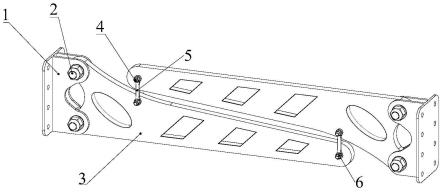
1.本发明属于中低速磁浮抗侧滚梁技术领域,具体涉及一种复合材料抗侧滚片梁、其成型工艺及复合材料中低速磁浮抗侧滚梁。
背景技术:
2.这里的陈述仅提供与本发明相关的背景技术,而不必然地构成现有技术。
3.中低速磁浮列车悬浮能力有限导致其运能受到一定限制,因此在中低速磁浮列车设计制造过程中,充分实现中低速磁浮列车悬浮架部件结构的轻量化设计迫在眉睫,目前的解决方法是将现有的抗侧滚梁结构的材质由金属材料替换为碳纤维复合材料,但是该种方案存在以下问题:
4.(1)该抗侧滚梁结构沿用金属材料结构(每个抗侧滚梁的两个片梁由六个相互平行的加强肋板连接形成一体化结构),采用材料替代的方式进行设计,该种结构设计方式不能够充分发挥复合材料的性能优势;
5.(2)现有技术中仅记载了采用碳纤维复合材料制备抗侧滚梁,并没有给出该种设计结构的成型工艺方式,但是复合材料结构的铺层设计以及成型工艺对结构件的机械性能是至关重要;
6.(3)由于现有的每个抗侧滚梁是其两个片梁由六个相互平行的加强肋板连接形成的一体化结构,该种结构不利于抗侧滚片梁的成型工艺,难以实现高效低成本制造以及抗侧滚梁的批量化生产制造。
技术实现要素:
7.针对现有技术存在的不足,本发明的目的是提供一种复合材料抗侧滚片梁、其成型工艺及复合材料中低速磁浮抗侧滚梁。
8.为了实现上述目的,本发明是通过如下的技术方案来实现:
9.第一方面,本发明提供一种复合材料抗侧滚片梁,由碳纤维复合材料制备而成,碳纤维的铺层方向包括0
°
、90
°
、-45
°
和45
°
;
10.±
45
°
的铺层碳纤维总量大于0
°
和90
°
的碳纤维铺层量;
11.其中,所述0
°
为片梁的长度方向,90
°
为片梁的宽度方向;
12.复合材料抗侧滚片梁沿其长度方向的宽度减小,沿其长度方向设置有多个减重孔,不同减重孔与片梁边缘之间的距离基本相等。
13.第二方面,本发明提供所述复合材料抗侧滚片梁的成型工艺,包括如下步骤:
14.采用碳纤维预浸料模具中进行铺层,碳纤维的铺层方向包括0
°
、90
°
、-45
°
和45
°
;
15.其中,
±
45
°
的铺层碳纤维总量大于0
°
和90
°
的碳纤维铺层量;
16.铺层完毕后,上下模具合模,加热加压,固化成型。
17.第三方面,本发明提供一种复合材料中低速磁浮抗侧滚梁,其包括安装座、第一复
合材料抗侧滚片梁、第二复合材料抗侧滚片梁、吊杆轴和吊杆;
18.第一复合材料抗侧滚片梁、第二复合材料抗侧滚片梁呈中心对称分布,构建平行四边形机构,其端部均安装于安装座上,吊杆轴沿厚度方向过盈安装在复合材料抗侧滚片梁上,两复合材料抗侧滚片梁之间通过吊杆轴和吊杆连接,吊杆轴和吊杆之间活动配合。
19.上述本发明的一种或多种实施例取得的有益效果如下:
20.1、该复合材料抗侧滚片梁采用一体化成型工艺,解决了金属材料片梁组装工艺复杂的问题,进而达到能够实现抗侧滚片梁的快速高效制备,及其轻量化目的,减重约36%左右;
21.抗侧滚片梁与吊杆轴采用过盈配合方式装配,可以大大提高复合材料片梁吊杆轴安装孔的抗疲劳性能;吊杆轴和吊杆之间活动配合,以保证吊杆的自由旋转,进而保证两复合材料抗侧滚片梁之间的相对运动。
22.2、该复合材料抗侧滚片梁根据中低速磁浮抗侧滚梁的实际服役工况进行承载分析,然后进行复合材料抗侧滚片梁结构设计和铺层设计,解决材料替代设计的弊端,能够充分发挥复合材料抗侧滚梁的机械性能优势;
23.3、该复合材料抗侧滚片梁采用模压成型工艺进行制备,设计了抗侧滚片梁的成型模具,解决了复合材料抗侧滚片梁成型困难、制造质量缺陷严重等问题,实现复合材料抗侧滚片梁的高效低成本制备。
附图说明
24.构成本发明的一部分的说明书附图用来提供对本发明的进一步理解,本发明的示意性实施例及其说明用于解释本发明,并不构成对本发明的不当限定。
25.图1为本发明实施例中复合材料中低速抗侧滚梁总组轴侧图;
26.图2为本发明实施例中复合材料中低速抗侧滚梁总组主视图;
27.图3为本发明实施例中吊杆安装局部放大图;
28.图4为本发明实施例中吊杆安装配合剖视图;
29.图5为本发明实施例中安装座轴测图;
30.图6为本发明实施例中吊杆主视图;
31.图7为本发明实施例中吊杆轴主视图;
32.图8为本发明实施例中机加工完成后复合材料抗侧滚片梁主视图;
33.图9为本发明实施例中复合材料抗侧滚片梁模压成型模具;
34.图10为本发明实施例中复合材料抗侧滚片梁模压成型初始结构;
35.图11为本发明实施例中吊杆组合结构。
36.其中,1、安装座,2、螺栓,3、复合材料抗侧滚片梁,4、吊杆轴,5、吊杆,6、安装螺母,7、平垫圈。
具体实施方式
37.应该指出,以下详细说明都是例示性的,旨在对本发明提供进一步的说明。除非另有指明,本发明使用的所有技术和科学术语具有与本发明所属技术领域的普通技术人员通常理解的相同含义。
38.第一方面,本发明提供一种复合材料抗侧滚片梁,由碳纤维复合材料制备而成,碳纤维的铺层方向包括0
°
、90
°
、-45
°
和45
°
;
39.±
45
°
的铺层碳纤维总量大于0
°
和90
°
的碳纤维铺层量;
40.其中,所述0
°
为片梁的长度方向,90
°
为片梁的宽度方向;
41.复合材料抗侧滚片梁沿其长度方向的宽度减小,沿其长度方向设置有多个减重孔,不同减重孔与片梁边缘之间的距离基本相等。
42.现有的抗侧滚梁大部分采用金属材质,由于金属材质密度较大,重量大,不利于悬浮架结构部件的轻量化。虽然已经有技术提出,采用碳纤维复合材料替代金属材料,以实现抗侧滚梁的轻量化。
43.但是仍旧存在以下问题:
44.1)现有的抗侧滚梁是两个片梁由六个相互平行的加强肋板连接形成一体化结构,两个片梁并列平行设置,具有复杂的型腔结构。
45.由于碳纤维增强复合材料中,如果需要实现抗压或/和抗拉等性能的大幅提高,需要采用连续碳纤维对树脂基体进行增强。所以结构件在成型时,首先需要对纤维预浸料按结构件的设计形状进行铺设,然后再进行热压固化成型。
46.现有的抗侧滚梁的结构,使得碳纤维预浸料难以进行均匀铺设,且设置有众多型腔结构也难以实现碳纤维预浸料的铺设,进而导致该种结构难以实现碳纤维增强材料的一体化成型。
47.如果采用多工艺协同手段实现复合材料抗侧滚梁的一体化成型,易出现结构质量缺陷,不利于提高抗侧滚梁的整体性能以及使用寿命。
48.2)抗侧滚梁在使用过程中,承载情况复杂多变,特别是在通过缓和曲线时,将会产生相对较为复杂的点头与摇头载荷,产生相应的多方向载荷共同作用,所以,如果碳纤维的铺设方向单一,抗侧滚梁难以应对各个方向的力的冲击,进而影响使用寿命。
49.3)由于碳纤维增强复合材料具有各向异性,吊杆轴在安装时需要在抗侧滚梁上开孔,运行过程中,吊杆轴可能对抗侧滚梁开孔的内壁施加各个方向的冲击力,产生的裂纹容易在碳纤维增强薄弱的方向发展,进而影响抗侧滚梁的使用寿命。
50.4)由于沿长度方向,抗侧滚梁是不等宽的,所以抗压能力不同,抗侧滚梁的整体抗压能力主要受其最薄弱部位影响。较大宽度的位置容易出现可承载能力富余的情况。在该种情况下,容易造成材料的过多使用,并导致制备得到的抗侧滚梁难以达到最佳的轻量化。
51.针对以上主要问题,发明人有针对性地对复合材料抗侧滚梁进行了改进,主要改进点包括以下几方面:
52.1)对抗侧滚梁的整体结构进行了改进,由现有的两个片梁及两片梁之间连接的六个加强肋的复杂型腔结构替换为一个抗侧滚片梁的形式,该种结构是单一片层结构,适合在模具中进行铺层,并适合模压成型。
53.2)为了保证单一抗侧滚片梁的整体性能以及与吊杆轴的连接位置处的抗疲劳及抗压、抗冲击性能,发明人经过试验发现,可以通过对碳纤维的铺设方向进行优化实现。
[0054]0°
方向铺设的碳纤维可以有效提高抗侧滚量的竖向抗压性能;90
°
方向铺设的碳纤维可以有效提高抗侧滚梁的抗侧向摩擦力的作用,在列车转弯等动作时,能够提供足够的支撑强度,而不发生损坏;
[0055]
±
45
°
铺层的碳纤维,可以应对其他各个方向的冲击力,并辅助0
°
方向铺设的碳纤维和90
°
方向铺设的碳纤维,提高抗侧滚梁的各个方向冲击力的承载能力,同时可以提高抗侧滚梁开孔位置的抗冲击能力,进而有效提高其使用寿命。
[0056]
3)为了最大限度提高抗侧滚梁的轻量化,沿抗侧滚梁的长度方向上开设多个减重孔,不同减重孔与片梁边缘之间的距离基本相等,采用该种设置方式,可以保证抗侧滚梁的承载能力。
[0057]
同时,在抗侧滚梁的主体上开设多个减重孔,为提高其厚度提供了可能,当抗侧滚梁的厚度较大时,更易实现对抗侧滚梁的局部压强进行分担,并可以对抗侧滚梁开设通孔的位置处(如安装吊杆轴的位置)的压强进行分担,进而有效提高抗侧滚梁的承载能力。
[0058]
在一些实施例中,所述减重孔的形状为平行四边形。根据拓扑优化设计结果和易实现铺层设计,具有较好的力学性能,以适应中低速磁浮环境,同时可以最大限度实现轻量化。
[0059]
优选的,所述复合材料抗侧滚片梁的最大宽度处设置有椭圆形减重孔。根据拓扑优化设计结果和易实现铺层设计,具有较好的力学性能,以适应中低速磁浮环境,同时可以最大限度实现轻量化。
[0060]
在一些实施例中,复合材料抗侧滚片梁上设置有3个平行四边形减重孔和一个椭圆形减重孔。
[0061]
在一些实施例中,0
°
碳纤维的铺设质量百分数为20%-30%,90
°
碳纤维的铺设质量百分数为20%-30%。
[0062]
第二方面,本发明提供所述复合材料抗侧滚片梁的成型工艺,包括如下步骤:
[0063]
采用碳纤维预浸料模具中进行铺层,碳纤维的铺层方向包括0
°
、90
°
、-45
°
和45
°
;
[0064]
其中,
±
45
°
的铺层碳纤维总量大于0
°
和90
°
的碳纤维铺层量;
[0065]
铺层完毕后,上下模具合模,加热加压,固化成型。
[0066]
在一些实施例中,所述模具的形状与复合材料抗侧滚片梁的形状相配合,在复合材料抗侧滚片梁的减重孔位置设置凸起。
[0067]
第三方面,本发明提供一种复合材料中低速磁浮抗侧滚梁,其包括安装座、第一复合材料抗侧滚片梁、第二复合材料抗侧滚片梁、吊杆轴和吊杆;
[0068]
第一复合材料抗侧滚片梁、第二复合材料抗侧滚片梁呈中性对称分布,构建平行四边形机构,其端部均安装于安装座上,吊杆轴沿厚度方向过盈安装在复合材料抗侧滚片梁上,两复合材料抗侧滚片梁之间通过吊杆轴和吊杆连接,吊杆轴和吊杆之间活动配合。
[0069]
将吊杆轴与复合材料抗侧滚片梁进行过盈配合,使两者紧固安装,吊杆轴对片梁通孔侧壁施加的作用力由通孔内壁大部分区域分担,可以有效降低对通孔内壁局部的冲击压强,进而可以有效提高复合材料抗侧滚片梁的抗疲劳性能,避免通孔内壁裂纹的扩展。
[0070]
在一些实施例中,每个吊杆轴的两端均连接有一个吊杆。
[0071]
即,两复合材料抗侧滚片梁的同一个连接部位的连接件的组成包括分别过盈安装于两个复合材料抗侧滚片梁上的两个吊杆轴,以及连接在两个吊杆轴之间的两个吊杆,并采用安装螺母和平垫圈进行紧固和限位。
[0072]
吊杆安装结构采用柔性化设计同时装配过程中与复合材料抗侧滚梁、平垫圈之间距离均为1mm,确保实现吊杆结构的自由旋转。
[0073]
每个吊点设置两根吊杆,可以实现结构安全冗余。
[0074]
此外,现有技术中的防侧滚梁的两个片梁之间只设置一个吊杆,在实际应用过程中发现,采用该种设置结构,当磁悬浮列车正常行驶时,沿列车的行驶方向,防侧滚梁易受到列车的冲击,进而易发生前后摇晃,防侧滚梁的不稳定性,在一定程度上影响列车的运行稳定性。
[0075]
在每个吊点设置两根吊杆,可以有效维持防侧滚梁的稳定性,避免其前后摇晃,进而有利于提高列车的运行稳定性。
[0076]
在一些实施例中,所述吊杆轴为阶梯状结构,与复合材料抗侧滚片梁过盈配合的位置直径最大,与吊杆配合的位置直径次之,与安装螺栓配合的位置直径最小。
[0077]
与复合材料抗侧滚片梁过盈配合的位置直径最大,该段的表面积最大,更容易实现对作用压强的分散。
[0078]
吊杆在旋转过程中,容易与复合材料抗侧滚片梁接触摩擦,造成其摩擦损伤。吊杆轴的阶梯状结构可以实现对吊杆的限位,避免吊杆对复合材料抗侧滚片梁产生过大的磨损;同时可以对安装螺栓和平垫圈进行限位,以保证安装螺栓和平垫圈安装的牢固性。
[0079]
下面结合附图和实施例对本发明作进一步说明。
[0080]
抗侧滚梁功能:在磁浮列车通过曲线时抑制悬浮架结构的侧滚运动,实现悬浮架左、右模块的解耦。
[0081]
如图1所示,复合材料中低速磁浮抗侧滚梁的主要包括:安装座1、螺栓2、复合材料抗侧滚片梁3、吊杆轴4、吊杆5等部件。该部件设置于中低速磁浮悬浮架结构的两端部与托臂相连接,抑制悬浮架结构的侧滚运动,实现悬浮架左、右模块的解耦。
[0082]
抗侧滚梁片梁椭圆孔所处端部采用螺栓连接结构与安装座配合,安装座采用机械连接方式与托臂配合,两片复合材料片梁呈中心对称分布,构建平行四边形机构,然后将吊杆轴安装在复合材料抗侧滚片梁上,然后每根抗侧滚片梁两侧均安装1根吊杆,然后采用平垫圈与螺母配合将吊杆固定于吊杆轴上。
[0083]
安装座结构采用金属材料进行设计制造,平面端采用螺栓或者铆钉与悬浮架托臂结构相连接,挂耳端同样采用螺栓与复合材料抗侧滚片梁相连接;
[0084]
复合材料抗侧滚片梁采用模压成型工艺实现一体化制造,复合材料抗侧滚片梁设置有与安装座安装过渡结构,根据抗侧滚梁的实际服役承载分析,为提高材料利用率以及结构轻量化目的,设置三处四边形减重孔洞和一处椭圆形孔洞;模压成型完成后的抗侧滚片梁结构(如图10)未设置吊杆轴安装孔以及抗侧滚片梁与安装座之间安装接口,为保证安装接口准确性,采用机加工的形式开设4处安装孔,分别是两处安装座连接的螺栓孔,两处安装吊杆轴的安装孔,机加工完成后的抗侧滚片梁结构如图8所示。
[0085]
复合材料抗侧滚片梁3上设置有与安装座1连接的安装孔,采用螺栓2与安装孔进行装配;还设置有片梁安装孔,通过吊杆轴4、吊杆5和安装螺母6将两复合材料片梁呈中心对称安装配合。
[0086]
其中,吊杆轴4(如图7)采用金属材料制造,每根抗侧滚梁共设置4根,并且为阶梯轴形式共计为5段阶梯呈对称分布,中间段用于与复合材料抗侧滚片梁配合,两侧中间轴肩用于与吊杆配合;两端设置为螺纹轴形式,用于安装螺母6用以固定吊杆结构。所述的吊杆轴4与复合材料抗侧滚片梁3采用过盈配合方式安装,采用过盈配合方式有利于复合材料抗
侧滚片梁安装孔的抗疲劳性能。
[0087]
吊杆5采用铝合金材料锻造而成,每个抗侧滚梁总共设置4根吊杆5,每根抗侧滚片梁的两侧分别安装一根吊杆5,每个吊点在复合材料抗侧滚片梁3的两侧分别设置一根吊杆是一种结构安全冗余措施,单根吊杆失效抗侧滚梁依然能够正常工作,吊杆5安装与吊杆轴4两侧中间轴肩配合,为保证吊杆5能够实现与抗测滚安装梁的相对运动,安装吊杆5的轴肩长度大于吊杆5孔洞厚度,避免吊杆5与复合材料抗侧滚片梁3发生碰撞;吊杆轴4的两端螺纹轴肩处安装平垫圈7后再装配安装螺母6,防止吊杆4的滑脱,复合材料抗侧滚片梁3、吊杆5、吊杆轴4、平垫圈7与安装螺母6装配完成(装配细节示意图,如图4所示)后的吊杆4与复合材料抗侧滚片梁3、平垫圈7之间距离均为1mm,确保所设计的抗侧滚片梁吊杆结构能实现相对转动,从而实现抗侧滚功能的抑制。
[0088]
复合材料中低速磁浮抗侧滚片梁制备工艺为:
[0089]
首先根据复合材料抗侧滚片梁的结构形式,设计抗侧滚片梁的模压成型模具下模腔(如图9),设计抗侧滚片梁模压成型模具设置拔模斜度设置为1.5
°
,所有棱角均设置3mm圆角,有利于脱模和延长模具使用寿命。
[0090]
完成模具设计后,采用预浸料根据样件形状进行铺层制备,制备过程中预浸料的铺层方向以及占比为:0
°
/占比23%,
±
45
°
/占比54%,90
°
/占比23%,根据上述的铺层方向依次进行对称交错铺层。
[0091]
将根据样件完成的预浸料铺层装入模具下腔体内部,然后上下模具进行合模,进行加热加压,进行固化成型;
[0092]
固化成型结束后,将模压完成后的复合材料抗侧滚片梁进行脱模,将完成的抗侧滚片梁取出,同时将模具进行清理;
[0093]
模压成型完成后的复合材料抗侧滚片梁采用机加工的手段进行修边、制孔,完成最终的复合材料抗侧滚片梁的制备。
[0094]
以上所述仅为本发明的优选实施例而已,并不用于限制本发明,对于本领域的技术人员来说,本发明可以有各种更改和变化。凡在本发明的精神和原则之内,所作的任何修改、等同替换、改进等,均应包含在本发明的保护范围之内。
再多了解一些
本文用于创业者技术爱好者查询,仅供学习研究,如用于商业用途,请联系技术所有人。