自中间至下端尺寸递增的通孔,由左右对称的凹槽i和凹槽ii组成;凹槽i设置在喷嘴座上且槽口位于喷嘴座面向压盖i的表面上,凹槽ii设置在压盖i上且槽口位于压盖i面向喷嘴座的表面上;凹槽i由上部分、中间部分、下部分组成,凹槽i的上部分与下部分为对称结构,长度都为15mm,最小直径都为2mm,最大直径都为4mm;上油管依次经过快插i、不锈钢杆和底座后,通过进油孔、一设置在喷嘴座内的出油孔与喷嘴座上的凹槽i的上部分连接;压空管用于提供5bar的气流,依次经过快插ii和底座后,通过进气孔、一设置在喷嘴座内的喷气孔与喷嘴座上的凹槽i的下部分连接;凹槽i上与上油管连接的点记为接点a,凹槽i上与压空管连接的点记为接点b,接点a与凹槽i的上端的距离为凹槽i的上部分长度的30%,接点b与凹槽i的下端的距离为凹槽i的下部分长度的45%;凹槽i的中间部分为圆柱状结构,直径同凹槽i的上部分的最小直径,长度为8mm;凹槽i的中间部分设有16个自上而下等间距排列且环绕丝条通道的中心轴设置的集油槽,间距为0.5mm;集油槽的槽体部分,深度为1mm,宽度为2mm;集油槽的槽体外边沿中与丝条通道中的丝条接触的边为齿条状,相邻的集油槽的齿条错开分布;各集油槽中齿条的齿数为15个,齿槽宽w0为0.3mm,齿的高度h0为1.0mm;底座、喷嘴座、压盖i和压盖ii上均设有上下两个定位螺孔,底座、喷嘴座、压盖i和压盖ii通过与定位螺孔配合的定位螺钉固定为一体;不锈钢杆的外表面设有定位孔,上油装置通过不锈钢杆上的定位孔固定在纺丝上油架上;上油装置的下方设有甬道,甬道的底端设有分流孔,甬道的下方设有预网络器,预网络器的下方设有牵伸热辊,牵伸热辊的侧方设有定型热辊,定型热辊的下方设有主网络器,主网络器的下方设有卷绕机。
26.一种多异形丝的制备方法,采用上述的一种多异形丝的生产设备进行加工;具体工艺流程为:熔体输送
→
熔体计量
→
组件过滤
→
熔体挤出
→
缓冷区缓冷
→
冷却成形
→
集束上油
→
牵伸定型
→
卷绕成型;
其中,工艺流程还包括熔体的制取、输送,熔体制取、输送过程为:采用对苯二甲酸和乙二醇作为原料,其中对苯二甲酸和乙二醇摩尔比为1:2.0,加入量为对苯二甲酸0.01wt%的乙二醇锑和对苯二甲酸加入量0.02wt%的磷酸三苯酯混合均匀后,在氮气氛围中通过控制反应温度和压力进行酯化反应,酯化反应时间为2.5小时,压力为0.15mpa,温度为260℃,酯化反应终点为酯化水馏出达到理论值的90%;经酯化后的对苯二甲酸乙二醇酯进入缩聚反应阶段,缩聚反应,为负压反应,共分为三步缩聚,缩聚一反应压力为90mbar,停留时间为1h,缩聚一的温度为260℃,缩聚二的温度为270℃,缩聚二的压力为30 mbar,停留时间约1.5h,终缩聚的温度为275℃,终缩聚的压力为20mbar,停留时间1.5h,制得聚合物熔体;缩聚反应后的熔体经过装有过滤精度为15μm滤芯的过滤器过滤掉熔体中15~25μm的机械杂质粒子,由熔体管道输送至增压泵增压,增压后的压力为175bar,保证熔体输送至单纺位计量泵熔体入口压力为78bar;经增压后的熔体再通过换热器调节温度为283℃后进入纺丝箱体中;工艺参数包括:熔体挤出温度286℃,缓冷区温度240℃,牵伸热辊速度2500m/min,牵伸热辊温度85℃,预网络器压力0.5bar,主网络器压力3.6bar,定型热辊速度4300m/min,定型热辊温度124℃,卷绕速度4200m/min,卷绕密度0.98g/cm
³
,卷绕直径355mm,卷绕角4.3,卷绕机压力辊与丝饼之间接触压力值300n。
27.最终制得的多异形丝的单丝纤度为3.6dtex,线密度偏差率为0.56%,断裂强度为4.39cn/dtex,断裂强度不匀率为2.8%,断裂伸长率为35.0%,断裂伸长率不匀率为4.5%,条干不匀率为0.7%,沸水收缩率为8.0%,上油率为1.05wt%,弹性回复率为85%,压缩弹性率为59%,异形度为30%,异形度测试方法为化学纤维异形度试验方法,具体为fz-t5002-2013中华人民共和国纺织行业标准:相对径向异形度dr=(1-r/r)
×
100%,其它指标的测试方法参考《gb/t 8960-2015涤纶牵伸丝》、《gb/t 14343化学纤维长丝线密度试验方法》、《gb/t 14344化学纤维长丝拉伸性能试验方法》、《gb/t 6505化学纤维长丝热收缩率试验方法》、《fz/t 01034-2008-纺织品机织物拉伸弹性试验方法》,下同。
28.实施例2一种多异形丝的生产设备,包括纺丝箱体;纺丝箱体采用气相热媒加热和保温,气相热媒由热媒蒸发器提供,热媒蒸发器内设有一个u型管热交换器,u型管热交换器采用液相热媒加热,液相热媒由热媒站供应;纺丝箱体内设有用于计量熔体的计量泵,计量泵的下方设有用于挤出熔体的纺丝组件,纺丝组件内设有环形结构的喷丝板,喷丝板内设有喷丝孔;喷丝板上喷丝孔的数量为36,喷丝孔的深度为28mm,喷丝孔包括微孔,位于微孔的上方、共轴且自上而下顺序连接的导流槽、导流孔和过渡孔;导流槽和导流孔构成的整体呈喇叭状,导流槽的上端即为喇叭的大端;喷丝板的一端面为熔体进料面,另一端面为喷丝面,导流槽的上端位于熔体进料面上,微孔的下端位于喷丝面上;微孔的深度为0.6mm;微孔的下端记为d,d在喷丝面上呈同心圆分布,同心圆由n个圆构成,n为4,同心圆的圆心为喷丝面的中心;相邻两圆上的d错位排列,同一圆上分布m个d,同一圆上的m个d对应的微孔与同一个环形的导流槽连接;同心圆中最外部的圆对应的导流槽记为第一导流槽,第一导流槽的上端的内侧边缘与熔体进料面的外侧边缘之间的距离为9mm;同心圆中最内部的圆对应的导流槽记为第n导流槽,第n导流槽的上端的内侧边缘与
熔体进料面的内侧边缘之间的距离为7mm;导流槽的槽深为2.1mm,环形的导流槽的上端记为u,u呈环形,该环形的内侧边缘为圆形a,外侧边缘为花瓣形,花瓣形由m个形状和尺寸相同的半圆相互连接而成,所有相邻的两个半圆的连接点连接形成一个与圆形a同心的圆形b,圆形a和圆形b的半径差为2.1mm;导流孔在熔体进料面上的正投影呈圆形,该圆形同时与所述半圆和所述圆形a相切;微孔的横截面主体呈错位丰字形;错位丰字形由丰字形错位形成;丰字形由三条左侧横条、一条中间竖条和三条右侧横条组成;中间竖条的上端融合标准三叶形,下端融合等腰三角形,中间竖条为两条短边位于上下侧、两条长边位于左右侧的长方形;上端融合标准三叶形即标准三叶形的一叶与长方形完全重合且该叶的中心轴与长方形的长对称轴重合,同时标准三叶形的中心点与长方形的上短边的中点重合,标准三叶形即三叶的叶长l3相等都为0.28mm、叶宽相等都为0.13mm、相邻两叶的中心轴线的夹角都为120
°
的三角形;下端融合三角形即等腰三角形的两腰分别经过长方形的两条长边,等腰三角形的顶点位于长方形的长对称轴上,同时等腰三角形的中心点与长方形的下短边的中点重合;等腰三角形的中心点与等腰三角形底边端点的距离l2为0.16mm;三条左侧横条等间距排列且间距为d,三条右侧横条等间距排列且间距为d;错位是指三条右侧横条下移d/2;三条左侧横条和三条右侧横条的尺寸相同,远离中间竖条的一端与中间竖条的竖直对称轴的距离l4为0.33mm,沿竖直方向的宽度w2为0.07mm;中间竖条沿竖直方向的长度l1为0.51mm,沿水平方向的宽度w1为0.12mm;每条左侧横条的左端都与一条位于其上方的弧形条连接成j形钩,每条右侧横条的右端都与一条位于其下方的弧形条连接成j形钩,各j形钩的钩尖与其主体部分的水平对称轴的距离h都相等,t=h/l4,t为0.32;喷丝板的下方设有缓冷区,缓冷区为设置在立方体内的圆柱形通孔,设有圆柱形通孔的立方体由对称的两部分用锁扣可拆卸连接而成,每部分都为中空结构,每部分的顶部设有气相热媒进气孔,底部设有气相热媒回流孔;缓冷区的下方设有环吹风冷却装置,环吹风冷却装置包括圆柱筒状的外环吹风滤芯、圆柱筒状的内环吹风滤芯、内环吹送风管和外环吹装置;内环吹风滤芯由圆柱筒状的多孔板、圆柱筒状的不锈钢烛芯风筒和环形密封垫组成,不锈钢烛芯风筒位于多孔板内且二者共轴,多孔板和不锈钢烛芯风筒的顶端和底端均通过环形密封垫相连;外环吹风滤芯的结构同内环吹风滤芯;内环吹风滤芯的外径与喷丝板的内径相同,为45mm,外环吹风滤芯的内径与喷丝板的外径相同,为95mm;内环吹风滤芯的内径为30mm,外环吹风滤芯的外径为110mm;外环吹装置包括顺序连接的风机、送风管一、送风软管、送风管二和环吹风箱;送风管一和送风管二均为圆柱形中空腔;环吹风箱内设有多孔板一、整流板和多孔板二,环吹风箱上设有风速检测点,检测点上设有安装在环吹风箱上的快插接头;送风管一上设有风阀,风阀上设有调节风速的0~100%开度值,通过调节风阀的开度调整进入环吹风箱的风速;送风管二内设有过滤整流装置,过滤整流装置包括设于下层
的钢丝网以及固定在钢丝网上的无纺布;多孔板一与多孔板二的表面均匀分布圆形风孔,开孔率为85%;多孔板一上风孔的直径为6mm,相邻两风孔的间距为4mm;多孔板二上风孔的直径为4mm,相邻两风孔的间距为3mm;多孔板一与多孔板二的上端和下端均与环吹风箱焊接连接;整流板为1.4mm厚度的不锈钢板;整流板的高度小于多孔板一与多孔板二,整流板的上端与环吹风箱焊接连接;外环吹风滤芯位于环吹风箱内,环吹风箱与送风管二的连接口记为接口c,多孔板一、整流板和多孔板二位于外环吹风滤芯以及接口c之间,整流板位于多孔板一与多孔板二之间;外环吹装置、外环吹风滤芯和内环吹风滤芯都位于喷丝板的下方且与其间隔一定的距离,外环吹装置与外环吹风滤芯的中空部分相对的区域为空心区域,内环吹风滤芯位于外环吹风滤芯内且二者共轴,内环吹风滤芯与喷丝板共轴;外环吹风滤芯与内环吹风滤芯的顶端齐平,与喷丝板的距离(即缓冷区高度)为40mm;外环吹风滤芯的底端向下延伸形成无孔筒i,内环吹风滤芯的底端向下延伸形成无孔筒ii;外环吹风滤芯和内环吹风滤芯的高度h1相等均为250mm,无孔筒i与无孔筒ii的高度h2相等均为50mm,h1与h2的比例为5:1;内环吹送风管穿过纺丝箱体1、纺丝组件和缓冷区穿入内环吹风滤芯内,用于为内环吹风滤芯提供风速为0.6m/s、温度为24℃、相对湿度为75%的冷却风;内环吹送风管位于纺丝箱体、纺丝组件和缓冷区内的长度段均采用海泡石保冷隔热材料制成;外环吹装置用于为外环吹风滤芯提供风速为0.6m/s、温度为24℃、相对湿度为85%的冷却风;环吹风冷却装置的下方设有上油装置,上油装置包括块体、上油管、压空管、底座、快插i、不锈钢杆、快插ii和压盖ii;块体由左右相对的喷嘴座和压盖i组成,压盖ii与压盖i背离喷嘴座的表面连接,压盖ii背离压盖i的表面为弧面,压盖i面向喷嘴座的表面的一边设为坡道结构;压盖ⅰ、压盖ⅱ与喷嘴座等长,压盖ⅰ或压盖ⅱ的宽度与喷嘴座的宽度之比为2:3;喷嘴座和压盖i都为立方体结构;喷嘴座背离压盖i的表面上设有上下两个圆柱形的凹槽,上凹槽的直径为6mm,下凹槽的直径为8mm;上凹槽的中心设有一直径为2mm的进油孔;上凹槽内设有一层80目过滤网片,用于过滤油剂中的杂质过滤;下凹槽的中心设有一直径为3mm的进气孔;下凹槽内进气孔的一侧设有一个长方形气流缓冲孔,压盖i上设有一个用于与气流缓冲孔连通且形状和尺寸同气流缓冲孔的通孔;底座为立方体结构,底座上设有直径为7mm的上螺纹孔、直径为10mm的下螺纹孔、o型圈ⅰ、o型圈ⅱ、直径为6mm的上通孔、直径为8mm的下通孔、进油凹槽和进气凹槽;不锈钢杆的一端插入底座的上螺纹孔内与其螺纹连接,同时与固定在底座的上螺纹孔内的o型圈ⅰ接触,底座的上螺纹孔、上通孔和进油凹槽顺序连接,底座的进油凹槽与喷嘴座的上凹槽相对;快插ii插入底座的下螺纹孔内与其螺纹连接,同时与固定在底座的下螺纹孔内的o型圈ii接触,底座的下螺纹孔、下通孔和进气凹槽顺序连接,底座的进气凹槽与喷嘴座的下凹槽相对;块体内设有丝条通道,丝条通道为横截面呈圆形、自上端至中间尺寸递减且自中
间至下端尺寸递增的通孔,由左右对称的凹槽i和凹槽ii组成;凹槽i设置在喷嘴座上且槽口位于喷嘴座面向压盖i的表面上,凹槽ii设置在压盖i上且槽口位于压盖i面向喷嘴座的表面上;凹槽i由上部分、中间部分、下部分组成,凹槽i的上部分与下部分为对称结构,长度都为20mm,最小直径都为5mm,最大直径都为8mm;上油管依次经过快插i、不锈钢杆和底座后,通过进油孔、一设置在喷嘴座内的出油孔与喷嘴座上的凹槽i的上部分连接;压空管用于提供8bar的气流,依次经过快插ii和底座后,通过进气孔、一设置在喷嘴座内的喷气孔与喷嘴座上的凹槽i的下部分连接;凹槽i上与上油管连接的点记为接点a,凹槽i上与压空管连接的点记为接点b,接点a与凹槽i的上端的距离为凹槽i的上部分长度的40%,接点b与凹槽i的下端的距离为凹槽i的下部分长度的50%;凹槽i的中间部分为圆柱状结构,直径同凹槽i的上部分的最小直径,长度为10mm;凹槽i的中间部分设有20个自上而下等间距排列且环绕丝条通道的中心轴设置的集油槽,间距为0.5mm;集油槽的槽体部分,深度为2mm,宽度为3mm;集油槽的槽体外边沿中与丝条通道中的丝条接触的边为齿条状,相邻的集油槽的齿条错开分布;各集油槽中齿条的齿数为20个,齿槽宽w0为0.5mm,齿的高度h0为0.9mm;底座、喷嘴座、压盖i和压盖ii上均设有上下两个定位螺孔,底座、喷嘴座、压盖i和压盖ii通过与定位螺孔配合的定位螺钉固定为一体;不锈钢杆的外表面设有定位孔,上油装置通过不锈钢杆上的定位孔固定在纺丝上油架上;上油装置的下方设有甬道,甬道的底端设有分流孔,甬道的下方设有预网络器,预网络器的下方设有牵伸热辊,牵伸热辊的侧方设有定型热辊,定型热辊的下方设有主网络器,主网络器的下方设有卷绕机。
29.一种多异形丝的制备方法,采用上述的一种多异形丝的生产设备进行加工;具体工艺流程为:熔体输送
→
熔体计量
→
组件过滤
→
熔体挤出
→
缓冷区缓冷
→
冷却成形
→
集束上油
→
牵伸定型
→
卷绕成型;其中,工艺流程还包括熔体的制取、输送,熔体制取、输送过程为:采用对苯二甲酸和乙二醇作为原料,其中对苯二甲酸和乙二醇摩尔比为1:1.5,加入量为对苯二甲酸0.03wt%的乙二醇锑和对苯二甲酸加入量0.03wt%的磷酸三苯酯混合均匀后,在氮气氛围中通过控制反应温度和压力进行酯化反应,酯化反应时间为3.5小时,压力为0.35mpa,温度为265℃,酯化反应终点为酯化水馏出达到理论值的99%;经酯化后的对苯二甲酸乙二醇酯进入缩聚反应阶段,缩聚反应,为负压反应,共分为三步缩聚,缩聚一反应压力为100mbar,停留时间为0.5h,缩聚一的温度为265℃,缩聚二的温度为275℃,缩聚二的压力为20 mbar,停留时间约1h,终缩聚的温度为280℃,终缩聚的压力为10mbar,停留时间1h,制得聚合物熔体;缩聚反应后的熔体经过装有过滤精度为15μm滤芯的过滤器过滤掉熔体中15~25μm的机械杂质粒子,由熔体管道输送至增压泵增压,增压后的压力为170bar,保证熔体输送至单纺位计量泵熔体入口压力为75bar;经增压后的熔体再通过换热器调节温度为285℃后进入纺丝箱体中;工艺参数包括:熔体挤出温度288℃,缓冷区温度245℃,牵伸热辊速度2900m/min,
牵伸热辊温度86℃,预网络器压力0.7bar,主网络器压力3.5bar,定型热辊速度4190m/min,定型热辊温度122℃,卷绕速度4100m/min,卷绕密度0.98g/cm
³
,卷绕直径358mm,卷绕角4.6,卷绕机压力辊与丝饼之间接触压力值280n。
30.最终制得的多异形丝的单丝纤度为2.3dtex,线密度偏差率为0.41%,断裂强度为4.28cn/dtex,断裂强度不匀率为3.0%,断裂伸长率为35.5%,断裂伸长率不匀率为5.2%,条干不匀率为0.85%,沸水收缩率为8.1%,上油率为1.09wt%,弹性回复率为86%,压缩弹性率为60%,异形度为35%。
31.实施例3一种多异形丝的生产设备,包括纺丝箱体;纺丝箱体采用气相热媒加热和保温,气相热媒由热媒蒸发器提供,热媒蒸发器内设有一个u型管热交换器,u型管热交换器采用液相热媒加热,液相热媒由热媒站供应;纺丝箱体内设有用于计量熔体的计量泵,计量泵的下方设有用于挤出熔体的纺丝组件,纺丝组件内设有环形结构的喷丝板,喷丝板内设有喷丝孔;喷丝板上喷丝孔的数量为72,喷丝孔的深度为24mm,喷丝孔包括微孔,位于微孔的上方、共轴且自上而下顺序连接的导流槽、导流孔和过渡孔;导流槽和导流孔构成的整体呈喇叭状,导流槽的上端即为喇叭的大端;喷丝板的一端面为熔体进料面,另一端面为喷丝面,导流槽的上端位于熔体进料面上,微孔的下端位于喷丝面上;微孔的深度为0.5mm;微孔的下端记为d,d在喷丝面上呈同心圆分布,同心圆由n个圆构成,n为5,同心圆的圆心为喷丝面的中心;相邻两圆上的d错位排列,同一圆上分布m个d,同一圆上的m个d对应的微孔与同一个环形的导流槽连接;同心圆中最外部的圆对应的导流槽记为第一导流槽,第一导流槽的上端的内侧边缘与熔体进料面的外侧边缘之间的距离为8mm;同心圆中最内部的圆对应的导流槽记为第n导流槽,第n导流槽的上端的内侧边缘与熔体进料面的内侧边缘之间的距离为6mm;导流槽的槽深为1.8mm,环形的导流槽的上端记为u,u呈环形,该环形的内侧边缘为圆形a,外侧边缘为花瓣形,花瓣形由m个形状和尺寸相同的半圆相互连接而成,所有相邻的两个半圆的连接点连接形成一个与圆形a同心的圆形b,圆形a和圆形b的半径差为2.0mm;导流孔在熔体进料面上的正投影呈圆形,该圆形同时与所述半圆和所述圆形a相切;微孔的横截面主体呈错位丰字形;错位丰字形由丰字形错位形成;丰字形由三条左侧横条、一条中间竖条和三条右侧横条组成;中间竖条的上端融合标准三叶形,下端融合等腰三角形,中间竖条为两条短边位于上下侧、两条长边位于左右侧的长方形;上端融合标准三叶形即标准三叶形的一叶与长方形完全重合且该叶的中心轴与长方形的长对称轴重合,同时标准三叶形的中心点与长方形的上短边的中点重合,标准三叶形即三叶的叶长l3相等都为0.23mm、叶宽相等都为0.11mm、相邻两叶的中心轴线的夹角都为120
°
的三角形;下端融合三角形即等腰三角形的两腰分别经过长方形的两条长边,等腰三角形的顶点位于长方形的长对称轴上,同时等腰三角形的中心点与长方形的下短边的中点重合;等腰三角形的中心点与等腰三角形底边端点的距离l2为0.16mm;
三条左侧横条等间距排列且间距为d,三条右侧横条等间距排列且间距为d;错位是指三条右侧横条下移d/2;三条左侧横条和三条右侧横条的尺寸相同,远离中间竖条的一端与中间竖条的竖直对称轴的距离l4为0.29mm,沿竖直方向的宽度w2为0.068mm;中间竖条沿竖直方向的长度l1为0.5mm,沿水平方向的宽度w1为0.13mm;每条左侧横条的左端都与一条位于其上方的弧形条连接成j形钩,每条右侧横条的右端都与一条位于其下方的弧形条连接成j形钩,各j形钩的钩尖与其主体部分的水平对称轴的距离h都相等,t=h/l4,t为0.28;喷丝板的下方设有缓冷区,缓冷区为设置在立方体内的圆柱形通孔,设有圆柱形通孔的立方体由对称的两部分用锁扣可拆卸连接而成,每部分都为中空结构,每部分的顶部设有气相热媒进气孔,底部设有气相热媒回流孔;缓冷区的下方设有环吹风冷却装置,环吹风冷却装置包括圆柱筒状的外环吹风滤芯、圆柱筒状的内环吹风滤芯、内环吹送风管和外环吹装置;内环吹风滤芯由圆柱筒状的多孔板、圆柱筒状的不锈钢烛芯风筒和环形密封垫组成,不锈钢烛芯风筒位于多孔板内且二者共轴,多孔板和不锈钢烛芯风筒的顶端和底端均通过环形密封垫相连;外环吹风滤芯的结构同内环吹风滤芯;内环吹风滤芯的外径与喷丝板的内径相同,为50mm,外环吹风滤芯的内径与喷丝板的外径相同,为105mm;内环吹风滤芯的内径为35mm,外环吹风滤芯的外径为120mm;外环吹装置包括顺序连接的风机、送风管一、送风软管、送风管二和环吹风箱;送风管一和送风管二均为圆柱形中空腔;环吹风箱内设有多孔板一、整流板和多孔板二,环吹风箱上设有风速检测点,检测点上设有安装在环吹风箱上的快插接头;送风管一上设有风阀,风阀上设有调节风速的0~100%开度值,通过调节风阀的开度调整进入环吹风箱的风速;送风管二内设有过滤整流装置,过滤整流装置包括设于下层的钢丝网以及固定在钢丝网上的无纺布;多孔板一与多孔板二的表面均匀分布圆形风孔,开孔率为82%;多孔板一上风孔的直径为6mm,相邻两风孔的间距为4mm;多孔板二上风孔的直径为4mm,相邻两风孔的间距为3mm;多孔板一与多孔板二的上端和下端均与环吹风箱焊接连接;整流板为1.2mm厚度的不锈钢板;整流板的高度小于多孔板一与多孔板二,整流板的上端与环吹风箱焊接连接;外环吹风滤芯位于环吹风箱内,环吹风箱与送风管二的连接口记为接口c,多孔板一、整流板和多孔板二位于外环吹风滤芯以及接口c之间,整流板位于多孔板一与多孔板二之间;外环吹装置、外环吹风滤芯和内环吹风滤芯都位于喷丝板的下方且与其间隔一定的距离,外环吹装置与外环吹风滤芯的中空部分相对的区域为空心区域,内环吹风滤芯位于外环吹风滤芯内且二者共轴,内环吹风滤芯与喷丝板共轴;外环吹风滤芯与内环吹风滤芯的顶端齐平,与喷丝板的距离(即缓冷区高度)为35mm;外环吹风滤芯的底端向下延伸形成无孔筒i,内环吹风滤芯的底端向下延伸形成无孔筒ii;外环吹风滤芯和内环吹风滤芯的高度h1相等均为250mm,无孔筒i与无孔筒ii的高度h2相等均为60mm,h1与h2的比例为4.1:1;内环吹送风管穿过纺丝箱体1、纺丝组件和缓冷区穿入内环吹风滤芯内,用于为内环吹风滤芯提供风速为0.7m/s、温度为22℃、相对湿度为80%的冷却风;内环吹送风管位于
纺丝箱体、纺丝组件和缓冷区内的长度段均采用海泡石保冷隔热材料制成;外环吹装置用于为外环吹风滤芯提供风速为0.5m/s、温度为22℃、相对湿度为80%的冷却风;环吹风冷却装置的下方设有上油装置,上油装置包括块体、上油管、压空管、底座、快插i、不锈钢杆、快插ii和压盖ii;块体由左右相对的喷嘴座和压盖i组成,压盖ii与压盖i背离喷嘴座的表面连接,压盖ii背离压盖i的表面为弧面,压盖i面向喷嘴座的表面的一边设为坡道结构;压盖ⅰ、压盖ⅱ与喷嘴座等长,压盖ⅰ或压盖ⅱ的宽度与喷嘴座的宽度之比为2:3;喷嘴座和压盖i都为立方体结构;喷嘴座背离压盖i的表面上设有上下两个圆柱形的凹槽,上凹槽的直径为5mm,下凹槽的直径为7mm;上凹槽的中心设有一直径为1.5mm的进油孔;上凹槽内设有一层60目过滤网片,用于过滤油剂中的杂质过滤;下凹槽的中心设有一直径为2mm的进气孔;下凹槽内进气孔的一侧设有一个长方形气流缓冲孔,压盖i上设有一个用于与气流缓冲孔连通且形状和尺寸同气流缓冲孔的通孔;底座为立方体结构,底座上设有直径为7mm的上螺纹孔、直径为9mm的下螺纹孔、o型圈ⅰ、o型圈ⅱ、直径为5mm的上通孔、直径为7mm的下通孔、进油凹槽和进气凹槽;不锈钢杆的一端插入底座的上螺纹孔内与其螺纹连接,同时与固定在底座的上螺纹孔内的o型圈ⅰ接触,底座的上螺纹孔、上通孔和进油凹槽顺序连接,底座的进油凹槽与喷嘴座的上凹槽相对;快插ii插入底座的下螺纹孔内与其螺纹连接,同时与固定在底座的下螺纹孔内的o型圈ii接触,底座的下螺纹孔、下通孔和进气凹槽顺序连接,底座的进气凹槽与喷嘴座的下凹槽相对;块体内设有丝条通道,丝条通道为横截面呈圆形、自上端至中间尺寸递减且自中间至下端尺寸递增的通孔,由左右对称的凹槽i和凹槽ii组成;凹槽i设置在喷嘴座上且槽口位于喷嘴座面向压盖i的表面上,凹槽ii设置在压盖i上且槽口位于压盖i面向喷嘴座的表面上;凹槽i由上部分、中间部分、下部分组成,凹槽i的上部分与下部分为对称结构,长度都为17mm,最小直径都为4mm,最大直径都为7mm;上油管依次经过快插i、不锈钢杆和底座后,通过进油孔、一设置在喷嘴座内的出油孔与喷嘴座上的凹槽i的上部分连接;压空管用于提供7.5bar的气流,依次经过快插ii和底座后,通过进气孔、一设置在喷嘴座内的喷气孔与喷嘴座上的凹槽i的下部分连接;凹槽i上与上油管连接的点记为接点a,凹槽i上与压空管连接的点记为接点b,接点a与凹槽i的上端的距离为凹槽i的上部分长度的30%,接点b与凹槽i的下端的距离为凹槽i的下部分长度的40%;凹槽i的中间部分为圆柱状结构,直径同凹槽i的上部分的最小直径,长度为9mm;凹槽i的中间部分设有19个自上而下等间距排列且环绕丝条通道的中心轴设置的集油槽,n为,间距为0.5mm;集油槽的槽体部分,深度为1.5mm,宽度为2.5mm;集油槽的槽体外边沿中与丝条通道中的丝条接触的边为齿条状,相邻的集油槽的齿条错开分布;各集油槽中齿条的齿数为19个,齿槽宽w0为0.4mm,齿的高度h0为0.8mm;底座、喷嘴座、压盖i和压盖ii上均设有上下两个定位螺孔,底座、喷嘴座、压盖i和
压盖ii通过与定位螺孔配合的定位螺钉固定为一体;不锈钢杆的外表面设有定位孔,上油装置通过不锈钢杆上的定位孔固定在纺丝上油架上;上油装置的下方设有甬道,甬道的底端设有分流孔,甬道的下方设有预网络器,预网络器的下方设有牵伸热辊,牵伸热辊的侧方设有定型热辊,定型热辊的下方设有主网络器,主网络器的下方设有卷绕机。
32.一种多异形丝的制备方法,采用上述的一种多异形丝的生产设备进行加工;具体工艺流程为:熔体输送
→
熔体计量
→
组件过滤
→
熔体挤出
→
缓冷区缓冷
→
冷却成形
→
集束上油
→
牵伸定型
→
卷绕成型;其中,工艺流程还包括熔体的制取、输送,熔体制取、输送过程为:采用对苯二甲酸和乙二醇作为原料,其中对苯二甲酸和乙二醇摩尔比为1:1.1,加入量为对苯二甲酸0.02wt%的乙二醇锑和对苯二甲酸加入量0.04wt%的磷酸三苯酯混合均匀后,在氮气氛围中通过控制反应温度和压力进行酯化反应,酯化反应时间为3小时,压力为0.3mpa,温度为262℃,酯化反应终点为酯化水馏出达到理论值的93%;经酯化后的对苯二甲酸乙二醇酯进入缩聚反应阶段,缩聚反应,为负压反应,共分为三步缩聚,缩聚一反应压力为93mbar,停留时间为0.8h,缩聚一的温度为263℃,缩聚二的温度为272℃,缩聚二的压力为27 mbar,停留时间约1.2h,终缩聚的温度为276℃,终缩聚的压力为18mbar,停留时间1.4h,制得聚合物熔体;缩聚反应后的熔体经过装有过滤精度为15μm滤芯的过滤器过滤掉熔体中15~25μm的机械杂质粒子,由熔体管道输送至增压泵增压,增压后的压力为165bar,保证熔体输送至单纺位计量泵熔体入口压力为73bar;经增压后的熔体再通过换热器调节温度为284℃后进入纺丝箱体中;工艺参数包括:熔体挤出温度290℃,缓冷区温度255℃,牵伸热辊速度3000m/min,牵伸热辊温度83℃,预网络器压力0.6bar,主网络器压力3.4bar,定型热辊速度4130m/min,定型热辊温度120℃,卷绕速度4050m/min,卷绕密度0.98g/cm
³
,卷绕直径360mm,卷绕角5,卷绕机压力辊与丝饼之间接触压力值260n。
33.最终制得的多异形丝的单丝纤度为1.43dtex,线密度偏差率为0.35%,断裂强度为4.16cn/dtex,断裂强度不匀率为2.9%,断裂伸长率为36.1%,断裂伸长率不匀率为4.8%,条干不匀率为0.89%,沸水收缩率为7.9%,上油率为1.15wt%,弹性回复率为82%,压缩弹性率为56%,异形度为30%。
34.实施例4一种多异形丝的生产设备,包括纺丝箱体;纺丝箱体采用气相热媒加热和保温,气相热媒由热媒蒸发器提供,热媒蒸发器内设有一个u型管热交换器,u型管热交换器采用液相热媒加热,液相热媒由热媒站供应;纺丝箱体内设有用于计量熔体的计量泵,计量泵的下方设有用于挤出熔体的纺丝组件,纺丝组件内设有环形结构的喷丝板,喷丝板内设有喷丝孔;喷丝板上喷丝孔的数量为144,喷丝孔的深度为20mm,喷丝孔包括微孔,位于微孔的上方、共轴且自上而下顺序连接的导流槽、导流孔和过渡孔;导流槽和导流孔构成的整体呈喇叭状,导流槽的上端即为喇叭的大端;喷丝板的一端面为熔体进料面,另一端面为喷丝面,导流槽的上端位于熔体进料面上,微孔的下端位于喷丝面上;
微孔的深度为0.27mm;微孔的下端记为d,d在喷丝面上呈同心圆分布,同心圆由n个圆构成,n为6,同心圆的圆心为喷丝面的中心;相邻两圆上的d错位排列,同一圆上分布m个d,同一圆上的m个d对应的微孔与同一个环形的导流槽连接;同心圆中最外部的圆对应的导流槽记为第一导流槽,第一导流槽的上端的内侧边缘与熔体进料面的外侧边缘之间的距离为6mm;同心圆中最内部的圆对应的导流槽记为第n导流槽,第n导流槽的上端的内侧边缘与熔体进料面的内侧边缘之间的距离为5mm;导流槽的槽深为1.5mm,环形的导流槽的上端记为u,u呈环形,该环形的内侧边缘为圆形a,外侧边缘为花瓣形,花瓣形由m个形状和尺寸相同的半圆相互连接而成,所有相邻的两个半圆的连接点连接形成一个与圆形a同心的圆形b,圆形a和圆形b的半径差为2.0mm;导流孔在熔体进料面上的正投影呈圆形,该圆形同时与所述半圆和所述圆形a相切;微孔的横截面主体呈错位丰字形;错位丰字形由丰字形错位形成;丰字形由三条左侧横条、一条中间竖条和三条右侧横条组成;中间竖条的上端融合标准三叶形,下端融合等腰三角形,中间竖条为两条短边位于上下侧、两条长边位于左右侧的长方形;上端融合标准三叶形即标准三叶形的一叶与长方形完全重合且该叶的中心轴与长方形的长对称轴重合,同时标准三叶形的中心点与长方形的上短边的中点重合,标准三叶形即三叶的叶长l3相等都为0.2mm、叶宽相等都为0.1mm、相邻两叶的中心轴线的夹角都为120
°
的三角形;下端融合三角形即等腰三角形的两腰分别经过长方形的两条长边,等腰三角形的顶点位于长方形的长对称轴上,同时等腰三角形的中心点与长方形的下短边的中点重合;等腰三角形的中心点与等腰三角形底边端点的距离l2为0.15mm;三条左侧横条等间距排列且间距为d,三条右侧横条等间距排列且间距为d;错位是指三条右侧横条下移d/2;三条左侧横条和三条右侧横条的尺寸相同,远离中间竖条的一端与中间竖条的竖直对称轴的距离l4为0.25mm,沿竖直方向的宽度w2为0.06mm;中间竖条沿竖直方向的长度l1为0.47mm,沿水平方向的宽度w1为0.15mm;每条左侧横条的左端都与一条位于其上方的弧形条连接成j形钩,每条右侧横条的右端都与一条位于其下方的弧形条连接成j形钩,各j形钩的钩尖与其主体部分的水平对称轴的距离h都相等,t=h/l4,t为0.2;喷丝板的下方设有缓冷区,缓冷区为设置在立方体内的圆柱形通孔,设有圆柱形通孔的立方体由对称的两部分用锁扣可拆卸连接而成,每部分都为中空结构,每部分的顶部设有气相热媒进气孔,底部设有气相热媒回流孔;缓冷区的下方设有环吹风冷却装置,环吹风冷却装置包括圆柱筒状的外环吹风滤芯、圆柱筒状的内环吹风滤芯、内环吹送风管和外环吹装置;内环吹风滤芯由圆柱筒状的多孔板、圆柱筒状的不锈钢烛芯风筒和环形密封垫组成,不锈钢烛芯风筒位于多孔板内且二者共轴,多孔板和不锈钢烛芯风筒的顶端和底端均通过环形密封垫相连;外环吹风滤芯的结构同内环吹风滤芯;内环吹风滤芯的外径与喷丝板的内径相同,为45mm,外环吹风滤芯的内径与喷丝板的外径相同,为105mm;内环吹风滤芯的内径为30mm,外环吹风滤芯的外径为120mm;
外环吹装置包括顺序连接的风机、送风管一、送风软管、送风管二和环吹风箱;送风管一和送风管二均为圆柱形中空腔;环吹风箱内设有多孔板一、整流板和多孔板二,环吹风箱上设有风速检测点,检测点上设有安装在环吹风箱上的快插接头;送风管一上设有风阀,风阀上设有调节风速的0~100%开度值,通过调节风阀的开度调整进入环吹风箱的风速;送风管二内设有过滤整流装置,过滤整流装置包括设于下层的钢丝网以及固定在钢丝网上的无纺布;多孔板一与多孔板二的表面均匀分布圆形风孔,开孔率为80%;多孔板一上风孔的直径为6mm,相邻两风孔的间距为4mm;多孔板二上风孔的直径为4mm,相邻两风孔的间距为3mm;多孔板一与多孔板二的上端和下端均与环吹风箱焊接连接;整流板为1.0mm厚度的不锈钢板;整流板的高度小于多孔板一与多孔板二,整流板的上端与环吹风箱焊接连接;外环吹风滤芯位于环吹风箱内,环吹风箱与送风管二的连接口记为接口c,多孔板一、整流板和多孔板二位于外环吹风滤芯以及接口c之间,整流板位于多孔板一与多孔板二之间;外环吹装置、外环吹风滤芯和内环吹风滤芯都位于喷丝板的下方且与其间隔一定的距离,外环吹装置与外环吹风滤芯的中空部分相对的区域为空心区域,内环吹风滤芯位于外环吹风滤芯内且二者共轴,内环吹风滤芯与喷丝板共轴;外环吹风滤芯与内环吹风滤芯的顶端齐平,与喷丝板的距离(即缓冷区高度)为30mm;外环吹风滤芯的底端向下延伸形成无孔筒i,内环吹风滤芯的底端向下延伸形成无孔筒ii;外环吹风滤芯和内环吹风滤芯的高度h1相等均为200mm,无孔筒i与无孔筒ii的高度h2相等均为50mm,h1与h2的比例为4:1;内环吹送风管穿过纺丝箱体1、纺丝组件和缓冷区穿入内环吹风滤芯内,用于为内环吹风滤芯提供风速为0.7m/s、温度为23℃、相对湿度为78%的冷却风;内环吹送风管位于纺丝箱体、纺丝组件和缓冷区内的长度段均采用海泡石保冷隔热材料制成;外环吹装置用于为外环吹风滤芯提供风速为0.6m/s、温度为23℃、相对湿度为83%的冷却风;环吹风冷却装置的下方设有上油装置,上油装置包括块体、上油管、压空管、底座、快插i、不锈钢杆、快插ii和压盖ii;块体由左右相对的喷嘴座和压盖i组成,压盖ii与压盖i背离喷嘴座的表面连接,压盖ii背离压盖i的表面为弧面,压盖i面向喷嘴座的表面的一边设为坡道结构;压盖ⅰ、压盖ⅱ与喷嘴座等长,压盖ⅰ或压盖ⅱ的宽度与喷嘴座的宽度之比为2:3;喷嘴座和压盖i都为立方体结构;喷嘴座背离压盖i的表面上设有上下两个圆柱形的凹槽,上凹槽的直径为6mm,下凹槽的直径为8mm;上凹槽的中心设有一直径为2mm的进油孔;上凹槽内设有一层80目过滤网片,用于过滤油剂中的杂质过滤;下凹槽的中心设有一直径为3mm的进气孔;下凹槽内进气孔的一侧设有一个长方形气流缓冲孔,压盖i上设有一个用于与气流缓冲孔连通且形状和尺寸同气流缓冲孔的通孔;底座为立方体结构,底座上设有直径为7mm的上螺纹孔、直径为9mm的下螺纹孔、o型圈ⅰ、o型圈ⅱ、直径为6mm的上通孔、直径为8mm的下通孔、进油凹槽和进气凹槽;不锈钢杆的一端插入底座的上螺纹孔内与其螺纹连接,同时与固定在底座的上螺纹孔内的o型圈ⅰ接
触,底座的上螺纹孔、上通孔和进油凹槽顺序连接,底座的进油凹槽与喷嘴座的上凹槽相对;快插ii插入底座的下螺纹孔内与其螺纹连接,同时与固定在底座的下螺纹孔内的o型圈ii接触,底座的下螺纹孔、下通孔和进气凹槽顺序连接,底座的进气凹槽与喷嘴座的下凹槽相对;块体内设有丝条通道,丝条通道为横截面呈圆形、自上端至中间尺寸递减且自中间至下端尺寸递增的通孔,由左右对称的凹槽i和凹槽ii组成;凹槽i设置在喷嘴座上且槽口位于喷嘴座面向压盖i的表面上,凹槽ii设置在压盖i上且槽口位于压盖i面向喷嘴座的表面上;凹槽i由上部分、中间部分、下部分组成,凹槽i的上部分与下部分为对称结构,长度都为20mm,最小直径都为5mm,最大直径都为8mm;上油管依次经过快插i、不锈钢杆和底座后,通过进油孔、一设置在喷嘴座内的出油孔与喷嘴座上的凹槽i的上部分连接;压空管用于提供8bar的气流,依次经过快插ii和底座后,通过进气孔、一设置在喷嘴座内的喷气孔与喷嘴座上的凹槽i的下部分连接;凹槽i上与上油管连接的点记为接点a,凹槽i上与压空管连接的点记为接点b,接点a与凹槽i的上端的距离为凹槽i的上部分长度的30%,接点b与凹槽i的下端的距离为凹槽i的下部分长度的40%;凹槽i的中间部分为圆柱状结构,直径同凹槽i的上部分的最小直径,长度为10mm;凹槽i的中间部分设有20个自上而下等间距排列且环绕丝条通道的中心轴设置的集油槽,n为,间距为0.5mm;集油槽的槽体部分,深度为2mm,宽度为3mm;集油槽的槽体外边沿中与丝条通道中的丝条接触的边为齿条状,相邻的集油槽的齿条错开分布;各集油槽中齿条的齿数为20个,齿槽宽w0为0.5mm,齿的高度h0为0.5mm;底座、喷嘴座、压盖i和压盖ii上均设有上下两个定位螺孔,底座、喷嘴座、压盖i和压盖ii通过与定位螺孔配合的定位螺钉固定为一体;不锈钢杆的外表面设有定位孔,上油装置通过不锈钢杆上的定位孔固定在纺丝上油架上;上油装置的下方设有甬道,甬道的底端设有分流孔,甬道的下方设有预网络器,预网络器的下方设有牵伸热辊,牵伸热辊的侧方设有定型热辊,定型热辊的下方设有主网络器,主网络器的下方设有卷绕机。
35.一种多异形丝的制备方法,采用上述的一种多异形丝的生产设备进行加工;具体工艺流程为:熔体输送
→
熔体计量
→
组件过滤
→
熔体挤出
→
缓冷区缓冷
→
冷却成形
→
集束上油
→
牵伸定型
→
卷绕成型;其中,工艺流程还包括熔体的制取、输送,熔体制取、输送过程为:采用对苯二甲酸和乙二醇作为原料,其中对苯二甲酸和乙二醇摩尔比为1:1.2,加入量为对苯二甲酸0.03wt%的乙二醇锑和对苯二甲酸加入量0.04wt%的磷酸三苯酯混合均匀后,在氮气氛围中通过控制反应温度和压力进行酯化反应,酯化反应时间为3小时,压力为0.3mpa,温度为264℃,酯化反应终点为酯化水馏出达到理论值的97%;经酯化后的对苯二甲酸乙二醇酯进入缩聚反应阶段,缩聚反应,为负压反应,共分为三步缩聚,缩聚一反应压力为97mbar,停留时间为0.7h,缩聚一的温度为264℃,缩聚二的温度为274℃,缩聚二的压力为23 mbar,停留时间约1.4h,终缩聚的温度为278℃,终缩聚的压力为14mbar,停留时间1.2h,制得聚合物熔体;
缩聚反应后的熔体经过装有过滤精度为15μm滤芯的过滤器过滤掉熔体中15~25μm的机械杂质粒子,由熔体管道输送至增压泵增压,增压后的压力为160bar,保证熔体输送至单纺位计量泵熔体入口压力为72bar;经增压后的熔体再通过换热器调节温度为284℃后进入纺丝箱体中;工艺参数包括:熔体挤出温度292℃,缓冷区温度260℃,牵伸热辊速度3100m/min,牵伸热辊温度81℃,预网络器压力0.6bar,主网络器压力3.3bar,定型热辊速度4100m/min,定型热辊温度118℃,卷绕速度4000m/min,卷绕密度0.98g/cm
³
,卷绕直径365mm,卷绕角5.4,卷绕机压力辊与丝饼之间接触压力值240n。
36.最终制得的多异形丝的单丝纤度为0.55dtex,线密度偏差率为0.38%,断裂强度为4.05cn/dtex,断裂强度不匀率为2.6%,断裂伸长率为35.8%,断裂伸长率不匀率为5.5%,条干不匀率为0.91%,沸水收缩率为7.9%,上油率为1.05wt%,弹性回复率为82%,压缩弹性率为55%,异形度为28%。
37.对比例1一种多异形丝的生产设备,基本同实施例1,不同之处仅在于,环吹风冷却装置为普通环吹风冷却装置,即tmt外环吹风装置(日本tmt公司ciq外环吹冷却装置),由送风机、送风管、滤芯组成,滤芯外径为100mm。
38.一种仿毛聚酯纤维的制备方法,采用上述的一种多异形丝的生产设备进行加工,工艺参数和工艺流程同实施例1。
39.最终制得的多异形丝的单丝纤度为3.6dtex,线密度偏差率为0.85%,断裂强度为4.31cn/dtex,断裂强度不匀率为3.1%,断裂伸长率为35.2%,断裂伸长率不匀率为5.1%,条干不匀率为0.86%,沸水收缩率为7.9%,上油率为1.10wt%,弹性回复率为81%,压缩弹性率为50%,异形度为27%。
40.对比例2一种多异形丝的生产设备,基本同实施例2,不同之处仅在于,环吹风冷却装置为普通环吹风冷却装置,即tmt外环吹风装置(日本tmt公司ciq外环吹冷却装置),由送风机、送风管、滤芯组成,滤芯外径为105mm。
41.一种仿毛聚酯纤维的制备方法,采用上述的一种多异形丝的生产设备进行加工,工艺参数和工艺流程同实施例2。
42.最终制得的多异形丝的单丝纤度为2.3dtex,线密度偏差率为0.75%,断裂强度为4.36cn/dtex,断裂强度不匀率为3.2%,断裂伸长率为34.5%,断裂伸长率不匀率为5.6%,条干不匀率为0.9%,沸水收缩率为7.8%,上油率为1.02wt%,弹性回复率为82%,压缩弹性率为51%,异形度为28%。
43.对比例3一种多异形丝的生产设备,基本同实施例3,不同之处仅在于,环吹风冷却装置为普通环吹风冷却装置,即tmt外环吹风装置(日本tmt公司ciq外环吹冷却装置),由送风机、送风管、滤芯组成,滤芯外径为120mm。
44.一种仿毛聚酯纤维的制备方法,采用上述的一种多异形丝的生产设备进行加工,工艺参数和工艺流程同实施例3。
45.最终制得的多异形丝的单丝纤度为1.43dtex,线密度偏差率为0.70%,断裂强度为
4.28cn/dtex,断裂强度不匀率为3.3%,断裂伸长率为33.5%,断裂伸长率不匀率为5.1%,条干不匀率为0.92%,沸水收缩率为7.7%,上油率为1.15wt%,弹性回复率为80%,压缩弹性率为53%,异形度为28%。
46.对比例4一种多异形丝的生产设备,基本同实施例4,不同之处仅在于,环吹风冷却装置为普通环吹风冷却装置,即tmt外环吹风装置(日本tmt公司ciq外环吹冷却装置),由送风机、送风管、滤芯组成,滤芯外径为120mm。
47.一种仿毛聚酯纤维的制备方法,采用上述的一种多异形丝的生产设备进行加工,工艺参数和工艺流程同实施例4。
48.最终制得的多异形丝的单丝纤度为0.55dtex,线密度偏差率为0.51%,断裂强度为3.81cn/dtex,断裂强度不匀率为3.3%,断裂伸长率为36%,断裂伸长率不匀率为5.6%,条干不匀率为0.93%,沸水收缩率为7.6%,上油率为1.08wt%,弹性回复率为81%,压缩弹性率为53%,异形度为26%。
49.实施例5一种多异形丝的生产设备,基本同实施例1,不同之处仅在于,环形的导流槽上端的外侧边缘不是呈花瓣形,而是呈圆形,大小同圆形b。
50.一种多异形丝的制备方法,采用上述的一种多异形丝的生产设备进行加工,工艺流程和工艺参数同实施例1。
51.最终制得的多异形丝的单丝纤度为1.8dtex,线密度偏差率为0.9%,断裂强度为3.95cn/dtex,断裂强度不匀率为3.5%,断裂伸长率为34.5%,断裂伸长率不匀率为5.8%,条干不匀率为0.85%,沸水收缩率为7.9%,上油率为1.10wt%,弹性回复率为82%,压缩弹性率为55%,异形度为29%。
52.实施例6一种多异形丝的生产设备,基本同实施例5,不同之处仅在于,微孔的横截面形状为三角形;如图20所示,三角形的叶长l5为0.25mm,外接圆半径r1为0.24mm,内切圆半径r2为0.089mm,叶端圆弧半径r3为0.04mm。
53.一种多异形丝的制备方法,采用上述的一种多异形丝的生产设备进行加工,工艺流程和工艺参数同实施例5。
54.最终制得的多异形丝的单丝纤度为2.5dtex,线密度偏差率为0.76%,断裂强度为4.36cn/dtex,断裂强度不匀率为2.8%,断裂伸长率为33.6%,断裂伸长率不匀率为4.2%,条干不匀率为0.78%,沸水收缩率为8.08%,上油率为1.08wt%,弹性回复率为81%,压缩弹性率为52%,异形度为32%。
55.实施例7一种多异形丝的生产设备,基本同实施例5,不同之处仅在于,微孔的横截面形状为三叶形;如图21所示,三叶形的三叶互成夹角a1为120
°
,叶长l6为0.5mm,叶宽w3为0.12mm。
56.一种多异形丝的制备方法,采用上述的一种多异形丝的生产设备进行加工,工艺流程和工艺参数同实施例5。
57.最终制得的多异形丝的单丝纤度为1.5dtex,线密度偏差率为0.72%,断裂强度为
4.06cn/dtex,断裂强度不匀率为3.1%,断裂伸长率为33.5%,断裂伸长率不匀率为5.1%,条干不匀率为0.88%,沸水收缩率为8.1%,上油率为1.12wt%,弹性回复率为81%,压缩弹性率为52%,异形度为33%。
58.实施例8一种多异形丝的生产设备,基本同实施例5,不同之处仅在于,微孔的横截面形状为十字形;如图22所示,十字形叶长l7为0.5mm,叶宽w4为0.08mm。
59.一种多异形丝的制备方法,采用上述的一种多异形丝的生产设备进行加工,工艺流程和工艺参数同实施例5。
60.最终制得的多异形丝的单丝纤度为2.0dtex,线密度偏差率为0.85%,断裂强度为4.21cn/dtex,断裂强度不匀率为3.0%,断裂伸长率为34.8%,断裂伸长率不匀率为5.6%,条干不匀率为0.83%,沸水收缩率为7.8%,上油率为1.06wt%,弹性回复率为82%,压缩弹性率为54%,异形度为28%。
61.实施例9一种多异形丝的生产设备,基本同实施例5,不同之处仅在于,微孔的横截面形状为w形;如图23所示,w形的曲度角a2为30
°
,四个边长l8为0.5mm,狭缝宽带w5为0.12mm。
62.一种多异形丝的制备方法,采用上述的一种多异形丝的生产设备进行加工,工艺流程和工艺参数同实施例5。
63.最终制得的多异形丝的单丝纤度为2.3dtex,线密度偏差率为0.89%,断裂强度为4.3cn/dtex,断裂强度不匀率为3.2%,断裂伸长率为35.2%,断裂伸长率不匀率为4.8%,条干不匀率为0.80%,沸水收缩率为8.1%,上油率为1.05wt%,弹性回复率为81%,压缩弹性率为51%,异形度为28%。
64.实施例10一种多异形丝的生产设备,基本同实施例5,不同之处仅在于,微孔的横截面形状为多c形;如图24所示,多c形为三个c组成圆环状,圆环之间的夹角a3为120
°
,圆环间距的缺口e为0.5mm,外圆直径r4为0.8mm,内圆直径r5为0.6mm。
65.一种多异形丝的制备方法,采用上述的一种多异形丝的生产设备进行加工,工艺流程和工艺参数同实施例5。
66.最终制得的多异形丝的单丝纤度为2.3dtex,线密度偏差率为0.78%,断裂强度为4.2cn/dtex,断裂强度不匀率为3.1%,断裂伸长率为35.5%,断裂伸长率不匀率为4.6%,条干不匀率为0.85%,沸水收缩率为7.7%,上油率为1.02wt%,弹性回复率为82%,压缩弹性率为51%,异形度为29%。
67.实施例11一种多异形丝的生产设备,基本同实施例5,不同之处仅在于,微孔的横截面形状为多h形;如图25所示,多h形为三个h连接而成,叶宽w6为0.06mm,横叶长l9为0.42mm,竖叶长l10为 0.18mm。
68.一种多异形丝的制备方法,采用上述的一种多异形丝的生产设备进行加工,工艺流程和工艺参数同实施例5。
69.最终制得的多异形丝的单丝纤度为1.1dtex,线密度偏差率为0.79%,断裂强度为4.05cn/dtex,断裂强度不匀率为2.8%,断裂伸长率为35.5%,断裂伸长率不匀率为4.5%,条
干不匀率为0.86%,沸水收缩率为7.9%,上油率为1.10wt%,弹性回复率为83%,压缩弹性率为52%,异形度为30%。
70.实施例12一种多异形丝的生产设备,基本同实施例5,不同之处仅在于,微孔的横截面形状为多叶形;如图26所示,多叶形为五叶形,叶与叶之间的夹角a4为72
°
,叶宽w7为0.08mm,叶长l11为0.4mm。
71.一种多异形丝的制备方法,采用上述的一种多异形丝的生产设备进行加工,工艺流程和工艺参数同实施例5。
72.最终制得的多异形丝的单丝纤度为1.7dtex,线密度偏差率为0.72%,断裂强度为4.2cn/dtex,断裂强度不匀率为3.0%,断裂伸长率为34.5%,断裂伸长率不匀率为4.3%,条干不匀率为0.90%,沸水收缩率为8.0%,上油率为1.08wt%,弹性回复率为82%,压缩弹性率为52%,异形度为29%。
73.实施例13一种多异形丝的生产设备,基本同实施例1,不同之处仅在于,上油装置为普通上油装置,由上油管、不锈钢杆和上油嘴组成;上油嘴为日本京瓷油嘴,仅设有一出油孔和储油槽,无压空装置,且不可分解清洗;上油管连接不锈钢杆,不锈钢杆另一端与上油嘴相连,油嘴与不锈钢杆之间通过胶水粘合,上油嘴上设有一出油孔,出油孔为2mm
×
0.8mm矩形孔,出油孔下面设有2个储油槽。
74.一种多异形丝的制备方法,采用上述的一种多异形丝的生产设备进行加工,工艺参数和工艺流程同实施例1。
75.最终制得的多异形丝的单丝纤度为3.6dtex,线密度偏差率为0.90%,断裂强度为4.50cn/dtex,断裂强度不匀率为3.20%,断裂伸长率为35.5%,断裂伸长率不匀率为5.2%,条干不匀率为0.85%,沸水收缩率为7.9%,上油率为0.98wt%,弹性回复率为80%,压缩弹性率为56%,异形度为28%。
76.实施例14一种多异形丝的生产设备,基本同实施例2,不同之处仅在于,上油装置为普通上油装置,由上油管、不锈钢杆和上油嘴组成;上油嘴为日本京瓷油嘴,仅设有一出油孔和储油槽,无压空装置,且不可分解清洗;上油管连接不锈钢杆,不锈钢杆另一端与上油嘴相连,油嘴与不锈钢杆之间通过胶水粘合,上油嘴上设有一出油孔,出油孔为2mm
×
0.8mm矩形孔,出油孔下面设有2个储油槽。
77.一种多异形丝的制备方法,采用上述的一种多异形丝的生产设备进行加工,工艺参数和工艺流程同实施例2。
78.最终制得的多异形丝的单丝纤度为2.3dtex,线密度偏差率为0.81%,断裂强度为4.32cn/dtex,断裂强度不匀率为3.4%,断裂伸长率为34.2%,断裂伸长率不匀率为5.9%,条干不匀率为0.86%,沸水收缩率为8.2%,上油率为0.99wt%,弹性回复率为84%,压缩弹性率为56%,异形度为31%。
79.实施例15一种多异形丝的生产设备,基本同实施例3,不同之处仅在于,上油装置为普通上油装置,由上油管、不锈钢杆和上油嘴组成;上油嘴为日本京瓷油嘴,仅设有一出油孔和储
油槽,无压空装置,且不可分解清洗;上油管连接不锈钢杆,不锈钢杆另一端与上油嘴相连,油嘴与不锈钢杆之间通过胶水粘合,上油嘴上设有一出油孔,出油孔为2mm
×
0.8mm矩形孔,出油孔下面设有2个储油槽。
80.一种多异形丝的制备方法,采用上述的一种多异形丝的生产设备进行加工,工艺参数和工艺流程同实施例3。
81.最终制得的多异形丝的单丝纤度为1.43dtex,线密度偏差率为0.75%,断裂强度为4.31cn/dtex,断裂强度不匀率为3.2%,断裂伸长率为34.5%,断裂伸长率不匀率为5.5%,条干不匀率为0.91%,沸水收缩率为8.2%,上油率为0.98wt%,弹性回复率为80%,压缩弹性率为52%,异形度为26%。
82.实施例16一种多异形丝的生产设备,基本同实施例4,不同之处仅在于,上油装置为普通上油装置,由上油管、不锈钢杆和上油嘴组成;上油嘴为日本京瓷油嘴,仅设有一出油孔和储油槽,无压空装置,且不可分解清洗;上油管连接不锈钢杆,不锈钢杆另一端与上油嘴相连,油嘴与不锈钢杆之间通过胶水粘合,上油嘴上设有一出油孔,出油孔为2mm
×
0.8mm矩形孔,出油孔下面设有2个储油槽。
83.一种多异形丝的制备方法,采用上述的一种多异形丝的生产设备进行加工,工艺参数和工艺流程同实施例4。
84.最终制得的多异形丝的单丝纤度为0.55dtex,线密度偏差率为0.75%,断裂强度为3.86cn/dtex,断裂强度不匀率为3.1%,断裂伸长率为35.2%,断裂伸长率不匀率为6.1%,条干不匀率为0.92%,沸水收缩率为8.1%,上油率为0.95wt%,弹性回复率为80%,压缩弹性率为50%,异形度为25%。
再多了解一些
本文用于创业者技术爱好者查询,仅供学习研究,如用于商业用途,请联系技术所有人。