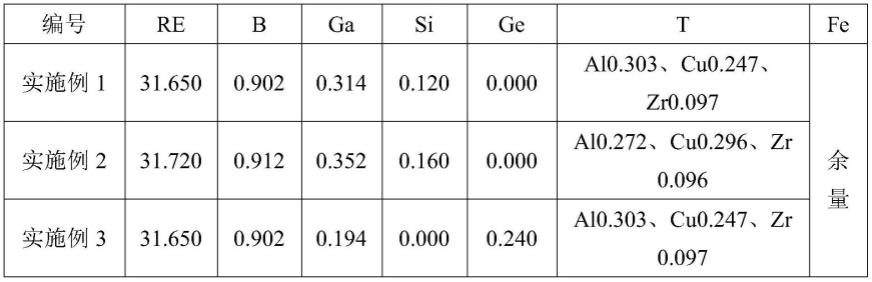
1.本发明属于磁性材料,具体涉及一种磁性材料及制备方法。
背景技术:
2.钕铁硼永磁材料由于其拥有高磁能积而广泛应用于新能源汽车、变频空调、工业电机等领域。这些领域中磁体的工作温度高,对磁体的耐高温性能要求高。改善磁体耐温性的途径主要有两种,一种是提高磁体的矫顽力,提高磁体的矫顽力主要通过添加重稀土tb或者dy,提高磁体磁晶各向异性场。由于dy和tb资源紧缺,成本高,该种方法会造成磁体成本的上升,另外一方面,由于tb和dy与fe的原子磁矩是反平行的,添加之后会造成剩磁下降,由此在制造高性能高矫顽力磁体方面就存在一定的局限性。另一种途径是提高磁体的电阻率。应用于永磁电机领域的钕铁硼磁体,处于交变的磁场环境中,容易由于涡流产生而发热,发热以后就会导致磁体矫顽力下降。而磁体由于涡流而导致的发热直接与磁体的电阻率有关,提高电阻率就有利于提高磁体的耐温能力。
3.通常在磁体中添加氧化物粉末,如氧化钙、氧化硅、氧化铝或者氟化物粉末来提高磁体的电阻率,但这些杂质粉末与钕铁硼磁粉混合之后,再进行烧结,存在因添加的粉末由于和钕铁硼磁粉末的兼容性差,粉末熔点较高,在烧结过程不易流动,造成磁体密度低,容易形成孔洞,磁体剩磁下降的问题。
技术实现要素:
4.本发明所要解决的第一个技术问题是提供一种矫顽力和电阻率均优异的磁性材料。
5.本发明解决第一个技术问题所采用的技术方案为:一种磁性材料,其特征在于:该磁性材料的质量百分比组成为re:29~32wt%,b:0.8~1.0wt%,ga:0.01~0.6wt%,a:0.1~0.5wt%,t:0.01~2.0wt%,其中,a选自si和ge中的至少一种,t选自al、cu、co、zr、ti中的至少一种,余量为fe和不可避免的杂质。
6.作为优选,所述a选自si和ge,并且,si、ga的质量比为1:(2~5)。
7.作为优选,该磁性材料的相组织包括2:14:1相以及分布在2:14:1相晶界处的晶界相,其中,晶界相包括富re相和r-t-ga相。2:14:1相为基体相,保证材料的剩磁性能,分布在晶界相中的富re相和r-t-ga相将2:14:1相晶粒相隔离,提高磁性材料的电阻率和矫顽力。其中,a元素分布在r-t-ga相中,r-t-ga相因还有半导体性的si或者ge具有较高的电阻率,同时r-t-ga相是非磁性相,分布在晶界上,从而增强去磁耦合作用,会提高矫顽力,同时,可以降低a元素进入2:14:1相中取代部分fe,保证2:14:1相的剩磁性能。
8.为实现剩磁和矫顽力的均衡,作为优选,所述晶界相在相组织中的面积含量为3~20%,所述r-t-ga相占晶界相面积含量的20~50%。r-t-ga相占晶界相面积含量的低于20%,将降低磁性材料的矫顽力,r-t-(ga)相占晶界相面积含量的高于50%,将降低磁性材料的剩磁。
9.本发明所要解决的第二个技术问题是提供一种磁性材料的制备方法。
10.本发明解决第二个技术问题所采用的技术方案为:一种磁性材料的制备方法,其特征在于:包括以下制备步骤:
11.1)配料:按照所需成分配料,包括合金m和合金n,其中,合金m的元素组成为re、b、ga、fe,合金n的元素组成为re、ga、t、a,其中,re选自pr和/或nd;将合金m和合金n混合形成混料;
12.2)粉末制备:将混料进行吸氢后再脱氢处理,将混料在保护气氛下进行制粉,保护气体中含有20~100ppm的氧气,余量为氮气;粉体的平均粒度为1.5~3μm;
13.3)压制成型:将粉体在磁场下取向,磁场强度为1.5~3.0t,然后在氮气保护气氛下压制成坯料;
14.4)烧结:烧结温度1000~1100℃,保温时间在6~10h,烧结真空度在2~5
×
10-3
pa;
15.5)回火:将温度降至850~950℃,保温时间1~3h后,温度再降至500~600℃,再保温2~6h。
16.合金m中不添加si或者ge,避免了在熔炼过程中这两种元素进入2:14:1相,降低磁性材料的剩磁性能。
17.合金n的元素组成为re、ga、t、a,re选自pr和/或nd,合金n的熔点在650~900℃之间,在该熔点范围内能够使合金n在晶界上分布连续,提升r-t-ga相的矫顽力。
18.为提升磁性材料的电阻率,从而提高矫顽力,保护气体中含有20~100ppm的氧气。粉体的平均粒度为1.5~3μm,与合金m中柱状晶平均晶粒尺寸相当,这样就保证粉末颗粒上都有富稀土相包裹,会提高矫顽力,同时降低晶粒长大的风险。
19.烧结温度1000~1100℃,过高的烧结温度使得2:14:1相晶粒在溶解析出再复合过程中长大,粉末粒度越小,晶粒会异常长大,从而导致磁体矫顽力降低。低的烧结温度会使得磁体的密度低,导致磁体性能变差。
20.为实现合金m、n晶粒细小,作为优选,所述步骤1)中,合金m、合金n为淬火态,合金m的熔炼温度为1450~1500℃,合金n的熔炼温度为1000~1400℃,均以≥1000℃/s的冷却速度凝固。
21.作为优选,所述步骤2)中,混料在低于500℃下进行脱氢处理。
22.与现有技术相比,本发明的优点在于:在磁性材料中添加a元素,a元素在提高材料电阻率的同时,在烧结过程易流动,提高磁性材料的密度,不容易形成孔洞,在实现高矫顽力的同时提高了材料的剩磁性,本发明合金的剩磁在13kgs以上,内禀矫顽力在21koe以上,电阻率在900(ω
·
mm2/m)以上。
附图说明
23.图1为本发明实施例2的背散射电子照片。
24.图2为本发明对比例2的电子显微镜照片。
具体实施方式
25.以下结合附图实施例对本发明作进一步详细描述。
26.本发明提供3个实施例和3个对比例,具体成分见表1。
27.实施例1的制备步骤为:
28.1)配料:按照所需成分配料,包括合金m和合金n,其中,以重量百分比计,合金m的组成为pr
7.5
nd
22.5
al
0.25
cu
0.1
ga
0.2
zr
0.1
fe
68.42b0.93
,合金n为pr
30
nd
55
al2cu5ga4si4;合金m、合金n为淬火态,合金m的熔炼温度为1450~1500℃,合金n的熔炼温度为1200-1300℃,合金m冷却速度为1000℃/s,合金n的冷却速度1100℃/s,将合金m和合金n混合形成混料;
29.2)粉末制备:将混料进行吸氢后再在450℃脱氢处理,将混料在保护气氛下进行制粉,保护气体中含有70ppm的氧气,余量为氮气;粉体的平均粒度为2.86μm;
30.3)压制成型:将粉体在磁场下取向,磁场强度为2.0t,然后在氮气保护气氛下压制成坯料;
31.4)烧结:烧结温度1060℃,保温时间在6h,烧结真空度在5
×
10-3
pa;
32.5)回火:将温度降至900℃,保温时间2h后,温度再降至540℃,再保温4h。
33.实施例2的制备步骤为:
34.1)配料:按照所需成分配料,包括合金m和合金n,其中,以重量百分比计,合金m的组成为pr
7.125
nd
21.375
dy1al
0.2
cu
0.1
ga
0.2
zr
0.1
fe
68.95b0.95
,合金n为pr
30
nd
55
al2cu5ga4si4;合金m、合金n为淬火态,合金m的熔炼温度为1450~1500℃,合金n的熔炼温度为1200-1300℃,合金m冷却速度为1500℃/s,合金n的冷却速度1100℃/s,将合金m和合金n混合形成混料;
35.2)粉末制备:将混料进行吸氢后再在480℃脱氢处理,将混料在保护气氛下进行制粉,保护气体中含有60ppm的氧气,余量为氮气;粉体的平均粒度为2.95μm;
36.3)压制成型:将粉体在磁场下取向,磁场强度为2.0t,然后在氮气保护气氛下压制成坯料;
37.4)烧结:烧结温度1050℃,保温时间在6h,烧结真空度在2
×
10-3
pa;
38.5)回火:将温度降至900℃,保温时间3h后,温度再降至580℃,再保温4h。
39.实施例3的制备步骤为:
40.1)配料:按照所需成分配料,包括合金m和合金n,其中,以重量百分比计,合金m的组成为pr5nd
25
al
0.25
cu
0.1
ga
0.2
zr
0.1
fe
68.42b0.93
,合金n为pr
30
nd
55
al2cu5ge8;合金m的熔炼温度为1450~1500℃,合金n的熔炼温度为1150-1250℃,合金m冷却速度为1200℃/s,合金n的冷却速度1000℃/s,将合金m和合金n混合形成混料;
41.2)粉末制备:将混料进行吸氢后再在450℃脱氢处理,将混料在保护气氛下进行制粉,保护气体中含有50ppm的氧气,余量为氮气;粉体的平均粒度为2.65μm;
42.3)压制成型:将粉体在磁场下取向,磁场强度为2.0t,然后在氮气保护气氛下压制成坯料;
43.4)烧结:烧结温度1040℃,保温时间在6h,烧结真空度在2
×
10-3
pa;
44.5)回火:将温度降至900℃,保温时间3h后,温度再降至580℃,再保温4h。
45.对比例1与实施例1的不同之处在于:不含有si元素。
46.对比例2与实施例2的不同之处在于:使用的是单合金,即合金m和合金n为同一合金,熔炼温度为1450~1500℃,冷却速度为1500℃/s;
47.对比例3与实施例3的不同之处在于:不含有ge元素。
48.对得到的实施例、对比例进行性能检测:
49.相组织:使用面积法对磁体的扫描电子像中测量不同相的含量,从附图1可以看
出,实施例2的磁性材料的相组织包括2:14:1相以及分布在2:14:1相晶界处的晶界相,其中,晶界相包括富re相和r-t-ga相。晶界相在相组织中的面积含量为18.7%,r-t-ga相占晶界相面积含量的43%。
50.从附图2可以看出,磁体有2:14:1相和晶界相组成,晶界上没有深灰色的r-t-ga相,晶界相的面积比例在17.6%。
51.压制成型后的坯料密度检测:压制的成型密度采用质量除以体积计算,其中体积使用游标卡尺通过尺寸测量计算。
52.磁性性能检测:检测方法按照gb13560-2017所示的方法检测得到的磁性材料加工成φ10mm
×
10mm的样柱,主要测试项目为剩磁br、内禀矫顽力hcj,检测结果见表2。
53.电阻率检测:按照四探针法测试磁体的电阻率。得到的磁性材料加工成1
×1×
10mm3样件测试电阻率,检测结果见表2。
54.表1本发明实施例和对比例的成分/wt%
[0055][0056]
表2本发明实施例、对比例的磁性性能和电阻率
[0057]
再多了解一些
本文用于创业者技术爱好者查询,仅供学习研究,如用于商业用途,请联系技术所有人。