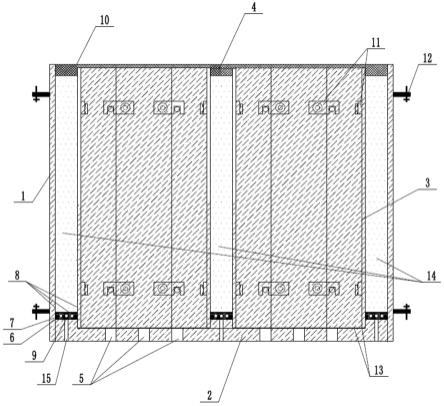
1.本发明属于陶瓷成型的技术领域,具体涉及凝胶注模成型模具及制备氧化铝双孔导轨生坯的工艺。
背景技术:
2.氧化铝、碳化硅等陶瓷材料具有高强度、高刚度等优点,成为三坐标、激光加工、光刻机等超精密测量、超精密加工及超精密装备制造的关键结构部件。陶瓷导轨主要用于承载运动工件台,为其快速、稳定移动提供支撑,导轨的分辨率与运动精度直接影响设备的精度。目前,国内精密加工、精密测量用大行程氧化铝陶瓷导轨等关键部件依赖于进口,国内大行程、复杂尺寸陶瓷部件生产制造实力较弱,这一高端装备用关键材料制造难题亟待攻克。
3.先进陶瓷材料的制备工艺包括成型、干燥(湿法成型)、预烧、高温烧结和冷加工等,成型体的质量不仅直接决定后期的干燥、预烧和烧结,还与原料利用率、工艺效率和冷加工成本等密切关联。大尺寸和复杂形状陶瓷的制备中要求成型体密度高、强度高和微结构均匀,从而有效防止变形、开裂等缺陷的产生。大尺寸陶瓷部件的成型方法包括冷等静压、压滤和注浆成型等。cn115070909a公开了一种陶瓷导轨横梁等静压模具及压制成型工艺,成功利用等静压工艺制备出一种大型双孔的陶瓷导轨横梁,具备密度大、强度高等优点,然而大型冷等静压设备昂贵,浪费原料,操作和维护成本高,且不适合制备复杂形状。压滤成型只能用于制备结构和形状简单的平板状样品;注浆成型适于制备薄壁样品,且素坯强度较低、无法满足素坯加工的要求。
4.注凝成型技术,成本低,操作简单,适合成型大尺寸陶瓷部件。现有注凝体系需要添加五种或三种或两种有机添加剂,工艺操作复杂,需要添加大量有机物,且单体有毒,所制备的素坯在脱水干燥和脱粘过程中易产生应力集中而导致变形,甚至开裂,不利于大行程氧化铝陶瓷导轨的制备。
5.cn114643632a公开了一种陶瓷坯体的成型方法,将陶瓷粉体、聚丙烯酸铵、异丁烯与马来酸酐共聚物分散于水中,混合得到固含量为50~56vol%的水基陶瓷浆料;将所得水基陶瓷浆料注入可滤水的平板模具中,在恒温恒湿环境下自发凝固成型,通过控制平板膜温度和湿度,浆料固化后再经脱模和干燥,成功得到φ230
×
25mm陶瓷坯体。该方法对平板类陶瓷坯体较为适合,对于复杂化、轻量化、大尺寸要求的双孔陶瓷导轨难以适用,容易出现开裂、尺寸不稳定等缺陷。
技术实现要素:
6.本发明要解决的技术问题是提供一种凝胶注模成型模具及制备氧化铝双孔导轨生坯的工艺,解决双孔氧化铝陶瓷导轨注凝成型过程中出现的弯曲、变形、开裂的问题,该工艺能够快速脱水固化,进而缩短生产周期。
7.本发明所述的凝胶注模成型模具,包括外模、底板、内模,外模内侧与内模外侧设
置有过滤膜,底板上设置有排水通道和平板膜,平板膜上设置有过滤膜,过滤膜上涂有润滑层,外模与底板接触位置设置有密封层,外模、底板、内模之间为填充区域,外模上设置有固定夹。底板上的排水通道是直径为8mm的贯穿孔,并且设置有多个。
8.外模、底板、内模均为304不锈钢钢板,内模由多块不锈钢钢板通过内模固定夹固定而成。底板与平板膜连接处的底板的部分设置有贯穿孔。贯穿孔设有三个,直径为4mm,起到排水的作用。
9.过滤膜通过8-11mm双面胶固定在外模内侧与内模外侧,过滤膜的孔径为0.5-1μm。过滤膜向外延伸至不锈钢底板侧面底部,向内延伸至内模底部。过滤膜为聚四氟乙烯材质。
10.平板膜为陶瓷平板膜,平板膜上设置有排水孔,平板膜覆盖在底板上,用以承重和排水。
11.润滑层的厚度为0.1-0.5mm。润滑层为白凡士林层,涂抹在过滤膜表面。
12.密封层为轻质粘土层,起到密封作用。
13.外模和内模上设置有固定梁,固定梁为高分子工字钢固定梁,固定梁上设置有密封膜。
14.所述的利用凝胶注模成型模具制备氧化铝双孔导轨生坯的工艺,包括以下步骤:(1)注模:将凝胶注模成型模具整体放置在振动台上固定,注入氧化铝陶瓷浆料,振动和注模同时进行,振动台振动频率为30-45hz,注模完成后继续振动3-5min,密封膜密封;(2)脱水固化、脱模:将凝胶注模成型模具转移至真空干燥箱,在常压、25-30℃条件下脱水固化30-40h,脱掉内模,继续固化24-36h,脱掉外模,坯体继续固化20-24h;(3)干燥:将固化后的坯体平放,先采用真空度≤-0.8mpa的真空干燥,再进行常压干燥,得到氧化铝双孔导轨生坯。
15.氧化铝陶瓷浆料固含量为56vol%,氧化铝双孔导轨生坯的标准规格为长、宽、高分别是300mm、180mm、200mm。
16.步骤(3)中,将固化后的坯体平放在铺有氧化铝滚珠的平板上面干燥,氧化铝滚珠粒径为0.5-1mm,平板放置在氧化铝耐火砖上。
17.步骤(3)中,真空干燥和常压干燥均采用点式升温、保温方式进行干燥,在25℃≤温度≤50℃下进行真空保温干燥,在50℃<温度≤100℃下进行常压保温干燥。优选的,点式升温、保温程序如表1所示:表1 保温程序
本发明采用过滤膜延伸排水技术,浆料中水分通过侧壁过滤膜排出,确保了固化收缩过程中上下水分排出速率的均匀一致性,使得坯体可以在自然环境下固化成型,减小了坯体的变形及上下因水分排出速率不同导致的收缩差,所获坯体尺寸可控。本发明的凝胶注模成型模具内、外模采用过滤膜依附,不需要任何脱模剂,便于脱模,所得坯体表面光滑,外观良好。坯体底部过滤膜表面涂抹0.1-0.5mm润滑剂,减小了坯体的摩擦系数,使得坯体在固化产生强度的过程中,避免因坯体收缩导致的底部开裂,增加了因需要一定坯体强度导致坯体收缩的容错空间。采用本发明的凝胶注模成型模具结合制备氧化铝双孔导轨生坯的工艺,所制备的氧化铝双孔导轨生坯,经过烧制成型以后,得到的氧化铝双孔导轨的硬度、密度等指标均符合应用要求,同时其机械性能好,如抗折强度高、硬度高等。
18.与现有技术相比,本发明具有的有益效果是:(1)采用本发明的利用凝胶注模成型模具制备氧化铝双孔导轨生坯的工艺,能够成功获得高度达到200mm的氧化铝双孔导轨坯体。
19.(2)本发明的采用凝胶注模成型模具制备氧化铝双孔导轨生坯的工艺,为近净尺寸成型,成本低、操作简单,适合大尺寸、轻量化设计的陶瓷部件。
20.(3)采用本发明的凝胶注模成型模具,在注模过程施加振动,既能保证浆料注模完成后的均匀性,又能除去注模过程中引入的气泡,从而获得完整的坯体。
21.(4)本发明的产品坯体在干燥时,平放到铺有滚珠的硅元膜平板上进行真空干燥,既减小了坯体的摩擦系数,又减轻了坯体的重力,大大降低了坯体干燥收缩过程中开裂的可能性,滚珠中间的间隙又有利于水分的排出。
附图说明
22.图1为本发明的凝胶注模成型模具的剖面结构示意图。
23.图2为本发明的氧化铝双孔导轨生坯放置在带有滚珠的干燥用平板的结构示意图。
24.图中:1、外模;2、底板;3、内模;4、固定梁;5、排水通道;6、平板膜;7、排水孔;8、过滤膜;9、润滑层;10、密封膜;11、内模固定夹;12、固定夹;13、密封层;14、填充区域;15、贯穿孔;16、平板;17、氧化铝滚珠;18、氧化铝耐火砖;19、氧化铝双孔导轨生坯。
具体实施方式
25.下面结合具体实施例对本发明作进一步说明。
26.实施例1如图1所示,所述的凝胶注模成型模具,包括外模1、底板2、内模3,外模1内侧与内模3外侧设置有过滤膜8,底板2上设置有排水通道5和平板膜6,平板膜6上设置有过滤膜8,过滤膜8上涂有润滑层9,外模1与底板2接触位置设置有密封层13,外模1、底板2、内模3之间为填充区域14,外模1上设置有固定夹12。底板2上的排水通道5的直径为4mm的贯穿孔15,并且设置有多个。外模1、底板2、内模3均为304不锈钢钢板,内模3由多块不锈钢钢板通过内模固定夹11固定而成。
27.过滤膜8通过11mm双面胶固定在外模1内侧与内模3外侧,过滤膜8的孔径为0.8μm。过滤膜8向外延伸至不锈钢底板侧面底部,向内延伸至内模底部。过滤膜8为聚四氟乙烯材质。
28.平板膜6为平板,平板膜6上设置有排水孔7,平板膜6覆盖在底板2上,用以承重和排水。
29.润滑层9的厚度为0.3mm。润滑层9为白凡士林层,涂抹在过滤膜8表面。
30.密封层13为轻质粘土层,起到密封作用。
31.外模1和内模3上设置有固定梁4,固定梁4为工字钢固定梁4,固定梁4上设置有密封膜10。
32.所述的利用凝胶注模成型模具制备氧化铝双孔导轨生坯的工艺,包括以下步骤:(1)注模:将凝胶注模成型模具整体放置在振动台上,用铁丝固定,注入固含量为56vol%的氧化铝陶瓷浆料,振动和注模同时进行,振动台振动频率为30hz,注模完成后继续振动5min,密封膜10密封;(2)脱水固化、脱模:将凝胶注模成型模具转移至真空干燥箱,在常压、25℃条件下脱水固化40h,脱掉内模,继续固化36h,脱掉外模,坯体继续固化24h;(3)干燥:将固化后的坯体平放,先采用真空度≤-0.8mpa的真空干燥,25℃下真空保温43h,27.5℃真空保温72h,30℃真空保温60h,35℃真空保温48h,40℃真空保温24h,50℃真空保温16h,再进行常压干燥,60℃常压保温10h,80℃常压保温5h,100℃常压保温2h,得到氧化铝双孔导轨生坯19。
33.如图2所示,步骤(3)中,将固化后的坯体平放在铺有氧化铝滚珠17的平板16上面,氧化铝滚珠17粒径为1mm,平板16放置在氧化铝耐火砖18上。
34.实施例2采用实施例1的凝胶注模成型模具。
35.所述的利用凝胶注模成型模具制备氧化铝双孔导轨生坯的工艺,包括以下步骤:(1)注模:将凝胶注模成型模具整体放置在振动台上,用铁丝固定,注入固含量为56vol%的氧化铝陶瓷浆料,振动和注模同时进行,振动台振动频率为38hz,注模完成后继续振动4min,密封膜10密封;(2)脱水固化、脱模:将凝胶注模成型模具转移至真空干燥箱,在常压、27.5℃条件下脱水固化36h后,脱掉内模,继续固化30h后,脱掉外模,坯体继续固化20h;(3)干燥:将固化后的坯体平放,先采用真空度≤-0.8mpa的真空干燥,27.5℃下真
空保温45h,30℃下真空保温72h,35℃真空保温48h,40℃真空保温24h,50℃真空保温16h,再进行常压干燥,60℃常压保温10h,80℃常压保温5h,100℃常压保温2h,得到氧化铝双孔导轨生坯19。
36.如图2所示,步骤(3)中,将固化后的坯体平放在铺有氧化铝滚珠17的平板16上面,氧化铝滚珠17粒径为0.8mm,平板16放置在氧化铝耐火砖18上。
37.实施例3采用实施例1的凝胶注模成型模具。
38.所述的利用凝胶注模成型模具制备氧化铝双孔导轨生坯的工艺,包括以下步骤:(1)注模:将凝胶注模成型模具整体放置在振动台上,用铁丝固定,注入固含量为56vol%的氧化铝陶瓷浆料,振动和注模同时进行,振动台振动频率为45hz,注模完成后继续振动3min,密封膜10密封;(2)脱水固化、脱模:将凝胶注模成型模具转移至真空干燥箱,在常压、30℃条件下脱水固化30h后,脱掉内模,继续固化24h后,脱掉外模,继续固化24h;(3)干燥:将固化后的坯体平放,先采用真空度≤-0.8mpa的真空干燥,30℃下真空保温45h,35℃真空保温72h,40℃真空保温48h,50℃真空保温24h,再进行常压干燥,60℃常压保温10h,80℃常压保温5h,100℃常压保温2h,得到氧化铝双孔导轨生坯19。
39.如图2所示,步骤(3)中,将固化后的坯体平放在铺有氧化铝滚珠17的平板16上面,氧化铝滚珠17粒径为1mm,平板16放置在氧化铝耐火砖18上。
40.将以上实施例制备的氧化铝双孔导轨生坯,根据固化干燥时间收缩尺寸检测标准,分别对其进行性能检测,检测结果如表1所示。
41.表1 检测结果
项目干燥时间/h上部长度/mm下部长度/mm长度差/mm上部宽度/mm下部宽度/mm宽度差/mm实施例1280293.7294.40.7173.7175.61.9实施例2222293.3294.71.4173.4175.82.4实施例3206293.1294.81.7173.2176.02.8
再多了解一些
本文用于创业者技术爱好者查询,仅供学习研究,如用于商业用途,请联系技术所有人。