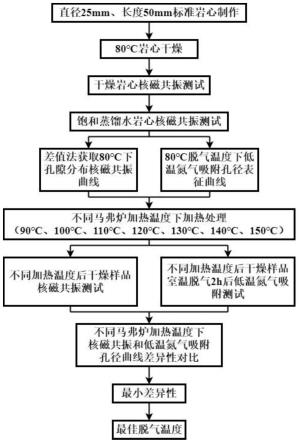
1.本发明涉及石油与天然气预处理领域,更具体的说是涉及一种低成熟度烃源岩最佳脱气温度确定方法。
背景技术:
2.低成熟度烃源岩具有水分含量高和挥发份含量高的典型特点,且低成熟度烃源岩微观孔隙结构非均质性强,准确获取低成熟度烃源岩的微观孔隙结构特征,对于判断低成熟度烃源岩储层质量至关重要。低温氮气吸附以及二氧化碳吸附是确定微观孔隙结构特征的最为常用手段,在进行相关实验测试时,对样品进行合适脱气温度下的脱气处理对于最终准确获取微观孔隙结构特征最为重要。石油天然气行业标准《sy/t 6154-1995》建议脱气温度100℃-300℃,国家标准《gb/t 19587-2017》中也未说明具体脱气温度,美国石油学会推荐的最佳脱气温度为110℃,但样品脱气时间长,且110℃无法完全脱出煤中的吸附水。已有学者研究表明,不同脱气温度下低成熟度烃源岩孔隙结构将发生不同变化,这与不同脱气温度下低成熟度烃源岩中挥发性物质的析出以及水分的挥发导致的孔隙结构动态变化密切相关。利用脱气温度对低成熟度烃源岩进行脱气处理的主要目的是为了去除低成熟度烃源岩中的自由水和吸附水,而不改变低成熟度烃源岩中挥发份物质的分布状态和含量。已有研究表明,低成熟度烃源岩脱气温度应控制在150℃以下,且不同脱气温度下样品脱气处理均采用小粒径煤样展开。小粒径煤样在制作过程中,由于人为破坏,势必增加了煤样的比表面积,其在脱气处理过程中会加大挥发分的析出,进而导致微观孔隙结构测试失真。因此,采用一定的技术方法去除低成熟度烃源岩中的水分且同时保留其中的挥发分,并尽可能的减少由于样品颗粒粒径导致的挥发分析出对于准确表征低成熟度烃源微观孔隙结构特征就显得极为重要。
技术实现要素:
3.有鉴于此,本发明提供了一种低成熟度烃源岩最佳脱气温度确定方法。
4.为了实现上述目的,本发明采用如下技术方案:
5.一种低成熟度烃源岩最佳脱气温度确定方法,包括以下步骤:
6.s1:分别制作直径25mm、长度50mm的标准岩心若干块;
7.s2:将获取的标准岩心置于80℃的烘箱中烘干48h,并对烘干后低成熟度烃源岩进行干燥条件下的核磁共振t2谱测试,获取核磁共振第一t2谱曲线;
8.s3:将干燥后岩心采用抽真空饱和装置使用蒸馏水进行饱和,并对饱和后岩心再次进行核磁共振t2谱测试,获取饱和蒸馏水后岩心核磁共振第二t2谱曲线;
9.s4:将第一t2谱曲线和第二t2谱曲线,采用差值法,获取低成熟度烃源岩初始孔隙分布的核磁共振第三t2谱曲线;
10.s5:将s3中的饱和蒸馏水岩心置于80℃的烘箱中烘干48h,采用实验室标准筛分法制作60-80目的颗粒煤样,将制作好的颗粒煤样置于低温氮气吸附实验脱气站中开展室温
条件下的脱气处理,脱气处理时间2h,随后对脱气处理后样品开展低温氮气吸附测试,获取低温氮气吸附/脱附测试曲线以及孔径表征曲线;
11.s6:取出一块80℃的烘箱中烘干48h后的标准岩心,置于马弗炉中,设置马弗炉加热温度为90℃,在马弗炉中加热48h,并对加热后标准岩心开展加热后饱和蒸馏水后核磁共振t2谱测试,获取核磁共振第四t2谱曲线,并将第四t2谱曲线与第一t2谱曲线进行差值计算获取90℃下低成熟度烃源岩孔隙分布的核磁共振第五t2谱曲线,将第五t2谱曲线和第三t2谱曲线进行差值计算;
12.s7:对s6获取的马弗炉加热温度为90℃下的饱和蒸馏水岩心,采用s5相同的样品处理方法,获取马弗炉加热温度为90℃下的低温氮气吸附/脱附测试曲线以及孔径表征曲线;
13.s8:将s2获取的干燥岩心置于马弗炉中,分别采用不同的加热温度(100℃、110℃、120℃、130℃、140℃、140℃和150℃),在马弗炉中加热48h,并对加热后标准岩心开展加热后饱和蒸馏水后核磁共振t2谱测试,并将获取的不同加热温度下核磁共振曲线与第一t2谱曲线进行差值计算,并将差值后获取的核磁共振曲线和第三t2谱曲线进行差值计算,以差值法获取的最小差异性变化所对应的加热温度作为基于核磁共振技术评价下烃源岩最佳脱气温度;
14.s9:对s8获取的不同加热温度下标准岩心,采用s5相同的样品处理方法,获取不同马弗炉加热温度下的低温氮气吸附/脱附测试曲线以及孔径表征曲线;
15.s10:将不同加热温度下获取的低温氮气吸附/脱附曲线和孔径表征曲线与80℃下低温氮气吸附/脱附测试曲线以及孔径表征曲线进行差值法处理,以差值法获取的最小差异性变化所对应的加热温度作为低温氮气吸附技术评价下烃源岩最佳脱气温度;
16.s11:综合上述步骤,将基于核磁共振技术评价以及低温氮气吸附技术评价下均表现为最小差异性变化所对应的加热温度作为低成熟度烃源岩最佳脱气温度。
17.可选的,制作标准岩心若干块在同一块全直径岩心上获取。
18.可选的,s4中的差值计算公式如下:
19.t
2(80p)
=t
2(sat)-t
2(80d)
ꢀꢀ
(1)
20.式中,t
2(sat)
为马弗炉加热温度80℃核磁共振横向弛豫时间下饱和蒸馏水样品的振幅强度;t
2(80d)
为马弗炉加热温度80℃核磁共振横向弛豫时间下干燥样品的振幅强度;t
2(80p)
为马弗炉加热温度80℃核磁共振横向弛豫时间下样品孔隙分布的振幅强度。可选的,s8和s10中以差值法获取的最小差异性变化所对应的加热温度作为烃源岩最佳脱气温度,计算公式如下:
21.d
v(i)
=100*(p
v(i)-p
v(80)
)/p
v(80)
ꢀꢀ
(2)
22.式中,d
v(i)
为不同马弗炉加热温度下核磁共振孔隙表征参数差异性或不同马弗炉加热温度下低温氮气吸附孔隙表征参数差异性;p
v(i)
为不同马弗炉加热温度i下核磁共振孔隙表征参数差异性或不同马弗炉加热温度i下低温氮气吸附孔隙表征参数;p
v(80)
为马弗炉加热温度80℃下核磁共振孔隙表征参数差异性或马弗炉加热温度80℃下低温氮气吸附孔隙表征参数。
23.经由上述的技术方案可知,与现有技术相比,本发明公开提供了一种低成熟度烃源岩最佳脱气温度确定方法,具有以下有益效果:
24.1、本发明避免了直接采用颗粒煤样进行脱气温度处理时造成的表面积增加导致的孔隙结构参数测试失真现象,其获取的孔径表征参数相较于传统低温氮气吸附有明显提升;
25.2、本发明采用核磁共振技术和低温氮气吸附相结合的方法,二者结合明确孔隙参数变化的最小值,采用双因素方法明显优于传统的仅依靠低温氮气吸附的单因素判断方法。
附图说明
26.为了更清楚地说明本发明实施例或现有技术中的技术方案,下面将对实施例或现有技术描述中所需要使用的附图作简单地介绍,显而易见地,下面描述中的附图仅仅是本发明的实施例,对于本领域普通技术人员来讲,在不付出创造性劳动的前提下,还可以根据提供的附图获得其他的附图。
27.图1为本发明的流程示意图;
28.图2为本发明岩心选取及制作示意图;
29.图3为本发明差值法获取的t
2(80p)
核磁共振分布曲线;
30.图4为本发明的不同脱气加热温度下核磁共振表征曲线;
31.图5a-图5d为本发明的不同脱气加热温度下孔径表征曲线;
32.图6为本发明的基于核磁共振和低温氮气吸附的孔隙参数变化率散点图。
具体实施方式
33.下面将结合本发明实施例中的附图,对本发明实施例中的技术方案进行清楚、完整地描述,显然,所描述的实施例仅仅是本发明一部分实施例,而不是全部的实施例。基于本发明中的实施例,本领域普通技术人员在没有做出创造性劳动前提下所获得的所有其他实施例,都属于本发明保护的范围。
34.本发明实施例公开了一种低成熟度烃源岩最佳脱气温度确定方法,如图1-4,图5a-图5d以及图6所示,具体为:基于制作的标准小直径岩心,开展常规80℃下的干燥处理,并对干燥处理后岩心开展核磁共振测试,对干燥处理后岩心开展蒸馏水饱和下的核磁共振t2谱测试和饱和蒸馏水岩心再次干燥后的低温氮气吸附测试,基于此获取脱气处理前孔隙分布特征;对标准小直径岩心分别开展马弗炉不同加热温度(90℃、100℃、110℃、120℃、130℃、140℃、150℃)的48h干燥处理以及干燥处理后饱和蒸馏水的核磁共振t2谱测试,并对饱和蒸馏水岩心再次干燥处理后样品采用实验室标准筛分法进行制样,对不同加热温度下颗粒样品开展室温下真空脱气2h,随后对脱气后样品开展低温氮气吸附测试;针对获取的不同加热温度下样品的核磁共振t2谱测试曲线和低温氮气吸附测试曲线,采用差值法与80℃下相应曲线进行对比,以不同加热温度下,基于核磁共振技术评价以及低温氮气吸附技术评价下均表现为最小差异性变化所对应的加热温度作为低成熟度烃源岩最佳脱气温度。
35.步骤一:基于《gb/t 291722012岩心分析方法》分别制作直径25mm、长度50mm的标准岩心若干块,制作的小直径岩心尽可能在同一块全直径岩心上获取,以避免储层非均质性可能带来的实验误差。
36.步骤二:将获取的标准岩心置于80℃的烘箱中烘干48h,并对烘干后低成熟度烃源岩进行干燥条件下的核磁共振t2谱测试,获取核磁共振t2谱曲线(t
2(80d)
)。
37.步骤三:将干燥后岩心采用抽真空饱和装置使用蒸馏水进行饱和,并对饱和后岩心再次进行核磁共振t2谱测试,获取饱和蒸馏水后岩心核磁共振t2谱曲线(t
2(sat)
)。
38.步骤四:将步骤二和步骤三获取的两条核磁共振曲线,采用差值法,获取低成熟度烃源岩初始孔隙分布的核磁共振t2谱曲线(t
2(80p)
)。
39.t
2(80p)
=t
2(sat)-t
2(80d)
ꢀꢀ
(1)
40.式中,t
2(sat)
为马弗炉加热温度80℃核磁共振横向弛豫时间下饱和蒸馏水样品的振幅强度;t
2(80d)
为马弗炉加热温度80℃核磁共振横向弛豫时间下干燥样品的振幅强度;t
2(80p)
为马弗炉加热温度80℃核磁共振横向弛豫时间下样品孔隙分布的振幅强度。
41.步骤五:将步骤三中核磁共振测试后岩心再次采用步骤二方式进行烘干后,采用实验室标准筛分法制作60-80目粒径煤样,并在室温下开展脱气处理2h,随后开展低温氮气吸附测试,获取低成熟度烃源岩低温氮气吸附/脱附测试曲线以及孔径表征曲线。
42.步骤六:取出一块步骤二中干燥后的标准岩心,将其置于马弗炉中,设置马弗炉加热温度为90℃,在马弗炉中加热48h,并对加热后标准岩心开展加热后饱和蒸馏水的核磁共振t2谱测试(t
2(90m)
),并将t
2(90m)
与t
2(80d)
利用公式(1)进行差值计算,获取马弗炉90℃加热温度下低成熟度烃源岩孔隙分布的核磁共振t2谱曲线(t
2(90p)
)。
43.t
2(90p)
=t
2(90m)-t
2(80d)
ꢀꢀ
(2)
44.式中,t
2(90m)
为马弗炉加热温度90℃下核磁共振横向弛豫时间下饱和蒸馏水样品的振幅强度;t
2(80d)
为马弗炉加热温度80℃核磁共振横向弛豫时间下干燥样品的振幅强度;t
2(90p)
为马弗炉加热温度90℃核磁共振横向弛豫时间下样品孔隙分布的振幅强度。
45.步骤七:将马弗炉90℃加热温度下饱和蒸馏水后岩心进行80℃干燥温度处理48h,将处理后的标准岩心,采用实验室标准筛分法制作60-80目的颗粒煤样,将制作好的颗粒煤样置于低温氮气吸附实验脱气站中开展室温条件下的脱气处理,脱气处理时间2h,随后对脱气处理后样品开展低温氮气吸附测试,获取低温氮气吸附/脱附测试曲线以及孔径表征曲线。
46.步骤八:将步骤三获取的饱和蒸馏水岩心置于马弗炉中,分别开展100℃、110℃、120℃、130℃、140℃和150℃等不同的加热温度,在马弗炉中加热48h,并对加热后标准岩心开展加热后饱和蒸馏水核磁共振t2谱测试,并将获取的不同加热温度下核磁共振曲线(t
2(100m)
、t
2(110m)
、t
2(120m)
、t
2(130m)
、t
2(140m)
、t
2(150m)
)与t
2(80d)
进行差值计算,获取不同加热温度下低成熟度烃源岩孔隙分布的核磁共振t2谱曲线(t
2(100p)
、t
2(110p)
、t
2(120p)
、t
2(130p)
、t
2(140p)
、t
2(150p)
),在此基础之上将不同加热温度下低成熟度烃源岩孔隙分布的核磁共振t2谱曲线(t
2(100p)
、t
2(110p)
、t
2(120p)
、t
2(130p)
、t
2(140p)
、t
2(150p)
)与马弗炉加热温度80℃核磁共振横向弛豫时间下样品孔隙分布的振幅强度t
2(80p)
进行差值计算,以差值法获取的最小差异性变化所对应的加热温度作为基于核磁共振技术的该烃源岩最佳脱气温度。。
47.d
v(i)
=100*(p
v(i)-p
v(80)
)/p
v(80)
ꢀꢀ
(3)
48.式中,d
v(i)
为不同马弗炉加热温度下核磁共振孔隙表征参数差异性;p
v(80)
为马弗炉加热温度80℃下核磁共振孔隙表征参数;p
v(i)
为不同马弗炉加热温度i下核磁共振孔隙表征参数,i=90℃,100℃,
…
,150℃。
49.步骤九:对步骤八获取的不同加热温度下饱和蒸馏水岩心,采用步骤二方式进行烘干后,采用步骤七相同的样品处理方法,获取不同马弗炉加热温度下的低温氮气吸附/脱附测试曲线以及孔径表征曲线。
50.步骤十:将不同加热温度下获取的低温氮气吸附/脱附曲线和孔径表征曲线与80℃下低温氮气吸附/脱附测试曲线以及孔径表征曲线,采用公式(3)进行差值法处理,以差值法获取的最小差异性变化所对应的加热温度作为基于低温氮气吸附技术的该烃源岩最佳脱气温度。
51.步骤十一:综合上述步骤,将基于核磁共振技术评价以及低温氮气吸附技术评价下均表现为最小差异性变化所对应的加热温度作为低成熟度烃源岩最佳脱气温度。
52.本说明书中各个实施例采用递进的方式描述,每个实施例重点说明的都是与其他实施例的不同之处,各个实施例之间相同相似部分互相参见即可。对于实施例公开的装置而言,由于其与实施例公开的方法相对应,所以描述的比较简单,相关之处参见方法部分说明即可。
53.对所公开的实施例的上述说明,使本领域专业技术人员能够实现或使用本发明。对这些实施例的多种修改对本领域的专业技术人员来说将是显而易见的,本文中所定义的一般原理可以在不脱离本发明的精神或范围的情况下,在其它实施例中实现。因此,本发明将不会被限制于本文所示的这些实施例,而是要符合与本文所公开的原理和新颖特点相一致的最宽的范围。
再多了解一些
本文用于创业者技术爱好者查询,仅供学习研究,如用于商业用途,请联系技术所有人。