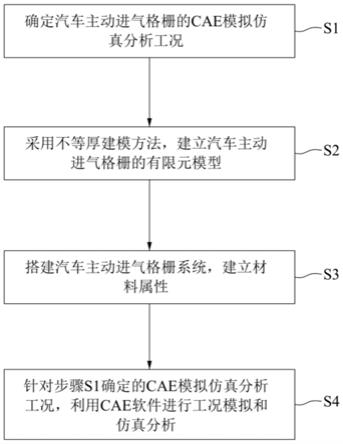
一种汽车主动进气格栅的cae仿真模拟方法
技术领域
1.本发明涉及汽车设计技术领域,尤其涉及一种汽车主动进气格栅的cae仿真模拟方法。
背景技术:
2.汽车主动进气格栅位于汽车车头的正前方,主要作用是为发动机提供进气及散热两大功能。汽车主动进气格栅能够通过改变进气格栅的开闭来控制进气量及风阻,从而提高燃油经济性,并使发动机快速达到较佳工作温度。
3.在设计汽车主动进气格栅时,汽车主动进气格栅的材料以塑料材料为主,目前其性能主要是通过试验进行验证。在试验验证汽车主动进气格栅的性能时,往往需要设计生产模具、制造样件并在车体上进行试验。若试验不合格,需反复修改设计方案并不断进行试验验证。由于调整模具的周期长,导致原料成本和时间成本都较高。
4.仿真分析相比试验验证,成本大大降低。但是现有技术中尚未利用仿真软件对汽车主动进气格栅的性能进行仿真分析。
技术实现要素:
5.本发明的目的在于提供一种汽车主动进气格栅的cae仿真模拟方法,以解决现有技术中存在的在设计阶段对汽车主动进气格栅的性能通过试验验证而导致的研发周期长、研发成本高的技术问题。
6.如上构思,本发明所采用的技术方案是:
7.一种汽车主动进气格栅的cae仿真模拟方法,包括以下步骤:
8.s1、确定汽车主动进气格栅的cae模拟仿真分析工况;
9.s2、采用不等厚建模方法,建立汽车主动进气格栅的有限元模型;
10.s3、搭建汽车主动进气格栅系统,建立材料属性;
11.s4、针对步骤s1确定的cae模拟仿真分析工况,利用cae软件进行工况模拟和仿真分析。
12.可选地,在步骤s1中,cae模拟仿真分析工况包括模态工况、刚度工况、强度工况和风载动压载荷工况。
13.可选地,步骤s4包括:
14.s41、模态工况模拟仿真分析:模拟汽车主动进气格栅系统安装在实车状态,汽车主动进气格栅的有限元模型与车身连接的位置约束全部自由度,利用hypermesh软件中的nastran模块,控制卡片采用sol103进行设置,计算汽车主动进气格栅的有限元模型的约束模态,要求一阶模态≥35hz;
15.s42、刚度工况模拟仿真分析:利用hypermesh软件中的nastran模块,控制卡片采用sol101进行设置,在汽车主动进气格栅的骨架的前端中间位置,沿z方向加载500n的载荷,计算汽车主动进气格栅的有限元模型的最大变形,要求汽车主动进气格栅的最大变形
不超过2mm;
16.s43、强度工况模拟仿真分析:利用hypermesh软件中的nastran模块,控制卡片采用sol101进行设置,在汽车主动进气格栅的骨架的前端中间位置,沿z方向加载2000n的载荷,计算汽车主动进气格栅的有限元模型的最大应力,要求汽车主动进气格栅的最大应力<许用应力;
17.s44、风载动压载荷工况模拟仿真分析:对汽车主动进气格栅的叶片进行动压变形量模拟仿真分析,利用hypermesh软件中的nastran模块,控制卡片采用sol101进行设置,计算得到动压值,对汽车主动进气格栅的叶片施加计算得到的动压值,计算最高车速情况下汽车主动进气格栅的叶片中心的变形量,要求最高车速情况下,汽车主动进气格栅的叶片中心的最大变形量不超过4mm。
18.可选地,步骤s41还包括:
19.若计算所得的一阶模态不满足要求,则对汽车主动进气格栅的有限元模型进行结构优化,优化完成后再次进行模态工况模拟仿真分析,直至计算所得的一阶模态满足要求。
20.可选地,步骤s42还包括:
21.若汽车主动进气格栅的最大变形不满足要求,则对汽车主动进气格栅的有限元模型进行结构优化,优化完成后再次进行刚度工况模拟仿真分析,直至汽车主动进气格栅的最大变形满足要求。
22.可选地,步骤s43还包括:
23.若汽车主动进气格栅的最大应力不满足要求,则对汽车主动进气格栅的有限元模型进行结构优化,优化完成后再次进行强度工况模拟仿真分析,直至汽车主动进气格栅的最大应力满足要求。
24.可选地,步骤s44还包括:
25.若汽车主动进气格栅的叶片中心的最大变形量不满足要求,则对汽车主动进气格栅的有限元模型进行结构优化,优化完成后再次进行风载动压载荷工况模拟仿真分析,直至汽车主动进气格栅的叶片中心的最大变形量满足要求。
26.可选地,对汽车主动进气格栅的有限元模型进行结构优化包括:
27.调整汽车主动进气格栅的有限元模型的加强筋的布置和加强筋的料厚。
28.可选地,在步骤s2中,选用中面网格shell section单元,采用不等厚建模方法,在不同的厚度区域赋予不同的料厚。
29.可选地,在步骤s2中,汽车主动进气格栅的有限元模型的连接支架与骨架之间的螺栓采用rbe2单元模拟连接。
30.本发明提出的汽车主动进气格栅的cae仿真模拟方法能够对汽车主动进气格栅的设计阶段进行指导。在汽车主动进气格栅的设计阶段,利用cae软件对汽车主动进气格栅进行工况模拟和仿真分析,能够确定所设计的汽车主动进气格栅的性能,提高设计效率和设计良品率,保证汽车主动进气格栅在设计开发阶段达到合格要求。相比现有技术中通过试验对所设计的汽车主动进气格栅的性能进行验证,汽车主动进气格栅的cae仿真模拟方法效率高而成本低,能够大大缩减设计阶段所需的时间成本和物料成本。采用cae软件进行建模仿真,能够保证建模精度,避免开发试制件出现问题而影响试验结果,缩短产品开发周期,降低开发成本。
附图说明
31.图1是本发明实施例提供的汽车主动进气格栅的cae仿真模拟方法的流程题;
32.图2是本发明实施例提供的汽车主动进气格栅的结构示意图。
33.图中:
34.1、骨架;11、加强筋;2、叶片;3、连接支架。
具体实施方式
35.为使本发明解决的技术问题、采用的技术方案和达到的技术效果更加清楚,下面结合附图并通过具体实施方式来进一步说明本发明的技术方案。可以理解的是,此处所描述的具体实施例仅仅用于解释本发明,而非对本发明的限定。另外还需要说明的是,为了便于描述,附图中仅示出了与本发明相关的部分而非全部。
36.参见图1和图2,本实施例提供一种汽车主动进气格栅的cae仿真模拟方法,其能够在汽车主动进气格栅的设计阶段对汽车主动进气格栅进行性能验证,提高设计效率和设计的良品率。
37.具体地,本实施例中,汽车主动进气格栅的cae仿真模拟方法包括以下步骤:
38.s1、确定汽车主动进气格栅的cae模拟仿真分析工况;
39.s2、采用不等厚建模方法,建立汽车主动进气格栅的有限元模型;
40.s3、搭建汽车主动进气格栅系统,建立材料属性;
41.s4、针对步骤s1确定的cae模拟仿真分析工况,利用cae软件进行工况模拟和仿真分析。
42.本实施例作用,在汽车主动进气格栅的设计阶段,利用cae软件对汽车主动进气格栅进行工况模拟和仿真分析,能够确定所设计的汽车主动进气格栅的性能,提高设计效率和设计良品率,保证汽车主动进气格栅在设计开发阶段达到合格要求。相比现有技术中通过试验对所设计的汽车主动进气格栅的性能进行验证,汽车主动进气格栅的cae仿真模拟方法效率高而成本低,能够大大缩减设计阶段所需的时间成本和物料成本。采用cae软件进行建模仿真,能够保证建模精度,避免开发试制件出现问题而影响试验结果,缩短产品开发周期,降低开发成本。
43.具体地,本实施例中,汽车主动进气格栅的有限元模型包括骨架1、设于骨架1上的叶片2和传动条,叶片2与传动条连接,传动条能够带动叶片2运动以打开或者关闭叶片2,骨架1上分布有加强筋11,骨架1的相对两侧均设置有连接支架3。具体地,汽车主动进气格栅包括多个叶片2,多个叶片2中既有主动叶片,又有被动叶片。
44.具体地,本实施例中,在步骤s1中,cae模拟仿真分析工况包括模态工况、刚度工况、强度工况和风载动压载荷工况。
45.在整车结构上,汽车主动进气格栅位于车头的正前方,主要为发动机提供进气并辅助发动机进行散热。在正常安装情况下,汽车主动进气格栅应当具有较高的抵抗变形能力。同时汽车主动进气格栅需要在极限受载情况下,保证其受到的最大应力不应该超过许用应力。当车辆高速行驶时,形成强大的气流,风阻成为燃油消耗的主要元凶,汽车主动进气格栅的叶片2进行适当的关闭,从而提升车辆的稳定性及燃油经济性。此时汽车主动进气格栅的叶片2承受比较大的风压,而汽车主动进气格栅主要为塑料件,需要保证汽车主动进
气格栅的叶片中心有较好的抵抗变形的能力,使汽车主动进气格栅达到最好的工作状态以及避免汽车主动进气格栅破坏。
46.因此,本实施例中,选择了对汽车主动进气格栅的模态工况、刚度工况、强度工况和风载动压载荷工况进行仿真分析。
47.具体地,本实施例中,汽车主动进气格栅的有限元模型为有限元网格模型。在步骤s2中,由于汽车主动进气格栅的截面厚度分布不均匀,选用中面网格shell section单元,采用不等厚建模方法,在不同的厚度区域赋予不同的料厚,以使得仿真结果更加精确。可选地,骨架1的料厚为3mm,分布于骨架1上的加强筋11的料厚为2mm,骨架1上凸起的凸台料厚为1.8mm,叶片2和传动条的连接处料厚为3.5mm。
48.由于骨架1上分布的加强筋11的数量较多,为保证仿真结果的准确性,所有的加强筋11在有限元网格模型中均需要保留,保留骨架1上的凸台结构,高度超过0.5mm的凸台要减少网格尺寸,倒角网格过渡平滑。
49.由于汽车主动进气格栅的材质为塑料材质,且其界面厚度分布不均匀,采用不等厚建模方法,建立的有限元模型更贴合实际结构,从而使得仿真结果更加精确。
50.在步骤s2中,汽车主动进气格栅的有限元模型的连接支架3与骨架1之间的螺栓采用rbe2单元模拟连接。骨架1与凸台之间及骨架1和加强筋11之间采用节点耦合的连接形式,并分别设置相对应的料厚。
51.具体地,在步骤s3中,搭建汽车主动进气格栅系统后,建立材料属性。在建立材料属性后,赋予材料相应的密度、弹性模量和泊松比。骨架1、设于骨架1上的叶片2和传动条的材质为塑料材质,连接支架3的材料为金属。
52.在搭建汽车主动进气格栅系统时,模拟汽车主动进气格栅的有限元模型安装在实车状态,连接支架3与车身处用螺钉连接,螺钉采用rbe2单元模拟,所有工况均在连接支架3与车身连接处约束,约束x、y、z三方向平动自由度和旋转自由度。
53.具体地,步骤s4包括:
54.s41、模态工况模拟仿真分析:模拟汽车主动进气格栅系统安装在实车状态,汽车主动进气格栅的有限元模型与车身连接的位置约束全部自由度,利用hypermesh软件中的nastran模块,控制卡片采用sol103进行设置,计算汽车主动进气格栅的有限元模型的约束模态,要求一阶模态≥35hz。
55.也即,在步骤s41中,模态工况的模拟仿真分析方法为利用hypermesh软件中的nastran模块,控制卡片采用sol103进行设置,通过软件能够获得汽车主动进气格栅的有限元模型的约束模态。对模态工况的评价标准为一阶模态≥35hz。只有当汽车主动进气格栅的模态工况满足要求,才能够避免怠速及常用工况发生共振。
56.s42、刚度工况模拟仿真分析:利用hypermesh软件中的nastran模块,控制卡片采用sol101进行设置,在汽车主动进气格栅的骨架1的前端中间位置,沿z方向加载500n的载荷,计算汽车主动进气格栅的有限元模型的最大变形,要求汽车主动进气格栅的最大变形不超过2mm。
57.也即,在步骤s42中,刚度工况的模拟仿真分析方法为:利用hypermesh软件中的nastran模块,控制卡片采用sol101进行设置,在汽车主动进气格栅的骨架1的前端中间位置,沿z方向加载500n的载荷,通过软件能够获取汽车主动进气格栅的最大变形。对刚度工
况的评价标准为汽车主动进气格栅的最大变形不超过2mm。
58.汽车主动进气格栅基本为左右对称结构,载荷的加载位置要求在骨架1的前端的中间位置。骨架1的前端的中间位置在后续试验比较容易放置加载力的试验设备,以进一步进行试验验证。
59.s43、强度工况模拟仿真分析:利用hypermesh软件中的nastran模块,控制卡片采用sol101进行设置,在汽车主动进气格栅的骨架1的前端中间位置,沿z方向加载2000n的载荷,计算汽车主动进气格栅的有限元模型的最大应力,要求汽车主动进气格栅的最大应力<许用应力。
60.也即,在步骤s43中,强度工况的模拟仿真分析方法为:利用hypermesh软件中的nastran模块,控制卡片采用sol101进行设置,在汽车主动进气格栅的骨架1的前端中间位置,沿z方向加载2000n的载荷,通过软件获取汽车主动进气格栅的有限元模型的最大应力。对强度工况的评价标准为汽车主动进气格栅的最大应力<许用应力。
61.在步骤s43中,为保证汽车主动进气格栅的正常使用,要求最大应力<许用应力。如st02d z-60/60力许用应力为260mpa。以保证汽车主动进气格栅系统中塑料件及钣金件都无塑性变形。
62.s44、风载动压载荷工况模拟仿真分析:对汽车主动进气格栅的叶片2进行动压变形量模拟仿真分析,利用hypermesh软件中的nastran模块,控制卡片采用sol101进行设置,计算得到动压值,对汽车主动进气格栅的叶片2施加计算得到的动压值,计算最高车速情况下汽车主动进气格栅的叶片中心的变形量,要求最高车速情况下,汽车主动进气格栅的叶片中心的最大变形量不超过4mm。
63.也即,在步骤s44中,风载动压载荷工况的模拟仿真分析方法为:对汽车主动进气格栅的叶片2进行动压变形量模拟仿真分析,利用hypermesh软件中的nastran模块,控制卡片采用sol101进行设置,计算得到动压值,对汽车主动进气格栅的叶片2施加计算得到的动压值,通过软件得到最高车速情况下汽车主动进气格栅的叶片中心的变形量。对风载动压载荷工况的评价标准为:最高车速情况下,汽车主动进气格栅的叶片中心的最大变形量不超过4mm。
64.具体地,在步骤s44中,动压是通过最高车速和当地的空气密度进行转换,其中动压计算公式为:
65.p=0.5ρv2;
66.式中,p-动压(n/m2);ρ-当地空气密度(kg/m3);v-风速(m/s)。
67.进一步地,步骤s41还包括:若计算所得的一阶模态不满足要求,则对汽车主动进气格栅的有限元模型进行结构优化,优化完成后再次进行模态工况模拟仿真分析,直至计算所得的一阶模态满足要求。具体地,需要对结构薄弱的地方进行结构优化。如此设置,若模态工况模拟仿真分析后发现汽车主动进气格栅的模态工况不合格,则对所设计的汽车主动进气格栅进行优化,保证设计阶段汽车主动进气格栅的模态工况符合要求。
68.进一步地,步骤s42还包括:若汽车主动进气格栅的最大变形不满足要求,则对汽车主动进气格栅的有限元模型进行结构优化,优化完成后再次进行刚度工况模拟仿真分析,直至汽车主动进气格栅的最大变形满足要求。如此设置,若刚度工况模拟仿真分析后发现汽车主动进气格栅的刚度工况不合格,则对所设计的汽车主动进气格栅进行优化,保证
设计阶段汽车主动进气格栅的刚度工况符合要求。
69.进一步地,步骤s43还包括:若汽车主动进气格栅的最大应力不满足要求,则对汽车主动进气格栅的有限元模型进行结构优化,优化完成后再次进行强度工况模拟仿真分析,直至汽车主动进气格栅的最大应力满足要求。如此设置,若强度工况模拟仿真分析后发现汽车主动进气格栅的强度工况不合格,则对所设计的汽车主动进气格栅进行优化,保证设计阶段汽车主动进气格栅的强度工况符合要求。
70.进一步地,步骤s44还包括:若汽车主动进气格栅的叶片中心的最大变形量不满足要求,则对汽车主动进气格栅的有限元模型进行结构优化,优化完成后再次进行风载动压载荷工况模拟仿真分析,直至汽车主动进气格栅的叶片中心的最大变形量满足要求。如此设置,若风载动压载荷工况模拟仿真分析后发现汽车主动进气格栅的风载动压载荷工况不合格,则对所设计的汽车主动进气格栅进行优化,保证设计阶段汽车主动进气格栅的风载动压载荷工况符合要求。
71.具体地,本实施例中,对汽车主动进气格栅的有限元模型进行结构优化包括:调整汽车主动进气格栅的有限元模型的加强筋11的布置和加强筋11的料厚。具体地,在步骤s44中,对汽车主动进气格栅的有限元模型进行结构优化包括对叶片2的料厚进行调整。
72.以上实施方式只是阐述了本发明的基本原理和特性,本发明不受上述实施方式限制,在不脱离本发明精神和范围的前提下,本发明还有各种变化和改变,这些变化和改变都落入要求保护的本发明范围内。本发明要求保护范围由所附的权利要求书及其等效物界定。
再多了解一些
本文用于企业家、创业者技术爱好者查询,结果仅供参考。