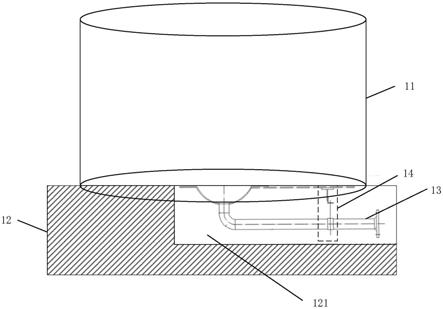
1.本技术涉及储油装置技术领域,特别涉及一种储油罐。
背景技术:
2.石油经过炼制等加工工艺生产出的油品一般存储在储油罐中。但是,油品中含有水分和杂质,在储油罐存储油品的过程中,油品中的水分和杂质从油品中分离,混合形成污水。由于污水会降低油品的品质,所以需要定期对储油罐内的污水进行排放。
3.相关技术中,储油罐包括罐体、罐体固定台和排液管;罐体设置在罐体固定台上,排液管填埋固定在罐体固定台的内部;排液管与罐体的底部连接,用于排放该储油罐内的污水;罐体固定台,用于固定罐体和排液管,罐体,用于存储油品。
4.但是,当罐体内存储的油品较多时,罐体的整体重量大,罐体固定台由于长期受到罐体的重力会发生沉降,罐体固定台上的罐体也会发生沉降,此时,排液管会受到罐体的挤压而发生开裂,导致储油罐发生油品泄漏事故,所以该储油罐的安全性低。
技术实现要素:
5.本技术实施例提供了一种储油罐,可以避免储油罐油品泄漏事故的发生,提高储油罐的安全性。所述技术方案如下:
6.本技术提供了一种储油罐,所述储油罐包括:罐体、罐体固定台、排液管和排液管固定件;
7.所述罐体设置在所述罐体固定台上,所述罐体固定台内设有观察通道,所述排液管和所述排液管固定件设置在所述观察通道内;
8.所述罐体的底部设有排液口,所述排液管的一端与所述排液口连接,所述排液管的另一端,用于与收集罐连接,所述排液管的中部,通过所述排液管固定件与所述罐体的底部连接;
9.所述罐体,用于存储油液;所述罐体固定台,用于支撑所述罐体;所述排液管,用于将所述油液中分离出的污水传输至所述收集罐;所述排液管固定件,用于固定所述排液管。
10.在一种可能的实现方式中,所述罐体包括储液腔体和排水槽;
11.所述排水槽与所述储液腔体的底部连接;所述排液口设置在所述排水槽的底部。
12.在本技术实施例中,由于排水槽设置在储液腔体的底部,油液中的污水在分离后向下移动,汇集在排水槽内,因此,通过排水槽能够对油液中的污水进行收集。一方面,排水槽能够避免油液从排水槽底部的排液口排出;另一方面,罐体内的污水能够通过排水槽底部的排液口直接流入排液管,从而提高了排放罐体内的污水的效率。
13.在另一种可能的实现方式中,所述排液管固定件包括u形螺栓、螺母和固定架;
14.所述固定架的底端设有螺栓孔,所述固定架的顶端与所述罐体的底部连接;
15.所述u形螺栓套在所述排液管外,且穿过所述螺栓孔与所述螺母连接,用以与所述固定架的底端配合固定所述排液管。
16.在本技术实施例中,通过u形螺栓与固定架的底端配合固定排液管,由于u形螺栓能够阻止排液管相对于罐体向下移动,固定架的底端能够阻止排液管相对于罐体向上移动,因此,该排液管固定件能够阻止排液管相对于罐体移动,从而在罐体发生沉降时,排液管与罐体能够保持同步沉降,避免了排液管受力拉伸或挤压而发生开裂,进而防止储油罐发生油品泄漏事故,所以提高了该储油罐的安全性。
17.在另一种可能的实现方式中,所述固定架包括垫板、吊板和支撑板;
18.所述垫板设置在所述吊板的顶端,所述支撑板设置在所述吊板的底端,且所述垫板、所述吊板和所述支撑板构成“工”字型结构;
19.所述支撑板上设有螺栓孔,所述u形螺栓套在所述排液管外,且穿过所述螺栓孔与所述螺母连接,用以与所述支撑板配合固定所述排液管;
20.所述垫板,用于与所述罐体的底部连接。
21.在本技术实施例中,通过垫板能够增加固定架与罐体的底部接触时的受力面积,在罐体发生沉降时,能够防止罐体的底部因局部受力而发生变形或损坏,因此,提高了该储油罐的安全性。
22.在另一种可能的实现方式中,所述排液管固定件还包括绝缘垫;
23.所述绝缘垫设置在所述u形螺栓与所述排液管之间,用于消除所述排液管与所述u形螺栓之间的静电。
24.在本技术实施例中,绝缘垫设置在u形螺栓与排液管之间,由于绝缘垫能够消除排液管与u形螺栓之间的静电,进而能够防止静电引发火灾事故,因此,提高了该储油罐的安全性。
25.在另一种可能的实现方式中,所述排液管包括第一排液直管、第二排液直管和弯管;
26.所述第一排液直管的一端,通过所述弯管与所述第二排液直管的一端连接;所述第一排液直管的另一端与所述排液口连接,所述第二排液直管的另一端,用于与所述收集罐连接。
27.在本技术实施例中,由于排液管包括第一排液直管、第二排液直管和弯管,通过弯管能够改变排液管的方向,进而提高了排液管的灵活性。
28.在另一种可能的实现方式中,所述储油罐还包括控制阀;
29.所述排液管的另一端,通过所述控制阀与所述收集罐连接;
30.所述控制阀,用于控制所述排液管内的污水的流速。
31.在本技术实施例中,由于通过能够控制排液管内的污水的流速,进而能够对储油罐内的污水进行定期排放,所以提高了该储油罐的灵活性。
32.在另一种可能的实现方式中,所述储油罐还包括保护网;
33.所述保护网设置在所述观察通道的通道口,用于保护所述排液管和所述排液管固定件。
34.在本技术实施例中,由于储油罐一般设置在野外环境中,而通过在观察通道的通道口设有保护网,能够阻止动物误入到观察通道内,避免对排液管和排液管固定件造成损伤,所以提高了该储油罐的安全性。
35.在另一种可能的实现方式中,所述排液管上设有防腐涂层。
36.在本技术实施例中,排液管上设有防腐涂层,由于防腐涂料能够阻止外界环境中的水和氧与排液管表面直接接触,避免排液管被腐蚀而发生损坏,进而能够防止油液在传输过程中发生泄漏,所以提高了该储油罐的安全性。
37.在另一种可能的实现方式中,所述防腐涂层包括第一防腐涂层和第二防腐涂层;
38.所述第一防腐涂层为环氧富锌,所述第二防腐涂层为环氧煤沥青。
39.本技术实施例提供的技术方案的有益效果至少包括:
40.本技术实施例提供了一种储油罐,一方面,由于该储油罐中的排液管通过排液管固定件与罐体固定在一起,因此,在罐体发生沉降时,排液管与罐体能够保持同步沉降,所以防止排液管受到罐体的挤压;另一方面,由于在罐体固定台上设置观察通道,将排液管设置在观察通道内,因此,在罐体发生沉降时,排液管不会与罐体固定台产生摩擦,进而不会受到罐体固定台的挤压。由此可知,该储油罐既能避免排液管受到罐体的挤压,又能避免排液管受罐体固定台的挤压,因此能够防止排液管由于受到挤压而发生开裂,进而防止储油罐发生油品泄漏事故,所以提高了该储油罐的安全性。
附图说明
41.为了更清楚地说明本技术实施例中的技术方案,下面将对实施例描述中所需要使用的附图作简单地介绍,显而易见地,下面描述中的附图仅仅是本技术的一些实施例,对于本领域普通技术人员来讲,在不付出创造性劳动的前提下,还可以根据这些附图获得其他的附图。
42.图1是根据本技术实施例提供的一种储油罐的结构示意图;
43.图2是根据本技术实施例提供的一种排液管的结构示意图;
44.图3是根据本技术实施例提供的一种排液管固定件的结构示意图。
45.附图标记:
46.11
ꢀꢀꢀ
罐体
47.12
ꢀꢀꢀ
罐体固定台
48.121
ꢀꢀ
观察通道
49.13
ꢀꢀꢀ
排液管
50.131
ꢀꢀ
第一排液直管
51.132
ꢀꢀ
弯管
52.133
ꢀꢀ
第二排液直管
53.14
ꢀꢀꢀ
排液管固定件
54.141
ꢀꢀ
u形螺栓
55.142
ꢀꢀ
螺母
56.143
ꢀꢀ
固定架
具体实施方式
57.为使本技术的目的、技术方案和优点更加清楚,下面将结合附图对本技术实施方式作进一步地详细描述。
58.图1是本技术提供的一种储油罐的结构示意图。参见图1,该储油罐包括:罐体11、
罐体固定台12、排液管13和排液管固定件14;
59.罐体11设置在罐体固定台12上,罐体固定台12内设有观察通道121,排液管13和排液管固定件14设置在观察通道121内;
60.罐体11的底部设有排液口,排液管13的一端与排液口连接,排液管13的另一端,用于与收集罐连接,排液管13的中部,通过排液管固定件14与罐体11的底部连接;
61.罐体11,用于存储油液;罐体固定台12,用于支撑罐体11;排液管13,用于将油液中分离出的污水传输至收集罐;排液管固定件14,用于固定排液管13。
62.本技术实施例提供了一种储油罐,一方面,由于该储油罐中的排液管13通过排液管固定件14与罐体11固定在一起,因此,在罐体11发生沉降时,排液管13与罐体11能够保持同步沉降,所以防止排液管13受到罐体11的挤压;另一方面,由于在罐体固定台12上设置观察通道121,将排液管13设置在观察通道121内,因此,在罐体11发生沉降时,排液管13不会与罐体固定台12产生摩擦,进而不会受到罐体固定台12的挤压。由此可知,该储油罐既能避免排液管13受到罐体11的挤压,又能避免排液管13受罐体固定台12的挤压,因此能够防止排液管13由于受到挤压而发生开裂,进而防止储油罐发生油品泄漏事故,所以提高了该储油罐的安全性。
63.罐体11的介绍:罐体11设置在罐体固定台12上,罐体11的底部设有排液口,排液管13的一端与排液口连接。罐体11,用于存储油液。可选的,油液为经过炼制等加工工艺生产出的油品。例如,汽油、煤油、柴油、石脑油等。
64.可选的,排液口的尺寸与排液管13的尺寸相匹配。排液口可以设置在罐体11的底部中心的位置。在本技术实施例中,对排液口的尺寸和位置不作具体限定,可以根据需要进行设置并更改。
65.在一种可能的实现方式中,排液管13的一端与排液口之间通过焊接连接,或者,排液管13的一端与排液口之间通过法兰连接。
66.罐体11的形状可以是圆柱体,也可以是长方体等。罐体11的材料可以是金属,例如,铜、铁等,也可以是非金属材料。罐体11的高度可以是5m
‑
20m之间的任一数值,例如,10m、12m、15m等。在本技术实施例中,对罐体11的形状、材料和尺寸不作具体限定,可以根据需要进行设置并更改。
67.在一种可能的实现方式中,罐体11包括储液腔体和排水槽;排水槽与储液腔体的底部连接;排液口设置在排水槽的底部。可选的,排水槽为半球形凹槽。
68.需要说明的一点是,油液中分离出的底水的质量大于油液的质量,底水在分离后向下移动,汇集在排水槽内。油液中的杂质也会向下移动,汇集在排水槽内,杂质和底水混合形成污水,所以需要定期排放罐体11内的污水。
69.在本技术实施例中,由于排水槽设置在储液腔体的底部,油液中的污水在分离后向下移动,汇集在排水槽内,因此,通过排水槽能够对油液中的污水进行收集。一方面,排水槽能够避免油液从排水槽底部的排液口排出;另一方面,罐体11内的污水能够通过排水槽底部的排液口直接流入排液管13,从而提高了排放罐体11内的污水的效率。
70.罐体固定台12的介绍:罐体11设置在罐体固定台12上,罐体固定台12内设有观察通道121,排液管13和排液管固定件14设置在观察通道121内。
71.罐体固定台12的形状为圆柱体,罐体固定台12的直径大于罐体11的直径,罐体固
定台12的高度可以是0.4m
‑
1m之间的任一数值。在本技术实施例中,对罐体固定台12的形状和尺寸不作具体限定,可以根据需要进行设置并更改。
72.在一种可能的实现方式中,罐体固定台12的材料为砂和砾石的混合物,通过层层夯实制成。罐体固定台12的外侧包裹混凝土材料。在本技术实施例中,由于罐体固定台12的材料为砂和砾石的混合物,而砂和砾石的成本低,所以通过砂和砾石的混合物制成的罐体固定台12的成本低。
73.在另一种可能的实现方式中,罐体固定台12的材料全部为混凝土材料。在本技术实施例中,由于罐体固定台12的材料为混凝土材料,而混凝土材料的硬度高,防腐蚀效果好,因此提高了罐体固定台12的稳定性。
74.需要说明的一点是,观察通道121的长度大于罐体11的半径。在一种可能的实现方式中,排液口设置在罐体11的底部中心。观察通道121的长度与罐体固定台12的半径相同。观察通道121的宽度和高度大于排液管13的直径。观察通道121可以设置在罐体固定台12的上部、中部或者底部。在本技术实施例中,对观察通道121的尺寸和位置不作具体限定,可以根据需要进行设置并更改。
75.可选的,排液管13的直径为10cm,观察通道121设置在罐体固定台12的上部;观察通道121的宽度为15cm至40cm之间的任一数值。观察通道121的高度为15cm至40cm之间的任一数值。
76.在本技术实施例中,由于排液管13和排液管固定件14设置在观察通道121内,所以能够通过观察通道121对排液管13和排液管固定件14的腐蚀情况进行检测,因此,在排液管13或者排液管固定件14发生损坏时,能够通过观察通道121及时发现,进而采取防护措施,避免大面积泄漏事故的发生,所以提高了该储油罐的安全性。
77.需要说明的一点是,通过观察通道121还能对罐体11进行检测。例如,通过观察通道121能够对罐体11是否发生沉降、罐体11是否发生腐蚀、罐体11是否发生开裂等情况进行检测。
78.排液管13的介绍:排液管13设置在观察通道121内。排液管13的一端与排液口连接,用于将油液中分离出的污水传输至收集罐;排液管13的另一端,用于与收集罐连接;排液管13的中部,通过排液管固定件14与罐体11的底部连接。
79.排液管13的材料可以是金属,例如,铜、铁等,也可以是金属合金,例如,铬钢、铝合金等。排液管13的直径可以是5cm至20cm之间的任一数值,例如,8cm、10cm、12cm等,排液管13的长度大于观察通道121的长度。在本技术实施例中,对排液管13的材料和尺寸不作具体限定,可以根据需要进行设置并更改。
80.在一种可能的实现方式中,参见图2,排液管13包括第一排液直管131、第二排液直管133和弯管132;第一排液直管131的一端,通过弯管132与第二排液直管133的一端连接;第一排液直管131的另一端与排液口连接,第二排液直管133的另一端,用于与收集罐连接。
81.在本技术实施例中,由于排液管13包括第一排液直管131、第二排液直管133和弯管132,通过弯管132能够改变排液管13的方向,进而提高了排液管13的灵活性。
82.第一排液直管131、第二排液直管133和弯管132之间可以是一体成型,也可以通过焊接连接,还可以通过法兰连接。可选的,第一排液直管131、第二排液直管133和弯管132为无缝钢管。
83.在本技术实施例中,由于第一排液直管131、第二排液直管133和弯管132为无缝钢管,而无缝钢管为耐腐蚀材料,能够避免排液管13被腐蚀而发生损坏,进而能够防止油液在传输过程中发生泄漏,所以提高了该储油罐的安全性。
84.在一种可能的实现方式中,排液管13上设有防腐涂层。防腐涂层的厚度可以是50微米至300微米之间的任意数值,例如,100微米、150微米、200微米等。防腐涂层为环氧树脂涂层,或者,陶瓷填充涂层。在本技术实施例中,对防腐涂层的厚度和材料不作具体限定,可以根据需要进行设置并更改。
85.在本技术实施例中,排液管13上设有防腐涂层,由于防腐涂料能够阻止外界环境中的水和氧与排液管13表面直接接触,避免排液管13被腐蚀而发生损坏,进而能够防止油液在传输过程中发生泄漏,所以提高了该储油罐的安全性。
86.在一种可能的实现方式中,防腐涂层包括第一防腐涂层和第二防腐涂层;第一防腐涂层为环氧富锌,第二防腐涂层为环氧煤沥青。
87.其中,第一防腐涂层的厚度可以是40微米至100微米之间的任意数值,例如,40微米、50微米、60微米等。第二防腐涂层的厚度可以是80微米至200微米之间的任意数值,例如,80微米、100微米、150微米等。在本技术实施例中,对第一防腐涂层和第二防腐涂层的厚度不作具体限定,可以根据需要进行设置并更改。
88.需要说明的一点是,通过观察通道121能够对排液管13上的防腐涂层的有效性进行检测。例如,通过观察通道121能够检测防腐涂层是否脱落,排液管13是否发生腐蚀、泄漏等情况。
89.排液管固定件14的介绍:排液管固定件14的一端与排液管13的中部连接,排液管固定件14的另一端与罐体11的底部连接;排液管固定件14,用于固定排液管13。
90.在一种可能的实现方式中,参见图3,排液管固定件14包括u形螺栓141、螺母142和固定架143;固定架143的底端设有螺栓孔,固定架143的顶端与罐体11的底部连接;u形螺栓141套在排液管13外,且穿过螺栓孔与螺母142连接,用以与固定架143的底端配合固定排液管13。可选的,固定架143的顶端与罐体11的底部通过焊接连接。
91.在本技术实施例中,通过u形螺栓141与固定架143的底端配合固定排液管13,由于u形螺栓141能够阻止排液管13相对于罐体11向下移动,固定架143的底端能够阻止排液管13相对于罐体11向上移动,因此,该排液管固定件14能够阻止排液管13相对于罐体11移动,从而在罐体11发生沉降时,排液管13与罐体11能够保持同步沉降,避免了排液管13受力拉伸或挤压而发生开裂,进而防止储油罐发生油品泄漏事故,所以提高了该储油罐的安全性。
92.在一种可能的实现方式中,固定架143包括垫板、吊板和支撑板;垫板设置在吊板的顶端,支撑板设置在吊板的底端,且垫板、吊板和支撑板构成“工”字型结构;支撑板上设有螺栓孔,u形螺栓141套在排液管13外,且穿过螺栓孔与螺母142连接,用以与支撑板配合固定排液管13;垫板,用于与罐体11的底部连接。
93.可选的,垫板、吊板和支撑板之间通过焊接连接。垫板与罐体11的底部通过焊接连接。
94.在本技术实施例中,通过垫板能够增加固定架143与罐体11的底部接触时的受力面积,在罐体11发生沉降时,能够防止罐体11的底部因局部受力而发生变形或损坏,所以提高了该储油罐的安全性。
95.在一种可能的实现方式中,排液管固定件14还包括绝缘垫;绝缘垫设置在u形螺栓141与排液管13之间,用于消除排液管13与u形螺栓141之间的静电。
96.在本技术实施例中,绝缘垫设置在u形螺栓141与排液管13之间,由于绝缘垫能够消除排液管13与u形螺栓141之间的静电,进而能够防止静电引发火灾事故,所以提高了该储油罐的安全性。
97.在一种可能的实现方式中,储油罐还包括控制阀;排液管13的另一端,通过控制阀与收集罐连接;控制阀,用于控制排液管13内的污水的流速。可选的,控制阀为球阀。
98.在本技术实施例中,由于通过能够控制排液管13内的污水的流速,进而能够对储油罐内的污水进行定期排放,所以提高了该储油罐的灵活性。
99.在一种可能的实现方式中,储油罐还包括保护网;保护网设置在观察通道121的通道口,用于保护排液管13和排液管固定件14。
100.在本技术实施例中,由于储油罐一般设置在野外环境中,而通过在观察通道121的通道口设有保护网,能够阻止动物误入到观察通道121内,避免对排液管13和排液管固定件14造成损伤,所以提高了该储油罐的安全性。
101.以上所述仅为本技术的可选实施例,并不用以限制本技术,凡在本技术的精神和原则之内,所作的任何修改、等同替换、改进等,均应包含在本技术的保护范围之内。
再多了解一些
本文用于企业家、创业者技术爱好者查询,结果仅供参考。