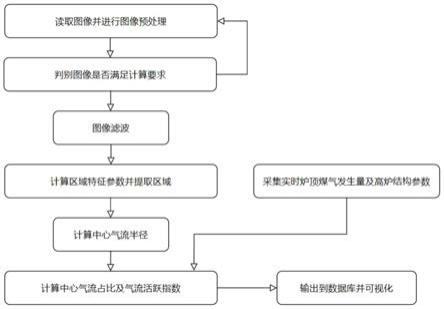
1.本发明涉及一种在线计算方法,尤其是涉及一种用于高炉中心气流大小的在线计算方法,属于冶金生产工艺技术领域。
背景技术:
2.气流的分布关系到炉内温度分布﹑软熔带结构﹑炉况顺行和煤气的利用状况。所以,连续地掌握煤气流的分布情况很有必要。但是由于在实际的生产过程中高炉内部是高温度、高压力、密闭复杂并且恶劣的环境,冶金过程很难进行实时的监测,煤气流分布也很难直接测量。因此中国许多高炉安装了十字测温探尺,能够连续准确地测出炉喉的径向温度,为判断径向煤气流分布提供了条件,另外还在高炉炉顶安装料面红外成像设备对高炉上部料面进行监控,以及时发现料面温度变化。但这些方法或者探测设备多对中心气流检测精度低,或者无法对气流大小进行量化,同时适用于钒钛磁铁矿冶炼高炉中心气流大小计算方法更少,因此开发一种简单高效适用性强的高炉中心气流大小计算方法便成为了本领域技术人员急需解决的技术问题。
技术实现要素:
3.本发明所要解决的技术问题是:提供一种有利于现场操作人员准确实时监控高炉煤气流波动情况,维护炉况稳定,简单、准确、高效的用于高炉中心气流大小的在线计算方法。
4.为解决上述技术问题所采用的技术方案是:一种用于高炉中心气流大小的在线计算方法,所述的在线计算方法先将选取的符合要求的高炉上部料面的实时图像经过至少两次图像处理,获得具有梯度的灰度计算梯度图并计算出该灰度计算梯度图的计算中心气流半径以及中心气流于料面所处的位置,然后以该计算中心气流半径为基础计算中心气流实际面积sc和料面的实际面积s
bf
,接着按下述公式计算出中心气流占比i,最后将中心气流面积数据、中心气流位置数据、中心气流占比数据保存到数据库并绘制实时中心气流位置图实现高炉中心汽流大小的可视化完成高炉中心气流大小的在线计算,
[0005][0006]
式中,i为中心气流占比,%;sc为中心气流实际面积,pt;s
bf
为料面的实际面积,pt。
[0007]
进一步的是,在计算中心气流占比i的同时还需要采集目标高炉实时炉顶煤气发生量g及炉喉截面积s
top
,并计算气流活跃指数k,然后与中心气流面积数据、中心气流位置数据和中心气流占比数据一起保存到数据库并绘制实时中心气流位置图实现高炉中心汽流大小的可视化,
[0008]
计算气流活跃指数k的计算公式为,
[0009]
式中,g为目标高炉实时炉顶煤气发生量,m3/s;s
top
为炉喉截面积,m2;k为目标高炉气流活跃指数,m/s。
[0010]
上述方案的优选方式是,在进行第一次实时图像色彩转换前,先需要读取目标高炉炉顶料面红外成像系统拍摄的高炉上部料面的实时图像,采集高炉结构参数及料面实时高度位置数据、炉顶红外摄像机安装角度及位置数据,并将彩色图像转换成灰度图,然后计算图像的最佳阈值并将图像转化为二进制图像,最后根据高炉结构参数与料面实时高度数据,过滤料面以外区域图像的干扰完成第一次实时图像色彩转换。
[0011]
进一步的是,在对实时图像完成一次色彩转换后还需要进行符合图像所属类别判定,其具体过程中为,将第一次色彩转换预处理的实时图像导入分类器进行图像所属类别判定,当判断其属于a类满足中心气流计算要求的图像类别时,则输入到下一步骤进行处理,否则,重新执行步骤一,即采集下一个实时图像导入分类器重新进行图像所属类别判定,
[0012]
其中所述的分类器是按下述步骤构建的,
[0013]
第一步,采集大量具有代表性和多样性的目标高炉炉顶料面红外成像系统拍摄的高炉上部料面图像,进行图像预处理与特征提取;
[0014]
第二步,基于模糊神经网络分类算法进行分类,确定并优化判别参数,寻找完全是由高炉中心气流大小计算所需的料面清晰无遮挡的理想图像所构成的类别并进行特殊标记,记为a类;
[0015]
第三步,构建标准库,得到符合要求的分类器。
[0016]
上述方案的优选方式是,对图像所属类别判定满足要求的灰度图进行图像滤波处理的二次色彩转换,其过程中为将图像所属类别判定满足要求的高炉炉顶料面二值图像进行多次开运算和闭运算的组合操作,完成图像滤波处理得到高温区域与低温区域对比明显的黑白图像。
[0017]
进一步的是,标记黑白图像中已连接的白色区域部分,计算该图像标记区域的特征尺寸并进行rgb图像转换,得到中心气流所在区域的彩色标记图像,
[0018]
其中所述的白色区域部分为图片中的高温区域以及中心气流所在的位置,所述的特征尺寸包括区域面积以及框架大小。
[0019]
上述方案的优选方式是,依据具有梯度的灰度计算梯度图计算中心气流半径时是按下述步骤进行的,先将通过rgb图像转换获得的彩色图像再次转化为灰度图,然后基于灰度图像的梯度,利用霍夫变换圆检测方法在标记的高温度区域内部寻找最大内接圆半径及圆心位置,
[0020]
所述霍夫变换圆检测方法的具体操作过程为,
[0021]
第一步,检测标记区域的边缘,计算标记区域内可能存在的圆心位置;
[0022]
第二步,在第一步的基础上从所有可能圆心位置数据集合中开始计算标记区域的最大内接圆半径大小;
[0023]
第三步,输出最大内接圆半径及圆心位置获得中心气流半径以及中心气流于料面所处的位置。
[0024]
进一步的是,根据中心气流半径计算中心气流实际面积时,需要根据炉顶红外摄像机的安装角度、安装位置以及高炉实时测定的料面高度对中心气流面积进行矫正以得到
中心气流的实际面积为sc。
[0025]
进一步的是,在计算料面的实际面积s
bf
时,需要结合高炉结构及料面高度进行计算并校正以得到料面的实际面积s
bf
。
[0026]
本发明的有益效果是:本技术提供的技术方案以现有布置在高炉炉顶料面处的红外成像设备拍摄到的实时图像为依据,通过至少两次图像处理,获得具有梯度的灰度计算梯度图并计算出该灰度计算梯度图的计算中心气流半径以及中心气流于料面所处的位置,然后以该计算中心气流半径为基础计算中心气流实际面积sc和料面的实际面积s
bf
,接着按下述公式计算出中心气流占比i,最后将中心气流面积数据、中心气流位置数据、中心气流占比数据保存到数据库并绘制实时中心气流位置图实现高炉中心汽流大小的可视化完成高炉中心气流大小的在线计算,式中,i为中心气流占比,%;sc为中心气流实际面积,pt;s
bf
为料面的实际面积,pt。解决了现有技术中的方法或者探测设备对中心气流的检测精度偏低,或者无法对气流大小进行量化,以及无法适用于钒钛磁铁矿冶炼高炉中心气流大小计算方法的技术问题,有利于现场操作人员准确实时监控高炉煤气流波动情况,维护炉况稳定,简单、准确、高效。
附图说明
[0027]
图1为本发明用于高炉中心气流大小的在线计算方法的模型计算流程图图;
[0028]
图2为本发明计算时输入r图片;
[0029]
图3为本发明计算中心气流区域最大内接圆过程示意图;
[0030]
图4为本发明计算模型实时运行界面及结果示意图。
具体实施方式
[0031]
如图1~图4所示是本发明提供的一种有利于现场操作人员准确实时监控高炉煤气流波动情况,维护炉况稳定,简单、准确、高效的用于高炉中心气流大小的在线计算方法。所述的在线计算方法先将选取的符合要求的高炉上部料面的实时图像经过至少两次图像处理,获得具有梯度的灰度计算梯度图并计算出该灰度计算梯度图的计算中心气流半径以及中心气流于料面所处的位置,然后以该计算中心气流半径为基础计算中心气流实际面积sc和料面的实际面积s
bf
,接着按下述公式计算出中心气流占比i,最后将中心气流面积数据、中心气流位置数据、中心气流占比数据保存到数据库并绘制实时中心气流位置图实现高炉中心汽流大小的可视化完成高炉中心气流大小的在线计算,
[0032][0033]
式中,i为中心气流占比,%;sc为中心气流实际面积,pt;s
bf
为料面的实际面积,pt。本技术提供的技术方案以现有布置在高炉炉顶料面处的红外成像设备拍摄到的实时图像为依据,通过至少两次图像处理,获得具有梯度的灰度计算梯度图并计算出该灰度计算梯度图的计算中心气流半径以及中心气流于料面所处的位置,然后以该计算中心气流半径为基础计算中心气流实际面积sc和料面的实际面积s
bf
,接着按下述公式计算出中心气流占比i,最后将中心气流面积数据、中心气流位置数据、中心气流占比数据保存到数据库并绘
制实时中心气流位置图实现高炉中心汽流大小的可视化完成高炉中心气流大小的在线计算,式中,i为中心气流占比,%;sc为中心气流实际面积,pt;s
bf
为料面的实际面积,pt。解决了现有技术中的方法或者探测设备对中心气流的检测精度偏低,或者无法对气流大小进行量化,以及无法适用于钒钛磁铁矿冶炼高炉中心气流大小计算方法的技术问题,有利于现场操作人员准确实时监控高炉煤气流波动情况,维护炉况稳定,简单、准确、高效。
[0034]
上述实施方式中,为了便于计算操作,同时提交计算的准确性,以及可操作性,本技术在计算中心气流占比i的同时还需要采集目标高炉实时炉顶煤气发生量g及炉喉截面积s
top
,并计算气流活跃指数k,然后与中心气流面积数据、中心气流位置数据和中心气流占比数据一起保存到数据库并绘制实时中心气流位置图实现高炉中心汽流大小的可视化,
[0035]
计算气流活跃指数k的计算公式为,
[0036]
式中,g为目标高炉实时炉顶煤气发生量,m3/s;s
top
为炉喉截面积,m2;k为目标高炉气流活跃指数,m/s。并且在进行第一次实时图像色彩转换前,先需要读取目标高炉炉顶料面红外成像系统拍摄的高炉上部料面的实时图像,采集高炉结构参数及料面实时高度位置数据、炉顶红外摄像机安装角度及位置数据,并将彩色图像转换成灰度图,然后计算图像的最佳阈值并将图像转化为二进制图像,最后根据高炉结构参数与料面实时高度数据,过滤料面以外区域图像的干扰完成第一次实时图像色彩转换。以及在对实时图像完成一次色彩转换后还需要进行符合图像所属类别判定,其具体过程中为,将第一次色彩转换预处理的实时图像导入分类器进行图像所属类别判定,当判断其属于a类满足中心气流计算要求的图像类别时,则输入到下一步骤进行处理,否则,重新执行步骤一,即采集下一个实时图像导入分类器重新进行图像所属类别判定,
[0037]
其中所述的分类器是按下述步骤构建的,
[0038]
第一步,采集大量具有代表性和多样性的目标高炉炉顶料面红外成像系统拍摄的高炉上部料面图像,进行图像预处理与特征提取;
[0039]
第二步,基于模糊神经网络分类算法进行分类,确定并优化判别参数,寻找完全是由高炉中心气流大小计算所需的料面清晰无遮挡的理想图像所构成的类别并进行特殊标记,记为a类;
[0040]
第三步,构建标准库,得到符合要求的分类器。
[0041]
相应的,对图像所属类别判定满足要求的灰度图进行图像滤波处理的二次色彩转换,其过程中为将图像所属类别判定满足要求的高炉炉顶料面二值图像进行多次开运算和闭运算的组合操作,完成图像滤波处理得到高温区域与低温区域对比明显的黑白图像。标记黑白图像中已连接的白色区域部分,计算该图像标记区域的特征尺寸并进行rgb图像转换,得到中心气流所在区域的彩色标记图像,
[0042]
其中所述的白色区域部分为图片中的高温区域以及中心气流所在的位置,所述的特征尺寸包括区域面积以及框架大小。依据具有梯度的灰度计算梯度图计算中心气流半径时是按下述步骤进行的,先将通过rgb图像转换获得的彩色图像再次转化为灰度图,然后基于灰度图像的梯度,利用霍夫变换圆检测方法在标记的高温度区域内部寻找最大内接圆半
径及圆心位置,
[0043]
所述霍夫变换圆检测方法的具体操作过程为,
[0044]
第一步,检测标记区域的边缘,计算标记区域内可能存在的圆心位置;
[0045]
第二步,在第一步的基础上从所有可能圆心位置数据集合中开始计算标记区域的最大内接圆半径大小;
[0046]
第三步,输出最大内接圆半径及圆心位置获得中心气流半径以及中心气流于料面所处的位置。相应的,根据中心气流半径计算中心气流实际面积时,需要根据炉顶红外摄像机的安装角度、安装位置以及高炉实时测定的料面高度对中心气流面积进行矫正以得到中心气流的实际面积为sc。在计算料面的实际面积s
bf
时,需要结合高炉结构及料面高度进行计算并校正以得到料面的实际面积s
bf
。
[0047]
本技术所述的二值图像将256个亮度等级的灰度图像通过适当的阈值选取而获得仍然可以反映图像整体和局部特征的二值化图像;本技术所述的开运算和闭运算,为现有常规的一种计算方法,只是在于模型中的开运算、闭运算的具体排布顺序和参数设定需要根据实际情况进行排布或选择。
[0048]
综上所述,采用本技术提供的在线计算方法,可在生产现场直接在线应用,应用价值大;运行仅需安装炉顶料面成像设备,设备简单,利于广泛推广应用;技术原理具有普适性,可应用于包括钒钛磁铁矿冶炼高炉在内的国内外普通高炉。
[0049]
1.该计算方法仅需采集炉顶料面成像系统拍摄的料面图片及部分高炉结构及运行参数等即可满足计算要求,且可实现在线应用,具有较高的经济性、实用性。
[0050]
2.该计算方法优化了中心气流位置及半径检测方法,可实时标记中心气流位置并量化中心气流大小,为现场操作者准确判断高炉煤气流分布情况提供了可靠依据。
[0051]
实现了对中心气流大小的量化工作,有助于高炉现场操作人员实时判断高炉中心气流大小,提前发现中心气流异常波动,优化高炉煤气流分布,减少炉况波动,增强高炉上部温度场分布均匀性,提高燃料利用率,保证高炉长期高效稳定顺行。
[0052]
具体实施例
[0053]
本发明的目的在于,提供一种用于高炉中心气流大小在线计算方法,该中心气流大小计算方法基于图像处理技术利用高炉炉顶料面红外成像图片即可快速计算高炉中心气流大小具体数值,有利于现场操作人员准确实时监控高炉煤气流波动情况,维护炉况稳定,简单、准确、高效。
[0054]
技术方案:为实现以上目的,本发明通过以下步骤计算高炉中心气流大小:
[0055]
步骤一:读取图像并进行图像预处理
[0056]
读取目标高炉炉顶料面红外成像系统拍摄的高炉上部料面的实时图像,采集高炉结构参数及料面实时高度位置数据、炉顶红外摄像机安装角度及位置数据,先将彩色图像转换成灰度图,然后计算图像的最佳阈值并将图像转化为二进制图像,最后根据高炉结构参数与料面实时高度数据,过滤料面以外区域图像的干扰。
[0057]
步骤二:判别图像是否满足计算要求
[0058]
将步骤一预处理的实时图像,导入分类器,判定图像所属类别,若属于a类(即满足中心气流计算要求的图像所属类别),则满足要求并输入到下一步骤进行处理,否则,重新执行步骤一,即采集下一个实时图像导入分类器。
[0059]
所述分类器构建方法为:第一步:采集大量具有代表性和多样性的目标高炉炉顶料面红外成像系统拍摄的高炉上部料面图像,进行图像预处理与特征提取;第二步:基于模糊神经网络分类算法进行分类,确定并优化判别参数,寻找完全是由高炉中心气流大小计算所需的料面清晰无遮挡的理想图像所构成的类别并进行特殊标记,记为a类;第三步:构建标准库,得到符合要求的分类器。
[0060]
步骤三:图像滤波
[0061]
将步骤二满足要求的高炉炉顶料面二值图像进行多次开运算和闭运算的组合操作,从而完成图像滤波,得到高温区域与低温区域对比明显的黑白图像。
[0062]
步骤四:计算区域特征参数并提取区域
[0063]
标记黑白图像中已连接的白色区域部分(即高温区域,中心气流所在位置),计算该图像标记区域的特征尺寸,包括区域面积、框架大小等,并进行rgb图像转换,得到中心气流所在区域的彩色标记图像。
[0064]
步骤五:计算中心气流半径
[0065]
将图像进行再次转化为灰度图,基于图像的梯度,利用霍夫变换圆检测方法在标记区域(即高温区域)内部寻找最大内接圆半径及圆心位置,具体方法:第一步:检测标记区域的边缘,计算标记区域内可能存在的圆心位置;第二步:在第一步的基础上从所有可能圆心位置数据集合中开始计算标记区域的最大内接圆半径大小;第三步:输出最大内接圆半径及圆心位置。
[0066]
步骤六:计算中心气流占比及气流活跃指数
[0067]
根据中心气流半径计算中心气流面积,并根据炉顶红外摄像机安装角度、位置及高炉实时测定的料面高度对中心气流面积进行矫正,得到中心气流实际面积为sc。然后结合高炉结构及料面高度,计算并校正料面的实际面积s
bf
,最后计算得到中心气流占比i。
[0068][0069]
式中:i为中心气流占比,%;sc为中心气流实际面积,pt;s
bf
为料面的实际面积,pt。
[0070]
采集目标高炉实时炉顶煤气发生量g及炉喉截面积s
top
,计算气流活跃指数k,计算公式如下:
[0071][0072]
式中:g为目标高炉实时炉顶煤气发生量,m3/s;s
top
为炉喉截面积,m2;k为目标高炉气流活跃指数,m/s。
[0073]
步骤七:输出到数据库并可视化
[0074]
将中心气流面积数据、位置数据、占比数据保存到数据库并绘制实时中心气流位置图,以实现可视化。
[0075]
实施例一
[0076]
为让本发明的上述特征和优点能更加明显易懂,结合附图以某钢铁公司高炉结构参数、运行数据及炉顶成像系统图片为例,对本发明作进一步详细说明:
[0077]
步骤一:读取图像并进行图像预处理
[0078]
读取目标高炉炉顶料面红外成像系统拍摄的高炉上部料面的实时图像,如图2所示,同时采集高炉结构参数及料面实时高度位置数据、炉顶红外摄像机安装角度及位置数据,先将彩色图像转换成灰度图,然后计算图像的最佳阈值并将图像转化为二进制图像,最后根据高炉结构参数与料面实时高度数据,过滤料面以外区域图像的干扰。
[0079]
步骤二:判别图像是否满足计算要求
[0080]
将步骤一预处理的实时图像,导入分类器,判定图像所属类别,若属于a类(即满足中心气流计算要求的图像所属类别),则满足要求并输入到下一步骤进行处理,否则,重新执行步骤一,即采集下一个实时图像导入分类器。
[0081]
所述分类器构建方法为:第一步:采集大量具有代表性和多样性的目标高炉炉顶料面红外成像系统拍摄的高炉上部料面图像,进行图像预处理与特征提取;第二步:基于模糊神经网络分类算法进行分类,确定并优化判别参数,寻找完全是由高炉中心气流大小计算所需的料面清晰无遮挡的理想图像所构成的类别并进行特殊标记,记为a类;第三步:构建标准库,得到符合要求的分类器。
[0082]
步骤三:图像滤波
[0083]
将步骤二满足要求的高炉炉顶料面二值图像进行多次开运算和闭运算的组合操作,从而完成图像滤波,得到高温区域与低温区域对比明显的黑白图像。
[0084]
步骤四:计算区域特征参数并提取区域
[0085]
标记二进制图像中已连接的白色区域部分(即高温区域,中心气流所在位置),计算该图像标记区域的特征尺寸,包括区域面积、框架大小等,并进行rgb图像转换,得到中心气流所在区域的彩色标记图像。
[0086]
步骤五:计算中心气流半径
[0087]
将图像进行再次转化为灰度图,基于图像的梯度,利用霍夫变换圆检测方法在标记区域(即高温区域)内部寻找最大内接圆半径及圆心位置,具体方法:第一步:检测标记区域的边缘,计算标记区域内可能存在的圆心位置;第二步:在第一步的基础上从所有可能圆心位置数据集合中开始计算标记区域的最大内接圆半径大小;第三步:输出最大内接圆半径及圆心位置。具体运算过程的实时效果图,如图3所示。
[0088]
步骤六:计算中心气流占比及气流活跃指数
[0089]
根据中心气流半径计算中心气流面积,并根据炉顶红外摄像机安装角度、位置及高炉实时测定的料面高度对中心气流面积进行矫正,得到中心气流实际面积为sc。然后结合高炉结构及料面高度,计算并校正料面的实际面积s
bf
,最后计算得到中心气流占比i,具体计算结果如图4所示,为7.7451%。
[0090][0091]
式中:i为中心气流占比,%;sc为中心气流实际面积,pt;s
bf
为料面的实际面积,pt。
[0092]
采集目标高炉实时炉顶煤气发生量g及炉喉截面积s
top
,计算气流活跃指数k,计算公式如下:
[0093]
[0094]
式中:g为目标高炉实时炉顶煤气发生量,m3/s;s
top
为炉喉截面积,m2;k为目标高炉气流活跃指数,m/s。
[0095]
代入g=92.92m3/s,s
top
=37.39m2到公式(2)中,计算得到当前高炉气流活跃指数k=2.485m/s。
[0096]
步骤七:输出到数据库并可视化
[0097]
将中心气流面积数据、位置数据、占比数据保存到数据库并绘制实时中心气流位置图,以实现可视化,具体可视化效果如图4所示。
再多了解一些
本文用于企业家、创业者技术爱好者查询,结果仅供参考。