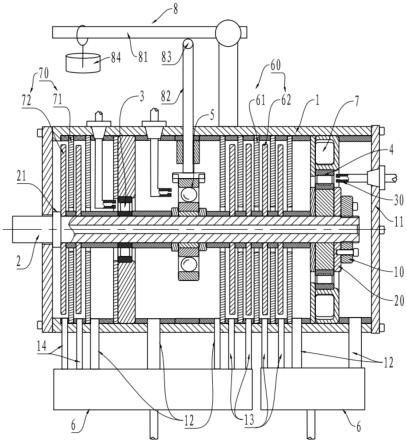
1.本发明涉及润滑油测试技术领域,具体涉及航空润滑油沉积性能试验装置。
背景技术:
2.航空润滑油是航空油料的一部分,主要为滚珠轴承、滚柱轴承和齿轮等关键活动零部件提供润滑、冷却与清洁作用,是航空器和涡扇发动机各系统不可缺少的功能材料。
3.以航空涡轮发动机使用的润滑油为例,润滑油通过润滑系统对涡轮发动机中存在相互运动的高温部件进行有效润滑的同时,带走高温部件的大量热量,使发动机的高温部件得以相对冷却而保持在适当的工作温度下稳定运行;此外,润滑系统中,润滑油在回收时,将发动机内存在的杂质带走,相当于对涡轮发动机实现了清洁功能。但在润滑系统中,润滑油是不断循环使用的,在整个循环过程中,润滑油经历了吸热、升温、氧化、冷却不断往复的过程,因此就产生了蒸发、结焦、腐蚀等反应倾向。那么有必要对润滑油的高温氧化安定性和抗磨性能进行研究和评定。
4.现有技术中针对航空润滑油需要采用满足fed-std-791e method3410标准方法或等效替代方法来对航空润滑油进行试验(该方法进行的试验在下文统称“沉积性能试验”),该方法需要用到相应的试验装置,该试验装置包括箱体、主轴、支撑轴承、试验轴承和加载轴承,主轴一端穿出箱体以与动力源连接,主轴另一端深入箱体内,主轴通过支撑轴承和试验轴承支撑在箱体内,加载轴承位于支撑轴承和试验轴承之间,加载轴承外接径向加载机构,以通过加载轴承给主轴施加径向载荷,试验轴承安装在主轴上,同时箱体上安装将试验轴承环绕的加热元件(如加热器);主轴在支撑轴承和试验轴承之间的位置设置有螺旋密封结构,螺旋密封结构包括内套和外套,内套转动连接在主轴上,外套固定连接在箱体上,内套带有外螺纹而外套带有与外螺纹啮合的内螺纹,螺旋密封结构通过内外螺纹配合将箱体分为支撑油腔和试验油腔,试验轴承位于试验油腔内,支撑轴承和加载轴承均位于支撑油腔内,试验时,通过不同的喷油嘴分别向三种不同的轴承喷出润滑油,位于支撑油腔的加载轴承和支撑轴承使用的是支撑润滑油(以下均简称支撑油),试验轴承使用的是被试验的航空润滑油(以下均简称试验油),喷向对应轴承的支撑油油温为71~82℃,喷向试验轴承的试验油油温为177℃左右,试验时主轴的转速约10000r/min,试验过程中,加热元件温度控制在约260℃,试验若干小时后,检查分析试验油的理化性能、油耗、油滤和轴承沉积等情况,以评判润滑油的高温氧化安定性和抗磨性能。
5.但是通过大量重复性试验发现,现有螺旋密封结构在高速旋转的条件下,难以有效密封试验油腔与支撑油腔,导致试验油腔中的试验油不断泄露至支撑油腔中,一方面试验油向支撑油腔泄露会使得试验油消耗的测试不准确而影响对试验油油耗的评判准确性;另一方面,试验油和支撑油所使用的润滑油并不相同,支撑油的粘度和抗磨性能均高于试验油,试验油混入后将降低支撑油粘度和抗磨性,加速支撑轴承和加载轴承磨损。
6.此外,现有试验装置的径向加载机构存在瑕疵,由于标准方法中使用的径向加载机构为气缸,试验时要求气缸采用高压压缩空气以通过气缸的活塞杆产生对加载轴承的垂
直向下作用力(在润滑油沉积性能试验中,气缸需要给主轴施加约2763n的力,而气缸的活塞杆直径只有约10cm),使加载轴承产生向下的力矩,从而使试验轴承加载。但由于润滑油沉积性能试验属于耐久性试验,试验时间长(润滑油试验时长在每次100小时至200小时不等),随着试验推进,气缸密封性随着密封环老化而逐渐失效,试验轴承加载压力逐渐降低,严重影响试验准确性。同时,由于气缸加载系统长时间承受高压高载荷,加之加载轴承随主轴的高速转动产生的温度会传递到气缸上,而加热元件距离气缸也不远,导致试验过程中气缸温度高而需要用循环冷却水对气缸的加载系统进行冷却,但随着长时间试验推进,气缸加载系统中的冷却水密封垫也会存在逐渐老化而出现渗水的情况,严重影响试验操作和台架使用寿命。
技术实现要素:
7.本发明意在提供航空润滑油沉积性能试验装置,以缓解现有技术中的试验装置存在密封结构密封不严实而带来试验准确性受影响的问题。
8.为达到上述目的,本发明采用如下技术方案:
9.航空润滑油沉积性能试验装置,包括箱体、主轴、支撑轴承、试验轴承、加载轴承和密封组件,箱体底部设有至少两个出油孔,出油孔位于密封组件两侧,主轴通过支撑轴承和试验轴承转动连接在箱体内,加载轴承套在主轴上,密封组件包括安装在箱体上的至少两个挡板一和固定在主轴上的至少两个挡板二,挡板一和挡板二沿主轴轴向交替设置,挡板一和挡板二在主轴横截面的投影存在连续交叠区域,挡板一和相邻的挡板二在主轴轴向存在3-5mm的间隙。
10.本方案的原理及优点是:本方案通过密封组件将箱体分隔为两个腔室,每个腔室均有出油孔,试验装置按照现有方法进行试验,试验过程中喷向轴承的润滑油能够在下落后从箱体底部的出油孔排出。
11.本方案在密封性能上,首先因密封组件的挡板二固定在主轴上而随主轴同步进行高速运转,挡板二在封闭箱体内的高速转动会带来较强的风压,风压的存在会阻挡呈雾状或滴状的润滑油(雾状润滑油以下简称油雾,滴状润滑油以下简称油滴)向密封组件靠近,形成对密封组件两侧润滑油的一级阻挡;而密封组件中交替排布且在主轴的横截面有连续交叠区域的挡板一和挡板二形成对箱体两个腔室的层层阻碍,形成了二级阻挡,使得油雾或油滴即便越过一级阻挡,也将在二级阻挡下大大降低窜移的速度,进一步降低油雾或油滴窜移到另一侧腔室中的概率;此外,位于密封组件中间区域的挡板因远离支撑油腔和试验油腔而温度较底,油雾在减速后触碰到更低温的挡板时更容易形成油滴而下落,进一步阻碍油雾的窜移(可视为三级阻挡);可见本方案的密封组件以简单的结构形成了对油雾或油滴的重重阻碍,使得本方案的密封性能优越。
12.经研究,现有技术中的螺旋密封结构其内套因安装在主轴上,而主轴会承受来自加载轴承的径向载荷,导致主轴长时间的高速转动中存在弯曲变形,加之试验时箱体内温度较高(温度会带来热胀冷缩而产生形变),使得螺旋密封结构受主轴和温度的影响,而导致螺旋密封结构的内外套的啮合间隙产生变化,局部区域的啮合间隙增大,导致润滑油的窜移,局部区域啮合间隙减小,导致密封结构的内套与外套之间产生剐蹭,造成螺旋密封结构的损坏。
13.而本方案中,挡板一和挡板二是交替排布的,且挡板一和挡板二之间具有轴向3-5mm的间隙,保证了即便主轴因承受径向载荷而产生弯曲的情况完全不会影响密封组件的密封性能;箱体内两个腔室温度的不同使得热胀冷缩带给密封组件两侧结构的形变不同,也会因为间隙的存在而完全不影响密封组件的密封性能,保证了本装置在具有优异的密封性能的基础上还不会因为试验时长的增加而降低密封组件的使用寿命。
14.总之,本装置密封性能的提升既有利于航空润滑油油耗测试的准确性,又能大大降低甚至避免润滑油窜移到箱体另一腔室后,带来的支撑轴承和加载轴承磨损的问题,且密封组件自身在长时间的试验中也不会有剐蹭,大大延长了整个试验装置的使用寿命。
15.优选的,所述挡板一与主轴的外表面之间存在3-5mm的间隙,挡板二与箱体内壁之间存在3-5mm的间隙。
16.有益效果:本方案使得挡板一与主轴之间仅有3-5mm间隙,挡板二与箱体之间也仅有3-5mm间隙,也即说明本方案中挡板一和挡板二在主轴横截面的投影存在的连续交叠区域更大,进一步增加了润滑油进入挡板一和挡板二之间的难度,有利于提高密封组件的密封效果。
17.此外,在润滑油的沉积性能试验中,间隙的存在使得挡板一和挡板二均呈薄板状(以挡板二为例,若挡板二采用圆盘结构,挡板二的外径约为230mm,而挡板二套在主轴上的内径约为50mm,而挡板二本身也只有5mm左右的厚度),薄板状的挡板有利于降低密封组件的材料成本,也有利于降低试验装置的整体重量,而也因为这些间隙的设置,使得密封组件在密封性能优越、材料成本低、重量更轻的基础上,能够降低对挡板一和挡板二的加工工艺要求和降低对挡板一和挡板二的强度要求,进一步降低密封组件的成本。
18.优选的,作为一种改进,所述挡板二的两侧均有挡板一。
19.有益效果:本方案使得密封组件沿主轴轴向的两端均为挡板一,挡板一安装在箱体上,挡板一的自由端靠向主轴,使得润滑油难以进入相邻的挡板一和挡板二之间,有利于提高本试验装置的密封性能。
20.优选的,作为一种改进,所述箱体底部还设有排油孔,排油孔位于相邻挡板一之间。
21.有益效果:采用本方案时,如果出现润滑油进入到相邻的挡板一和挡板二之间,则进入的润滑油也将在重力的作用下落入箱体底部而沿设置在相邻挡板一之间的排油孔及时排出,进而完全避免箱体一侧的润滑油混入另一侧润滑油的情况。
22.优选的,作为一种改进,所述箱体上安装径向加载机构,径向加载机构包括加载杆和承压杆,加载杆位于箱体外,承压杆竖向滑动连接在箱体上,承压杆的底部抵压在加载轴承的外圈上,加载杆压在承压杆上,加载杆的一端转动连接在箱体上。
23.有益效果:通过径向加载机构向加载轴承施加径向载荷时,通过在加载杆的自由端施加外力(外力施加方式可以是悬挂重物的方式施加(如悬挂砝码)也可以是从上往下按压加载杆的方式施加),进而使得承压杆承受来自加载杆的压力,压力传递到加载轴承上,完成径向载荷的施加。相比现有技术,本方案仅仅承压杆伸入箱体内,不会存在现有技术中气缸作为径向加载机构而带来的气缸内密封环老化而容易出现加载压力逐渐降低的问题、不会存在需要单独的循环冷却水对气缸进行冷却的问题、更不会出现因冷却水密封垫老化而带来的渗水的问题。
24.此外,本方案在径向加载时,只需要调整加载杆自由端施加的外力大小就能调整施加在加载轴承上的径向载荷的大小,相比气缸通过高压压缩气体调整径向载荷的情况,本方案径向载荷的调整更加简单方便。
25.优选的,作为一种改进,所述加载杆与承压杆之间设有压力传感器。
26.有益效果:通过压力传感器能够非常直观地知晓径向加载载荷的大小。
27.优选的,作为一种改进,所述支撑轴承和试验轴承与箱体之间设有轴承座,轴承座和挡板一均安装在箱体内壁同一个连续的表面。
28.有益效果:本方案的轴承座和挡板一均安装在箱体内壁同一表面,使得对箱体内表面呈整体式,相比现有技术中不同轴承座、密封结构安装在箱体不同内表面的情况,本方案对箱体的加工工艺更加简单,易于实现箱体的高精度加工。
29.此外,挡板一均安装在箱体的同一内表面,使得所有挡板一形状尺寸完全相同,降低了挡板一的安装难度。
30.优选的,作为一种改进,所述加载轴承、支撑轴承和试验轴承均安装在主轴的同一个连续外表面上。
31.有益效果:本方案使得加载轴承、支撑轴承和试验轴承均处在主轴的同一段光轴上,避免了现有技术中不同轴承附近的主轴上设计轴肩而带来的轴肩处应力集中最终导致主轴在高速旋转下容易断裂的问题。
32.此外,本方案将主轴安装加载轴承、支撑轴承和试验轴承的一段设计为光轴段,易于实现光轴段的高精度加工,避免因多个轴肩设计带来的加工误差。
33.优选的,作为一种改进,所述主轴上设有轴肩,主轴的自由端连接有锁紧件,锁紧件和轴肩位于箱体的两端,主轴上套有多个固定套,多个固定套用于填补主轴在轴肩和锁紧件之间安装支撑轴承、加载轴承、试验轴承和挡板二后留下的间隙。
34.有益效果:本方案通过固定套来填补主轴上除轴承和挡板二后的间隙,使得主轴在轴肩和锁紧件之间安装的零件(支撑轴承、加载轴承、试验轴承以及多个挡板二)能够安装方便又能实现稳固安装。
35.优选的,作为一种改进,所述锁紧件采用锁紧螺母,锁紧螺母与试验轴承之间设有垫片,锁紧螺母能够通过螺钉与垫片固定连接。
36.有益效果:在锁紧螺母通过垫片将试验轴承安装在主轴上后,通过螺钉将锁紧螺母与垫片形成固定连接,操作简单方便,且有利于提高锁紧螺母的锁紧效果,避免主轴反向旋转而将锁紧螺母旋松的情况。
37.优选的,作为一种改进,所述箱体内还安装有封隔组件,封隔组件与密封组件将箱体内支撑轴承所在的腔室封闭,封隔组件包括安装在箱体内的至少两个挡板三和安装在主轴上的至少两个挡板四,挡板三和挡板四沿主轴轴向交替设置。
38.有益效果:本方案通过与密封组件结构相似的封隔组件实现对主轴穿出箱体一端的支撑油腔的密封作用,保证了密封效果,同时也避免了现有技术中采用端盖配合密封圈对主轴穿出箱体部位进行密封带来的密封圈容易磨损的问题。
附图说明
39.图1为本发明实施例的主视剖视图。
40.图2为图1中的密封组件与箱体和主轴的连接关系示意图。
具体实施方式
41.下面通过具体实施方式进一步详细说明:
42.说明书附图中的附图标记包括:箱体1、端盖11、出油孔12、排油孔13、回油孔14、主轴2、轴肩21、支撑轴承3、试验轴承4、加载轴承5、密封组件60、封隔组件70、径向加载机构8、挡板一61、挡板二62、挡板三71、挡板四72、回收容器6、加热元件7、加载杆81、承压杆82、压力传感器83、砝码84、锁紧螺母10、垫片20、喷油嘴30。
43.实施例基本如附图1和图2所示,航空润滑油沉积性能试验装置,包括箱体1、主轴2、支撑轴承3、试验轴承4、加载轴承5、密封组件60、封隔组件70和径向加载机构8,主轴2通过支撑轴承3和试验轴承4转动连接在箱体1内,加载轴承5套在主轴2上,密封组件60位于试验轴承4和加载轴承5之间,封隔组件70和加载轴承5位于支撑轴承3两侧,径向加载机构8用于给加载轴承5施加径向载荷。
44.主轴2在封隔组件70远离支撑轴承3的一端(也即本实施例的左侧)一体成型有轴肩21,主轴2的轴肩21两侧不再设置轴肩21,避免了主轴2上因应力集中位置靠近轴承而导致主轴2容易断裂的问题。
45.箱体1内壁呈圆柱状,箱体1两端固定有端盖11,其中一个端盖11上设有供主轴2穿过的避空孔,另一个端盖11将箱体1另一端封闭,箱体1底部设有至少两个出油孔12,不带避空孔的端盖11、密封组件60和封隔组件70将箱体1分隔为支撑油腔和试验油腔,本实施例中支撑油腔位于箱体1左侧,试验油腔位于箱体1右侧,箱体1在支撑油腔一侧的底部开设有3个出油孔12,箱体1在试验油腔一侧的底部开有2个出油孔12,还包括用于回收润滑油的两个回收容器6,两个回收容器6分别用于回收支撑油腔的润滑油和试验油腔的润滑油。
46.密封组件60包括安装在箱体1上的至少两个挡板一61和固定在主轴2上的至少两个挡板二62,挡板一61和挡板二62沿主轴2轴向交替设置,挡板一61和挡板二62在主轴2横截面的投影存在连续交叠区域,挡板一61和相邻的挡板二62在主轴2轴向存在3-5mm的间隙;挡板一61与主轴2的外表面之间存在3-5mm的间隙,挡板二62与箱体1内壁之间存在3-5mm的间隙。本实施例中挡板一61呈圆环状,挡板二62呈圆盘状;挡板一61的数量比挡板二62数量多1个,挡板二62的两侧均有挡板一61,本实施例中挡板一61的数量有5个,挡板二62的数量有4个。
47.箱体1底部还加工有排油孔13,排油孔13位于相邻挡板一61之间,位于密封组件60左半部分位置的排油孔13与收集支撑油的回收容器6连通,位于密封组件60右半部分位置的排油孔13与收集试验油的回收容器6连通。
48.为方便轴承的安装,在支撑轴承3与箱体1之间、试验轴承4与箱体1之间设置轴承座,轴承座和挡板一61均安装在箱体1内壁同一个连续的表面,以方便箱体1作为整体式箱体1,且箱体1的安装面均为同一个内表面,方便箱体1成型的同时,降低箱体1内表面的加工精度控制难度,方便安装面实现高精度加工,箱体1安装面上套装有多个分隔套,分隔套用于填补安装面上零件之间的间隙,比如填补相邻挡板一61之间的间隙,填补挡板一61与轴承座之间的间隙。
49.径向加载机构8包括加载杆81、承压杆82、压力传感器83和砝码84,加载杆81位于
箱体1外,承压杆82竖向滑动连接在箱体1上,承压杆82的底部抵压在加载轴承5的外圈上,加载杆81压在承压杆82顶部,加载杆81的右端通过球铰接方式转动连接在箱体1上,加载杆81的左端(也即自由端)能够施加外力,本实施中采用悬挂砝码84的方式施加外力,压力传感器83安装在承压杆82顶部。
50.此外,为保证本试验装置进行润滑油的沉积性能试验,在安装试验轴承4的轴承座内安装有加热元件7。
51.加载轴承5、支撑轴承3和试验轴承4均直接安装或通过设有的固定座间接安装在主轴2的同一个连续外表面上。
52.主轴2的自由端螺纹连接有锁紧螺母10,锁紧螺母10和轴肩21位于箱体1的两端,主轴2上套有多个固定套,多个固定套用于填补主轴2在轴肩21和锁紧螺母10之间安装支撑轴承3、加载轴承5、试验轴承4和挡板二62后留下的间隙。
53.锁紧螺母10与试验轴承4之间设有垫片20,垫片20套在主轴2上,锁紧螺母10的端面上开设有两个腰型孔,通过螺钉贯穿腰型孔以将锁紧螺母10与垫片20形成轴向的固定连接,以保证在主轴2被动力源带动着反转时,锁紧螺母10不会被拧松。
54.封隔组件70与密封组件60结构相同,封隔组件70包括安装在箱体1内的至少两个挡板三71和固定在主轴2上的至少两个挡板四72,挡板三71和挡板四72沿主轴2轴向交替设置,本实施例中挡板三71、挡板四72均有2个。
55.每一个挡板四72对应的箱体1底部均开有回油孔14,回油孔14与收集支撑油的回收容器6连通。
56.箱体1上还安装有三个喷油嘴30,三个喷油嘴30分别正对支撑轴承3、加载轴承5和试验轴承4。
57.具体实施过程如下:
58.采用本实施例的试验装置按照fed-std-791e method 3410标准方法或等效替代方法进行试验,试验过程中喷油嘴30分别向对应的支撑轴承3、加载轴承5和试验轴承4喷出相应的润滑油,通过向径向记载机构80的加载杆81上悬挂砝码84使得加载轴承5对主轴2产生径向载荷,试验中产生的支撑油和试验油通过出油孔12、排油孔13和回油孔14回收到相应的回收容器6内以便于对相应的润滑油进行循环利用。
59.在试验过程中,首先因密封组件60的挡板二62固定在主轴2上而随主轴2同步进行高速运转,挡板二62在封闭箱体1内的高速转动会带来较强的风压,风压的存在会阻挡呈雾状或滴状的润滑油(雾状润滑油以下简称油雾,滴状润滑油以下简称油滴)向密封组件60的靠近,形成对密封组件60两侧润滑油的一级阻挡;而密封组件60中交替排布且在主轴2的横截面有连续交叠区域的挡板一61和挡板二62形成对箱体1两个腔室的层层阻碍,形成了二级阻挡,使得油雾或油滴即便越过一级阻挡,也将在二级阻挡下大大降低窜移的速度,进一步降低油雾或油滴窜移到另一侧腔室中的概率;此外,位于密封组件60中间区域的挡板因远离支撑油腔和试验油腔而温度较底,油雾在减速后触碰到更低温的挡板时更容易形成油滴而下落,进一步阻碍油雾的窜移(可视为三级阻挡);可见本实施例的密封组件60以简单的结构形成了对油雾或油滴的重重阻碍,使得本实施例的密封性能非常优越;而即便是在重重阻挡下依然有油雾形成油滴进入到相邻的挡板一61之间,则该进入的润滑油也将在重力的作用下落入箱体1底部而沿设置在相邻挡板一61之间的排油孔13及时排出,进而完全
避免箱体1一侧的润滑油混入另一侧润滑油的情况。
60.此外,本实施例中,挡板一61和挡板二62是交替排布的,且挡板一61和挡板二62之间具有轴向3-5mm的间隙,挡板一61与主轴2之间仅有3-5mm的径向间隙,挡板二62与箱体1之间也仅有3-5mm的径向间隙,保证了即便主轴2因承受来自径向载荷而产生弯曲的情况,也完全不会影响密封组件60的密封性能;箱体1内两个腔室温度的不同使得热胀冷缩带给密封组件60两侧结构的形变不同,也会因为间隙的存在而完全不影响密封组件60的密封性能,保证了本装置在具有优异的密封性能的基础上还不会因为试验时长的增加而降低密封组件60的使用寿命。
61.而在径向载荷的加载时,只需要调整加载杆81自由端悬挂的砝码84重量就能调整施加在加载轴承5上的径向载荷的大小,相比气缸通过高压压缩气体调整径向载荷的情况,本实施例径向载荷的调整更加简单方便,且本实施例的径向加载机构8不会存在加载载荷波动、零件容易老化以及加载机构渗水的问题。
62.除此之外,本实施例的封隔组件70的设置在保证支撑油腔密封效果的同时也避免了现有技术中采用端盖11配合密封圈对主轴2穿出箱体1部位进行密封带来的密封圈容易磨损的问题。
63.总之,本装置无论是密封结构、径向加载方式还是主轴2的结构均在现有技术上进行了极大地改善,使得润滑油沉积性能试验下航空润滑油的油耗测试准确性得以保证,又能大大降低甚至避免润滑油的窜移,降低甚至避免出现因窜油带来的支撑轴承3和加载轴承5磨损的问题,且密封组件60自身在长时间的试验中也不会有剐蹭、径向加载机构8的加载方式更加简单方便且有保障、主轴2和箱体1强度也容易做到更高,极大延长了整个试验装置的使用寿命。
64.以上所述的仅是本发明的实施例,方案中公知的具体技术方案和/或特性等常识在此未作过多描述。应当指出,对于本领域的技术人员来说,在不脱离本发明技术方案的前提下,还可以作出若干变形和改进,这些也应该视为本发明的保护范围,这些都不会影响本发明实施的效果和专利的实用性。本技术要求的保护范围应当以其权利要求的内容为准,说明书中的具体实施方式等记载可以用于解释权利要求的内容。
再多了解一些
本文用于创业者技术爱好者查询,仅供学习研究,如用于商业用途,请联系技术所有人。