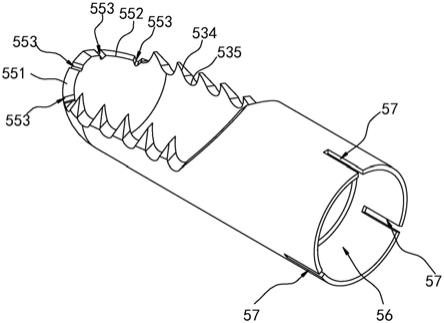
1.本实用新型涉及医疗器械技术领域,特别是涉及一种具有断屑槽的刨削刀具。
背景技术:
2.刨削刀具应用在关节镜手术、耳鼻喉手术中,实现对软组织的切削处理。现有的刨削刀具通常包括外刀管和设置在外刀管内的内刀管,外刀管的远端设置有外切削窗口,外切削窗口的侧边缘设置有若干外刀齿,外刀齿包括外齿尖、外齿侧面和外齿底面,外齿侧面与外刀管的内壁面相交形成外切削刃。内刀管的远端设置有内切削窗口,内切削窗口的侧边缘设置有若干内刀齿,内刀齿包括内齿尖、内齿侧面和内齿底面,内齿侧面与内刀管的外壁面相交形成内切削刃。内刀管相对于外刀管旋转时,外刀齿和内刀齿相对运动将伸入外切削窗口内的软组织切断,并将组织吸入内切削窗口,通过真空系统将碎屑吸出,达到切削目的。
3.现有刨削刀具的外切削窗口的前边缘顶面和内切削窗口的前边缘顶面均为0度后角(即外切削窗口的前边缘顶面与垂直于与其对应的外刀头横截面中心线的参考线的夹角为0度,内切削窗口的前边缘顶面与垂直于与其对应的内刀头横截面中心线的参考线的夹角为0度),刃面为钝口切削,不锋利,导致对刀具前侧的组织切削效果不佳。
技术实现要素:
4.针对上述现有技术现状,本实用新型所要解决的技术问题在于,提供一种对刀具前侧的组织切削效率高的具有断屑槽的刨削刀具。
5.为了解决上述技术问题,本实用新型所提供的一种具有断屑槽的刨削刀具,包括:外刀头,该外刀头上设置有外切削窗口,所述外切削窗口包括周向上的两条外侧边缘以及连接在两条外侧边缘的远端之间的外前边缘;内刀头,该内刀头设置在所述外刀头内且可相对于所述外刀头周向旋转,该内刀头的前端设置有内切削窗口,该内切削窗口包括周向上的两条内侧边缘以及连接在两条内侧边缘的远端之间的内前边缘;所述外前边缘的顶面与所述外刀头的内壁面相交形成外预切削刃,所述外前边缘的顶面设置有至少一个第一断屑槽以将所述外预切削刃分割成至少两段;所述内前边缘的顶面与所述内刀头的外壁面相交形成内预切削刃,所述内前边缘的顶面上设置有至少一个第二断屑槽以将所述内预切削刃分割成至少两段,且所述第一断屑槽与所述第二断屑槽相互错开。
6.上述结构的具有断屑槽的刨削刀具,由于外前边缘的顶面和内前边缘的顶面分别设置有第一断屑槽和第二断屑槽,第一断屑槽和第二断屑槽分别将外预切削刃和内预切削刃分割成至少两段,可以将刀具前侧的组织切割成多段,减小组织体积,以方便吸入内切削窗口内。
7.在一个实施例中,所述外前边缘的顶面以外倾角α3向外侧倾斜,所述外倾角α3为过所述外预切削刃上任意一点w3的法向截面s5-s5与所述外前边缘的顶面的交线w3g3,与位于所述法向截面s5-s5内且垂直于过点w3的切线的参考线w3x5之间的夹角;所述内前边
缘的顶面以内倾角β3向内侧倾斜,所述内倾角β3为过所述内预切削刃上任意一点n3的法向截面s6-s6与所述内前边缘的顶面的交线n3h3,与位于所述法向截面s6-s6内且垂直于过点n3的切线的参考线n3x6之间的夹角。
8.在一个实施例中,所述第一断屑槽为沿所述外前边缘的顶面的宽度方向贯通的通槽,所述第二断屑槽为沿所述内前边缘的顶面的宽度方向贯通的通槽。
9.在一个实施例中,所述第一断屑槽的横截面为上宽下窄的v形,所述第二断屑槽为上宽下窄的v形。
10.在一个实施例中,所述第一断屑槽位于所述外刀头的轴线的一侧或两侧,所述第二断屑槽位于所述内刀头的轴线的一侧或两侧。
11.在一个实施例中,所述第一断屑槽的底面相对于垂直于与其对应的所述外刀头横截面的中心线的参考线向外侧倾斜,所述第二断屑槽的底面相对于垂直于与其对应的所述内刀头横截面的中心线的参考线向内侧倾斜。
12.在一个实施例中,所述外前边缘的顶面为向外凸出的凸形,所述内前边缘的顶面为向内凹陷的凹形。
13.在一个实施例中,所述外前边缘的顶面为倒“v”形,所述内前边缘的顶面为“v”形。
14.在一个实施例中,两条所述外侧边缘中的至少一条包括多个外刀齿,所述外刀齿包括第一齿尖、两第一齿侧面以及第一齿底面,所述第一齿侧面与所述外刀头的内壁面相交形成第一外切削刃;两条所述内侧边缘中的至少一条包括多个内刀齿,所述内刀齿包括第二齿尖、两第二齿侧面和第二齿侧面,所述第二齿侧面与所述内刀头的外壁面相交形成第一内切削刃。
15.在一个实施例中,同一所述外侧边缘上的所述第一齿尖与所述外刀头的轴线的距离沿从所述外刀头近端至远端方向逐渐减小,同一所述内侧边缘上的所述第二齿尖与所述内刀头的轴线的距离沿从所述内刀头近端至远端方向逐渐减小。
16.本实用新型附加技术特征所具有的有益效果将在本说明书具体实施方式部分进行说明。
附图说明
17.图1为本实用新型实施例中的具有断屑槽的刨削刀具的立体图;
18.图2为图1中所示具有断屑槽的刨削刀具的外刀管组件的立体图;
19.图3为图2中i处的局部放大示意图;
20.图4和图5为图2中所示外刀管组件的外刀头的立体图,其中,图4为从前往后看的立体图,图5为从后往前看的立体图;
21.图6为图2中所示外刀管组件的外刀头的主视图;
22.图7为图2中所示外刀管组件的外刀头的俯视图;
23.图8为图2中所示外刀管组件的外刀头的左视图;
24.图9为图1中所示具有断屑槽的刨削刀具的内刀管组件的立体图;
25.图10为图9中p处的局部放大示意图;
26.图11和图12为图9中所示内刀管组件的内刀头的立体图,其中,图11为从前往后看的立体图,图12为从后往前看的立体图;
27.图13为图10中所示内刀管组件的内刀头的主视图;
28.图14为图10中所示内刀管组件的内刀头的俯视图;
29.图15为图10中所示内刀管组件的内刀头的左视图;
30.图16为外刀头与内刀头的配合示意图,示出的是内刀头相对于外刀头逆时针旋转100度时的状态;
31.图17为沿图16中l-l线的剖视图;
32.图18为沿图16中m-m线的剖视图;
33.图19为沿图16中n-n线的剖视图;
34.图20为外刀头与内刀头的配合示意图,示出的是内刀头相对于外刀头逆时针旋转180度时的状态;
35.图21为图20中o-o线的剖视图。
36.附图标记说明:10、刨削刀具;20、外刀管组件;30、座体;40、外刀杆;41、第一连接头;50、外刀头;51、外切削窗口;52、外侧边缘;53、外刀齿;531、第一齿尖;532、第一齿侧面;533、第一齿底面;534、外切削侧刃;535、外切削底刃;536、齿背面;54、内壁面;55、外前边缘;551、外前边缘的顶面;552、外预切削刃;553、第一断屑槽;56、第一安装孔;57、第一焊接槽;60、内刀管组件;70、连接件;80、内刀杆;81、第二安装孔;82、第二焊接槽;90、内刀头;91、内切削窗口;92、内侧边缘;93、内刀齿;931、第二齿尖;932、第二齿侧面;933、第二齿底面;934、内切削侧刃;935、内切削底刃;94、外壁面;95、内前边缘;951、内前边缘的顶面;952、内预切削刃;953、第二断屑槽;96、第二连接头。
具体实施方式
37.下面参考附图并结合实施例对本实用新型进行详细说明。需要说明的是,在不冲突的情况下,以下各实施例及实施例中的特征可以相互组合。
38.在本文中,所涉及的前、后、上、下等方位词是以附图中零部件位于图中以及零部件相互之间的位置来定义的,只是为了表达技术方案的清楚及方便。应当理解,所述方位词的使用不应限制本技术请求保护的范围。
39.如图1所示,本实用新型其中一个实施例中的具有断屑槽的刨削刀具10包括外刀管组件20和内刀管组件60,内刀管组件60设置在外刀管组件20内并可以相对于外刀管组件20周向旋转。
40.图2所示为外刀管组件20的立体图,如图所示,外刀管组件20包括座体30和外刀管,座体30为筒状结构,座体30的前端设置有固定孔。外刀管靠近座体30的一端为近端,另一端为远端,外刀管的近端插入固定在座体30的固定孔内,外刀管包括管状的外刀杆40和与外刀杆40远端连接的外刀头50。
41.如图2、3所示,作为示例的外刀杆40和外刀头50为分体式结构,外刀杆40的远端设置有台阶状第一连接头41,外刀头50的近端设置有与第一连接头41配合的台阶状的第一安装孔56,第一连接头41插入第一安装孔56内,两者通过焊接固定。为了加强外刀头50与外刀杆40焊接的稳定性,在外刀头50的近端上开设有至少一条沿轴向方向延伸的第一焊接槽57,外刀头50的近端的端面以及第一焊接槽57与第一连接头41焊接,这样,外刀头50与外刀杆40同时在圆周方向和轴向方向上焊接,增加了连接强度。作为示例的第一焊接槽57为三
条,三条第一焊接槽57沿圆周方向均布。作为替代方案,第一连接头41与第一安装孔56的位置对调,即第一连接头41设置在外刀头50的近端,第一安装孔56设置在外刀杆40的远端。
42.如图4、5所示,外刀头50的靠近远端的管壁上开设置有外切削窗口51,外切削窗口51包括位于外刀头50周向上的两外侧边缘52和连接在外侧边缘52远端之间的外前边缘55,两外侧边缘52中的至少一外侧边缘52为锯齿状结构,该外侧边缘52包括沿外刀头50轴向排列的若干外刀齿53,外刀齿53包括第一齿尖531、位于第一齿尖531在外刀头50轴向上两侧的两第一齿侧面532以及过渡连接在相邻两个外刀齿53的第一齿侧面532底端之间的第一齿底面533,第一齿侧面532与外刀头50的内壁面54相交形成外切削侧刃534,第一齿底面533与外刀头50的内壁面54相交形成外切削底刃535。本实施例中,两外侧边缘52均为锯齿状结构,这样,内刀头90沿正反两个方向旋转均可以切割。
43.如图6所示,第一齿底面533以第一外倾角α1向外侧倾斜,第一外倾角α1为过外切削底刃535上任意一点w1的第一法向截面s1-s1与第一齿底面的交线w1g1,与位于第一法向截面s1-s1内且垂直于过点w1的切线的第一参考线w1x1之间的夹角。由于外切削底刃535包括第一外倾角α1,从而形成锋利的切削刃口,该刃口除在径向具有切削性能之外,在任意一段刃形轮廓的垂直方向均有锋利刃口特性和切削能力,整个曲线刃口轮廓无切削死角。
44.如图6所示,第一齿侧面以第二外倾角α2向外侧倾斜,第二外倾角α2为过外切削侧刃534上任意一点w2的第三法向截面s3-s3与第一齿侧面的交线w2g2,与位于第三法向截面s3-s3内且垂直于过点w2的切线的第三参考线w2x3之间的夹角。由于外切削侧刃534包括第二外倾角α2,从而形成锋利的切削刃口,该刃口除在径向具有切削性能之外,在任意一段刃形轮廓的垂直方向均有锋利刃口特性和切削能力,整个曲线刃口轮廓无切削死角。第二外倾角α2与第一外倾角α1相同或者不同。
45.如图4所示,作为示例的外刀齿53为三角形齿,外刀齿53的在外刀头50轴向上的两侧面为第一齿侧面532,两第一齿侧面532的顶端相交形成第一齿尖531,第一齿尖531向外侧倾斜。作为示例的外刀齿53还包括背对外刀头50的内壁面54的齿背面536,且齿背面536的顶端相对于底端向外侧倾斜,使在外刀齿53背部形成铲背角,以增加其锋利性,并且使位于外刀齿53外侧的组织更容易被刀具内的负压吸入刃部从而被切削,提升刨削效率。
46.如图6所示,作为示例,同一外侧边缘52上的第一齿尖531与外刀头50的中心线α1的距离沿从外刀头50近端至远端方向逐渐减小,即同一外侧边缘52上的第一齿尖531的连线l1相对于外刀管的中心线α1以倾角γ1向前倾斜,可有效保障外刀头50的强度在切削过程中承受更大的扭矩而靠近尾端处不断裂,同时也形成沿轴向逐渐切入组织的剪切运动效应,使切断组织更省力、切削效率更高。
47.参见图4、5,作为示例的外前边缘的顶面551与外刀头50的内壁面54相交形成外预切削刃552,外预切削刃552与内刀头90上的内预切削刃952配合将位于刀具前侧的组织切断。
48.如图7所示,外前边缘的顶面551以第三外倾角α3向外侧倾斜,第三外倾角α3为过外预切削刃552上任意一点w3的第五法向截面s5-s5与外前边缘的顶面551的交线w3g3,与位于第五法向截面s5-s5内且垂直于过点w3的切线的第五参考线w3x5之间的夹角。由于外预切削刃552包括第三外倾角α3,从而形成锋利的切削刃口,该刃口除在径向具有切削性能之外,在任意一段刃形轮廓的垂直方向均有锋利刃口特性和切削能力,整个曲线刃口轮廓
无切削死角。第三外倾角α3与第一外倾角α1相同或者不同。
49.进一步参见图4、5、8,作为示例的外前边缘的顶面551为向外凸出的凸形,本实施例中外前边缘的顶面551为倒“v”形,使得外预切削刃552在外刀头50端部形成高低差,形成端部的剪切效应,便于端部预切段切削。优选地,外前边缘的顶面551设置有至少一个第一断屑槽553,第一断屑槽553用于将外预切削刃552分割成至少两段,这样,可以将刀具前侧的组织切割成多段,减小组织体积,以方便吸入内切削窗口91内。作为示例,第一断屑槽553为四个,四个第一断屑槽553对称地布置在外刀头50的轴线的两侧。作为示例,第一断屑槽553为沿外前边缘的顶面551的宽度方向贯通的通槽,第一断屑槽553的横截面为上宽下窄的“v”形。作为示例的第一断屑槽553的底面的外端相对于内端向外侧倾斜。
50.如图9所示,作为示例的内刀管组件60包括内刀管和连接件70,内刀管靠近座体30的一端为近端,另一端为远端,内刀管的近端与连接件70连接,连接件70用于与刀具驱动装置(图中未示出)连接,刀具驱动装置通过连接件70带动内刀管旋转。内刀管包括中空的内刀杆80和与内刀杆80的远端连接的内刀头90。
51.如图9、10所示,作为示例的内刀杆80和内刀头90为分体式结构,内刀杆80的远端设置有台阶状第二安装孔81,内刀头90的近端设置有与第二安装孔81配合的第二连接头96,第二连接头96插入第二安装孔81内,两者通过焊接固定。为了加强内刀头90与内刀杆80焊接的稳定性,在内刀杆80的远端上开设有至少一条沿轴向方向延伸的第二焊接槽82,内刀杆80的远端的端面以及第二焊接槽82与第二连接头96焊接,这样,内刀杆80和内刀头90同时在圆周方向和轴向方向焊接,增加了连接强度。作为示例的第二焊接槽82为三条,三条第二焊接槽82沿圆周方向均布。为了增加刀具整体强度,内刀杆80的远端的端面和外刀头50的近端的端面的位置在轴向上相互错开,第二焊接槽82和第一焊接槽57的位置在圆周方向上相互错开。作为替代方案,第二连接头96与第二安装孔81的位置对调,即第二连接头96设置在内刀杆80的远端,第二安装孔81设置在内刀头90的近端。
52.如图11、12所示,内刀头90的靠近远端的管壁上开设置有内切削窗口91,内切削窗口91包括位于内刀头90周向上的两内侧边缘92和连接在内侧边缘92远端之间的内前边缘95,两内侧边缘92中的至少一内侧边缘92为锯齿状结构,该内侧边缘92包括沿内刀头90轴向排列的若干内刀齿93,内刀齿93包括第二齿尖931、位于第二齿尖931在内刀头90轴向两侧的两第二齿侧面932以及过渡连接在相邻两内刀齿93的第二齿侧面932底端之间的第二齿底面933,第二齿侧面932与内刀头90的外壁面94相交形成内切削侧刃934,第二齿底面933与内刀头90的外壁面94相交形成内切削底刃935。本实施例中,两内侧边缘92均为锯齿状结构,这样,内刀头90沿正反两个方向旋转均可以切割。
53.如图13所示,第二齿底面933以第一内倾角β1向内侧倾斜,第一内倾角β1为过内切削底刃935上任意一点n1的第二法向截面s2-s2与第二齿底面的交线n1h1,与位于第二法向截面s2-s2内且垂直于过点n1的切线的第二参考线n1x2之间的夹角。由于第二齿底面933以第一内倾角β1向内侧倾斜,从而形成锋利的切削刃口,该刃口除在径向具有切削性能之外,在任意一段刃形轮廓的垂直方向均有锋利刃口特性和切削能力,整个曲线刃口轮廓无切削死角。
54.如图13,第二齿侧面932以第二内倾角β2向内侧倾斜,第二内倾角β2为过内切削侧刃934上任意一点n2的第四法向截面s4-s4与第二齿侧面932的交线n2h2,与位于第四法向
截面s4-s4内且垂直于过点n2的切线的第四参考线n2x4之间的夹角。由于第二齿侧面以第二内倾角β2向内侧倾斜,从而形成锋利的切削刃口,该刃口除在径向具有切削性能之外,在任意一段刃形轮廓的垂直方向均有锋利刃口特性和切削能力,整个曲线刃口轮廓无切削死角。β2与β1相同或者不相同。
55.如图11、12所示,作为示例,本实施例中的内刀齿93为三角形齿,内刀齿93的在内刀头90轴向上的两侧面为第二齿侧面932,两第二齿侧面932的顶端相交形成第二齿尖931,第二齿尖931向外侧倾斜。
56.如图13所示,作为示例,同一内侧边缘92上的第二齿尖931与内刀头90的中心线a2的距离沿从内刀头90近端至远端方向逐渐减小,即同一内侧边缘92上的第二齿尖931的连线l2相对于内刀管的中心线a2以倾角γ2向前倾斜,可有效保障内刀头90的强度在切削过程中承受更大的扭矩而靠近尾端处不断裂,同时也形成沿轴向逐渐切入组织的剪切运动效应,使切断组织更省力、切削效率更高。
57.参见图11、12,作为示例的内前边缘的顶面951与内刀头90的外壁面94相交形成内预切削刃952,内预切削刃952与外刀头50上的外预切削刃552配合将位于刀具前侧的组织切断。
58.如图14所示,内前边缘的顶面951以第三内倾角β3向内侧倾斜,第三内倾角β3为过内预切削刃952上任意一点n3的第六法向截面s6-s6与内前边缘的顶面的交线n3h3,与位于第六法向截面s6-s6内且垂直于过点n3的切线的第六参考线n3x6之间的夹角。由于内前边缘的顶面以第三内倾角β3向内侧倾斜,从而形成锋利的切削刃口,该刃口除在径向具有切削性能之外,在任意一段刃形轮廓的垂直方向均有锋利刃口特性和切削能力,整个曲线刃口轮廓无切削死角。β3与β1相同或者不相同。
59.进一步参见图11、12、15,作为示例的内前边缘的顶面951为向内凹陷的凹形,本实施例中内前边缘的顶面951为“v”形,使得内预切削刃952在内刀头90端部形成高低差,形成端部的剪切效应,便于端部预切段切削。优选地,内前边缘的顶面951设置有至少一个第二断屑槽953,第二断屑槽953用于将内预切削刃952分割成至少两段,这样,可以将刀具前侧的组织切割成多段,减小组织体积,以方便吸入内切削窗口91内。作为示例,第二断屑槽953为两个,两个第二断屑槽953对称地布置在内刀头90的轴线的两侧。作为示例,第二断屑槽953为沿内前边缘的顶面951的宽度方向贯通的通槽,第二断屑槽953的横截面为上宽下窄的v形。第二断屑槽953的底面的内端相对于外端向内侧倾斜。
60.工作时,刀具驱动装置驱动内刀管组件60相对于外刀管组件20顺时针或者逆时针旋转。图16-19所示为内刀管组件60相对于外刀管组件20逆时针旋转100度时的切削示意图,如图所示,外刀齿53与内刀齿93在轴向上错开布置,即外刀齿53的第一齿尖531与内刀齿93的第二齿底面933相对,外刀齿53的第一齿底面533与内刀齿93的第二齿尖931相对。由于第一齿尖531、第一齿侧面532和第一齿底面533外倾,第二齿尖931、第二齿侧面932和第二齿底面933内倾,使内刀头90在往复刨削过程中外刀齿53和内刀齿93交错时形成锋利的剪切刃口,即形成在内刀齿93、外刀齿53的各处配合处形成类似于剪刀状的剪切结构,便于高效剪切组织。而且,由于第一齿底面533向外侧倾斜形成具有第一外倾角α1的锋利的外切削底刃535,第二齿底面933向内侧倾斜形成具有第一内倾角β1的锋利的内切削底刃935,这样当切削筋膜等高弹性组织时,内刀齿93的第一齿尖开始切入并抓取组织,继续旋转时被
抓取的组织在两个刀齿之间被挤压,当旋转至齿底时利用外切削底刃535和内切削底刃935完成最后切削并分离组织,使组织更容易被刀具内的负压吸入刃部从而被切削,提升刨削效率。
61.如图16所示,由于所有第一齿尖531相对于外刀管的中心线α1以倾角γ1向前倾斜,所有第二齿尖931的连线l2相对于内刀管的中心线a2以倾角γ2向前倾斜,使得除了在内刀头90旋转方向上形成剪切之外,还在轴向方向上形成剪切,即形成类似剪刀的双剪切效果,使切削组织更加省力,切削效率更高。
62.如图20、21所示,由于外前边缘的顶面551与外刀头50的内壁面54相交形成具有第三外倾角α3的外预切削刃552,内前边缘的顶面951与内刀头90的外壁面94相交形成具有第三内倾角β3的内预切削刃952,增加了外预切削刃552和内预切削刃952的锋利性,提高了切削效率。利用外预切削刃552和内预切削刃952将刀具前侧的组织切断并被吸入内切削窗口91内。而且,由于外前边缘的顶面551设置有第一断屑槽553,内前边缘的顶面951设置有至少一个第二断屑槽953,可以将组织切割成多段,减小组织的体积,降低内刀头的负载,有利于提高切割效率。
63.以上实施例仅表达了本实用新型的几种实施方式,其描述较为具体和详细,但并不能因此而理解为对本实用新型专利范围的限制。应当指出的是,对于本领域的普通技术人员来说,在不脱离本实用新型构思的前提下,还可以做出若干变形和改进,这些都属于本实用新型的保护范围。
再多了解一些
本文用于企业家、创业者技术爱好者查询,结果仅供参考。