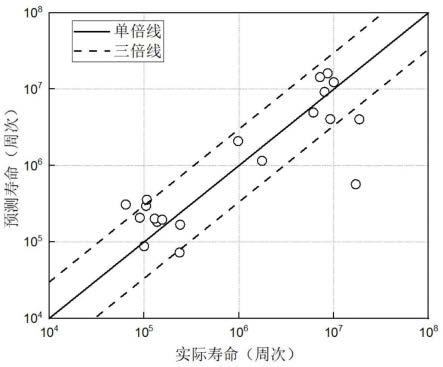
1.本发明属于疲劳寿命预测领域,特别涉及一种镍基单晶高温合金的高周疲劳寿命预测方法。
背景技术:
2.镍基单晶高温合金具有高温强度高、抗氧化性强、抗疲劳性能优异等优点,是先进航空发动机涡轮叶片的主要选用材料。在涡轮叶片服役过程中,高周疲劳是一种常见的失效方式。镍基单晶铸造缺陷处应力集中,疲劳裂纹因此在缺陷萌生。
3.缺陷处应力集中程度不仅与缺陷的尺寸有关,还与缺陷的形状以及到表面位置有关,根据有限元分析结果,对于同一个缺陷,越靠近表面,其应力集中程度越严重。
4.缺陷可以视作一种裂纹。当承受外加载荷时,裂纹尖端会形成塑性区,塑性区的出现降低了材料的刚度,相当于裂纹的增长。因此,在考虑缺陷尺寸对应力集中程度的影响时,需要将塑性区考虑在内。
5.以往的针对含缺陷的镍基单晶高周疲劳寿命预测模型仅仅考虑了缺陷大小的影响,因此,构建一个应力集中参数,该参数体现缺陷的形状、大小、位置以及塑性区对缺陷处应力集中程度的影响,并通过该参数来预测含缺陷的镍基单晶高周疲劳寿命是十分有意义的。
技术实现要素:
6.为实现上述目的,本发明提出一种新的参数d,并将该参数用于寿命预测。该参数综合考虑了缺陷的形状、大小、位置的影响,还考虑了裂纹尖端塑性区的影响。本发明采用下述技术方案:
7.一种镍基单晶高温合金高周疲劳寿命预测方法,寿命预测方法是基于d参数的,d参数的表达式为:
[0008][0009]
式中,l为位置应力强度因子,s为圆度构成形状因子,a为缺陷尺寸,σy为屈服强度,σ为应力。
[0010]
进一步,包括以下步骤:
[0011]
(1)进行高周疲劳试验,获取寿命、应力以及断口;
[0012]
(2)测量裂纹萌生处缺陷的缺陷面积area
defect
、缺陷周长c
defect
、缺陷尺寸a、缺陷到表面距离d
defect
、断口直径d;
[0013]
(3)通过有限元分析,确定位置应力强度因子l与d
defect
/d的关系式:
[0014]
l=f(d
defect
/d);
[0015]
(4)构建圆度构成形状因子s:
[0016][0017]
(5)根据步骤(1)~步骤(4),构建d参数;
[0018]
(6)根据参数d,建立寿命预测模型。
[0019]
进一步,所述寿命预测模型为:
[0020]
lgnf=α-βlg(i)
[0021][0022]
δd=d
max-d
min
式中,nf为疲劳寿命;σ
max
为最大拉应力;σ
min
为最小拉应力;当应力为负时,σ
min
=0;δd
th
表示各试件δd参数值中的最小值,δσ=σ
max-σ
min
,α、β为拟合参数。
[0023]
本发明相对于现有技术的有益效果:
[0024]
针对镍基单晶高周疲劳寿命预测问题,本发明提出了一种新的寿命预测参数d,该参数考虑了缺陷的形状、位置以及塑性区的影响,依据该参数建立寿命预测模型,实现对镍基单晶低周疲劳寿命的有效预测。
附图说明
[0025]
图1为[001]取向dd6镍基单晶高温合金850℃下高周疲劳断口;
[0026]
图2为本发明方法对850℃下dd6镍基单晶高温合金高周疲劳预测寿命与试验寿命比较。
具体实施方式
[0027]
以下将结合具体实施例对本发明的思路、具体结构及产生的技术效果进行清楚、完整地描述,以充分地理解本发明的目的、特征和效果。
[0028]
一种镍基单晶高温合金高周疲劳寿命预测方法,采用下述技术方案:
[0029]
首先,缺陷可以视为一种裂纹,根据断裂力学的原理,裂纹尖端存在塑性区,塑性区的出现降低了材料的刚度,因此需要将其等效为裂纹长度的增长,增长量ry为:
[0030][0031]
其中,σy为屈服强度,k为应力强度因子,其表达式为:
[0032][0033]
其中,y为几何形状因子,σ为应力,a为缺陷尺寸。
[0034]
根据式(1)、(2),可以得出:
[0035][0036]
其次,缺陷附近存在应力集中,且应力集中程度与缺陷的形状有关。因此,采用圆度构成形状因子,如式(4)所示:
[0037][0038]
其中,s为圆度构成形状因子,area
defect
为缺陷面积,c
defect
为缺陷周长。
[0039]
再者,缺陷附近应力集中程度还与缺陷位置有关。以缺陷到表面距离与断口直径之比表示缺陷位置特征,并且通过有限元分析,确定应力集中系数与缺陷到断口边缘距离的数学关系,得到位置应力强度因子l(即缺陷处应力集中系数)的表达式,如式(5)所示:
[0040]
l=f(d
defect
/d)
ꢀꢀꢀ
(5)
[0041]
其中,l为位置应力强度因子,d
defect
为缺陷到表面距离,d为断口直径。
[0042]
将圆度构成形状因子s、位置应力强度因子l引入以代换式(3)中的y,可以得到新的应力强度因子表达式,即参数d:
[0043][0044]
具体实施步骤如下:
[0045]
第一步:设计加工高周疲劳试件,并在不同应力水平下测试,获得试件的疲劳数据与断口。
[0046]
第二步:测量致使裂纹萌生的缺陷的面积area
defect
、周长c
defect
、尺寸a、缺陷到表面距离d
defect
以及断口直径d。这里对于缺陷尺寸的定义为:过缺陷内任意两点的距离的最大值。
[0047]
第三步:通过有限元分析,确定位置应力强度因子l与缺陷到表面距离d
defect
以及断口直径d之间的数学关系式。
[0048]
第四步:按前文所述计算各个试件的参数d。
[0049]
第五步:利用步骤四计算得到的参数d,构建寿命预测模型,从而进行高周疲劳寿命预测。
[0050]
实施例一
[0051]
以850℃[001]取向镍基单晶高温合金dd6为例,本发明的具体应用过程如下:
[0052]
(1)在850℃下,进行[001]取向镍基单晶高温合金dd6疲劳测试,测试载荷分别为900mpa、800mpa、850mpa、680mpa、675mpa、600mpa、580mpa与575mpa,应力比为0.05。测试结果如表1所示。
[0053]
表1疲劳试验结果
[0054][0055]
(2)通过扫描电镜获取断口的宏观图像以及裂纹萌生处缺陷的微观形貌,例如图1。测量不同试件断口源区缺陷的周长、面积、长度、到表面的距离以及断口的直径,测试结果如表2所示。
[0056]
表2断口测量结果
[0057]
[0058][0059]
(3)通过有限元分析,确定位置应力强度因子l与缺陷位置的关系式为:
[0060][0061]
(4)计算出各个试件的参数d。结果如表3所示。
[0062]
表3参数计算结果
[0063][0064]
(5)构建寿命预测模型。
[0065]
基于参数d,这里构建如下的寿命预测模型
[0066]
lgnf=α-βlg(i)
ꢀꢀꢀ
(10)
[0067][0068]
[0069]
式中,nf为疲劳寿命;σ
max
为最大拉应力;σ
min
为最小拉应力;当应力为负时,σ
min
=0;δd
th
表示各试件δd参数值中的最小值,δσ=σ
max-σ
min
,α、β为拟合参数。
[0070]
预测的疲劳寿命与实际疲劳寿命对比如图2所示,可以看到预测寿命基本上在三倍线内,具有较高精度,表明通过d参数,构建寿命预测模型是有效的。
[0071]
以上所述仅为本发明的具体实施方式,并不用于限定本发明的保护范围,凡在本发明的精神和原则之内,所做的任何修改、等同替换、改进等,均应包含在本发明的保护范围之内。
再多了解一些
本文用于企业家、创业者技术爱好者查询,结果仅供参考。