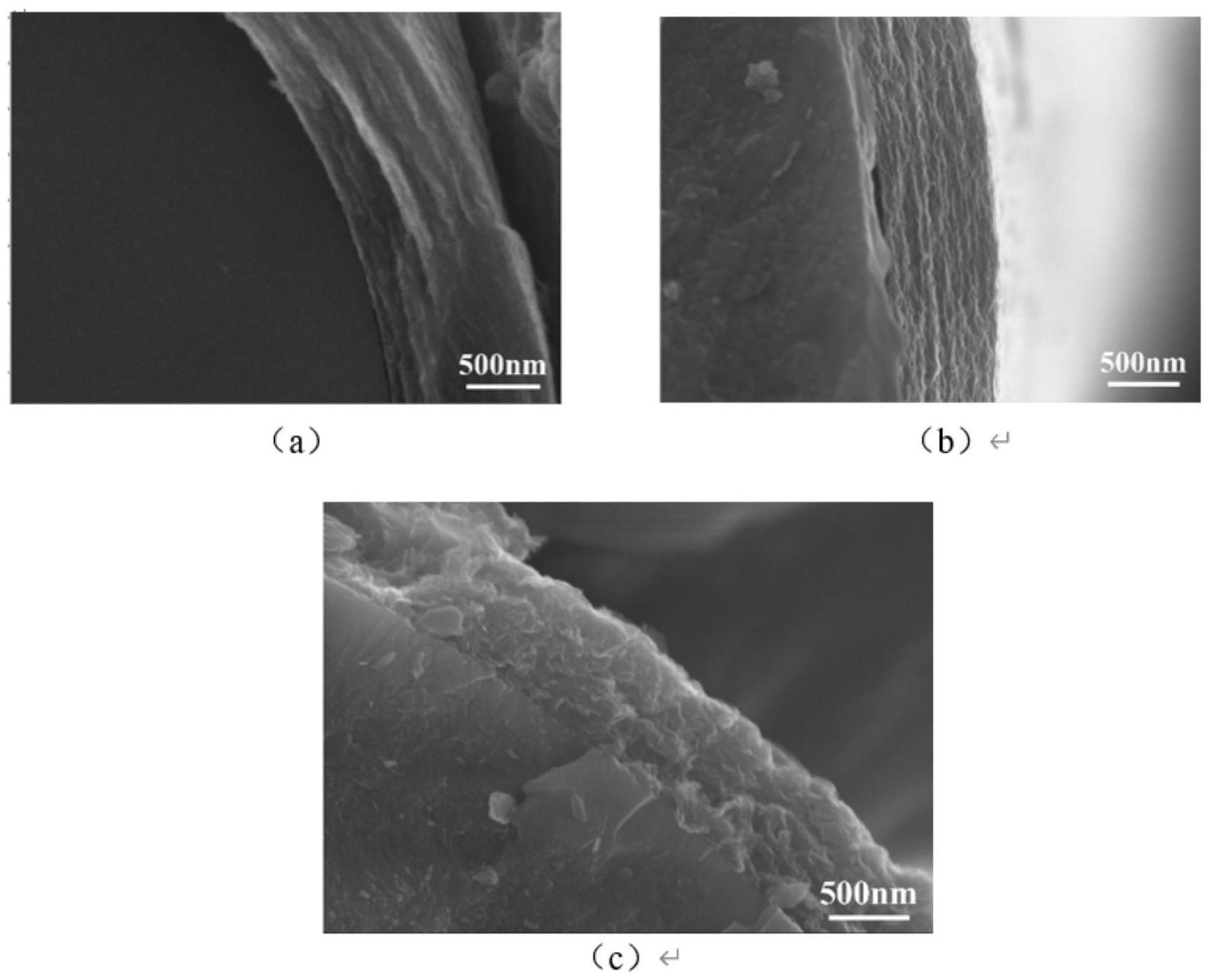
1.本发明涉及碳化硅纤维增强碳化硅sicf/sic复合材料界面涂层制备技术领域,具体涉及一种使用混合前驱体制备热解碳界面涂层的方法。
背景技术:
2.碳化硅纤维增强碳化硅(sicf/sic)复合材料具有高强度、高模量、低密度、力学性能优异、高耐温性、抗氧化性能良好等特点,应用在航空发动机热端构件能够显著提升工作温度,简化冷却结构,进而有效提升航空发动机的推重比,是新一代高性能航空发动机热端构件的理想候选材料。sicf/sic复合材料的韧性和损伤容限高,界面层作为sicf/sic复合材料中调控力学行为的重要组元起到了传递载荷和偏转裂纹的重要作用。其中,热解碳界面层具有典型的层状结构,不仅能在sic纤维和sic基体之间形成较弱的界面结合,促使裂纹偏转和纤维拔出,其石墨微晶还能修复sic纤维的表面缺陷,是sic纤维界面涂层的理想材料。
3.目前,热解碳结构根据其外部形貌特点可分为四类:各向同性层(isotropic,简称iso)、再生层(regenerative laminar,简称rel)、光滑层(smooth laminar,简称sl)和粗糙层(rough laminar,简称rl),其中再生层为各向同性层和光滑层的中间结构。粗糙层热解碳(即高织构热解碳)片层取向度高,断口平滑,片层间仅少量细小裂纹,密度高,可石墨化程度高。可石墨化程度是决定sicf/sic复合材料热物理、摩擦磨损、力学等性能最重要的结构参数之一。现有研究发现,具有高织构粗糙层热解碳的复合材料的力学性能值最优;具有各向同性层热解碳的密度最低,力学性能最差;而低织构热解碳易出现热应力微裂纹。
4.现有技术中,制备不同织构类型的热解碳多采用甲烷、丙烷或乙烯等烷烃类小分子或乙醇等醇类物质为单一前驱体。其中,甲烷作为常用烷烃类前驱体时,均气相反应过程不易控制,导致获取的高织构热解碳的工艺参数范围很窄;乙醇作为单一前驱体时,因其乙醇的扩散系数低,沉积过程中易形成有害产物。中国专利cn101439981a公开了碳/碳复合材料的制备方法,采用乙醇改性甲烷作为前驱体,其只是降低了前驱体的含碳量,并不能解决热解碳界面层相关的沉积速率;中国专利cn113004051a公开了一种sicf/sic复合材料燃料包壳的界面层结构及制备方法,将乙醇放入沉积炉中升温,再通入甲烷气体,设计了(pyc/sic)2复合界面层,解决了sicf/sic复合材料中界面层稳定性以及使用寿命的问题,但是该方法工艺复杂,且不能用来调整热解碳界面层的致密性和织构类型。
5.因此,需要研究一种制备热解碳界面涂层的方法来制备高织构热解碳结构进一步提高sicf/sic复合材料的韧性。
技术实现要素:
6.鉴于上述问题,本发明提供了一种使用混合前驱体制备热解碳界面涂层的方法,通过调控沉积工艺参数,制备致密均匀、厚度和织构可控的热解碳界面层。解决了现有技术中热解碳界面层制备过程中存在的沉积速率缓慢、加工过程不易控制、热解碳织构形态无
法有效调控的问题。
7.本发明的目的在于提供了一种使用混合前驱体制备热解碳界面涂层的方法,包括以下步骤:
8.s1、将sic纤维束置于相应的模具中,然后将模具放置于化学气相沉积炉内进行热解碳涂层沉积;
9.优选的,步骤s1中所述热解碳涂层沉积的工艺参数为:将所述沉积炉内抽真空,真空度小于100pa,通入氮气,沉积压力为2000~7000pa,将炉内温度升至1000~1200℃,并保温2-4h;所述氮气的通入流量为800-1000sccm;所述炉内温度的升温速率为5-10℃/min。
10.优选的,步骤s1中所述模具放置于化学气相沉积炉内距进气口距离为2-18cm。
11.进一步的,所述模具放置于化学气相沉积炉内距进气口距离为2cm。
12.本发明技术方案中调整了样品在化学气相沉积炉内距进气口距离,改变了样品与前驱体气体发生反应的时间,继而改变了前驱体气体在sic纤维表面的滞留时间。在反应温度、反应压力和总气体流量不变的情况下,反应区体积越小,滞留时间越短,即可获得高织构热解碳。
13.s2、待步骤s1中炉内温度升高至一定温度,在炉内通入甲烷和无水乙醇,沉积压力为2000~7000pa,开始沉积;
14.优选的,步骤s2所述无水乙醇的通入方式为:以氮气为载气,采用鼓泡法带入炉内,所述载气流量与所述甲烷的通入流量比为1-5:2-5;所述甲烷的体积分数为99.00-99.99%,无水乙醇的纯度为99.50-99.80%;所述沉积时间为2-4h。
15.进一步的,所述载气流量与所述甲烷的通入流量比为1:1;所述甲烷的通入流量为200-500sccm,载气流量为200-500sccm。
16.本发明技术方案通过调节随甲烷和乙醇前驱体流量比例,获得了热解碳界面层的织构形态发生由粗糙层热解碳到光滑层热解碳的转变。
17.本发明技术方案中使用甲烷和无水乙醇作为混合前驱体,既解决了单一使用甲烷作前驱体时,沉积速率慢,热解碳织构形态不易调控的问题,又解决了单一乙醇作为前驱体时,扩散系数低,实验过程不易控制易产生有害副产物的问题,在较宽工艺参数范围内制备得到力学性能优异的高织构热解碳界面涂层。
18.s3、结束沉积,停止通入甲烷和无水乙醇,继续通入氮气作为保护气体,调节炉内压力与步骤s2所述沉积压力一致,将炉内温度降至700-900℃后停止加热,使化学气相沉积炉自然冷却至室温,得到热解碳界面涂层。
19.优选的,步骤s3所述氮气的通入流量为800-1000sccm,所述温度降至700-900℃的冷却速度为5-10℃/min。
20.本发明技术方案通过精准调控反应温度、反应压力、反应时间,甲烷及乙醇前驱体的比例,系统调控了热解碳界面层的织构形态,提高了制备工艺稳定性和界面涂层的微结构可设计性。
21.与现有技术相比,本发明至少具有现如下有益效果:
22.(1)本发明使用甲烷和乙醇作为混合前驱体,既能克服使用甲烷作为单一前驱体时,沉积速率缓慢,热解碳织构形态不易调控的问题,又能克服使用乙醇作为单一前驱体时,扩散系数低,易生成烟炱及炭黑等有害产物,实验过程不易控制的问题,能在较宽工艺
参数范围内制备得到力学性能优异的高织构热解碳界面涂层;
23.(2)本发明通过精准调控反应温度、反应压力、反应时间,甲烷及乙醇前驱体的比例,能够系统调控热解碳界面层的织构形态,提高了制备工艺稳定性和界面涂层的微结构可设计性;
24.(3)本发明采用两种碳源混合前驱体,能够增加热解碳的产量,提高了界面涂层生产效率。
附图说明
25.附图仅用于示出具体实施例的目的,而并不认为是对本发明的限制。
26.图1为本发明使用的实验气路示意图;
27.图2为本发明实施例(1-1)~(1-9)所制备热解碳界面层拉曼光谱缺陷峰半高宽的原理图;
28.图3是本发明实施例(1-1)~(1-9)所制备热解碳界面层的截面扫描电镜照片原理图;
29.图4是本发明实施例(2-1)~(2-5)、(3-1)~(3-5)、(4-1)~(4-5)所制备热解碳界面层在不同沉积压力和沉积温度下的拉曼光谱缺陷峰半高宽变化的原理图;
30.图5是本发明实施例(2-2)~(2-4)、(3-2)~(3-4)、(4-2)~(4-4)所制备热解碳界面层在不同沉积压力和沉积温度下的厚度变化的原理图;
31.图6是本发明实施例5所制备热解碳界面层拉曼光谱;
32.图7是本发明实施例6所制备热解碳界面层的表面扫描电镜照片原理图。
33.附图标号说明:
34.1-甲烷质量流量计;2-氮气质量流量计;3-氮气质量流量计
具体实施方式
35.为了能够更清楚地理解本发明的上述目的、特征和优点,下面结合附图和具体实施方式对本发明进行进一步的详细描述。需要说明的是,在不冲突的情况下,本发明的实施例及实施例中的特征可以相互组合。另外,本发明还可以采用其他不同于在此描述的其他方式来实施,因此,本发明的保护范围并不受下面公开的具体实施例的限制。
36.本发明的一个具体实施例,如图1-7,公开了一种sicf/sic(碳化硅/碳化硅)复合材料界面涂层及其制备方法,具体实施步骤如下:
37.实施例1-1
38.s1、将sic纤维束缠绕在石墨框上,获得sic纤维预制体,将sic纤维预制体放入石墨模具中,然后将石墨模具分别放置于化学气相沉积炉内进行热解碳涂层沉积,将sic纤维预制体与化学气相沉积炉进气口的距离调整为2cm,在室温下抽真空至炉内压力为100pa,以1000sccm的流量通入氮气作为保护气体,使用真空泵调节炉内压力为2000pa,以10℃/min的升温速率将炉温从室温升温至1150℃,并保温2h;
39.s2、待步骤s1中炉内温度进入所述保温阶段,以200sccm的流量在炉内通入甲烷,同时以氮气为载气将乙醇通过鼓泡法载入化学气相沉积炉内,载气流量为200sccm,沉积压力为2000pa,沉积2h;
40.s3、沉积2h后,停止通入甲烷和乙醇,继续以1000sccm的流量通入氮气作为保护气体,调节炉内压力为2000pa,以10℃/min的冷速将温度降至900℃,使其与步骤s1所述真空度一致,自然冷却至室温,得到热解碳界面涂层。
41.实施例(1-2)~(1-9)与实施例1-1的区别在于:步骤s1、将sic纤维预制体与化学气相沉积炉进气口的距离分别调整为4、6、8、10、12、14、16、18cm。
42.实施例(1-1)~(1-9)通过调控反应区距沉积炉进气口的距离得到具有不同厚度和织构形态的热解碳界面层,图2为实施例(1-1)~(1-9)制备得到的热解碳界面层的拉曼光谱缺陷峰半高宽,其中,拉曼光谱缺陷峰半高宽波数小于90cm-1
的为高织构粗糙层热解碳,拉曼光谱缺陷峰半高宽波数在90~140cm-1
之间的为中织构光滑层热解碳,拉曼光谱缺陷峰半高宽波数大于140cm-1
的为低织构再生层热解碳;将不同织构形态的热解碳界面层的截面进行电镜扫描,结果如图3所示,图3(a)为高织构粗糙层热解碳界面的截面形貌,可以清晰地看到热解碳的层状结构,片层取向度高,图3(b)为中织构光滑层热解碳界面的截面形貌,片层取向度低,图3(c)为低织构再生层热解碳界面的截面形貌,为乱层石墨结构。由此可见,随着sic纤维预制体与沉积炉进气口的距离的增加,热解碳界面层的织构形态发生粗糙层热解碳
→
光滑层热解碳
→
再生层热解碳
→
光滑层热解碳的转变,即织构程度呈现先降低再增加的趋势。
43.实施例2-1
44.s1、将sic纤维束缠绕在石墨框上,获得sic纤维预制体,将sic纤维预制体放入石墨模具中,然后将石墨模具分别放置于化学气相沉积炉内进行热解碳涂层沉积,将sic纤维预制体与化学气相沉积炉进气口的距离调整为2cm,在室温下抽真空至炉内压力为100pa,以1000sccm的流量通入氮气作为保护气体,使用真空泵调节炉内压力为2000pa,以10℃/min的升温速率将炉温从室温升温至1000℃,并保温2h;
45.s2、待步骤s1中炉内温度进入所述保温阶段,以200sccm的流量在炉内通入甲烷,同时以氮气为载气将乙醇通过鼓泡法载入化学气相沉积炉内,载气流量为200sccm,沉积压力为2000pa,沉积2h;
46.s3、沉积2h后,停止通入甲烷和乙醇,继续以1000sccm的流量通入氮气作为保护气体,使用真空泵调节炉内压力为2000pa,以10℃/min的冷速将温度降至900℃,使其与步骤s1所述真空度一致,自然冷却至室温,得到热解碳界面涂层。
47.实施例(2-2)~(2-5)与实施例(2-1)的区别在于:步骤s1、沉积炉内温度分别升高至1050、1100、1150和1200℃。
48.实施例(3-1)~(3-5)分别与实施例(2-1)~(2-5)的区别在于:步骤s1、沉积炉内压力为5000pa。
49.实施例(4-1)~(4-5)分别与实施例(2-1)~(2-5)的区别在于:步骤s1、沉积炉内压力为7000pa。
50.本实施例通过调节沉积温度和沉积压力制备得到具有不同厚度和织构形态的热解碳界面层,图4为实施例(2-1)~(4-5)制备得到的热解碳界面层的拉曼光谱缺陷峰半高宽,如图4所示,同一沉积压力下,随沉积温度升高,热解碳界面层的织构程度呈现先增高再降低的趋势,而在同一沉积温度下,随沉积压力升高,热解碳界面层的织构程度降低。通过实施例(2-1)~(4-5)获得制备高织构热解碳界面层的沉积温度为1100℃和1150℃,沉积压
力为2kpa。
51.分别在2000、5000、7000pa获取1050、1100、1150℃下热解碳界面层的厚度变化,如图5所示,在同一炉内压力条件下,热解碳沉积速率随沉积温度的升高而增加。
52.实施例5
53.实施例5与实施例(1-1)的区别在于:s2、待步骤s1中炉内温度进入所述保温阶段,以200sccm的流量在炉内通入甲烷,同时以氮气为载气将乙醇通过鼓泡法载入化学气相沉积炉内,载气流量为100sccm,沉积压力为2000pa,沉积2h;
54.图6为沉积压力为2000pa时,不同前驱体比例下制备得到的热解碳界面层的拉曼光谱,(a)为粗糙层热解碳的拉曼光谱,对应甲烷及载气流量比为1:1,(b)为光滑层热解碳的拉曼光谱,对应甲烷及载气流量比为2:1。由此可知,随甲烷和乙醇前驱体流量比比例升高,热解碳界面层的织构形态发生由粗糙层热解碳到光滑层热解碳的转变。
55.实施例6-1
56.实施例(6-1)与实施例(1-1)区别在于:步骤s1、以10℃/min的升温速率将炉温从室温升温至1100℃,保温2h。
57.实施例6-2
58.实施例(6-2)与实施例(6-1)区别在于:步骤s1、以10℃/min的升温速率将炉温从室温升温至1100℃,保温4h。
59.本实施例通过调节反应时间制备得到具有不同厚度和织构形态的热解碳界面层,随沉积时间增加,热解碳界面层的织构形态发生由粗糙层热解碳到再生层热解碳的转变。将不同织构形态的热解碳界面层的表面进行电镜扫描,结果如图7所示。图7(a)为高织构粗糙层热解碳涂层的表面形貌,高织构粗糙层热解碳主要发生表面连续生长机制,因而形成光滑型的热解碳形貌;图7(b)为低织构再生层热解碳涂层的表面形貌,低织构粗糙层热解碳主要发生气相形核机制,因而热解碳涂层表面有颗粒状大分子生成。
60.以上所述,仅为本发明较佳的具体实施方式,但本发明的保护范围并不局限于此,任何熟悉本技术领域的技术人员在本发明揭露的技术范围内,可轻易想到的变化或替换,都应涵盖在本发明的保护范围之内。
再多了解一些
本文用于创业者技术爱好者查询,仅供学习研究,如用于商业用途,请联系技术所有人。