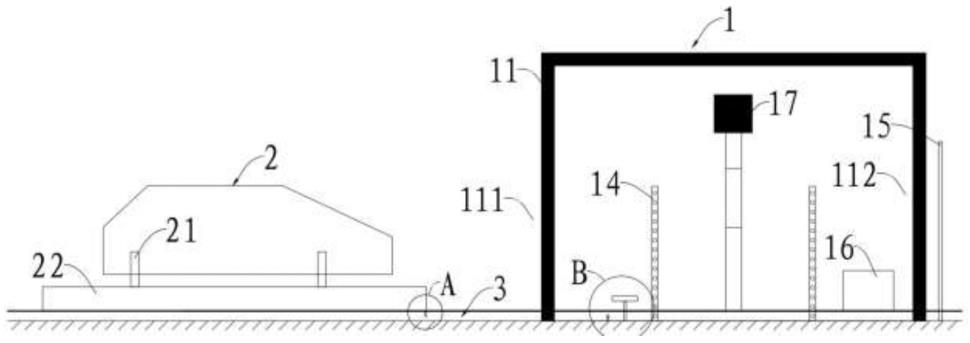
1.本发明涉及信息化和自动化控制技术领域,具体涉及一种生产线上台车信息获取装置及其工作方法。
背景技术:
2.随着我国人民生活水平提高,人们对高品质产品的需求日趋增长,同时我国制造业也在加速转型升级,提高产品质量和竞争力。因此在产品生产过程中进行生产过程控制、数据追溯、过程数据管理,质量分析等必不可少。
3.现阶段生产线上台车或其他产品数据的追溯和产品在生产线上定位加工在大规模生产领域极其常见,目前多采用二维码识别和rfid识别两种方式,二维码识别由于其不可循环利用,扫码条件苛刻从而使用范围受限。rfid识别由于其感应距离长、抗干扰能力强、数据获取方便快捷等优势而大面积使用。
4.当前在生产线上普遍采用每个工位设置一套rfid读写装置和传感器,来进行台车的定位以及获取生产数据。此方式需安装较多rfid读写装置和传感器,系统复杂、数据流大、成本高、故障率高。
技术实现要素:
5.本发明实施例提供了一种生产线上台车信息获取装置及其工作方法,通过在生产线入口处设置本生产线上台车信息获取装置,在台车进入生产线时识别其产品信息,测量其行走距离,生成一条数据队列,在后续生产过程中能准确计算其在产线上的位置,从而判断到达了哪个工位该进行哪种加工,解决了现有生产线存在的需安装较多rfid读写装置和传感器,导致系统复杂、数据流大、成本高、故障率高的问题。
6.鉴于上述问题,本发明提出的技术方案是:
7.一种生产线上台车信息获取装置,设置在生产线的轨道上,包括:
8.检测组件,所述检测组件包括框架、台车上线传感器、编码器、检测传感器、光栅传感器、控制器和rfid设备,
9.其中,所述框架设置在所述轨道上,所述台车上线传感器、所述编码器、所述检测传感器、所述rfid设备和所述光栅传感器依次设置于所述轨道上,且所述台车上线传感器、所述编码器、所述检测传感器和所述rfid设备按照所述框架的入口至出口的方向依次设置于所述框架的内部,所述光栅传感器位于所述框架的出口处,所述控制器设置于所述轨道的一侧;
10.所述轨道位于所述框架的入口一侧上设置有台车,所述台车包括有托架和滑板,所述台车通过托架与所述滑板连接,所述滑板的底部设置有触发支架。
11.为了更好的实现本发明技术方案,还采用了如下技术措施。
12.进一步的,所述控制器的信号输入端分别与台车上线传感器、所述编码器、所述检测传感器、所述rfid设备和所述光栅传感器的信号输出端通信连接,所述控制的信号输出
端分别与所述编码器和所述rfid设备的信号输入端通信连接。
13.进一步的,所述触发支架靠近所述入口的一侧与所述滑板靠近所述入口的一侧齐平。
14.进一步的,所述触发支架用于触发所述台车上线传感器。
15.进一步的,所述编码器的数量为两个,分布于所述轨道的两侧,所述编码器与所述滑板的边缘接触,用于测量台车移动距离。
16.进一步的,所述台车的数量至少大于一个,且相邻的台车的所述滑板之间紧密贴合。
17.一种生产线上台车信息获取装置的工作方法,包括以下步骤:
18.步骤1,台车随滑板往前移动,进入框架的内部;
19.步骤2,进入框架的内部后,首先滑板底部设置的触发支架与台车上线传感器接触,触发上线传感器,编码器数据清零,接着编码器开始计数,计算当前滑板进入到框架内部的移动距离;
20.步骤3,台车继续往前移动,当台车移动距离达到编码器计数预设值后,检测传感器检测判断是否为空台车;
21.步骤4,若非空台车则触发rfid设备开始读取台车车身上的rfid信息,读取完成后给控制器发送台车的标签数据,若未读取到标签数据则给控制器发送读取失败信息;
22.步骤5,若为空台车则不触发rfid设备读取数据,直接放行台车通过,同时给控制器发送空台车信息;
23.步骤6,控制器在接受rfid设备发送的信息后,结合编码器当时值,进行队列的生成,生成数据队列信息;
24.步骤7,控制器根据生成的数据队列信息获取台车在产线上的具体位置和对应的工位;
25.步骤8,根据台车在产线上的具体位置,得到当前台车与相对应工位的实际距离。
26.进一步的,编码器开始计算当前滑板进入到框架内部的移动距离的起点为台车上线传感器的安装位置。
27.相对于现有技术而言,本发明的有益效果是:通过在生产线入口处设置本生产线上台车信息获取装置,在台车进入生产线时识别其产品信息,测量其行走距离,生成一条数据队列,在后续生产过程中能准确计算其在产线上的位置,从而判断到达了哪个工位该进行哪种加工,解决了需安装较多rfid读写装置和传感器,导致的系统复杂、数据流大、成本高、故障率高的问题。
28.上述说明仅是本发明技术方案的概述,为了能够更清楚了解本发明的技术手段,而可依照说明书的内容予以实施,并且为了让本发明的上述和其它目的、特征和优点能够更明显易懂,以下特举本发明的具体实施方式。
附图说明
29.图1为本发明实施例公开的生产线上台车信息获取装置的结构示意图;
30.图2为图1中a处放大结构示意图;
31.图3为图1中b处放大结构示意图;
32.图4为本发明实施例公开的生产线上台车信息获取装置的通信框图;
33.图5为现有技术中的安装在生产线上的检测装置的结构示意图;
34.图6为本发明实施例公开的安装在生产线上的检测组件的结构示意图;
35.图7为本发明实施例公开的一种生产线上台车信息获取装置的工作方法流程示意图;
36.图8为本发明实施例公开的步骤6中数据队列信息结构示意图。
37.附图标记:1、检测组件;11、框架;111、入口;112、出口;12、台车上线传感器;13、编码器;14、检测传感器;15、光栅传感器;16、控制器;17、rfid设备;2、台车;21、托架;22、滑板;221、触发支架;3、轨道。
具体实施方式
38.下面将结合本发明实施例中的附图,对本发明实施例中的技术方案进行清楚、完整地描述,显然,所描述的实施例仅仅是本发明一部分实施例,而不是全部的实施例。
39.参照附图5所示,生产线的传统方案中有多少采集数据的工位就安装多少台rfid读写装置和传感器来获取台车的位置以及台车的生产数据。
40.参照附图1-6所示,一种生产线上台车信息获取装置,设置在生产线的轨道3上,其包括检测组件1,检测组件1包括框架11、台车上线传感器12、编码器13、检测传感器14、光栅传感器15、控制器16和rfid设备17,框架11设置在轨道3上,台车上线传感器12、编码器13、检测传感器14、rfid设备17和光栅传感器15依次设置于轨道3上,且台车上线传感器12、编码器13、检测传感器14和rfid设备17按照框架11的入口111至出口112的方向依次设置于框架11的内部,光栅传感器15位于框架11的出口112处,控制器16设置于轨道3的一侧,轨道3位于框架11的入口111一侧上设置有台车2,台车2包括有托架21和滑板22,台车2通过托架21与滑板22连接,滑板22的底部设置有触发支架221,通过在生产线入口111处设置本生产线上台车2信息获取装置,在台车2进入生产线时识别其产品信息,测量其行走距离,生成一条数据队列,在后续生产过程中能准确计算其在产线上的位置,从而判断到达了哪个工位该进行哪种加工,解决了现有生产线存在的需安装较多rfid读写装置和传感器,导致系统复杂、数据流大、成本高、故障率高的问题。
41.在本实施例中,分别限定台车上线传感器12的型号为图尔克ni50u-qv40-ap6x2-h1141;编码器13的型号为西克dbs36e-s3gko2000;rfid设备17为:倍加福iuh-f192-v1-fr2、ic-kp2-1hb17-2v1d;检测传感器14的型号为:欧姆龙接近开关,e2b-m30ln30-wz-c1,欧姆龙光电传感器e3jm-10m4-g-nn,其中欧姆龙接近开关的数量为四个,欧姆龙光电传感器的数量为五个,通过传感器支架设置在轨道3上;光栅传感器15的型号为:欧姆龙f3sg-sr;
42.需要说明的是,控制器16的信号输入端分别与台车上线传感器12、编码器13、检测传感器14、rfid设备17和光栅传感器15的信号输出端通信连接,控制的信号输出端分别与编码器13和rfid设备17的信号输入端通信连接,当台车2进入到框架11内部时,编码器13达到预设值,检测传感器14检测到滑板22和台车2时,rfid设备17故障时:rfid设备17开始读取标签数据,在通过编码器13和检测传感器14判断台车2离开读写区域后,rfid设备17识别还未读到标签数据,控制器16发送读取失败信号。
43.本发明实施例还通过以下技术方案进行实现。
44.参照附图1和2所示,在本发明实施例中,触发支架221靠近入口111的一侧与滑板22靠近入口111的一侧齐平,触发支架221用于触发台车上线传感器12。
45.需要说明的是,设置在滑板22底部的触发支架221与台车上线传感器12接触后对台车上线传感器12进行触发,控制器16在判断台车2上线的同时清零编码器13数据、重新开始计数测量、降低编码由于其他原因导致的累计误差。
46.参照附图1和3所示,在本发明实施例中,编码器13的数量为两个,分布于轨道3的两侧,编码器13与滑板22的边缘接触,用于测量台车2移动距离。
47.需要说明的是,编码器13通过测量当前台车2滑板22与上线点距离,控制器16即可分析出台车2滑板22在产线上的位置,当台车上线传感器12触发后,滑板22开始接触到编码器13的计程轮,由摩擦力带动计程轮旋转,从而驱动编码器13旋转计数,为了防止编码器13等设备出现异常,设置了两个编码器13,当两个编码器13数值相差超过预设值时,报警提示故障,同时根据编码器13数据变化情况判断出故障编码器13,将其剔除,启用另一编码器13保证是生产线正常运行,提高系统的稳定性。
48.参照附图5、6和8所示,在本发明实施例中,台车2的数量至少大于一个,且相邻的台车2的滑板22之间紧密贴合。
49.需要说明的是,由于生产线上台车2的滑板22和生产线长度为一定值,同时台车2生产线为推动方式,滑板22间间隙极小可忽略不计,依据编码器13值和队列信息可精准计算出每辆台车2离上线点距离,即实现台车2在线体上的实时定位。
50.滑板22位置计算公式为:sn=l*n d(l:为滑板22长度,n:为队列中的滑板22第几块滑板22,d:为编码器13当前值,以上所有单位都为米)
51.依据此定位即可判断某辆台车2到达或即将到达哪个工位,工位加工数据、加工时间等信息。
52.参照附图1-8所示,本发明还提出一种生产线上台车信息获取装置的工作方法,包括以下步骤:
53.步骤1,台车2随滑板22往前移动,进入框架11的内部;
54.步骤2,进入框架11的内部后,首先滑板22底部设置的触发支架221与台车上线传感器12接触,触发上线传感器,编码器13数据清零,接着编码器13开始计数,计算当前滑板22进入到框架11内部的移动距离,编码器13开始计算当前滑板22进入到框架11内部的移动距离的起点为台车上线传感器12的安装位置;
55.步骤3,台车2继续往前移动,当台车2移动距离达到编码器13计数预设值后,检测传感器14检测判断是否为空台车2;
56.步骤4,若非空台车2则触发rfid设备17开始读取台车2车身上的rfid信息,读取完成后给控制器16发送台车2的标签数据,若未读取到标签数据则给控制器16发送读取失败信息;
57.步骤5,若为空台车2则不触发rfid设备17读取数据,直接放行台车2通过,同时给控制器16发送空台车2信息;
58.步骤6,控制器16在接受rfid设备17发送的信息后,结合编码器13当时值,进行队列的生成,生成数据队列信息;
59.参照附图8所示,需要说明的是,生成的队列信息的结构包括台车2的位置以及台车2的信息,图中,n12345~n12352等为rfid设备17读取的数据,读取的数据中还包括生产数据。
60.步骤7,控制器16根据生成的数据队列信息获取台车2在产线上的具体位置和对应的工位;
61.步骤8,根据台车2在产线上的具体位置,得到当前台车2与相对应工位的实际距离。
62.具体的,在台车2进入到检测组件1中后,通过台车上线传感器12检测到台车2的滑板22,控制器16根据台车上线传感器12输出的信号,将编码器13数据清零,编码器13的计程轮与台车2的滑板22接触,对台车2的移动距离进行检测,当台车2移动距离达到编码器13计数预设值后,触发检测传感器14检测判断是否为空台车2,若为空台车2则不触发rfid设备17读取数据,直接放行台车2通过,同时给控制器16发送空台车2信息,若为非空台车2则触发rfid设备17开始读取台车2车身上的rfid信息,读取完成后给控制器16发送台车2的标签数据,若未读取到标签数据则给控制器16发送读取失败信息,控制器16在接受rfid设备17发送的信息后,结合编码器13当时值,进行队列的生成,生成数据队列信息,通过对数据队列信息进行分析,能获取台车2在产线上的具体位置和对应的工位以及当前台车2与相对应工位的实际距离,在后续生产过程中能准确计算其在产线上的位置,从而判断到达了哪个工位该进行哪种加工,相对于现有技术来说,不需要针对不同的工位安装多个rfid设备17和传感器,整体结构简单,解决了现有生产线存在的需安装较多rfid读写装置和传感器,导致系统复杂、数据流大、成本高、故障率高的问题。
63.需要说明的是,台车上线传感器12、编码器13、检测传感器14、光栅传感器15、控制器16和rfid设备17具体的型号规格需根据该装置的实际规格等进行选型确定,具体选型计算方法采用本领域现有技术,故不再详细赘述。
64.台车上线传感器12、编码器13、检测传感器14、光栅传感器15、控制器16和rfid设备17的供电及其原理对本领域技术人员来说是清楚的,在此不予详细说明。
65.显然,本领域的技术人员可以对本发明进行各种改动和变型而不脱离本发明的精神和范围。这样,倘若本发明的这些修改和变型属于本发明权利要求及其等同技术的范围之内,则本发明也意图包含这些改动和变型在内。
再多了解一些
本文用于创业者技术爱好者查询,仅供学习研究,如用于商业用途,请联系技术所有人。