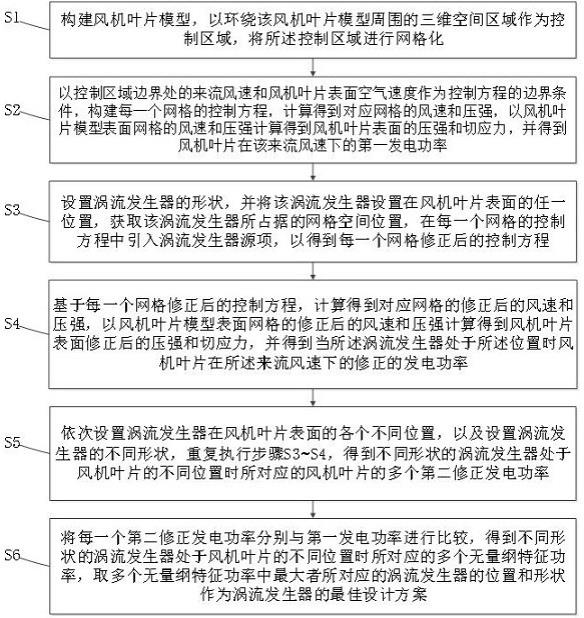
1.本发明涉及风力发电技术领域,尤其涉及一种风机叶片涡流发生器优化方法及系统。
背景技术:
2.近年来,风力发电行业正在快速发展。由于风向与风速的随机性,风机叶片易在短时间内运行在大攻角工况,导致叶片表面出现气流分离现象,同时叶根多采用厚翼型来满足强度要求,在大攻角下其叶根也容易发生气流分离,导致叶片性能下降。对于风机叶片而言,新技术的研发用以提升叶片的气动性能并实现机组发电量的提升,是必需的。在风机叶片的众多提质增效技术中,涡流发生器(vortex generator,简称vg)是相对成熟且广泛应用的技术之一。
3.安装涡流发生器是控制流动分离的一种低成本且有效的方法,最早是针对机翼在大攻角条件控制失速而提高机动性的一个经典设计。在大攻角情况 下,涡流发生器能够大幅度增加翼段的升力系数,减小阻力系数。在风力发电机组上合理安装涡流发生器,能够有效地提高风轮的输出功率和轴向推力,从而能够降低风力发电机组叶片的制造成本,使风能较其他能源产业更具竞争力。涡流发生器自身型阻可能导致翼型总体阻力的增加,影响风电机组的发电量。
4.公开号为cn105556114a的专利给出了完整的涡流发生器参数与安装方案,但是该专利并没有提出针对不通叶片的涡流发生器的具体设计和优化方法,随着叶片设计的不断更新发展,该专利提出的方案已经难以再适应新型叶片上涡流发生器的设计。公开号为cn108280259a的专利,提出了一种基于计算流体力学cfd方法对涡流发生器进行优化设计的方案,该方案需要对涡流发生器的局部结构进行cad建模,使计算资源的消耗很大,对设计进行更新优化的难度较大。公开号cn111859651a的专利,通过使用叶素动量法则对叶片的气动性能进行快速计算和优化设计,但是该方法简化过多,无法准确体现出涡流发生器对叶片性能的具体影响,故优化的效果也不明确。公开号为cn112943565的专利,提出了针对一种具体的涡流发生器形式,即波浪形涡流发生器的优化设计方法,无法针对其他的涡流发生器提出设计优化方案。
技术实现要素:
5.鉴于此,本发明提供一种风机叶片涡流发生器优化方法及系统,使用计算流体力学方法对涡流发生器的具体参数进行分析,从而提供对任意设计参数下的涡流发生器性能评估标准。
6.为实现上述目的,本发明提供一种风机叶片涡流发生器优化方法,所述方法包括步骤:s1、构建风机叶片模型,以环绕该风机叶片模型周围的三维空间区域作为控制区域,将所述控制区域进行网格化;
s2、以控制区域边界处的来流风速和风机叶片表面空气速度作为控制方程的边界条件,构建每一个网格的控制方程,计算得到对应网格的风速和压强,以风机叶片模型表面网格的风速和压强计算得到风机叶片表面的压强和切应力,并得到风机叶片在该来流风速下的第一发电功率;s3、设置涡流发生器的形状,并将该涡流发生器设置在风机叶片表面的任一位置,获取该涡流发生器所占据的网格空间位置,在每一个网格的控制方程中引入涡流发生器源项,以得到每一个网格修正后的控制方程;s4、基于每一个网格修正后的控制方程,计算得到对应网格的修正后的风速和压强,以风机叶片模型表面网格的修正后的风速和压强计算得到风机叶片表面修正后的压强和切应力,并得到当所述涡流发生器处于所述位置时风机叶片在所述来流风速下修正的发电功率;s5、依次设置涡流发生器在风机叶片表面的各个不同位置,以及设置涡流发生器的不同形状,重复执行步骤s3-s4,得到不同形状的涡流发生器处于风机叶片的不同位置时所对应的风机叶片的多个第二修正发电功率;s6、将每一个第二修正发电功率分别与第一发电功率进行比较,得到不同形状的涡流发生器处于风机叶片的不同位置时所对应的多个无量纲特征功率,取多个无量纲特征功率中最大者所对应的涡流发生器的位置和形状作为涡流发生器的最佳设计方案。
7.优选的,所述步骤s1包括:构建风机叶片模型的三维空间坐标体系,以风机轮毂的原点中心为坐标体系的原点,x轴方向垂直于风机叶轮指向风机的下游方向,以重力的方向作为z轴方向,y轴方向与x轴方向和z轴方向垂直。
8.优选的,所述步骤s1包括:所述控制区域是以风机叶片的质量中心为原点,分别向x、y、z轴三个轴方向上扩充6倍叶片弦长距离的三维空间区域。
9.优选的,所述步骤s2包括:以控制区域边界处的来流风速作为控制方程的边界条件: (1);风机叶片表面空气速度作为控制方程的边界条件,风机叶片表面空气速度为: (2);其中,为边界点到轮毂中心的矢量位移,η为来流风速下叶片的叶尖速比,r为叶轮半径;对于控制区域中网格的控制方程为:
ꢀ
(3);其中, (4); (5); (6);其中,t为时间,(u
x
, uy, uz)为网格风速在x,y,z三个轴向上的速度,p为网格的压强,ρ为空气的密度,νa为空气的有效动力学粘度,ν
t
为空气的湍流动力学粘度,gz为z轴方向的重力加速度,u为网格风速的空间导数矩阵。
10.优选的,所述步骤s2包括:根据风速随位置变化的关系,计算速度梯度,构建风机叶片表面切应力τ(u)为:
ꢀꢀ
(7)。
11.优选的,所述步骤s2包括:将切应力τ(u)和压强p沿着叶片表面和叶片表面单位法向量相点乘,基于面积微元da进行面积分,求得叶片所受合力矩tr(u)为: (8);其中,ρ为空气的密度,为边界点到风机轮毂中心的矢量位移;
计算得到风机叶片在该来流风速下的第一发电功率p1为: (9)。
12.优选的,所述步骤s3包括:涡流发生器源项表示为: (10); (11);(12);其中,为模型常数,通常取值为10,为涡流发生器表面的单位法向向量,为涡流发生器表面的单位切向向量,为和垂直的单位法向向量,(w
x
, wy, wz)分别为引入涡流发生器后网格风速在x、y、z三个轴向上的速度,v
cell
为当前涡流发生器的单个网格体积,s
vg
为涡流发生器的表面积,l
vg
和h
vg
分别为涡流发生器的长与高,vs为引入了涡流发生器修正模型的网格的总体积。
13.优选的,所述步骤s3包括:在网格的控制方程中引入涡流发生器源项,以控制区域边界处的来流风速和风机叶片表面空气速度作为控制方程的边界条件,以得到修改正后的控制方程为: (13);其中, (14);
ꢀ
(15)。
14.将解得的w代入公式(8),得到有涡流发生器时的叶片所受合力矩tr(w),基于公式(9)计算得到第二修正发电功率为p2: (16)。
15.优选的,所述步骤s6包括:无量纲特征功率为第二修正发电功率与第一发电功率的比值。
16.为实现上述目的,本发明提供一种风机叶片涡流发生器优化系统,所述系统包括:叶片模型模块,用于构建风机叶片模型,以环绕该风机叶片模型周围的三维空间区域作为控制区域,将所述控制区域进行网格化;控制方程模块,以控制区域边界处的来流风速和风机叶片表面空气速度作为控制方程的边界条件,构建每一个网格的控制方程,计算得到对应网格的风速和压强,以风机叶片模型表面网格的风速和压强计算得到风机叶片表面的压强和切应力,并得到风机叶片在该来流风速下的第一发电功率;修正控制方程模块,用于设置涡流发生器的形状,并将该涡流发生器设置在风机叶片表面的任一位置,获取该涡流发生器所占据的网格空间位置,在每一个网格的控制方程中引入涡流发生器源项,以得到每一个网格修正后的控制方程;修正模块,用于基于每一个网格修正后的控制方程,计算得到对应网格的修正后的风速和压强,以风机叶片模型表面网格的修正后的风速和压强计算得到风机叶片表面修正后的压强和切应力,并得到当所述涡流发生器处于所述位置时风机叶片在所述来流风速下修正的发电功率;重复执行模块,用于依次设置涡流发生器在风机叶片表面的各个不同位置,以及设置涡流发生器的不同形状,重复执行修正控制方程模块和修正模块,得到不同形状的涡流发生器处于风机叶片的不同位置时所对应的风机叶片的多个第二修正发电功率;优化模块,用于将每一个第二修正发电功率分别与第一发电功率进行比较,得到不同形状的涡流发生器处于风机叶片的不同位置时所对应的多个无量纲特征功率,取多个无量纲特征功率中最大者所对应的涡流发生器的位置和形状作为涡流发生器的最佳设计方案。
17.与现有技术相比,本发明提供的一种风机叶片涡流发生器优化方法及系统,所带来的有益效果为:本发明使用计算流体力学cfd方法对涡流发生器的具体参数进行分析,从而提供对任意设计参数下的涡流发生器性能评估标准,以能够判别设计的优劣;使用源项的形式对涡流发生器进行描述,因此不需要对于涡流发生器的具体几何结构进行单独的网格划分,而是在涡流发生器所在位置处的流体控制方程进行修改,从而实现真实涡流发生器对流场的影响,大大提高了计算的效率;可以采用源项对任意形成的涡流发生器进行建
模,大大提高了设计分析的便捷性,不是局限于几种有限的设计方案,如v型、w型波浪型涡流发生器,而是可以快速分析任意形状的涡流发生器设计方案。
附图说明
18.图1是根据本发明的一个实施例的风机叶片涡流发生器优化方法的流程示意图。
19.图2是根据本发明的一具体实施例的涡流发生器模型示意图。
20.图3是根据本发明的一具体实施例的引入涡流发生器源项的网格示意图。
21.图4是根据本发明的一个实施例的风机叶片涡流发生器优化系统的系统示意图。
具体实施方式
22.以下将结合附图所示的具体实施方式对本发明进行详细描述,但这些实施方式并不限制本发明,本领域的普通技术人员根据这些实施方式所做出的结构、方法、或功能上的变换均包含在本发明的保护范围内。
23.如图1所示的本发明的一个实施例,本发明提供一种风机叶片涡流发生器优化方法,所述方法包括步骤:s1、构建风机叶片模型,以环绕该风机叶片模型周围的三维空间区域作为控制区域,将所述控制区域进行网格化;s2、以控制区域边界处的来流风速和风机叶片表面空气速度作为控制方程的边界条件,构建每一个网格的控制方程,计算得到对应网格的风速和压强,以风机叶片模型表面网格的风速和压强计算得到风机叶片表面的压强和切应力,并得到风机叶片在该来流风速下的第一发电功率;s3、设置涡流发生器的形状,并将该涡流发生器设置在风机叶片表面的任一位置,获取该涡流发生器所占据的网格空间位置,在每一个网格的控制方程中引入涡流发生器源项,以得到每一个网格修正后的控制方程;s4、基于每一个网格修正后的控制方程,计算得到对应网格的修正后的风速和压强,以风机叶片模型表面网格的修正后的风速和压强计算得到风机叶片表面修正后的压强和切应力,并得到当所述涡流发生器处于所述位置时风机叶片在所述来流风速下的修正的发电功率;s5、依次设置涡流发生器在风机叶片表面的各个不同位置,以及设置涡流发生器的不同形状,重复执行步骤s3-s4,得到不同形状的涡流发生器处于风机叶片的不同位置时所对应的风机叶片的多个第二修正发电功率;s6、将每一个第二修正发电功率分别与第一发电功率进行比较,得到不同形状的涡流发生器处于风机叶片的不同位置时所对应的多个无量纲特征功率,取多个无量纲特征功率中最大者所对应的涡流发生器的位置和形状作为涡流发生器的最佳设计方案。
24.构建风机叶片模型,以环绕该风机叶片模型周围的三维空间区域作为控制区域。从风机的计算机辅助设计模型中提取风机叶片部分,以该风机叶片部分构建风机叶片模型,构建风机叶片模型的三维空间坐标体系,其中,以风机轮毂的原点中心为坐标体系的原点,x轴方向垂直于风机叶轮指向风机的下游方向,以重力的方向作为z轴方向,y轴方向与x轴方向和z轴方向垂直。以环绕该风机叶片模型周围的三维空间区域作为控制方程计算区
域。作为本发明可实现的技术方式,控制区域是以风机叶片的质量中心为原点,分别向x、y、z轴三个轴方向上扩充6倍叶片弦长距离的三维空间区域。对该控制区域进行网格化,每个网格的尺寸为(sx,sy,sz)。
25.以控制区域边界处的来流风速和风机叶片表面空气速度作为控制方程的边界条件,构建每一个网格的控制方程,计算得到对应网格的风速和压强,以风机叶片模型表面网格的风速和压强计算得到风机叶片表面的压强和切应力,并得到风机叶片在该来流风速下的第一发电功率。
26.以控制区域边界处的来流风速作为控制方程的边界条件: (1);在贴近叶片壁面处,空气的流动速度遵循无滑移边界条件,风机叶片表面空气速度和叶片移动速度一样,风机叶片表面空气速度作为控制方程的边界条件,风机叶片表面空气速度为: (2);其中,为边界点到轮毂中心的矢量位移,η为来流风速下叶片的叶尖速比,r为叶轮半径。本实施方式中,使用来流风速作为边界条件,也可以使用控制区域边界的压强分布作为控制方程的边界条件。
27.对于控制区域中网格的控制方程为:
ꢀꢀ
(3);其中,
ꢀꢀ
(4);
ꢀꢀ
(5);
ꢀꢀ
(6);其中,t为时间,(u
x
, uy, uz)为网格风速在x,y,z三个轴向上的速度,p为网格的压强,网格的压强和三个轴向上的速度分量为需要求解的未知数,ρ为空气的密度,νa为空气的有效动力学粘度,两者均为物性常数,ν
t
为空气的湍流动力学粘度,由湍流模型求解,非本专利发明范畴,不做赘述。gz为z轴方向的重力加速度,即9.8m/s2,u为网格风速的空间导数矩阵。
28.将公式(3)~(6)使用计算流体力学求解器进行求解,可以商用或者开源的流体力学软件,比如使用openfoam作为分析工具,也可以使用其他分析工具,比如fluent,comsol,starccm等。求解后得到每一个网格的风速在x,y,z三个轴向上的速度(u
x
, uy, uz)和压强p,以此得到以风机叶片模型表面网格的风速和压强。
29.以风机叶片模型表面网格的风速和压强计算得到风机叶片表面的压强和切应力。根据风速随位置变化的关系,计算速度梯度,构建风机叶片表面切应力τ(u)为: (7);将切应力τ(u)和压强p沿着叶片表面和叶片表面单位法向量相点乘,基于面积微元da进行面积分,求得叶片所受合力矩t
r(u)
为: (8);其中,ρ为空气的密度,为边界点到风机轮毂中心的矢量位移。
30.计算得到风机叶片在该来流风速下的第一发电功率p1为:
ꢀꢀ
(9)。
31.设置涡流发生器的形状,并将该涡流发生器设置在风机叶片表面的任一位置,获取该涡流发生器所占据的网格空间位置,在每一个网格的控制方程中引入涡流发生器源项,以得到每一个网格修正后的控制方程。如图2所示的涡流发生器模型。在控制方程中通过引入涡流发生器源项,不需要对于涡流发生器的具体几何结构进行单独的网格划分,而是在涡流发生器所在位置处的控制方程进行修改,从而实现真实涡流发生器对流场的影响。图3为引入涡流发生器源项的网格处理示意图。
32.涡流发生器源项表示为: (10);
ꢀꢀ
(11); (12);其中,为模型常数,通常取值为10,为涡流发生器表面的单位法向向量,为涡流发生器表面的单位切向向量,为和垂直的单位法向向量,(w
x
, wy, wz)分别为引入涡流发生器后网格风速在x、y、z三个轴向上的速度,v
cell
为当前涡流发生器的单个网格体积,s
vg
为涡流发生器的表面积,l
vg
和h
vg
分别为涡流发生器的长与高,vs为引入了涡流发生器修正模型的网格的总体积。
33.在网格的控制方程中引入涡流发生器源项,以控制区域边界处的来流风速和风机叶片表面空气速度作为控制方程的边界条件,即公式(1)和(2)作为控制方程的边界条件,以得到修改正后的控制方程为: (13);其中,
ꢀꢀ
(14);
ꢀꢀ
(15)。
34.将解得的w代入公式(8),求得有涡流发生器情况下的叶片所受合力矩tr(w),再基于公式(9),求出此时的风机功率,即第二修正发电功率p2:
ꢀ
(16)。
35.基于每一个网格修正后的控制方程,计算得到对应网格的修正后的风速和压强,以风机叶片模型表面网格的修正后的风速和压强计算得到风机叶片表面修正后的压强和切应力,并得到当所述涡流发生器处于所述位置时风机叶片在所述来流风速下的修正的发电功率。基于修正后的控制方程,过公式(12)求解得到修正后的网格的风速在x,y,z三个轴向上的速度(w
x
, wy, wz)和压强p,通过公式(7)求解得到修正后的切应力,并通过公式(8)和(9)得到风机叶片在该来流风速下修正后的发电功率。
36.依次设置涡流发生器在风机叶片表面的各个不同位置,以及设置涡流发生器的不同形状,重复执行步骤s3-s4,得到不同形状的涡流发生器处于风机叶片的不同位置时所对应的多个风机叶片的第二修正发电功率。涡流发生器的形状和尺寸大小不一样,也会影响方案的优化,本发明不仅考虑了涡流发生器在风机叶片表面的位置,也考虑了涡流发生器的形状,涡流发生器的形状不同,其尺寸大小不同,涡流发生器所占据的网格空间位置也不同,对控制方程的影响也不同。设置涡流发生器的形状,将涡流发生器在风机叶片表面上任意设置任意一个位置。采用源项对任意形状的涡流发生器进行建模,在控制方程中通过引入涡流发生器源项,来描述不同形状的涡流发生器在不同位置时,对网格的风速的影响,可以快速分析任意形状的涡流发生器设计方案。
37.将每一个第二修正发电功率分别与第一发电功率进行比较,得到不同形状的涡流发生器处于风机叶片的不同位置时所对应的多个无量纲特征功率,取多个无量纲特征功率中最大者所对应的涡流发生器的位置和形状作为涡流发生器的最佳设计方案。无量纲特征功率为第二修正发电功率分别与第一发电功率的比值。根据该技术方案,可以实现分析任意形状的涡流发生器的优化设计。
38.如图4所示的本发明的一个实施例,本发明提供一种风机叶片涡流发生器优化系统,所述系统包括:叶片模型模块40,用于构建风机叶片模型,以环绕该风机叶片模型周围的三维空间区域作为控制区域,将所述控制区域进行网格化;控制方程模块41,以控制区域边界处的来流风速和风机叶片表面空气速度作为控制方程的边界条件,构建每一个网格的控制方程,计算得到对应网格的风速和压强,以风机叶片模型表面网格的风速和压强计算得到风机叶片表面的压强和切应力,并得到风机叶片在该来流风速下的第一发电功率;修正控制方程模块42,用于设置涡流发生器的形状,并将该涡流发生器设置在风机叶片表面的任一位置,获取该涡流发生器所占据的网格空间位置,在每一个网格的控制方程中引入涡流发生器源项,以得到每一个网格修正后的控制方程;修正模块43,用于基于每一个网格修正后的控制方程,计算得到对应网格的修正后的风速和压强,以风机叶片模型表面网格的修正后的风速和压强计算得到风机叶片表面修正后的压强和切应力,并得到当所述涡流发生器处于所述位置时风机叶片在所述来流风速下修正的发电功率;重复执行模块44,用于依次设置涡流发生器在风机叶片表面的各个不同位置,以及设置涡流发生器的不同形状,重复执行修正控制方程模块和修正模块,得到不同形状的
涡流发生器处于风机叶片的不同位置时所对应的风机叶片的多个第二修正发电功率;优化模块45,用于将每一个第二修正发电功率分别与第一发电功率进行比较,得到不同形状的涡流发生器处于风机叶片的不同位置时所对应的多个无量纲特征功率,取多个无量纲特征功率中最大者所对应的涡流发生器的位置和形状作为涡流发生器的最佳设计方案。
39.尽管为示例目的,已经公开了本发明的优选实施方式,但是本领域的普通技术人员将意识到,在不脱离由所附的权利要求书公开的本发明的范围和精神的情况下,各种改进、增加以及取代是可能的。
再多了解一些
本文用于企业家、创业者技术爱好者查询,结果仅供参考。